Entretien d'expert :Exploration de la technologie d'impression polymère à la lumière du jour de Photocentric avec le directeur général Paul Holt
Photocentric est un fabricant britannique d'imprimantes et de matériaux 3D. La société, fondée en 2002, est connue pour son approche unique et innovante de l'impression 3D, qu'elle appelle Daylight Polymer Printing.
Contrairement aux technologies similaires à base de résine comme la stéréolithographie (SLA) ou le traitement numérique de la lumière (DLP), la technologie Daylight Polymer Printing de Photocentric n'utilise pas de laser UV ou de projecteur pour produire des pièces imprimées en 3D.
Au lieu de cela, sa technologie utilise la lumière des écrans LCD pour créer des pièces imprimées en 3D en durcissant couche par couche la résine photopolymère liquide. Ces résines Daylight, également fabriquées par Photocentric, se solidifient lorsqu'elles sont exposées à la lumière des écrans LCD de ses imprimantes.
Notamment, les imprimantes 3D de Photocentric utilisent des écrans LCD de mobiles, de télévisions et de tablettes, ce qui les rend plus abordables que les technologies SLA/DLP, mais offrant la même qualité.
Pour en savoir plus sur la technologie unique de Photocentric et des exemples d'utilisation, nous discutons avec Paul Holt, directeur général de Photocentric.
Pouvez-vous me parler de Photocentric et de votre mission en tant qu'entreprise ?
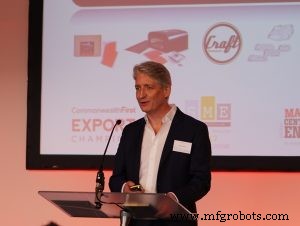
Photocentric a été fondée à l'origine pour fabriquer un ensemble breveté de photopolymères. Depuis lors, notre entreprise s'est développée pour pénétrer une variété de marchés, et nous appliquons nos innovations photopolymères à un large éventail d'industries, y compris l'impression 3D.
La technologie photopolymère innovante est au cœur même de notre activité . En 2005, nous avons inventé le concept d'utilisation d'écrans LCD pour l'impression 3D. En 2014, nous avons développé notre premier prototype LCD. Nous venons de lancer notre septième imprimante LCD, et d'autres sont en préparation.
Les utilisateurs de notre technologie comprennent des créateurs de bijoux cherchant à accélérer la production ou à fabriquer des pièces géométriques uniques avec l'impression 3D, des prothésistes dentaires qui ont besoin d'une imprimante haute capacité et précise pour des modèles et fabricants spécifiques au patient, des ingénieurs et les inventeurs qui souhaitent transformer leurs concepts de conception en prototypes tangibles ou en pièces fonctionnelles d'utilisation finale.
En fin de compte, notre mission est de changer la fabrication mondiale - pas seulement l'impression 3D. Nous y parvenons en rendant l'impression 3D abordable, à grande échelle et fonctionnelle, et en permettant une fabrication de masse personnalisée à l'échelle mondiale.
Comment fonctionne votre technologie Daylight Polymer Printing et qu'est-ce qui la distingue des autres machines à base de résine disponibles sur le marché ?
Daylight Polymer Printing utilise notre résine photopolymère liquide Daylight formulée en interne. La résine est durcie couche par couche lorsqu'elle est exposée à nos imprimantes 3D à écran LCD haute résolution.
Une pièce est créée une fois que chaque couche de résine a été durcie par la lumière émise par l'écran LCD.
L'un des principaux différenciateurs de notre technologie est la qualité de nos machines. Chaque étape de nos produits passe par une procédure de contrôle qualité approfondie pour garantir que nos clients obtiennent la meilleure expérience et le meilleur produit disponible.
En outre, notre approche est conçue pour réduire le coût de l'impression 3D et permettre le plus large application de la technologie. Les écrans de tous les jours, comme les écrans de téléphone ou de télévision, sont devenus le cœur de nos imprimantes 3D. Ces écrans LCD sont des appareils d'imagerie numérique fiables et peu coûteux.
Cela, associé à notre résine photopolymère, signifie que nous pouvons offrir un package d'impression 3D abordable. De nombreuses sociétés d'impression 3D font l'ingénierie puis sous-traitent la chimie - nous faisons tout en interne.
Nous proposons également la plus grande imprimante à écran LCD à volume de construction sur le marché, avec notre machine Liquid Crystal Magna , ce qui nous permet d'atteindre un haut niveau de précision à grande échelle.
Quelles industries pourraient bénéficier le plus de votre technologie ?
Nous sommes en mesure de fournir des solutions d'impression 3D aux industries comme la dentisterie et la bijouterie, où les applications petites et précises sont typiques, ainsi que de fournir des solutions aux industries où des composants et des prototypes à grande échelle sont nécessaires.
En particulier, nous pensons qu'il existe un énorme potentiel dans le domaine de la dentisterie pour Photocentric. Après avoir visité le salon IDS 2019 cette année, nous avons constaté une énorme demande d'impression LCD dans ce secteur.
