Mécanisme de déformation du sous-sol lors de la nanocoupe d'arséniure de gallium à l'aide d'une simulation de dynamique moléculaire
Résumé
Au cours du processus de nano-coupe, l'arséniure de gallium monocristallin est confronté à diverses déformations et dommages de surface/subsurface qui influencent considérablement les performances du produit. Dans cet article, des simulations de dynamique moléculaire de nano-coupe sur l'arséniure de gallium sont menées pour étudier le mécanisme de déformation de la surface et du sous-sol. Des dislocations se trouvent dans le sous-sol usiné. La transformation de phase et l'amorphisation sont étudiées au moyen de nombres de coordination. Les résultats révèlent l'existence d'une phase intermédiaire avec un nombre de coordination de cinq pendant le processus de coupe. Des modèles avec différentes vitesses de coupe sont établis pour étudier les effets sur la luxation. L'effet de l'anisotropie cristalline sur le type et la densité des dislocations est étudié via des modèles avec différentes orientations de coupe. De plus, la contrainte souterraine est également analysée.
Introduction
L'arséniure de gallium (GaAs) est un type typique de composé III-V, et c'est également l'un des matériaux semi-conducteurs les plus importants. Favorisé par ses excellentes propriétés telles que la bande interdite directe, la mobilité électronique élevée et la résistivité élevée, l'arséniure de gallium monocristallin trouve de nombreuses applications dans divers domaines tels que les dispositifs optiques infrarouges et les dispositifs à micro-ondes. Avec le développement continu de sa production, les exigences strictes en matière de rugosité de surface, de précision de forme de surface et de dommages souterrains sont de plus en plus demandées. La technologie de nano-coupe est bénéfique pour améliorer les performances des éléments optiques en arséniure de gallium et élargir le champ de ses applications. Le processus de nano-coupe du cristal d'arséniure de gallium est confronté à de nombreuses difficultés telles que la fissuration fragile, l'anisotropie et d'autres dommages souterrains. Par conséquent, l'étude sur le mécanisme de nano-coupe de l'arséniure de gallium est d'une grande importance pour résoudre les problèmes d'usinage, améliorer la qualité de surface de l'arséniure de gallium et développer la technologie de traitement nanométrique associée.
De nombreuses études ont réalisé des expériences à l'échelle nanométrique sur l'arséniure de gallium. Fang et al. [1] ont comparé les caractéristiques de nanoindentation et de nanorayure de l'arséniure de gallium et du silicium. Taylor et al. [2] ont étudié les nanoindentations à charge ultra-faible dans l'arséniure de gallium (100) avec une pointe en coin de cube. Bradby et al. [3] ont trouvé les événements pop-in de l'arséniure de gallium dans une indentation sphérique. Fang et al. [4, 5] ont étudié les propriétés d'usinage de semi-conducteurs mous et cassants et ont obtenu pour la première fois une surface de miroir en arséniure de gallium par tournage au diamant. Bien que de nombreuses études sur l'indentation et les propriétés physiques de l'arséniure de gallium aient été rapportées, on sait peu de choses sur son processus de nano-coupe et le mécanisme de formation des dommages. Ceci est principalement dû à la grande difficulté de mener les expériences et les caractérisations ultérieures. D'une part, il est presque impossible d'inspecter le processus de nano-découpe et de mesurer les données nanométriques à l'aide de mesures en ligne en raison de l'échelle nanométrique et de la vitesse de coupe élevée. D'un autre côté, il est coûteux de mener une série d'expériences d'usinage et de mesure nanométriques.
La simulation de dynamique moléculaire (MD) est l'une des méthodes les plus efficaces pour explorer le mécanisme de l'usinage nanométrique. Shimada et al. [6, 7] ont prouvé que la simulation MD est un moyen efficace de décrire le processus d'usinage nanométrique. Komanduri et al. [8] ont trouvé le phénomène de transition structurelle du silicium dans le processus de nano-coupe avec la simulation MD. Pei et al. [9] ont étudié la formation de dislocations de cuivre avec les modèles MD à grande échelle d'usinage nanométrique. Lai et al. [10] ont étudié les effets de l'angle de coupe critique et la déformation matérielle du germanium dans la coupe nanométrique et ont en outre étudié le processus de nano-coupe partiellement chevauché [11]. De plus, l'approche de modélisation multi-échelle s'est beaucoup développée dans le domaine de l'usinage d'ultraprécision [12,13,14]. La simulation multi-échelle combine des méthodes de simulation à différentes échelles, telles que le modèle MD à l'échelle nanométrique et le modèle FE à l'échelle nano/micro [15], pour étudier le processus d'usinage de manière plus complète et réaliste. Dans cet article, le mécanisme de déformation du sous-sol du processus de nano-coupe est focalisé, c'est pourquoi la simulation MD est sélectionnée comme méthode de recherche.
En ce qui concerne les matériaux étudiés, la plupart des études de simulation MD en usinage nanométrique se concentrent sur les éléments semi-conducteurs tels que le silicium et le germanium ou les métaux tels que le cuivre et l'aluminium. Moins d'études ont été rapportées sur l'analyse numérique de la nano-coupe de l'arséniure de gallium. Fan et al. [16] ont étudié la réponse ductile de l'arséniure de gallium par simulation MD et expériences de tournage. Yi et al. [17] ont étudié la transformation de phase et l'anisotropie de l'arséniure de gallium dans le processus de nanoscratch via une simulation MD. Dans cet article, une série de simulations MD tridimensionnelles est réalisée pour étudier la déformation ductile dans le processus de nano-coupe sur l'arséniure de gallium monocristallin. L'effet des paramètres de coupe tels que la vitesse de coupe et l'orientation de coupe sont également systématiquement étudiés.
