Automatisation des Job Shops ? Vous pariez !
Un seul opérateur peut parfois s'occuper de plusieurs robots, dont chacun s'occupe de plusieurs machines - tout s'additionne !
Si "l'automatisation" est le bourdonnement constant que vous entendez de pratiquement tout le monde dans le travail des métaux ces jours-ci, les propriétaires d'ateliers de travail pourraient être les seuls à crier "Non!" Ou au moins « Attendez ! » Comment, demandent-ils, pouvez-vous automatiser de manière rentable des pièces à faible volume et à grande diversité ? Pourtant, ce n'est pas seulement faisable, mais probablement nécessaire.
Comme Steve Alexander, vice-président des opérations chez Acieta LLC, un intégrateur d'automatisation avec des sites à Waukesha, Wis., et Council Bluffs, Iowa, l'a dit :« Les États-Unis sont en tête du monde en matière de fabrication, mais ont également l'un des taux horaires de fabrication les plus élevés. les coûts de main-d'œuvre. Les magasins d'emploi ne sont pas seulement en concurrence avec d'autres magasins locaux pour les affaires, ils sont également en concurrence avec d'autres pays. L'automatisation peut réduire leurs coûts afin qu'ils soient plus compétitifs."
Il a ajouté que la demande de capacité de fabrication dépasse l'offre de main-d'œuvre disponible et que "les ateliers de travail peuvent avoir du mal à rivaliser avec des ateliers d'usinage plus grands et mieux établis" pour des talents toujours plus chers. Mais un robot peut s'occuper de plusieurs machines et, dans certains cas, un seul opérateur peut s'occuper de plusieurs robots, chacun s'occupant de plusieurs machines.
"Cela libère les opérateurs pour effectuer des opérations secondaires, comme l'ébavurage des pièces, l'assemblage ou passer plus de temps sur les contrôles de qualité", a déclaré Alexander. Pour ne citer que deux exemples, Central United à Newburg, Wisconsin, utilise un seul robot FANUC M-20iB pour s'occuper de deux tours. Un autre client d'Acieta à New Berlin, Wisconsin, utilise un seul robot FANUC R-2000iB pour s'occuper de quatre machines. "Dans les deux cas, il n'y a qu'un seul opérateur responsable du chargement des pièces brutes sur le convoyeur ou la file d'attente pour que le robot les saisisse."
Alexander a ajouté une autre raison impérieuse d'automatiser :l'ergonomie. « Les blessures au travail sont une préoccupation pour les ateliers de toutes tailles. Quelque chose d'aussi simple que de charger une pièce dans un mandrin de tour peut rapidement se transformer en blessure de stress répétitif pour un opérateur lorsque ce processus est répété des centaines de fois par jour. Entre le temps perdu et les sinistres, ces blessures coûtent aux entreprises des milliards de dollars chaque année. Des robots correctement intégrés peuvent supprimer un processus répétitif de l'opérateur, améliorant ainsi le bien-être des employés."
