Salon du Bourget 2019 :Faits saillants
Exposition statique de l'avion de transport militaire Airbus A400M à forte intensité de composites au salon du Bourget 2019. Origine | CW
Les attentes étaient mitigées à l'approche du salon du Bourget 2019 (17-23 juin). On espérait que Boeing jetterait les bases du New Midsize Aircraft (NMA), mais la crise du 737 MAX a consommé une grande partie de l'énergie et de l'attention de l'entreprise. En effet, le premier jour du salon aérien, Boeing a fait une annonce très générale concernant les conditions commerciales et a publié ses prévisions d'avions commerciaux sur 20 ans. Rien sur NMA. Le plus gros événement de Boeing pendant le salon a été l'annonce de la vente de 200 avions 737 MAX à International Airline Group (IAG).
Airbus, de son côté, a annoncé l'A321XLR (LR =long range), la dernière itération de l'A320neo. Prévu pour entrer en service en 2023, l'A321XLR aura une autonomie de 4 700 milles nautiques, réalisable grâce à une capacité de stockage de carburant supplémentaire. Airbus a déclaré que la gamme de l'avion offrira aux compagnies aériennes des options de monocouloir moins chères sur des itinéraires désormais desservis principalement par des avions à double couloir plus chers. Ces itinéraires incluent New York-Rio, Shanghai-Sydney et Madrid-Dubaï.
Malgré le manque de nouvelles NMA, parmi les sociétés liées aux composites exposant au Salon du Bourget, il reste un effort définitif pour développer et aligner les matériaux et la technologie des procédés pour répondre à toutes les demandes que Boeing et Airbus placent sur la chaîne d'approvisionnement au cours de la prochaine décennie. Cela comprend les préimprégnés thermodurcissables traditionnels avec durcissement en autoclave, l'infusion de résine liquide de fibres sèches avec durcissement hors autoclave, les composites thermoplastiques et la fabrication additive. Le sentiment d'attente tout au long de la chaîne d'approvisionnement est palpable.
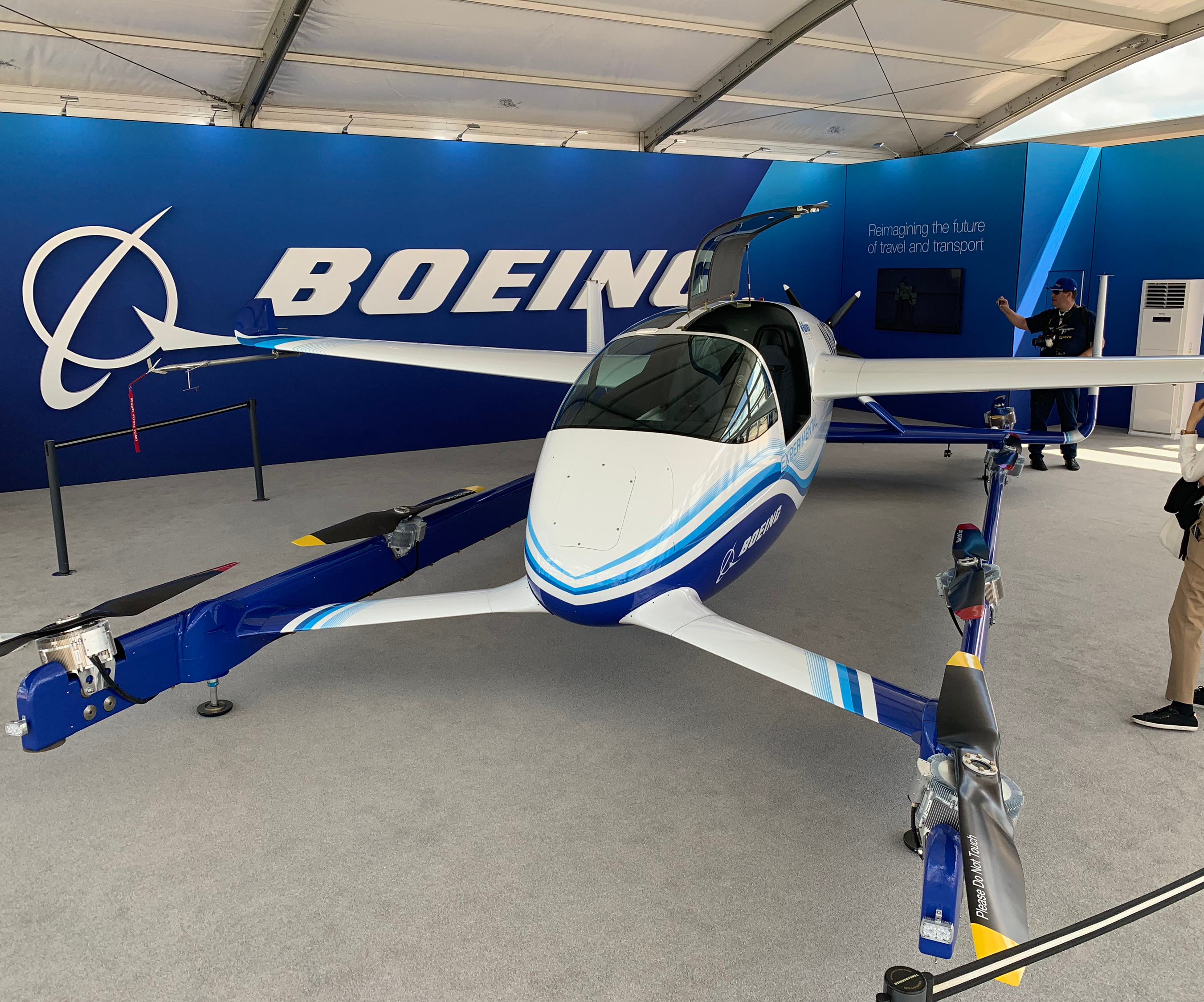
Sur la ligne de vol, il y avait la panoplie habituelle d'avions commerciaux, militaires et civils, avec des démonstrations de vol quotidiennes. Des démonstrations d'avions à propulsion électrique étaient remarquables dans les airs, qui contrastaient fortement et silencieusement avec le rugissement assourdissant associé aux avions de chasse et commerciaux. Dans les expositions statiques, il y avait un certain nombre d'engins EVTOL (décollage et atterrissage verticaux électriques) destinés au marché de la mobilité urbaine. Ce type d'avion, en particulier, s'avère une cible importante des matériaux composites, qui sont une nécessité pour le vol à propulsion électrique. Cependant, les volumes de production de certaines de ces plates-formes se compteront probablement par milliers par an, ce qui pousse les technologies des matériaux et des processus davantage vers un modèle de production de type automobile. Cela dit, les EVTOL sont encore jeunes, compte tenu notamment des obstacles réglementaires, de qualification et de gestion de l'espace aérien qui restent à surmonter.
