Les tests de résistance d'isolement en continu augmentent la productivité du moteur
Pendant des décennies, le personnel de l'usine a effectué des tests de résistance d'isolement avec des mégohmmètres portables pour éviter les pannes de moteur qui entraînent des arrêts imprévus coûteux, des pénalités de non-production et des réparations de rembobinage. Cependant, ces tests ne fournissent qu'un « instantané » de la santé motrice. En quelques jours, les enroulements et les câbles du moteur exposés à l'humidité, aux produits chimiques, aux contaminants ou aux vibrations peuvent être compromis et tomber en panne au démarrage.
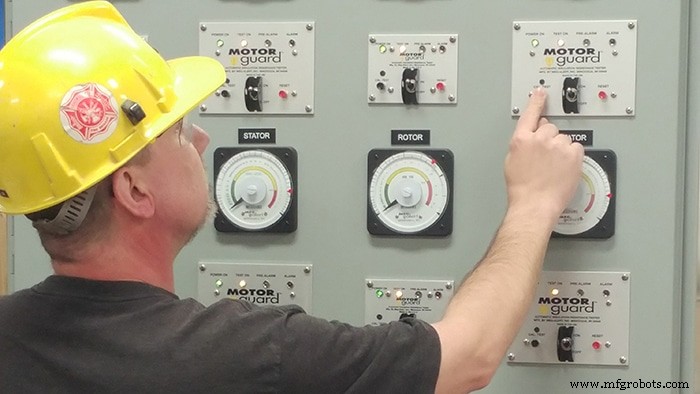
Les mégohmmètres portables exigent également que les techniciens en électricité déconnectent manuellement les câbles de l'équipement et connectent les cordons de test sur l'équipement potentiellement sous tension ou endommagé pour effectuer le test manuel. Ces tests exposent les techniciens à des arcs électriques potentiels lorsqu'ils accèdent à l'armoire. Aux États-Unis, des arcs électriques non mortels se produisent environ cinq à dix fois par jour, avec environ un décès par jour.
Avec autant de risques, les responsables d'usine reconnaissent la valeur de la surveillance continue en mégohms de la résistance d'isolement qui s'active dès que le moteur est éteint jusqu'à ce qu'il soit redémarré.
Fort de ces informations en temps réel, le personnel de maintenance peut prendre des mesures correctives à l'avance pour éviter une panne qui interromprait la production. Ce faisant, ils peuvent faire économiser aux services publics des centaines de milliers de dollars en frais de réparation pour un rembobinage coûteux, des pénalités de non-production et une perte de temps de production.
De plus, des dispositifs de test automatiques installés en permanence permettent une surveillance "sans intervention" sans avoir à accéder aux armoires, ce qui protège les techniciens de tout danger.
Protection du moteur dans les services publics
Quelle que soit l'industrie, les usines de fabrication et de transformation dépendent fortement des moteurs, bien que le nombre et le type varient en fonction de la taille de l'usine et du type de carburant brûlé. Certaines usines peuvent avoir jusqu'à 20 à 30 moteurs critiques, avec cinq à dix en moyenne.
Les moteurs critiques sont ceux qui pourraient considérablement nuire à la capacité d'atteindre en toute sécurité les objectifs commerciaux ou affecter les niveaux de production s'ils se déconnectaient de manière inattendue. Les exemples incluent des moteurs allant de 480 à 13 800 V utilisés pour faire fonctionner des compresseurs, des pompes et des ventilateurs.
La plupart des services publics entretiennent ces moteurs par le biais de programmes de maintenance préventive (MP) basés sur le temps. Les tests de résistance d'isolement sont généralement programmés sur une base semestrielle. Cependant, compte tenu de la réduction du personnel dans la plupart des usines, cela peut même être moins fréquent. Sur la base de ces tests, les moteurs peuvent être programmés pour être envoyés aux ateliers de réparation pour reconditionnement.
