Éjecteurs de moulage par injection :types et considérations
L'introduction du moulage par injection de broches d'éjecteur dans les processus de fabrication a permis d'automatiser les opérations, d'améliorer la vitesse de production et de garantir des produits plus efficaces. Il a également amélioré la cohérence dans la conception des produits.
Malgré l'amélioration des procédés de fabrication par moulage par injection, il existe cependant de nombreux défauts dans sa conception qui doivent être optimisés. Ceci afin de garantir des produits meilleurs et plus efficaces.
Ainsi, cet article se penche sur le moulage par injection des éjecteurs et comment optimiser sa conception pour avoir des produits plus efficaces.
Que sont les broches d'éjection de moulage par injection ?
Les broches d'éjection sont essentielles dans la création de pièces. Ils font partie intégrante du système d'éjection dans le moule, qui détermine le résultat final des produits dans un processus de moulage par injection.
Le moulage par injection est un processus de fabrication qui consiste à injecter du plastique fondu dans un moule en métal pour prendre la forme du moule. Par conséquent, le moulage par injection des éjecteurs implique le retrait des pièces terminées des moules. Le moule en métal est composé de deux parties :les faces A et B. Lors du refroidissement du matériau fondu dans le moule, les deux parties du moule métallique sont séparées pour permettre l'élimination du plastique solide. Les moules d'injection sont construits de telle sorte que lorsqu'ils sont ouverts, la moitié du côté A est soulevée, laissant la pièce formée et le côté B.
Les broches d'éjection sont situées sur la moitié du côté B d'un moule, à partir de laquelle elles poussent la pièce formée hors du moule. La marque d'épingle d'un moule éjecteur est généralement imprimée sur les produits finis sous forme de bosse.
Types de broches d'éjection
Il existe de nombreux types d'éjecteurs utilisés dans la fabrication de produits. Vous trouverez ci-dessous les types les plus courants que vous trouverez idéaux pour le processus.
Broches d'éjection rigides
Ces goupilles d'éjection sont traitées thermiquement pour assurer l'uniformité de la dureté à travers le diamètre de la goupille. Les goupilles dures peuvent résister à des températures de travail allant jusqu'à 200 °C et conviennent principalement aux systèmes d'éjection de plastique dans le moule.
Broches d'éjection cémentées
Ils sont également connus sous le nom de goupilles Nitrure H13, sont des goupilles beaucoup plus dures que les goupilles dures traversantes et conviennent aux systèmes d'éjection de moulage sous pression dans le moule. Les goupilles cémentées sont nitrées à 65 – 70 HRC et peuvent résister à des températures supérieures à 200 °C.
Broches d'éjection noires
Les fabricants ont développé ces broches d'éjection en raison de l'incapacité des broches Nitrure H13 à être utilisées à des températures de travail supérieures à 600°C. L'éjecteur noir est recouvert d'un traitement de surface noir qui lui permet d'être autolubrifiant et de résister à des températures élevées jusqu'à 1000°C. C'est une broche d'éjection coûteuse et convient à un système d'éjection de métal dans le moule pour automobiles.
Considérations relatives à la conception du moulage par injection
Une conception de moule à injection doit être telle qu'elle fonctionne comme prévu. Une erreur de conception peut entraîner la fissuration ou le rétrécissement de la pièce, ce qui peut s'avérer trop coûteux ou trop difficile à corriger.
Par conséquent, la nécessité d'exécuter une conception bien structurée est importante et certains facteurs doivent être pris en compte.
● Créer des angles de dépouille
L'angle de dépouille est une forme inclinée qui est appliquée des deux côtés d'un moule à injection. Cette légère déformation de la forme du moule permet de retirer facilement le plastique du moule.
Un moule d'ébauche doit être présent pour fournir une résistance contre le frottement lors du retrait de la pièce du moule. Permettre plus d'angles de dépouille assurerait la libération facile des pièces du système d'éjection dans le moule.
L'absence d'angles de dépouille entraînerait de grandes marques d'éjecteur sur la pièce lors du retrait et des éraflures sur la paroi du moule.
● Épaisseur de paroi uniforme
Lorsque le matériau fondu est versé dans un moule avec une épaisseur de paroi uniforme, il s'écoule librement sans restriction, remplissant la cavité de la paroi et prenant sa forme définie.
Des parois de moule non uniformes entraîneront le refroidissement de la section la plus mince du matériau fondu. Par conséquent, à mesure que la section plus épaisse refroidit, cela entraînera le rétrécissement du matériau, la concentration des contraintes et éventuellement la fissuration lors du retrait.
Néanmoins, si votre conception ne permet pas une épaisseur de paroi uniforme, vous pouvez y remédier en creusant et en ajoutant des goussets.
(Le carottage est un processus d'élimination du plastique fondu de la zone étendue pour assurer l'uniformité le long du mur. Les goussets sont des structures de support que vous ajoutez au mur en tant que renforts pour réduire l'épaisseur du mur)
● Assurez-vous que les bords sont arrondis
Avoir des coins arrondis à l'intérieur et à l'extérieur de la pièce présente plusieurs avantages. Il réduit la concentration de contraintes et empêche la pièce de se fissurer.