Vous trouverez ci-dessous les faits saillants de l'émission.
Spirit AeroSystems. Le plus grand avionneur au monde, Spirit AeroSystems (Wichita, Kan. États-Unis), a commencé le spectacle tôt lundi matin avec une conférence de presse annonçant l'introduction de son panneau de fuselage ASTRA (Advanced Structures Technology and Revolutionary Architecture), conçu pour montrer comment un avion entièrement composite le fuselage pourrait être conçu pour répondre aux exigences de performance, de vitesse et de coût d'un avion monocouloir de nouvelle génération. La conception et la fabrication de ce panneau sont décrites dans une histoire autonome ici.
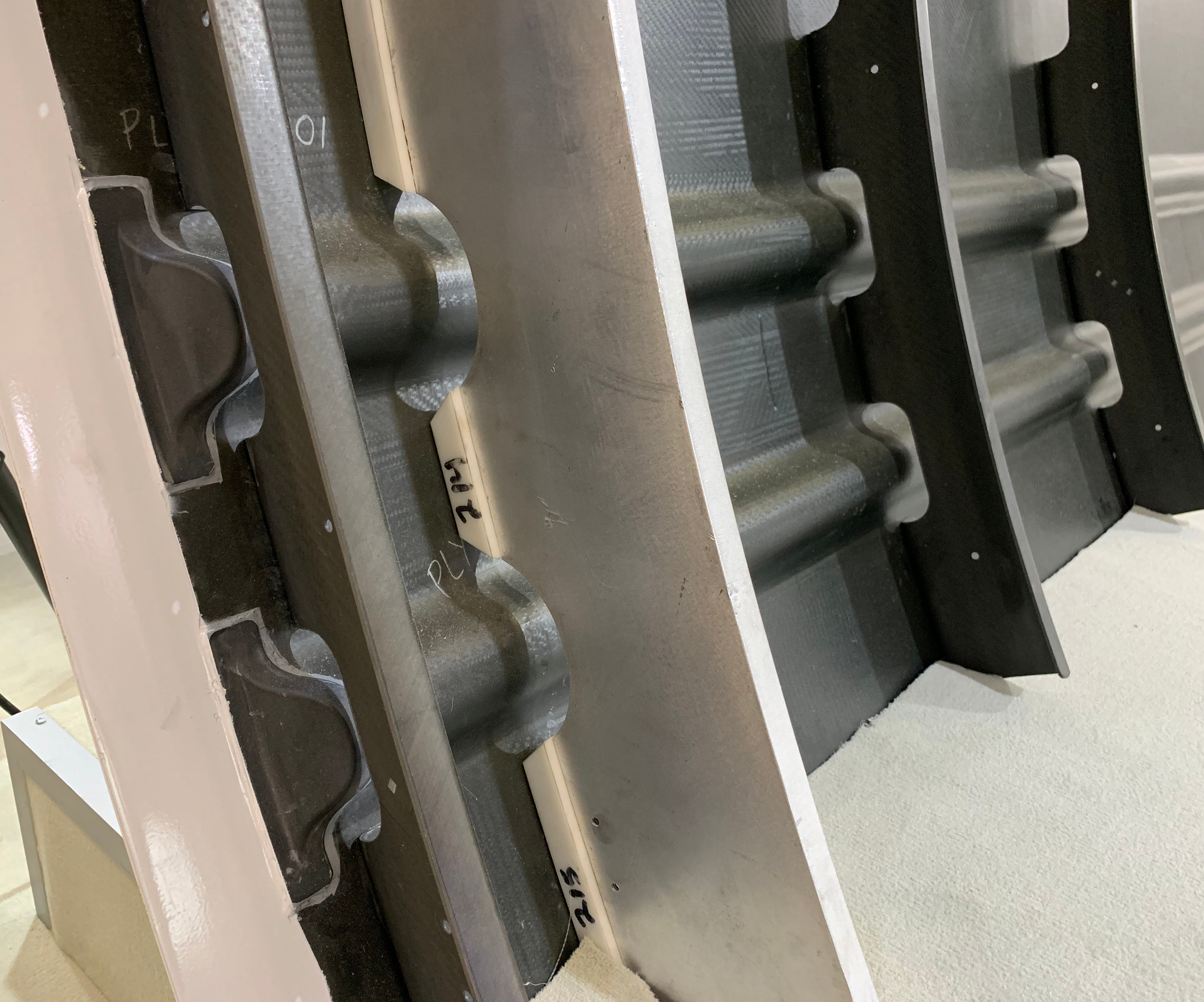
MTorres. Un autre panneau composite remarquable du salon a été trouvé sur le stand MTorres (Torres de Elorz, Navarre, Espagne). Cette «structure de grille/peau» renforcée de nervures, fabriquée par infusion de résine de fibres de carbone sèches, est en fait l'idée originale de Stephen Tsai, vétéran des composites et professeur émérite d'aéronautique et d'astronautique à l'Université de Stanford, qui était au stand MTorres pour Explique le. Tsai a déclaré qu'il avait conçu ce design il y a plusieurs années et l'avait basé sur la structure grille/peau déployée dans la fabrication du Vickers Wellington , un bombardier britannique de la Seconde Guerre mondiale fabriqué par Vickers-Armstrongs et célèbre pour maintenir l'intégrité structurelle en cas d'accident. Pour donner vie à cette conception dans une application composite, Tsai a conçu les nervures dans une structure en treillis, chaque nervure ayant une largeur et une hauteur fixes, et l'espacement entre les nervures également fixe.
