Composites thermoplastiques recyclés pour la production
La recyclabilité est un avantage promis depuis longtemps grâce à l'utilisation de composites thermoplastiques (TPC). Mais il n'a pas encore été utilisé commercialement à grande échelle. Le fournisseur de matériaux TenCate Advanced Composites et le ThermoPlastic composites Research Center (TPRC) se sont associés au fabricant de niveau 1 GKN Fokker pour démontrer un tel processus en 2016. L'équipe a développé un panneau de porte d'accès à l'aide de ferraille TenCate Cetex TC1100 tissé en fibre de carbone/sulfure de polyphénylène (CF/ PPS) de la production de GKN Fokker de l'ascenseur et du gouvernail Gulfstream G650. Les déchets de production ont été hachés puis moulés par compression à l'aide d'un procédé et d'un moule conçus par TPRC. Le panneau de la porte d'accès comportait des nervures de renforcement moulées, des variations d'épaisseur et des trous moulés avec des bossages. (Un bossage est un élément saillant qui guide une attache dans le trou). L'utilisation du matériau récupéré a permis d'obtenir une pièce légère avec une plus grande fonctionnalité moulée tout en formant un processus de fabrication en boucle fermée, car le panneau de porte d'accès a ensuite été utilisé sur le bord d'attaque du gouvernail Gulfstream G650. Le projet a remporté un JEC Innovation Award en 2016.
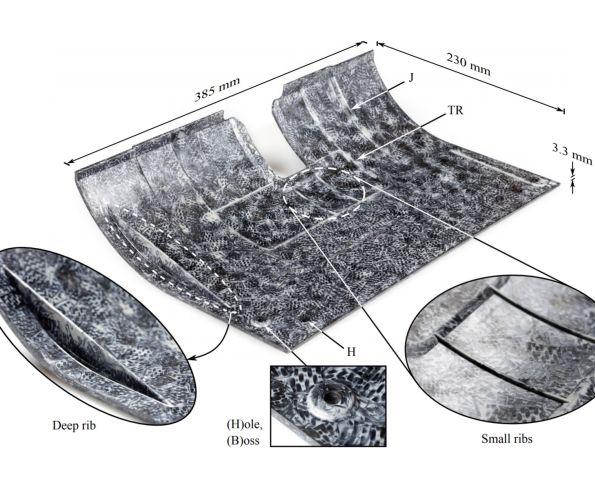
Panneau de porte d'accès démontré en 2016 est fabriqué à partir de matériaux de rebut Cetex CF/PPS et comporte des nervures de renforcement et des trous moulés avec des bossages. SOURCE | TPRC.
Depuis cette recherche, une nouvelle organisation a été mise en place, le ThermoPlastic composites Applications Center (TPAC). « Le TPRC a été créé il y a dix ans et travaille principalement dans la recherche fondamentale de TPC pour l'industrie aérospatiale », explique Thomas de Bruijn, chercheur en structures légères au TPAC. « Le TPAC a été formé à peu près deux il y a des années, et a une façon de travailler plus appliquée. Il est lié à l'Université Saxonne et également aux PME. Nous nous concentrons sur la réduction des coûts en développant des processus plus rentables. Ensemble, ces deux groupes forment TPC NL, une industrie intelligente, un pôle d'innovation numérique pour la technologie TPC. »
L'implication du TPAC ainsi que la R&D continue de TenCate ont démontré que ce type de fabrication en boucle fermée est non seulement possible, mais économiquement avantageux. Au départ, l'accent est mis sur les matériaux CF/PPS, et la recherche est menée en collaboration avec des partenaires de l'industrie pour aider à mettre en œuvre cette production de pièces améliorée par le recyclage TPC.
Cependant, les processus réels développés diffèrent. TenCate s'est concentré sur un matériau à fibres plus courtes utilisé comme couche d'écoulement pour ajouter des caractéristiques géométriques moulées et des fonctionnalités aux pièces en fibres continues. Pendant ce temps, TPRC et TPAC ont cherché à maintenir une plus grande longueur de fibre, créant un matériau semblable à une pâte qui peut être moulé par compression en pièces avec des propriétés mécaniques plus élevées que celles possibles avec les composés traditionnels à fibres courtes.