Les angles vifs limitent l'écoulement du plastique fondu dans la matrice et, lors du refroidissement, le plastique tire contre les angles vifs et est difficile à retirer.
Les pièces à bords arrondis sont faciles à produire, plus économiques et permettent une meilleure formation et évacuation des produits.
● Réduire les contre-dépouilles
Les contre-dépouilles sont des caractéristiques saillantes dans la conception du moule qui empêchent le retrait de chaque côté du moule. Les contre-dépouilles sont nécessaires et inévitables dans une conception de moule car elles empêchent la pièce d'être directement éjectée du moule.
Cependant, les contre-dépouilles peuvent être corrigées en créant des verrouillages ou des loquets qui permettent un retrait ou un assemblage facile. Autant que possible, l'équipe de conception doit conserver le nombre de contre-dépouilles dans un système d'éjection dans le moule au minimum.
● Emplacements des portes
Les portes sont les points d'entrée du plastique fondu dans le moule. Cependant, lors du refroidissement de la pièce, la porte laisse une marque d'épingle, qui est la plupart du temps encore visible même après le débosselage.
L'équipe de conception peut utiliser une porte de bord pour remédier à cela, où les bosses résultantes seraient moins visibles. Le matériau fondu est également injectable par une extension située sur la broche d'éjection.
Lors du refroidissement de la pièce, la broche d'éjection peut repousser la marque de broche résultante de la porte lors du retrait de la pièce du moule.
● Nature du matériel
Le type de matériau utilisé doit dépendre de la fonction du produit
Certains matériaux sont épais, certains sont flexibles, tandis que d'autres sont durs ou cassants. Le type de matériau choisi déterminera à quoi sert la pièce et sa conception.
Bien que vous puissiez épaissir certains matériaux, il est également possible de les plier en formes. De plus, vous devriez en tenir compte avant de choisir le type de matériau.
Défauts courants et solutions
Le moulage par injection à l'aide d'éjecteurs présente certains défauts. Vous trouverez ci-dessous les défauts possibles et les solutions nécessaires.
Pauses
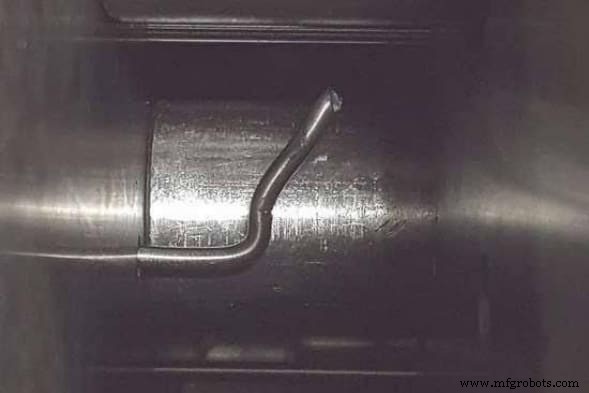
La principale raison de la rupture des broches d'éjection est la différence entre la force requise pour éjecter la pièce du moule et la force de la broche.
L'éjection des pièces du moule nécessite de la force. Parfois, la force requise dépasse la résistance de la goupille en raison de sa longueur non supportée, ce qui entraîne une rupture.
Par conséquent, la manière la plus efficace de remédier aux ruptures de broches d'éjecteur consiste à utiliser de grandes quantités de broches d'éjecteur avec des diamètres plus grands. De cette façon, la force requise est répartie uniformément sur les différentes broches, réduisant ainsi la casse.
Marques de broche d'éjecteur

Ce sont des « bosses » laissées sur la pièce par les éjecteurs lors du démoulage. Cette marque d'épingle peut entraîner la fissuration des produits lors de leur utilisation. Par conséquent, il est important de concevoir un système d'éjection dans le moule pour éviter les marques d'éjecteur.
- Disposez les broches d'éjection de manière à ce que la force d'éjection à travers la pièce soit constante.
- Placez les éjecteurs sur des pièces dures telles que des inserts métalliques, des piliers et des nervures pour éviter les défauts de marques d'éjecteur.
- Concevez la position des éjecteurs sur la surface plane de la pièce plutôt que sur des pentes.
Jet
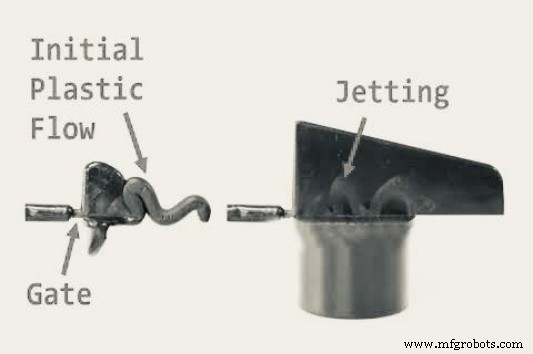
Le jet se produit en raison de la petite taille de la porte ou de l'injection rapide de matériau fondu dans le moule, ce qui entraîne une forme déformée.
