La demande de bras de rampe de pulvérisation plus longs permet d'utiliser des composites dans les équipements agricoles
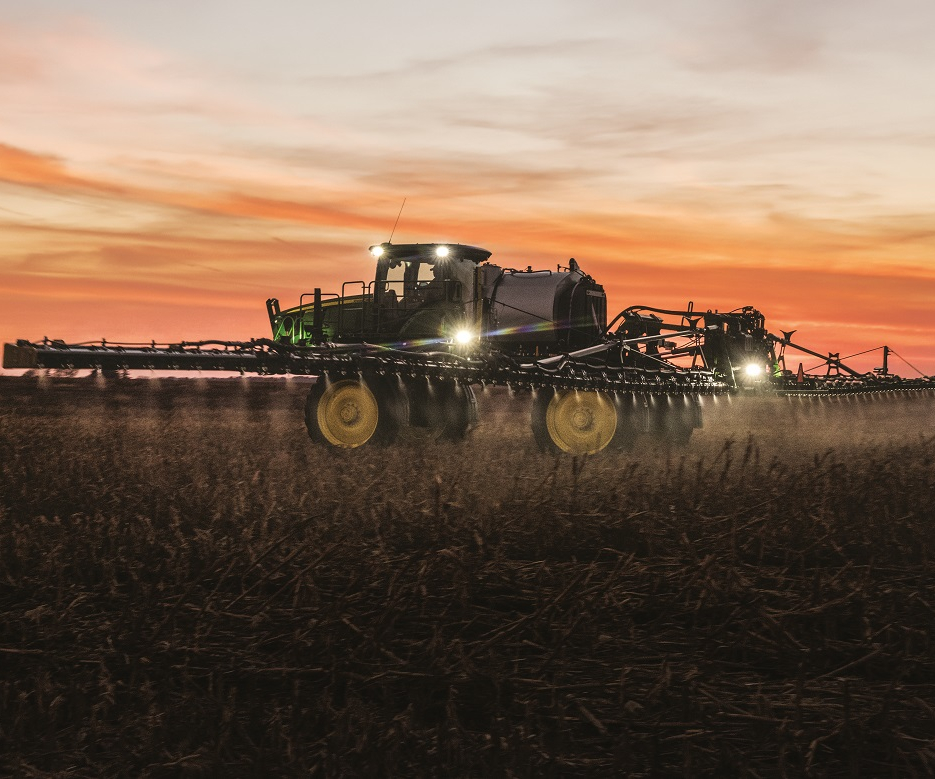
Répondre à la demande agricole. Une application croissante des composites sur le marché des équipements agricoles est constituée par les bras de flèche pour les équipements de pulvérisation automoteurs, utilisés pour appliquer des produits chimiques liquides sur les cultures. Origine | Deere &Co.
Alors que les champs agricoles contigus dans des régions telles que l'Amérique du Nord, l'Argentine et le Brésil se sont agrandis grâce à la consolidation, et que l'agriculture sans labour augmente dans certaines zones géographiques, les agriculteurs veulent des systèmes de pulvérisation avec des bras de rampe plus longs pour réduire le nombre de passages nécessaires pour couvrir de plus en plus champs plus grands. Cela réduit également le compactage du sol, augmentant la productivité et les rendements des cultures.
En réponse à ce besoin, la branche argentine de King Marine SA (Valence, Espagne), dont le cœur de métier, ironiquement, était la fabrication de pièces de bateaux en composite à l'aide de plastique renforcé de fibres de carbone (CFRP) de qualité aérospatiale, a utilisé son expertise en composites sur d'autres marchés. pour développer de nouveaux bras de rampe de pulvérisation pour les équipements de pulvérisation automoteurs. En cours d'utilisation, les bras de flèche se déplient et s'étendent perpendiculairement à l'axe principal des tracteurs et permettent aux agriculteurs d'appliquer des produits chimiques liquides (par exemple, des insecticides, des herbicides et des engrais) sur les cultures. Après utilisation, ils se replient et se rangent le long de la carrosserie du tracteur pour éviter de s'emmêler avec les poteaux de clôture et pour permettre aux agriculteurs de circuler sur les routes.