TenCate — Pièces organo-feuilles améliorées pour la couche Flow
« Il y a trois ans, nous avons commencé à investir une plus grande partie de notre budget de R&D dans le recyclage », déclare Frank ten Napel, chef de produit TenCate pour les thermoplastiques. « Il ne s’agit pas seulement d’obtenir un ‘label vert’. Nous sommes convaincus que l'incorporation de matériaux recyclés dans votre pièce offre de réels avantages économiques et constructifs. Nous pouvons appliquer un niveau de géométrie à une pièce que nous ne pourrions pas atteindre autrement. En appliquant une couche fluide de matériau recyclé, nous pouvons mouler des nervures de renforcement et d'épaisseur variable à travers la pièce, ainsi que des bossages autour des trous, qui répartissent les charges induites par les fixations. Tout cela permet d'utiliser moins de fibres continues, pour des pièces plus fines, plus légères et plus économiques par rapport à l'utilisation de matériaux vierges. » Il note que ces caractéristiques moulées sont difficiles à obtenir avec des matériaux à fibres continues, "mais en combinant à la fois des fibres continues et un surmoulage localisé, vous obtenez plus de liberté de conception."
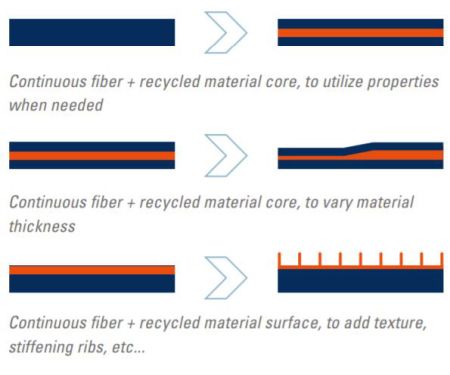

Ce démonstrateur de type bracket montre les deux faces d'une même pièce, mettant en évidence une couche d'organosheet tissée conventionnelle et une couche d'écoulement en TPC recyclé. Ce dernier présente des nervures de rigidification et des bossages pour inserts. SOURCE | TenCate
Projet Cycle TPC
Ce projet de quatre ans a débuté en septembre 2015 et comprend des partenaires de toute la chaîne d'approvisionnement des composites thermoplastiques (TPC) :
- TenCate Advanced Composites (Toray Group) – matériaux
- GKN Fokker Aerostructures - Conception et fabrication de niveau 1 de structures et d'assemblages aérospatiaux
- Composants thermoplastiques néerlandais (DTC) - PME de conception et de fabrication de nervures, longerons, supports, clips, boîtiers pour l'aérospatiale
- Cato Composites - PME de fabrication et de conception de pièces pour les marchés de l'aéro, de l'automobile, de la défense, du sport et de la consommation
- Nido RecyclingTechniek (NRT) – technologie de broyage et de réduction de la taille des matériaux/pièces à recycler
TPC-Cycle est facilité par TPAC et l'Université des sciences appliquées de Saxion, en particulier son groupe de recherche sur les structures légères, et financé par Regieorgaan SIA, qui fait partie de l'Organisation néerlandaise pour la recherche scientifique (NWO).
Thomas de Bruijn est chef de projet TPC-Cycle et chercheur en structures légères chez Saxion/TPAC. Il explique qu'il y avait de nombreux pilotes pour démarrer le projet TPC-Cycle. « Nous avons pu constater une augmentation de l'utilisation des TPC à fibres continues, en particulier pour le formage de tampons, comme dans les clips et les supports. Avec cette augmentation, le volume de déchets post-industriels devient important. Ainsi, le recyclage était nécessaire, à la fois pour l'environnement et l'économie, et aussi pour répondre aux réglementations. Par exemple, la législation européenne sur la fin de vie exige que 95 % des matériaux utilisés dans les automobiles soient recyclés. Il note qu'Airbus s'est également fixé des objectifs de recyclage et de fin de vie, et les a communiqués à ses fournisseurs. « La chaîne d'approvisionnement doit non seulement dire qu'elle peut atteindre ces objectifs, mais également prouver cette capacité avec des démonstrateurs », ajoute de Bruijn.
"Nous avons également vu les TPC se développer en dehors de l'aérospatiale, dans des applications telles que les caisses de nourriture, les meubles et les composants industriels, car ils offrent des temps de cycle plus courts, des structures légères et plus intelligentes", déclare de Bruijn.
