Experts :une automatisation accrue essentielle pour répondre à la demande d'avions
Les seuls besoins commerciaux au cours des 20 prochaines années suggèrent un doublement des taux de production
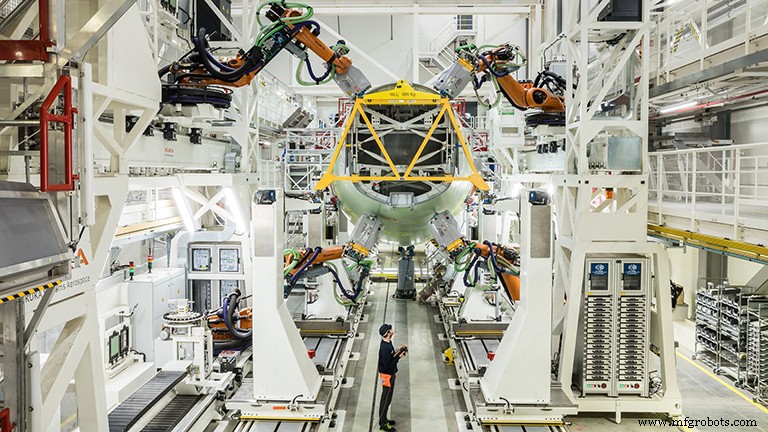
Avant que la pandémie de coronavirus ne bouleverse la vie normale et ne ferme essentiellement les avions de ligne commerciaux, l'industrie aéronautique avait un besoin prévu de 40 000 nouveaux avions - avions, hélicoptères, taxis aériens et véhicules aériens sans pilote - au cours des 20 prochaines années. Le volume comprend les remplacements d'embarcations qui vieillissent hors service après une durée de vie moyenne de 25 à 30 ans et s'ajoute à un arriéré d'environ huit ans.
Si la demande de vols reprend son niveau antérieur une fois les restrictions liées à la pandémie assouplies, la seule façon de satisfaire le besoin prévu est d'augmenter l'automatisation, ont déclaré certains experts du secteur.
Contrairement à de nombreux autres secteurs, l'industrie aéronautique est celle où le travail manuel est courant car il n'existe actuellement aucun processus de fabrication alternatif réalisable. Mais compte tenu de l'enregistrement par Statista des augmentations d'une année sur l'autre de la demande de 2006 à 2019 pour la demande mondiale de passagers du trafic aérien (les augmentations allaient de 2,4% à 8,1%, sauf pour 2009 au plus fort de la Grande Récession) et d'autres facteurs, une plus grande efficacité est obligatoire si l'industrie veut suivre.
Les chercheurs tentent de comprendre comment automatiser certains processus, tels que la pose des mains. Mais il existe d'autres mesures automatisées actuellement disponibles, notamment la projection d'instructions pour l'assemblage sur les postes de travail et pour les processus automatisés de scellement, de fixation, de marquage et de manutention.
Les seuls besoins de l'aviation commerciale nécessiteraient un doublement effectif des taux de production, a déclaré John D. Russell, chef de la branche de la technologie des structures au Laboratoire de recherche de l'armée de l'air.
En plus des avions commerciaux, l'armée explore des avions attritables qui pourraient être produits par milliers.
Enfin, le concept de taxi aérien gagne du terrain auprès des compagnies d'aviation traditionnelles et des entreprises comme Uber et nécessiterait encore plus de production.
"Pour chacun de ces cas individuellement, j'entends de mes contacts dans l'industrie que les États-Unis n'ont pas la capacité actuellement", a déclaré Russell, avertissant que ses informations datent d'avant que le virus ne frappe le monde. "Si les trois se réalisent en même temps, l'industrie devra faire preuve de créativité pour résoudre le problème de capacité.
"La grande alternative que j'entends est l'utilisation de l'automatisation pour augmenter la productivité et le débit, en particulier pour l'aviation commerciale. Les entreprises étudient toutes les manières dont l'automatisation peut améliorer les choses, de la fabrication de pièces à l'assemblage. J'entends dire que les dépenses en capital pour l'automatisation sont inférieures à celles nécessaires pour ajouter de nouvelles lignes de production."