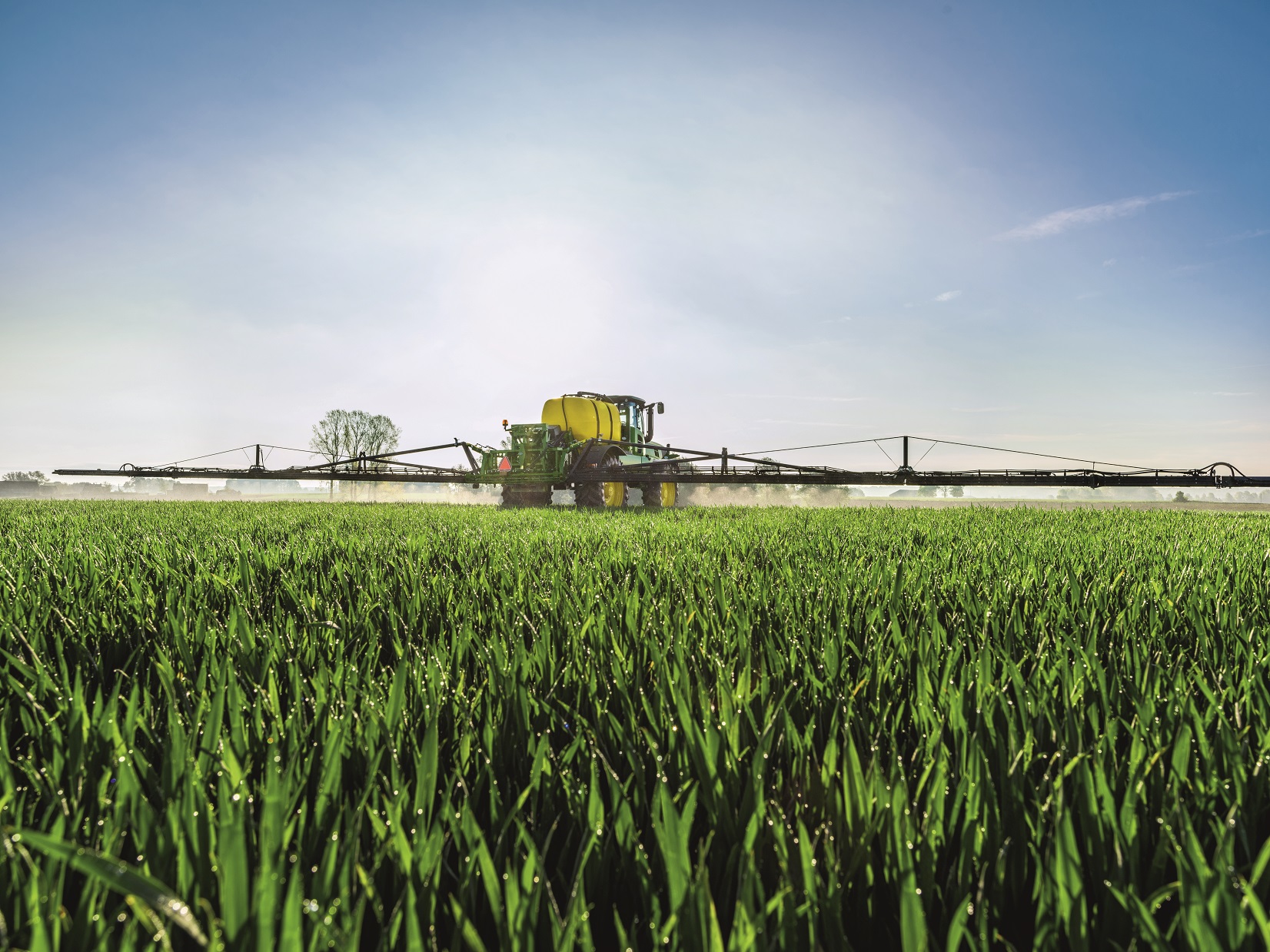
Les limites du métal. Traditionnellement fabriqués en acier, les bras de rampe de pulvérisation avaient atteint leurs limites structurelles et de largeur pratiques en raison des grandes structures de support requises pour empêcher les bras de se plier sous les charges de torsion et de fatigue. Origine | Deere &Cie
Les flèches ont longtemps été fabriquées en acier, mais à mesure que la longueur augmentait, des structures de support plus grandes étaient nécessaires pour empêcher les bras de se plier sous des charges de torsion et de fatigue et lors d'impacts involontaires avec des clôtures, des arbres et d'autres structures. (Les charges de fatigue élevées sont la raison pour laquelle les rampes ne sont jamais passées à l'aluminium.) À leur tour, les rampes plus longues avec des structures de support plus grandes ont obligé les agriculteurs à acheter des tracteurs plus gros pour transporter des équipements de pulvérisation plus lourds et des réservoirs plus grands contenant de plus grands volumes de liquides ; cependant, en résolvant un problème, l'équipement plus lourd conduit à un compactage accru du sol et, par conséquent, à une réduction des rendements des cultures. De plus, de nombreux produits chimiques agricoles corrodent les métaux et les rampes plus longues nécessitent des mécanismes de pliage plus élaborés pour l'arrimage des rampes. Finalement, les barrages en acier ont atteint une limite pratique d'environ 36 mètres (120 pieds) d'un côté à l'autre. Pourtant, le marché, en particulier dans les Amériques, souhaitait des booms plus longs.