Méthodes
Des modèles de simulation MD sont établis pour étudier les comportements de déformation des cristaux cassants d'arséniure de gallium dans le processus de nano-coupe. Le modèle de simulation MD tridimensionnel est illustré à la Fig. 1. La pièce est constituée d'arséniure de gallium monocristallin, cristallisant dans le réseau de zincblende avec des atomes Ga et As occupant les deux sous-réseaux FCC. La taille de la pièce est de 85 nm × 30 nm × 35 nm. Le modèle de pièce se compose de trois couches :couche limite, couche thermostatique et couche newtonienne. La pièce est fixée par la couche limite, tandis que la couche thermostatique est réglée à une température constante de 293 K pour imiter la dissipation de chaleur dans le processus d'usinage réel. La couche newtonienne est la zone de coupe qui révélera le mécanisme du processus de nano-coupe. Les mouvements des atomes dans la couche newtonienne obéissent à la deuxième loi classique de Newton. Pour imiter l'outil diamanté dans le processus de coupe réel, un modèle d'outil diamanté hémisphérique avec un rayon d'arête d'outil de 10 nm est construit et la profondeur de coupe est définie sur 4 nm. L'outil diamanté est réglé à certaines vitesses pour couper dans la pièce. Avec la limitation des ressources de calcul, le modèle est minimisé et simplifié, mais il reste convaincant pour expliquer la déformation ductile et la formation des dommages à l'échelle nanométrique. L'outil diamant est simplifié comme un hémisphère pour étudier les comportements d'enlèvement ductile dans la direction horizontale comme l'écoulement latéral et l'empilement des deux côtés de l'outil, ce qui est les caractéristiques importantes de la simulation tridimensionnelle. Pour étudier l'effet des paramètres du processus, des modèles avec différentes vitesses et orientations de coupe sont construits. Le tableau 1 liste les paramètres des modèles.
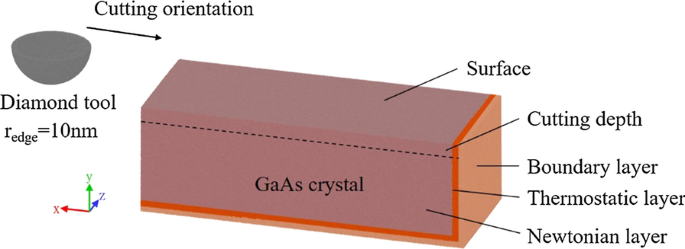
Modèle de simulation MD
Le potentiel est la base du calcul de la force et de l'énergie entre les atomes, et c'est également l'un des paramètres les plus importants de la simulation MD. Dans l'étude précédente, un système de potentiel composé de trois types de potentiel a été déterminé pour la simulation de l'arséniure de gallium et du modèle d'outil diamanté [18]. Dans ce système, un potentiel de Tersoff-Brenner est utilisé pour décrire l'interaction entre Ga et As, montrant un bon effet de simulation [19]. Un potentiel répulsif exponentiel est établi pour décrire l'interaction entre l'outil diamanté et la pièce en arséniure de gallium via une méthode de chimie quantique, qui se présente sous la forme d'un potentiel de Born-Mayer simplifié [18]. Un potentiel Tersoff-ZBL est utilisé dans l'outil diamanté. Le système potentiel est résumé dans la figure 2.
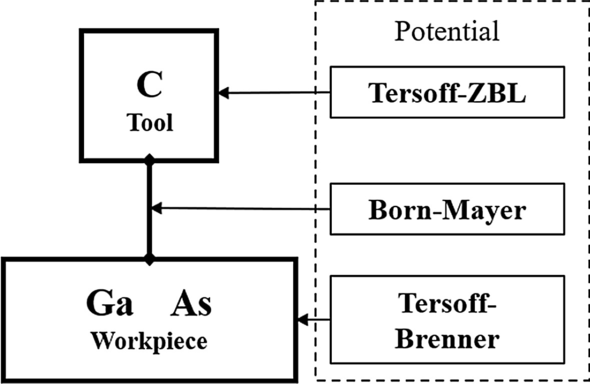
Système potentiel dans le modèle
LAMMPS est utilisé pour effectuer la simulation MD, tandis que la visualisation et l'analyse se font via OVITO, y compris l'analyse de la dislocation (DXA), le calcul des contraintes et l'analyse de la coordination. La relaxation de la pièce est définie comme un ensemble NPT pour minimiser l'énergie du système et stabiliser la surface libre, tandis que le processus de nano-coupe est défini comme un ensemble NVE. Le pas de temps pour l'intégration dans la simulation est de 1,0 fs.
