Entretien d'experts :Josh Martin, PDG de Fortify, sur sa technologie de fabrication de composites numériques
[Crédit image :Fortifier]
Fortify est une startup basée à Boston qui a développé une nouvelle approche de l'impression 3D composite. Cette approche combine l'alignement magnétique des composites avec la technologie de traitement numérique de la lumière (DLP), permettant aux utilisateurs de produire des pièces composites de haute qualité qui seraient autrement impossibles à fabriquer.
La technologie, appelée Fluxprin t™ , alimente la plate-forme de fabrication de composites numériques (DCM) de Fortify. La plateforme vise tout d'abord à permettre aux entreprises de produire des outils durables tels que des moules d'injection et des pièces de production d'utilisation finale.
Dans l'interview d'aujourd'hui, nous sommes rejoints par le PDG de Fortify, le Dr Joshua Martin, pour en savoir plus sur la technologie passionnante de Fortify et discuter de ce qui stimule la croissance de l'impression 3D composite.
Pourriez-vous me parler un peu de Fortify ?
Fortify est une société de fabrication additive basée à Boston qui commercialise la plate-forme de nouvelle génération pour l'impression composite.
Chez Fortify, nous nous concentrons sur la combinaison des performances que vous obtenez des matériaux renforcés de fibres avec la résolution que vous auriez traditionnellement attendez des technologies photopolymères telles que SLA et DLP.
Nous avons fondé l'entreprise parce que nous en avions marre d'avoir à choisir entre forme et fonction. Traditionnellement, il y a eu un compromis entre avoir un prototype qui ressemble à la vraie chose mais qui est généralement médiocre en termes de performances, ou avoir une pièce qui est un prototype fonctionnel mais qui est très éloigné de l'ajustement et de la finition d'une production -matériau prêt.
Chez Fortify, nous pensons que la chimie des polymères à elle seule ne peut atteindre qu'une petite partie de l'espace de propriété requis par les applications d'ingénierie. Dans les photopolymères, de nombreux matériaux de base n'ont pas vraiment changé au cours des dernières décennies. Au cours des 25 à 30 dernières années, cela a été à peu près basé sur les mêmes types de chimie, bien que les choses se soient accélérées au cours des cinq dernières années environ.
Fortify apporte une technologie qui nous permet de remplir les chimies à haute résolution avec des additifs de renforcement, avec l'avantage critique de pouvoir contrôler l'alignement des particules de renforcement.
Si vous examinez toutes les technologies d'impression 3D existantes, les plates-formes basées sur SLA/DLP sont les plus avancées en termes de finition de surface et de précision des pièces lorsqu'elles sortent de l'imprimante.
Nous avons développé une technique qui nous permet d'orienter magnétiquement des fibres au sein d'un milieu fluide. Les pièces que nous imprimons sont essentiellement les composites de la plus haute résolution produits à ce jour. Par rapport à d'autres formes de composites additifs, vous comptez généralement sur les forces de cisaillement pour aligner les particules afin d'optimiser la résistance. Cependant, le cisaillement n'est pas toujours la force dirigée la plus facile à contrôler.
Avec l'assemblage magnétique, nous sommes en mesure de contrôler plusieurs propriétés telles que la résistance, la rigidité, la conductivité thermique en trois dimensions dans chaque voxel.
Est-ce que cela comprend votre plate-forme de fabrication de composites numériques (DCM) ?
Oui. La plate-forme DCM est tout ce qui nous permet de régler l'architecture de la fibre pour l'optimiser en termes de performances. Cela couvre le matériel, les logiciels et les matériaux.
La technologie d'alignement magnétique spécifique est appelée Fluxprint ™ , qui concerne davantage l'application de champs magnétiques à la zone de construction pour orienter un matériau magnétiquement sensible.
Quelles industries et applications conviendraient le mieux à votre technologie ?