La récession offre des opportunités
La Grande Récession de 2008 a été catastrophique tant pour les particuliers que pour les entreprises. King Marine, une entreprise familiale de vingt ans, qui possède des installations de fabrication à Picassent, en Espagne, et à Campana, en Argentine, est entrée en 2008 avec une entreprise en plein essor produisant des composants en PRFC, en particulier des mâts, pour les yachts hautes performances.
«C'est à ce moment-là que la récession économique mondiale a commencé et que le marché de la marine de luxe a été durement touché», se souvient Natalia Dacko, chef de l'administration européenne et audit interne chez King Marine. « Nos ventes ont chuté de façon spectaculaire et nous avons cessé de construire des bateaux. Nous étions en mode crise car notre entreprise était en danger. Nous avions une grande équipe de techniciens, d'ingénieurs et de spécialistes — qui étaient tous des experts en fibre de carbone [composites]. La grande question était : « Qu'allons-nous faire maintenant ? » » King Composite S.L. a été créé pour explorer les applications CFRP non marines.
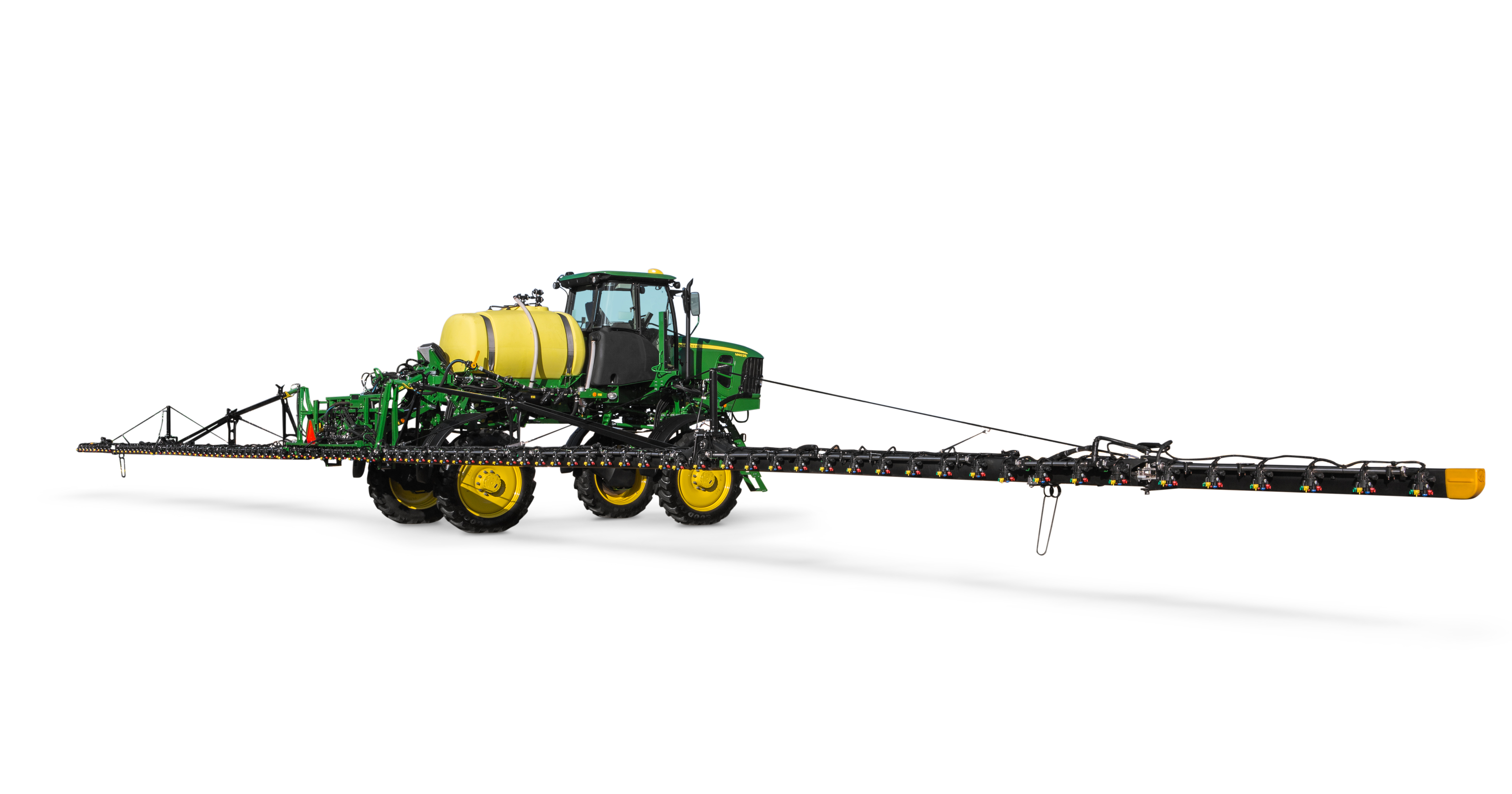
