Les composites permettent un nouveau hors-bord volant
L'électrification mondiale des transports est une évolution inégale, simultanément permise et entravée par la myriade de forces qui régissent le développement technologique et affectent tout, des automobiles et des aéronefs sans pilote au transport ferroviaire et aux engins marins. Ces forces habilitantes/entravantes comprennent des batteries à maturation rapide mais lourdes, une surveillance gouvernementale parfois lente à s'adapter, des principes de gravité et de friction, des exigences strictes en matière de sécurité des passagers, des assureurs anxieux et un développement inégal de matériaux légers.
Pourtant, les innovations en matière de matériaux, de traitement, de matériel et de logiciels rendent possibles des produits qui étaient inconcevables il y a quelques années à peine, et il n'y a peut-être pas de meilleur exemple que les Sept , un nouveau hors-bord à foils tout électrique, haut de gamme et tout composite, fabriqué par Candela Boats (Lidingö, Suède) à l'aide de solutions à matrice de résine fournies par Sicomin Epoxy Systems (Châteauneuf les Martigues, France).
Comment en sommes-nous arrivés ici
Candela Boats a été fondée en 2014 par le PDG Gustav Hasselskog qui, bien qu'ingénieur de formation, avait auparavant travaillé en tant que consultant et sur le marché des produits chimiques de consommation. De son propre aveu, Hasselskog « s'était ennuyé » du monde du travail en entreprise et a décidé qu'il voulait trouver un travail plus significatif. Il a quitté son emploi en entreprise en 2014 et, au cours de cet été, s'est retiré avec sa famille dans une maison située sur l'un des archipels qui entourent Stockholm, en Suède.
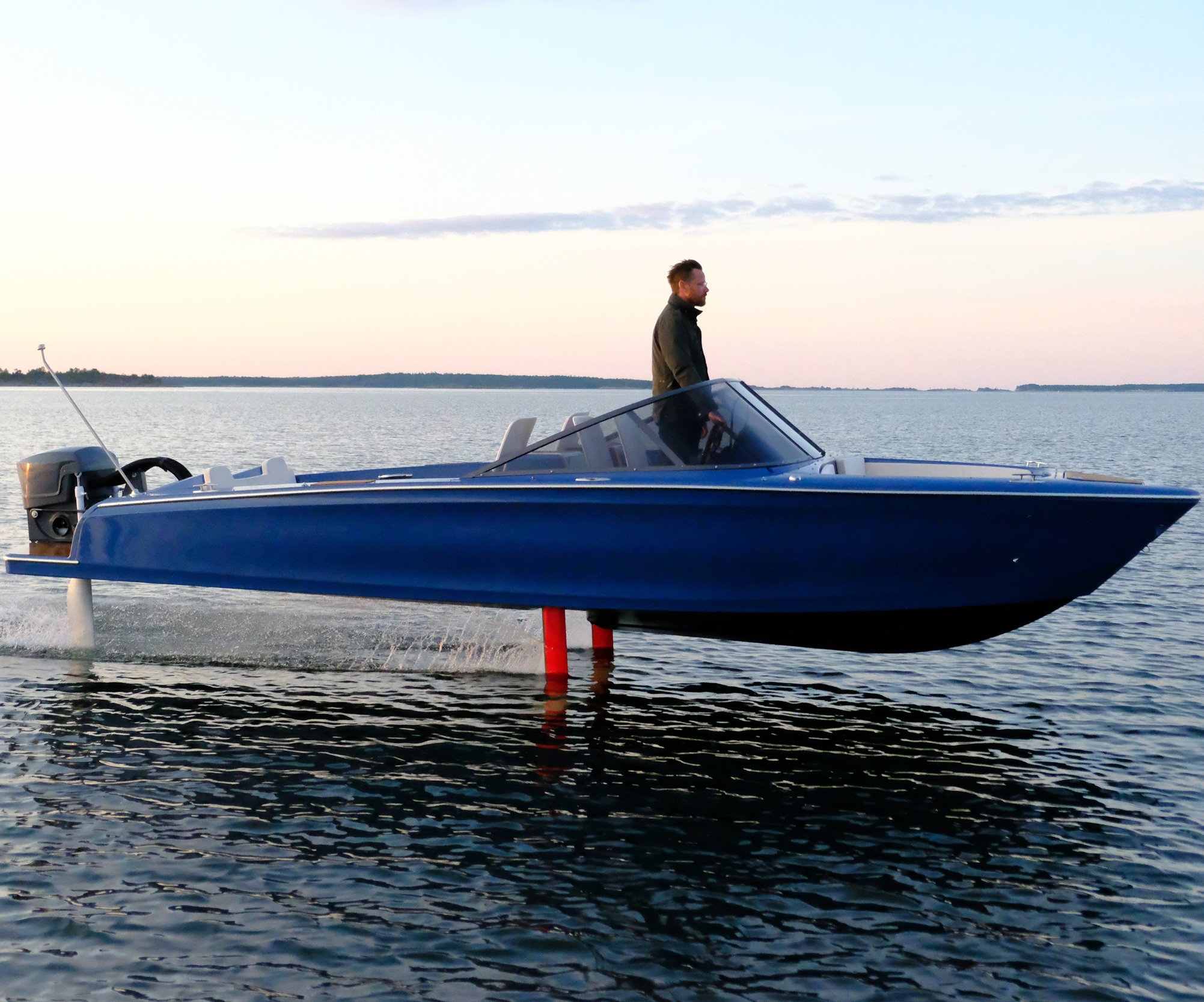