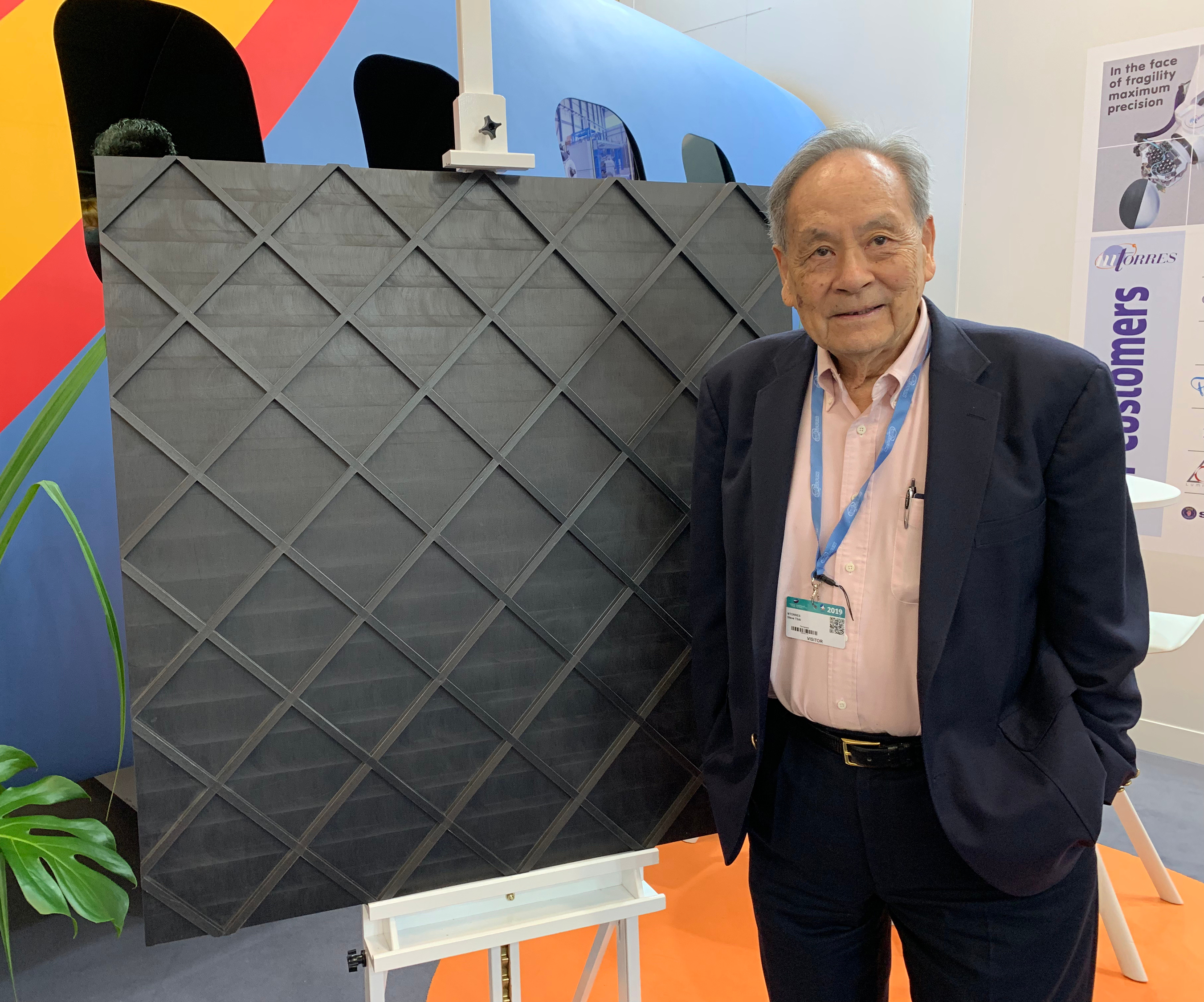
Steve Tsai se tient debout avec le panneau renforcé de nervures qu'il a conçu et MTorres l'a aidé à fabriquer. Le facteur clé est le placement précis des fibres pour construire les côtes. Origine | CW
Le défi de sa conception, a déclaré Tsai, était de développer des intersections de nervures capables de résister à de grandes charges mécaniques. Ce qu'il a proposé, c'est une architecture de nervures qui utilise des rubans en fibre de carbone placés en continu dans une direction (appelez-le A) et de manière discontinue dans la direction d'intersection (appelez-le B). Ensuite, pour la couche suivante, les bandes seraient placées de manière discontinue dans la direction A et en continu dans la direction B. Ce motif se poursuivrait jusqu'à ce que l'épaisseur souhaitée de la nervure soit atteinte. De cette façon, chaque joint de nervure serait toujours traversé par une bande continue. Une fois que les nervures sont construites dans l'outil, une peau est posée dessus via un placement automatisé de fibres (AFP) ou une pose automatisée de ruban (ATL) et l'ensemble de la structure est co-polymérisé.
Les avantages de cette conception, a déclaré Tsai, sont nombreux, mais le principal est qu'il est "difficile pour les dommages d'aller au-delà de la zone localisée", ce qui signifie qu'une fissure qui s'est propagée dans la peau ne peut pas facilement migrer au-delà des côtes qui bordent le régions touchées. Tsai a également déclaré que la structure grille/peau est très efficace en termes de poids et de matériaux. Pourtant, il a noté:"C'est facile à concevoir mais difficile à faire." C'est là qu'intervient MTorres.