Résultats et discussion
Description générale
Comme le montre la Fig. 3, la pièce en arséniure de gallium est usinée à une distance de coupe de 60 nm avec une vitesse de coupe de 400 m/s le long de la direction [\(\overline{1}\)00] sur le (010) avion. La pièce est colorée avec le déplacement de l'atome dans le y -direction. On observe que les atomes devant l'outil s'écoulent vers le haut, devenant des copeaux par extrusion. Une montagne d'atomes coule vers le bas et forme la surface usinée. De part et d'autre de la rainure usinée, les atomes s'empilent sur une hauteur de 2 nm en raison de l'extrusion et du labourage de l'outil. Le résultat révèle que la déformation et l'élimination du cristal d'arséniure de gallium fragile représente un comportement ductile lorsque l'usinage est à l'échelle nanométrique. Peu d'amas d'arséniure précipitant vers la surface usinée sont évidents dans le processus de simulation. Cette étude révèle la présence de précipitation d'arséniure après recuit [20]. Le potentiel de Tersoff-Brenner a permis de simuler la précipitation d'amas d'arséniure [19]. Dans le processus de coupe, le matériau de surface est chauffé avec une chaleur de coupe puis recuit, formant des grappes d'arséniure. Cependant, cette précipitation n'est pas une préoccupation majeure dans le processus de nano-coupe. Par conséquent, ces atomes seront cachés dans l'analyse ultérieure.
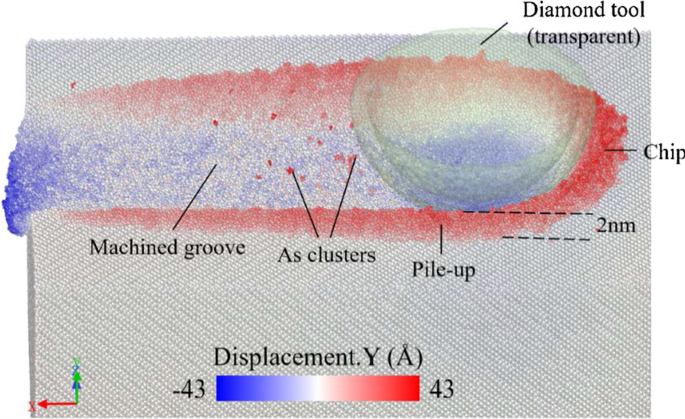
Résultat de la simulation de nano-coupe coloré avec le déplacement de l'atome dans le y -direction
Comparez la courbe de force de coupe pendant le processus d'usinage sur la figure 4. Initialement, la force tangentielle et la force normale augmentent avec l'outil coupant le matériau. La force latérale fluctue autour de 0 car les forces s'annulent dans le z -direction. Lorsque les forces sont stabilisées, la force normale et la force tangentielle fluctuent autour de 1700 nN et 700 nN, respectivement. On constate que la force dans le y -La direction est dominante dans le processus de coupe en raison du grand angle de coupe négatif effectif de l'outil diamanté tel que présenté dans le modèle. L'angle de coupe négatif apporte une contrainte de compression importante, ce qui provoque une force normale élevée dans le processus de coupe.
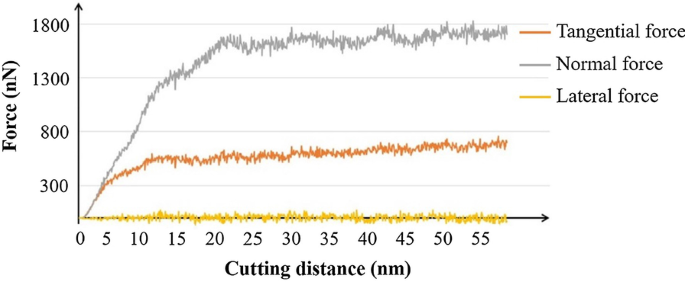
Force de coupe dans le processus de nano-coupe
Dislocations et défauts d'empilement
La formation des dommages sous la surface est une partie importante de l'étude du mécanisme de nano-coupe. Il est nécessaire de comprendre le mécanisme de formation des dommages de l'arséniure de gallium pendant l'usinage pour optimiser davantage les paramètres de traitement. Les cristaux ont une anisotropie sur la structure atomique, et c'est l'un des problèmes les plus sérieux dans le processus d'usinage, qui affecterait les performances du processus avec différentes orientations.
La distribution des dislocations dans la sous-surface usinée est illustrée à la Fig. 5, et le mouvement de l'outil est le long de l'orientation de coupe (010) [\(\overline{1}\)00]. Les dislocations sont observées autour du sillon usiné formant une couche de dislocation d'environ 8 nm. Deux principaux types de dislocations sont présents dans le sous-sol usiné. Les dislocations 1/2[110] glissent principalement dans les deux flancs de la rainure usinée, tandis que les dislocations 1/6[112] se répartissent sous le fond de rainure. Les dislocations 1/2[110] et 1/6[112] se sont avérées être des dislocations parfaites (lignes bleues) et des dislocations partielles (lignes vertes), respectivement. La formation de dislocations désigne les mouvements transitifs des atomes locaux, ce qui implique que la déformation et l'enlèvement sont à l'état ductile. Il est prouvé que le matériau fragile présente également un état ductile à une échelle suffisamment petite.
