De nouvelles approches pour fabriquer des pièces pour le champ pétrolier
La fracturation a entraîné de grands changements dans le secteur pétrolier et de grands changements dans l'usinage des pièces.
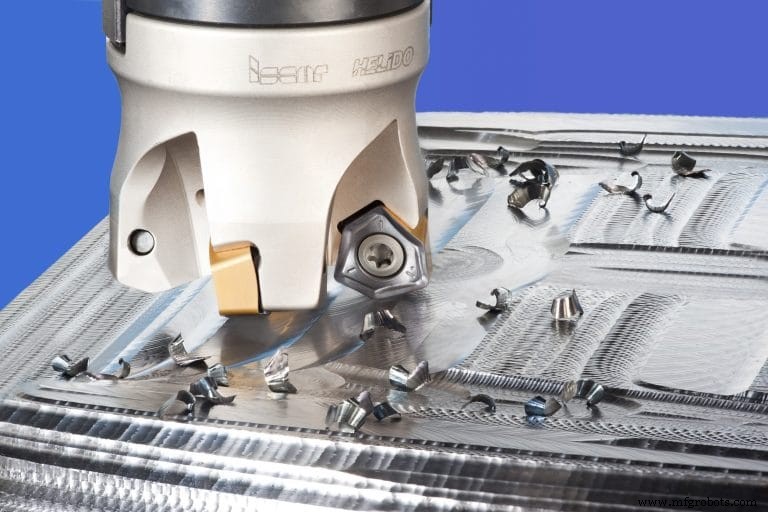
Rod Zimmerman du fabricant d'outils coupants Iscar Metals vit dans une zone verte agréable dans une banlieue de Fort Worth. Pourtant, à moins d'un demi-mille de son domicile, une compagnie pétrolière a creusé un trou vertical de 7 500 pieds (2 286 m) de profondeur, à partir duquel elle a évasé neuf lignes latérales, chacune d'environ un demi-mille. Il pompe du fluide de fracturation dans ces conduites à 9 000 psi pour extraire le gaz naturel. C'est un aussi bon exemple que n'importe lequel de l'omniprésence de la révolution de la fracturation hydraulique et de l'incroyable technologie impliquée.
Et bien que la révolution ne soit pas littéralement «partout», Salvatore Deluca, chef de produit pour un autre fabricant d'outils de coupe, Allied Machine &Engineering, a déclaré que les installations de fracturation géantes de son comté sont appelées «villes». Sauf que contrairement à Dallas-Fort Worth, ces "villes" se trouvent dans le lointain Ohio, un état jusqu'alors inconnu pour le pétrole. Il n'est donc pas surprenant que de grands changements dans le secteur pétrolier aient entraîné de grands changements dans l'usinage des pièces pour le secteur pétrolier.
S'attaquer au bloc de fracturation
Comme évoqué ci-dessus, la fracturation hydraulique (plus communément appelée fracturation) récupère le gaz et le pétrole des formations de schiste en forant dans le sol et en injectant un mélange d'eau, de sable et de produits chimiques dans la roche à une pression extrêmement élevée. La génération de cette pression nécessite des pompes géantes, dont l'un des composants clés est la « extrémité fluide » ou le « bloc de fracturation » et ses vannes, pistons et chemises.
La haute pression et l'abrasivité de la boue pompée à travers ces blocs provoquent une usure et une fissuration rapides. Et comme les exploitants de champs pétrolifères doivent maintenir une pression élevée, ils sont obligés de remplacer les extrémités fluides tous les quelques jours, selon Paul Best, spécialiste des produits chez Allied Machine, Dover, Ohio. Lesdites extrémités fluides sont usinées à partir de blocs d'acier solides et mesurent généralement environ 3′ de haut, 4′ de large et 2-3′ (0,61-0,91 m) d'épaisseur. Avec des contours complexes, de nombreux canaux, trois à cinq trous traversants (chacun jusqu'à 8″ [203,2 mm] de diamètre) et trois à cinq trous transversaux qui se croisent, les extrémités fluides nécessitent d'énormes quantités de fraisage, de perçage et de filetage. /P>
Zimmerman, vice-président des ventes, West Zone pour Iscar, a déclaré que les extrémités fluides étaient traditionnellement fabriquées à partir d'acier allié de la série 4000, mais pour lutter contre l'usure, les utilisateurs essaient «des alliages plus exotiques comme l'acier inoxydable 17-4 PH, l'acier inoxydable super duplex et 15-5 inoxydable. Deluca a estimé qu'environ la moitié des extrémités fluides qu'il voit maintenant sont une variante d'un acier inoxydable pré-durci et la proportion continue de croître.