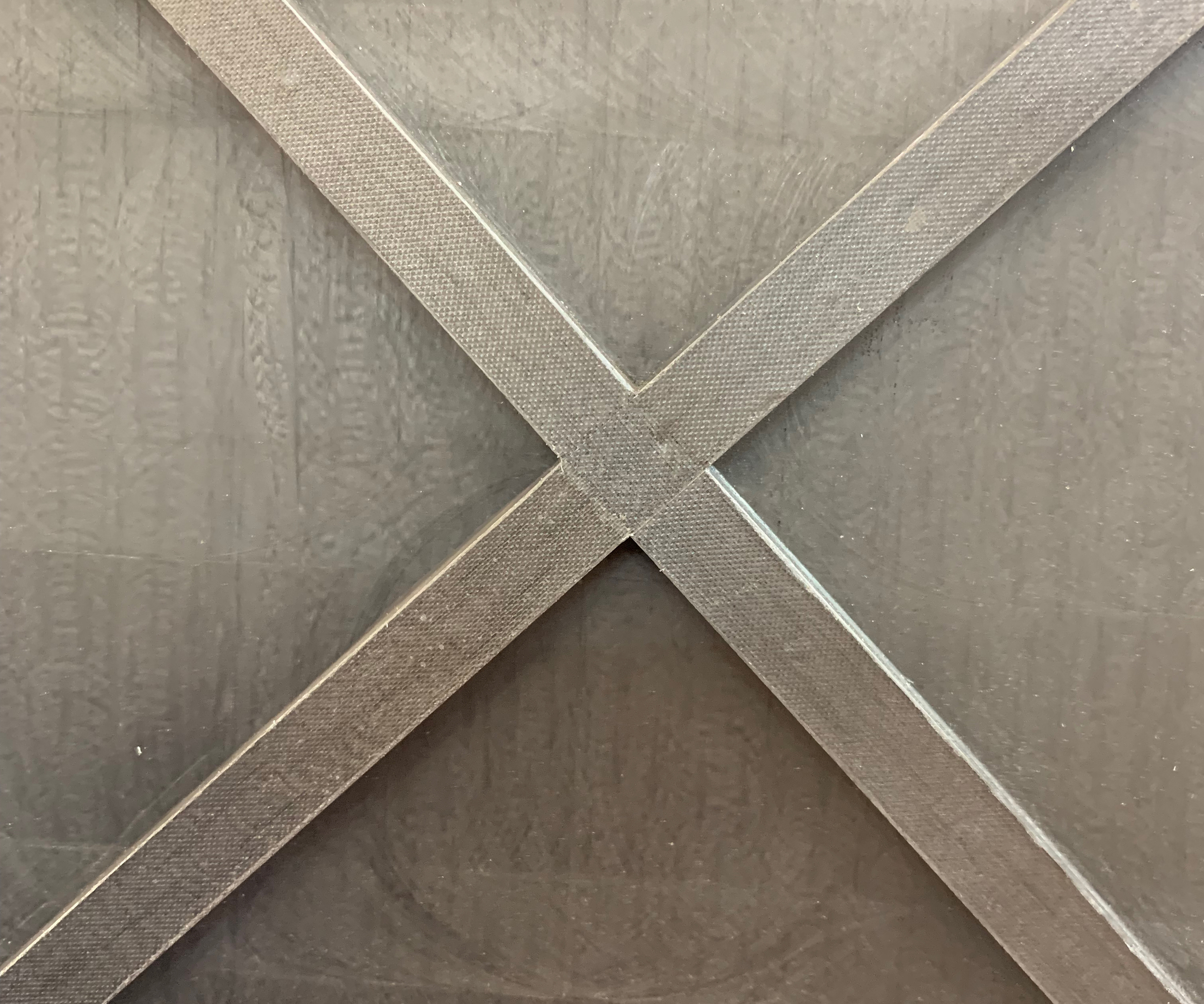
Tsai a déclaré que le facteur limitant dans la fabrication de sa conception de panneau avait été le placement des bandes de côtes. Pour être pleinement industrialisés, ils nécessitaient une vitesse de découpe et une précision de placement de bande qui, jusqu'à récemment, n'étaient pas possibles. Cependant, Tsai a approché MTorres avec sa conception et a demandé si le spécialiste ATL/AFP pouvait faire le travail. Iñigo Idareta, chef du département projets spéciaux de l'entreprise, et l'équipe composites de MTorres ont été mis à contribution et ont travaillé avec Tsai pour adapter les technologies de MTorres à l'application. Il y avait deux défis, a déclaré Idareta lors du salon aéronautique :affiner la vitesse de coupe et la précision du placement de la bande, où la capacité de coupe à la volée AFP de MTorres était essentielle pour maintenir une vitesse de superposition élevée et constante; et le développement de solutions d'outillage qui ont permis l'accumulation de chaque nervure sans que la nervure perde l'intégrité de la pile. De plus, l'utilisation du propre format de fibre de carbone sèche de MTorres pour les applications AFP était nécessaire pour rendre ce travail d'infusion difficile. Tous ont été atteints, a déclaré Idareta. Sur la base de la conception de Tsai, on obtient également l'utilisation d'un placement de fibre hors angle de la peau du panneau, qui est de quatre plis et d'environ 1,2 mm d'épaisseur.
