L'application en vedette :l'impression 3D pour les implants médicaux
[Crédit image :Santé Canada]
Créer des implants osseux mieux ajustés, plus durables et plus performants est une quête permanente pour les orthopédistes et les chirurgiens. L'impression 3D contribue énormément aux avancées dans ce domaine.
La technologie permet aux fabricants d'implants de créer des implants avec des fonctionnalités améliorées et plus personnalisés pour les besoins spécifiques des patients. De plus, l'impression 3D ouvre la porte à des implants personnalisés qui peuvent être créés sur le lieu des soins.
Cette semaine, nous continuons notre série Spotlight sur les applications d'impression 3D en examinant l'utilisation de l'impression 3D pour les implants médicaux, ainsi que les avantages et les applications actuelles de la technologie.
Jetez un œil aux autres applications couvertes dans cette série :
Impression 3D pour échangeurs de chaleur
Impression 3D pour roulements
Impression 3D pour la fabrication de vélos
Impression 3D pour la dentisterie numérique et la fabrication d'aligneurs transparents
Les fusées imprimées en 3D et l'avenir de la fabrication d'engins spatiaux
Impression 3D pour la fabrication de chaussures
Impression 3D pour composants électroniques
Impression 3D dans l'industrie ferroviaire
Lunettes imprimées en 3D
Impression 3D pour la production de pièces finies
Impression 3D pour supports
Impression 3D pour pièces de turbine
Comment l'impression 3D permet des composants hydrauliques plus performants
Comment l'impression 3D soutient l'innovation dans l'industrie de l'énergie nucléaire
Le marché de l'impression 3D médicale en 2019
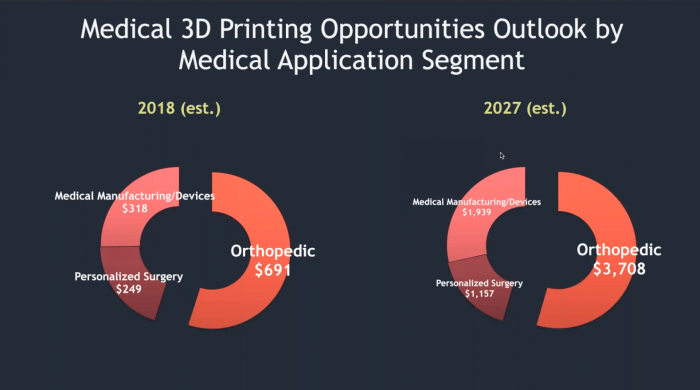
Les implants orthopédiques - des dispositifs médicaux utilisés chirurgicalement pour remplacer une articulation ou un os manquant - ne sont qu'une des opportunités offertes par l'impression 3D à l'industrie médicale.
Le marché de l'impression 3D orthopédique était évalué à 691 millions de dollars en 2018 et devrait, selon SmarTech Analysis, devenir un marché de 3,7 milliards de dollars d'ici 2027.
Bien que la fabrication d'implants soit un marché assez nouvelle application pour l'impression 3D - elle a été utilisée pour la première fois vers 2007 - elle a connu une croissance rapide au cours de la dernière décennie.
En 2010, l'un des premiers à avoir adopté la technologie d'impression 3D métallique par fusion par faisceau d'électrons (EBM) d'Arcam a reçu les premières approbations de la FDA pour les implants imprimés en 3D. Sept ans plus tard, plus de 300 imprimantes 3D dans le monde produisaient des produits orthopédiques.
Aujourd'hui, la technologie est utilisée pour créer des prothèses articulaires de la hanche et du genou, des implants de reconstruction crânienne et des implants rachidiens. En 2019, plus de 600 000 implants devraient être produits à l'aide de l'impression 3D. D'ici 2027, ce nombre devrait dépasser les 4 millions.
Avec une telle opportunité de croissance, il n'est pas surprenant que tous les principaux fabricants de dispositifs médicaux adoptent de plus en plus la technologie d'impression 3D.
Stryker, l'une des plus grandes sociétés de technologie médicale au monde, a récemment lancé ses propres implants imprimés en 3D, y compris la cage lombaire postérieure incurvée Tritanium TL imprimée en 3D. Cet implant rachidien à corps creux a reçu l'approbation de la FDA en mars 2018.
A côté de Stryker, d'autres fabricants d'appareils orthopédiques notables comme DePuy Synthes, une filiale de Johnson &Johnson, et Medtronic investissent massivement dans l'impression 3D. Ce dernier a lancé une plateforme d'impression 3D, TiONIC Technology, en mai 2018, dans le but de permettre des conceptions plus complexes et des technologies de surface intégrées pour les implants chirurgicaux rachidiens.
