L'application en vedette :l'impression 3D pour les cabines d'avion
Lorsque vous voyagez en avion, vous ne vous rendrez probablement pas compte que votre accoudoir ou votre plateau a été imprimé en 3D, mais l'utilisation de cette technologie pour les pièces de cabine peut ouvrir un tout nouveau monde de possibilités pour les compagnies aériennes.
Ces possibilités incluent, par exemple, une personnalisation intérieure rentable et une production et une livraison plus rapides des pièces de rechange.
Nous explorons les principaux moteurs de l'utilisation de l'impression 3D pour les intérieurs d'avions tout en montrant comment les entreprises leaders de l'industrie aérospatiale appliquent la technologie aujourd'hui.
Regardez les autres applications couvertes dans cette série :
Impression 3D pour échangeurs de chaleur
Impression 3D pour roulements
Impression 3D pour la fabrication de vélos
Impression 3D pour la dentisterie numérique et la fabrication d'aligneurs transparents
Impression 3D pour implants médicaux
Les fusées imprimées en 3D et l'avenir de la fabrication d'engins spatiaux
Impression 3D pour la fabrication de chaussures
Impression 3D pour composants électroniques
Impression 3D dans l'industrie ferroviaire
Lunettes imprimées en 3D
Impression 3D pour la production de pièces finies
Impression 3D pour supports
Impression 3D pour pièces de turbine
Comment l'impression 3D permet des composants hydrauliques plus performants
Comment l'impression 3D soutient l'innovation dans l'industrie de l'énergie nucléaire
Pourquoi adopter l'impression 3D pour les pièces de cabine ?
Innovation de conception de cabine
Les compagnies aériennes sont toujours à la recherche de moyens d'améliorer l'expérience de vol de leurs clients, et la conception de la cabine joue un rôle essentiel à cet égard.
La création d'intérieurs personnalisés qui répondent aux besoins et aux fonctions spécifiques des compagnies aériennes est une tendance croissante et une tâche parfaite pour l'impression 3D.
L'impression 3D ouvre de nouvelles possibilités de personnalisation des pièces de la cabine car elle ne nécessite pas de changements d'outillage coûteux basés sur des spécifications individuelles. La fabrication de pièces sur mesure est donc plus rapide et plus rentable.
Réduction de poids
Les dépenses en carburant étant l'un des principaux coûts pour les opérateurs aériens, ils ont tendance à investir dans des avions avec une efficacité énergétique supérieure. Cependant, les méthodes de fabrication traditionnelles ont une capacité limitée à réduire le poids des pièces d'avion.
Les fabricants poursuivent donc la recherche de méthodes plus avancées et alternatives de fabrication de pièces avec un poids réduit.
L'impression 3D fournit l'une des solutions pour obtenir une réduction de poids grâce à une géométrie de pièce optimisée qui permet des économies de matière.
Avec l'impression 3D, les fabricants peuvent construire des pièces de cabine dans des matériaux légers, avec des parois plus fines que le moulage par injection.
En outre, la technologie permet une intégration fonctionnelle, tandis que plusieurs parties distinctes d'un composant peuvent être conçues et imprimées comme une seule unité, réduisant encore le poids d'une pièce.
Impression 3D à la demande de pièces détachées pour l'intérieur des avions
Prévoir la demande de pièces de rechange est un défi et, parfois, une pièce de rechange peut ne plus être en production. Ces facteurs rendent le service après-vente des avions difficile et entraînent des inefficacités globales de la chaîne d'approvisionnement. Bien que des niveaux de stocks élevés puissent réduire les temps d'arrêt de l'avion, ils entraînent des coûts astronomiquement élevés pour le maintien d'un tel inventaire.
En outre, il est souvent problématique de fournir des services MRO en temps opportun. La nécessité de produire des pièces de rechange de haute qualité, avec des matériaux coûteux dans des délais courts, met les fabricants sous pression, car les délais s'étendent souvent jusqu'à plusieurs mois, en utilisant des procédés de fabrication traditionnels.
De plus, lors de la réparation ou du remplacement de composants d'avions hérités, les outils associés peuvent ne plus être disponibles à l'achat auprès des équipementiers.
Il existe une énorme opportunité pour l'impression 3D de surmonter certains de ces défis, en permettant un délai d'exécution plus rapide et en réduisant les stocks grâce à la fabrication à la demande.