Options et intégrateurs
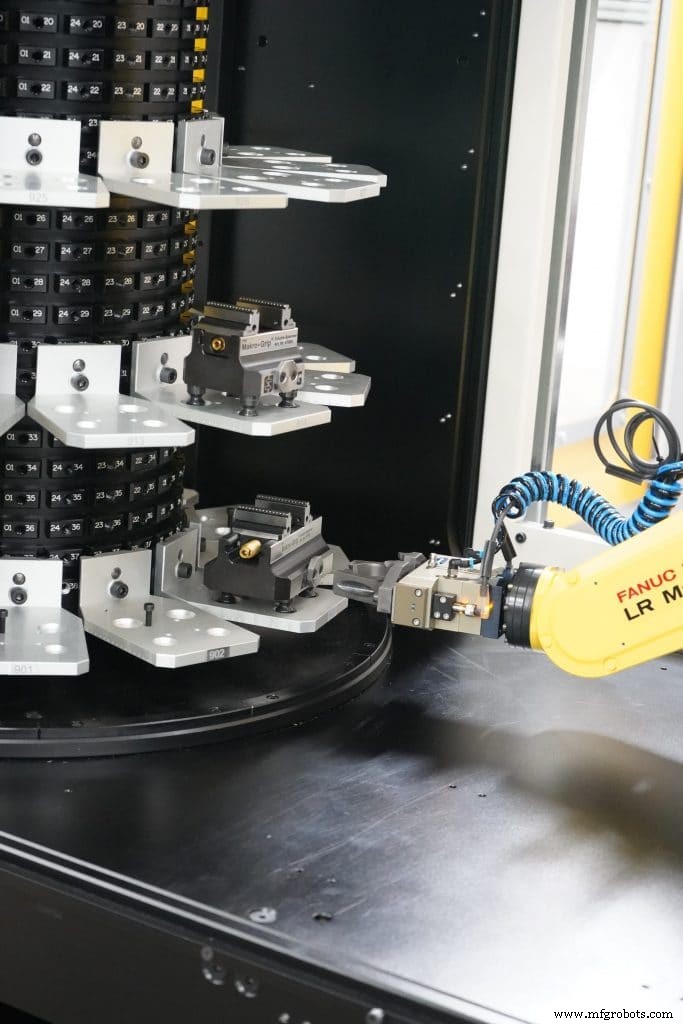
Jusqu'ici tout va bien. Mais comme John Lucier, responsable de l'automatisation pour Methods Machine Tools Inc., Sudbury, Mass., l'a expliqué, le simple objectif de « fabriquer plus de pièces plus efficacement » peut conduire à des approches très différentes selon le type de travail produit et les volumes impliqués. .
Par exemple, supposons qu'un atelier de taille moyenne doive changer de poste plusieurs fois par semaine. "Avec une bonne planification, une cellule pourrait être changée pendant le quart de travail, ce qui permettrait une bonne quantité de production sans surveillance pendant le quart de travail suivant." Et dans ce contexte, la vitesse requise du robot dépendrait en grande partie du temps de cycle d'usinage des pièces produites. Plus le temps de cycle est court, plus le robot doit être rapide et moins un robot peut prendre en charge plusieurs machines.
Mais les magasins avec des volumes encore plus faibles - même des tailles de lot d'un seul - peuvent également être de bons candidats pour l'automatisation, a expliqué Lucier. Sauf que « la considération la plus importante est de réduire le temps de changement, voire d'éliminer totalement le temps de configuration. Les gens sont rattrapés par le temps de cycle et le temps de chargement/déchargement, mais si vos volumes sont si faibles que la moitié de votre temps est consacrée au changement, alors attaquer le temps de changement, même au détriment du temps de cycle, peut avoir du sens. »
Une façon « d'éliminer » la configuration est de l'automatiser, et les robots d'aujourd'hui peuvent être programmés pour changer à la fois leur propre outillage en bout de bras et le serrage de la machine. Une autre approche consiste à charger des palettes courantes à partir d'un carrousel (ou d'un autre type de gerbeur) quelle que soit la pièce produite. Cela élimine le besoin de changer l'outillage du robot ou de programmer différents mouvements de chargement/déchargement pour différentes pièces.
Le système Methods PlusK va encore plus loin dans ce concept et charge également les porte-outils à partir du carrousel. Conçu pour prendre en charge les machines de la série RoboDrill de FANUC, le carrousel de PlusK comporte cinq anneaux, chacun ayant 12 stations, pour un total de 60 stations. Chaque station peut contenir une palette de pièces ou un porte-outils et le robot peut charger les deux pièces sur la table de travail du RoboDrill et les outils dans la tourelle à 21 outils intégrée de la machine.
Mais comme l'a souligné Lucier, si vous souhaitez automatiser la production de 30 ou 40 pièces complètement différentes, 21 outils peuvent ne pas suffire. « Nous chargeons généralement des pièces dans de minuscules étaux à cinq axes de fournisseurs comme Lang Technovation », a expliqué Lucier. « Et nous mélangeons et assortissons généralement les pièces et les outils dans le carrousel. Disons qu'un travail nécessite cinq outils qui diffèrent des outils utilisés pour le travail précédent. Je peux utiliser le robot pour charger chaque outil selon les besoins, ou pour charger les cinq outils dans la tourelle en même temps, un peu comme un opérateur configurerait une tâche. »
Si ces considérations commencent à vous faire mal à la tête, c'est compréhensible. Parce que même s'il est devenu beaucoup plus facile de mettre en œuvre l'automatisation ces dernières années, il est encore assez difficile pour la plupart des ateliers de travail de tirer parti d'intégrateurs comme Acieta et Methods. Du point de vue de Lucier, la programmation du robot est la partie la plus facile. Des choses comme la gestion du serrage automatique, l'élimination des copeaux dans la zone de travail et la meilleure façon de présenter les pièces au robot constituent le plus grand défi. C'est là que les conseils d'experts sont vraiment payants.
