Les secteurs de la fabrication non automobile se tournent vers la robotique
Mais les robots peuvent ne jamais exécuter complètement la production.
Des robots moins chers avec plus de fonctions, ainsi que des cellules de travail et des installations plus flexibles qui facilitent la robotique, accélèrent la croissance des installations de fabrication automatisées dans le secteur non automobile. Cependant, les idées sur la question de savoir si la robotique et l'automatisation conduisent à une fabrication sans éclairage dans l'atelier sont mitigées.
Alors que le nombre total d'unités vendues et les revenus de la robotique en 2018 étaient en baisse, les commandes de robots industriels ont en fait augmenté de 24 % par rapport à l'année précédente dans les secteurs des sciences de la vie, de l'alimentation et des biens de consommation, des plastiques et du caoutchouc et de l'électronique, selon la Robotics Industries Association. .
Il existe de nombreuses raisons à cette croissance, parmi lesquelles les systèmes robotiques sont plus faciles à installer, à intégrer dans un système et un programme d'automatisation.
Par exemple, l'approche de la société suisse ABB consiste à produire une gamme de solutions d'automatisation standardisées et modulaires au lieu de concevoir et d'ingénierie des cellules de travail sur mesure pour chacun de ses clients.
"Tout cela réduit le temps parce que nous ne passons pas des semaines ou des mois à les concevoir et à les concevoir", a déclaré Dwight Morgan, vice-président des ventes et du marketing pour ABB USA Robotics, Auburn Hills, Michigan. "Ainsi, dans toutes les applications dans lesquels nous nous engageons, comme l'entretien de machines-outils ou l'emballage, nous disposons d'une famille de solutions standard qui nous permettent d'agir très rapidement et d'établir des délais de livraison courts. »
FANUC America Corp., Rochester Hills, Michigan, propose des robots mobiles qui peuvent être mis sur roues ou ramassés avec un chariot élévateur et mis en place.
"Et, généralement, ils sont un peu plus autonomes, donc il y a moins de connexions dessus", a déclaré Rick Maxwell, directeur de l'ingénierie pour l'industrie générale et le segment automobile.
Le collègue de Maxwell, John Tuohy, directeur exécutif des comptes mondiaux, a déclaré que FANUC avait également un certain nombre de clients intéressés par l'assistance au levage semi-autonome.
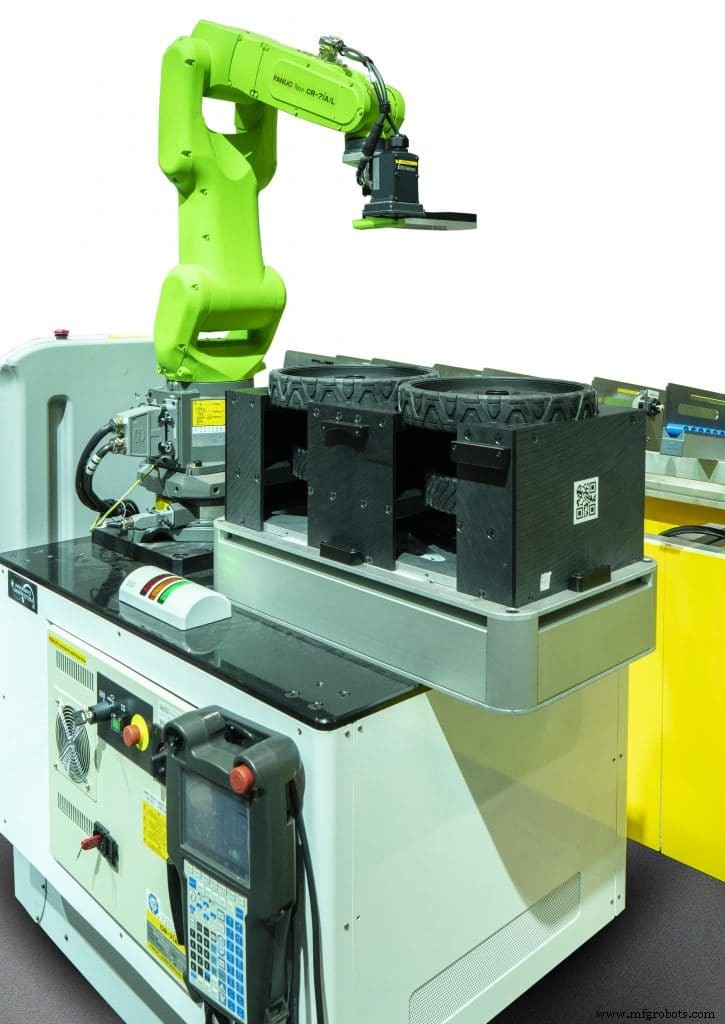
"Dans une forme de collaboration, FANUC a la capacité d'adapter n'importe lequel de nos robots en un dispositif d'assistance au levage similaire à ce que l'on peut voir avec un contrepoids ou un dispositif d'assistance au levage dans une usine aujourd'hui", a déclaré Tuohy. "Un opérateur manipule manuellement le robot dans la position souhaitée, termine la tâche et renvoie le robot pour prendre une autre pièce de manière autonome."