En règle générale, des tests de résistance d'isolement sont également effectués au début des révisions annuelles ou des arrêts planifiés pour identifier les moteurs qui pourraient également nécessiter une réparation. Pourtant, malgré les programmes PM, les moteurs qui sont hors ligne ou qui sont fréquemment cyclés peuvent être rapidement compromis. "Nous avons eu notre juste part de pannes de moteur, et cela est devenu assez coûteux", a déclaré Richard Hohlman, qui a pris sa retraite après 37 ans de travail dans des centrales électriques.
"Parfois, les échecs peuvent coûter très cher", a-t-il déclaré. "Dans cette usine particulière, nous avions deux moteurs à induction à courant alternatif PAM à deux vitesses Westinghouse et le rembobinage de l'un d'eux aurait représenté une dépense à six chiffres."
Du point de vue de l'exploitation et de la maintenance (exploitation et maintenance), "si nous pouvons identifier un moteur faible et éviter le risque d'essayer de le démarrer et de le voir tomber en panne, c'est une grande économie", a-t-il ajouté.
Pour éviter les pannes de moteurs, Hohlman a déclaré qu'il exigeait que tous les moteurs critiques d'une usine de 1 500 mW de Long Island Sound qui ont été arrêtés pendant 24 heures ou plus soient testés manuellement avec un mégohmmètre avant d'être redémarrés. "Cela est devenu une dépense en soi, car les tests sont souvent effectués à différentes heures de la journée, à des taux d'heures supplémentaires", a déclaré Hohlman. "Mais, en le faisant, nous avons évité un certain nombre de pannes de moteur."
Hohlman a déclaré qu'un membre de son équipe a découvert Meg-Alert, un dispositif de test et de surveillance en continu fabriqué par Meg-Alert, Minocqua, Wis. L'usine l'a initialement installé sur quatre pompes de circulation et plusieurs ventilateurs à tirage induit. Plus tard, les dispositifs ont également été ajoutés à plusieurs ventilateurs à tirage forcé et autres moteurs critiques dans toute l'usine.
L'unité Meg-Alert est installée en permanence à l'intérieur du compartiment haute tension du MCC ou de l'appareillage de commutation et se connecte directement aux enroulements du moteur ou du générateur. L'unité détecte lorsque le moteur ou le générateur est hors ligne, puis effectue un test diélectrique continu sur l'isolation de l'enroulement jusqu'à ce que l'équipement soit redémarré.
L'unité fonctionne en appliquant une tension de test CC non destructive et limitée en courant aux enroulements de phase, puis mesure en toute sécurité tout courant de fuite à travers l'isolation vers la terre. Le système utilise des niveaux de tension CC de 500, 1 000, 2 500 ou 5 000 V qui respectent les normes internationales IEEE, ABS, ANSI/NETA et ASTM pour une tension de test de résistance d'isolement appropriée en fonction de la tension de fonctionnement de l'équipement.
Le test ne provoque aucune détérioration de l'isolation et inclut une technologie de limitation de courant qui protège le personnel.
"Grâce à une surveillance continue, l'équipe O&M est consciente à tout moment de l'aptitude du moteur à fonctionner", a déclaré Hohlman. "Chaque fois que le moteur s'arrête, que ce soit pendant quelques secondes, un jour ou pendant les 10 jours d'une panne, le moteur est testé. Et s'il descend en dessous d'un niveau de sécurité, il déclenche immédiatement une alarme et peut empêcher le moteur de démarrer."
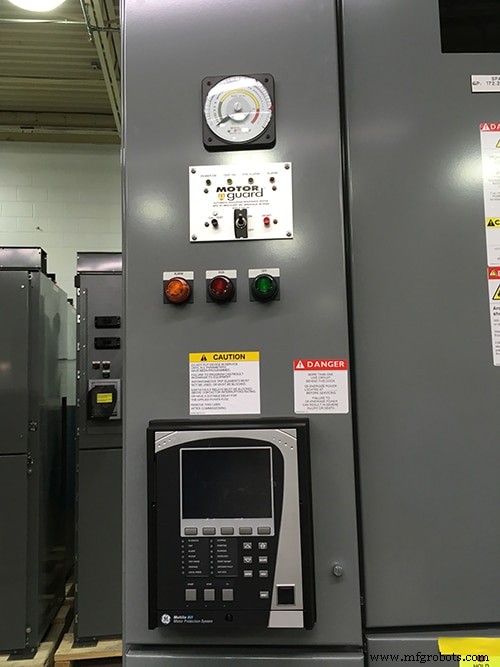
Cela contraste fortement avec l'instantané pris par un mégohmmètre au début d'un arrêt. Le moteur peut rapidement absorber une humidité considérable en raison de l'humidité et de la contamination.
