Acier à outils :un acier qui fait avancer les choses
La composition du métal et la production d'aciers à outils
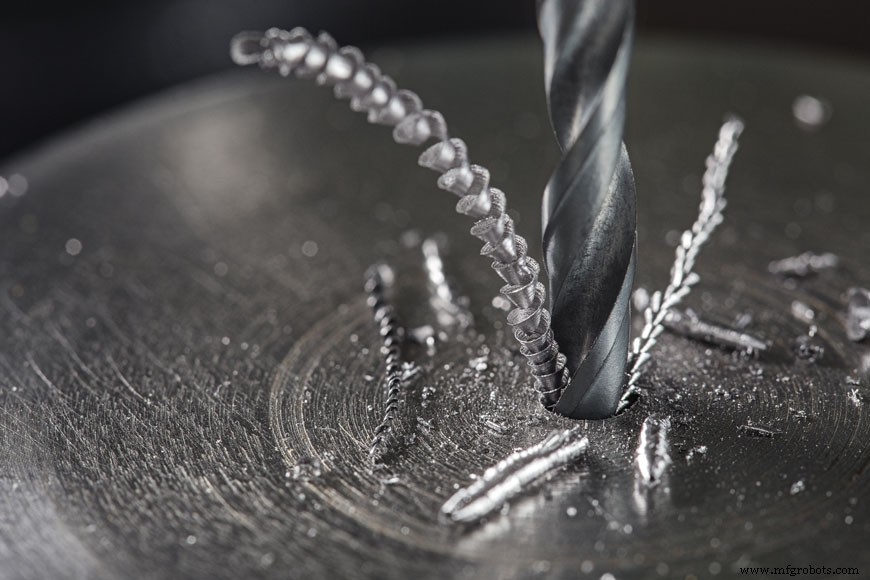
Qu'est-ce que l'acier à outils ?
Les aciers à outils sont des alliages exceptionnellement durs, résistants ou résistants à l'usure. Leurs propriétés proviennent à la fois de leur chimie et de leur fabrication. Comme leur nom l'indique, ces aciers sont prêts à couper, meuler, percer, poinçonner, frapper ou effectuer d'autres travaux difficiles. Les aciers à outils doivent avoir les bonnes propriétés matérielles pour leur application. Par exemple, un foret et un poinçon ont chacun besoin de dureté et de résistance à l'usure. Cependant, le poinçon subit plus d'impact tandis que le foret subit plus de cisaillement. Les ingénieurs et les métallurgistes choisissent le type d'acier à outils en fonction de l'utilisation de l'outil.
Les aciers à outils ont tous des éléments d'alliage qui produisent des carbures, un réseau métallique dense qui contient un métal et du carbone. Les carbures sont un matériau réfractaire, ce qui signifie qu'ils résistent à la dégradation sous la pression, les produits chimiques ou la chaleur.
Cependant, ce n'est pas seulement la chimie qui fait un acier à outils. Un acier à outils tire également sa dureté d'un traitement thermique et d'une trempe contrôlés avec précision.
Durcissement de l'acier à outils par trempe
Trempe est un procédé pour durcir l'acier en modifiant sa microstructure.
L'acier est d'abord chauffé. Les alliages d'acier sont chauffés à différentes températures en fonction de la quantité de carbone dans le mélange. Le fer et le carbone passent par différentes "phases", dans lesquelles les molécules prennent des formes différentes, et ces phases dépendent de la chimie globale.
Une fois que la bonne chaleur a été atteinte et maintenue, l'alliage est ensuite trempé ou refroidi par exposition à un gaz ou un liquide beaucoup plus froid. Cette trempe gèle le métal rapidement. Lorsque le métal est congelé par choc comme celui-ci, de nombreux minuscules grains de cristal de métal commencent tous à geler en même temps, avec beaucoup de déplacement dans chaque grain et entre eux. Comparez cela à un refroidissement très lent, où les grains se refroidissent lentement au fil du temps dans des fleurs circulaires plus grandes. Les grains de métal refroidis lentement peuvent se croiser lorsque le métal est touché, bosselant le métal mais ne le cassant pas. La congélation par choc donne à la structure moléculaire moins d'espace pour bouger lorsqu'elle est frappée, ce qui la rend plus dure et moins susceptible de se bosseler. Le réseau métallique de ces structures est appelé martensite, et c'est la structure moléculaire déchiquetée et choquée de la martensite qui donne aux métaux trempés leur dureté caractéristique.