Automatiser les anciennes machines
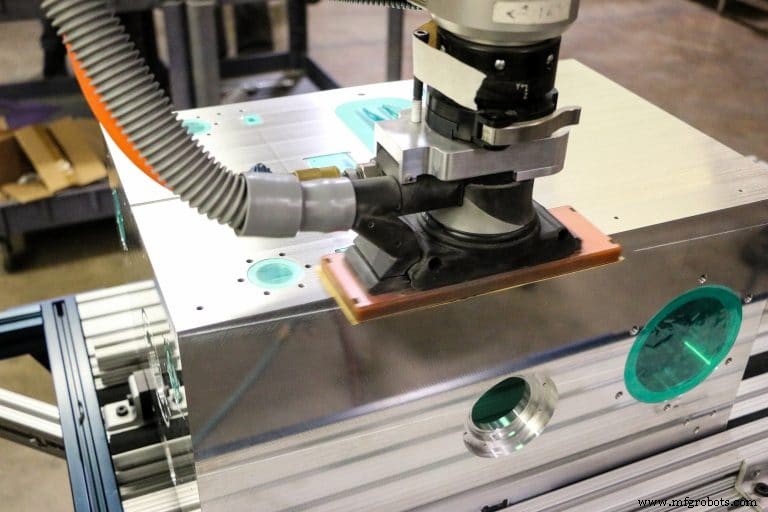
Voici un exemple de comment cela peut arriver. À la mi-2017, Gary Kuzmin, propriétaire de All Axis Machining à Dallas, au Texas, était un exemple classique de la frustration de l'atelier. Il avait plus de travail potentiel que la main-d'œuvre disponible ne pouvait en supporter et un magasin rempli de centres d'usinage à cinq axes allemands haut de gamme, d'EDM et d'autres technologies que les équipementiers ne pouvaient pas automatiser économiquement avec le type de polyvalence qui pourrait le sortir de là. lier. Sa solution consistait à investir dans un robot collaboratif d'Universal Robots (UR), Ann Arbor, Michigan.
Comme tout propriétaire d'atelier, la principale exigence de Kuzmin était de conserver une "flexibilité totale" dans son fonctionnement. « Nous ferons une partie pendant deux ou trois jours, puis nous passerons à une autre. Au cours d'un mois donné, nous pourrions fabriquer 30 à 40 pièces différentes sur une seule machine. Il avait donc besoin d'un robot facile à installer et à changer. Et il avait besoin de fonctionnalités telles que des pinces à contrôle de force pour que le robot puisse s'adapter à différentes pièces et passer d'un brut à une pièce finie à paroi plus fine.
UR livré sur tous les plans. Ses robots disposent d'une interface de programmation sur un pendentif portatif. Ils fonctionnent côte à côte avec les humains en toute sécurité car les robots s'arrêtent automatiquement lorsqu'ils contactent un opérateur (d'où le terme robot collaboratif, ou « cobot »). Ils sont faciles à former et non intimidants.
Kuzmin a expliqué que l'une des principales raisons de la flexibilité de la solution d'UR est une architecture ouverte qui a permis à des tiers de développer des logiciels, des systèmes de vision, des effecteurs terminaux et d'autres accessoires qui fonctionnent avec les robots UR. UR facilite l'effort d'intégration en fournissant une salle d'exposition en ligne unique appelée UR+.
Même avec cela, Kuzmin a découvert qu'il n'y avait pas de solution prête pour programmer le robot pour effectuer le ponçage ou l'ébavurage, deux fonctions qu'il souhaitait automatiser car elles sont difficiles pour les humains, et en particulier pour les travailleurs âgés. All Axis a donc utilisé le kit de développement logiciel gratuit d'UR pour créer ses propres routines, qui suivent la courbure de la pièce en fonction du modèle CAO.