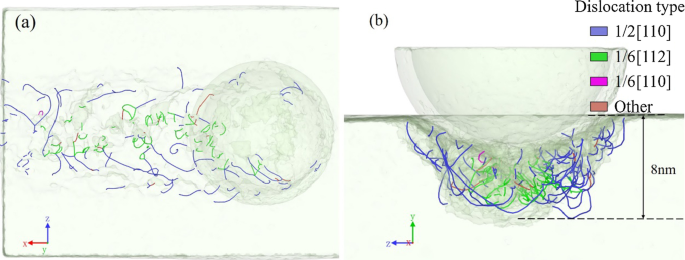
Vues en perspective de la distribution des dislocations dans le sous-sol usiné, en a y -direction et b x -direction
La contrainte de von Mises, qui est calculée en incluant les composants de contrainte de cisaillement, est généralement utilisée pour déterminer la formation de dislocation. La figure 6 est la vue en coupe de la dislocation et de la distribution des contraintes de von Mises. La zone à forte contrainte est concentrée sous l'outil en raison de l'extrusion. Lorsque la contrainte exercée par l'outil dépasse la limite d'élasticité du matériau de la pièce, le matériau glissera le long de la surface de glissement et le mouvement relatif du matériau de glissement entraînera des dislocations. Par conséquent, les dislocations nucléent et s'étendent dans le monocristal en raison de contraintes élevées dans la zone d'usinage. L'énergie locale sera libérée par le mouvement atomique.
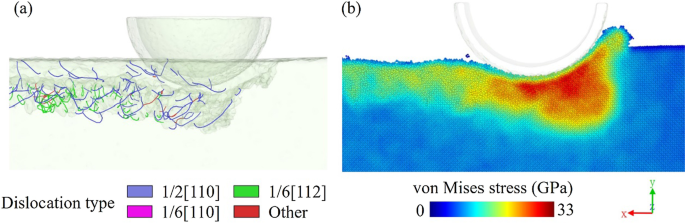
un Distribution des luxations et b Distribution des contraintes de von Mises dans la sous-surface du modèle de nano-coupe
Les dislocations dans les matériaux fragiles et ductiles sont très différentes. L'arséniure de gallium est un cristal cassant typique, et les dislocations sont concentrées près de la surface usinée. Cependant, les dislocations dans les matériaux ductiles comme le cuivre vont s'étendre et glisser profondément dans la pièce et former un groupe de dislocations à haute densité pendant le processus de coupe [21], comme le montre la figure 7a. Les dislocations résultent de la déformation ductile des matériaux. L'extension des amas de dislocations pour les matériaux ductiles conduit à une large gamme de déformations ductiles et à une contrainte diffuse. Cependant, la localisation des dislocations dans les matériaux fragiles tels que l'arséniure de gallium indique que la déformation ductile ne se produit que près de la surface sans relâchement complet de la contrainte. Lorsque la contrainte est concentrée à une valeur seuil, d'autres types de dommages, tels que des transformations de phase ou des fissures, peuvent apparaître. Dans notre étude précédente [18], la formation de fissures d'arséniure de gallium a été étudiée et il a été constaté que le mode d'élimination passera du mode ductile avec formation de dislocations au mode fragile avec fissures lorsque la vitesse de coupe augmente. La formation de dislocation relâchera la contrainte qui peut provoquer l'amorçage des fissures, et le mode de déformation aura tendance à être ductile au lieu d'être fragile dans ce cas.
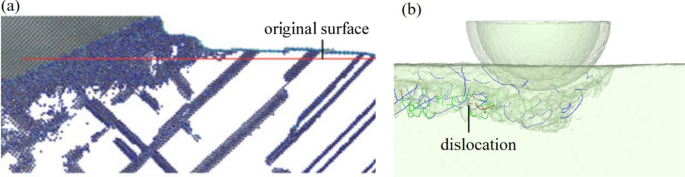
Dislocation en nano-coupe de différents matériaux monocristallins :a cuivre [21] et b arséniure de gallium
La figure 8 révèle les défauts d'empilement trouvés dans le sous-sol usiné. Les atomes de la pièce sont colorés en fonction du numéro de coordination. Pour une inspection pratique, des atomes à quatre coordinations avec une structure originale de zincblende sont cachés. On peut observer qu'il existe des atomes à trois coordinations placés périodiquement dans le sous-sol usiné. Combinées aux dislocations partielles retrouvées sous le fond de rainure, les dislocations partielles qui sont principalement émises par les joints de grains ou les surfaces libres peuvent provoquer la formation de défauts d'empilement ou de macle [22, 23]. Les failles d'empilement dans le modèle ne sont pas des plans atomiques complètement disloqués mais plusieurs petites zones à la limite du monocristal et de la couche amorphe, donc les dislocations partielles existent aux limites des failles d'empilement. On peut également en déduire qu'il peut y avoir des défauts d'empilement dans la sous-surface usinée réelle.
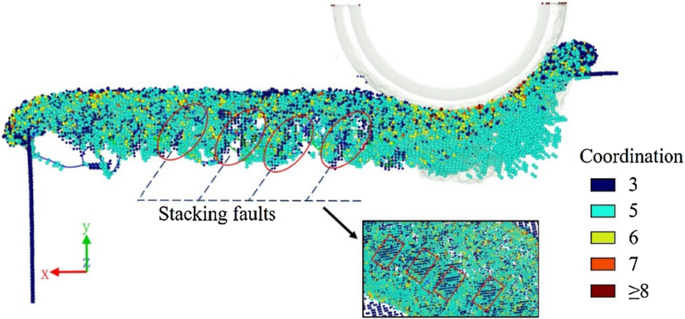
Défauts d'empilement dans le sous-sol usiné
Transformation de phase et amorphisation
La structure en treillis du matériau peut changer en raison de contraintes élevées lors de la nano-coupe. En étudiant le processus de transformation de phase, une meilleure compréhension de la coupe de l'arséniure de gallium peut être obtenue, ce qui est utile pour optimiser les paramètres du processus ou pour concevoir l'expérience de prétraitement avant la nano-coupe.