Russell a déclaré qu'il ne serait pas surpris de voir l'industrie du taxi aérien se tourner vers la production à l'étranger, car le prix des véhicules est susceptible d'être un facteur important pour leur modèle commercial. Il doute que nous assistions à une délocalisation pour l'aviation commerciale, car l'industrie serait susceptible de s'en tenir aux relations établies avec les fournisseurs en raison du niveau de compétence élevé de la main-d'œuvre. De toute évidence, la délocalisation ne serait une option pour aucun véhicule militaire, a-t-il noté.
Livrer 40 000 avions en 20 ans nécessiterait de produire 2 000 avions par an, ce qui est bien plus que les livraisons avant la pandémie.
Un arriéré de livraisons a été créé lorsque les fabricants n'ont pas pu s'équiper assez rapidement pour répondre à la demande accrue créée par une augmentation du transport aérien.
De plus, les consommateurs considèrent désormais les voyages en avion comme une nécessité plutôt qu'un luxe et ont les moyens de payer leurs déplacements personnels.
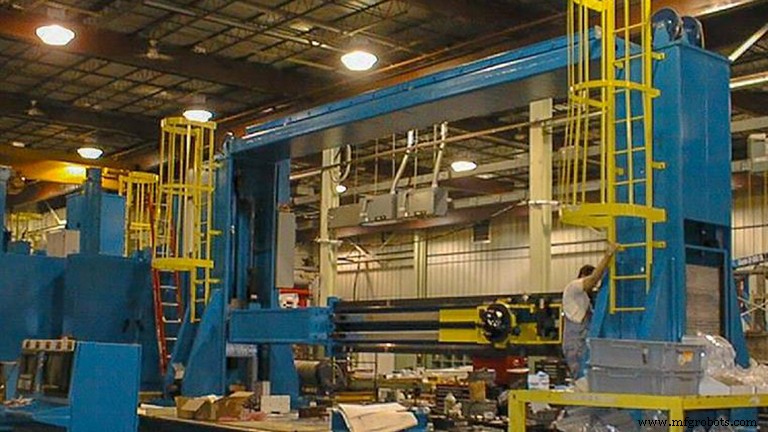
En conséquence, les compagnies aériennes commerciales ont élargi leurs offres pour offrir aux consommateurs avides de vols une flexibilité dans les heures de décollage.
Boeing avait un carnet de commandes de 5 049 appareils au 1er mai, tandis que les commandes en souffrance d'Airbus s'élevaient à 7 650 au 31 mars.
Avant la pandémie, une reprise de la concurrence entre Boeing et Airbus devait entraîner une livraison record de leurs plates-formes à fuselage étroit très populaires et une croissance de 9,4 % de la production en glissement annuel en 2019. Boeing et Airbus devaient produire plus plus de 1 750 avions l'an dernier, contre 1 606 unités en 2018, selon un communiqué de presse publié à la mi-juin 2019 par la société de recherche et d'analyse Frost &Sullivan.
En août, cependant, d'autres réduisaient ces chiffres.
La production mondiale d'avions avait chuté d'un quart après l'échouement du jet 737 Max de Boeing en mars 2019 à la suite de deux accidents mortels, selon un article du journal The Guardian. ADS, le groupe de pression britannique de l'aérospatiale, a déclaré que 88 avions avaient été livrés en juillet 2019, en baisse de 24% par rapport aux livraisons du même mois de l'année précédente, la chute étant largement due à la baisse de la production d'avions monocouloirs comme le 737. /P>
À la fin de l'année dernière, Airbus et Boeing avaient livré ensemble 1 243 appareils.
L'industrie agit pour augmenter ces chiffres.
"Les deux plus grands constructeurs d'avions commerciaux, Boeing et Airbus, investissent tous deux beaucoup d'argent supplémentaire pour augmenter le taux de production", a déclaré Bill Bigot, vice-président du développement commercial pour l'aérospatiale et la défense chez JR Automation.
À la fin de l'année dernière à Hambourg, en Allemagne, Airbus a mis en place sa chaîne d'assemblage hautement automatisée de la structure du fuselage de la famille A320.
