Comment mettre en œuvre un plan de maintenance productive totale (TPM)
La mise en œuvre réussie et durable de la maintenance productive totale (également connue sous le nom de TPM) devrait être une préoccupation majeure pour tout directeur d'usine ou chef de production consciencieux. Le TPM réduit les temps d'arrêt, les arrêts et les pannes, et réduit la probabilité que les produits souffrent de défauts de qualité pendant le processus de fabrication.
Pourquoi le TPM est-il un outil si efficace ? En bref, parce que des opérateurs responsabilisés qui jouent un rôle actif dans l'inspection et la maintenance de leurs propres équipements contribueront toujours à améliorer la production et la fiabilité des équipements.
Au fil des ans, des études ont confirmé la corrélation positive entre la mise en place d'un programme TPM et la performance globale de fabrication. Certains résultats indiquent qu'une entreprise peut réduire la perte de production d'environ 20 % en exécutant un plan de maintenance productif total. Néanmoins, une question importante se pose :comment une entreprise peut-elle efficacement mettre en œuvre le TPM ? ? Les informations suivantes répondront à cette question.
Vous souhaitez économiser sur les coûts de maintenance ?
Vous pouvez accéder à des ressources et des documents de recherche plus utiles ici.
Qu'est-ce que la maintenance productive totale ?
En guise d'examen, tout programme TPM implique au moins 8 concepts de base qui jouent un rôle important dans la détermination du succès final de l'initiative. Ces 8 notions sont :
-
Maintenance autonome
Cet élément fondamental du TPM se concentre sur la formation et l'habilitation du personnel de maintenance, comme les opérateurs de machines, à effectuer eux-mêmes la gestion de la maintenance de routine. -
Amélioration ciblée
Ce pilier de la TPM fait référence aux techniques de maintenance proactive :examiner un processus actuel de manière holistique et identifier les moyens de l'améliorer. -
Maintenance planifiée
Un programme de maintenance planifiée exploite les données historiques sur les temps d'arrêt et les analyses prédictives pour planifier les tâches de maintenance clés en fonction des taux de défaillance probables ou des temps d'inactivité anticipés. -
Maintien de la qualité
Le processus de maintenance de la qualité est conçu pour s'assurer que les tâches de maintenance réellement exécutées atteignent efficacement les objectifs généraux de détection des erreurs, de prévention des défauts et d'assurance qualité. -
Gestion précoce de l'équipement
Tirant parti des commentaires des opérateurs ayant une expérience pratique, la gestion précoce des équipements garantit que la conception de nouveaux équipements optimisera la durée de vie, l'accessibilité et la productivité des machines. -
Formation
Chaque programme TPM devrait inclure un élément de formation et d'éducation pour les opérateurs et les gestionnaires. -
Sécurité et santé
Tous les processus TPM doivent tenir compte des facteurs de sécurité et de santé afin de favoriser un environnement de travail sécurisé pour les opérateurs et les autres employés. -
Administration orientée TPM
Outre les considérations purement mécaniques, un programme TPM bien conçu prendra également en compte les fonctions administratives telles que le traitement des commandes et la gestion des plannings, et cherchera des moyens de les améliorer pour soutenir l'atelier de production.
Comment mettre en œuvre le TPM
Bien qu'un programme TPM doive être adapté aux besoins et circonstances spécifiques de l'entreprise, il existe 7 étapes de base pour mettre en œuvre TPM, comme indiqué ci-dessous :
1. Annoncer les plans de mise en œuvre du TPM
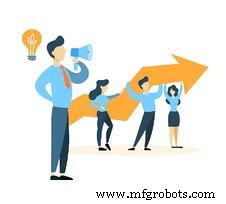
2. Identifier un domaine pour un programme pilote de TPM
Vous pouvez vous concentrer sur une pièce d'équipement qui serait la plus facile à améliorer, ou sur une zone de production qui s'est avérée problématique et qui doit être réparée afin d'améliorer rapidement la rentabilité. Dans cette étape initiale du processus TPM, identifiez les objectifs qui sont SMART :Spécifiques, Mesurables, Atteignables, Réalistes et Temporels.3. Concentrez-vous sur la restauration des équipements ciblés en parfait état de fonctionnement