En plus des fabricants de dispositifs médicaux établis, des startups médicales ont également émergé au cours de la dernière décennie, développant des approches propriétaires d'implants orthopédiques imprimés en 3D.
Parmi eux se trouvent des sociétés comme Osseus Fusion Systems, Nexxt Spine, 4WEB Medical et SI-BONE. Certains des produits de ces sociétés ont déjà reçu l'approbation de la FDA et ont été utilisés pour traiter avec succès des patients.
De toute évidence, il y a eu une trajectoire ascendante pour les implants imprimés en 3D au cours de la dernière décennie. Mais qu'est-ce qui rend cette technologie si utile pour les implants médicaux ?
Les avantages des implants imprimés en 3D
Flexibilité de conception
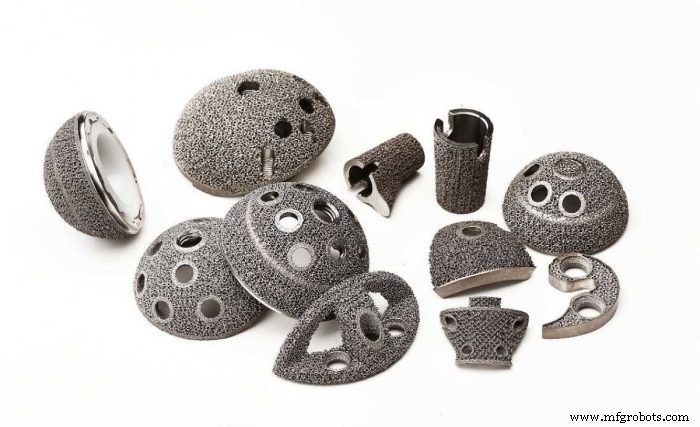
Avec l'impression 3D, il est possible de créer des conceptions complexes qui seraient autrement difficiles à réaliser avec les technologies traditionnelles. Les fabricants d'implants peuvent utiliser cet avantage pour produire des implants avec des caractéristiques de conception complexes telles que des structures trabéculaires.
L'os trabéculaire est l'un des deux types de tissus osseux présents dans le corps humain. Il a une structure spongieuse et poreuse qui peut être difficile à imiter dans un implant. Traditionnellement, les fabricants d'implants utilisent un revêtement spécial pour créer une structure trabéculaire sur l'implant. Cependant, cela comporte un risque de délamination et d'échec de l'implant.
Avec l'impression 3D, d'autre part, les implants à structure trabéculaire peuvent être produits directement, évitant ainsi le processus de revêtement. Plus important encore, la structure trabéculaire et poreuse intégrée dans un implant imprimé en 3D crée un implant plus solide avec un risque réduit de délaminage.
Une telle flexibilité de conception est offerte par les technologies d'impression 3D métalliques comme la fusion sélective au laser ou l'électron Faisceau de fusion. Ces technologies appliquent une puissante source d'énergie comme un laser (SLM) ou un faisceau d'électrons (EBM) sur une fine couche d'une poudre biocompatible comme le titane.
En répétant ce processus sur des centaines de couches, il est possible de créer un implant complexe qui s'adaptera à la structure osseuse humaine beaucoup plus efficacement que les implants traditionnels.
Un autre avantage important des implants poreux imprimés en 3D est l'amélioration de l'ostéointégration.
L'ostéointégration est un processus qui permet à un implant de devenir une partie permanente du corps. La structure trabéculaire poreuse permet à un os de se développer à l'intérieur des pores, renforçant davantage la liaison entre l'implant et l'os existant.
Protection contre le stress réduite
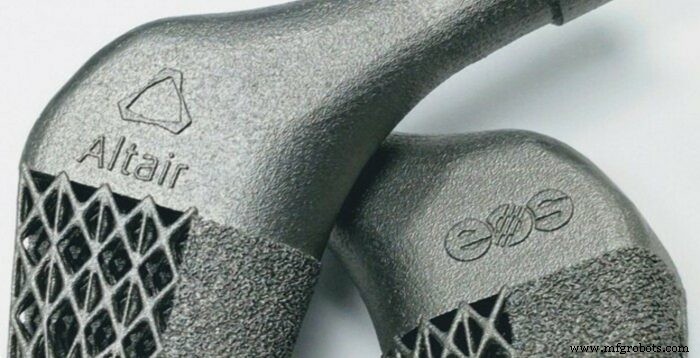
En outre, les fabricants de dispositifs médicaux peuvent concevoir des implants qui imitent la rigidité et la densité osseuses d'un patient. En plus d'améliorer l'ostéointégration, les implants imprimés en 3D peuvent réduire la protection contre le stress et améliorer encore la fonction physique.