Il poursuit :« Nous voulions prouver une chaîne de processus de recyclage commercialement viable, mais pas seulement le broyage, qui est le downcycling. Nous voulions des performances élevées. Nous avons donc choisi une approche de mélange à faible cisaillement pour conserver une longueur de fibre de 0,5 à 1,0 pouce. Pour la rigidité, vous n'avez besoin que de quelques mm de longueur. Mais pour la solidité et la résistance aux chocs, vous avez besoin de plus de 0,5 pouce de longueur. En plus de maintenir la longueur des fibres, un autre défi clé était d'obtenir une bonne homogénéité dans le mélange des matériaux et dans le produit recyclé final.
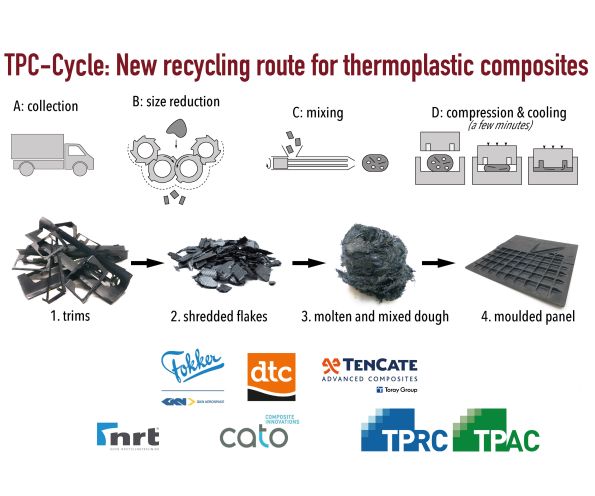
"L'objectif est de collecter les déchets, de les broyer en flocons de 0,5 à 1,0 pouce et de les transformer en une pâte homogène, qui est extrudée et directement transférée dans une presse de moulage par compression", explique le chercheur et doctorant du TPRC. étudiant Guillaume Vincent. « Le traitement de la pâte se fait en alimentant des flocons et des granulés de polymère vierge dans un mélangeur à faible cisaillement, ce qui réduit la fraction pondérale des fibres à 25-40%. » Il note que le processus est très similaire au compoundage direct des thermoplastiques à fibres longues (D-LFT), qui est courant dans l'automobile. « Cependant, les processus D-LFT nécessitent des millions de dollars d'investissement, ils ne sont donc utilisés que dans la production en grande série. Nous avons modifié notre approche en utilisant des machines plus petites, mais nous obtenons des résultats similaires. Nos volumes sont faibles par rapport aux processus D-LFT. »
Vincent décrit un exemple où l'inclusion de la chaîne de valeur complète du recyclage est payante :« NRT nous a aidés à nous connecter avec des fabricants de broyeurs plus gros, comme Untha. » Il s'agit d'un élément clé de la mise à l'échelle du processus de production de pièces en série.
La première chaîne de processus en cours de développement est pour CF/PPS. Vincent dit que TPC-Cycle a construit des modèles de simulation et des méthodes d'analyse pour caractériser la longueur et la distribution des fibres dans le matériau recyclé. « Nous comprenons également comment ces caractéristiques matérielles se transfèrent aux propriétés de la pièce moulée », observe-t-il. C'est d'ailleurs l'objet de son doctorat. thèse, qui sera publiée d'ici la fin de 2019.
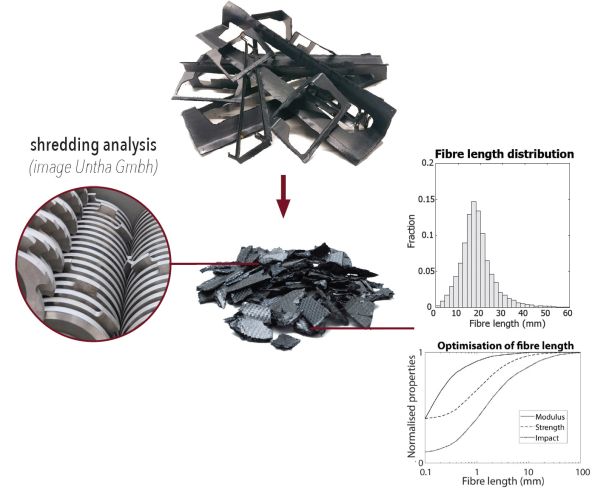
Le TPC- Le projet Cycled a développé une chaîne de processus complète pour le recyclage des composites thermoplastiques, y compris le déchiquetage rentable et la caractérisation de la longueur et de la distribution des fibres. SOURCE | TPRC/TPAC.