Tom Fischer, directeur des opérations de RobotWorx, Marion, Ohio, une société qui vend et intègre des robots ABB, FANUC, Kuka et Motoman dans des cellules de travail, a déclaré que les progrès de la communication Ethernet par rapport aux configurations analogiques ont rendu beaucoup plus facile l'utilisation de plusieurs fonctions. (comme interagir avec d'autres robots, des interfaces homme-machine et des stations de commande à bouton-poussoir) du robot en même temps.
"Vous pouvez transmettre plusieurs signaux à la fois au lieu d'avoir à câbler chaque signal individuellement", a-t-il déclaré. "C'est juste une simple prise, puis la configuration de votre E/S Ethernet."
Il y a aussi un facteur humain qui facilite l'installation des robots, a déclaré Fischer. "Je pense que nous arrivons à une génération qui comprend mieux l'électronique, et grâce à leur expérience avec les jeux vidéo, ils sont plus aptes à contrôler les choses avec un clavier (ou un pendentif d'apprentissage robotique) que directement", a déclaré Fischer. "Ils peuvent appliquer cette expérience à la robotique."
Chez MC Machinery Systems Inc., la robotique en aval est la prochaine grande chose. La filiale de Mitsubishi Corp. est basée à Elk Grove Village, dans l'Illinois, et vend des machines d'électroérosion à fil, des fraiseuses et des découpeuses laser, et les intègre dans des lignes automatisées.
"Vous prenez une pièce, vous la choisissez, vous l'empilez correctement et elle se déplace vers un endroit où la robotique peut la déplacer vers un emplacement séparé", a déclaré Jason LeGrand, spécialiste de l'automatisation. "Peut-être qu'il passe par une machine qui fait gagner du temps ou un aplatisseur ou une presse plieuse. C'est la prochaine grande étape et nous organisons littéralement des réunions avec des intégrateurs pour connaître leurs exigences pour y parvenir. »
Faciliter la robotique en aval est l'acquisition par Mitsubishi en 2018 d'Astes4, une société suisse qui fabrique Astes4Sort, un système de fabrication flexible conçu pour le tri.
"Ils sont absolument, sans aucun doute, à la pointe du tri automatisé des pièces d'un laser industriel", a déclaré LeGrand. "Leur fonction est la prochaine étape où nous devons prendre notre automatisation laser. L'Astes4Sort prend les pièces finies qui sortent et les empile comme on lui dit de le faire ; qui, en soi, devient très attrayant pour les utilisateurs finaux. »
Les pièces sont empilées et palettisées, prêtes pour la prochaine étape du processus de fabrication. "Cela facilite beaucoup l'intégration d'une opération robotique à l'arrière, car nous savons qu'il existe une pile de pièces similaires, les unes sur les autres, dans la même orientation", a déclaré LeGrand. "C'est la première étape pour permettre à un robot de partir de là et de passer à l'opération suivante sans avoir à disposer d'un système de vision plus coûteux ou quelque chose de ce genre."
Les prix des robots s'aplatissent-ils ?