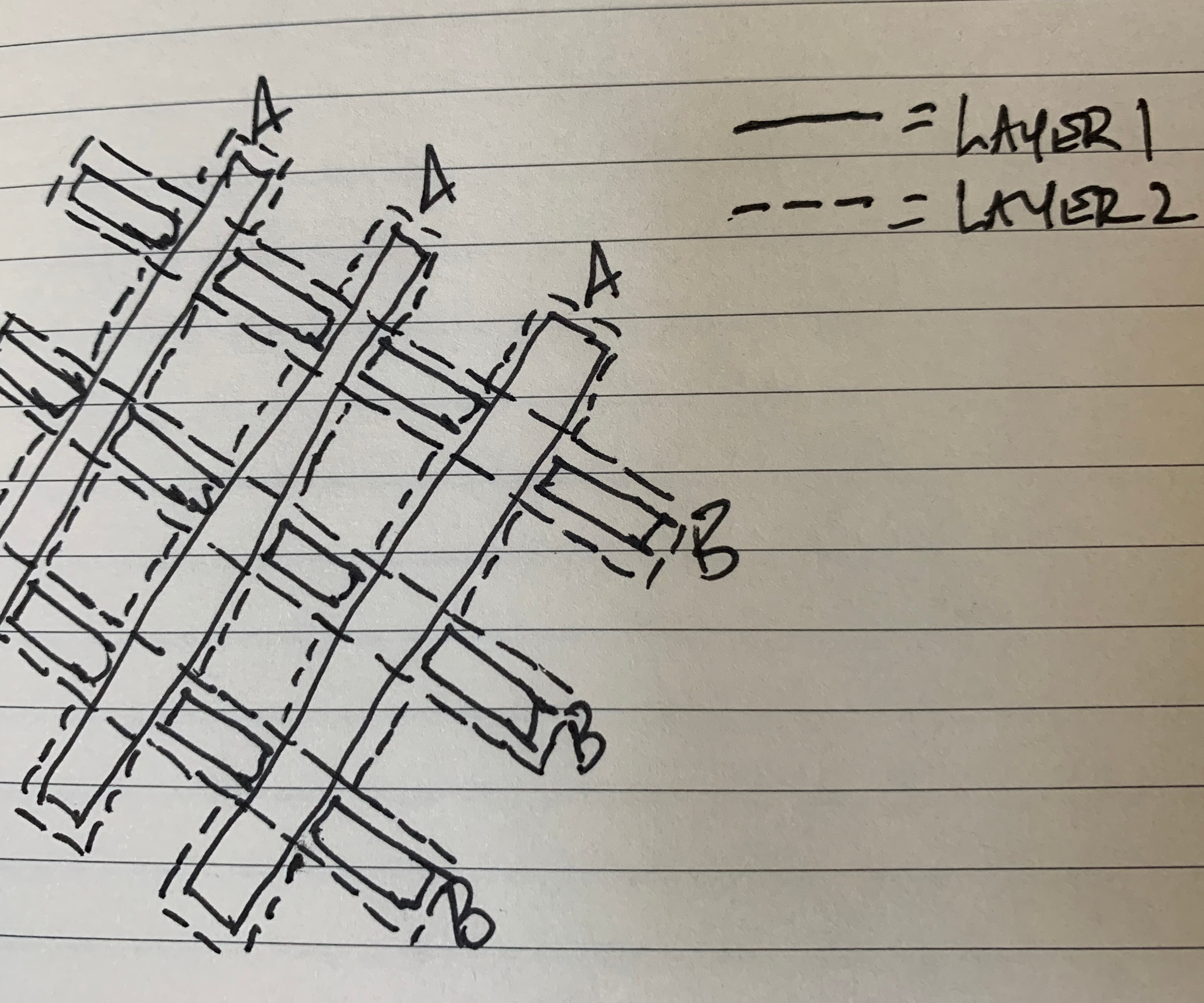
La fibre de carbone utilisée était un matériau sec 50K de Mitsubishi Chemical Carbon Fiber &Composites Inc. (Sacramento, Californie, États-Unis), choisi principalement parce qu'il s'agissait du matériau que MTorres avait sous la main. La résine était un époxyde durci de qualité industrielle « standard ». Idareta dit que le panneau a été testé par Alan Nettles à la NASA et a bien fonctionné. La liaison côtes/peau en particulier, a-t-il dit, était excellente. Tsai a admis que le point faible du panneau est le joint de nervure qui est un stratifié à plis croisés [0/90]. Les côtes étaient toutes [0]. Ainsi, les joints avaient environ la moitié de la résistance à la traction uniaxiale et un peu plus de la moitié de la résistance à la compression uniaxiale. Même avec cette faiblesse, la résistance de la grille/peau est plus du double de la technologie en aluminium actuelle de la même conception, sans compter le poids supplémentaire plus léger des composites. Tsai a également déclaré que l'aluminium, pour obtenir les mêmes propriétés de résistance que celles fournies par sa conception, pèserait trois fois plus.
Quelle est la prochaine étape pour cette technologie ? Tsai a déclaré qu'il était "prêt à être utilisé" et a énuméré plusieurs types de pièces possibles :structures de fuselage, carrosseries de lanceurs spatiaux, panneaux automobiles, boîtiers de batterie. Idareta a déclaré que MTorres travaillait sur l'itération de la conception, y compris le développement d'un panneau incurvé et d'un panneau de canon complet. Les deux, dit-il, sont à portée de main.
En outre, plusieurs aspects de la conception de Tsai pourraient être modifiés pour répondre à une variété de cas de charge. Ceux-ci incluent la largeur des nervures, la hauteur des nervures, l'angle d'intersection et l'espace entre les nervures. De plus, bien que MTorres ait utilisé l'infusion pour fabriquer le panneau exposé au salon aéronautique, il pourrait être fabriqué à l'aide d'un préimprégné thermodurcissable traditionnel.
GKN Aérospatiale. Le spécialiste des ailes commerciales GKN Aerospace (Redditch, Royaume-Uni) a annoncé lors du salon aéronautique qu'il avait fabriqué les premières pièces pour sa partie des travaux sur le programme Airbus Wing of Tomorrow, un programme de cinq ans (2018-2022), multi-entreprises, Royaume-Uni Catapulter les efforts pour développer des matériaux et des technologies de processus pour la fabrication à haut débit (100 par mois) d'ailes composites en fibre de carbone infusées de résine à déployer sur un avion monocouloir de nouvelle génération.
Paul Perera, vice-président de la technologie chez GKN Aerospace, était présent au salon aérien et a fourni plus de détails sur le programme. Il a déclaré que GKN comptait actuellement 60 personnes travaillant sur le longeron et les nervures de l'aile, le gros du travail étant effectué par le Global Technology Center de GKN, qui déménagera dans de nouvelles installations à Filton, au Royaume-Uni, plus tard cette année.
Le longeron sera en fibre sèche placée par GKN puis infusée. Les nervures seront fabriquées à partir de composites thermoplastiques et d'aluminium. Le National Composites Center (Bristol, Royaume-Uni) travaille sur plusieurs technologies pour Wing of Tomorrow, notamment iCAP (programme d'acquisition de capacités numériques) pour développer des solutions d'automatisation basées sur les données, ainsi que des systèmes automatisés de découpe et de placement de fibres développés par Loop Technology (Poundberry , Dorchester, Royaume-Uni) qui seront employés dans la fabrication des ailes. Northrop Grumman (anciennement Orbital ATK, Clearfield, Utah, États-Unis) développe des longerons pour le programme. Les revêtements d'aile inférieure seront fabriqués par Spirit AeroSystems dans son usine de Prestwick, en Écosse ; Les peaux d'ailes supérieures seront fabriquées par Airbus. L'objectif est la livraison de trois ensembles de navires à l'usine d'ailes d'Airbus à Broughton, au Royaume-Uni, pour assemblage au cours des 18 prochains mois, le premier en juin 2020, le deuxième fin 2020 et le troisième début 2021. En fin de compte, si le programme progresse comme prévu, il s'avérera que l'infusion de résine est un procédé viable pour la production à haut débit d'une aile composite pour un monocouloir de nouvelle génération. Perera affirme que les sections de longeron d'un mètre produites et évaluées dans l'installation GKN sur l'île de Wight, au Royaume-Uni, montrent que les matériaux et le processus conviennent bien à l'application.