Ces plug-ins intègrent le contrôle de l'application via le pendentif d'apprentissage du cobot. "Universal Robots a fait un travail fantastique en mettant cette solution à la disposition de magasins comme le nôtre", a déclaré Kuzmin. « Nous ne sommes pas enfermés dans un environnement propriétaire. Au lieu de cela, on nous donne un livre de recettes avec un moyen simple d'étendre la communication », ajoutant qu'All Axis utilise des protocoles tels que TCP/IP, Ethernet, Modbus et Profinet pour connecter les cobots et les machines.
"Un autre avantage est que nous n'avons pas à payer de contrats de licence spéciaux - tout vient avec l'achat du cobot UR", a déclaré Kuzmin. "On s'inscrit sur le site UR pour devenir développeur, et on télécharge les éléments dont on a besoin."
Dans un autre exemple, All Axis a décidé qu'il voulait pouvoir déplacer un cobot d'une machine à l'autre le plus rapidement possible. Le défi consistait à créer un système qui réorientait le cobot vers la machine suivante et le fixait au sol sans percer de trous dans le béton. La solution était d'époxy un réceptacle sur le béton et de fixer une goupille d'indexation.
"Si le robot doit être déplacé ou entretenu, il vous suffit de déverrouiller et de tirer les broches et de déplacer le robot au besoin", a déclaré Kuzmin. « Lorsque vous repositionnez le robot et verrouillez les broches, tout est toujours indexé. Nous avons également fixé le plateau de présentation au support du robot, de sorte que sa position par rapport à l'axe du robot ne change jamais. »
En quelques mois à peine, Kuzmin et son équipe sont devenus si bons dans l'intégration des cobots (ils en ont maintenant sept) et tellement enthousiasmés par les avantages de l'automatisation qu'ils ont créé une société distincte appelée All Axis Robotics. Bien que Kuzmin ait déclaré qu'il est relativement facile d'automatiser une nouvelle machine en dépensant environ 150 000 USD avec l'OEM, il voit un énorme potentiel dans l'automatisation des anciennes machines, ce qui est leur priorité.
Pour prendre un exemple de la façon dont l'automatisation a contribué au résultat net de All Axis Machining, un travail qui prenait généralement six mois pour s'exécuter s'est terminé en 2 mois et demi en utilisant le robot. « C'était phénoménal. Le retour sur investissement était d'environ sept à huit mois », a déclaré Kuzmin.
Dans son innovation peut-être la plus impressionnante, All Axis a combiné un robot UR avec un microscope et une caméra prêts à l'emploi, ainsi que l'intelligence artificielle (IA) et l'apprentissage en profondeur, pour créer un système qui détecte les bavures, les bords roulés ou toute anomalie (telle que matériel manquant) sur une pièce.
C'est important, car comme l'a expliqué Kuzmin, de nombreuses bavures ne peuvent être identifiées que sous grossissement et les yeux d'un humain se fatigueront après seulement 20 à 30 minutes d'une telle inspection. Mais c'est aussi difficile à automatiser.
"Les bavures sont comme des flocons de neige - il n'y en a pas deux pareils", a déclaré Kuzmin. "Notre système, que nous appelons Aurora, utilise l'IA pour apprendre à quoi ressemble une bavure. Plus il voit de bavures, mieux il est capable de les détecter. Le système identifiera la bavure, la classera et triera la pièce après l'avoir rejetée en raison de la bavure. Il enregistre également l'inspection et l'emplacement de la bavure afin que les opérateurs puissent revenir en arrière pour corriger efficacement la pièce et la déplacer. »
All Axis a introduit Aurora en 2018 et Kuzmin dit que la réponse la plus importante a été :"Nous recherchons quelque chose comme ça depuis des années !" Une prochaine version du système inclura également la possibilité d'insérer des inserts hélicoïdaux (communément appelés Heli-Coils) et du matériel dans les pièces.
Les robots industriels contre-attaquent !
