FRACAS :Le secret pour une meilleure fiabilité des actifs
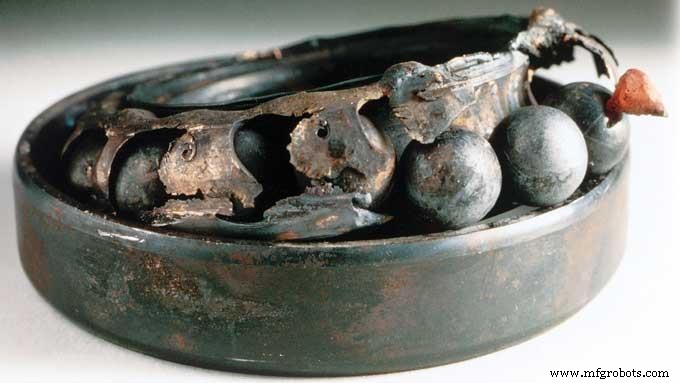
Fondamentalement, l'ingénierie de la fiabilité consiste à prévoir et à prévenir les défaillances. En énumérant toutes les manières dont un système peut échouer, il devient possible de déterminer toutes les manières dont la défaillance peut être détectée, retardée ou arrêtée avant même qu'elle ne puisse vraiment commencer.
Le système de signalement, d'analyse et d'action corrective des défaillances (FRACAS) est une méthode organisée de tri des moyens possibles de défaillance des actifs et de recherche de toutes les causes profondes possibles. Le produit final agit comme une carte de toutes les manières dont les choses peuvent échouer, permettant d'élaborer un plan pour corriger les problèmes au fur et à mesure qu'ils surviennent, et pour éliminer les problèmes chroniques dès le début.
Le processus FRACAS doit englober une compréhension de la criticité des composants dans l'ensemble du système et doit faire appel à des planificateurs, des mainteneurs et des opérateurs expérimentés pour répertorier toutes les innombrables façons dont une machine tombe en panne.
Échec
L'échec est mieux défini comme tout état de fonctionnement autre qu'idéal. La plupart considéreraient l'échec comme un état d'inopérabilité totale, mais fonctionner dans un état dégradé devrait tout de même être considéré comme un échec. J'étais récemment dans une usine où une machine avait été rééquipée pour fonctionner à une vitesse supérieure à celle conçue à l'origine. Les opérateurs et les responsables de la maintenance dans cette zone spécifique de l'usine ont considéré que c'était un grand succès d'avoir fait fonctionner leur système si bien, mais juste en bas de la ligne, la suralimentation n'avait pas été prise en compte et le produit se déversait au prochain pompage. point, créant un gros tas de déchets. Ainsi, l'échec peut être quelque chose qui fonctionne mieux qu'il n'est censé fonctionner et qui fonctionne moins bien.
La meilleure façon de procéder est de répertorier toutes les manières dont une machine peut tomber en panne en la décomposant en sous-composants plus petits qui seraient soit travaillés, soit remplacés dans le cadre d'une réparation. Le niveau des sous-composants peut aller jusqu'aux écrous et boulons ou à des équipements « sur étagère » qui peuvent facilement être remplacés, comme un petit moteur ou un capteur. Il est très utile d'avoir accès au programme d'inventaire des matériaux que votre site utilise.
Cela peut déjà être lié à la GMAO en cours d'utilisation ou peut être un système distinct. L'utilisation du programme d'inventaire des matériaux sera à nouveau utile plus tard au cours de la section des actions correctives pour déterminer combien de pièces de rechange et de consommables doivent être conservés.
Rapports
Un autre mot qui conviendrait bien ici serait enregistrement. Le slogan de mon premier responsable de la maintenance était « tu dois l'écrire ». Il est important de tout enregistrer dans une méthode structurée et organisée. Il existe de nombreuses options logicielles qui peuvent être achetées pour vous aider dans ce domaine, mais pour une usine ou un système plus petit, envisagez d'utiliser des projets ou une feuille de calcul. Il est important d'avoir une cascade structurée de sous-composants et de types de défaillance car des modèles et des méthodes de défaillance répétées se produiront. Théoriquement, il existe une infinité de façons dont quelque chose peut échouer, mais dans la pratique, vous en retrouverez souvent les mêmes.
Une autre méthode de rapport consiste à utiliser une carte des causes pour chaque système. Il s'agit d'une approche plus graphique et peut être plus difficile à capturer électroniquement sans une certaine expérience dans ce processus, mais dans de nombreux cas, cela permet une compréhension plus facile de ce qui se passe par d'autres en dehors du processus FRACAS. Une version simple serait un dessin ou une image de base du système ou de la machine en question avec des zones de texte arborant les points de défaillance. Ces boîtes peuvent ensuite se ramifier en d'autres causes ou effets créant une sorte de nuage de modes de défaillance autour de l'équipement au milieu.
Analyse
Le fait d'avoir toutes les méthodes d'échec répertoriées de manière organisée permet désormais à une équipe d'experts en la matière d'examiner et de remarquer les tendances. Le fait d'avoir un groupe expérimenté qui examine les données permet également à une bonne quantité d'historique d'entrer en jeu. Chaque usine possède au moins une machine avec un record établi de pannes et il est essentiel de disposer d'une équipe de personnes familières avec ce genre d'incidents pour réussir la phase d'analyse.