L'arséniure de gallium monocristallin a une structure zincblende sous pression et température normales. Cependant, la structure se transforme en un GaAs-II à six coordonnées lorsque la contrainte de compression atteint 17 GPa [24]. La transformation de phase aboutit à une structure de wurtzite lorsque la contrainte augmente au-delà de 60 GPa [25].
La figure 9a présente le changement structurel dans le modèle avec une vitesse de coupe de 400 m/s à l'orientation (010)[\(\overline{1}\)00]. On observe qu'une couche de la zone usinée présente une structure amorphe d'une épaisseur d'environ 6 nm sans la structure caractéristique du cristal.
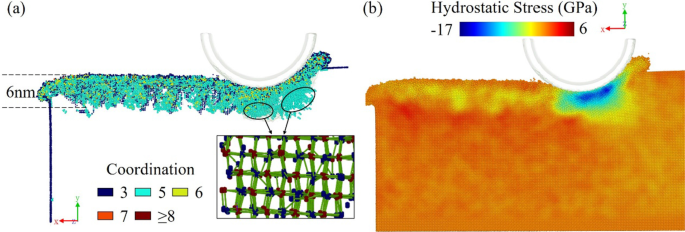
Répartition de a atomes de coordination élevée et structure à cinq coordinations et b répartition des contraintes hydrostatiques
Il est évident que certains atomes sous la position d'usinage se transforment en une structure à cinq coordinations. Semblable à la structure bct-5 de la formation de cristaux de silicium sous contrainte de compression, cette structure à cinq coordinations est considérée comme un intermédiaire dans la formation de GaAs-I à six coordonnées. La contrainte hydrostatique augmente et provoque la déformation du treillis avec la coupe de l'outil. Cependant, comme le montre la distribution des contraintes hydrostatiques de la figure 9b, la contrainte hydrostatique maximale est de 17 GPa, ce qui atteint juste la valeur critique de transformation de GaAs-I en GaAs-II. La zone souterraine où la contrainte hydrostatique est supérieure à 17 GPa est très petite et la majeure partie de la surface de la pièce a une contrainte hydrostatique inférieure au seuil de transition. En conséquence, il est difficile de trouver de gros morceaux d'atomes avec une structure à six coordinations et la structure à cinq coordinations est une phase intermédiaire de GaAs-I à GaAs-II.
La figure 10 illustre les courbes de fonction de distribution radiale d'une zone sélectionnée dans le processus de coupe, qui est la zone située sous l'outil diamanté. Les courbes de distribution radiale avant, pendant et après le traitement sont calculées. La pièce a une structure ordonnée de zincblende au début, dont la courbe se compose de pics réguliers. Lorsque l'outil diamanté atteint la zone sélectionnée, la fonction de distribution radiale montre un état désordonné à la fois à courte et à longue portée. Ceci implique la présence d'une forte amorphisation avec l'arrangement désordonné des atomes dans la zone. Cependant, la courbure du sous-sol usiné implique que la structure peut récupérer et devient ordonnée sur la courte portée et désordonnée sur la longue portée. Avec la libération de la contrainte, le matériau changera la structure en une structure avec un état d'énergie minimum. Les atomes avec une phase intermédiaire peuvent passer à un état amorphe ou autre. Ainsi, la courbe montre un état usiné stable avec de l'arséniure de gallium amorphe. On peut constater qu'il y a un pic latéral à 3,3 Å dans le processus d'usinage, et le pic disparaît lorsque l'outil quitte. Ce phénomène révèle la formation et la disparition de la phase intermédiaire, qui peut être considérée comme la déformation élastique dans le processus de coupe. Sans la force de l'outil, une partie des atomes récupérera la structure de zincblende, et les autres passeront à une autre phase stable ou à un état amorphe, ce qui représente la déformation ductile permanente.
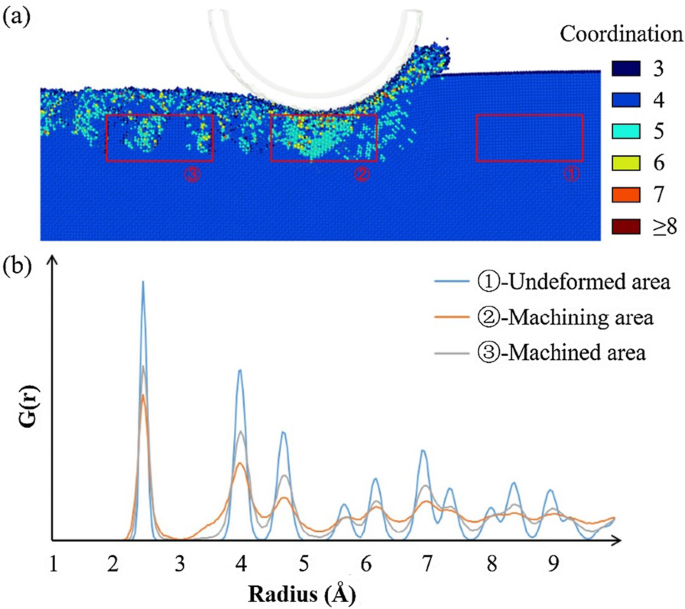
Fonction de distribution radiale de la zone sélectionnée :a zones sélectionnées; b courbes de fonction de distribution radiale correspondantes
Effets de la vitesse de coupe et de l'orientation sur la déformation du sous-sol
La formation des dommages de surface/subsurface est influencée par de nombreux facteurs, et différents paramètres de coupe affecteront la formation de la luxation.