Gayle Vollmer, des services d'ingénierie pour Hartwig à Houston (concessionnaire d'Okuma dans la région), a déclaré qu'il y avait également une tendance à utiliser des matériaux plus durs pour les parties d'un bloc de fracturation qui sont les plus susceptibles de s'user, et une tentative de reconception des blocs de fracturation afin que plus de composants sont facilement remplaçables. Mais il a supposé que la demande actuelle pour une production élevée a mis une telle recherche "en veilleuse".
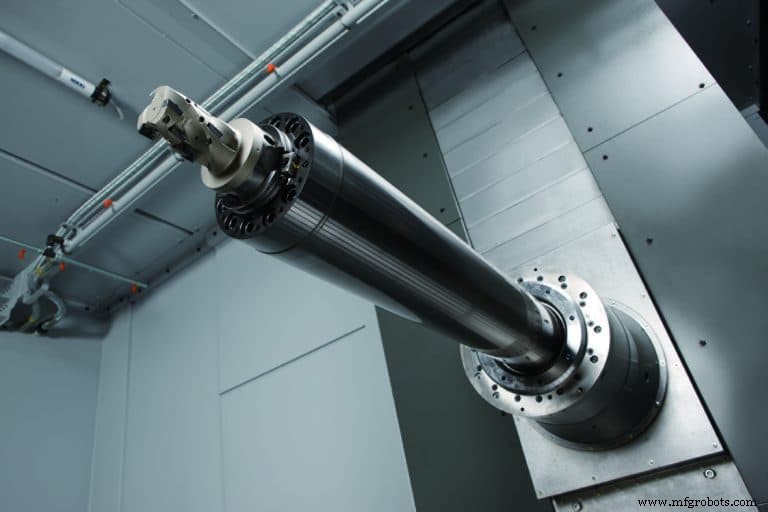
Qu'il soit fabriqué à partir de 4340 ou d'un acier inoxydable plus dur, s'attaquer à une tête fluide nécessite pratiquement une grande aléseuse ou un centre d'usinage horizontal. Jason Schooley, directeur régional des ventes pour JTEKT Toyoda Americas, Arlington Heights, Illinois, a déclaré que l'objectif était d'effectuer autant d'opérations que possible sur une seule machine, ce qui est doublement important sur une pièce aussi grande et difficile à déplacer.
Schooley a déclaré que si les aléseuses ont généralement des tables plus grandes pour des pièces encore plus grandes, les horizontales comme le FH1250SX de Toyoda sont presque quatre fois plus rapides. Cela est dû en partie à une broche entraînée par engrenage à 6 000 tr/min (en option à 8 000 tr/min ou à une broche à couple élevé de 15 000 tr/min) et à une vitesse d'avance rapide de 1 654 ipm (42 m/min). La machine est construite sur une base en fonte Meehanite pour une rigidité maximale avec des guides à rouleaux cylindriques pour une vitesse accrue, tandis que l'entraînement à double vis à billes sur les axes Y et Z augmente la stabilité d'usinage lors des coupes lourdes.