Plus longtemps que jamais. Les rampes composites ont la capacité de se déplier et de s'étendre pour une utilisation facile. Origine | Deere &Co.
Une solution inattendue aux préoccupations de l'entreprise est venue en 2009 d'un Argentin dont la propre entreprise fabriquait des systèmes de pulvérisation agricole. L'homme était frustré par les problèmes qui tourmentaient ses rampes métalliques. « Il nous a dit qu'il aimerait que les rampes soient plus légères, plus longues, sans fatigue, résistantes à la corrosion et faciles à réparer », se souvient Dacko. Bien que King Composite n'ait aucune expérience en matériel agricole, une équipe a construit un prototype de CFRP, et la société argentine l'a adoré, donnant le coup d'envoi à l'activité croissante de King Composite avec les équipementiers d'équipement agricole en Argentine. King Composites sera finalement rebaptisé King Agro SL.
Au fur et à mesure que les affaires dans les rampes de pulvérisation composites se développaient, King Agro s'est fait connaître pour ses produits innovants et de qualité. Après quelques années, son succès est remarqué par un leader du matériel agricole qui livre ses propres batailles de rampes de pulvérisation. Les membres de l'équipe d'ingénierie de Deere &Co. (Moline, Illinois, États-Unis) ont rencontré King Agro en 2015 pour discuter des opportunités, et bientôt King Agro produisait et distribuait des rampes CFRP pour la marque John Deere.
