Entretien d'expert :Yves Hagedorn, directeur général d'Aconity3D, sur le fait d'aider les entreprises à innover grâce à la fabrication additive
L'adoption de l'impression 3D métal peut être difficile en raison de la nécessité de développer des applications, de qualifier des matériaux et des processus. Pour surmonter ces défis, la société allemande Aconity3D fournit des systèmes d'impression 3D métalliques de laboratoire flexibles qui permettent à ses clients d'expérimenter les paramètres de processus et de rechercher de nouvelles applications pour la technologie.
Dans l'interview d'experts de cette semaine, Yves Hagedorn, directeur général d'Aconity3D, discute des avantages des systèmes matériels à architecture ouverte et des raisons pour lesquelles les logiciels de conception sont l'un des principaux défis de l'impression 3D métal.
Pouvez-vous me parler d'Aconity3D ?
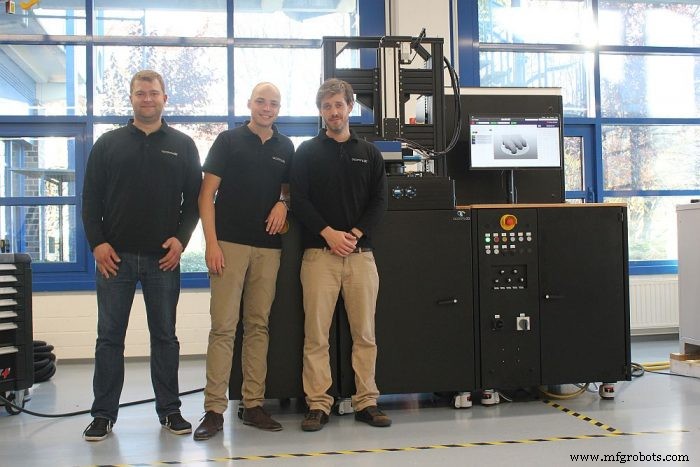
Chez Aconity3D, nous proposons tout ce dont vous avez besoin pour la fabrication additive métallique.
Nous fournissons des composants de machine spéciaux et différents modules, qui peuvent être combinés pour créer des équipements conçus pour des applications spécialisées. C'est parce que nous pensons qu'il n'y a pas un seul système qui puisse convenir à toutes les applications possibles sur l'ensemble du marché.
Notre parcours client commence par le conseil. Par exemple, un client peut nous contacter pour voir s'il est possible d'imprimer en 3D du magnésium. Dans ce cas, nous ferions des recherches dans notre deuxième unité commerciale, qui est la distribution des matériaux, et découvririons pour notre client où se procurer le matériau spécifique en question.
Dans notre troisième unité commerciale, nous effectuons des tests pour nous assurer que le matériau peut être traité avec la fabrication additive. Et si tout fonctionne et qu'un client est satisfait, nous agirons en tant qu'atelier de travail et fabriquerons cette application spécifique pour le client.
À long terme, le client peut décider d'acheter notre équipement qui a été conçu pour cette application spécifique.
Notre approche permet à nos clients de mener des recherches efficaces en termes d'extension du champ des matériaux applicables.
Si les clients ont certains matériaux pour des applications spéciales qui ne sont pas encore qualifiés, ils peuvent faire de nombreuses recherches en vue de leur qualification avec nos équipements. Ils peuvent utiliser divers paramètres, ils sont totalement libres du côté logiciel et peuvent également effectuer des modifications sur le matériel, en fonction des paramètres dont ils ont besoin.
En fin de compte, nous voulons être un guichet unique pour les clients. Cependant, la vente de matériel est notre activité principale.
Quelle a été la motivation derrière la création de l'entreprise ?
Eh bien, si vous souhaitez étendre le périmètre de la fabrication additive, soit en termes de matériaux applicables, soit en augmentant la productivité ou la précision dimensionnelle, vous avez besoin d'un accès complet au matériel et à tous les paramètres possibles dans le processus.
Nous avons vu qu'il n'y avait aucun système sur le marché qui vous permette de le faire. Et c'est à ce moment-là que nous est venue l'idée d'offrir aux clients la possibilité d'affiner leur processus. C'est alors qu'Aconity3D est né.
Nous nous sommes vite rendu compte que nous disposions d'un réel atout et que nous pouvions réellement répondre à un réel besoin du client d'avoir accès à la fois au matériel et aux logiciels.