Cette pâte recyclée est parfois appelée composé de moulage en vrac (BMC). Historiquement, le BMC était un mélange pâteux de fibres de verre courtes (<25 mm), de pâte de résine thermodurcissable et de charges moulées par compression en pièces composites. Avec moins de volume de fibres et plus de fluidité par rapport au composé de moulage en feuille (SMC), il offrait également des propriétés mécaniques légèrement inférieures. TenCate a vendu des thermodurcissables et thermoplastiques BMC pendant des années, bien que ce dernier soit un processus dans lequel des bandes préimprégnées unidirectionnelles hachées sont étalées dans un moule et pressées. « Notre produit est en fait assez différent », affirme Vincent. « Avec le BMC thermoplastique conventionnel, il n'y a généralement pas de mélange et nécessite un long cycle de chauffage et de consolidation. Nous avons constaté qu'avec le mélange, vous obtenez un produit plus homogène et moins de concentrations de contraintes dans la pièce, donc des propriétés plus élevées. Avec le BMC thermoplastique conventionnel, vous obtenez des flocons plus épais qui ont des régions riches en matrice aux extrémités qui produisent des concentrations de contraintes dans le stratifié composite. »
Le processus de mélange à faible cisaillement démêle les flocons en couches, puis sépare les couches en faisceaux et les faisceaux en fibres lâches. Le polymère est également mélangé pour diminuer la teneur en fibres afin d'obtenir de meilleures propriétés d'écoulement, de sorte que le matériau est plus facile à transformer en formes.
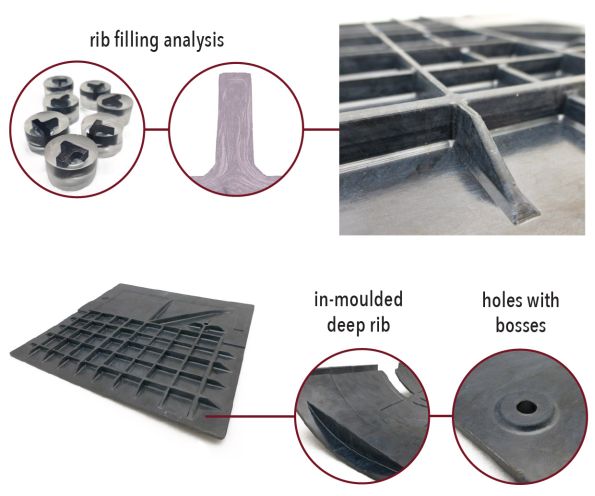
« La pâte est extrudée puis placée de manière robotique dans un moule de compression ouvert et isotherme [chauffé] », explique de Bruijn. « Après le malaxage, les fibres de la pâte sont orientées de manière aléatoire. Mais lors du pressage, le flux de matière réoriente les fibres. Cette orientation est moindre par rapport aux mélanges utilisant des fibres plus courtes moulées par injection, mais elle est similaire d'une pièce à l'autre. C'est l'un de nos sujets d'étude continue. »
Coût
La chaîne de processus TPC-Cycle développée à ce jour apparaît économiquement avantageuse. « Nous espérons savoir dans quelle mesure nous pouvons réduire les coûts des pièces plus tard en 2019 », déclare de Bruijn. "Mais c'est complexe car vous avez besoin d'un marché et devez vendre le matériau recyclé." Il note qu'il existe de nombreux facteurs économiques. Par exemple, la plupart des fabricants d'aujourd'hui se contentent de jeter les déchets de production. Le coût local de mise en décharge est de 80 € par tonne (90 $). «Mais ce matériel jeté a de la valeur», déclare de Bruijn. « En outre, vous devez prendre en compte les coûts de collecte des déchets, de les déchiqueter, de les mélanger puis de les mouler par compression en de nouvelles pièces. Cependant, il s'agit également d'un processus presque en forme de filet avec des temps de cycle courts en raison de la moisissure isotherme. En d'autres termes, il devrait y avoir une réduction ou une élimination drastique de la finition secondaire et de l'usinage. De Bruin indique que TPC-Cycle envisage maintenant de terminer l'analyse des coûts et l'analyse du cycle de vie.