La nouvelle installation comprend 20 robots, un nouveau concept logistique, un positionnement automatisé par mesure laser, ainsi qu'un système d'acquisition de données numériques, a indiqué la société.
Outre l'utilisation de robots, Airbus met également en œuvre de nouvelles méthodes et technologies dans la logistique des matériaux et des pièces pour optimiser la production, améliorer l'ergonomie et raccourcir les délais. Cela comprend la séparation des niveaux de logistique et de production, le réapprovisionnement en matériel axé sur la demande et l'utilisation de véhicules guidés autonomes.
À peu près à la même époque, cependant, Boeing a mis fin à un effort d'automatisation total de quatre ans dans son usine d'Everett, Washington, qui utilisait des bras robotiques pour insérer des fixations sur deux sections principales du fuselage de ses avions de ligne 777 et du 777X, optant plutôt pour l'insertion manuelle par mécaniciens qualifiés.
Selon des rapports publiés, des robots forent toujours les trous pour les attaches sur un système automatisé de "voies flexibles", ce qui entraîne une combinaison de processus humain et robotique.
L'effort peut cependant être payant à la fin.
L'échec des efforts d'utilisation de la robotique a enseigné à Boeing quelques leçons précieuses de sa "première plongée très profonde dans ce type de technologie", a déclaré Jason Clark, vice-président de Boeing supervisant la production du 777X, au Los Angeles Times. "Cela nous a appris à concevoir pour l'automatisation", a déclaré Clark dans un article de novembre.
La nouvelle méthode crée moins d'usure pour les travailleurs puisque les machines développées par Electroimpact Inc. gèrent l'une des tâches les plus exigeantes physiquement de l'assemblage du fuselage :percer des trous dans le métal, selon l'article du Times.
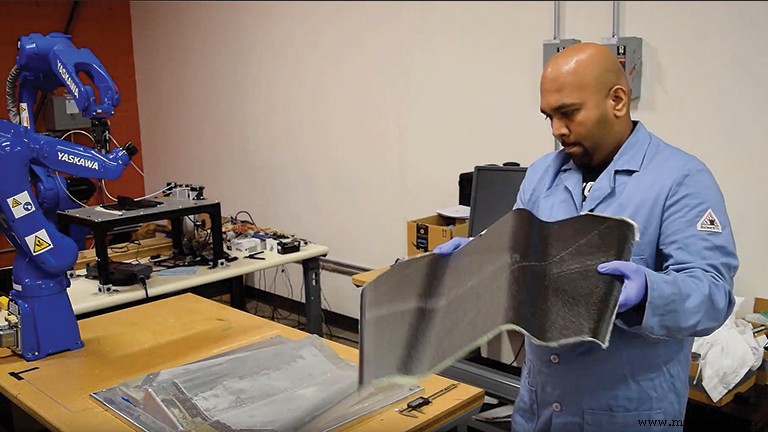
De plus, "Nous avons repensé des parties de la construction pour remplacer les rivets par des formes de fixations moins difficiles, améliorant encore l'ergonomie", a déclaré un porte-parole de l'entreprise.
Toutes les mesures visant à augmenter la production n'incluent pas de nouvelles lignes et de nouveaux robots.
Dans son usine de North Charleston, S.C., Boeing :a équipé les mécaniciens d'exosquelettes conçus pour réduire les contraintes liées aux travaux aériens soutenus; déployé des clés intelligentes compatibles Bluetooth pour s'assurer que les travailleurs appliquent le bon couple à un écrou et utilisent la réalité virtuelle pour que les mécaniciens testent de nouveaux outils, selon Reuters.
Les robots peuvent-ils prendre en charge la pose des mains ?
Avant que les structures de fuselage ne soient expédiées à Hambourg ou aux usines de Boeing dans l'État de Washington, elles sont fabriquées selon des processus de fabrication composite automatisés (ACM), y compris le placement automatisé des fibres et la pose automatisée des bandes.
L'ACM convient aux pièces moyennes ou grandes comme les fuselages, les ailes et les cloisons qui sont également plates ou légèrement profilées.
