La formule parfaite pour aligner les opérations et la maintenance
Lorsque les opérations et la maintenance ne fonctionnent pas bien ensemble, cela peut être coûteux. Et en désordre. Prenez cette histoire d'un fabricant de produits alimentaires comme exemple.
L'installation utilise un laminoir, qui roule d'énormes boules de pâte. Le laminoir doit être nettoyé tous les jours. L'équipe de production nettoie régulièrement la machine à l'eau. Il n'y a qu'un seul problème avec cela :l'eau fait s'agglutiner la pâte et casser la machine. En conséquence, l'entretien d'urgence est la norme.
Si cette situation vous semble familière, vous n'êtes pas seul. Cela arrive des milliers de fois par jour. Les opérations et la maintenance ont des objectifs, des motivations et des processus différents. Le résultat est la confusion, la frustration et le doigté. Ce n'est pas bon pour la santé des entreprises ou des employés.
Cet article a pour but d'apprendre à briser ce cycle et à améliorer l'alignement entre les opérations et la maintenance, notamment :
- Métriques à partager
- Comment augmenter la collaboration
- Conseils pour créer des processus communs
Pourquoi l'alignement des opérations et de la maintenance devrait être votre priorité absolue
Tout fabricant qui s'efforce de réduire les déchets est soit en tête du peloton, soit sur le point de s'éloigner du terrain. Pour preuve, ne cherchez pas plus loin que le fait que les fabricants gaspillent 20 % de chaque dollar qu'ils dépensent.
Des déchets apparaissent souvent pendant la production, comme le soulignent ces statistiques effrayantes (avec l'aimable autorisation d'automation.com) :
- Les grandes installations industrielles perdent plus de 323 heures de production par an en raison d'arrêts imprévus
- Le coût annuel moyen des temps d'arrêt est de 532 000 $ par heure ou de 172 millions de dollars par usine
- Le coût des temps d'arrêt pour les fabricants Fortune 500 est égal à 8 % des revenus annuels
Les coûts énormes sont une chose. Mais les retards de travail, la maintenance réactive et les achats d'urgence ont également un impact mental et physique.
L'amélioration de la relation entre l'exploitation et la maintenance est essentielle pour réduire les temps d'arrêt à la source.
« Lorsque la maintenance et les opérations sont alignées, cela permet à l'entreprise de détecter les problèmes au sein des opérations », explique Jason Afara, ingénieur de solutions senior chez Fiix.
« Et ensuite, les chefs d'entreprise peuvent prendre des décisions éclairées sur la façon de corriger ces problèmes avec les ressources appropriées. Cela transforme les jeux de devinettes et les jeux de blâme en un effort unifié. »
Où aligner les processus d'exploitation et de maintenance
Planification des temps d'arrêt programmés
La définition d'une maintenance efficace est de maintenir l'équipement opérationnel avec le moins de temps d'arrêt possible. Bien sûr, c'est plus facile à dire qu'à faire. L'équipe de production a des quotas à remplir. Tout ce qui empêche d'atteindre cette cible est une menace. Cela inclut la maintenance.
"Nous combattions les opérations juste pour obtenir un peu de maintenance sur une machine", explique Jason, se souvenant de son temps en tant que responsable de la maintenance.
Tout cela est trop courant et improductif. Heureusement, il existe deux manières pour la maintenance et les opérations de créer un plan de maintenance préventive qui profite aux deux groupes :
- Utilisez les données pour comparer l'impact de la maintenance à l'impact d'une panne
- Développer des processus partagés qui réduisent le temps d'arrêt planifié
La première étape consiste pour les deux équipes à comprendre comment leurs activités affectent les performances des équipements. Encore une fois, c'est souvent plus compliqué qu'il n'y paraît.
« C'est là que les services de maintenance échouent généralement », explique Charles Rogers, consultant principal en implémentation chez Fiix avec plus de 33 ans d'expérience dans la maintenance.
« Ils n'ont pas de données pour étayer leurs demandes. Vous devez être en mesure de prouver votre cas et de prouver que si vous ne faites pas la maintenance dans les délais, les conséquences seront bien pires à un moment donné, probablement plus tôt que plus tard. »
La meilleure façon d'aligner vos efforts est de déterminer le risque acceptable et les conséquences d'un échec en tant qu'équipe. Partagez des informations sur les modes de défaillance courants, la fréquence à laquelle ils devraient se produire, ainsi que les délais et les coûts de réparation pour chacun. Comparez cela à la fréquence de la maintenance planifiée, au temps qu'il faut pour effectuer ces tâches et aux coûts impliqués.