Une fois que votre zone pilote a été identifiée, enregistrez une norme de base pour la productivité actuelle. Organisez et définissez votre plan de mise en œuvre du TPM . Utilisez la méthodologie 5S (Sort, Set, Shine, Standardize, Sustain). Concentrez-vous d'abord sur l'exécution d'un programme de maintenance autonome et offrez une formation aux opérateurs d'équipement au besoin. Tout comme un propriétaire de voiture peut économiser une somme importante sur les coûts de réparation en effectuant un entretien de routine de base, les entreprises peuvent également prolonger la durée de vie de la machine et identifier les problèmes mécaniques dès le début en permettant à leurs opérateurs de participer régulièrement aux procédures d'entretien de base.4. Commencer à mesurer l'efficacité globale de l'équipement (OEE)
Quelle que soit la manière dont vous décidez de suivre l'OEE, il est impératif que les heures d'arrêt imprévues soient documentées et qu'une raison soit donnée pour chaque occurrence. Fournir une catégorie pour « cause inconnue » ou « heure d'arrêt non attribuée » pour les cas où l'opérateur n'est pas sûr de la cause de l'arrêt. Au fil du temps, cela vous aidera d'abord à identifier principales causes de perte, qui à son tour conduit à l'étape 5 :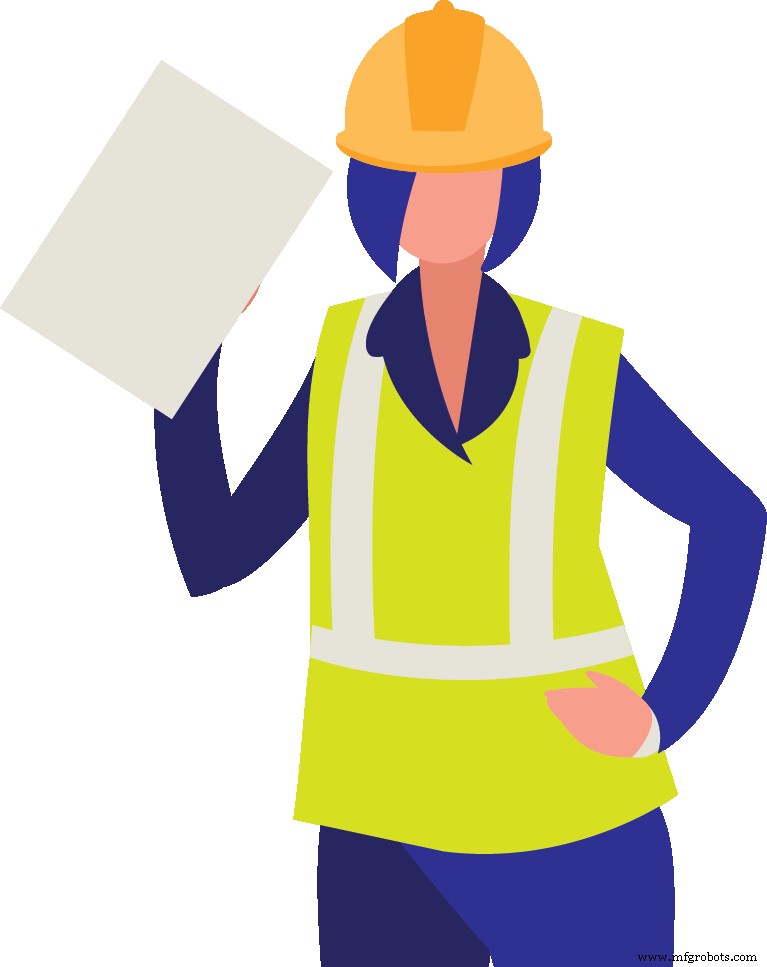
5. Traiter les principales causes de perte
Au cours de cette étape, vous devrez désigner une équipe interfonctionnelle d'environ 4 à 6 employés pour enquêter sur une cause majeure de temps d'arrêt . Cette équipe créera un plan pour éliminer la cause de la perte et planifiera l'heure d'arrêt prévue pour exécuter cette initiative. Par exemple, si vos pertes majeures proviennent de bourrages fréquents de remplisseurs, cette équipe examinera les processus actuels de l'opérateur et les options de réparation, créera un plan pour arrêter les bourrages, puis planifiera du temps pour mettre le plan en action. Une fois l'action désignée terminée, ils mesureront l'OEE à l'avenir et redémarreront le processus si nécessaire.
6. Mettre en œuvre une maintenance proactive
Dans cette étape, vous vous concentrez sur la prévention des pannes ou des temps d'arrêt. Identifiez les principaux "points douloureux" qui pourraient entraîner une défaillance de l'équipement , et créez un calendrier de maintenance préventive à intervalles réguliers. Enfin, instituez un processus de rétroaction qui vous permettra de surveiller en permanence l'efficacité de votre programme. Ce système de retour d'information peut inclure des journaux de maintenance, des audits mensuels ou bimensuels et une compilation de données issues de la thermographie et/ou de l'analyse des vibrations.
7. Mettre en œuvre des concepts TPM spécifiques selon les besoins
Par exemple, la gestion précoce de l'équipement devrait entrer en jeu lors de la conception et/ou de l'installation de nouvelles machines pour l'atelier de production. Peut-être que la conception de nouveaux équipements devrait être optimisée pour inclure une meilleure accessibilité, des procédures de nettoyage ou de lubrification plus faciles ou l'ajout de dispositifs de sécurité. D'un autre côté, s'il y a des problèmes d'approvisionnement ou des retards dans le traitement des ordres de travail, vous devez résoudre ces goulots d'étranglement administratifs dès que possible.Exploiter le TPM pour améliorer la gestion de la maintenance
La maintenance productive totale est un élément clé pour réduire les pertes de production dues aux temps d'arrêt. Un programme TPM efficace peut permettre aux employés de prendre des mesures proactives dans l'entretien des machines vitales ; cela permettra à son tour aux équipements de production de bénéficier d'une durée de vie fonctionnelle plus longue. La mise en œuvre du TPM contribuera également à réduire les défauts de qualité et les durées d'exécution sous-optimales.
Il existe de nombreux outils disponibles sur le marché, tels que les plateformes de gestion des actifs d'entreprise et les programmes associés, qui peuvent aider les entreprises à mettre en œuvre le TPM. En dernière analyse, bien qu'un plan de maintenance productif total nécessite des efforts pour une conception et une exécution correctes, les récompenses en valent bien l'investissement !
Entretien et réparation d'équipement
- Mettre en œuvre votre plan TPM :un guide étape par étape
- Comment conserver la maintenance en mode proactif
- Comment mettre en œuvre une maintenance productive totale
- Vodcast :introduction à la maintenance productive totale
- Comment créer un programme de maintenance électrique
- Unilever étend son programme Total Productive Maintenance avec l'aide d'Informance
- Comment les directeurs d'usine peuvent-ils planifier l'entretien régulier des machines
- Maintenance productive totale et IoT industriel
- Comment mettre en œuvre la maintenance centrée sur la fiabilité (RCM)