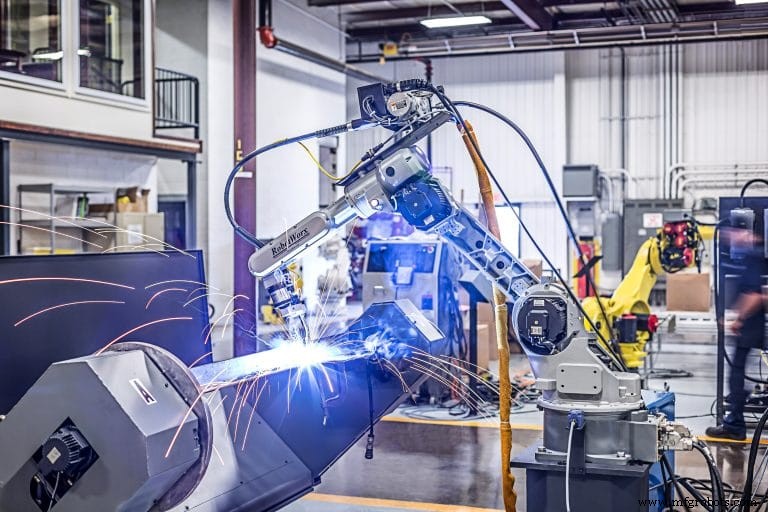
Historiquement, les robots sont devenus moins chers, mais selon des informations anecdotiques, les prix se sont stabilisés tandis que la valeur a augmenté.
Au cours des 30 dernières années, le prix moyen d'un robot industriel a diminué de moitié, selon le consultant mondial en gestion McKinsey &Co. Le prix de vente moyen des robots industriels est passé de 63 000 $ en 2009 à 45 000 $ en 2018, selon statista.com.
Le site Web de RobotWorx, qui vend des robots neufs et reconditionnés, rapporte que la nouvelle robotique industrielle, avec contrôleurs et pendentifs d'apprentissage, coûte entre 50 000 $ et 80 000 $. En règle générale, les robots reconditionnés coûtent deux fois moins cher que les nouveaux robots, selon RobotWorx.
Dans un passé récent, le prix des robots n'a pas vraiment diminué, mais les entreprises de robotique ont ajouté plus de fonctionnalités, a déclaré Fischer de RobotWorx.
Un exemple de fonctionnalité améliorée se trouve dans l'interface homme-machine, a-t-il déclaré. « Dans le passé, vous deviez câbler un accessoire secondaire à utiliser comme IHM », a-t-il déclaré. "Maintenant, des entreprises comme FANUC ajoutent cela dans leur logiciel afin qu'il puisse être exécuté à partir de leur pendentif."
Un autre exemple de fonctionnalité supplémentaire peut être vu dans les robots collaboratifs, a-t-il déclaré. "Leur plus grande utilisation est dans l'entretien des machines, c'est le plus chaud en ce moment", a-t-il déclaré. "Vous pouvez avoir un opérateur dans la cellule de travail avec le robot travaillant côte à côte."
Maxwell de FANUC était d'accord avec l'aspect fonctionnalité. Tout comme dans l'industrie informatique, où vous ne payez pas nécessairement moins pour un ordinateur portable mais en avez plus pour votre argent, lorsque vous payez le même prix pour un robot, vous obtenez beaucoup plus de fonctionnalités. Les robots d'aujourd'hui sont plus rapides, ont plus de capacité de calcul, plus de puissance de traitement et/ou une charge utile plus élevée, a-t-il déclaré.
LeGrand de MC Machinery a également accepté. "[Les robots sont] mieux adaptés à une plus grande variété d'applications", a-t-il déclaré. « En conséquence, les fabricants les utilisent pour plus. Ce qui se passe, c'est que les fabricants prennent une pile de pièces bien coupées et les livrent à un endroit où les robots peuvent y accéder.
"Maintenant, les fabricants disent" Que puis-je faire à partir de maintenant avec un robot pour rationaliser l'opération et lui donner un temps de cycle reproductible afin que nous puissions planifier efficacement la production ", et ainsi de suite", a-t-il poursuivi.