Avec cela, il est également important de faire la distinction entre les défaillances chroniques et les événements ponctuels. Il peut y avoir une tendance à se concentrer sur des événements notables ou particulièrement catastrophiques et à essayer d'empêcher que le même ensemble de circonstances spécifiques ne se reproduise. Bien qu'il soit important de considérer toutes les possibilités, l'échec matériel est parfois un événement si étrange qu'il n'y a aucune leçon pratique à tirer.
Parallèlement à l'analyse des défaillances, une évaluation de la criticité est effectuée. Lorsqu'elle est combinée avec la cascade structurée d'équipements, de sous-composants et de modes de défaillance, une évaluation de la criticité aidera à déterminer jusqu'à quel point l'équipe d'analyse doit être détaillée dans l'attribution des actions correctives. La criticité doit être définie par une combinaison du prix de réparation ou de remplacement, du coût de la main-d'œuvre pour la réparation ou le remplacement et l'effet du temps d'arrêt sur le système ou l'usine dans son ensemble.
Dans le monde Lean/Six Sigma, l'accent a été mis sur la réduction des stocks et la livraison juste à temps des produits ou du matériel pour économiser sur les coûts de stockage. L'application d'une analyse de criticité à votre système vous permettra de voir quelles machines ou composants ont besoin d'être remplacés sur étagère et lesquels peuvent se permettre d'être commandés au fur et à mesure. Cela permet également de décider combien de temps une machine défaillante peut être autorisée à fonctionner dans cet état.
Considérez une machine qui nécessiterait l'arrêt de l'ensemble du système mais qui pourrait être réparée en deux jours avec une pièce déjà en main plutôt que d'utiliser ce même système à 90 % jusqu'à la fin du mois en attendant l'arrivée d'une machine de remplacement pouvant être échangés instantanément. Une efficacité de 90 % semble être la voie à suivre, mais l'utilisation complète du système pendant 28/30 jours est supérieure à 93 %, une augmentation non négligeable de la production de l'usine pour cette période. Une évaluation approfondie de la criticité aidera à répertorier ces types d'actions à pondérer par rapport à la liste d'actions correctives éventuelle.
Action corrective
L'action corrective la plus simple à lister pour chaque instance de défaillance consiste à remplacer le composant défaillant. Un peu plus complexe est de le réparer. Répertoriez librement toutes les actions correctives possibles pour chaque panne, mais ajoutez également un montant en dollars qui prend en compte à la fois la pièce et la main-d'œuvre nécessaires pour réparer ou remplacer. Des ordres de travail pré-écrits peuvent être écrits pour les deux cas et stockés dans la GMAO pour une utilisation en cas de défaillance.
Une action corrective possible qui peut être répertoriée peut être « courir jusqu'à l'échec ». Il n'existe pas de véritable solution universelle pour prévenir ou corriger chaque mode de défaillance, mais l'application du principe de Pareto produira une liste d'activités et d'actions facilement gérées qui peuvent être appliquées rapidement. En d'autres termes, on découvrira probablement que la plupart des problèmes chroniques affectant un système proviennent d'une liste de défauts plus petite et gérable et peuvent être corrigés par une liste tout aussi gérable d'actions de suivi.
Système
La partie la plus importante de FRACAS est qu'il est maintenu en tant que système. La répétabilité de ce processus est vitale pour ajouter des systèmes supplémentaires, de nouveaux équipements, des technologies émergentes et même du nouveau personnel dans l'usine. Ayez un plan pour examiner l'efficacité des actions correctives et amenez de nouveaux membres dans le groupe d'analyse pour aider à mettre en lumière toute zone de l'usine qui ne semble pas montrer d'amélioration marquée de la disponibilité.
Une autre partie systématique de ce processus réside dans l'éducation des autres membres de l'usine. Cela augmente l'appropriation du processus pour le personnel non impliqué dans l'analyse initiale et peut être un événement de construction de la culture. Former d'autres personnes au début du processus les aide à voir que le processus est impartial et qu'il est également ouvert à l'intégration de leurs idées.
L'échec est aléatoire, mais dans la plupart des cas, il peut être détecté, retardé ou totalement évité grâce à une approche systématique. La collecte et l'examen des données par le personnel expérimenté de l'usine sont essentiels, tout comme la détermination d'un montant en dollars pour chaque action ou résultat possible afin de guider le processus correctif éventuel. L'application méthodique de ces méthodes au fil du temps, ainsi que l'enseignement des principes de base du processus aux autres membres de l'équipe, contribueront à améliorer la culture et à augmenter la fiabilité globale des actifs. N'oubliez pas que vous voulez avoir un FRACAS, pas un fracas.
Entretien et réparation d'équipement
- Le cas de la maintenance mobile :Fiix s'arrête au podcast Asset Reliability @ Work
- Quel est le rôle de l'ingénieur fiabilité ?
- La clé n°1 du succès de la fiabilité
- RH :le chaînon manquant vers la fiabilité
- Le côté non technique de la fiabilité
- L'importance des tendances en matière de fiabilité des moteurs électriques
- La valeur de la fiabilité en tant que service
- Le système secret qui soutiendra l'ensemble de l'industrie de l'IoT
- Comment l'IIoT améliore-t-il la viabilité d'un système de surveillance des actifs ?