Cela peut être résolu en :
- Augmenter la taille de la porte
- Contrôle de l'écoulement du matériau fondu vers le moule
Autres types d'éjecteurs
Bien qu'ils ne soient pas communs à de nombreux machinistes, il existe également d'autres types d'éjecteurs. Voici quelques exemples.
Manchons d'éjection
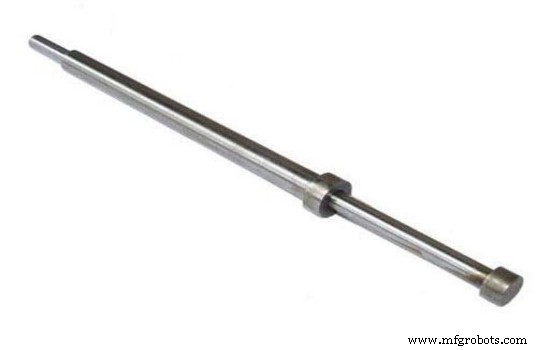
Ce sont simplement des éjecteurs creux. Il se compose d'une goupille à surface dure avec un trou et d'une goupille centrale qui s'insère dans le trou. Les trous dans les manchons d'éjection servent à guider et à protéger la broche.
Plaques d'éjection
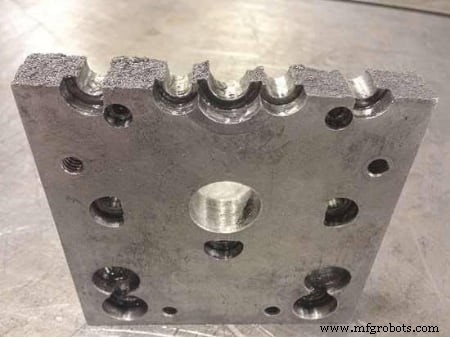
Dans un système d'éjection dans un moule, les plaques d'éjection fonctionnent parallèlement aux broches d'éjection. Il maintient la tête des broches pour les empêcher de sortir pendant le processus de moulage par injection des broches d'éjection.
Blocs d'éjection
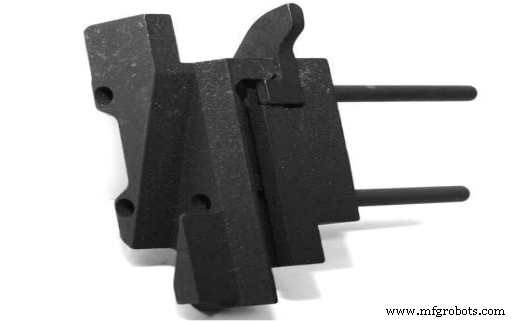
Ils ont des rainures creuses lubrifiantes et sont appliqués à la surface de produits minces qui nécessitent une finition de surface élevée mais qui seraient gâchés par des défauts de marques d'éjecteur.
Ils limitent les marques d'éjecteurs et sont également applicables pour une utilisation sur la surface de produits à fort gauchissement.
Conclusion
Les experts en conception ne peuvent ignorer l'importance des éjecteurs dans le processus de moulage par injection. En effet, le produit formé dans le moule dépend de l'efficacité des éjecteurs pour éviter les défauts de marques d'éjecteurs.
Par conséquent, il est important de faire confiance à une entreprise connaissant la conception pour la fabrication, l'utilisation des éjecteurs et un excellent dossier de gestion de la conception du moulage par injection des éjecteurs.
Chez RapidDirect, nous pouvons garantir des conceptions optimisées pour votre processus de moulage par injection d'éjecteurs. Consultez notre équipe support pour des conseils de fabrication et si vous avez déjà un fichier CAO il reste une petite étape. Téléchargez-le maintenant pour obtenir un devis instantané pour votre conception.
FAQ
Quelles conceptions de moulage par injection peuvent être utilisées, si la surface est limitée ?
Dans les cas de conception, où la surface est limitée, de sorte qu'il n'y a pas de points sur la pièce permettant l'éjection du moule, vous pouvez optimiser votre conception en :
– Ajout de bossages pour agir comme des patins éjectés
– Remplacement des broches d'éjection par des pièces en caoutchouc de silicone liquide, de sorte que lors du refroidissement, les pièces sont éjectées manuellement des moules via le caoutchouc de silicone liquide.
Lors du choix d'un matériau, il est préférable de considérer la fonction de votre produit et les propriétés qu'il doit posséder. Des alternatives moins chères échoueraient à long terme. Par conséquent, il est préférable d'utiliser des matériaux performants qui répondent aux besoins de nos produits.
Technologie industrielle
- Avantages et inconvénients du moulage par injection thermodurcissable
- Tutoriel de moulage par injection :vidéos
- PEEK à haute viscosité pour le moulage par injection et l'extrusion
- Types de démarreurs de moteur et considérations d'application
- Qu'est-ce que le sable de moulage ? - Types et propriétés
- Processus de moulage par injection
- L'importance de la technique de moulage par injection
- Éjecteurs de moulage par injection :types et considérations
- Explication des termes courants du moulage par injection :multi-empreintes, famille, inserts, etc.