L'impression 3D permet aux entreprises de produire des pièces directement à partir d'un fichier de conception numérique, sans utiliser d'outillage, comme des moules. Cela signifie que certaines pièces de rechange, en particulier les pièces les moins demandées comme les composants obsolètes, peuvent être repensées pour l'impression 3D et stockées dans un inventaire virtuel, libérant ainsi de l'espace dans un entrepôt et réduisant les coûts d'inventaire.
Lorsqu'un remplacement est nécessaire, une conception peut simplement être extraite du catalogue de pièces virtuel et envoyée pour impression.
Grâce à sa capacité à produire de petits volumes de pièces de manière économique, l'impression 3D permet également aux entreprises de ne créer qu'autant de pièces que nécessaire, résolvant ainsi le problème de surproduction, typique des méthodes de production traditionnelles.
4 exemples d'utilisation de l'impression 3D pour les pièces de cabine
De nombreux composants intérieurs d'avions, des évents et boîtiers électriques aux panneaux d'espacement et aux accoudoirs, peuvent bénéficier de l'impression 3D. Ci-dessous, nous explorons comment les équipementiers et les opérateurs aériens tirent parti de la technologie pour les pièces de cabine.
1. Etihad Airways voit une valeur ajoutée significative dans l'impression 3D
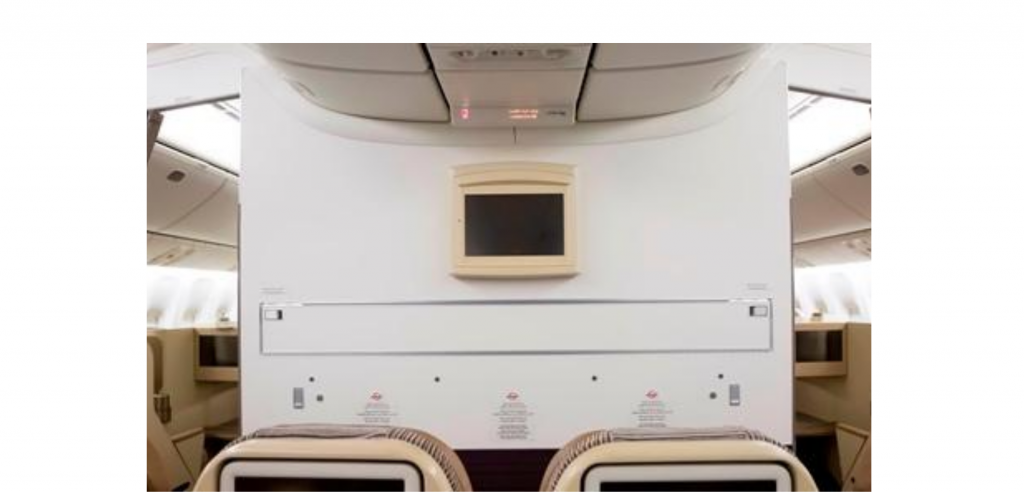
La deuxième compagnie aérienne des Émirats arabes unis, Etihad Airways, a été l'une des premières compagnies aériennes à explorer le potentiel de l'impression 3D pour les pièces de cabine.
En 2017, la société a présenté la première pièce intérieure d'avion imprimée en 3D certifiée de la région, un cadre de moniteur en plastique, et depuis lors, Etihad a intensifié ses efforts d'impression 3D.
La création de partenariats stratégiques avec des sociétés d'impression 3D, EOS et BigRep, fait partie de ces efforts.
Les résultats de la collaboration avec les principaux fabricants de matériel 3D ne se sont pas fait attendre. L'année dernière, Etihad a ouvert une usine de fabrication additive (AM) à Abu Dhabi, qui avait reçu l'approbation de conception et de production de l'Agence européenne de la sécurité aérienne (EASA), pour produire des pièces d'avion en utilisant la technologie de fusion sur lit de poudre d'EOS.
Etihad Engineering, une division du groupe Etihad Aviation, utilisera désormais l'imprimante 3D EOS pour concevoir, produire et certifier des composants AM pour des applications aéronautiques et des pièces de cabine de haute qualité.
L'entreprise estime que l'utilisation de l'impression 3D ira bien plus loin que le remplacement de pièces simples et non critiques.
La production additive de pièces de cabine offre une valeur ajoutée substantielle en termes de réparation optimisée, de conception légère, de délais de livraison plus courts et de personnalisation. Le nouveau « Greenliner » d'Etihad, par exemple, un projet conjoint avec Boeing conçu pour faire progresser la durabilité dans l'industrie de l'aviation, comprendrait de nombreux composants imprimés en 3D.
En regardant plus loin, Etihad envisage un rénovation complète d'un avion en seulement 30 jours grâce à l'impression 3D, ce qui permet des mises à niveau 30 % plus rapides.