C'est pourquoi une grande partie de notre recherche et développement est consacrée à la production de produits dentaires spécifiques, tels que Liquid Crystal Dental - notre imprimante dentaire optimisée pour le fauteuil ou le laboratoire dont la sortie est prévue plus tard cette année.
D'autre part, notre technologie est également adaptée aux applications de gros composants dans les industries de l'automobile et du divertissement. La portée est énorme, surtout compte tenu de la polyvalence de nos développements d'imprimantes LCD.
Pourriez-vous partager une ou deux applications réussies sur la façon dont votre technologie a été utilisée ?
Un client unique est Quimbaya Orfebreria, un orfèvre argentin qui produit des pièces artisanales spéciales pour ses clients.
Alors que la demande commençait à l'emporter sur l'offre et qu'ils étaient confrontés à des limitations de conception, Quimbaya a décidé de mettre de côté les méthodes traditionnelles et d'introduire l'impression 3D dans leur flux de travail. Ils ont choisi d'utiliser notre imprimante de bureau haute résolution LC Precision 1.5.
En utilisant l'impression 3D, ils ont pu réduire leur temps de fabrication de 80%. Leur production a également augmenté de 400 % et ils sont désormais en mesure de produire des conceptions plus complexes et plus complexes pour leurs clients.
Plus près de chez nous au Royaume-Uni, un autre exemple est l'hôpital orthopédique Robert Jones et Agnes Hunt à Oswestry, un hôpital orthopédique spécialisé avec une longue tradition d'innovation dans le traitement de leurs patients.
Avec l'utilisation de modèles imprimés sur le LC Pro, le prédécesseur du LC Magna, un chirurgien a pu aider à planifier une ostéotomie fémorale complexe chez un patient juvénile qui avait une déformation de la hanche. Les coupes nécessaires ont été planifiées à l'avance, ainsi que le préformage de l'implant nécessaire pour une correction réussie. Ces impressions 3D ont finalement permis au NHS d'économiser plus de 1 000 £ et d'économiser une heure sur le théâtre.
Quels sont les défis à relever pour accélérer l'adoption de la fabrication additive ?
Le plus grand défi est le manque de propriétés matérielles.
Lorsque nous avons commencé dans l'impression 3D, nous avons constaté que trois problèmes clés empêchaient l'adoption plus large de l'impression 3D :1) le coût extrêmement élevé, 2) le manque d'évolutivité de la fabrication et 3) le manque des propriétés fonctionnelles.
Les écrans LCD ont certainement changé le premier problème, avec des milliers d'écrans mobiles à moindre coût offrant une impression à très haute résolution. Les écrans LCD grand format ont commencé à répondre au problème de l'échelle, cependant, la question des propriétés des matériaux n'a pas encore été correctement traitée.
Nous travaillons actuellement avec BASF pour développer la plus large gamme de résines offrant des propriétés durables pouvant être utilisées fonctionnellement dans l'industrie.
Comment voyez-vous les technologies de fabrication additive et l'industrie évoluer ?
Pour nous, les écrans LCD sont vraiment perturbateurs et changeront la donne pour l'impression SLA.
Grâce aux écrans LCD, nous pouvons permettre la fabrication en série de pièces sur mesure, soit à l'aide de grands écrans uniques qui peuvent produire de grandes pièces en une fraction du temps des technologies utilisant des lasers ou des projecteurs, ou une série de plus petits , des écrans à plus haute résolution qui produisent de nombreuses pièces plus petites.
Je vois aussi toutes les machines devenir automatiques, supprimant le besoin d'une intervention manuelle. Je m'attends à ce que les pièces en plastique fonctionnelles imprimées en 3D soient utilisées dans les lignes de production d'ici 2 ans, car les avantages de l'absence d'outillage, de conceptions personnalisées et de liberté de géométrie sont utilisés industriellement.
L'autre changement que je vois transformer la fabrication de pièces en céramique et en métal est la création du corps vert via l'impression 3D avec un frittage ultérieur pour fournir des céramiques et des métaux solides et viables. Ce processus est à la fois moins énergivore et moins coûteux, permettant une fabrication sur mesure plus large de ces matériaux.
Photocentric a récemment annoncé sa nouvelle imprimante 3D Liquid Crystal Magna. Pourriez-vous nous expliquer certaines des caractéristiques et les avantages de cette machine ?