"Nous avions un bateau de 25 pieds avec un moteur V-8", se souvient Hasselskog, ajoutant que pour aller n'importe où et obtenir quoi que ce soit, il fallait un voyage en bateau jusqu'à Stockholm, qui coûtait au moins 50 $ par voyage. "C'était un peu bizarre de dépenser autant d'argent pour un bateau", dit-il. Hasselskog a commencé à faire quelques calculs, se demandant ce qu'il faudrait pour rendre la navigation de plaisance plus efficace. "Ce que j'ai découvert", dit-il, "c'est que le sujet n'a pas été abordé pour rendre les bateaux plus efficaces et les rendre électriques."
Hasselskog a commencé à étudier plus avant le marché de la navigation de plaisance. Il a étudié la technologie des batteries et de la propulsion électrique, déterminant ce qui serait nécessaire pour donner à un bateau planant une autonomie d'au moins 50 milles marins - un objectif qu'il jugeait raisonnable. Jusqu'à présent, l'application de la propulsion tout électrique dans les embarcations planantes a été entravée par le manque de puissance et le manque de portée, principalement en raison de la friction à la surface de l'eau qu'un bateau doit surmonter. De plus, pour augmenter la portée ou la puissance d'un bateau planant, il faut ajouter des batteries, ce qui ajoute également du poids et, par extension, de la traînée. Bref, a découvert Hasselskog, il n'était pas possible de rendre un bateau planant plus efficace. « Un bateau planeur est une impasse. Vous ne pouvez pas le rendre plus efficace », dit-il. « Déjouer est le seul moyen. » Ainsi, Hasselskog a vendu la maison d'été de la famille sur l'archipel, et en 2014, Candela Boats est né.
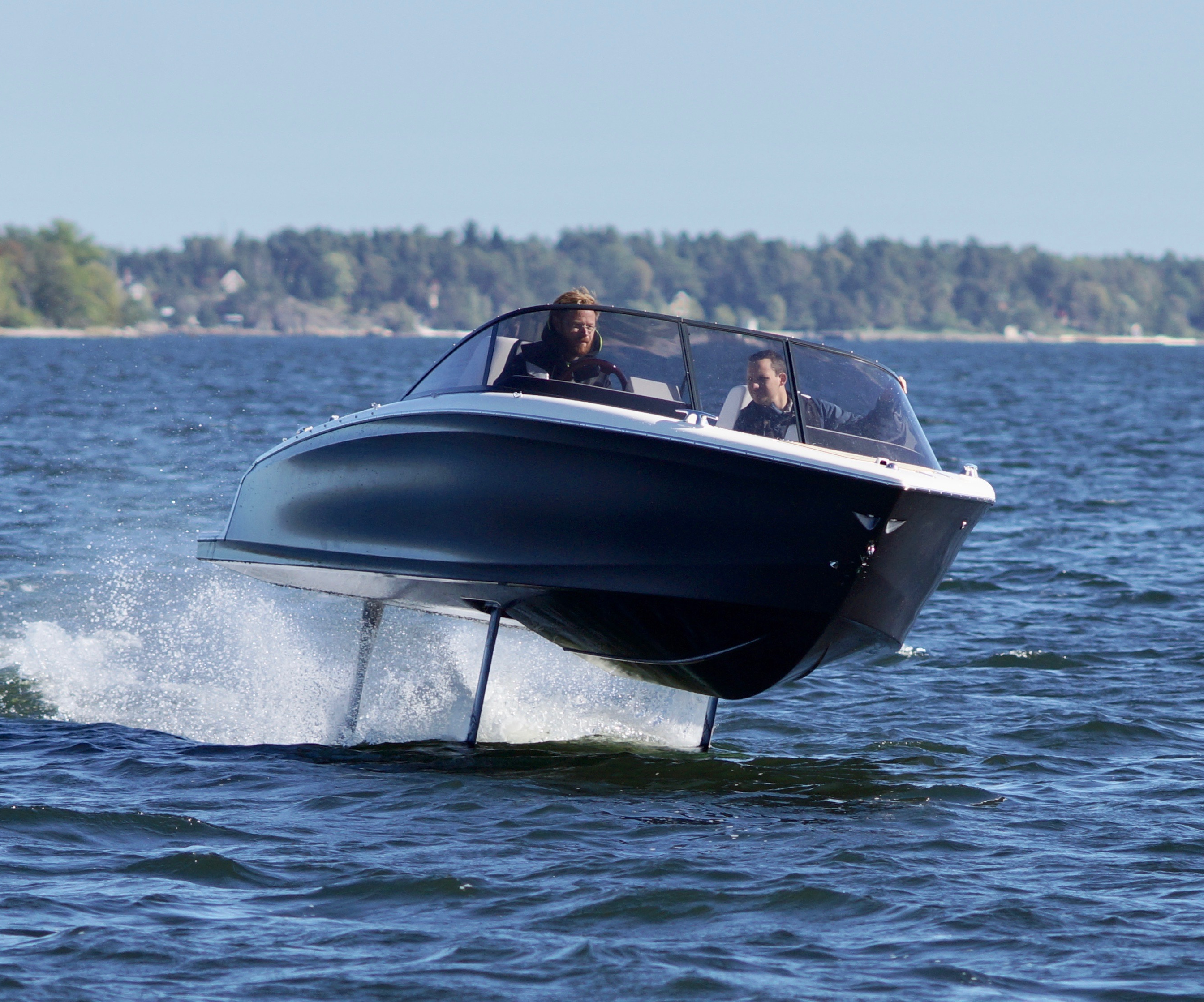