Perera a noté qu'une grande partie du programme Wing of Tomorrow tournera autour du développement de l'automatisation. En fait, a-t-il déclaré, l'automatisation sera un élément clé de l'infusion de résine pour la fabrication aérospatiale de prochaine génération.
Matériaux composites Solvay. Si vous cherchez des preuves de la façon dont l'accent mis sur l'industrialisation de la fabrication aérospatiale et l'efficacité de la production se répercute sur les fournisseurs de matériaux, ne cherchez pas plus loin que Solvay Composite Materials (Alpharetta, Géorgie, États-Unis), qui est au milieu d'une période de plusieurs années effort pour réévaluer où et comment il produit des résines, des rubans et des préimprégnés de qualité aérospatiale. L'accent est mis pour Solvay sur le développement d'une stratégie d'exploitation axée sur des installations qui produisent moins de numéros de produits sur des équipements hautement spécialisés pouvant répondre aux exigences de cadence et de qualité des avions de nouvelle génération. Marc Doyle, vice-président exécutif de l'aérospatiale de Solvay, a déclaré que la nouvelle installation de l'entreprise à Wrexham, au Pays de Galles, au Royaume-Uni, est symbolique de cet effort. Cette usine, qui a ouvert ses portes en septembre 2018, ne produit que deux numéros de produits (adhésifs), mais dans un environnement hautement structuré, hautement optimisé et dominé par l'automatisation, conçu pour répondre aux exigences juste-à-temps de ses clients. L'entreprise prévoit de suivre ce modèle avec toutes les nouvelles installations et tentera également de convertir les anciennes usines.
Sur le front de l'innovation des matériaux, Solvay a souligné deux efforts notables, l'un axé sur les thermoplastiques et l'autre sur les fibres de carbone. Mike Blair, vice-président exécutif de la recherche et de l'innovation, a déclaré que l'un des plus grands défis/opportunités des thermoplastiques est leur delta à haute température; c'est-à-dire que les températures de traitement élevées des thermoplastiques peuvent causer des problèmes de coefficient de dilatation thermique (CTE) dans les pièces lorsqu'elles refroidissent, en particulier les grandes pièces. Le but? Modifier la chimie des polycétones pour réduire les températures de processus, sans affecter la transition vitreuse (Tg ) Température. L'entreprise cherche également des moyens d'améliorer l'aptitude au traitement et la manipulation dans les équipements automatisés de ses thermoplastiques. "Nos matériaux PEEK et PEKK standard fonctionnent bien", a déclaré Blair. « Nous avons juste besoin de les modifier pour les rendre plus adaptables. »
L'innovation entourant les fibres de carbone est tout aussi intrigante. En 2017, Solvay a acquis le fabricant de polyacrylonitrile (PAN) à gros remorquage European Carbon Fiber GbmH (Kelheim, Allemagne), ce qui a donné à Solvay un nouvel approvisionnement sain de PAN pour la fibre de carbone de remorquage 50K. Compte tenu de cela, le défi s'est posé :une fibre de carbone à gros câble peut-elle être formatée pour fournir les caractéristiques de performance d'une fibre de carbone à petit câble à module intermédiaire (IM) ? Blair a déclaré que l'idée incitait à la réflexion, mais n'était pas anodine. Il a noté que la simple manipulation de la fibre de remorquage 50K peut, en soi, endommager la fibre. Ainsi, sans trop révéler ce que Solvay a en tête, Blair a déclaré que la société travaillait sur une technologie de gestion conçue pour éviter d'endommager les fibres. "Un calendrier agressif pour cela", a-t-il déclaré, "serait de 18 mois."
Toray Advanced Composites. L'ancien TenCate Advanced Composites est désormais entièrement absorbé par Toray et, depuis mars, passe par Toray Advanced Composites (Morgan Hill, Californie, États-Unis). Steve Mead, directeur général, explique que l'EVOTL est particulièrement actif pour l'entreprise en ce moment (thermodurcissables et thermoplastiques). Il a noté que « nous fournissons du matériel aux programmes EVOTL émergents », ajoutant que « les composites sont un véritable catalyseur en raison du poids parasite de la batterie sur ces avions. Les matériaux non composites ne sont pas une option. La combinaison d'une fabrication de qualité aérospatiale à des tarifs automobiles est intrigante, a-t-il déclaré.
Éviter. Parmi les présentations les plus médiatisées au salon du Bourget figurait Alice , un avion tout électrique et tout composite présenté par Eviation (Kadima-Tzoran, Israël). Alice est un avion de transport régional de neuf places qui a une autonomie de 650 milles/1 000 kilomètres à une vitesse de croisière de 240 nœuds. L'avion dispose d'une hélice propulsive principale à l'empennage et de deux hélices propulsives supplémentaires aux extrémités des ailes pour réduire la traînée et créer une redondance. Omar Bar-Yohay, PDG d'Eviation, a présenté l'avion et a déclaré que les essais en vol seraient effectués à Moses Lake, Washington, États-Unis, suivis de la certification de la Federal Aviation Administration (FAA) des États-Unis fin 2020 ou début 2021. L'avion aura un prix catalogue de 4 millions de dollars et Bar-Yohay a déclaré que la société est entièrement financée par la certification et la production précoce.