Nous avons une stratégie de déploiement qui nous permet de capitaliser d'abord sur l'espace d'outillage, car nous travaillons sur certains besoins de benchmarking pour la production de pièces d'usage final
En ce qui concerne l'outillage, notre avantage concurrentiel est que nous pouvons fournir le même niveau de résolution que vous attendez d'une technologie photopolymère, avec la capacité de résister à des températures proches de 300°C, tout en maintenant la meilleure résistance et rigidité de sa catégorie.
Nous sommes très bien placés pour perturber le marché du moulage par injection, où les investissements en outillage sont importants et la fabrication d'outillage prend beaucoup de temps. Le marché du moulage par injection a été amorcé au cours de la dernière décennie par d'autres solutions qui n'ont pas tout à fait résolu le problème de résolution des performances. Nous pouvons imprimer en une heure, alors que cela peut prendre 10 semaines pour s'approvisionner de manière conventionnelle avec ce même outil.
Nous avançons fortement sur le marché car nos outils sont capables de gérer beaucoup plus de coups et de cycles que les solutions concurrentes. Nous serons bientôt en mesure de démontrer comment ils peuvent gérer la fabrication à faible volume pour des applications à haute valeur ajoutée.
Cela dit, nous avons plusieurs projets actifs qui ouvriront la production de pièces d'utilisation finale à l'aide de la plate-forme DCM . Notre technologie nous permet d'augmenter les propriétés physiques au-delà de la résistance et de la rigidité, par exemple en permettant des pièces hautes performances avec des certifications telles que FST (inflammabilité, fumée et toxicité).
Nous pensons que l'avenir de l'adoption dans le domaine des additifs repose sur l'ouverture de la palette des matériaux pour couvrir les applications actuellement adressables par la suite standard de polymères. Le coût et le débit sont bien sûr nécessaires, et il n'y a pas de meilleur exemple de réussite que les technologies à base de photopolymère.
Que pensez-vous de l'état actuel de l'impression 3D composite et comment évolue la technologie ?
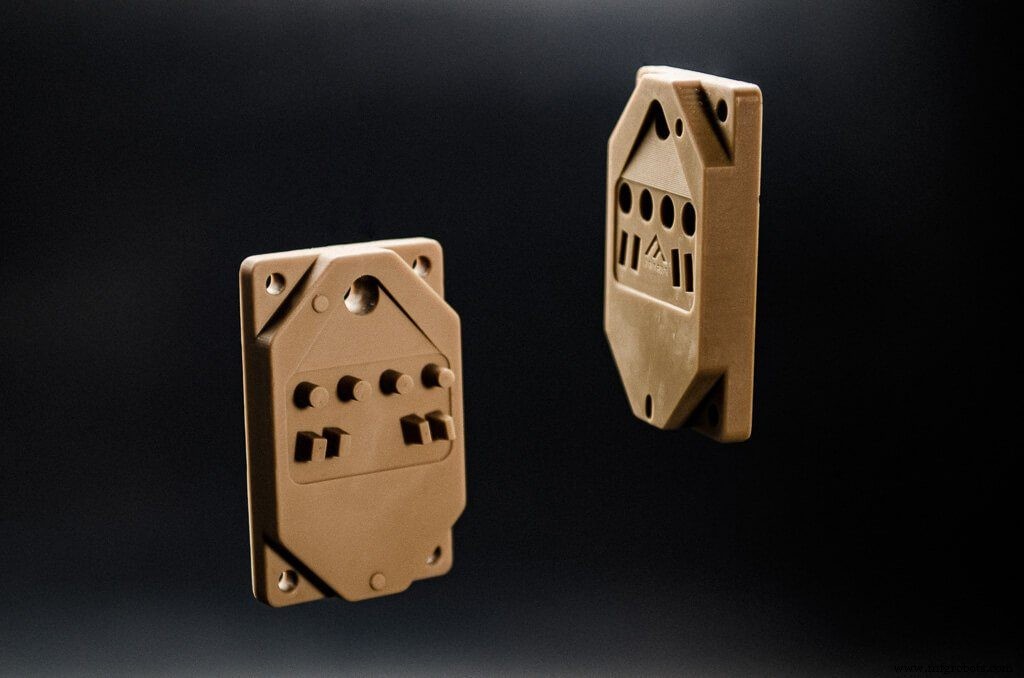
Ce qui est intéressant, c'est que si vous regardez l'industrie de l'impression 3D au cours des 10 dernières années et les domaines dans lesquels les entreprises investissent, c'est très asymétrique.