2. Enceinte de tête de rideau imprimée en 3D par Diehl Aviation
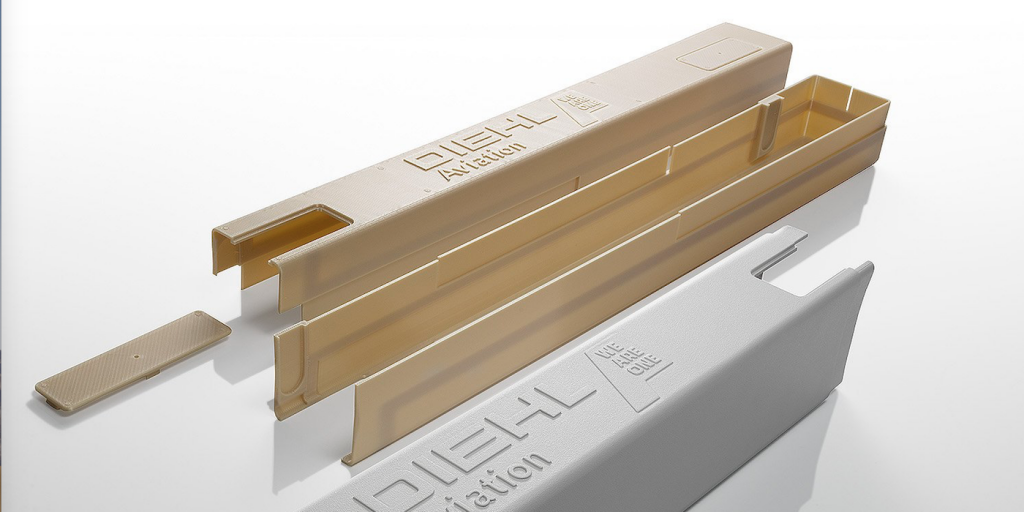
Le constructeur aéronautique spécialisé dans la cabine et l'avionique, Diehl Aviation, a présenté un autre exemple d'impression 3D pour les pièces intérieures.
En collaboration avec Airbus, Diehl a développé un Curtain Comfort Header imprimé en 3D - une enceinte qui se trouve au-dessus du rail de rideau, séparant les classes à bord - installé sur un Airbus A350 XWB de Qatar Airways.
Le boîtier était auparavant construit à l'aide de plusieurs couches de fibre de verre stratifiée et nécessitait un outillage spécialisé en aluminium, ce qui prenait du temps et était coûteux.
Diehl a pu assembler cette pièce à partir de 12 composants thermoplastiques imprimés en 3D, réduisant considérablement les coûts d'outillage et économisant des heures de main-d'œuvre.
De plus, les pièces nécessitent moins de retouches et peuvent être facilement retirées pour des réparations ou des remplacements, ce qui signifie des délais de livraison encore plus courts lors de la réparation.
Cette pièce est, semble-t-il, la plus grande pièce d'avion de passagers entièrement imprimée en 3D produite pour les avions de passagers à ce jour.
3. British Airways prévoit une adoption accrue de l'impression 3D pour les intérieurs d'avions
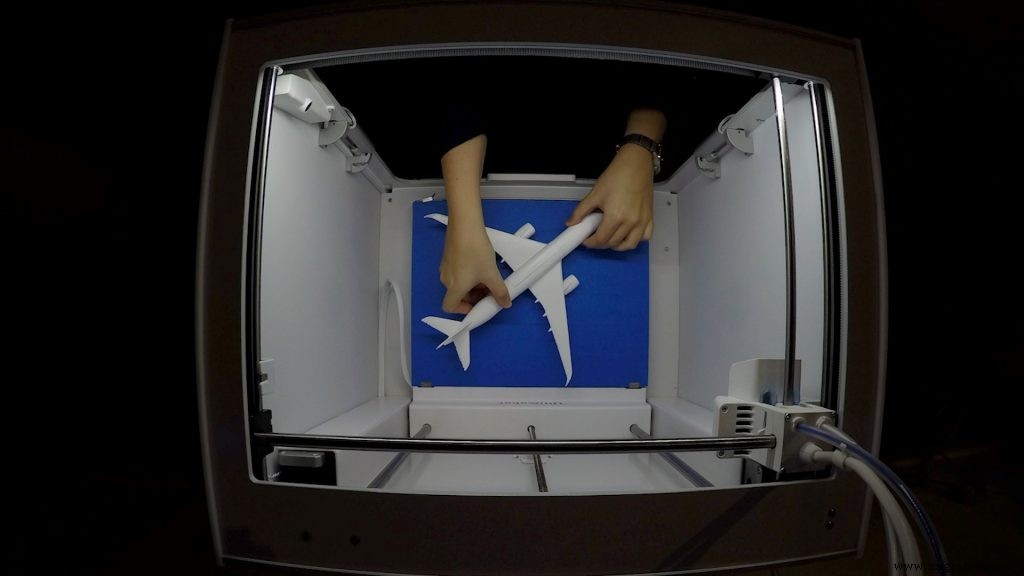
Bien qu'il semble que la plupart des efforts pour l'impression 3D de pièces de cabine soient concentrés dans la région EMEA, les compagnies aériennes européennes rattrapent leur retard.