La protection contre les contraintes fait référence aux phénomènes par lesquels les implants métalliques éliminent les contraintes typiques de l'os d'un patient. Le résultat est la réduction de la densité osseuse, ce qui affaiblit l'os. La protection contre le stress peut entraîner des fractures et des luxations. Pour cette raison, concevoir un implant aussi près que possible du tissu osseux du patient est essentiel pour réduire la protection contre le stress et éliminer ces effets indésirables.
Dans un exemple récent, la société informatique Altair a combiné l'impression 3D et un logiciel d'optimisation de la topologie pour créer un implant de tige de hanche amélioré.
En entrant des paramètres tels que la taille, le poids et la charge attendue que l'implant supporterait, un logiciel d'optimisation de la topologie a été utilisé pour créer une nouvelle conception pour un implant de hanche. La conception optimisée répartit les contraintes et les contraintes d'une manière plus efficace qu'un implant générique.
En outre, un logiciel d'optimisation de la topologie a permis de déterminer où le matériau pouvait être remplacé par des structures en treillis pour alléger l'implant.
Lorsqu'il a été testé, l'implant optimisé a offert une réduction de la résistance aux contraintes de 50,7 %. Dans le même temps, sa limite d'endurance est passée à environ 10 millions de cycles. Cela signifie que l'implant de hanche pourrait supporter le jogging de Los Angeles à New York et retour — deux fois.
Impression 3D d'implants spécifiques au patient
Dans les cas plus complexes, les implants prêts à l'emploi ne peuvent souvent pas fournir la flexibilité nécessaire requise. L'impression 3D pourrait aider dans de tels cas, offrant la possibilité de personnaliser et de personnaliser les dispositifs médicaux, y compris les implants.
Pour produire un implant spécifique au patient, les fabricants utilisent les données acquises à partir d'un scan du patient, comme une tomodensitométrie (TDM) ou une imagerie par résonance magnétique (IRM). Les données du patient sont ensuite importées dans la CAO, préparées pour la production, imprimées en 3D et finies.
L'utilisation d'un implant personnalisé imprimé en 3D offre la possibilité de réduire le temps chirurgical et d'améliorer l'ajustement de l'implant.
Actuellement, l'impression 3D peut être utilisée pour créer des implants crâniens et maxillaires personnalisés où les exigences esthétiques sont aussi importantes que la fonctionnalité.
Par exemple, un garçon chinois de 10 ans a reçu un implant de mâchoire imprimé en 3D en 2018. Il avait une tumeur à la mâchoire qui n'aurait pas pu être retirée sans provoquer une malformation faciale importante.
L'équipe chirurgicale a conclu qu'une reconstruction faciale conventionnelle était trop dangereuse pour un patient aussi jeune. À la recherche d'une meilleure solution, ils se sont tournés vers l'impression 3D, en utilisant des modèles numériques de la mâchoire du garçon pour concevoir un implant en titane sur mesure parfaitement adapté.
Selon les chirurgiens, l'implant de mâchoire était facile à installer car il était basé sur l'anatomie du patient. Trois mois après l'intervention, l'implantation s'est avérée réussie, la mâchoire étant bien alignée et une grande quantité de tissu se développant.
3 exemples d'implants imprimés en 3D
Un implant de hanche imprimé en 3D permet l'escalade extrême
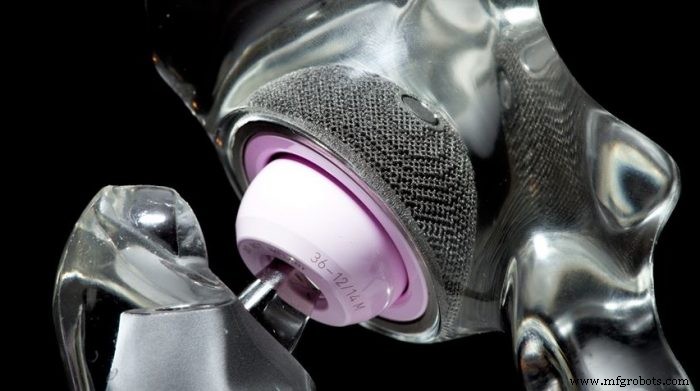
Romano Benet et sa femme, Nives Meroi, gravissent depuis de nombreuses années les montagnes les plus dangereuses du monde. En 2017, l'équipe d'alpinisme est devenue le premier couple à gravir les 14 plus hauts sommets du monde. Cependant, réaliser cet exploit aurait probablement été impossible sans l'aide de l'impression 3D.