Mais les petites et moyennes pièces composites sont fabriquées à la main, un processus très inefficace qui gaspille beaucoup de matière.
C'est un gros problème car ces pièces (clips, supports, poutres en I et portes d'accès) peuvent représenter jusqu'à la moitié du poids d'une structure et se compter par milliers pour un seul avion.
"De plus, ces pièces qui doivent être posées à la main doivent être coupées et fléchées, pressées, qu'est-ce que vous avez", a déclaré Les Cohen, un consultant en composites. "Cela signifie donc que votre rapport achat-vol peut être un facteur de 2 :si vous travaillez avec un matériau qui coûte 40 $ la livre, il s'agit en fait d'un matériau à 80 $ la livre."
Une équipe de l'Université de Californie du Sud a récemment terminé un projet de démonstration pour automatiser le drapage avec des bras robotiques.
Bien qu'il n'y ait pas d'automatisation, il est encore possible d'améliorer les matériaux utilisés dans la construction des avions.
L'industrie comprend que le temps qu'il faut pour stériliser à l'autoclave les pièces en cours dans les opérations de réduction de masse toutes les quelques couches ainsi que le durcissement de la pièce finale prend beaucoup de temps. Les résines à durcissement rapide qui ont les propriétés des pièces durcies en autoclave mais sans le processus d'autoclave sont la réponse, mais elles ne sont pas disponibles, a déclaré Cohen. Avec des investissements pouvant atteindre cinq ans en moyenne et des coûts estimés à 10 millions de dollars pour développer de nouveaux matériaux, sans aucune garantie qu'ils seront acceptés, il est compréhensible que ce défi ne soit pas relevé, a-t-il déclaré.
La 4e révolution industrielle tarde à décoller dans l'aérospatiale
L'industrie 4.0, avec sa promesse d'une productivité et d'une qualité accrues, pourrait également contribuer à stimuler la production aéronautique, mais l'industrie a mis du temps à adopter le monde connecté, numérisé et axé sur les données de la quatrième révolution industrielle.
"Je dirais que ce matériel est en train d'être mis en ligne maintenant en production et donne des résultats. Nous sommes très impliqués et nous sommes juste au point où nous pouvons déployer cela au niveau du programme et vraiment donner quelque chose à une usine qui affectera absolument son efficacité », a déclaré Andrew Purvis, chef de projet pour la stratification et l'automatisation des composites. chez Electroimpact Inc. "Lorsque vous commencez à obtenir les données et que vous commencez à calculer les chiffres, vous commencez à trouver beaucoup d'or dans cette montagne de données et souvent des diamants, des choses qui commencent vraiment à augmenter votre production."
Le côté qualité de la production est mûr pour l'automatisation, a déclaré Purvis.
Electroimpact intègre la surveillance de la qualité dans des systèmes dotés d'une technologie d'inspection qui mesure tout ce que ses machines AFP font lorsqu'elles fabriquent ou impriment une pièce. L'inspection automatique active un processus que l'entreprise appelle "réglage continu".
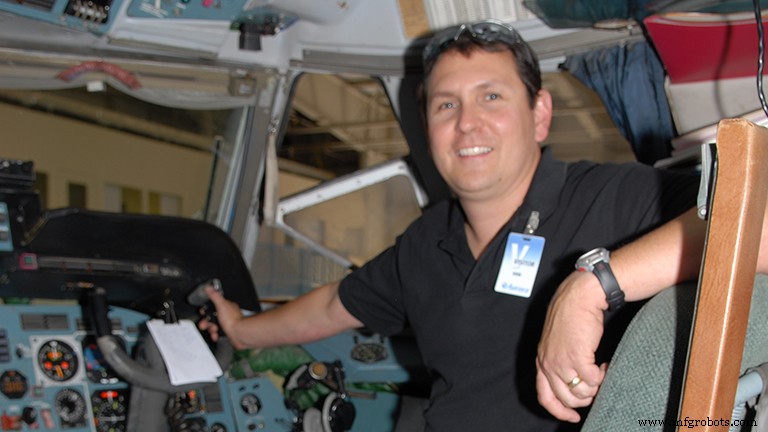
"Le système se maintient en fait en calibrage en surveillant ce qu'il fait, et il s'ajuste en permanence", a-t-il déclaré. "Comme une machine AFP ou une imprimante peut regarder la sortie avec un appareil photo ou des capteurs et dire" Hé, j'ai remarqué que vous commencez à dériver un peu, donc je vais compenser "."