Ce que je veux dire par là, c'est qu'il y a littéralement des milliards de dollars qui vont aux entreprises d'impression 3D polymères et aux entreprises d'impression 3D métal. Tout récemment, Carbon a annoncé avoir reçu plus de 260 millions de dollars supplémentaires de financement. Cette seule entreprise a levé plus de 600 millions de dollars en environ six ans.
Dans l'espace composite, il y a peut-être cinq entreprises qui exercent vraiment la technologie et produisent des pièces dans ce segment, telles que Markforged, Arevo, Continuous Composites et Impossible Objects. Mais Carbon à lui seul, qui est peut-être l'une des 150 entreprises du secteur de l'impression 3D polymère, a levé plus d'argent que toutes les entreprises d'impression 3D composites réunies.
Lorsque vous regardez comment cela se passe, vous ont beaucoup plus d'argent pour l'impression 3D polymère et l'impression 3D métal par rapport aux composites. Mais quand vous regardez les opportunités de marché entre les plastiques, les métaux et les composites, elles sont très similaires. Ils sont tous supérieurs à 300 milliards de dollars dans le monde.
Vous avez un énorme marché des polymères, où vous avez un déplacement du moulage par injection, par exemple, et vous avez un énorme marché des métaux où vous avez un déplacement de métaux coupés, métaux coulés et moulage par injection de métal pour certaines applications.
Ensuite, vous avez cet énorme marché des composites, qui comprend le drapage à la main, le moulage par injection, les plastiques chargés de fibres, etc.
Ils sont tous énormes. Mais l'investissement du côté de l'impression 3D va en grande partie aux technologies plus anciennes comme l'extrusion de thermoplastiques et les procédés à base de lumière.
Cela dit, l'espace composite est peut-être le segment le plus récent de l'impression 3D. Il y a des défis qui vont avec, mais il y a aussi beaucoup d'opportunités.
La façon dont nous le voyons est que la plupart des entreprises de l'industrie des composites se sont jusqu'à présent concentrées sur des techniques basées sur l'extrusion comme le FDM. Le problème est que cela ne résout pas vraiment certains des défauts majeurs du FDM en premier lieu, qui seraient une mauvaise finition de surface et une anisotropie - où vous avez un matériau qui est 10 fois plus résistant dans une direction que dans une autre.
Il va y avoir de très bonnes applications pour cela, mais je pense que dans l'espace composite, à la recherche de moyens d'atteindre de meilleurs niveaux d'isotropie, de prévisibilité, de meilleurs niveaux de contrôle et de performances qui ne sont pas simplement dictés en maximisant la force dans quelques directions, va être la clé.
Notre mission chez Fortify est de permettre l'impression 3D à grande échelle, avec des matériaux qui doivent généralement être découpés ou fabriqués à l'aide de moyens traditionnels.
Il existe, par exemple, de nombreux matériaux qui sont traditionnellement soit assemblés à la main, soit sourcés dans un énorme bloc très coûteux, puis usinés pour obtenir la pièce. Nous intégrons à notre plate-forme ces types de matériaux afin que vous puissiez les imprimer directement en 3D.
Pourquoi a-t-il fallu autant de temps à l'industrie pour reconnaître les composites comme une excellente opportunité pour l'impression 3D ?
C'est une très bonne question. Je pense que cela est dû en grande partie à la maturité du marché d'achat. En d'autres termes, de 2000 à 2014, l'industrie était dans un état où il y avait beaucoup moins de fruits à saisir.
Lorsque Formlabs a introduit la Form1, c'était le premier vrai 3D de bureau haute résolution. imprimante à ce prix. C'est ce que leur image de marque a réussi à capturer. Maintenant, il y a 10 à 100 entreprises qui essaient de faire la même chose.