Nouvelles générations, nouvelles permutations
« Nous avons commencé par les conceptions et les recommandations de King Agro, ainsi que par ce que Deere avait développé, et nous avons trouvé qu'elles étaient assez applicables », explique Phillip Ferree, directeur général de King Agro. « Tout d'abord, notre équipe commune a apporté quelques changements pour améliorer la fiabilité et la durabilité pour le marché sud-américain et a lancé ces produits en 2015. Simultanément, nous avons commencé à concevoir des produits de deuxième génération pour l'Amérique du Nord et l'Europe. Pour répondre aux réglementations locales, nous avions besoin de différentes fonctionnalités dans des domaines tels que la durabilité et l'impact, ce qui nécessitait de traduire les spécifications des métaux en conceptions composites. Ces produits ont été commercialisés en 2017.
« Lors de notre première réunion, nous avons passé trois heures à discuter des différentes caractéristiques des pulvérisateurs en Amérique du Nord et du Sud », se souvient Thomas Bartlett, responsable de l'ingénierie des produits de pulvérisation Deere. « Non seulement ils utilisent des modèles de pliage différents – il existe 20 façons différentes de plier ces systèmes en fonction du marché et des réglementations – mais les conditions agricoles sont également différentes. Au Brésil, ils pratiquent l'agriculture sans labour. En Amérique du Nord, c'est plus limité avec des pratiques agricoles différentes et plus de réglementation. L'Europe a d'autres différences et des exploitations beaucoup plus petites. Ils gardent leurs produits chimiques centralisés, de sorte que les pulvérisateurs sont amenés au dépôt pour les recharges plutôt que d'emmener les produits chimiques dans les champs pour les recharges comme nous le faisons dans les Amériques. De plus, dans certaines régions, la plomberie transportait des liquides du réservoir aux buses à travers les bras, mais dans d'autres endroits, la plomberie passait sous les bras. Un autre défi était de savoir combien de temps prolonger les rampes, car l'ajout d'un autre mètre ici ou là ne fournirait pas nécessairement une solution viable. Au lieu de cela, les ingénieurs ont dû tenir compte de la manière dont les cultures étaient plantées dans chaque zone géographique et des distances entre et dans les rangées.
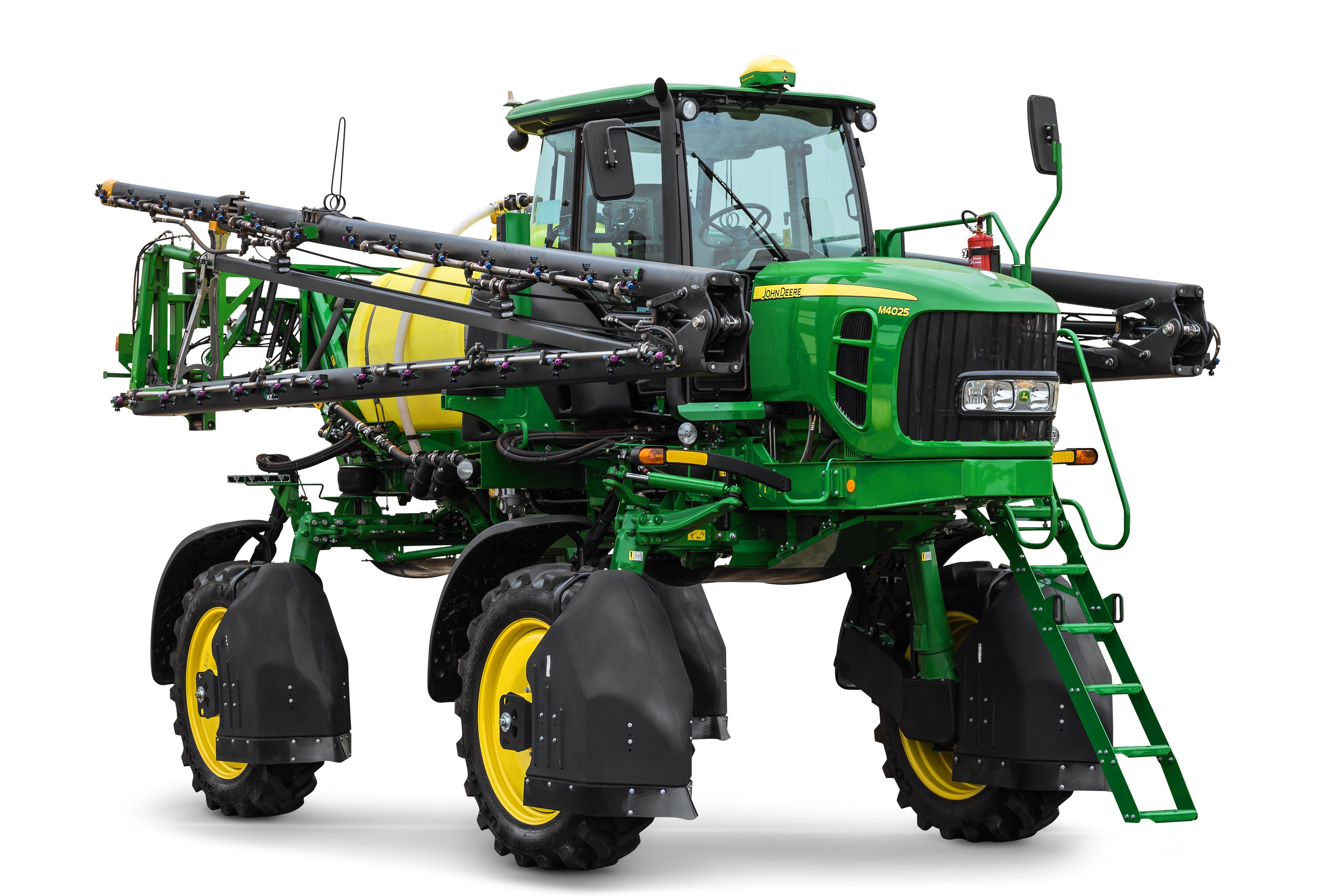
Plié pour un rangement facile. Les bras de flèche se rangent pour faciliter les déplacements entre les champs et le stockage de l'équipement. Origine | Deere &Co.