"Un moteur électrique peut absorber suffisamment d'humidité en quelques heures seulement dans la région sud du pays pour causer des dommages au démarrage", a déclaré Ricky Loupe, responsable de l'électricité et des instruments dans une grande usine qui fabrique une forme de poudre de chlorure de polyvinyle ( PVC) ainsi que le composant principal, le chlorure de vinyle. "Il y a beaucoup de jours de pluie avec une humidité élevée ici dans le Sud, et l'humidité et l'électricité ne font pas bon ménage.
"Lorsqu'un moteur est plein d'humidité et est démarré, les enroulements vont se mettre à la terre et endommager le moteur", a poursuivi Loupe. "Alors maintenant, vous avez un moteur critique avec des enroulements endommagés qui coûteront beaucoup d'argent à réparer."
Ingénieur à l'époque, lui et son équipe ont mené une analyse pour déterminer la cause profonde du problème et comment le prévenir. Après en avoir appris davantage sur le Meg-Alert, il en a acheté un à titre d'essai. Loupe a déclaré qu'il était installé sur un moteur de boîtier WP de 4 160 V et 1 200 hp qui était utilisé pour entraîner un compresseur sur une unité de refroidissement.
En fonction des exigences de production, certains des refroidisseurs ont été éteints et utilisés uniquement en cas de besoin. Cela signifiait que les moteurs de certaines unités pouvaient rester inactifs. Avant de faire fonctionner à nouveau un refroidisseur, les moteurs devaient être testés à l'aide de mégohmmètres portables. « Souvent, ce travail se faisait après les heures, en raison des exigences des opérations et de la nécessité de les démarrer le plus rapidement possible », a expliqué Loupe. "Nous faisions venir des techniciens les week-ends, souvent en heures supplémentaires, juste pour tester les moteurs afin qu'ils puissent les démarrer."
Loupe a déclaré qu'avec les unités Meg-Alert, ces informations sont désormais disponibles en temps réel. Il était en outre convaincu après que l'appareil, qui est connecté au démarreur, ne permettrait pas au moteur de s'allumer en raison de faibles lectures de résistance en mégohm après un jour de pluie. "Le Meg-Alert ne permettait pas au moteur de démarrer car il y avait trop d'humidité dans le moteur", a expliqué Loupe. "Cela, juste là, a payé dix fois l'unité de surveillance continue."
Aujourd'hui, l'usine dispose de Meg-Alerts sur les dix moteurs de refroidisseur ainsi que sur quatre pompes de tour de refroidissement de 900 hp dans une autre zone de l'usine.
Surveillance "sans intervention"
Le système de surveillance continue permet également une approche « sans intervention » qui ne nécessite pas que les techniciens de maintenance accèdent aux armoires de commande pour effectuer un test manuel de résistance d'isolement. Au lieu de cela, un compteur analogique à l'extérieur sur la porte de l'armoire de commande affiche les lectures de résistance d'isolement mesurées en mégohms en temps réel. Le compteur indique également les niveaux d'isolation bons, moyens et médiocres grâce à une simple palette de couleurs "vert, jaune, rouge".
Lorsque les niveaux de consigne de résistance d'isolement prédéterminés sont atteints, les voyants s'allument pour signaler une condition d'alarme et des notifications automatiques peuvent être envoyées au réseau de surveillance. Une surveillance continue peut également indiquer si les éléments chauffants utilisés pour maintenir les températures thermiques ou empêcher la condensation fonctionnent correctement.
La plupart des moteurs utilisent des réchauffeurs pour maintenir la température à l'intérieur du moteur afin qu'elle ne varie pas considérablement de la température de fonctionnement ou des températures ambiantes à l'extérieur de l'unité. S'il descend en dessous du point de rosée, le moteur commencera à ramasser de la condensation lorsqu'il sera hors ligne.