Benet souffrait d'une nécrose avasculaire bilatérale qui, pour l'essentiel, conduit à un collapsus osseux.
Lors du premier diagnostic, Benet et sa femme étaient à trois sommets de boucler le circuit mondial des 14 montagnes. Pour continuer leur voyage, l'alpiniste avait besoin d'un implant stable qui lui permettrait de récupérer rapidement.
Pour cette raison, le chirurgien de Benet a décidé d'opter pour un implant imprimé en 3D.
L'implant, connu sous le nom de marque de cupule Delta Trabecular Titanium (TT), a été produit par la société italienne de dispositifs médicaux, Lima Corporate, à l'aide de l'imprimante 3D Arcam' EBM.
En combinant la technologie Trabecular Titanium de Lima et l'impression 3D, il a été possible de créer des implants imitant la structure poreuse de l'os naturel.
Grâce à cette structure trabéculaire, un implant imprimé en 3D peut résister aux contraintes mécaniques lors d'une activité rigoureuse. Le chirurgien de Benet, qui avait implanté des cupules TT à quelques reprises sur d'autres patients, pensait qu'en plus d'offrir une grande stabilité et résistance, les implants imprimés en 3D ont également le potentiel de durer au-delà de la durée de vie des implants conventionnels.
Lorsque Benet a reçu son premier implant non imprimé en 3D, il avait souffert de plusieurs mois d'inactivité avant de recommencer à grimper. Avec un implant imprimé en 3D, l'alpiniste a pu reprendre son activité après deux mois et demi.
En fin de compte, l'implant imprimé en 3D a fait son travail :il a permis à Benet de récupérer rapidement et de terminer avec succès sa quête pour atteindre les trois derniers sommets d'altitude.
Osseus Fusion Systems :en route vers des implants métalliques personnalisés

Fondée en 2012, Osseus Fusion Systems est une société basée aux États-Unis qui se concentre sur le développement de produits médicaux avancés pour les blessures à la colonne vertébrale.
Pour améliorer la qualité et la fonctionnalité de ses produits, Osseus a développé une technologie d'impression 3D propriétaire appelée PL3XUS.
La technologie est basée sur l'impression 3D par fusion sur lit de poudre, en particulier la fusion laser sélective (SLM), et permet de créer des implants en titane poreux à 80 %, optimisés pour la fusion osseuse et la fixation biologique (processus par lequel un os vivant se fixe de façon permanente à la surface de l'implant).
En août 2018, Osseus a obtenu l'autorisation FDA 510(k) pour Aries, sa famille de dispositifs de fusion intersomatique lombaire fabriqués de manière additive. La famille d'implants Aries est conçue pour aider les chirurgiens à soulager les maux de dos et à réduire le temps de récupération de la colonne vertébrale.
Plus tôt cette année, le produit Aries d'Osseus a, pour la première fois, été mis en pratique par Joseph Spine, un centre de chirurgie du rachis et de la scoliose. La technologie PL3XUS a permis de concevoir l'implant avec une architecture similaire à l'os d'un patient, facilitant la croissance osseuse.
Au cours des deux prochaines années, Osseus prévoit de lancer des dispositifs personnalisés basés sur les tomodensitogrammes, les radiographies et les IRM des patients.
Avec cette prochaine étape, la société envisage de permettre aux hôpitaux de fournir des soins de qualité supérieure aux patients et, en fin de compte, d'améliorer davantage les résultats de la chirurgie pour les patients.