Si vous regardez Markforged, ils ont sorti la première imprimante 3D composite en 2014. D'autre part, FDM existe depuis des décennies et SLA existe depuis que Chuck Hull l'a inventé dans les années 80.
L'industrie n'était pas forcément prête à adopter les composites car elle est encore en train d'apprendre à adopter l'impression 3D en général. Il existe de nombreux obstacles en termes de conception et d'analyse comparative, qui prennent un certain temps à résoudre.
Il y a une raison pour laquelle les composites n'ont traditionnellement été utilisés que sur des applications très performantes et très coûteuses. tels que les composants aérospatiaux ou les équipements récréatifs haut de gamme tels que les pièces automobiles et les vélos.
Si vous regardez le cycle de battage médiatique de Gartner, nous sommes maintenant à un point où les applications dans l'espace industriel commencent vraiment à prendre pied.
L'approche générale était d'essayer d'obtenir l'impression 3D partout. Maintenant, cette perspective a changé pour se concentrer beaucoup plus sur la spécialisation. L'industrie dans son ensemble se spécialise pour s'assurer que la portée de la technologie correspond vraiment aux besoins d'applications spécifiques. Il y a plus d'efforts concentrés sur la résolution de problèmes très spécifiques, et c'est là que les composites sont vraiment bénéfiques.
En pensant à l'industrie de la FA de manière plus générale, comment la voyez-vous évoluer au cours des cinq prochaines années ?

Si vous participez au circuit annuel des conférences de l'industrie, vous pouvez généralement déterminer dans quelle direction toutes les entreprises cherchent vraiment à orienter l'industrie.
Il y a cinq ans, nous avons vraiment commencé à entendre des rumeurs sur l'impression industrielle. L'objectif n'était plus d'amener les technologies d'impression 3D jusqu'au consommateur, mais de les amener dans des environnements industriels haut de gamme, où nous pouvons faire une fabrication « lumières éteintes ».
Des entreprises comme Carbon ont fait de grands progrès pour y parvenir, même s'il reste encore beaucoup de chemin à parcourir. Je pense que l'un des fils conducteurs sur lesquels nous allons nous concentrer au cours des cinq prochaines années vient des innovations matérielles, logicielles et matérielles.
Pour être précis, si vous regardez ce que l'industrie pharmaceutique a fait avec la généalogie par lots, cela commence à être mis en œuvre grâce à l'apprentissage automatique.
L'idée est de savoir comment suivre le fil numérique depuis le numéro de lot de vos matières premières jusqu'au post-test et à la validation, en passant par tous les processus subis par le matériau pendant l'impression. C'est quelque chose que l'impression 3D doit prendre plus au sérieux car elle est assez bien définie dans l'espace de fabrication traditionnel.
Une autre façon de dire cela est qu'au cours des cinq prochaines années, les entreprises devront se concentrer sur la démonstration de niveaux élevés de répétabilité et de fiabilité.
La raison pour laquelle il est réconfortant d'utiliser différents types de matériaux conventionnels est que si vous vous procurez de l'acier laminé à froid, vous savez à quoi vous attendre en termes de propriétés et de performances et comment travailler avec.
Le problème avec l'impression 3D en ce moment est qu'il y a encore une grande plage de variabilité. Par exemple, si vous achetez deux des mêmes imprimantes et que vous imprimez pendant deux semaines d'affilée sur les deux, vous ne faites que rassembler des échantillons à tester.
Lorsque vous testez tous ces spécimens, vous vous retrouvez avec un gros nuage de données qui, dans certains cas, est partout. La question est donc de savoir comment un ingénieur est censé exercer un niveau de prévisibilité, en particulier s'il doit utiliser la technologie à grande échelle.
Ainsi, une partie du processus d'apprentissage automatique consiste à introduire un niveau élevé de répétabilité et permettent à l'utilisateur de prévoir plus facilement comment les performances vont fonctionner.
Quels sont les défis que l'industrie devra surmonter ?