L'engin exposé au salon était un prototype non volant assemblé juste la semaine précédente. Reste à voir où et comment cet avion sera finalement produit. Le prototype, quant à lui, a été assemblé à partir de structures composites fabriquées par plusieurs fournisseurs. L'une est Multiplast (Vannes, France), qui fait partie de Carboman Group SA (Vannes), un regroupement de cinq sociétés qui comprend également Decision (Ecublens, Suisse), SNE SMM (Lanester, France), Plastinov (Samazan, France) et Plastéol (Samazan). Multiplast, qui a une histoire dans la fabrication de structures marines, a fabriqué le fuselage de l'Alice en autoclave (OOA) utilisant une structure sandwich avec âme en nid d'abeille Nomex. Le fuselage a été construit en deux moitiés sur la base d'une configuration d'axe tribord/bâbord, avec les deux sections de fuselage collées/fixées ensemble (voir la vidéo en accéléré ci-dessous). Multiplast ne sait pas si elle remportera le contrat pour la production en série de l'engin, mais la société dit qu'elle évalue ce qui serait nécessaire du point de vue des matériaux et des processus pour industrialiser la fabrication. Ailes et carénages ventral pour Alice ont été fournis par Composite Cluster Singapore (CCS).
Stratasys. Le spécialiste des machines de fabrication additive (FA) Stratasys (Eden Prairie, Minn., États-Unis) était au salon du Bourget pour souligner sa capacité à utiliser la FA pour la production de pièces et d'outillage. Pour la fabrication des composites, l'accent a été mis sur l'outillage. L'entreprise avait sur son stand deux moules réalisés à l'aide de machines Stratasys. Le matériau est l'ULTEM 1010 de SABIC, un polyétherimide non renforcé (PEI) propice au traitement en autoclave. Le premier moule était destiné à la fabrication d'un bord d'attaque d'aile en fibre de carbone et comporte des électrodes dans le moule pour augmenter la capacité de chauffage du préimprégné et réduire le temps de durcissement de 1,5 heure à seulement 10 minutes. L'autre partie était un outil de drapage fabriqué par Boom Aerospace (Centennial, Colorado, États-Unis) pour la production de petites pièces pour l'Overture avion commercial supersonique que la société développe. Scott Sevcik, vice-président des solutions de fabrication chez Stratasys, a déclaré que Boom avait déjà deux machines Stratasys en service, une troisième étant livrée plus tard cette année. Sevcik a déclaré que Stratasys devrait introduire deux nouveaux matériaux renforcés de fibres de carbone hachées pour une utilisation en AM plus tard cette année; Stratasys, a-t-il déclaré, travaille également sur le renforcement des fibres continues pour la FA.
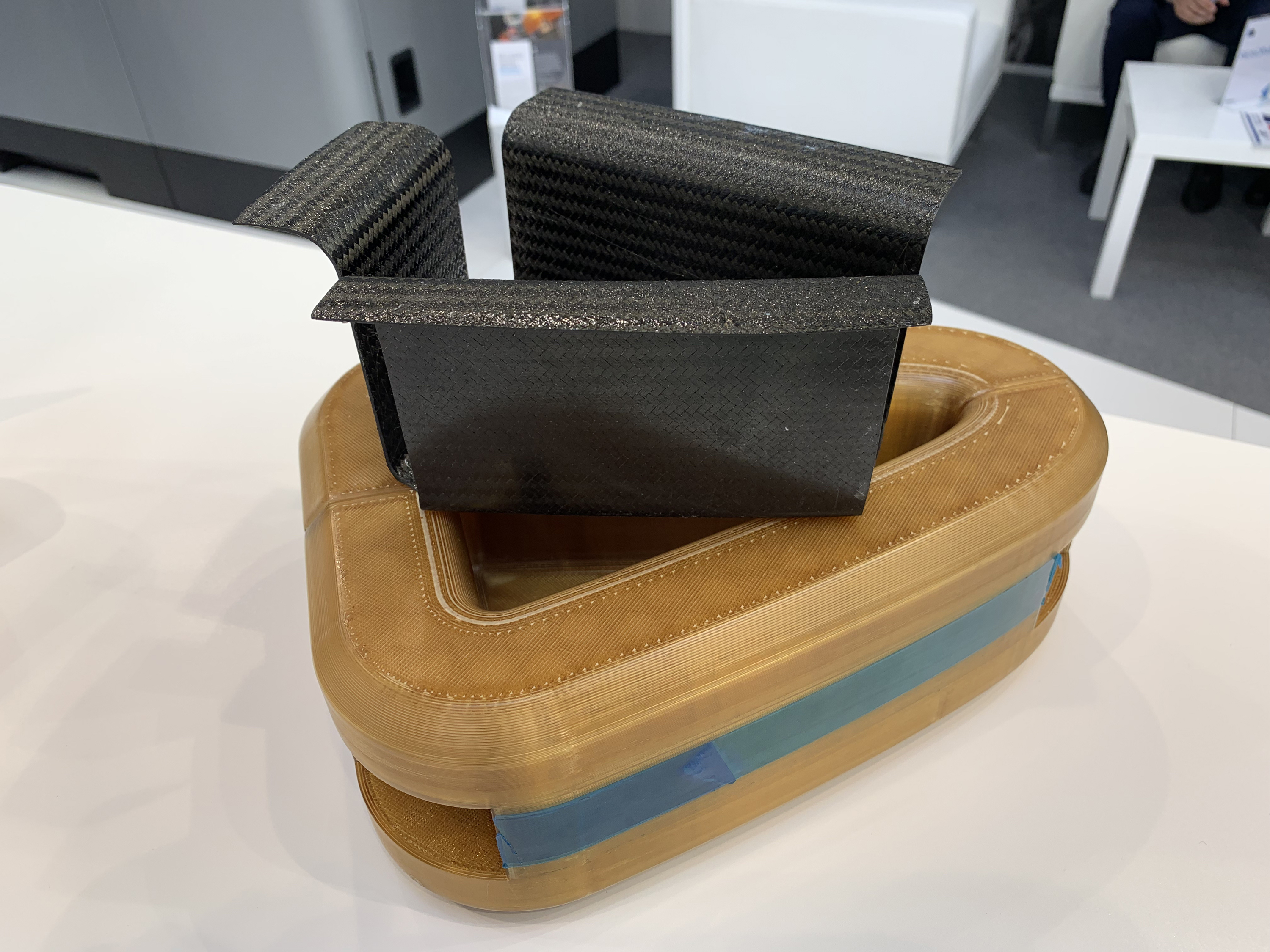
Boom Aérospatiale. Une autre annonce éclatante au salon du Bourget est venue de Boom Aerospace (Englewood, Colorado, États-Unis), qui, comme indiqué, développe Overture , un tout nouvel avion de passagers supersonique. Le PDG et fondateur de Boom, Blake Scholl, a déclaré lors d'une conférence de presse que Boom était sur le point d'achever le XB-1 à forte intensité de composites. , un prototype à petite échelle de l'Overture qui devrait être déployé d'ici la fin de 2019 et des essais en vol dans le courant de 2020. Ces vols d'essai, a déclaré Scholl, sont conçus pour aider Boom à évaluer les principes de conception et d'ingénierie de l'avion, et à appliquer les leçons apprises à la conception finale et à la production de Ouverture , qui devrait entrer en service au milieu des années 2020. Il s'agit d'un calendrier plus long que prévu par Boom. "C'est un projet ambitieux", a déclaré Scholl. "Au début, il est facile d'être trop optimiste."