La trempe à l'eau est le moyen le plus rapide de tremper et la trempe à l'air le moyen le plus lent. Ce que l'alliage peut supporter dépend de sa chimie. Certains alliages peuvent se fissurer ou se déformer s'ils sont refroidis trop rapidement, mais ils durciront bien dans une trempe à l'air plus douce. D'autres ne créeront pas de couche de martensite dure à moins d'être choqués par un changement de température important comme celui de l'eau.
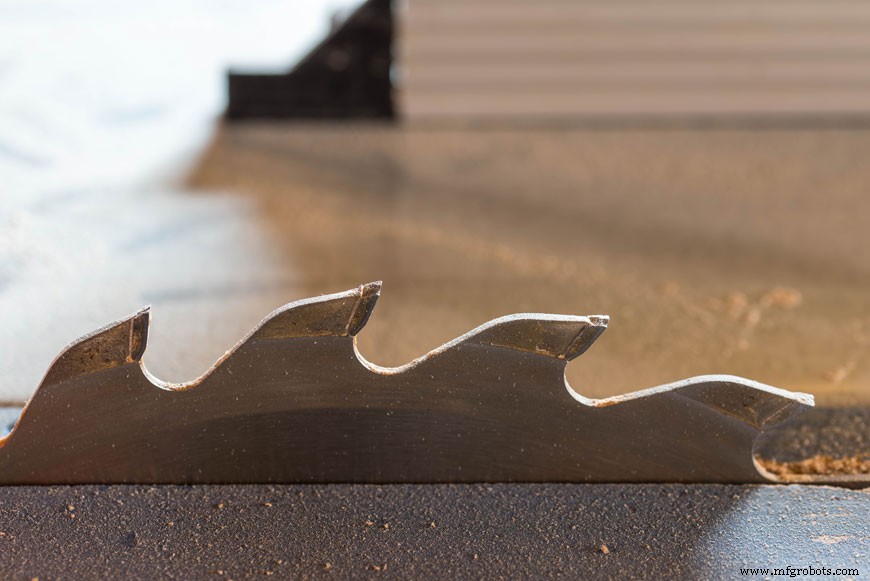
Catégories d'acier à outils
Il existe six grandes catégories d'acier à outils. Les quatre plus courants sont les aciers à outils trempés à l'eau, pour travail à froid, pour travail à chaud et à grande vitesse. Les applications spécialisées utilisent également des aciers à outils résistants aux chocs et spéciaux.
-
Durci à l'eau
Ce groupe d'aciers à outils est essentiellement de l'acier au carbone traité thermiquement. Ils ont 0,5 à 1,5% de carbone. D'autres éléments d'alliage peuvent être présents pour leurs différentes qualités, mais ceux-ci sont généralement inférieurs à 0,5 %. Ces métaux, comme le nickel, le tungstène ou le molybdène, sont chers. Utiliser moins de métal coûteux offre de la valeur pour les applications plus légères.
Le choc extrême de la trempe à l'eau est nécessaire avec ce groupe d'aciers pour obtenir une couche externe dure. Les outils légers, les petites pièces comme les ressorts et les petites attaches sont probablement des produits finaux. Ils ne doivent pas être utilisés dans des environnements extrêmes car les aciers de la série W sont un peu plus cassants que les autres aciers à outils. Les aciers de la série W sont plus vulnérables à la fissuration et ne peuvent supporter des températures continues que jusqu'à 150 °C (302 °F).
-
Acier à outils pour travail à froid
Les aciers à outils pour travail à froid sont destinés à être utilisés à des températures «froides» - ils sont durs, résistants et résistants à l'usure, mais pas dans des environnements chauds. Étant donné que la coupe de matériaux froids peut demander plus de force que la coupe de matériaux chauds, la résistance à la compression est indispensable dans l'acier à outils pour travail à froid.