Le déjouage est intrinsèquement instable en raison de la thermodynamique complexe impliquée. Candela Boats a développé un système sophistiqué de capteurs et de commandes pour manipuler les foils et assurer une navigation fluide et sûre. Origine | Candela Bateaux
Déjouer n'est pas pour les âmes sensibles
Le principal défi du foiling réside dans l'instabilité inhérente d'un bateau qui se déplace et au-dessus l'eau, mais pas à la surface de l'eau. Un foil - ou, plus précisément, un hydrofoil - est une structure en forme d'aile attachée au fond d'une coque de bateau. Le foil traverse l'eau perpendiculairement à la direction de déplacement et, en utilisant les mêmes principes de vol d'un avion, à une certaine vitesse, il fournit suffisamment de portance pour élever le bateau complètement hors de l'eau. Le frottement de la coque est ainsi éliminé, laissant la traînée du foil et l'air comme seules résistances.
Les foils peuvent prendre diverses formes, mais dans tous les cas, ils doivent fournir une surface plane qui traverse le bord de l'eau en premier. Et, comme une aile d'avion, l'angle d'attaque d'un foil dans l'eau peut être ajusté pour augmenter ou diminuer la portance. Les foils peuvent également être déployés à différentes profondeurs d'eau, mais la profondeur a un effet sur l'efficacité. Par exemple, un foiling relativement peu profond et perçant la surface est plus stable, mais moins efficace. Un foil plus profond est plus efficace mais moins stable.
Dans tous les cas, « voler » au-dessus de l'eau présente un environnement hydrodynamique très différent de celui auquel est confronté un bateau planant à la surface de l'eau. Hors de l'eau et surfant sur des foils, un bateau se comporte de manière très différente :la répartition du poids, les virages, la résistance au vent et les eaux agitées doivent être soigneusement gérés.