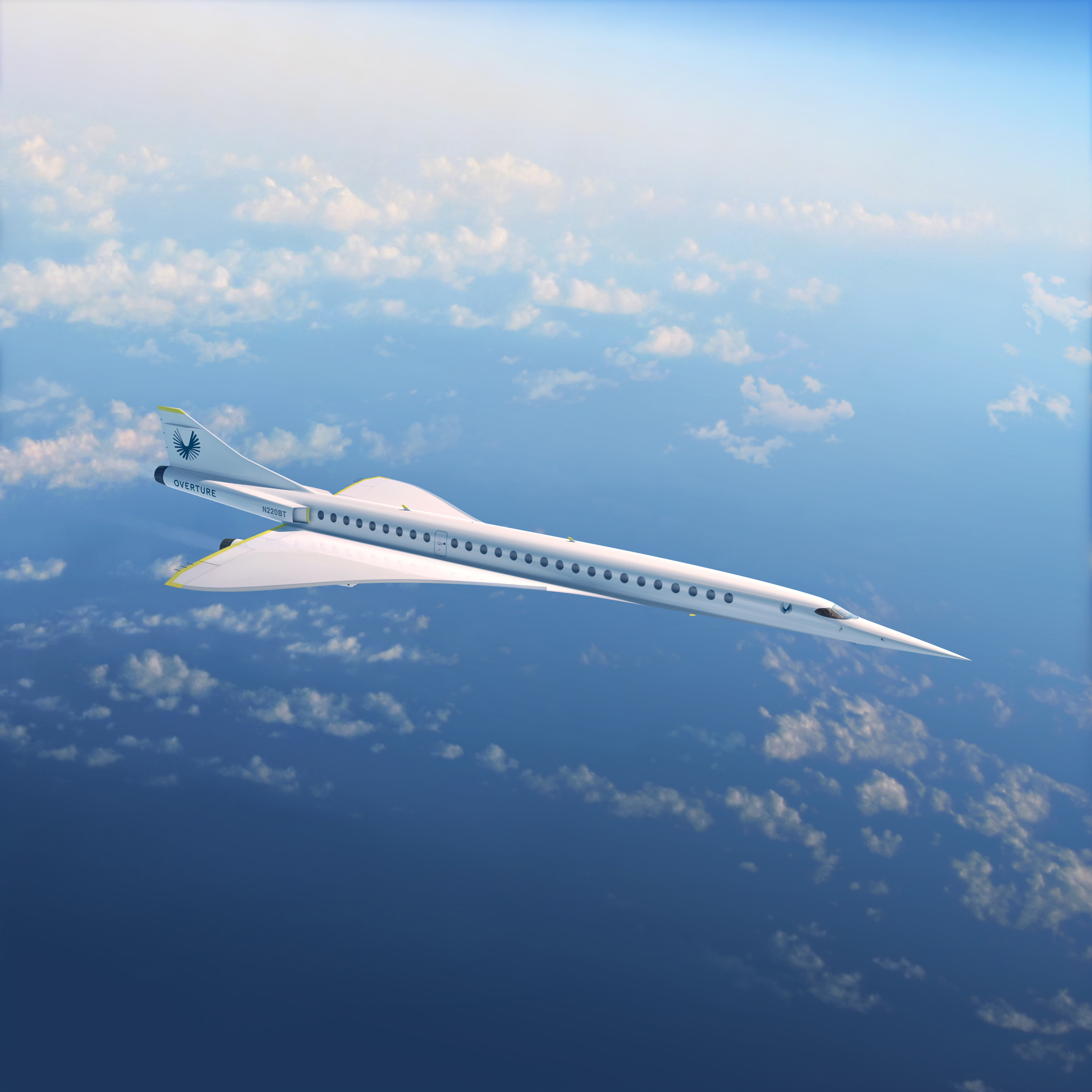
Ouverture devrait avoir une vitesse maximale de Mach 2,2, une altitude de croisière de 60 000 pieds (19 354 mètres) et transportera des passagers (55-75) de Sydney à Los Angeles en seulement 7 heures, ou de Washington D.C. à Londres en seulement 3,5 heures. Scholl a déclaré que le coût du billet sur Overture devrait être compétitif, sur une base de siège par mile, avec les tarifs actuels des compagnies aériennes. Scholl a également déclaré que Overture devrait utiliser une technologie appelée Prometheus Fuels, qui convertit le carbone atmosphérique en essence ou, dans le cas de Boom, en carburéacteur, en utilisant de l'électricité provenant de ressources renouvelables. De cette façon, a-t-il déclaré, l'avion fournira un vol supersonique net à zéro carbone.
Résine
- Renesas met l'accent sur l'intelligence des terminaux au salon Embedded World 2019
- Bett Show 2019 - Rejoignez-nous sur place
- L'inspection non destructive joue un rôle clé sur la base aérienne
- JEC World 2019 :Hexcel
- JEC World 2019 :Hexion
- Sommet SAMPE 19 Paris
- 3 façons de montrer de l'amour à votre système d'air comprimé
- Atlas Copco exposera au salon SEMA 2017
- L'air comprimé aide à alimenter les voyages de vacances