Les rampes comportent de multiples structures tubulaires composites avec des sections transversales carrées qui, à leur tour, sont connectées via des « extrémités » spéciales qui se connectent aux systèmes de distribution de fluide. Des caractéristiques spécialement conçues et moulées dans les structures principales fournissent aux composants la fonctionnalité requise pour ouvrir/fermer hydrauliquement et transporter des fluides sous haute pression. « Avec l'hydraulique, nous avons pu intégrer de nombreuses fonctionnalités dont nous avions besoin afin de pouvoir assembler les éléments et créer une conception globale plus simpliste », ajoute Bartlett. Deere exige que les rampes se déploient/se replient en moins d'une minute et que le fluide soit délivré dans les deux secondes suivant le démarrage de la pompe.
Tous les composites utilisent une matrice époxy et sont mis sous vide et durcis à l'autoclave. Une combinaison de renforcement en carbone et en verre est utilisée selon que les composants nécessitent une résistance plus élevée ou un impact plus élevé. La plupart de la fibre de carbone est constituée d'étoupes 24K, mais dans une variété de formats, allant du tissage unidirectionnel au sergé pour les couches d'apparence extérieure avec une finition transparente. Dans les joints et les endroits où l'hydraulique interagit, où plus de résistance et de rigidité sont nécessaires, des structures plus lourdes avec plus de plis sont utilisées. Selon le modèle et le marché, les volumes de production varient de 100 à 1 000 systèmes par an. King Agro estime qu'en 2017, le marché mondial total des pulvérisateurs automoteurs était de 14 000 unités/an.
« En entrant dans ce programme, nos objectifs étaient d'étendre les rampes à 40 mètres mais à une masse inférieure de 30 %, car le poids était très important », note Jonathan Nelson, ingénieur en conception de rampes de pulvérisation composites Deere. « Lorsque vous suspendez une grande masse à l'avant ou à l'arrière d'une machine, vous luttez contre l'inertie, il est donc beaucoup plus difficile d'équilibrer les charges entre les essieux avant et arrière. Nous voulions également améliorer la résistance à la corrosion, mais nous devions également considérer la corrosion galvanique en présence de fibre de carbone. Une autre exigence était un impact plus élevé, car vous ne voyez jamais un pulvérisateur qui n'a pas touché quelque chose . Nous avons effectué des tests standardisés développés pour les métaux qui impliquent l'installation de flèches dans des poteaux de clôture pendant plusieurs centaines de cycles. » Les charges de travail et la fatigue sur les pièces sont étonnamment élevées, car l'équipement se déplace à 24-30 kilomètres par heure [15-19 miles par heure] et la plomberie voit des pressions de pulvérisation de 276-414 KPa [40-60 psi].