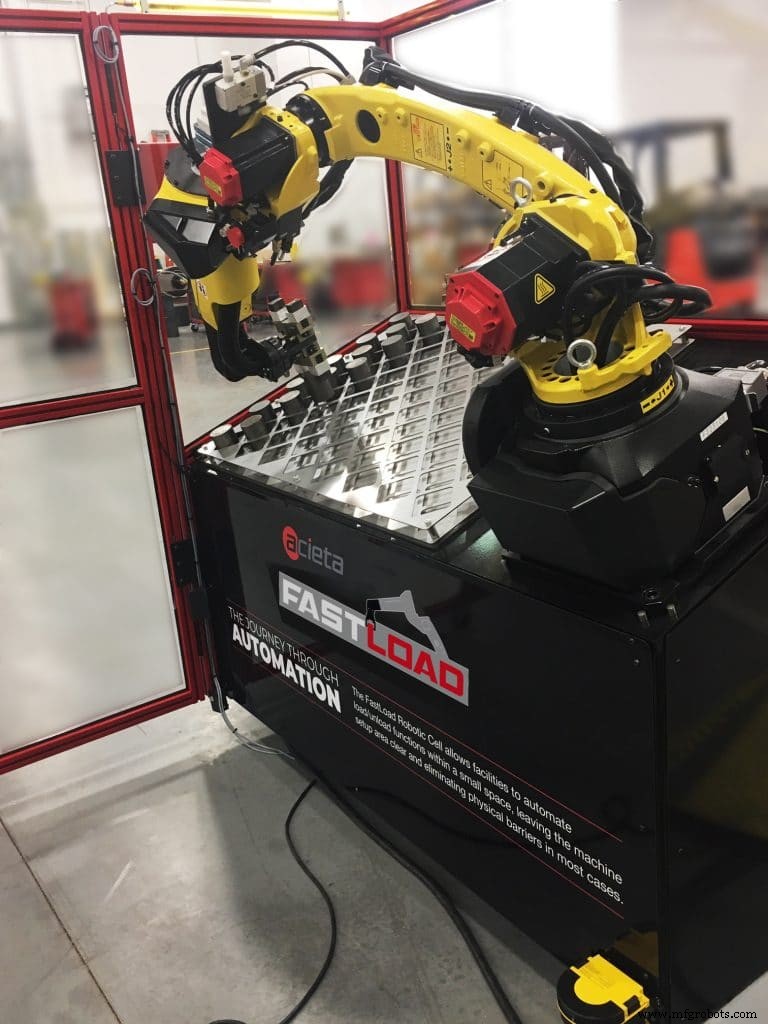
Comme indiqué, les cobots UR sont faciles à configurer et à intégrer à une variété de machines et d'accessoires. Mais les fournisseurs de robots industriels tels que FANUC et KUKA Robotics ont remarqué des fonctionnalités telles que le pendentif d'apprentissage manuel intuitif et ont présenté leurs propres versions.
Lucier de Method a reconnu qu'« à une certaine époque, il était absolument vrai que les robots collaboratifs étaient plus faciles à programmer. Mais mettre en place un robot industriel n'est plus vraiment différent de mettre en place un robot collaboratif. Même la fonction de configuration "saisir et faire glisser" est disponible sur les robots traditionnels, bien que Lucier ait déclaré qu'il valait mieux l'utiliser dans les cas où vous souhaitez simplement placer la pièce sur une table ou contre un bloc.
« C'est parfait pour quelque chose comme apprendre au robot à charger une MMT parce que la machine a juste besoin de savoir approximativement où se trouve la pièce afin de trouver le bord, puis de continuer à effectuer les mesures », a-t-il déclaré. "Mais si je charge dans un mandrin ou un étau, j'ai plus de contrôle lorsque je l'enseigne avec le pendentif de programmation."
Il existe également une variété d'accessoires pour les robots industriels. Par exemple, a déclaré Lucier, les pinces à changement rapide et à contrôle de force ne sont pas propres aux cobots. "Schunk propose une gamme de pinces à détection de force qui utilisent des servomoteurs, s'éloignant de la pneumatique, qui est plus difficile à commuter. Vous pouvez vraiment composer avec l'électricité. »
Les robots industriels ont également des solutions qui vous permettent de repositionner rapidement le robot d'une machine à l'autre. Dans le cas de FANUC, une caméra sur le robot scanne trois décalcomanies sur la "nouvelle" machine pour se réorienter automatiquement.