À ce stade, l'adoption de l'industrie 4.0 est plus une aspiration qu'un accomplissement, en partie en raison des implications en matière de cybersécurité et de gestion des données, a déclaré Mick Maher, président de la société de conseil Maher Associates.
"Je ne pense pas que l'industrie aérospatiale se redresse plus lentement que toute autre industrie", a-t-il déclaré. "Je pense que l'industrie 4.0 est encore trop immature pour lui céder les rênes à ce stade. Cela dit, l'automatisation est un élément clé de l'Industrie 4.0. Mais tout comme certaines parties de l'automatisation sont matures, comme le placement des bandes, le placement des fibres, il reste encore beaucoup de développement à faire."
Gros gains à réaliser
Randy Rounkles, qui a été directeur technique pour l'aérospatiale chez JR Automation, était auparavant chez Spirit Aerosystems où il faisait partie d'une équipe chargée de déployer l'Industrie 4.0 début 2019.
La production cible héritée de Spirit, une ancienne usine de Boeing qui a été cédée en 2005, était de 21 avions par mois en raison de ses limites physiques et de sa taille, a déclaré Rounkles. Avant son départ, la production mensuelle de l'usine était de 57 avions, aidés par des équipes supplémentaires, plus d'employés et une automatisation accrue, en particulier dans la fixation.
"L'un des (derniers) projets avant mon départ était la collecte de données de l'industrie 4.0 sur l'utilisation de l'équipement et cela a en fait changé le visage de cette entreprise en comprenant ce que faisait son équipement et ce qu'il était capable de faire", a déclaré Rounkles. "Et cela a eu un impact significatif sur les dépenses en capital pour les tarifs futurs."
« Dabber dans le numérique »
Des recherches sont en cours dans le monde entier sur l'application de l'industrie 4.0 à la fabrication aérospatiale, mais l'adoption est lente et la production actuelle d'avions est plus analogique que numérique, a déclaré Russell de l'AFRL.
"Les entreprises se lancent dans le numérique pour résoudre des problèmes spécifiques, comme le suivi des actifs, mais peu de fabricants disposent d'un véritable environnement Industrie 4.0 à l'échelle de l'entreprise", a-t-il déclaré.
En ce qui concerne l'état actuel des composants de l'industrie 4.0, la fabrication additive est à l'étude pour l'outillage et les pièces non structurelles, certains processus sont automatisés avec l'utilisation de robots et, en ce qui concerne l'analyse des données, la R&D a été effectuée pour lier l'inspection non destructive données aux modèles d'origine pour comprendre l'impact des défauts de fabrication sur les performances des pièces, a déclaré Russell.
Dans la vidéo publiée sur YouTube, un bras robotique Kuka avec un rouleau en bout de bras lisse la couche de composite pré-imprégné sur la couche précédente tandis que deux robots avec des pinces maintiennent le matériau tendu de chaque côté.
Combien d'artistes du lay-up ont souhaité cet équivalent d'une troisième main qui a été démontré dans l'enregistrement de la cellule robotique intelligente ?
La cellule, et toute la technologie qui la sous-tend, est un projet de démonstration de Satyandra K. Gupta, professeur de génie mécanique et d'informatique à l'Université de Californie du Sud, de ses collègues et de ses étudiants. Ils ont réalisé la partie sur la base des suggestions de Boeing, Lockheed Martin et United Technologies, dans le but d'évaluer la faisabilité de l'automatisation. Les résultats des tests sur les pièces fabriquées avec leur automatisation robotique ont été envoyés aux trois sociétés, a déclaré Gupta.
"À l'heure actuelle, le principal défi auquel tout le monde est confronté dans l'aérospatiale est la pénurie de main-d'œuvre", a-t-il déclaré.