Par exemple, British Airways explore la possibilité d'utiliser des imprimantes 3D pour créer des pièces d'avion, en commençant par des pièces de cabine non essentielles, notamment des pièces de plateaux, des systèmes de divertissement en vol (IFE) et des toilettes.
Bien que ces composants n'aient pas d'impact sur le fonctionnement sûr d'un vol, s'ils sont cassés, ils peuvent réduire le nombre de sièges ou de toilettes disponibles pour les clients et entraîner des retards car les ingénieurs attendent que les pièces soient réparées ou remplacées .
Selon la compagnie aérienne, les imprimantes 3D peuvent produire des pièces de rechange qui, bien qu'aussi solides et durables que les composants traditionnels, peuvent être disponibles dans un délai beaucoup plus court.
Citant la réduction de poids comme un autre moteur pour l'adoption de la FA, British Airways affirme que l'impression 3D peut aider à réduire le poids d'une pièce jusqu'à 55 %. Même avec de petits composants, les effets peuvent être importants, car chaque kilogramme supprimé permet d'économiser des tonnes d'émissions de CO2 pendant la durée de vie d'un avion.
À l'avenir, la compagnie aérienne prédit qu'il sera possible d'imprimer en 3D un gamme beaucoup plus étendue de pièces de cabine, des couverts et sièges aux conteneurs à bagages et hublots d'avion.
4. Stratasys, SIA Engineering Company et Additive Flight Solutions impriment en 3D des milliers de pièces de cabine
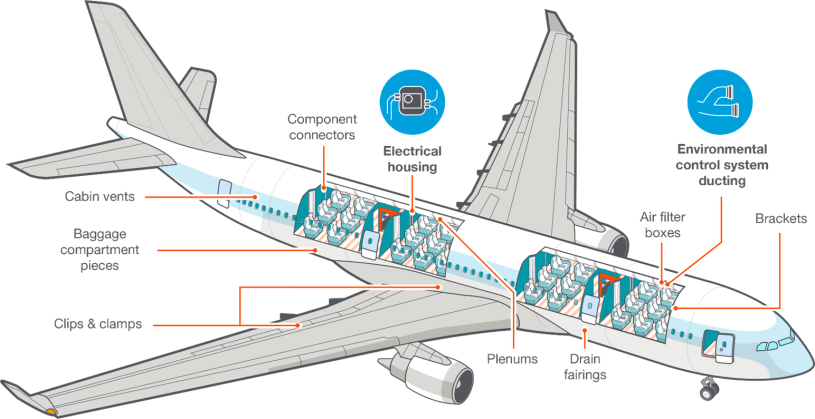
Stratasys, en collaboration avec SIA Engineering Company, qui fournit des services MRO d'avions, et un bureau de service d'impression 3D, Additive Flight Solutions, considèrent également la FA comme une technologie critique pour fournir des solutions aux compagnies aériennes.
Dans une joint-venture, formée en 2018, 3 partenaires utilisent à ce jour la technologie Stratasys FDM pour produire plus de 5 000 pièces certifiées pour les cabines d'avions.
L'une de ces pièces est un couvercle destiné à protéger les contrôleurs de siège, empêchant les passagers d'appuyer accidentellement sur les boutons. L'une des principales raisons du choix du processus de FA par rapport à un autre plus traditionnel est la possibilité de produire une commande de faible volume de ces couvertures plus rapidement et de manière plus rentable.
Dans un autre exemple, l'équipe a imprimé en 3D un clip pour retenir les rideaux des avions qui se détachaient trop souvent. Il existe 7 conceptions différentes pour ces couvertures/rideaux, ce qui signifie que l'équipe a dû personnaliser les couvertures d'extrémité des tringles à rideaux pour chacune des conceptions. L'impression 3D est beaucoup plus flexible que les autres technologies pour permettre un tel niveau de personnalisation.