Mais après des mois d'essais, Lucier a déclaré qu'ils ne trouvaient pas de situation dans laquelle une telle capacité serait utile. « Déplacer un robot d'une machine à l'autre implique plus que simplement déplacer le robot. Pensez à toutes les choses que vous devez changer :peut-être l'outillage en bout de bras, l'entrée, la sortie..." La meilleure solution est celle dans laquelle chaque machine a son propre robot ou un robot dessert plusieurs machines, peut-être avec des effecteurs à double extrémité afin qu'il puisse basculer entre les types de pièces sans intervention.
Il est également vrai que des intégrateurs comme Acieta et Methods peuvent ajouter des robots traditionnels aux machines héritées, et les prix des robots sont à peu près les mêmes que ceux des cobots. Ainsi, compte tenu des offres actuelles, le plus grand avantage des cobots est leur capacité à fonctionner à proximité des humains sans l'espace et les frais d'une clôture.
L'inconvénient est qu'ils sont plus lents que les robots industriels traditionnels et se limitent à des pièces plus légères. Le plus grand modèle d'UR gère des pièces jusqu'à 24 lb (10 kg). Des temps de chargement/déchargement plus lents ne sont pas significatifs sur les pièces avec des temps de cycle longs, mais ils peuvent réduire la production sur des travaux de volume moyen à élevé avec des temps de cycle plus courts.
Kuzmin d'Axis Machining ne voit pas le besoin de vitesse, "juste la cohérence et la fiabilité, en particulier sur les pièces avec un temps de cycle long. It’s better to have a cobot load parts at a reliable speed and then use it to deburr other parts while the machine runs. And if you don’t need the speed, why risk it?”
Lucier and Alexander caution against exaggerating the benefit of being able to work right next to the robot. For one thing, Lucier pointed out, you already have to shield the operator from the machining area. Alexander added that if a cobot is handling a part with sharp edges (as is commonly the case in machining), “it’s not collaborative or safe for an operator to work in its proximity anyway.”
Both Lucier and Alexander said combining “collaborative techniques” with industrial robots offered a useful compromise. “For those manufacturers seeking an open floor with minimal fencing, industrial robots have the ability to work in a fenceless environment by using area safety scanners,” explained Alexander. “And they can work in this fenceless environment without sacrificing speed. When an operator enters the first safety zone, the robot slows down. When the operator enters the second safety zone, the robot stops completely.”
On the other hand, said Lucier, since the safety zone for this approach is 3-4′, the robot would often be slowing down if fork trucks or other traffic passed by frequently.
As suggested earlier, one area that’s perfect for cobots is in tending a CMM. “CMM’s are intrinsically safe to begin with,” as Lucier put it. “There’s no guarding, except around moving components. They’re not fast. You can stand right next to them. And generally you’re not putting the part into a fixture, perhaps just holding it against a V-block or something similar. That’s where I’ve seen a collaborative robot shine.”
Both experts agree, as Alexander summed up, that “industrial robots are much more applicable than cobots in the majority of job shop and manufacturing applications.”