Avec des bras robotiques faisant du drapage, un opérateur humain pourrait superviser plusieurs cellules à la fois, a-t-il expliqué. Cela augmenterait non seulement la capacité, mais pourrait éventuellement éliminer l'étape de réduction du volume dans le processus de fabrication de pièces tout en garantissant la qualité.
En effet, pour une pièce critique hypothétique composée de 100 couches de pré-imprégné, la pièce en cours de traitement doit être ensachée et soumise à une application sous vide toutes les trois (ou cinq) couches pour s'assurer qu'il n'y a pas de vides, pour un total de 33 dégonflements.
Mais avec les robots, la pression de l'outil robotique peut être mesurée, contrairement à la main humaine, la qualité est donc assurée et le processus peut aller plus vite.
L'automatisation du processus ne le rend pas seulement cohérent et rationalisé. Le drapage des mains est un travail fastidieux et physiquement exigeant.
Travaillant pendant deux ans et demi, Gupta et son équipe ont intégré les bras robotiques avec des outils de bout de bras, la vision par ordinateur, la détection de force, des algorithmes d'intelligence artificielle, des contrôleurs avancés et une interface homme-machine. Leurs pièces de démonstration comprenaient jusqu'à 15 couches de plis pré-imprégnés en fibre de carbone standard à base d'époxy.
La partie la plus difficile de leur travail consistait à intégrer la vision par ordinateur en temps réel.
"Vous devez obtenir la caméra pour voir quels défauts se forment", a déclaré Gupta. « (Maintenant) si le robot voit un pli parfois il tirera la feuille de cette façon, puis de cette façon… »
Lorsque la cellule rencontre un problème qu'elle ne peut pas résoudre, elle alerte un opérateur humain avec un bip sonore, un e-mail ou un SMS.
Mais ce n'est que si nécessaire.
"Parfois, tout le processus se déroule sans accroc", a déclaré Gupta.
Écoute, maman, pas de mains ! (L'outillage en bout de bras effectue une mise en place automatisée du pré-imprégné)
L'ajout Rego-Fix ouvert il y a trois ans intègre des fonctionnalités avancées de conservation de l'énergie et des ressources naturelles. Il s'agit notamment d'un système spécial de ventilateur à échange d'air, d'un chauffage aux granules de bois, de plusieurs unités de climatisation progressives, d'un toit « vert » et de l'utilisation de l'éclairage naturel et contrôlé par des capteurs.
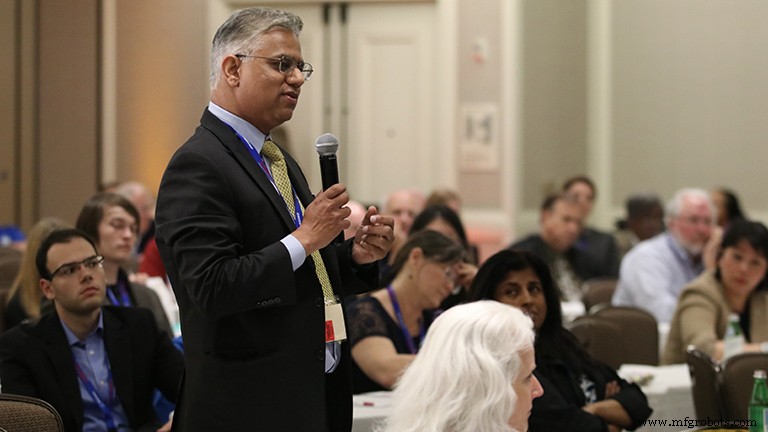
Le système de ventilation à échange d'air renouvelle l'air à l'intérieur du nouveau bâtiment sept fois par heure. Il extrait la chaleur résiduelle de l'atelier de fabrication, la chaleur générée principalement par les gros compresseurs d'air nécessaires aux machines-outils de l'entreprise. Pendant les mois froids, qui représentent le reste de l'année, la chaleur résiduelle récupérée est ensuite utilisée pour réchauffer l'air frais entrant que le système puise à l'extérieur du bâtiment et circule vers l'atelier de fabrication.