Le FH1250SW dispose également d'un fourreau à axe W pour les opérations de forage et d'alésage profonds. Il a ajouté que ces dernières années, "un certain nombre de constructeurs de machines-outils ont opté pour une tête d'axe U intégrée" ou un axe W, qui roulent parallèlement à l'axe X ou à l'axe Z respectivement. Cela permet de changer le centre de rotation d'un outil de tournage fixe, une caractéristique utile lors de la coupe de grands alésages ou d'autres grands contours. En effet, non seulement les extrémités fluides ont de grands alésages, mais les alésages sont souvent "en forme de bouteille" à l'intérieur, de sorte qu'ils ne peuvent pas simplement être percés. Pour les machines qui n'ont pas d'axe U intégré, les utilisateurs peuvent ajouter une tête de "sortie" qui remplit la même fonction, D'Andrea étant l'un de ces fournisseurs.
Le montage d'une grande tête sur une broche rotative présente des inconvénients, notamment une éventuelle interférence des pièces et une incompatibilité avec la distribution de liquide de refroidissement à travers la broche. L'option de rechange nécessite également son propre lecteur externe et il peut ne pas être possible de désactiver automatiquement la plate-forme comme vous le feriez avec d'autres changements d'outils.
Mais Schooley a déclaré que les interférences ne sont pas un problème sur les applications de blocs de fracturation si la course de l'axe Z de la machine est suffisamment longue pour empêcher la tête supplémentaire de dépasser la ligne de jauge. Avec une course de 1 850 mm sur l'axe Z et une bande morte de 200 mm entre le nez de la broche et le centre de la table, la machine 1250 s'attaque aux blocs de fracture sans interférence. Il a ajouté que Toyoda a encore développé la capacité de changement automatique de ses têtes de contournage pour "aider nos clients à garder une longueur d'avance dans une industrie aussi volatile que le pétrole".
D'après l'expérience de Schooley, les outils d'alésage modulaires disponibles auprès d'Innovative Tooling Solutions et d'autres sont livrés avec un liquide de refroidissement à travers la broche en tant que caractéristique standard et de nombreux ateliers fabriquant des blocs de fracturation utilisent une aléseuse horizontale dédiée avec une tête de contournage pour finir les alésages. Toyoda propose également des centres d'usinage horizontaux à broche fourreau avec un couple de 1 560 lb-pi pour les opérations intensives. Schooley a déclaré que la broche fourreau de 4 000 tr/min combine la portée et la force nécessaires pour l'alésage et le perçage profond, permettant aux pièces nécessitant auparavant deux opérations d'être réalisées sur une seule machine. La palette rotative à 360 000 positions de la machine offre une flexibilité maximale pour l'usinage intensif sur une variété de pièces.
Okuma America Inc., Charlotte, N.C., a développé une option de programmation appelée Turn-Cut qui permet à un centre d'usinage horizontal d'imiter un tour en coupant des caractéristiques circulaires et angulaires sur de grandes pièces déséquilibrées sans utiliser de tête en U. Comme l'a expliqué Ted Winkle, coordinateur du centre technique d'Okuma à Houston, "au lieu de faire tourner la pièce, ce qui serait difficile ou impossible pour certaines pièces énormes, vous faites tourner l'outil autour de la pièce. Et au lieu d'une tête en U déplaçant l'outil hors du centre de l'axe de rotation, Turn-Cut interpole ces axes en X et Y tout en alimentant également un outil de tournage à point unique en Z."
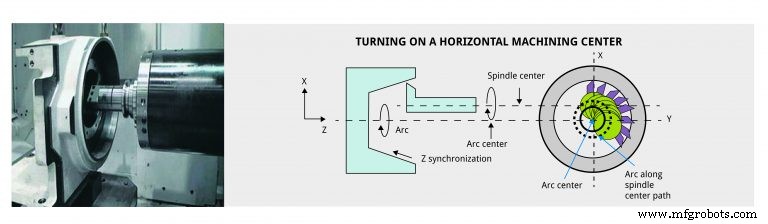
Winkle pense que Turn-Cut jouera un rôle plus important dans l'industrie pétrolière et gazière pour des pièces telles que les blocs de fracturation, car "à mesure que les alésages augmentent en diamètre, il faut beaucoup de couple pour faire fonctionner un outil solide pour faire un trou de cette taille. Disposer d'une capacité de coupe par rotation, par opposition à une tête en U et à tous les outils coûteux qui y sont associés, est un avantage."