Le froid, dans ce contexte, ne signifie pas qu'il est temps pour le métallurgiste d'enfiler un pull. 392°F (200°C) et moins est considéré comme un environnement de travail froid pour ces outils. Contrairement à de nombreux types d'acier, le graphite se forme souvent dans les aciers pour travail à froid. Ce graphite rend bon nombre de ces alliages usinables :le graphite assure la lubrification.
Les sous-catégories d'acier à outils pour travail à froid sont :
- Durcissement à l'huile (Série O) :Pendant la production, ces alliages sont trempés dans l'huile. Ils contiennent de 0,85 à 2,00 % de carbone et généralement moins de 1 % de chacun des autres éléments d'alliage. Ces éléments peuvent inclure le manganèse, le silicium, le tungstène, le chrome, le vanadium et le molybdène.
- Durcissement à l'air (Série A) :Pendant la production, ces alliages sont trempés à l'air. Ils ont 0,05 à 2,85% de carbone. Ces aciers peuvent contenir jusqu'à 5% de chrome. Le chrome élevé signifie que pendant le traitement thermique, la série A ne subira pas de distorsion dimensionnelle. Le chrome produit des tolérances plus étroites.
- Chrome à haute teneur en carbone (Série D) :Ces aciers pour travail à froid fonctionnent jusqu'à 797°F (425°C). Ils contiennent 1,4 à 2,5% de carbone et 11 à 13% de chrome. Ils peuvent être trempés à l'air ou à l'huile, selon l'alliage, et subissent très peu de distorsion dans les deux méthodes de refroidissement. Ces alliages ont généralement une très grande résistance à l'abrasion.
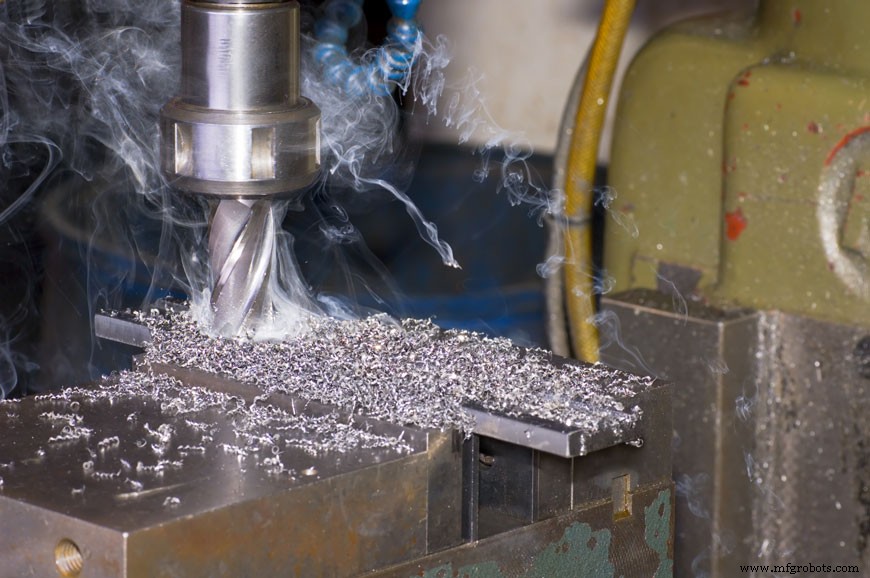
-
Acier à outils pour travail à chaud
Les aciers à outils pour travail à chaud ont tous un pourcentage plus élevé d'éléments d'alliage pour créer plus de carbures et supporter des températures de travail plus élevées. Les aciers à outils pour travail à chaud peuvent fonctionner à des températures allant jusqu'à 1004°F (540°C). En tant que groupe, la plupart ont des pourcentages de carbone faibles, inférieurs à 0,6 %.
L'acier à outils pour travail à chaud est souvent utilisé dans la fabrication à haute température avec des matériaux chauds malléables comme le métal et le verre. Les matrices, les poinçons, les extrudeuses et les compresseurs peuvent tous être fabriqués avec de l'acier pour travail à chaud. L'outil doit continuer à fonctionner même en cas d'exposition prolongée à la chaleur.