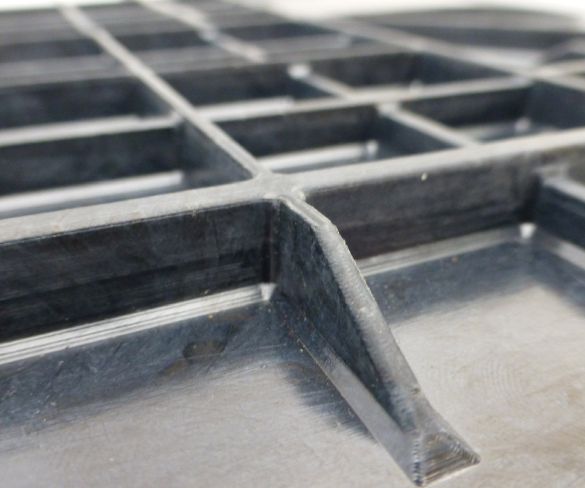
SOURCE | TPRC/TPAC
Réinitialiser le ciel propre
Un troisième projet qui réitère l'importance du travail réalisé par TenCate et également dans le projet TPC-Cycle est le projet RESET, qui s'est déroulé de janvier 2016 à décembre 2017 et a été coordonné par l'Institut technologique Leitat à Barcelone, en Espagne. Il semble que RESET ait été commencé sous Clean Sky (2008-2016) et achevé pendant Clean Sky 2 (2017-2021).
Les programmes Clean Sky et Clean Sky 2 sont organisés en un niveau supérieur de programmes de démonstration d'avions innovants (voir les IADP de véhicules dans l'image ci-dessous) et un niveau inférieur de démonstrateurs de technologies innovantes (voir les grands systèmes ITD dans l'image ci-dessous). La RÉINITIALISATION a été effectuée dans le cadre de l'ITD de la cellule, en particulier du Work Package (WP) A-3.4 Eco-Design for Airframe.
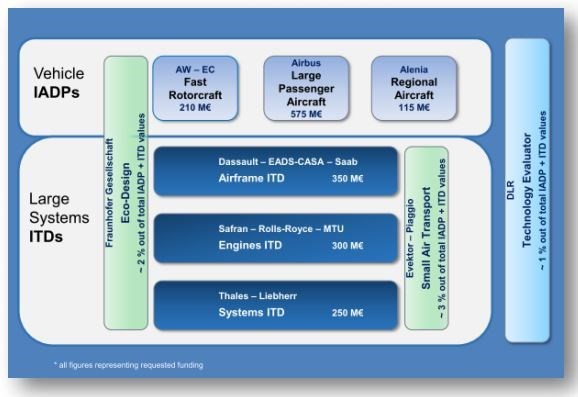
SOURCE :nettoyer Technique conjointe Sky 2 Proposition
Pour plus de détails, voir "Démonstrateurs composites thermoplastiques — Feuille de route de l'UE pour les futures cellules"
Selon Elena Pedone, responsable du projet Clean Sky, l'équipe RESET de Leitat a développé un processus pour recycler les matériaux composites d'avions précédemment utilisés et les utiliser pour fabriquer de nouvelles pièces. Ils ont comparé ces pièces recyclées à celles fabriquées commercialement et ont découvert qu'elles avaient des caractéristiques mécaniques similaires. "La technologie développée dans ce projet pourrait être commercialisée de manière réaliste dans le secteur aéronautique au cours des prochaines années et éventuellement se répercuter sur d'autres secteurs économiques", déclare Pedone.
Au cours du projet RESET, des travaux ont été menés pour étudier les effets des matériaux matriciels thermoplastiques PEEK et PPS et la nature chimique du renforcement en fibre de carbone. La forme du renfort a été étudiée, y compris la longueur des fibres et le tissé par rapport au non tissé. L'effet de la teneur en fibres (rapport polymère/fibre) a également été étudié.
Dans un deuxième lot de travaux, l'objectif principal était le conditionnement et la caractérisation de CF/PPS recyclés basés sur l'extrusion et les composites moulés résultants. Deux parties - un support thermoplastique et un taquet thermoplastique - ont été créées par moulage par injection et deux autres par thermoformage, explique la coordinatrice scientifique du projet Leitat, Claudia Aguilar. Ces pièces ont ensuite été testées. « Les propriétés mécaniques du matériau se sont avérées comparables à celles de son équivalent commercial », explique Aguilar.