D'un autre côté, Turn-Cut n'est pas bon marché car il nécessite un logiciel supplémentaire pour l'accélération, la décélération et la synchronisation spécialisées, ainsi que des échelles de verre et le refroidissement de la vis à billes. Mais vous obtiendrez une meilleure précision pour une variété de pièces avec ces fonctionnalités et cela augmente la probabilité de pouvoir finir des pièces en une seule configuration.
Schooley a répliqué que la technique nécessite beaucoup de mouvements répétitifs dans la même zone des vis à billes et des glissières (plus le diamètre est petit, plus cela se produirait) et cela pourrait réduire la durée de vie de la machine.
Encore une fois, a déclaré Winkle, à moins que vous n'utilisiez cette capacité fréquemment sur des pièces de même taille, vous n'auriez pas de mouvement excessif dans la même zone. Et si vous n'avez pas besoin de cette capacité fréquemment, vous ne seriez pas en mesure de justifier les dépenses importantes d'un axe U, donc Turn-Cut serait une option plus logique. Comme toute fonctionnalité de machine-outil, il y a des compromis.
Le paradis de la puissance
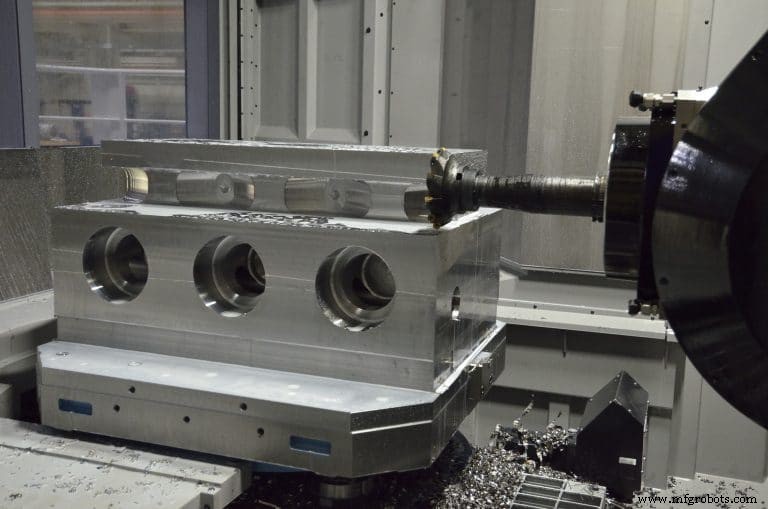
Pour Makino Inc., Mason, Ohio, les plates-formes incontournables pour les pièces telles que les blocs de fracturation sont ses centres d'usinage horizontaux à cinq axes T1 et T2. David Ward, directeur du marketing produit, a déclaré que les deux machines sont équipées de broches à entraînement direct "idéales pour les aciers inoxydables et fortement alliés difficiles utilisés dans cette industrie".
Le T1 est équipé d'une broche HSK100 de 12 000 tr/min avec 143 ch et un couple nominal de 740 lb-pi. La plus grande broche T2 utilise une interface HSK125 pour la rigidité radiale. La broche T2 à 4 000 tr/min délivre 200 ch et 1 107 pi-lb de puissance et de couple nominaux.
Ward a ajouté que les deux broches maintiennent leurs valeurs de couple maximales jusqu'à 1 000 tr/min. "En portant les valeurs de couple maximales jusqu'à ce point, cela garantit que la broche sera en mesure de tirer parti des nouvelles avancées de la technologie des outils de coupe, comme les revêtements de plaquette à haute température."
Winkle a observé que le champ pétrolier est dominé par les machines CAT 50 mais a convenu que le contact de face fourni par les interfaces HSK et BIG Plus serait un avantage « si vous avez un long porte-à-faux. Mais comme la plupart des forces d'usinage sont axiales, peu importe le type de broche que vous choisissez. Tant que c'est costaud. "Approcher un bloc de fracturation avec une machine à broche ISO 40 serait un exercice futile", a-t-il déclaré.