À l'heure actuelle, de nombreux obstacles empêchent l'impression 3D d'atteindre l'objectif de l'Industrie 4.0. Nous parlons de fabrication distribuée, par exemple, un débit plus élevé, une répétabilité élevée et un coût unitaire inférieur.
Pour atteindre ces objectifs, l'industrie doit traiter les machines moins comme des imprimantes 3D et plus comme des imprimantes 3D. unités de fabrication et mettre en place de nombreux freins et contrepoids qu'un système de fabrication traditionnel aurait.
Si vous allez à l'International Manufacturing Technology Show (IMTS), c'est une leçon d'humilité car il y en a environ 140 000 participants, et environ 90 % d'entre eux sont issus de la fabrication traditionnelle. L'impression 3D n'est qu'une goutte d'eau dans l'océan.
Vous avez une idée de la maturité de bon nombre de ces systèmes traditionnels. Nous y arrivons dans le sens où les machines AM commencent maintenant à ressembler et à avoir le même niveau d'entrées et de sorties qu'un système de fabrication traditionnel comme une CNC aurait.
Combien de temps faudra-t-il à l'industrie pour devenir plus qu'un simple pourcentage du marché manufacturier global ? Ou pensez-vous que la technologie devrait être vue dans sa propre voie, pour ainsi dire ?
Je pense que comparer la taille de l'industrie de la fabrication additive avec l'ensemble du marché de la fabrication n'est pas la meilleure façon de l'examiner, car l'industrie n'existe pas uniquement pour remplacer le moulage par injection ou la CNC. Ce serait dommage que le but soit simplement cela.
L'accent doit être mis sur les nouveaux types d'applications et les nouveaux types d'avantages qui ne peuvent être obtenus qu'avec des additifs.
C'est une grande partie de ce que nous attendons avec impatience chez Fortify :la possibilité d'utiliser une variété de technologies de FA pour créer une pièce très solide, dotée d'une géométrie unique et d'un niveau élevé de conductivité thermique. Cela créera de nouveaux marchés.
Mais je pense qu'il faudra un certain temps avant d'atteindre complètement cet objectif, même si, bien sûr, ce n'est pas un jeu à somme nulle.
Cette année, Fortify a annoncé un tour de table de 2,5 millions de dollars. Pourriez-vous nous parler un peu de ce que cet investissement signifie pour Fortify à l'avenir ?
Le cycle de financement que nous avons annoncé en janvier était un récapitulatif des financements déjà clôturés. L'objectif est essentiellement de préparer notre système pour les tests bêta et de le mettre entre les mains des utilisateurs avec lesquels nous travaillons en étroite collaboration maintenant. Nous venons de fermer une série A supplémentaire de 10 millions de dollars, dirigée par Accel Partners.
Nous voulons que le système soit prêt afin que nos clients, qui nous paient pour produire des pièces pour leurs besoins de fabrication actuels, peut réellement l'utiliser.
Nos deux premiers systèmes de matériaux nous ont donné de bons retours sur le flux de travail entre le logiciel matériel et les matériaux.
La prochaine étape consiste donc à saisir l'opportunité d'outillage, puis à commencer à identifier et à travailler sur la production de pièces d'utilisation finale pour d'autres systèmes d'ingénierie.
Pourriez-vous nous en dire plus sur votre collaboration avec l'entreprise chimique DSM ? Que signifie ce partenariat pour Fortify et vos clients à l'avenir ?
DSM a été le premier partenaire sur notre plate-forme de matériaux ouverte. L'idée derrière cette plateforme est que nous ne voulons pas tout posséder en matière de formulation de matériaux. Nous voulons pouvoir nous concentrer sur les additifs, les systèmes matériels et le contrôle logiciel pour permettre aux clients d'avoir plus d'un choix en ce qui concerne les fournisseurs.
Quand il s'agit d'entreprises comme BASF, DSM, Mitsubishi et Henkel ont chacun leurs avantages et leurs applications uniques dans le domaine de la fabrication additive. Et nous aimerions travailler avec eux d'une manière qui nous permette de créer plus de valeur que si nous devions simplement contrôler l'ensemble de la chaîne d'approvisionnement.