Software Considerations
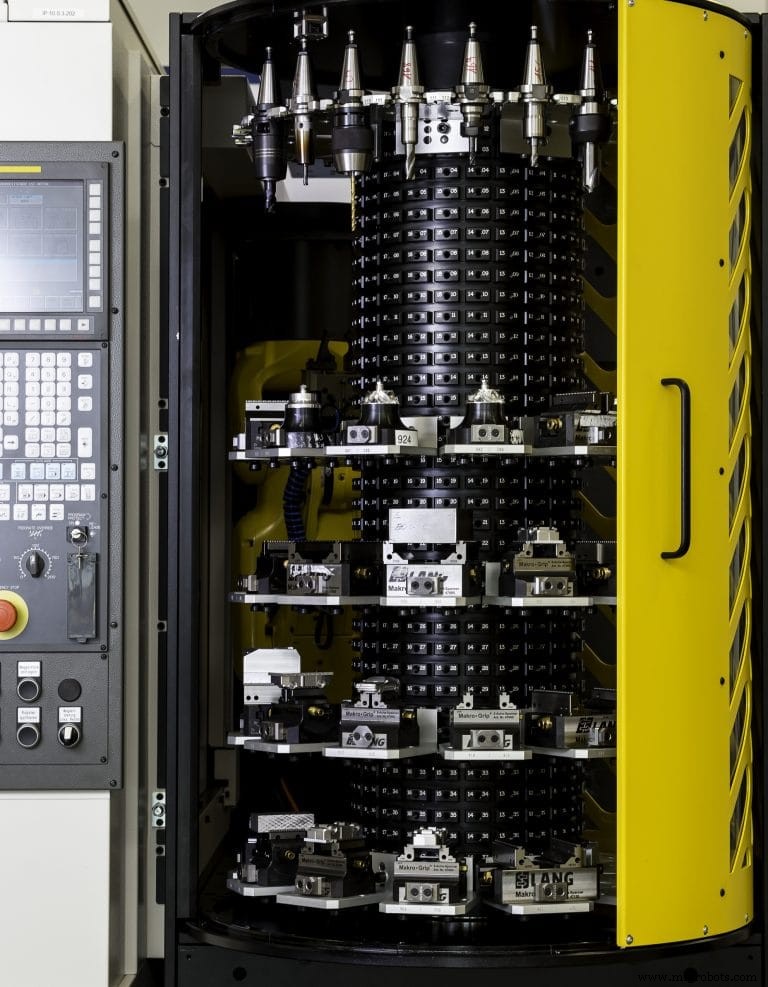
According to Greg Mercurio, president of Shop Floor Automations, La Mesa, Calif, “software is the most essential component in job shop automation.” He said direct numerical control (DNC) software (also known as distributed numerical control software or “drip feed” software) “allows for streamlined machine communication, as well as revision control for managing quality/scrap, and a means to organize thousands of programs.”
The main function of DNC software is to send machining programs directly to the machine, enabling a machine with a relatively low-grade control to handle a complex surface.
Mercurio and all the experts agree that some degree of machine monitoring is helpful “to increase uptime and machine capacity.” Mercurio added that Production Data Management software enables companies to go paperless and that “tool crib management is also a necessity. The best part is that these solutions can all integrate with CAD/CAM, ERP, MES, CMMS and more.”
On the other hand, he pointed out that smaller shops can greatly benefit from a simple hardware addition before spending thousands on software. For example, adding an RS232 to USB interface to older equipment makes drip-feeding programs easier.
“The hardware is easy to use, set up and maintain, so it is the least time-consuming automation
option for a smaller shop. Older RS232 machines can use a USB drive like newer CNC machines that have that function built in from the factory. It’s also a more affordable way for them to modernize their shop floor without replacing equipment altogether. It also allows for affordable memory upgrades,” added Mercurio.
Getting back to robots, Alexander said there are numerous software packages offered by robot OEMs and third parties that enable robot programming off-line on a PC while the robot keeps working. “These software packages allow you to load a CAD file and then give you the freedom to ‘draw’ your robot path using a stylus or a mouse,” explained Alexander. “The software will then convert your drawn path into robot code that can be loaded directly into the robot.”
It’s fitting that job shop owner Kuzmin gets the last word:“I wanted to improve productivity. I did it by adding robots. And I’m very pleased with what we’ve accomplished. While doing it I said we ought to make this available to everybody out there, because that’s what’s going to make manufacturing in our country much more competitive.”
Système de contrôle d'automatisation
- Pariez sur le cloud qui vous convient
- Combien de détails pour les plans de travail ?
- Vous n'avez pas le temps de négliger la sécurité des travailleurs
- La tourelle de travail final réduit le temps de cycle
- Si vous voulez améliorer quelque chose, mesurez-le
- L'automatisation des petites tâches de programmation CN rapporte gros au fil du temps
- Cinq signes que vous avez besoin de réparations de grue
- Comment savoir si vous avez besoin de nouvelles pièces de grue
- Avez-vous besoin d'un nouveau matériel de freinage industriel ?