Des sources ont convenu que le liquide de refroidissement haute pression est essentiel pour l'élimination de la chaleur et des copeaux dans de nombreuses applications pétrolières et gazières, ou comme l'a dit Zimmerman d'Iscar, "presque quelle que soit l'application. Lorsque vous travaillez profondément dans un alésage sur une extrémité fluide, il est essentiel de rincer les copeaux et difficile à faire. Un outil de fraisage alimenté en liquide de refroidissement est de loin la voie à suivre pour de telles applications. »
Donc, si la machine n'était pas dotée de cette capacité, les utilisateurs l'ajoutent avec des unités de fournisseurs tels que ChipBLASTER. "Je n'envisagerais même pas d'acheter une fraiseuse aujourd'hui sans arrosage haute pression à travers la broche", a déclaré Zimmerman. "C'est un changement de jeu pour le fraisage et le forage." La seule exception est une situation dans laquelle vous ne pouvez pas diriger le liquide de refroidissement vers le tranchant. Dans ce cas, le liquide de refroidissement "agit parfois contre vous et il est préférable de sécher à la machine pour éviter la fissuration thermique des inserts", a-t-il déclaré.
Deluca a déclaré que les constructeurs de machines-outils ont répondu à cette demande de telle sorte qu'il trouve maintenant couramment des machines avec une pompe fournie par l'OEM délivrant 1 000 psi à 20 gpm. Ward a déclaré que le T1 de Makino fournit 26 gpm à 1 000 psi tandis que le T2 fournit cette même pression à 53 gpm.
Avance de l'outil de coupe
Alors que vous aimeriez peut-être avoir un monstre de grande puissance pour vos blocs de fracturation, Deluca d'Allied Machine a déclaré qu'ils étaient de plus en plus confrontés au défi opposé :la nécessité de percer de grands trous avec des machines axées sur le fraisage où les vitesses de broche sont plus élevées mais la puissance maximale à 40 chevaux. à 50.
"Les entreprises qui fabriquent ces pièces sont généralement de taille petite à moyenne et ne se consacrent généralement pas à la fabrication de blocs de fracturation", a-t-il déclaré. "Et beaucoup de gens hésitent à se concentrer sur ce marché et à dépenser un demi-million de dollars pour une machine pour une industrie qui fonctionne comme des montagnes russes. Nous avons donc dû développer un outil capable de percer un trou de 4″ de diamètre à des vitesses de broche beaucoup plus élevées et à des vitesses d'avance beaucoup plus faibles que nos produits de perçage traditionnels. »
Le défi du forage de blocs de fracturation va au-delà de la taille des trous requis. "Les coupes interrompues sont inhérentes à la fabrication de blocs d'extrémité fluides puisque les trous transversaux sont percés perpendiculairement aux trous existants", a déclaré Allied Machine's Best. "En raison de la forme résultante des trous qui se croisent, les bords extérieurs du foret continueront d'être engagés dans la coupe, tandis que le bord intérieur ne le sera pas. Cela peut déstabiliser la foreuse, ce qui peut détruire l'outil et endommager l'intégrité du bloc de fracturation."
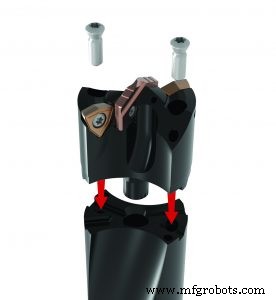
De plus, si le client économise en utilisant un matériau qui n'a pas été traité thermiquement, la perceuse peut rencontrer des variations importantes. Deluca d'Allied a déclaré que cela signifie généralement qu'un opérateur doit constamment surveiller le processus ou risquer une défaillance catastrophique du forage quelques secondes après avoir heurté une poche dans le moulage, ce qui pourrait détruire une pièce dans laquelle vous avez mis des heures. Les ateliers connaissent également des variations de matériaux d'un bloc à l'autre, ce qui rend difficile le choix de la perceuse et des paramètres de fonctionnement parfaits.