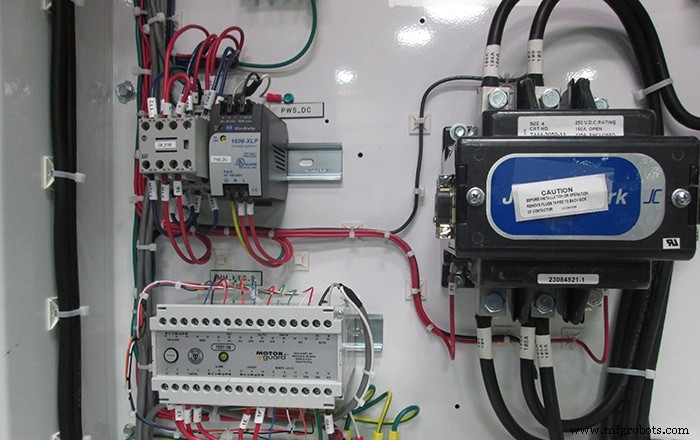
Cependant, si ces éléments chauffants ne fonctionnent pas correctement ou si le disjoncteur est déclenché, le personnel de maintenance peut ne pas en être conscient jusqu'à ce que le moteur tombe en panne au démarrage. Bien que ces réchauffeurs de moteur soient vérifiés régulièrement, cela peut laisser des moteurs et des générateurs critiques sans protection pendant des semaines, voire des mois.
Prévenir les arcs électriques
Peut-être plus important encore, Loupe a déclaré que l'approche sans intervention réduit l'exposition des employés aux dommages potentiels causés par les éclairs d'arc. "Avec les dispositifs de surveillance continue de la résistance d'isolement, vous éliminez les dommages potentiels des éclairs d'arc en n'ayant pas du tout le technicien ouvert les armoires pour les tests de mégohm", a déclaré Loupe.
Les arcs électriques sont une décharge électrique indésirable qui se déplace dans l'air entre les conducteurs ou d'un conducteur à la terre. Le flash est immédiat et peut produire des températures quatre fois supérieures à celles de la surface du soleil. La chaleur intense provoque également une expansion soudaine de l'air, ce qui entraîne une onde de choc qui peut projeter les travailleurs à travers les pièces et les faire tomber des échelles. Les blessures par arc électrique comprennent les brûlures au troisième degré, la cécité, la perte auditive, les lésions nerveuses, l'arrêt cardiaque et même la mort.
Parmi les causes potentielles d'un arc électrique répertoriées par la norme NFPA 70E figure "une mauvaise utilisation de l'équipement de test". Bien qu'il soit recommandé de mettre l'équipement hors tension avant de tester et de porter un équipement de protection individuelle (EPI) approprié, la meilleure solution consiste à éliminer complètement le besoin d'accéder aux armoires de commande afin d'effectuer des tests de résistance d'isolement.
En plus du risque d'arcs électriques, Loupe a été témoin d'un autre risque potentiel qui peut survenir si un moteur court-circuite à quelques pieds d'un employé. Dans l'usine, le personnel ne se trouve qu'à environ cinq pieds du moteur lors du démarrage du refroidisseur. Si le moteur court-circuite, il peut faire un bruit énorme et projeter une masse d'étincelles.
"Grâce à la surveillance continue de la résistance d'isolement, vous n'avez aucun employé en danger si le moteur tombe en panne au démarrage", a déclaré Loupe. "L'appareil évite également ce problème de sécurité."
Pour plus d'informations, visitez www.megalert.com ou appelez le 800-778-5689.
Système de contrôle d'automatisation
- Moteurs à induction monophasés
- Moteurs à collecteur AC
- Conseil de test :Défauts d'induit sur les moteurs à courant continu
- Conseil technique :Moteurs
- IQ Motion Control lance une nouvelle gamme de servomoteurs
- La zone grise entre les servomoteurs et les moteurs pas à pas
- À propos des moteurs industriels et des applications
- Une introduction au moteur BLDC
- Couplage de réducteurs avec des servomoteurs