La technologie du foil, bien que vieille de plus de 100 ans, était jusqu'à présent principalement utilisée dans les grands yachts de course et certains ferries à passagers. Les yachts de course à foils sont généralement pilotés par de grands équipages bien entraînés pour gérer une structure à foils dynamique et rapide. Les ferries à foils reposent sur des foils perforants, qui, comme indiqué, sont plus stables.
Hasselskog a décidé de rendre son hors-bord aussi efficace que possible et a donc opté pour des foils profonds . Le défi serait de faire en sorte qu'un bateau à foils profonds fonctionne facilement, de manière transparente et en toute sécurité, peu importe qui est au volant. Cela nécessiterait le développement d'un système de contrôle de foils sans précédent et d'une structure de bateau non seulement légère, mais conçue spécifiquement pour le foil.
Construire le foil parfait
Les Sept mesure 7,7 mètres de long, 2,4 mètres de large, pèse 1 300 kilogrammes et peut accueillir six personnes. Il utilise deux foils dont le plus grand est déployé à environ 2 mètres de l'avant du bateau. La conception du foil primaire est relativement simple :deux entretoises traversent la coque dans l'eau et se fixent à angle droit sur un foil de 2,35 mètres de long, 200 millimètres de large et 25 millimètres d'épaisseur. La feuille - également appelée feuille ∏ inversée - est orientée perpendiculairement à la direction de déplacement. Les supports de foil sont actionnés par moteur pour se déplacer de haut en bas pour abaisser et relever le foil. Lorsque le bateau ne foile pas, le foil est entièrement rétracté au ras de la coque du bateau. À des vitesses de foiling, le foil est déployé dans l'eau jusqu'à une profondeur maximale de 550 millimètres.
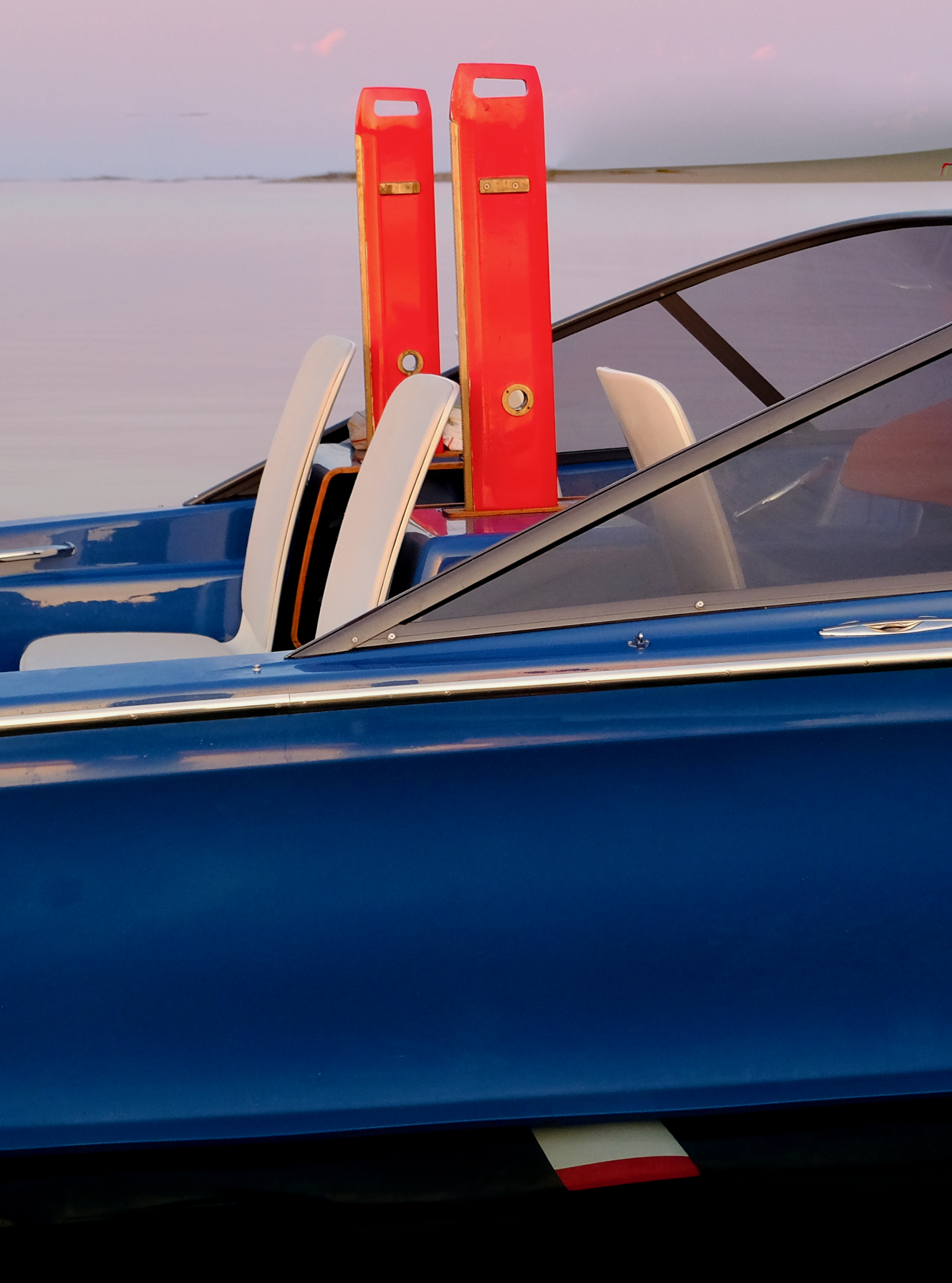
Lorsque les Sept n'est pas en mode foil, les deux entretoises orange qui se connectent et actionnent le foil pour le tirer au ras de la coque. Le foil blanc et orange est visible ici juste en dessous de la coque et juste au-dessus du niveau de l'eau. Origine | Candela Bateaux
À l'arrière du bateau se trouve un deuxième foil en T plus petit qui sert également de gouvernail. Il est attaché à un moteur électrique de 55 kilowatts qui actionne un arbre de transmission dans le gouvernail qui fait tourner une hélice à l'extrémité du gouvernail. Le moteur est alimenté par des batteries rechargeables, situées dans la partie très en avant de la coque, pour assurer l'équilibre lorsque le bateau est en foil. Les Sept commence à voler à 14-15 nœuds, navigue à 22 nœuds, a une vitesse maximale de 30 nœuds et une portée de 50 milles marins.