Les distributions des dislocations avec différentes vitesses de coupe sont comparées sur la Fig. 11a–c. La densité de dislocation diminue progressivement à mesure que la vitesse de coupe augmente. Le sous-sol usiné est richement alimenté en dislocations, en particulier lorsque la vitesse de coupe descend à 200 m/s. Lorsque le processus de coupe est soumis à une vitesse de déformation élevée, le temps est insuffisant pour la nucléation et la propagation des dislocations. En conséquence, il y a moins de luxations, et la déformation ductile qui est induite par les luxations est également moins dominante. Le matériau sera déformé et désorganisé rapidement, et le temps de récupération est également court, et les atomes amorphes avec une structure non régulière seront plus faciles à former. Par conséquent, une vitesse de coupe plus élevée est un moyen de limiter la formation de luxations. Les figures 11d–f sont les vues en coupe de la distribution des contraintes de von Mises dans les trois modèles correspondants. À une vitesse de coupe plus élevée, la contrainte du matériau à proximité de l'outil est relativement plus élevée en raison de la grande énergie de coupe. En comparant les trois modèles, le modèle 800 m/s a une concentration de contrainte plus élevée devant l'outil, et la sous-surface usinée présente une région de contrainte plus continue avec des valeurs plus élevées. Au contraire, la contrainte est relâchée du fait de la formation de dislocations dans les modèles à basse vitesse. La déformation ductile induite par les dislocations libérera l'énergie de déformation locale et la contrainte causée par la flexion et la déformation élastique du réseau. Par conséquent, dans la pièce avec une vitesse de coupe plus élevée, l'état de contrainte peut être sévère en raison de l'absence de dislocations, ce qui facilite la formation de fissures lors du processus de coupe.
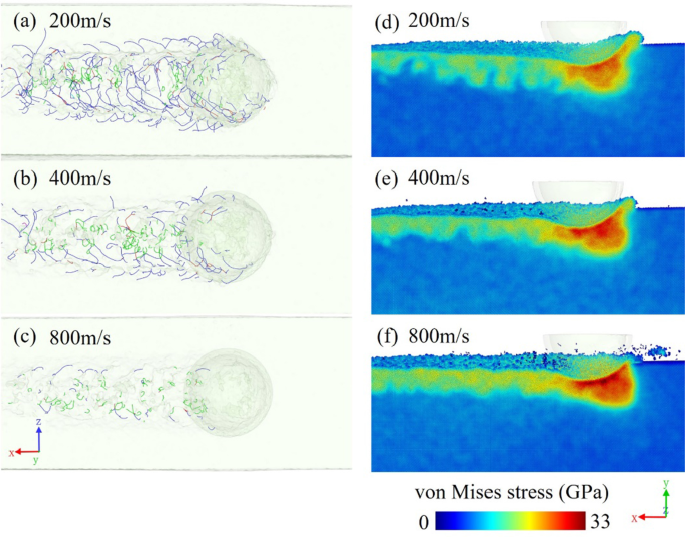
Vues en perspective de la distribution des dislocations et des distributions des contraintes de von Mises dans des modèles avec différentes vitesses de coupe de a , d 200 m/s, b , e 400 m/s, et c , f 800 m/s
L'anisotropie est un problème sérieux dans le processus de nano-coupe du cristal [26, 27], y compris l'arséniure de gallium monocristallin. En raison de sa structure monocristalline, le cristal d'arséniure de gallium présente des propriétés distinctes dans différentes orientations cristallines. Trois modèles avec des plans de coupe et des orientations différents sont construits pour étudier l'anisotropie. Les orientations de coupe sont (010)[\(\overline{1}\)00], (\(\overline{1}\)10)[\(\overline{1}\)\(\overline{1}\ )0], et \((\overline{2}11)\,[\overline{1}\overline{1}\overline{1}]\). Les figures 12a–f reflètent les grandes différences qui existent entre les distributions des dislocations. Comme indiqué ci-dessus, il existe deux types de dislocations dans le modèle (010)[\(\overline{1}\)00]. Lorsque la direction de coupe est le long de la direction \((\overline{1}10)\,[\overline{1}\overline{1}0]\), la plupart des dislocations sont au fond de la rainure usinée, tandis que certaines dislocations groupées s'étendent jusqu'à la surface devant l'outil. Peu de luxations sont trouvées des deux côtés de la paroi latérale sur la figure 12b. À l'orientation de coupe \((\overline{2}11)\,[\overline{1}\overline{1}\overline{1}]\), des dislocations arborescentes qui s'étendent du milieu aux deux côtés sont observées , couvrant la sous-surface usinée comme indiqué dans la Fig. 12c. Cependant, contrairement au premier modèle, il existe peu de luxations partielles dans les \((\overline{1}10)\,[\overline{1}\overline{1}0]\) et \((\overline{2} 11)\,[\overline{1}\overline{1}\overline{1}]\), et la plupart des dislocations sont des dislocations parfaites le long de l'orientation [110]. De même, les défauts d'empilement ne sont pas trouvés dans la zone usinée de \((\overline{1}10)\,[\overline{1}\overline{1}0]\) et \((\overline{2}11) \,[\overline{1}\overline{1}\overline{1}]\), correspondant à l'absence de luxations partielles. Cela prouve également l'effet de l'anisotropie dans le matériau.