Quantifier la différence montre clairement que planifier des interruptions fréquentes de la production pour la maintenance est un meilleur moyen pour les deux équipes d'atteindre leurs objectifs et d'éviter les pannes importantes et chronophages.
Utilisez ce modèle AMDEC pour calculer le risque de panne et prioriser la maintenance
La création de processus partagés entre l'exploitation et la maintenance permet aux équipes de partager et d'agir sur les données. Par exemple, il permet aux opérateurs de détecter les petites pannes et aux techniciens de maintenance d'y répondre plus rapidement. Voici des exemples de ces processus :
- Réunions régulières entre les responsables des opérations et de la maintenance pour discuter des calendriers de production et de maintenance préventive, des modifications des spécifications des machines ou d'autres mises à jour
- Réunions trimestrielles entre les deux équipes pour discuter des réussites, des défis, des solutions et de l'analyse des causes profondes
- Un processus de demande de travail qui permet aux opérateurs de machines d'identifier rapidement et en toute confiance les problèmes et aux techniciens de hiérarchiser et de résoudre les problèmes avec un minimum de perturbations
Créer un travail partagé et des responsabilités claires
Toute mention d'opérations et de maintenance travaillant ensemble conduira inévitablement à parler de maintenance productive totale (TPM). Vous pouvez lire une brève introduction sur la TPM ici, mais l'idée est que tout le monde dans une entreprise (des techniciens aux comptables) est responsable et impliqué dans la maintenance.
Intégrer les opérations au processus de maintenance est l'un des moyens les plus simples et les plus efficaces de commencer à créer un programme TPM. Voici un exemple de la façon dont cela pourrait être fait :
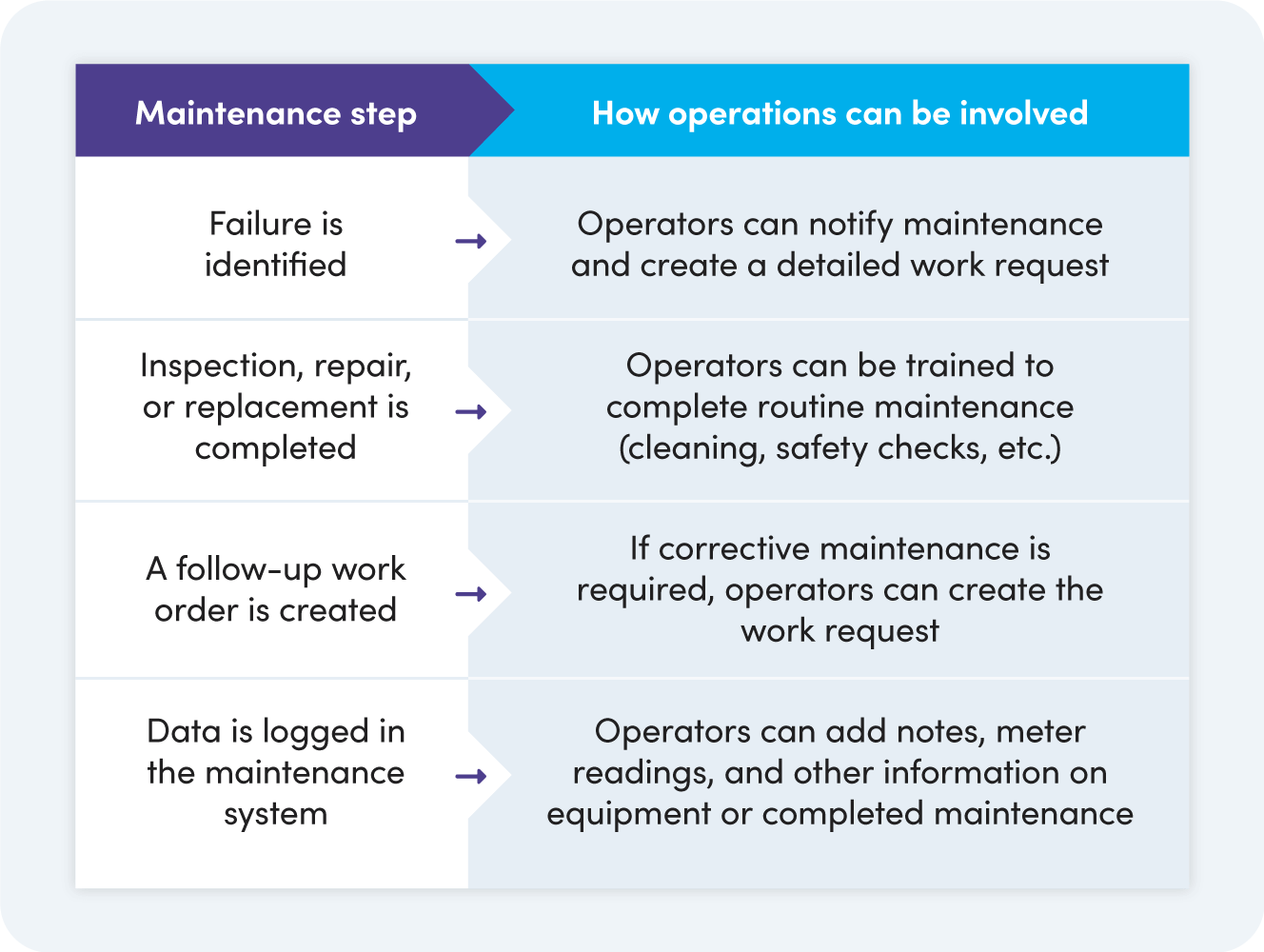