Avec DSM en particulier, nous cherchons des moyens de prendre certains de leurs systèmes qui ont des applications dans l'espace sous le capot. Ils ont une ténacité raisonnable, ils peuvent maintenir la résistance et la rigidité à peut-être 100°C.
En superposant, la plate-forme technologique Fortify peut atteindre des niveaux beaucoup plus élevés de résistance, de rigidité, de résistance au fluage et il peut fonctionner à des températures plus élevées. Cela permettrait à nos partenaires matériels de fournir des solutions à leur clientèle existante qui n'obtient pas nécessairement tout ce qu'ils veulent de la technologie.
Pour Fortify, c'est formidable car DSM est l'un des premiers photopolymères producteurs dans le monde. Nous sommes ravis de travailler avec eux. C'est un groupe formidable et ensemble, nous pouvons aller assez loin avec nos technologies.
Vous avez évoqué le modèle des matériaux ouverts. Pensez-vous que c'est l'avenir des matériaux d'impression 3D ?
Si vous regardez l'industrie informatique dans les années 80, elle était intégrée verticalement. Par exemple, IBM fabriquerait des mémoires et des processeurs et devrait également créer des logiciels et des périphériques.
Ensuite, l'industrie a changé. Maintenant, si vous regardez où il en est aujourd'hui, il existe des sociétés spécialisées dans chacun de ces segments :logiciels, processeurs, puces mémoire, etc. Le marché a été décloisonné.
À certains égards, l'industrie de l'impression 3D suit cette trajectoire, où des entreprises traditionnelles comme Stratasys et 3D Systems construisent le matériel, développent le logiciel et produisent leurs propres matériaux, ce qui signifie que vous ne pouvez acheter que dans cette chaîne d'approvisionnement.
Cependant, de nombreux clients souhaitent avoir plus d'options. Ils veulent pouvoir choisir les matériaux qu'ils utilisent et savoir qu'il existe une autre option.
Le modèle des matériaux ouverts va prendre du temps pour être standardisé dans l'ensemble de l'industrie.
Que réservent les 12 prochains mois à Fortify ?
Nous faisons évoluer l'équipe pour nous assurer que nous pouvons atteindre nos objectifs de produits. Nous embauchons rapidement et nous souhaitons développer davantage l'équipe pour pouvoir mettre en place nos programmes bêta, entre le début et la mi-2020.
Ensuite, nous pourrons passer à l'échelle en termes de passage de cette plate-forme à la disponibilité générale.
Nous pensons que nous sommes en mesure de fournir la technologie en 2021. Nous chercherons très probablement un peu plus de capital fin 2021 pour faire fabriquer un système fin 2021, début 2022.
Il y a beaucoup de travail vraiment passionnant devant nous . Nous sommes déjà en contact étroit avec les clients.
Si les gens sont intéressés à s'impliquer dès le début, ils ont la capacité de le faire. Mais nous avons du pain sur la planche pour mettre les systèmes entre les mains des personnes avec qui nous travaillons actuellement.
Pour en savoir plus sur Fortify, visitez : https://3dfortify.com
impression en 3D
- Entretien avec un expert :Dr Bastian Rapp de NeptunLab
- Entretien d'experts :Felix Ewald, PDG de DyeMansion
- Entretien d'experts :Duncan McCallum, PDG de Digital Alloys, sur l'impression Joule et l'avenir de l'impression 3D sur métal
- Entretien d'experts :James Hinebaugh d'Expanse Microtechnologies
- Entretien d'experts :Guillaume de Calan, PDG de Nanoe, sur l'avenir de l'impression 3D céramique
- Entretien d'experts :PDG de PostProcess Technologies sur la résolution du goulot d'étranglement du post-traitement pour la fabrication additive
- Tirer parti de la technologie numérique dans la fabrication
- Profil de l'entreprise :Expert manufacturier et technologique SourceDay
- L'essor des plateformes numériques dans le secteur manufacturier