Le projet RESET prétend avoir démontré un processus de recyclage qui peut prendre les déchets de TPC de la production d'avions et les utiliser comme matière première pour produire de nouvelles pièces pour avions. « Jusqu'à 70 % des matériaux recyclés ont été utilisés pour produire une nouvelle famille de matériaux composites », explique Aguilar. Elle ajoute que « le processus de recyclage de RESET permet à l'aviation européenne de limiter l'empreinte environnementale et de réduire les coûts de production des nouvelles pièces d'avion. Par conséquent, le projet rend l'industrie aéronautique plus compétitive et plus verte. »
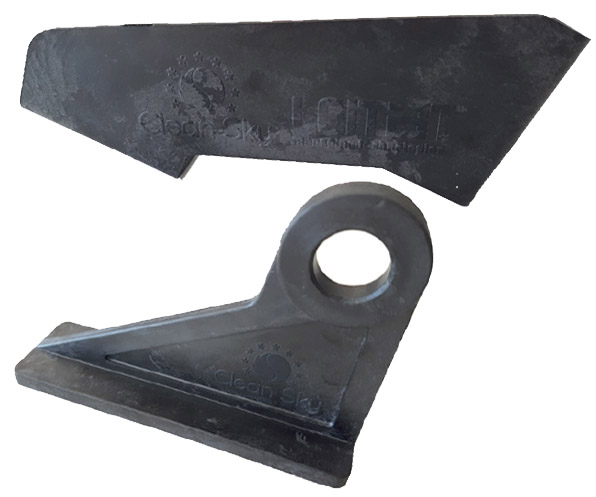
Support (à gauche) et taquet (à droite) fabriqués à partir de matériaux CF/PPS recyclés démontrés par le projet Clean Sky RESET. SOURCE | Institut technologique Leitat
L'avenir de TPC commence par le design
L'affirmation de TenCate et TPRC/TPAC est que ces procédés de recyclage qui ont maintenant été démontrés ne sont pas seulement verts, mais économiquement attractifs. Alors, quel type d'investissement est nécessaire? « Cela dépend du volume de production », explique Ten Napel chez TenCate. « Les broyeurs nécessaires ne sont ni volumineux ni coûteux et le processus a été développé de manière à être assez simple. » Le type de matrice affecte-t-il la recyclabilité ? "Non", dit Ten Napel, "mais en termes de viabilité économique, la fibre de carbone et le PPS, le PEEK ou le PEKK sont plus viables que la fibre de verre et le polypropylène en raison de leur valeur plus élevée par rapport à ce dernier."
"Je pense que si cela doit être repris par l'industrie, cela devrait commencer par le design", poursuit-il. « Le plus gros obstacle à l'heure actuelle est l'état d'esprit des ingénieurs. Sortir et concevoir avec des matériaux recyclés (ou les concevoir partiellement dans un nouveau produit) est assez nouveau pour eux. »
Ten Napel concède que TenCate ne conçoit ni ne fabrique de pièces commercialement, "mais nous essayons d'inspirer les concepteurs à penser de cette façon lors du développement de leurs nouvelles pièces et structures". Il cite les intérieurs d'avions, les panneaux d'accès et les portes d'accès comme des fruits à portée de main pour la réutilisation de matériaux recyclés. « Si, en tant qu'industrie, nous pouvons nous habituer à réutiliser nos propres rebuts et déchets, alors nous pouvons passer à l'étape suivante et commencer à chercher comment traiter les pièces en fin de vie. »
Le mantra sur le recyclage des composites thermoplastiques - simplement le meulage et le remoulage - peut certainement être adopté, dit Ten Napel, mais cela n'a souvent pas beaucoup de sens sur le plan économique. « Nous avons démontré un meilleur processus et un qui peut réellement créer des pièces et des programmes globaux plus rentables. Nous avons choisi de diffuser ces connaissances, avec le TPRC et le TPAC, afin d'inspirer l'industrie sur ce qui est pleinement possible avec les composites thermoplastiques. Si les composites thermoplastiques doivent être adoptés à grande échelle, le recyclage en tant que partie intégrante de la production n'est plus une option, c'est une nécessité.
Résine
- Recyclage :composites thermoplastiques renforcés de fibres continues avec polycarbonate recyclé
- Biomatériau thermoplastique « affiné » pour les applications médicales
- Karl Mayer lance une ligne de production de rubans thermoplastiques UD
- INEOS Styrolution va construire un site de production pour le composite thermoplastique StyLight
- Hexion présente une solution époxy à deux composants pour la production de composites aérospatiaux
- Porte thermoplastique une première pour les composites automobiles
- LANXESS étend sa capacité de production de composites thermoplastiques renforcés de fibres continues
- Aperçu CAMX 2018 :TenCate Advanced Composites
- Soudage de composites thermoplastiques