Y a-t-il des secteurs spécifiques qui bénéficieraient le plus de la technologie et des services fournis par Aconity3D ?
Il n'y a pas d'industrie spécifique, car les applications industrielles des additifs sont aussi multiples que les possibilités.
Prenons l'industrie médicale, où le champ d'applications est immense. Par exemple, vous pouvez avoir des implants en titane ou même en magnésium, qui est biorésorbable. Il existe également des applications dans l'industrie des capteurs médicaux.
Il en va de même pour l'aérospatiale. L'industrie aérospatiale a intérêt à étendre la portée des alliages applicables pour le placage, par exemple, ou des alliages à haute température.
L'automobile est également un autre exemple intéressant car l'industrie est très soucieuse des coûts. Cela signifie que les constructeurs automobiles ne veulent payer que pour ce qu'ils obtiennent.
Notre proposition de valeur est notre grande flexibilité, qui nous permet de laisser de côté tout ce qui n'est pas nécessaire pour cette application spécifique. Cela nous permet de rivaliser avec les technologies de fabrication traditionnelles.
En ce qui concerne l'impression 3D métal, quelles applications sont les mieux adaptées à la technologie, et comment les entreprises peuvent-elles commencer à identifier les bons types d'applications ?
Il est bon d'envisager la fabrication additive si vous avez des composants de petites tailles et de structures complexes. Une autre raison d'utiliser un additif peut être de combiner de nouveaux matériaux là où il était auparavant impossible de le faire - prenons le cuivre et le chrome comme exemple.
Le principal obstacle ici est que pour presque toutes les applications, produire une pièce est plus cher avec la fabrication additive par rapport au fraisage ou à d'autres technologies de fabrication traditionnelles.
Seule exception, les restaurations dentaires :pour celles-ci, la fabrication additive est moins chère que le fraisage. C'est pourquoi ce fut l'une des premières applications industrielles de la fusion laser à base de poudre. Une autre exception concerne les montures de lunettes, qui sont également une excellente application pour les additifs.
Mais pour tous les autres, il y a souvent un conflit entre l'analyse de rentabilisation et les coûts du cycle de vie du produit. C'est le principal obstacle car de nombreux clients n'ont tout simplement aucune idée des coûts du cycle de vie de leurs produits.
Pour le dire autrement, vous êtes désormais en mesure d'avoir une intégration fonctionnelle. Ainsi, par exemple, vous pouvez intégrer des canaux de refroidissement dans un boîtier, mais il est vraiment difficile de mettre un prix là-dessus. Le principal défi consiste donc à effectuer le tri des pièces et à trouver une analyse de rentabilisation valable pour votre application et votre production d'additifs.
Quels sont les principaux défis de l'impression 3D métal et comment les avez-vous relevés ?
À mon avis, l'un des principaux défis réside dans la conception des pièces et les solutions logicielles correspondantes pour la préparation des données. En matière de fabrication additive, la standardisation reste un défi et je pense que c'est en partie dû au fait que le logiciel n'est pas vraiment standardisé. Par exemple, prenez les nombreux formats de données différents pour chaque fournisseur de système individuel. De plus, en termes de conception de pièces, il n'y a pas ou peu de directives en raison de la grande flexibilité de la production additive. C'est également la raison pour laquelle les armatures de restauration dentaire ont été la première véritable application industrielle :une structure de conception de pièces et de préparation de données entièrement automatisée - une condition préalable à la production en série de pièces de taille unique.
Pour la première fois depuis les années 70, nous sommes maintenant dans une situation où nous pouvons construire des pièces plus complexes que nous ne pouvons réellement concevoir ou simuler.
Ainsi, la conception et la préparation des données sont toujours un goulot d'étranglement dans cette industrie alors que l'accent est mis sur les systèmes matériels à plus haute productivité, les solutions logicielles intelligentes étant exclues de cette équation. Préparer les pièces pour qu'elles soient adaptées à la fabrication additive est une compétence clé et demande également beaucoup de temps.
J'ai vu des exemples où la conception de la pièce et la préparation des données prenaient plus de deux semaines, alors que l'impression de la pièce ne prenait que deux jours. C'est tout simplement inefficace pour concevoir une pièce pour ce laps de temps. Et c'est là qu'intervient le problème, à mon avis.
Pourriez-vous partager l'une des réussites de vos clients ?