Utilisez vos mains
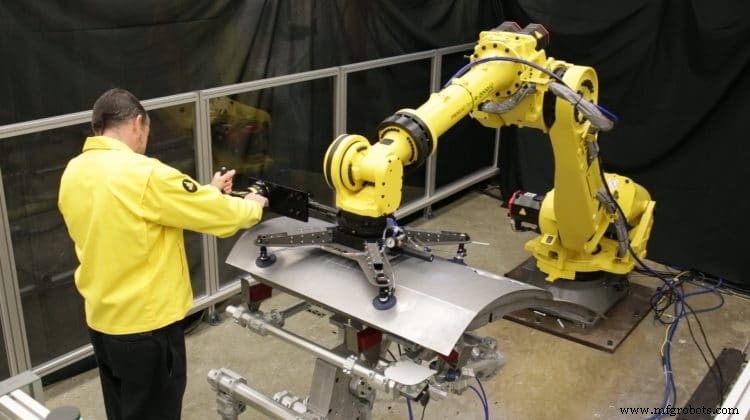
Une fois que les fabricants ont identifié ce que les robots peuvent faire pour rendre les opérations plus efficaces et les ont installés dans leur usine, ces fabricants peuvent profiter d'un logiciel plus intuitif et convivial pour les programmer.
"Il y a eu un effort énorme dans notre entreprise ainsi que dans l'ensemble de l'industrie pour rendre l'utilisation et la programmation de l'automatisation plus intuitives avec des choses comme le guidage manuel, les programmes de menus, ce genre de choses", a déclaré Maxwell. "Ce que vous découvrirez, c'est que de nombreux fabricants, et FANUC en particulier, proposent des options de base, faciles à utiliser et pilotées par menus. Notre iHMI vous expliquera comment générer des programmes. C'est graphique, et vraiment très simple."
Une fois le robot programmé et fonctionnel, les entreprises de robotique ont facilité la migration de la programmation de base vers des tâches plus compliquées pour intégrer les fonctionnalités accrues du robot, en fonction de la tâche à accomplir, a déclaré Maxwell.
Les fabricants de robots comme FANUC et ABB ont également ajouté un guidage manuel pour la programmation. Pour une opération de prise et de placement, l'opérateur enseigne au robot une position en saisissant une poignée et en faisant glisser l'outillage d'extrémité de bras (EOAT) jusqu'à l'endroit où se trouve une pièce, puis en faisant glisser l'EOAT vers une position dégagée, puis en le faisant glisser vers une boîte. L'ancienne façon d'enseigner la même tâche consistait à utiliser le pendentif d'apprentissage du robot et à appuyer sur divers boutons pour les axes X, Y et Z pour mettre le robot en position.
"Maintenant, vous êtes prêt à courir", a déclaré Maxwell. « Au cours de ces trois ou quatre étapes, vous avez appris au robot quoi faire. C'est donc beaucoup plus intuitif et beaucoup plus facile à utiliser."
YuMi d'ABB, un robot à double bras entièrement intégré avec vision, préhension par le vide, deux types de préhension mécanique et contrôle de la force, peut également être programmé avec un guidage manuel. "C'est comme apprendre à votre enfant à faire du vélo", a déclaré Morgan.
Les applications courantes de YuMi sont la manutention, l'assemblage, l'emballage et la production alimentaire. "Lorsque vous sortez un YuMi de la boîte, il est prêt à partir", a déclaré Morgan. "Il a deux bras, donc l'un peut être un appareil pour tenir une pièce et l'autre peut être une main de travail. Vous n'avez pas besoin d'un convoyeur, vous n'avez pas besoin d'une palette, vous n'avez pas besoin d'un appareil."
Pas de véritables situations d'extinction ?

L'utilisation de la fabrication sans éclairage a été entravée par des problèmes de manutention des pièces et de logistique, mais la planification détaillée, l'Internet industriel des objets (IIoT) et les fonctionnalités encore en développement, telles que l'intelligence artificielle (IA), promettent de les surmonter. Là encore, l'extinction complète des feux n'est peut-être pas la solution, a déclaré un fabricant.
Pour tous ceux qui ont un type d'automatisation, l'objectif est d'éteindre les lumières, a déclaré LeGrand. Dans les cellules de travail de son entreprise, l'idée est de garder le laser allumé autant que possible.
"Tout le monde s'y dirige", a-t-il déclaré. "Auparavant, avec les systèmes d'automatisation et, plus important encore, les techniques de programmation et les configurations des machines, ils n'étaient pas tout à fait configurés pour une véritable extinction des feux. Il y avait beaucoup de pannes de pièces et de choses qui empêcheraient la machine de fonctionner. Nous avons tous appris de nos erreurs."