12 façons d'utiliser les bons de travail pour démarrer votre programme TPM
La clé du succès de ces processus partagés est de créer des responsabilités professionnelles claires. Lorsque les gens savent exactement ce qu'ils doivent faire, cela vous aide :
- Fournir la bonne formation et les bons supports aux bonnes personnes
- Créer des calendriers et des budgets précis
- Testez de nouveaux processus, optimisez-les et développez-les
- Recherchez les mauvaises données et déterminez leur cause
Commencez à définir des responsabilités claires en créant un type de maintenance pour les opérateurs. Cela vous permet de suivre la quantité de travail que vous consacrez aux opérations. Il vous aide également à concevoir des modèles d'ordre de travail pour les opérateurs afin qu'ils sachent quoi faire et où aller si la portée du travail change.
Créer des échéanciers de travail réalistes
Lorsque les opérations et la maintenance savent combien de temps il faut pour faire avancer les choses, il est plus facile de définir des calendriers, des budgets et des objectifs en conséquence. Cela évite également les retards imprévus, réduit la frustration et favorise le respect entre les deux équipes. Mais il n'est pas utile de partager des calendriers de maintenance s'ils ne sont pas précis. Il existe quelques stratégies pour s'assurer que les attentes correspondent à la réalité :
- Consultez les journaux de maintenance des équipements. Identifiez les tâches qui prennent souvent plus de temps que prévu et ajustez les délais en conséquence.
- Analysez les données de vos ordres de travail pour trouver des MP avec un taux élevé de maintenance de suivi requis. Tenez-en compte dans votre briefing à l'équipe des opérations.
- Comptabiliser les parties d'un ordre de travail qui se situent en dehors du temps réel de la clé. Cela comprend la récupération de pièces, l'exécution de procédures de sécurité et l'exécution de tests sur les machines.
