Défauts de fonderie :types, causes et remèdes
Dans cet article, nous allons en apprendre davantage sur les défauts de moulage, leurs causes et leurs remèdes. Les défauts sont un phénomène courant dans tout processus d'ingénierie. Il y a une telle limitation de tout processus, qui provoque des défauts. Une conception et un moulage appropriés peuvent donner un moulage sans défaut, mais en raison de certaines limitations de contrôle et d'interférences humaines, des défauts se produisent généralement. Grâce à une assistance appropriée sur le travail, nous pouvons minimiser les défauts de coulée. En règle générale, un produit de moulage approprié présente également des défauts, de sorte qu'une recherche est en cours dans l'industrie de la fonderie pour minimiser ces défauts. Ces défauts de coulée peuvent être découverts par les méthodes de test non destructives qui comprennent les tests par ultrasons, les tests de radiographie, les tests de particules magnétiques, les tests de pénétration de matrice, etc. Aujourd'hui, je vais souligner quelques défauts de coulée courants, leurs causes et leurs remèdes.
Types de défauts de moulage :
Ces défauts peuvent être classés en trois grandes catégories.1. Souffler :
C'est un trou de gaz ou une cavité de gaz qui se produit à la surface ou à l'intérieur de la pièce coulée. Cela est dû au gaz interrompu dans la coulée en raison d'une mauvaise ventilation. La plupart du temps, il se produit à la surface, ce qui crée un trou de gaz circulaire de forme ovale. Ces défauts sont visibles après usinage de surface. Ces défauts sont dus à un système de ventilation inapproprié, à une teneur excessive en gaz ou en humidité et à une faible perméabilité du sable et à une température élevée du sable. Cela est également dû à la faible température de coulée du métal.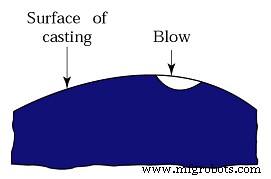
2. Cicatrice :
La cicatrice se produit généralement sur une surface plane et est due à une mauvaise ventilation ou à la perméabilité du sable. Le coup est recouvert par la fine couche de métal.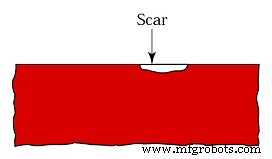
3. Croute :
Ceci est également connu sous le nom d'inclusion de laitier d'inclusion de sable. Cela ressemble à du laitier à l'intérieur de la fonte et il est très difficile d'y remédier car généralement cela ne se produit pas en un seul point. Ce défaut se produit généralement en raison d'un moule ou d'un noyau défectueux, d'une faible force de liaison du matériau de moulage ou du sable. Cela est également dû à la faible perméabilité du sable.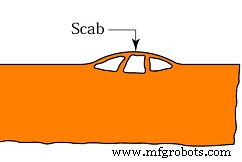
4. Pénétration :
Ce défaut se produit lorsque la fluidité du métal en fusion est élevée. Lorsque le moule est poreux et n'est pas assez solide pour résister au métal en fusion, ce défaut se produit. Le métal liquide pénètre dans le moule et se mélange au sable. Cela donne une surface de coulée inégale.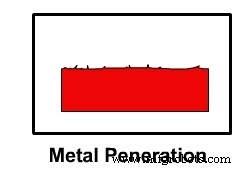
5. Fermeture à froid :
C'est le défaut de base qui survient généralement. Cela se produit lorsque le métal en fusion emprunte deux chemins différents. Lorsque les deux flux de métal en fusion entrent en contact et se solidifient avant de se mélanger complètement, des bulles se forment entre eux. Ce phénomène est connu sous le nom de fermeture à froid. Il est également connu sous le nom de tour froid.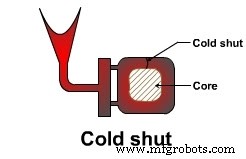
6. Non-concordance :