Plus léger, meilleur, plus rapide
Après trois ans, la collaboration s'est avérée si fructueuse qu'en 2018, Deere a acquis King Agro, qui construit désormais des rampes dans ses installations et les expédie aux usines John Deere à Des Moines, Iowa, États-Unis, et Horst, Pays-Bas, pour l'assemblage final. L'accord permettrait à King Agro de conserver son nom de marque, sa marque et ses relations commerciales.
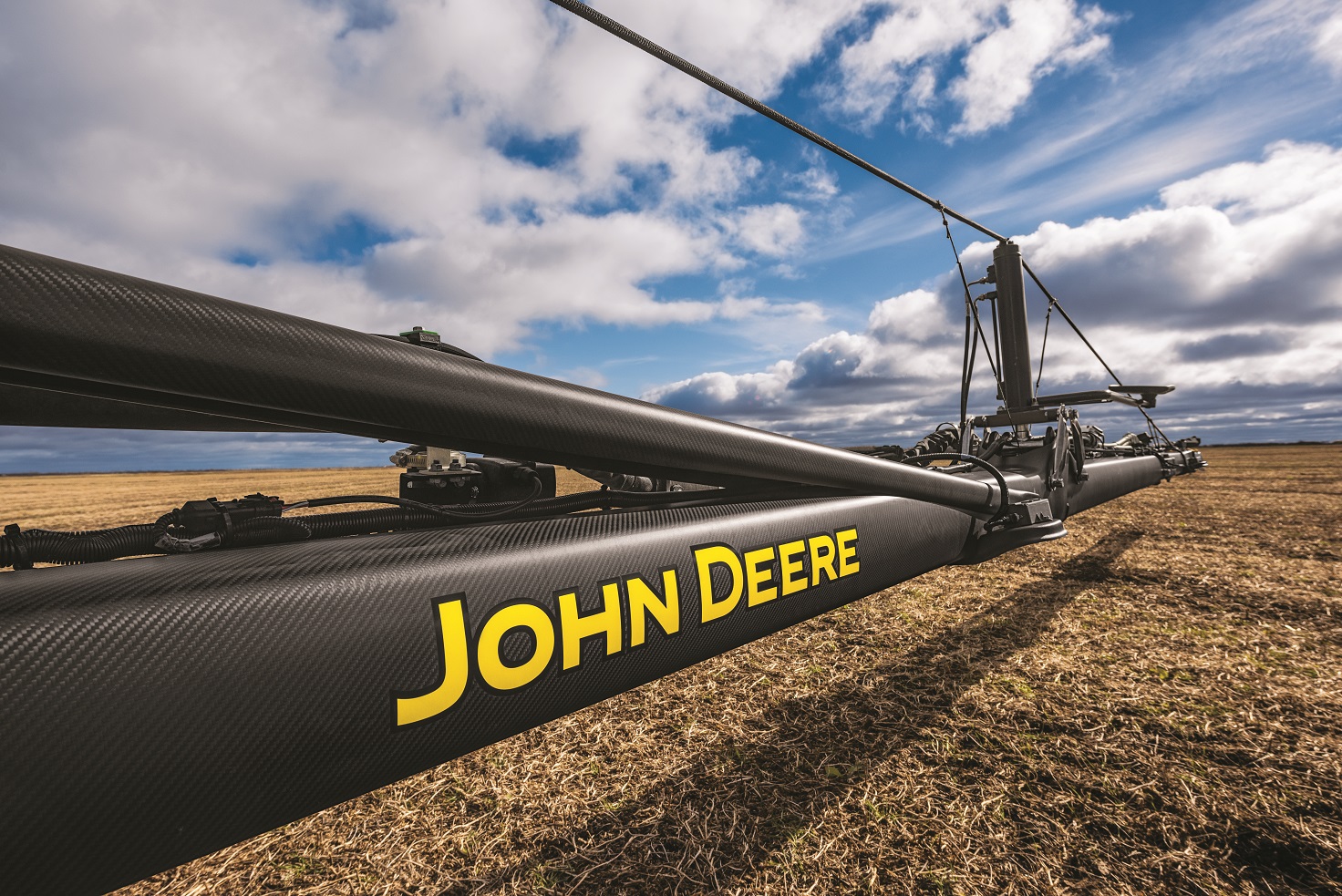
Les avantages de rampes plus légères. Des flèches plus légères signifient une meilleure économie de carburant, moins d'entretien, une plus grande largeur de travail, une durée de vie plus longue, des coûts d'exploitation inférieurs, une réparabilité plus facile sur le terrain et une meilleure efficacité avec moins de traînées de machine pour un plus grand volume de récolte. Origine | Deere &Co.