Fournir des délais réalistes ne signifie pas toujours que vos horaires correspondent. Mais cela aide les opérations et la maintenance à discuter de ce qui peut être fait dans le temps dont vous disposez. Pour déterminer quelle maintenance peut être sacrifiée pour la production, voici quelques questions à poser :
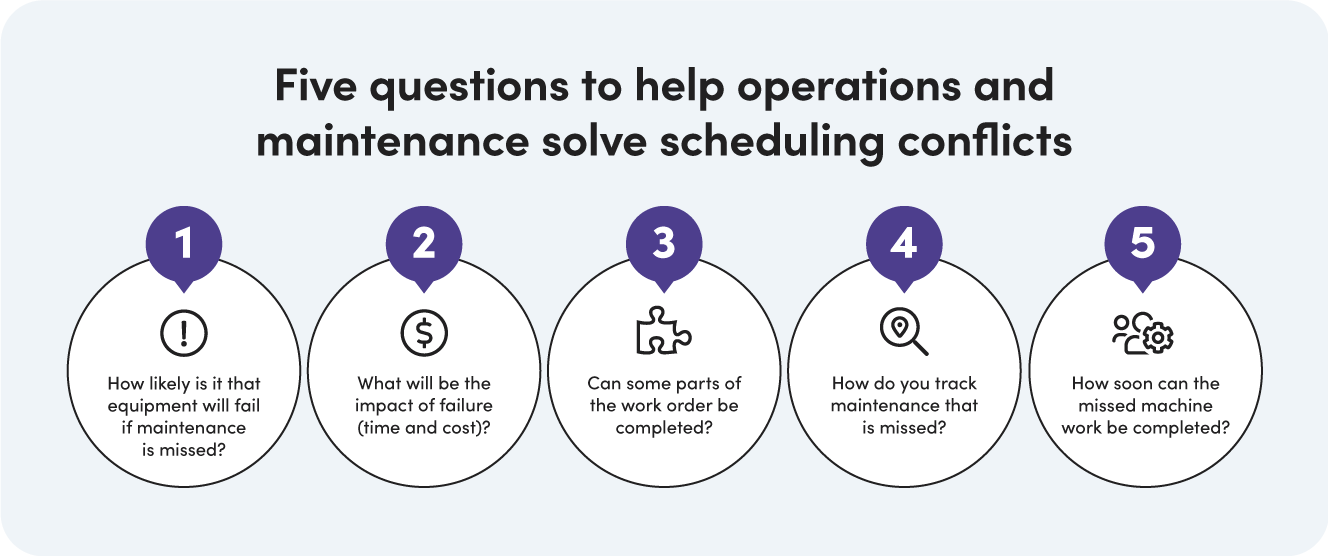
Cinq façons d'établir une relation solide entre l'exploitation et la maintenance
Vos équipes d'exploitation et de maintenance pourraient être les meilleures amies. Ou peut-être y a-t-il une certaine tension entre eux. Quelle que soit la relation, il y a toujours une opportunité de l'améliorer avec quelques stratégies simples.
Créez plusieurs façons pour les deux équipes de communiquer
Communiquer avec d'autres équipes est souvent l'une des premières activités à abandonner lorsque le travail est chargé. C'est pourquoi des processus formels doivent être mis en place pour maintenir le flux d'informations. La création de canaux de communication dédiés peut inclure :
- Réunions d'équipe :les réunions régulières créent un espace pour que la voix de chacun soit entendue et pour garder les défis, les plans et les mises à jour visibles
- Canaux pour publier et voir les mises à jour :il peut s'agir de n'importe quoi, d'un tableau blanc à un groupe WhatsApp, ou d'un portail de demande de travail numérique pour suivre l'état des demandes
- Évaluations par les pairs :il s'agit d'un processus au cours duquel les membres des équipes d'exploitation et de maintenance s'examinent mutuellement de manière anonyme pour déterminer comment ils peuvent mieux travailler ensemble
Il y a quelques informations clés à discuter lorsque vous travaillez dans ces canaux :
- Mises à jour des machines :indiquez les modifications apportées aux spécifications, les problèmes potentiels, les risques pour la sécurité ou les mises à jour des procédures d'exploitation standard
- Calendriers :Parlez des travaux à venir, des risques ou des conflits, de ce qui est nécessaire pour réussir et de tout changement par rapport à ce qui a été discuté précédemment
- Rapports :examinez les objectifs, les progrès, les tendances inquiétantes ou les principales réussites de vos rapports
- Barrières et solutions :discutez des principaux défis ou questions de votre équipe et collaborez pour trouver des moyens de supprimer ces obstacles
- Planification à long terme :découvrez comment les deux équipes peuvent s'améliorer en permanence, notamment comment mieux gérer les budgets, atteindre les objectifs à long terme et développer de nouvelles compétences
Disposer d'un cadre de communication entre l'exploitation et la maintenance vous permet de transformer la parole en action. Voici quelques règles de base :
- Concentrez-vous sur les solutions, pas sur le blâme :trouver une solution doit être l'objectif de toutes vos conversations
- Concentrez-vous sur le collectif :trouvez des solutions qui fonctionnent pour tout le monde, au lieu d'essayer de gagner un argument ou une bataille pour votre équipe
- Développez une boucle de rétroaction :créez la confiance en agissant sur les commentaires et en tenant tout le monde au courant des progrès
- Valorisez la cohérence, mais restez flexible :engagez-vous à communiquer, mais comprenez que les réunions peuvent avoir besoin de se déplacer de temps en temps en cas d'urgence
- Créez un ordre du jour pour toutes les réunions :ayez un plan pour ce dont vous allez parler afin de tirer le meilleur parti du temps de chacun
Définir les mêmes objectifs
Il y aura moins de frictions entre les opérations et la maintenance lorsque les deux équipes définiront le succès de la même manière. Il peut y avoir des idées différentes sur la façon d'atteindre votre objectif, mais les deux départements iront dans la même direction.