De plus, l'impression 3D a été appliquée pour produire un loquet de niveau de sécurité pour les portes de secours du Boeing 787. La pièce est un composant essentiel destiné à garantir que les portes de secours ne s'ouvrent pas pendant que l'avion est au sol, créant un risque de blessures, car les toboggans d'évacuation pourraient être déclenchés accidentellement.
D'autres produits créés étaient des supports pour le dessous du siège passager, un plateau à cocktail imprimé en 3D, des supports pour la salle de bain distributeurs de savon et de désinfectant.
Toutes les pièces doivent répondre à des exigences strictes, telles que la résistance thermique et les indices de flamme, de fumée et de toxicité (FST) pour les intérieurs d'avion.
Tant d'applications, déjà développées par l'équipe et installées dans des avions commerciaux, indiquent que l'avenir des intérieurs d'avions est étroitement lié à la maturation des technologies d'impression 3D.
Normalisation de la FA pour les pièces de cabine
Cela dit, il n'y a pas d'avenir pour l'impression 3D dans l'industrie aéronautique sans standardisation. Sans surprise, le manque de normes et de certification reste un goulot d'étranglement massif dans l'utilisation de la FA pour les pièces de cabine d'avion.
'Dans l'aérospatiale, si vous n'avez pas de norme contre laquelle vous pouvez certifier une pièce, ou généralement plusieurs normes, alors vous ne pouvez pas la mettre sur une plate-forme aérospatiale' , a déclaré Matthew Donovan, maintenant ancien ingénieur principal pour la fabrication additive chez Oerlikon, dans une interview avec AMFG.
Sans les bonnes normes en place, les entreprises aérospatiales ne pourront pas utiliser la technologie avec la même confiance que les méthodes de fabrication traditionnelles.
Le manque de normes à l'échelle de l'industrie pour les matériaux, les processus, l'évaluation de la qualité et la conception de FA, ainsi que les données limitées sur le traitement des matériaux, entraînent des périodes de certification plus longues.
Actuellement, les compagnies aériennes et les entreprises fabriquant des pièces pour avions certifient les pièces pièce par pièce, ce qui est une entreprise coûteuse et chronophage.
Heureusement, il y a une forte pression pour développer les normes, les politiques et les directives pour l'application de la FA pour les composants d'avion.
Des autorités, comme la Federal Aviation Administration (FAA) et l'aviation européenne La Safety Agency (EASA) travaille avec l'industrie de la fabrication additive et les organisations de développement de normes, telles que l'ASTM, la SAE et l'ISO, pour surmonter les défis actuels de la normalisation.
Un cahier des charges pour l'impression 3D polymère dans le secteur aérospatial, publié par SAE International, a été l'une des avancées récentes dans ce domaine.
Les spécifications, nommées AMS7100 :Fused Filament Fabrication Process et AMS7101 :Material for Fused Filament Fabrication, ont été développées spécifiquement pour le procédé FDM afin d'encourager l'adoption de l'impression 3D pour les pièces de cabine en plastique.
L'avenir de l'impression 3D pour les intérieurs d'avions
L'impression 3D est l'une des technologies clés qui aident les compagnies aériennes à maintenir les cabines d'avions à la pointe de l'innovation. La technologie améliore les opérations de MRO en permettant la production de pièces de rechange à faible volume et améliore l'expérience client grâce à des conceptions personnalisées de pièces de cabine.
Des centaines de composants intérieurs imprimés en 3D déjà installés dans des avions mettent en évidence le potentiel et la valeur que la technologie apporte à l'industrie aérospatiale. Il est désormais crucial de se concentrer sur l'extension de l'utilisation de l'impression 3D, grâce à la collaboration et au développement de normes, pour pouvoir utiliser ce potentiel au maximum.
impression en 3D
- Les émirats adopteront la technologie d'impression 3D pour les pièces d'avion
- L'application en vedette :l'impression 3D pour les implants médicaux
- Spécialiste de l'application :impression 3D pour la dentisterie numérique et la fabrication d'aligneurs transparents
- Spécialiste de l'application :Impression 3D pour la fabrication de vélos
- L'application en vedette :l'impression 3D pour les roulements
- L'application en vedette :l'impression 3D pour les échangeurs de chaleur
- L'application en vedette :l'impression 3D dans l'industrie ferroviaire
- L'application en vedette :5 composants électroniques pouvant bénéficier de l'impression 3D
- 10 matériaux les plus solides pour l'impression 3D