Allied a relevé ces défis avec un outil de « nouvelle génération » appelé APX. Il dispose d'un substrat en carbure plus résistant et d'un revêtement exclusif pour résister au choc de frapper une poche. "Vous pouvez ébrécher l'outil et vous obtiendrez un cri", a déclaré Deluca, "mais vous serez toujours en mesure de finir le trou."
Il a ajouté qu'Allied a résolu les difficultés du forage de trous transversaux en ajoutant un racleur à l'insert pour améliorer la stabilité, ainsi que des patins d'usure pour fournir une stabilité supplémentaire lorsque le pilote sort dans un espace vide ou un trou transversal. "Nous recommandons également d'alléger l'avance et de maintenir la même vitesse lors du perçage de trous de sortie inclinés afin que l'outil ne veuille pas pousser ou marcher. Ce n'est généralement pas nécessaire lors du perçage de la ligne principale ou des trous transversaux, mais il n'y a que peu d'ingénierie que vous pouvez mettre dans un outil pour compenser la coupe extrêmement interrompue des trous inclinés."
Pour le fraisage, Zimmerman a déclaré que la plaquette à six coins double face HeliDo H600 d'Iscar fonctionne extrêmement bien pour ce type de matériau. "Nous proposons également la Mill 4 Feed, une plaquette carrée à une face avec une géométrie plus positive pour une coupe plus douce nécessitant moins de puissance."
Son principal message est que, comme Iscar est engagé depuis longtemps dans l'industrie pétrolière et gazière et n'embauche que des machinistes expérimentés, il peut développer le processus optimal pour un client et choisir parmi une grande variété d'outils. "Nous avons de nombreux types de broyeurs d'aliments et pouvons optimiser un broyeur d'aliments en fonction de l'application, du matériau et de la machine, en tenant compte de sa rigidité, de sa puissance et de son couple."
Multitâche et automatisation
Il est probable que des blocs de fracturation de 9 500 lb ne conduisent pas à penser à « l'automatisation », mais Makino et d'autres constructeurs proposent des solutions qui permettent à un opérateur de faire fonctionner plusieurs machines. Pour les blocs de fracturation, cela signifie généralement un changeur de palettes rotatif qui bascule entre une pièce moulée brute et une pièce finie en moins d'une minute. Après cela, l'opérateur a tout le temps de retirer la pièce finie.
Avec des temps de cycle de quelques minutes, les tubes des pistolets de fracturation se situent à l'autre extrémité du spectre. Et comme il s'agit d'un "article à usage unique", a déclaré Vollmer, "les taux de production sont astronomiques. Des milliers sont fabriqués chaque jour."
En conséquence, la pièce est idéale pour l'automatisation, et Hartwig et Okuma ont travaillé ensemble pour proposer plusieurs options. Il s'agit notamment de robots pour les systèmes de type chargement/déchargement et ravitailleur de barres comme ceux utilisés pour les petites pièces sur les tours de type suisse, sauf qu'ici ils traitent des diamètres de 2 à 4″. L'approche la plus rapide consiste à introduire le brut dans une machine à deux broches, en usinant une extrémité, puis en alimentant la pièce directement dans la sous-broche pour travailler à l'autre extrémité.
Vollmer a déclaré que les pièces nécessitent un tournage, un filetage et un peu de fraisage, idéalement en utilisant des outils en direct pour ce dernier, une caractéristique que Winkle a qualifiée de "l'un des plus grands changements dans l'industrie ces dernières années". La fracturation hydraulique et le forage directionnel sont à nouveau une raison majeure de cette transition.
Cependant, pour la plupart des pièces en grande partie cylindriques nécessaires dans les opérations "en fond de trou" d'aujourd'hui, le tour idéal a plus qu'un outillage motorisé et une tourelle ou deux. Il a une tête pivotante et une capacité de fraisage multi-axes comme la série de fraisage-tournage MULTUS d'Okuma.