LeGrand a déclaré que les lumières éteintes peuvent nécessiter des compromis, surtout si les opérateurs font une nidification dynamique où chaque nid est unique. Ceci est courant, en particulier dans les magasins sous contrat.
"Et dans de nombreux ateliers de travail, les situations qu'ils croient être éteintes ne s'appliquent pas à eux", a-t-il déclaré. "Ils peuvent le faire, cependant, ils doivent juste aborder l'imbrication, la programmation, tout un peu différemment. Ils doivent utiliser un ensemble de paramètres différent pour couper. »
Ce n'est peut-être pas le moyen le plus rapide de couper, mais lent et régulier gagne la course dans les lumières éteintes, a déclaré LeGrand.
« Il doit se déplacer régulièrement sans s'arrêter. Alors peut-être que l'espacement des pièces devient un peu plus grand, peut-être que le tapotement pour empêcher les pièces de basculer devient un peu plus agressif. »
En conséquence, ses clients peuvent se retrouver avec deux programmes différents pour les machines de MC Machinery ; un pour les feux éteints et un pour les opérations habitées.
Maxwell de FANUC a convenu que l'extinction des feux est l'avenir et reste un objectif pour plusieurs de ses clients. "Nous avons connu un succès relativement bon pour courir de très longues périodes de temps", a-t-il déclaré. «Peut-être un quart de travail, peut-être un quart de travail et demi, mais tout au long du processus de fabrication, il y a encore des domaines où ils doivent intervenir et faire certaines choses. Là où cela a réussi, c'est généralement le troisième quart de travail, le deuxième à le troisième quart de travail. »
En effet, les opérations d'extinction ne dépendent pas uniquement de l'automatisation, mais également d'autres machines et processus, tels que la manutention. La logistique est importante, dit-il, et si elle n'est pas bien planifiée, des pénuries de matériel peuvent survenir.
Le conseil de Maxwell à toute personne désireuse d'effectuer des opérations sans pilote est d'analyser d'abord leurs opérations et de les décomposer en étapes discrètes. Ensuite, considérez ce qui pourrait mal tourner à chaque étape et déterminez comment ce problème pourrait être résolu sans opérateur.
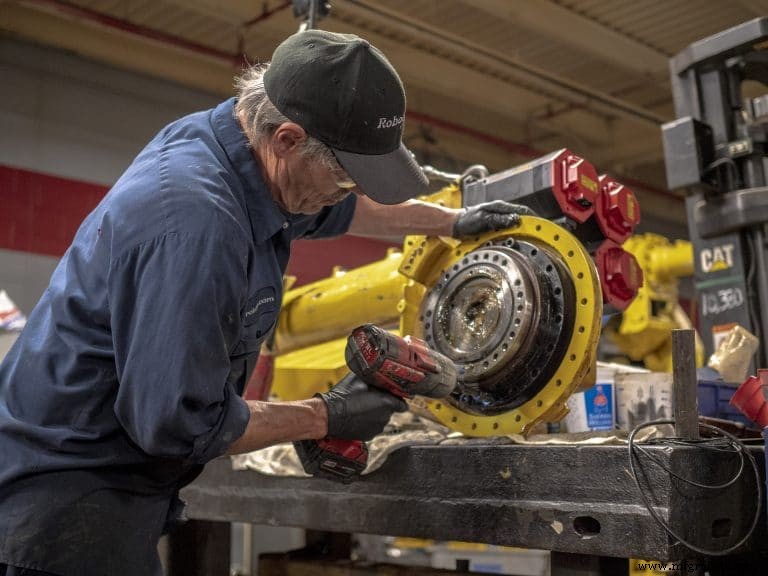
Avoir des travailleurs sous la main sera toujours nécessaire, a déclaré Fischer de RobotWorx. "Lights out est une sorte d'appellation impropre pour la production", a-t-il déclaré. "Il n'y a vraiment pas de véritable situation de production sans lumière. Vous avez toujours un certain soutien. Mais les entreprises vont squelettiquer l'automatisation des équipages. »
À ce stade, il est encore nécessaire de garder les personnes essentielles pour soutenir la ligne, a-t-il déclaré; pas nécessairement des opérateurs, mais des techniciens de maintenance et des robots pour une assistance en cas de panne ou de réparation.