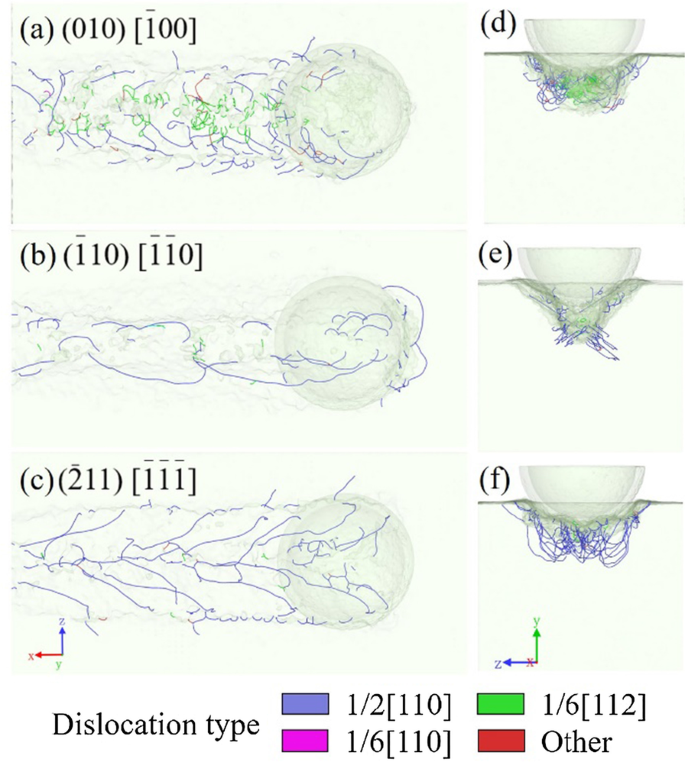
Vues en perspective de la distribution des dislocations dans les modèles avec des orientations de coupe le long de a , d \((010)\,[\overline{1}00]\), b , e \((\overline{1}10)\,[\overline{1}\overline{1}0]\), et c , f \((\overline{2}11)\,[\overline{1}\overline{1}\overline{1}]\)
Les figures 13a–f comparent la distribution des dislocations et la distribution des contraintes de von Mises des trois modèles avec différentes orientations de coupe. L'orientation cristalline a un effet évident sur la propagation des contraintes. Dans les modèles (010)[\(\overline{1}\)00] et \((\overline{2}11)\,[\overline{1}\overline{1}\overline{1}]\) , la contrainte est concentrée devant l'outil diamanté, mais les directions d'extension sont différentes. Cependant, la zone de contrainte concentrée du modèle \((\overline{1}10)\,[\overline{1}\overline{1}0]\) est plus large, et la zone de contrainte élevée devant l'outil s'étend à la surface. En raison de la différence d'orientation des cristaux, les composantes de contrainte le long de la direction de glissement seront différentes, entraînant des apparences différentes de dislocations. Lorsque l'angle de la direction de la contrainte et de la surface de glissement est petit, le glissement est plus susceptible d'apparaître et le matériau se déformera en mode ductile. Au contraire, la fissure et la rupture fragile ont tendance à s'amorcer lorsque le rapport de la contrainte de traction perpendiculaire au plan de clivage à la contrainte de cisaillement le long du plan de glissement augmente.