Il existe trois principaux types d'acier à outils pour travail à chaud, basés sur l'élément d'alliage principal :le chrome, le tungstène ou le molybdène. Quelques-uns ont des niveaux élevés de chrome et de tungstène, et sont donc classés en tungstène ou en chrome selon le fabricant. L'élément d'alliage majeur produit le type de carbure dans l'acier, et chaque carbure offre des avantages différents.
Les sous-catégories d'acier à outils pour travail à chaud sont :
- Chrome :Les aciers à outils pour travail à chaud au chrome contiennent 3 à 5 % de chrome. D'autres éléments d'alliage comme le tungstène, le vanadium ou le molybdène sont inférieurs à 5 %. Le vanadium est généralement utilisé dans l'acier utilisé pour les outils de coupe. Ce groupe d'alliages (et plus particulièrement AISI H13) sont les outils de travail à chaud les plus utilisés.
- Tungstène :Ces alliages ne contiennent souvent ni molybdène ni vanadium. Au lieu de cela, ils contiennent 9 à 18% de tungstène. La plupart des aciers à outils de travail à chaud au tungstène contiennent entre 2 et 4% de chrome. Ce n'est pas universellement vrai :par exemple, l'alliage AISI H23 contient 12 % de chrome et 12 % de tungstène. Le H23 est parfois appelé un acier au chrome, parfois un acier au tungstène, et parfois les deux. Les aciers au tungstène offrent une excellente résistance à la chaleur mais peuvent être cassants; ceci est géré par le préchauffage à la température de fonctionnement avant utilisation.
- Molybdène :De nombreux aciers à outils pour travail à chaud au chrome contiennent un peu de molybdène. Les aciers de travail à chaud de qualité supérieure pour les environnements très difficiles en ont beaucoup. Le molybdène crée une stabilité à la chaleur et une résistance à l'usure plus élevées dans les applications de travail à chaud sévères. Les alliages de molybdène AISI H42 et H43 sont souvent utilisés comme matrices ou fraises dans les laminoirs pour gérer la chaleur et la force de coupe et de forgeage.
-
Acier à outils rapide
Les processus de production modernes sont en partie possibles à l'invention de cette classe d'acier à outils. Les outils de coupe et les mèches de machine qui tournent à grande vitesse chauffent à cause du frottement. L'innovation des matériaux à grande vitesse a permis aux machinistes d'augmenter leur taux de production.
En 1900, l'acier à outils rapide fait ses débuts à l'Exposition de Paris. Une foule de fabricants ont eu le souffle coupé de voir un tranchant commencer à briller à cause de la friction tout en continuant à fonctionner. Là où les vitesses de coupe dans les années 1890 étaient de 5 à 30 pieds par minute, en 1905, il y avait des machines se déplaçant à 150 pieds par minute.
Les aciers à outils rapides contiennent 14 à 18 % de tungstène, 3 à 5 % de chrome, 0,6 % de carbone et d'autres éléments en fonction de l'application.