Oui définitivement. Nous avons eu des clients qui produisent maintenant des pièces en magnésium pour des applications médicales. Nous en avons d'autres qui ont obtenu l'approbation de la FDA pour leurs implants en titane.
Dans l'industrie automobile, nous avions une demande spécifique pour un système à haute productivité. Nous avons donc fourni un système à quatre lasers avec un chevauchement complet sur une plaque de 400 millimètres de diamètre. Je pense que nous sommes les seuls sur le marché à pouvoir le faire, et cela a un impact significatif sur la productivité.
D'autres clients exploitent la possibilité de préchauffage à haute température pour étendre la portée des matériaux applicables aux aciers à outils hautement alliés, aux aluminures de titane et à certains superalliages à base de nickel.
Comment voyez-vous l'industrie de la FA évoluer au cours des prochaines années ?
L'industrie a définitivement mûri au cours des 12 années où j'ai été impliqué dans l'additif. Quand j'ai commencé, il y avait beaucoup de battage médiatique. Maintenant, le battage médiatique a quelque peu diminué.
L'évolution de la technologie a permis de débloquer de nombreuses applications pour la fabrication additive, mais toutes ces applications nécessitent encore un haut niveau d'expertise.
Aujourd'hui, vous pouvez acheter certaines imprimantes 3D de bureau pour moins de 1000 euros, ce qui fait croire à beaucoup de gens que vous pouvez acheter des machines-outils industrielles, comme ces coûteux systèmes de fusion laser à base de poudre, appuyez sur play et vous vous aurez immédiatement votre analyse de rentabilisation.
Évidemment, ce n'est pas le cas avec la fabrication additive industrielle. Il y a un enjeu majeur de formation et de développement de l'expertise. Et je pense que c'est là que l'ensemble de l'industrie devra continuer à évoluer.
Avoir plus d'expertise au sein de l'industrie et, surtout, avoir des processus plus standardisés et des produits fiables sera la clé pour l'adoption industrielle de la fabrication additive.
Y a-t-il des développements dans l'industrie de la FA qui vous enthousiasment ?
Oui définitivement. Nous nous concentrons non seulement sur la surveillance en cours de processus, ce qui signifie utiliser différents capteurs pour obtenir autant d'informations que possible de votre processus, mais également sur l'utilisation de ces informations pour effectuer un contrôle en cours de processus.
Je pense que c'est le Saint Graal de la FA car avec le contrôle en cours de processus, vous êtes capable de réagir presque immédiatement aux lacunes de votre processus.
Cela rendra les systèmes beaucoup plus intelligents.
Pourriez-vous nous en dire un peu plus sur la surveillance et le contrôle en cours de processus, et sur ce que fait Aconity3D dans cet espace ?
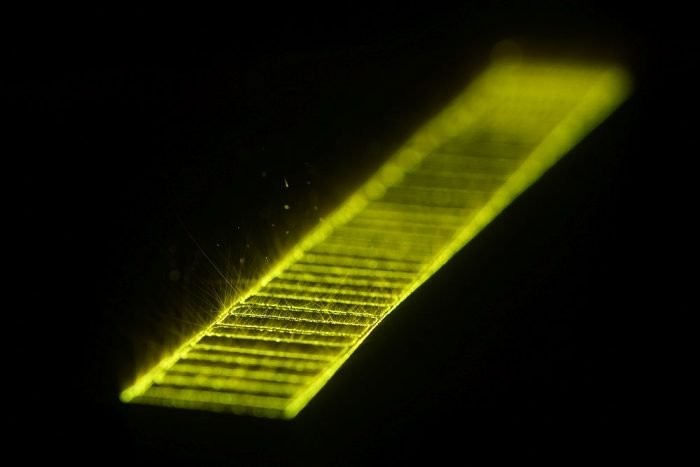
Notre société est une spin-off de l'Institut Fraunhofer de technologie laser, à l'origine de la fusion laser sur lit de poudre.
Avec ce bagage, nous avons pu mettre en œuvre différents capteurs optiques pour accompagner le laser de traitement. Et cela vous permet de tirer immédiatement de nombreuses informations de la zone d'interaction, du bain de fusion et du laser.
Ceci, cependant, conduit à d'autres défis associés au Big Data. Que faites-vous avec cette énorme quantité de données enregistrées ? Comment vous assurez-vous d'ignorer les données dont vous n'avez pas réellement besoin ? Et comment distinguer les données utiles des données inutiles ?