« Dans le pire des cas, ces départements sont des frères et sœurs qui se battent constamment », explique Jason.
"Mais dans le meilleur des cas, vous travaillez ensemble pour atteindre les mêmes objectifs, célébrez ensemble lorsque vous atteignez ces objectifs et unissez vos forces pour revenir sur la bonne voie lorsque vous ne les atteignez pas.
Il existe quelques mesures dont les opérations et la maintenance peuvent partager la responsabilité :
- Démarrages propres après maintenance et rendement au premier passage/premier passage bon :les deux chiffres visent à mesurer l'efficacité et le gaspillage
- Coût total par unité de production :les opérations et la maintenance peuvent être responsables de la réduction des coûts tout en améliorant la qualité
- Temps passé à soutenir la production/la maintenance :le suivi du temps que chaque équipe passe à soutenir l'autre vous aidera à allouer des ressources et à créer des plans de recrutement efficaces
- Temps d'arrêt imprévus (90 derniers jours) :découvrez l'impact de la maintenance préventive et les processus partagés qui rendent ce travail efficace
- Délai moyen de détection et de réparation :tout le monde a un rôle à jouer dans la détection et la résolution des pannes avant qu'elles ne conduisent à des pannes, et ce en perturbant le moins possible l'activité
Utilisez ce modèle pour créer des objectifs partagés entre les opérations et la maintenance
Intégrer les systèmes de production et de maintenance
Il est facile pour les opérations d'avoir une vision négative de la maintenance lorsque leur seule exposition à celle-ci est une panne ou une interruption de service. L'intégration des systèmes utilisés pour la production et la maintenance offre une visibilité sur le travail de chaque équipe. Cela vous permet de voir l'impact positif de chaque service et de vous aider mutuellement à accomplir encore plus.
L'équipe de maintenance de Ryan Robinson est un excellent exemple de la façon dont l'intégration d'un logiciel de maintenance avec des équipements et des systèmes de production peut produire des résultats incroyables. Ryan, le gérant du magasin d'un grossiste en arboriculture, a connecté des capteurs sur plusieurs machines avec une GMAO. Cela lui a donné les données dont il avait besoin pour optimiser les intervalles de maintenance et augmenter l'efficacité de la production.
« Parce que nous savons comment l'équipement est utilisé au quotidien, nous avons une idée de ce que l'on attend de la maintenance demain, le lendemain et le lendemain », explique Ryan.
Ryan a également pu utiliser ces données pour repérer les véhicules avec des temps de ralenti élevés. Il a apporté cette information au gestionnaire de la ferme, qui a compris la raison et trouvé une solution.
Lire l'histoire de Ryan
Les équipes de maintenance de classe mondiale sont alignées sur les opérations
Les opérations et la maintenance sont le cœur de toute entreprise avec de nombreux actifs et de grands objectifs de production. C'est pourquoi il est essentiel qu'ils développent une relation saine et des processus formels pour travailler ensemble. Les deux équipes doivent tout partager, des métriques qu'elles visent aux systèmes qu'elles utilisent, en passant par le calendrier qui guide leur travail. Unir leurs forces leur donne une meilleure visibilité sur les défis auxquels l'entreprise est confrontée et le pouvoir de les surmonter. C'est une situation gagnant-gagnant pour toutes les personnes impliquées.
Entretien et réparation d'équipement
- Stylo et papier vs logiciel de maintenance :la meilleure méthode pour réduire les temps d'arrêt
- Naviguer dans la modernisation de la maintenance et de la gestion des installations
- Quel est le remède à la maintenance imprévue ?
- Partager la responsabilité de la réalisation de la maintenance préventive
- Une leçon de conduite pour les opérations et la maintenance
- Le besoin d'une planification de la maintenance
- L'effort multi-compétences pour la maintenance
- 5 règles d'exploitation et de maintenance en partenariat
- Lockheed Martin a attribué un contrat d'exploitation et de maintenance