C'est un défaut dû à une inadéquation de la chape et de la traînée. Il est également connu sous le nom de décalage. Lorsque le décalage de la chape par rapport à la traînée est connu sous le nom de déplacement du moule et lorsque le décalage de la traînée est connu sous le nom de décalage de la chape. Cela est dû au rebond du métal en fusion, des broches de la boîte lâche, etc.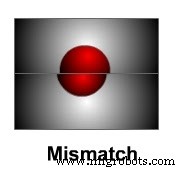
7. Erreurs d'exécution :
Les ratés sont un phénomène lorsque les matériaux coulés se solidifient avant le bon remplissage du moule. Il en résulte la présence d'un remplissage incomplet de la cavité. Cela est dû à une épaisseur de paroi trop mince, à un système de porte inapproprié, à une coulée lente, à un motif endommagé et à une mauvaise fluidité du métal en fusion.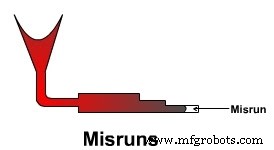
8. Déchirure à chaud :
Une déchirure ou une fissure à chaud n'est généralement pas visible car le moulage ne s'est pas séparé en fragments. Cela se produit en raison d'un refroidissement inégal et d'une mauvaise position des frissons. Cela se produit généralement en cas de changement brusque de section. Cela se produit lors de la solidification de la coulée lorsque la partie solide n'a pas une résistance suffisante pour résister à la force de traction.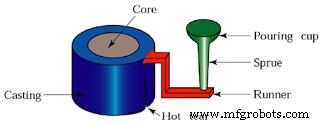
9. Rétrécissement :
Ce défaut survient généralement lors de la contraction volumique lors de la solidification. Cela se produit lorsque le métal liquide n'est pas suffisant pour compenser le retrait volumique. Cela est dû à une taille insuffisante de la colonne montante, à une mauvaise direction de la solidification de la coulée, à un mauvais emplacement des refroidisseurs ou dans les vannes.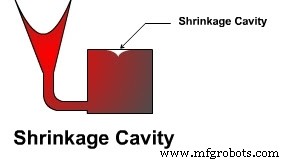
10. Boucle :
La formation d'une ligne inégale sur la surface moulée est connue sous le nom de boucle. Il génère une défaillance due à la surface du sable ou une expansion de la surface du sable due à la chaleur du métal en fusion.11. Trou d'épingle :
Les trous d'épingle sont similaires aux trous de soufflage mais de plus petite taille. Ceux-ci sont généralement présents en surface ou sous la surface et en grand nombre. Cela est dû à une mauvaise ventilation des gaz et à une faible perméabilité du matériau de moulage.12. Déformation :
C'est le défaut ou la déformation d'une pièce moulée qui se produit pendant ou après la solidification en raison des différents taux de solidification des différentes sections de la pièce coulée, de sorte que des contraintes sont créées dans les murs adjacents, ce qui entraîne un gauchissement de ces zones.13. Éclater :
Ce défaut généré en raison d'une résistance insuffisante du moule lorsque le métal s'écoule vers le moule en raison de la pression du métal liquide, la paroi de la cavité du moule endommage. C'est aussi dû à la rigidité du motif qui est insuffisante alors qu'il ne peut pas résister à la pression d'enfoncement et à l'endommagement de la paroi de la cavité.
Processus de fabrication
- Sable de moulage :types et constituants | Coulée | Métallurgie
- Types de défauts de moulage | Métaux | Secteurs | Métallurgie
- Qu'est-ce que la coulée de métal ? - Définition, types et processus
- Définition, types et procédés de coulée de métal
- Causes et remèdes aux irrégularités et aux bris de l'outil de poinçonnage
- Différents types de moulage sous pression et leurs applications
- Différents types de coulée centrifuge et leur principe de fonctionnement
- Différents types de défauts de soudure et remèdes
- Différents types de laminoirs et défauts du métal laminé