Je pense que c'est là où en est l'industrie actuellement. Et c'est ce que nous faisons aussi. Nous utilisons une caméra à haute vitesse pour regarder à l'intérieur du processus et en tirer des enseignements, et nous avons également différents capteurs permettant un contrôle de processus en boucle fermée.
Donc, si vous avez ce système en place, vous peut détecter si votre bain de fusion est trop chaud ou trop grand, et vous pouvez réguler cela grâce à la puissance du laser, réagissant ainsi à ce signal du processus.
C'est vraiment fascinant pour moi. Et je pense qu'il y a encore beaucoup de potentiel ici.
Aconity3D a récemment annoncé un partenariat avec Aerosint. Que signifie ce partenariat pour votre entreprise à l'avenir ?
Depuis que je suis dans l'industrie, les gens s'intéressent aux pièces métalliques multi-matériaux. Et c'était toujours le problème de ce qui devait venir en premier, l'application ou le développement technique.
Depuis quelques temps, il ne s'est vraiment rien passé dans ce sens. Et puis nous avons rencontré Aerosint, une entreprise belge qui a développé un dispositif de dépôt de poudre capable de déposer deux matériaux différents dans les dimensions X et Y sur un lit de poudre. C'est en gros ce qui manquait à la fabrication additive multi-matériaux.
Nous entrons maintenant dans l'équation avec la capacité de réagir au modèle de poudre ou au modèle de matériau modifié sur notre plaque de fabrication en modifiant les paramètres de processus requis pour chaque matériau individuel.
Cela signifie que les deux partenaires, Aconity3D et Aerosint, disposent d'une base solide pour réaliser ce rêve de FA multi-matériaux.
Quelles nouvelles applications pourraient être ouvertes avec la possibilité de l'impression 3D métal multi-matériaux ?
Une industrie qui pourrait vraiment en bénéficier est l'industrie de la bijouterie.
Créer des matériaux gradués, du cuivre au chrome, peut être une autre opportunité. Ceux-ci pourraient être utilisés pour l'outillage dans les industries du moulage ou de la forge. Par exemple, avec l'impression 3D multi-matériaux, vous pouvez utiliser du cuivre pour créer des structures de refroidissement et du chrome ou de l'acier pour créer la surface extérieure de la pièce.
Si vous avez des dégradés, vous pourrez peut-être également évaluer vos propriétés mécaniques. Cela pourrait être utile dans le domaine médical pour la réduction de la protection contre le stress. Cet effet se produit lorsque les implants métalliques sont trop denses, provoquant une perte de résistance de l'os. La protection contre le stress pourrait également être réduite en modifiant les propriétés mécaniques de l'implant à l'aide de l'impression 3D multi-matériaux.
Cependant, avant que de nouvelles applications ne soient développées, je pense qu'il doit y avoir une poussée technologique pour montrer des capacités similaires aux capacités actuelles de la fabrication additive.
Quel est l'avenir d'Aconity3D ?
Nous continuerons d'élargir le champ des matériaux applicables qui, à l'instar des multi-matériaux, nous permettront de proposer de nouvelles applications à nos partenaires industriels. Nous voulons plonger profondément dans les applications de séries spécialisées.
Nous comprenons qu'avec des applications de niche, il peut être très difficile de qualifier de nouveaux matériaux, surtout lorsqu'il s'agit d'un seul client. Cependant, notre pain et notre beurre sont de s'assurer que nos clients sont satisfaits et peuvent exploiter les applications qu'ils ont en tête.
Nous voulons à terme être le catalyseur de l'innovation pour nos clients.
Pour en savoir plus sur Aconity3D, visitez : aconity3d.com
impression en 3D
- Comment les entreprises aérospatiales peuvent-elles faire passer la fabrication additive au niveau supérieur avec le MES ?
- Pourquoi les entreprises devraient-elles adopter la fabrication additive distribuée ?
- Entretien d'experts :Pat Warner, spécialiste de la fabrication additive de Renault Formula One Team
- Entretien avec un expert :professeur Neil Hopkinson, directeur de l'impression 3D chez Xaar
- Entretien avec un expert :Dr Alvaro Goyanes de FabRx
- Entretien avec un expert :Dr Bastian Rapp de NeptunLab
- Entretien d'experts :Felix Ewald, PDG de DyeMansion
- Entretien avec un expert :Ibraheem Khadar de Markforged
- Amélioration de la fabrication additive avec la rétro-ingénierie