De plus, la circulation d'eau dans un système fermé aide à maintenir les compresseurs d'air de plancher de fabrication au frais pendant le fonctionnement. Dans le processus de refroidissement, l'eau devient chaude et cette eau chauffée est ensuite stockée dans un réservoir de 1849 gal (7007 l). Cette eau est utilisée pour réchauffer davantage le bâtiment via un système de chauffage intégré dans les sols des espaces de bureaux du bâtiment.
L'installation comprend également un système de chauffage de 390 kW qui brûle des granules de bois plutôt que des combustibles fossiles. Les granulés sont un sous-produit des industries du bois et de la fabrication de meubles, qui sont courantes dans la région. Le système consomme très peu de granulés car il fonctionne en secours des autres sources de chauffage et n'est utilisé que lorsque les températures extérieures sont extrêmement basses.
Pendant les étés, un système de climatisation à trois unités de type progressif à économie d'énergie fonctionnant avec le système dans le plancher et le système d'échange d'air, maintient l'addition fraîche. L'échangeur d'air extrait la chaleur du bâtiment et l'eau froide circule dans le système de plancher.
Si la température à l'intérieur du bâtiment dépasse un certain niveau, l'une des unités du système de climatisation progressive s'enclenchera en secours du plancher et de l'échangeur d'air. Les unités de climatisation sont régulées en régime, donc si les niveaux de température continuent d'augmenter, forçant la première unité de climatisation à dépasser sa limite, la deuxième unité de climatisation du système s'activera. Et à son tour, si la deuxième unité atteint sa limite de régime, la troisième unité est activée. Une fois que le bâtiment commence à refroidir, les unités de climatisation individuelles s'éteignent dans l'ordre inverse.
Les murs extérieurs du bâtiment sont complètement isolés. Contrairement aux conceptions de toit typiques, celle pour laquelle Rego-Fix a opté est assez inhabituelle avec des propriétés isolantes élevées. Considéré comme un toit «vert» ou «planté», il est recouvert d'un sol dans lequel pousse du gazon. En plus de sa valeur isolante, le toit capte l'eau de pluie qui est ensuite collectée dans un réservoir de 13 200 gal (50 000 l) et est utilisée pour la chasse d'eau des toilettes du bâtiment.
Combinées, toutes les caractéristiques de chauffage et de refroidissement du bâtiment fournissent des températures ambiantes stables et constantes dans la zone de fabrication. Cela a un avantage de fabrication critique. La température constante aide à maintenir une précision constante de la machine-outil pour produire les systèmes de porte-outils de haute précision de l'entreprise.
Pour plus d'économies d'énergie, le nouveau bâtiment de fabrication est doté de nombreuses grandes fenêtres isolées à triple vitrage qui laissent entrer une lumière naturelle abondante. De plus, les fenêtres sont équipées de stores qui s'ouvrent et se ferment automatiquement. C'est une aide majeure pour garder le bâtiment frais en été. Alors que les stores bloquent beaucoup de chaleur, ils sont perforés pour laisser entrer la lumière.
Lorsqu'un éclairage supplémentaire est nécessaire, des lampes à économie d'énergie de type LED, ainsi qu'une activation de la commande de mouvement, sont utilisées. Il n'y a pas d'interrupteurs muraux dans le bâtiment et les lumières s'allument uniquement lorsque les zones sont occupées, puis s'éteignent lorsqu'elles ne le sont pas.
Système de contrôle d'automatisation
- L'avenir de l'automatisation dans l'industrie aéronautique
- Comment l'automatisation perturbe tous les types de fabrication en 2020
- Le rôle de la robotique et de l'automatisation dans l'industrie 4.0
- Automatisation et industrie de la mode :une révolution tranquille
- L'automatisation dans l'industrie 4.0
- La demande mondiale de véhicules de tourisme chute de 11 %, selon une enquête
- STAEDTLER :la valeur de l'automatisation dans l'industrie manufacturière
- La demande d'automatisation, les robots augmentent
- Répondre au grand besoin d'automatisation des composites