"Ce qui permet la tendance aux opérations sans éclairage, c'est l'utilisation de robots pour l'entretien des machines et la manutention des matériaux", a déclaré Fischer. "L'avenir, c'est l'IA et l'IIoT."
L'IIoT permet d'envoyer des alertes à un emplacement distant pour qu'un travailleur surveille et intervienne en cas de problème en planifiant la maintenance et lui permettrait de suivre les chiffres de production. L'IA est plus prédictive et permet à un robot d'initier et de faire des ajustements par lui-même.
L'IA robotique est en cours de développement et n'est encore disponible dans aucun robot, a déclaré Fischer. "Tous les équipementiers y travaillent en tant que projets de R&D, mais rien n'existe encore", a-t-il déclaré. "Peut-être que nous le verrons dans les cinq à 10 prochaines années."
La qualité des pièces est un autre gros problème qui empêche les vraies lumières de s'éteindre, a déclaré Fischer.
"Si vous effectuez un processus d'assemblage, un processus de soudage, à moins que la qualité de vos pièces ne soit parfaite, vous rencontrez des problèmes que seule une personne peut identifier du point de vue de la qualité ou du point de vue de la réparation et de la maintenance", a-t-il déclaré. Les constructeurs automobiles doivent procéder à une inspection visuelle des soudures de sécurité pour s'assurer que les soudures sont correctement situées et sans défaut. Une caméra est trop limitée pour faire l'inspection, a-t-il ajouté.
Morgan d'ABB a détourné son attention des lumières éteintes vers l'Industrie 4.0. "Vous savez, nous sommes dans le secteur des robots depuis des décennies maintenant, et je dirais que le terme" production sans éclairage "était presque considéré comme le Saint Graal de la fabrication automatisée", a-t-il déclaré. "Les gens ont pensé qu'une fois que vous avez mis votre processus et votre entreprise à ce niveau, vous êtes arrivé."
Alors que d'autres se concentrent sur les lumières éteintes, ABB a plutôt jeté son dévolu sur l'usine du futur et l'industrie 4.0, avec une usine de fabrication flexible et agile qui peut fonctionner dans des environnements à faible mix, à haut volume ainsi qu'à high-mix, low- travail en volume.
"Si vous regardez les produits traditionnels à haut volume comme les téléphones portables, regardez simplement combien de couleurs et de configurations de mémoire vous pouvez acheter, par exemple, un téléphone Samsung Android aujourd'hui", a déclaré Morgan. "C'est ce que nous constatons aujourd'hui dans le secteur manufacturier."
Tout nouveau est l'écosystème intégré où toute la configuration de l'automatisation est intégrée aux besoins des clients, comme une livraison rapide. Par exemple, a déclaré Morgan, un fabricant de lentilles de contact peut produire des milliards de lentilles de contact souples, mais il dispose désormais d'une opération de traitement électronique dans l'usine avec des sociétés de livraison et de logistique intégrées comme FedEx sur site.
"Nous voyons vraiment une grande concentration sur tout ce pour quoi vous dépensez votre argent en tant que fabricant, il doit être fiable et disponible avec un énorme accent sur l'efficacité globale de l'équipement", a déclaré Morgan. «Le nombre OEE de classe mondiale avant de 80 à 85% est maintenant une barre très basse et pour être de classe mondiale aujourd'hui, ils commencent avec 90%. C'est une question d'efficacité à tous les niveaux. Cela signifie un robot collaboratif travaillant aux côtés d'un opérateur dans un environnement de fabrication, et tout est connecté numériquement."
Système de contrôle d'automatisation
- Tendances de fabrication :robotique, qualité et efficacité
- La robotique et l'avenir de la production et du travail
- La robotique de fabrication peut-elle augmenter la sécurité des employés ?
- Comment les robots ont-ils changé la fabrication ?
- Opinion :Une accélération de la robotique et de l'automatisation induite par le coronavirus se produit en Chine
- AV&R et APN s'associent pour développer la robotique pour la fabrication aéronautique
- Robots dans la fabrication :conseils et prédictions des panélistes
- Yaskawa Motoman, RAMTEC entre dans un partenariat éducatif
- L'histoire de la robotique dans la fabrication