"Les pièces nécessaires à la fois pour le forage et la phase de complétion sont beaucoup plus complexes qu'avec les puits verticaux traditionnels", a expliqué Winkle. « Il faut pouvoir ouvrir et fermer des vannes pour changer de zone de production. Les pièces sont traversées par une plomberie hydraulique, ainsi que par un équipement de surveillance électronique. »
Cela nécessite des trous transversaux et des caractéristiques de fraisage complexes sur l'OD et l'ID, de sorte que les machines ont besoin d'un positionnement sur cinq axes et d'environ neuf axes de mouvement de la machine pour couper une pièce à une extrémité et changer les broches pour travailler l'autre.
Les fils sont un autre défi. Winkle a déclaré qu'il existe littéralement des centaines de types et que les tolérances sont strictes:"Plus 1,5 mille, moins rien." C'est parce que dans le pétrole et le gaz, les filetages ne font pas que maintenir les pièces ensemble, "ils doivent sceller parfaitement et supporter d'énormes contraintes de traction de la gigantesque chaîne de pièces qui pénètrent à des kilomètres de profondeur dans le trou", a déclaré Winkle. « Et ils doivent faire face à la dilatation thermique et aux charges de choc. Ce composant étanche et porteur n'existe dans aucune autre industrie. »
Couper ces fils nécessite une machine rigide et une configuration qui résiste au broutage. Kyle Downs, directeur de la gestion de projet et du marketing pour SMW Autoblok, Wheeling, Illinois, a déclaré que tout cela était compliqué par le fait que « le matériel entrant est très incohérent. L'automatisation du centrage des tuyaux crochus, courbés et/ou oblongs peut être réalisée avec deux scénarios, soit un mandrin à centrage automatique et compensateur 3+3, soit un mandrin compensateur et une solution de centrage montée sur poupée mobile, qui est généralement également un mandrin ."
Enfin, l'ajout de la capacité de dépôt de métal au laser aux machines d'enlèvement de métal ajoute de nouvelles possibilités, comme en témoigne la nouvelle série LASER EX d'Okuma. Si, par exemple, vous aviez une pièce avec seulement quelques caractéristiques saillantes, vous pouvez ajouter ces caractéristiques au corps principal, plutôt que de découper les caractéristiques d'un stock plus important. C'est potentiellement une énorme économie de temps d'usinage.
Winkle a ajouté que vous pouvez également fusionner des matériaux différents, en combinant, par exemple, l'Inconel et l'acier inoxydable, ce qui n'est «jamais possible avec une technologie purement soustractive. Le joint est aussi solide ou plus solide que s'il était usiné dans du solide », a-t-il déclaré.
Cela a un potentiel immédiat dans le pétrole et le gaz pour ajouter les patins d'usure nécessaires sur les ensembles de forage ou ajouter les ailettes latérales utilisées pour empêcher le tuyau de gratter l'ID d'un tubage de puits lorsqu'il se déplace dans un virage dans un puits directionnel. Okuma offre également la possibilité de durcir une zone de matériau jusqu'à environ 50 Rockwell en utilisant le même laser avec une ouverture différente.
Système de contrôle d'automatisation
- Nouvelle certification pour l'élite de la lubrification
- Présentation des arguments en faveur des puces neuromorphiques pour l'IA informatique
- Repenser la fabrication intelligente pour la nouvelle norme
- Si les données sont le nouveau pétrole, qui est votre raffineur ?
- Pour les chaînes d'approvisionnement, l'expérience client est le nouveau différenciateur
- Préparez votre chaîne d'approvisionnement pour la nouvelle normalité
- La pandémie est à l'origine d'un nouveau modèle de prise de décision dans la chaîne d'approvisionnement
- La nouvelle vague de défis pour les fabricants d'équipements industriels
- Top 5 des pièces Stromag pour votre plate-forme pétrolière