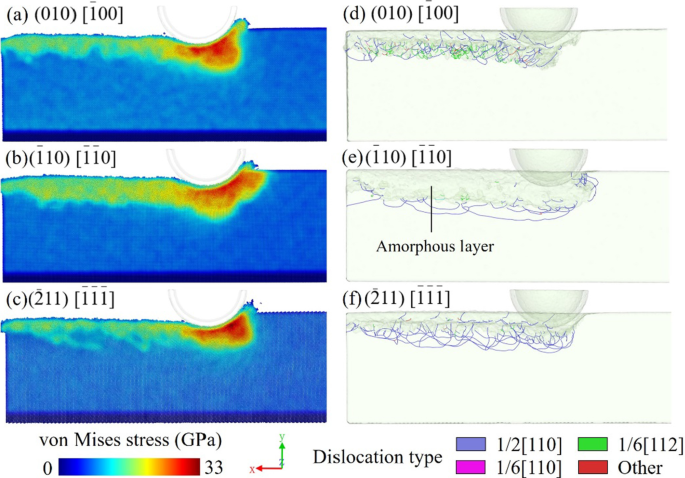
Distribution des contraintes de Von Mises et distribution des dislocations dans les modèles avec des orientations de coupe le long de a , d \((010)\,[\overline{1}00]\), b , e \((\overline{1}10)\,[\overline{1}\overline{1}0]\), et c , f \((\overline{2}11)\,[\overline{1}\overline{1}\overline{1}]\)
En comparant les distributions de contraintes et de dislocations, les modèles avec une densité de dislocations plus élevée peuvent avoir des contraintes plus faibles dans la sous-surface usinée. La figure 13e montre une couche de dommages amorphe plus épaisse dans la sous-surface du modèle \((\overline{1}10)\,[\overline{1}\overline{1}0]\), qui correspond aux régions de dislocation dense dans les autres modèles. Ce phénomène montre que l'anisotropie peut avoir un effet sur les types de dommages. Dans le modèle \((\overline{1}10)\,[\overline{1}\overline{1}0]\), la contrainte concentrée est difficile à relâcher en raison de la moindre formation de dislocation. En conséquence, l'arrangement des atomes est perturbé sous un état de contrainte sévère. La plage de contraintes est plus grande dans la sous-surface usinée et la contrainte résiduelle est plus élevée. Au contraire, le modèle \((\overline{2}11)\,[\overline{1}\overline{1}\overline{1}]\) a une couche de contrainte plus mince dans la sous-surface usinée en raison de la plus grande densité de luxation. La formation de dislocation libère une partie de la contrainte lors du processus de coupe. Dans l'étude précédente [18], lorsque le mode d'endommagement ductile passe de la dislocation à l'amorphisation, la sous-surface usinée présente un état de contrainte sévère et un endommagement amorphe. Les fissures souterraines sont plus faciles à former à la limite du cristal amorphe et du monocristal. On peut en déduire que les fissures sont plus susceptibles de se produire lorsque l'orientation de coupe est dans la direction \((\overline{1}10)\,[\overline{1}\overline{1}0]\). La formation de luxation peut réduire la formation de dommages fragiles. En plus du mécanisme de clivage, c'est aussi une raison pour laquelle la formation de fissures est affectée par l'anisotropie.
Au cours du processus de coupe, le matériau à proximité de l'outil de coupe subit une contrainte élevée et une compression sévère, ce qui entraînera des changements structurels du matériau tels que la transformation de phase et l'amorphisation. Sous la couche amorphe, un glissement se produira dans une plus grande zone et des dislocations se formeront dans le monocristal en raison des effets de contrainte généralisés. Ce sont les principales déformations ductiles dans la nano-coupe de l'arséniure de gallium. Des conditions de coupe différentes affecteront l'état de contrainte local et la facilité de formation de dislocations. Lorsque les dislocations sont difficiles à générer en raison de la vitesse de traitement élevée ou de l'anisotropie, le mode de déformation ductile aura tendance à être dominé par l'amorphe en raison de l'amorphisation causée par la contrainte non libérée. La fissure sera également facile à former dans cette situation. Au contraire, les dislocations seront la principale composante de la déformation ductile si les conditions sont propices au glissement du matériau.
Conclusion
MD simulation is used to study the mechanism of damage formation in the nano-cutting process of gallium arsenide crystal. The atomic motion and cutting force of the process are also analyzed. The dislocation, stacking fault, and phase transformation are mainly studied as the surface/subsurface damages. The conclusions can be summarized as follows:
- 1.
In the nano-cutting of gallium arsenide, the dislocation and structural transformation are found as the main deformation mechanism in the machined subsurface.
- 2.
Dislocations and stacking faults are observed in the machined subsurface groove, and the formations of stacking faults and partial dislocations are consistent.
- 3.
An intermediate phase with five-coordination is found in front of the tool because hydrostatic stress is close to but not higher than the transition threshold (17 GPa). An amorphous layer forms in the machined subsurface.
- 4.
With increasing cutting speed, the dislocation density decreases because of the high strain rate. Anisotropy has a great effect on the dislocation type and density. Partial dislocations are easier to form in the (010) [\(\overline{1}\)00] model. Moreover, the \((\overline{1}10)\,[\overline{1}\overline{1}0]\) model has a lower dislocation density and a more severe amorphization.
Disponibilité des données et des matériaux
The datasets generated or analysed during the current study are not publicly available due the data also forms part of an ongoing study, but are available from the corresponding author on reasonable request.
Abréviations
- MD :
-
Dynamique moléculaire
- GaAs:
-
Gallium arsenide
- FE :
-
Finite element
- FCC :
-
Face centered cubic
- Tersoff-ZBL:
-
Tersoff-Ziegler–Biersack–Littmark
- LAMMPS :
-
Simulateur massivement parallèle atomique/moléculaire à grande échelle
- OVITO :
-
Open visualization tool
- NPT :
-
Number-pressure–temperature, isothermal-isobaric ensemble
- NVE :
-
Number-volume-energy, microcanonical ensemble
Nanomatériaux
- C# en utilisant
- Avancement vers 7 nm
- Utiliser les angles pour améliorer l'avenir de l'électronique
- Béton intelligent utilisant des nanoparticules
- Effet de surface sur le transport du pétrole dans les nanocanaux :une étude de dynamique moléculaire
- Modélisation et simulation de dynamique moléculaire de la coupe de diamant de cérium
- Étude de l'effet de la direction d'impact sur le processus de coupe nanométrique abrasif avec la dynamique moléculaire
- Préparation et propriétés optiques des films GeBi à l'aide de la méthode d'épitaxie par faisceau moléculaire
- Comment l'arséniure d'indium et de gallium (InGaAs) améliore la détection SWIR