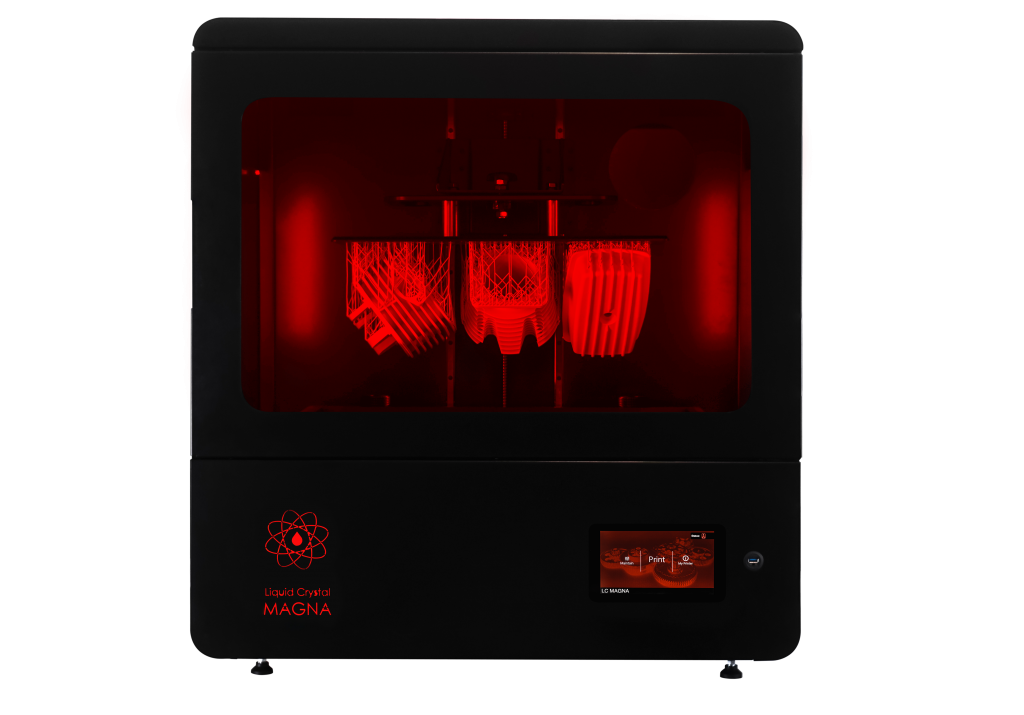
La vision derrière notre machine LC Magna est de permettre la fabrication en série sur mesure et le prototypage de grands composants à un prix rentable. LC Magna peut créer des centaines de pièces personnalisées à des coûts très bas.
LC Magna a un grand volume de fabrication et offre une impression très précise, ce qui le rend idéal pour la fabrication de masse personnalisée. Son volume de construction est de 510 mm x 280 mm x 350 mm, ce qui en fait la plus grande imprimante 3D à écran LCD actuellement disponible.
Le LC Magna dispose également d'un écran 23,4" 4K Ultra HD, couplé à un rétroéclairage sur mesure. Ces deux éléments fonctionnent ensemble pour garantir une précision et des détails d'impression extrêmement élevés. La luminosité du rétroéclairage permet à l'imprimante d'exposer des couches de 100 microns en 3 à 8 secondes.
La machine est principalement destinée aux techniciens dentaires, aux concepteurs de produits, aux ingénieurs et aux fabricants, qui pourront augmenter leur débit, accélérer les productions d'assemblage et réduire les délais.
Par exemple, un fabricant de lunettes peut désormais produire en série 36 montures optiques en 12 heures, soit moins de 20 minutes pour chaque ensemble. Un prothésiste dentaire qui a besoin d'un volume élevé de modèles spécifiques au patient peut désormais imprimer 46 arcades plates en un peu plus d'une heure - celles-ci coûtent moins de 1,06 £ par arcade lorsqu'elles sont utilisées avec notre résine pour modèle dentaire interne Daylight.
Que réservent les 12 prochains mois pour Photocentric ?
Nous pensons que l'industrie de l'impression 3D ouvre de nombreuses opportunités - elle a un impact sur tous les aspects de la fabrication. Compte tenu de la grande variété de possibilités inexplorées dans ce domaine, nous sommes fortement impliqués dans une série de projets passionnants.
Par exemple, nous travaillons sur une gamme de nouvelles imprimantes 3D pour produire des plastiques, des céramiques et les métaux.
Nous élargissons également notre équipe, en particulier dans le département R&D, pour approfondir l'impression 3D de métaux et de céramiques. Cela aura un impact considérable sur notre approche de la fabrication des matériaux.
Pour en savoir plus sur Photocentric, visitez :https://photocentricgroup.com/
impression en 3D
- Entretien avec un expert :professeur Neil Hopkinson, directeur de l'impression 3D chez Xaar
- Entretien avec un expert :Philip Cotton, fondateur de 3Dfilemarket.com
- Entretien avec un expert :Spencer Wright de pencerw.com et nTopology
- Entretien avec un expert :Dr Alvaro Goyanes de FabRx
- ACEO® dévoile une nouvelle technologie pour l'impression 3D avec du silicone
- Entretien avec un expert :Dr Bastian Rapp de NeptunLab
- Entretien d'experts :Felix Ewald, PDG de DyeMansion
- Entretien avec un expert :Ibraheem Khadar de Markforged
- Entretien d'experts :Guillaume de Calan, PDG de Nanoe, sur l'avenir de l'impression 3D céramique