Impression 3D d'implants avec des thermoplastiques hautes performances
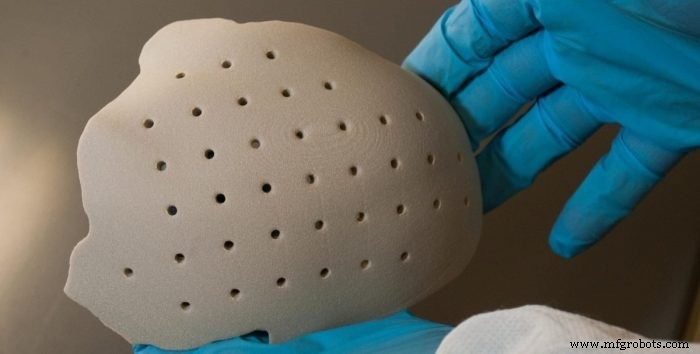
En plus du titane et d'autres métaux biocompatibles, l'impression 3D peut être couplée à des polymères comme le PEEK et le PEKK pour produire des implants. Ces thermoplastiques sont connus pour leur haute résistance et leur biocompatibilité, et offrent également quelques avantages par rapport aux implants métalliques, tels que des coûts réduits et une radiotransparence.
En 2013, Oxford Performance Materials (OPM) est devenu la première entreprise à recevoir l'autorisation de la FDA pour un implant crânien PEKK imprimé en 3D sur mesure. En 2017, OPM avait expédié plus de 1 400 implants crâniens et reçu les autorisations de la FDA pour deux autres dispositifs :les implants maxillo-faciaux et rachidiens.
La société utilise la technologie de frittage laser sélectif, qui alimente la plate-forme propriétaire OsteoFab® d'OPM pour le développement et la production d'implants. Dans un exemple, cette plate-forme a permis à un implant crânien spécifique au patient d'être conçu, fabriqué, testé et expédié depuis OPM en seulement 3 jours ouvrables. En moins d'une semaine, les chirurgiens ont réalisé l'opération avec succès, sans aucune modification de coupe ou de forage pour remodeler l'implant.
Impression 3D pour implants médicaux :avoir un impact
La biocompatibilité, la capacité de charge et la durabilité sont les exigences fondamentales des implants orthopédiques. L'impression 3D répond pleinement à ces exigences tout en améliorant la fonctionnalité et l'ajustement des implants.
Cela peut principalement être attribué à la capacité de la technologie à créer des formes complexes comme des structures poreuses, qui aident le corps d'un patient à s'adapter à un implant plus rapidement et avec moins de complications.
À l'avenir, l'impression 3D pour implants continuera d'évoluer. Un domaine de recherche en cours particulièrement passionnant est la combinaison d'implants et de capteurs imprimés en 3D. En développant des implants alimentés par des capteurs, les prestataires de soins de santé peuvent potentiellement améliorer les résultats des patients de manière significative.
Les capteurs intégrés pourraient collecter des données telles que la température autour de l'implant, le mouvement et la contrainte exercée sur l'implant. Cela permettra aux chirurgiens de réagir rapidement à tout problème potentiel et d'adapter le traitement aux besoins de chaque patient.
Renishaw, un fabricant britannique d'imprimantes 3D métal, et Western University ont déjà mis en place le centre Additive Design in Surgical Solutions (ADEISS) sur le campus de l'université. Le centre rassemble des universitaires et des cliniciens pour travailler sur le développement de nouveaux dispositifs médicaux imprimés en 3D comme ceux décrits ci-dessus.
De toute évidence, la technologie d'impression 3D est en train de s'implanter fortement dans le segment de l'orthopédie.
Cependant, la technologie devra mûrir pour vraiment libérer son potentiel pour les implants créés sur mesure et produits sur le lieu des soins.
Certes, seul un faible pourcentage des implants sont actuellement créés sur mesure avec l'impression 3D. Bien que la technologie recèle un potentiel énorme, les questions relatives à la normalisation et à la réglementation doivent encore être résolues.
Cela dit, c'est dans la création d'implants médicaux personnalisés que la technologie pourrait avoir le plus d'impact et permettre à un plus grand nombre de personnes de bénéficier de soins de santé personnalisés. Nous pensons que cette direction connaîtra un essor important dans les années à venir.
Dans notre prochain article, nous verrons comment l'impression 3D peut améliorer la fabrication de fusées. Restez à l'écoute !
impression en 3D
- Micro poudres de tantale pour application médicale
- Spécialiste de l'application :impression 3D pour la dentisterie numérique et la fabrication d'aligneurs transparents
- Spécialiste de l'application :Impression 3D pour la fabrication de vélos
- L'application en vedette :l'impression 3D pour les roulements
- L'application en vedette :l'impression 3D pour les échangeurs de chaleur
- L'application en vedette :l'impression 3D dans l'industrie ferroviaire
- L'application en vedette :5 composants électroniques pouvant bénéficier de l'impression 3D
- L'application en vedette :l'impression 3D pour les chaussures
- 10 matériaux les plus solides pour l'impression 3D