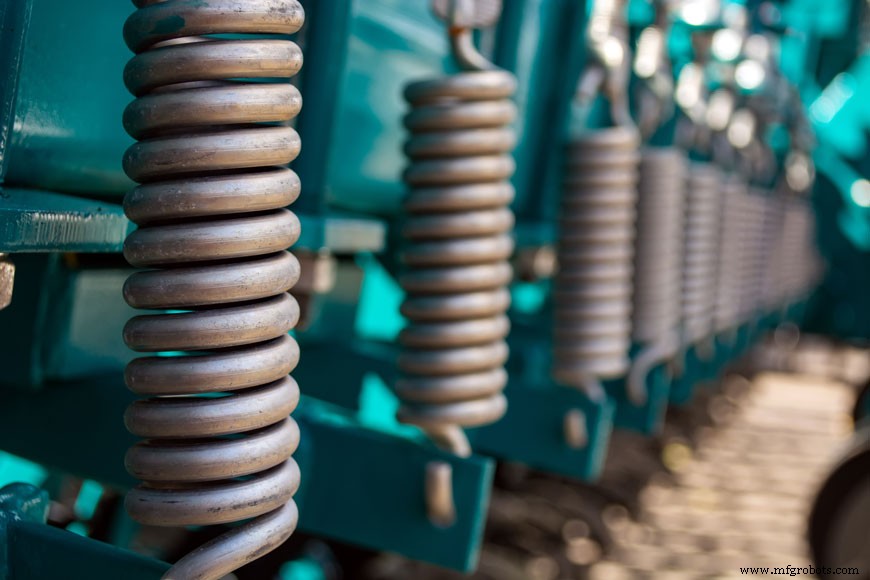
-
Acier à outils résistant aux chocs
Les aciers à outils résistants aux chocs du groupe S sont incroyablement solides, conçus pour avoir une résistance élevée aux chocs. Leur force ne réside pas simplement à la surface ou à la couche « choquée » de l'outil. Ils peuvent être utilisés pour les ressorts, les ciseaux, les matrices d'estampage et les poinçons. Ce groupe d'alliages contient souvent de nombreux éléments d'alliage, dont la plupart sont présents dans d'autres aciers à outils. Cependant, le silicium, de l'ordre de 0,15 à 3 %, est présent dans cette classe d'aciers.
-
Acier à outils à usage spécial
Ce groupe d'alliages est l'endroit où les canards étranges vont se percher; ces métaux sont utilisés dans des applications spécifiques et peuvent même être créés pour un fabricant particulier par un métallurgiste. Ce groupe comprend les aciers faiblement alliés à haute teneur en fer où tous les autres éléments d'alliage sont utilisés avec parcimonie. Ceux-ci ressemblent le plus aux aciers W bon marché et sont également trempés à l'eau. L'ajout minutieux d'autres éléments augmente les propriétés mécaniques mais réduit les coûts. Les aciers «moulés» à faible teneur en carbone font également partie de ce groupe d'alliages spéciaux. Ceux-ci sont utilisés pour le moulage thermoplastique qui doit être tolérant à la chaleur et résistant à l'usure mais n'a pas besoin d'une résistance élevée aux chocs.
Choisir un acier à outils
Si vous concevez une machine industrielle ou achetez une machine à des fins industrielles ou de fabrication, le type d'acier à outils utilisé est important et doit être spécifié par un ingénieur.
Le besoin de savoir est différent pour les particuliers qui achètent des outils à main. Souvent, un fabricant d'outils à main proposera de l'"acier trempé", puis choisira l'acier en fonction de l'utilisation prévue de l'outil. Cependant, la nuance d'acier utilisée est un secret industriel pour chaque fabricant d'outils. Les fabricants équilibrent la valeur et les contraintes du travail pièce par pièce. La meilleure façon de choisir des outils est d'obtenir des recommandations de professionnels du domaine, d'amis et d'avis en ligne, plutôt que de se soucier de l'alliage lui-même. Si le fabricant a des compétences métallurgiques et ne prend pas de raccourcis, la conception d'un outil à main devient plus importante que l'alliage.
Les forgerons, fondeurs et autres métallurgistes seront plus curieux, même au niveau amateur. La recherche de ressources et de forums dans ces groupes fournit une mine d'informations sur ce à quoi on peut s'attendre et quels types de métal pourraient être mieux utilisés.
Articles associés :
- L'acier au carbone est-il meilleur que l'acier doux ?
- Acier contre acier inoxydable
- Classification de l'acier :chimie et propriétés
Métal
- Éléments à considérer lors du choix d'une nuance d'acier inoxydable
- Nuances d'acier à outils
- Caractéristiques et fonctions de l'acier à outils résistant aux chocs
- Facteurs clés à prendre en compte lors de la sélection d'une nuance d'acier à outils
- Différentes propriétés et nuances d'acier à outils
- Un aperçu de l'acier à outils et de ses applications
- Éléments à prendre en compte lors du choix d'une nuance d'acier à outils
- Un aperçu de l'acier à outils et de ses applications connexes
- Tout ce que vous devez savoir sur l'acier à outils résistant aux chocs