La conversion aux composites a permis aux rampes de s'étendre au-delà de 36 mètres (120 pieds) à 40 mètres (132 pieds). Comparé à l'acier, le CFRP est six fois plus résistant, 5,5 fois plus léger, offre un impact plus important et ne se corrode pas. Des flèches plus légères signifient une meilleure économie de carburant, moins d'entretien, une plus grande largeur de travail, une durée de vie plus longue, des coûts d'exploitation inférieurs et une meilleure efficacité avec moins de traînées de machine pour un plus grand volume de récolte. Un autre avantage est la réparabilité. « Nos revendeurs peuvent prendre une panne catastrophique, couper le composant en deux, ajouter de la résine, le serrer et le laisser durcir et ils sont prêts à partir », ajoute Nelson. "C'est en fait plus facile à réparer que de souder de l'acier."
« Le meilleur, ce sont les avantages pour le client », ajoute Bartlett. « Avec les produits en fibre de carbone, ils peuvent être plus productifs. Ils peuvent aller plus loin sans pénalité de poids, couvrir plus d'acres, subir moins de compactage du sol et la réduction de la pression au sol affecte positivement le rendement. »
Ferree est d'accord :« Du point de vue de la conception, les composites nous permettent de faire des choses que nous ne pouvions pas faire avec les matériaux actuels, qui étaient à leurs limites structurelles et de largeur », explique-t-il. « Nous avons effectué une transition solide entre nos offres d'acier et nos offres de CFRP haut de gamme, en particulier dans les Amériques, car nous apportons une productivité plus élevée, ce qui, dans ce segment, est plus large. Des flèches plus légères et plus larges peuvent être installées sur des tracteurs plus petits et moins coûteux. Ou, plus de liquide peut être transporté sur un tracteur donné tout en maintenant la même masse. Dans tous les cas, l'équilibre de charge entre les essieux avant et arrière est amélioré et le centre de gravité est plus proche du centre de la machine, améliorant ainsi la conduite pour l'opérateur. »
« Nous voyons des applications pour la fibre de carbone dans d'autres produits », prédit Aaron Wetzel, vice-président, Deere ag &turf Crop Care Platform. "Dans les années à venir, nous explorerons d'autres opportunités où la légèreté et les capacités plus solides que l'acier ajouteront une valeur supplémentaire à nos produits pour nos clients."
Résine
- Composites TPE ultra-légers pour chaussures
- Les prix se stabiliseront-ils pour les résines de base ?
- Des hayons élévateurs EV pour stimuler la demande de LFT PP
- RS Electric Boats sélectionne Norco pour la fabrication de composites
- Thermocouple haute température PEEKSense pour le durcissement des composites PEEK
- Solvay composites sélectionnés pour catamaran de course
- Récolter les bénéfices :l'utilisation des composites se développe dans les équipements agricoles
- Équipement de travail :est-il temps de procéder à une mise à niveau ?
- Préparation de l'équipement pour l'expédition à l'étranger