Teodor Hällestrand, chef de produit chez Candela Boats, déclare que les entretoises et les foils sont des composites fibre de carbone/époxy et ont posé un défi d'ingénierie de conception important. Pour fournir le contrôle requis pour une navigation en douceur, Candela devait être capable d'ajuster le foil aux conditions changeantes du bateau. Cela nécessite un système de capteur/contrôle très dynamique associé à une feuille très réactive. "Le foil est droit, mais nous voulions pouvoir le tordre dans l'eau, en fonction de la vitesse, de l'angle de roulis, de l'angle de tangage et de l'angle de lacet", explique Hällestrand. « Nous pouvons comprendre comment le bateau est positionné, puis ajuster l'orientation pour rendre la navigation aussi fluide que possible. » Ceci est accompli par le système de contrôle, qui ajuste dynamiquement les jambes de force soit pour changer l'angle d'attaque du foil, soit pour tordre le foil, en particulier pour tourner.
Hasselskog déclare :« Nous devons être capables de tordre le foil avant ou de fournir un angle d'attaque différent. » Toutes ces actions se produisent sous charge, dit-il, "nous avons donc besoin d'un matériau avec une faible rigidité en torsion, mais avec une rigidité à la flexion élevée." Le résultat est un « plan de superposition assez élaboré » qui utilise des rubans en fibre de carbone unidirectionnels (UD) (principalement ±45 degrés) pour fournir la rigidité et les capacités de flexion requises. La feuille utilise de la fibre de carbone à module standard provenant de divers fournisseurs et infusée de résine époxy SR1710 fournie par Sicomin Epoxy Systems. La feuille est durcie à température ambiante, suivie d'un post-durcissement à 40°C.
Pas votre coque moyenne
Nulle part n'est Sept L'écart des normes de conception de bateaux planants est plus apparent que dans la coque, à la fois dans la conception et l'ingénierie. Le plus remarquable est le fait que, bien qu'il présente une coque standard en forme de V et brise les vagues à l'avant du bateau, la coque est plate des foils avant à l'arrière. Hasselskog indique plusieurs raisons à cela.
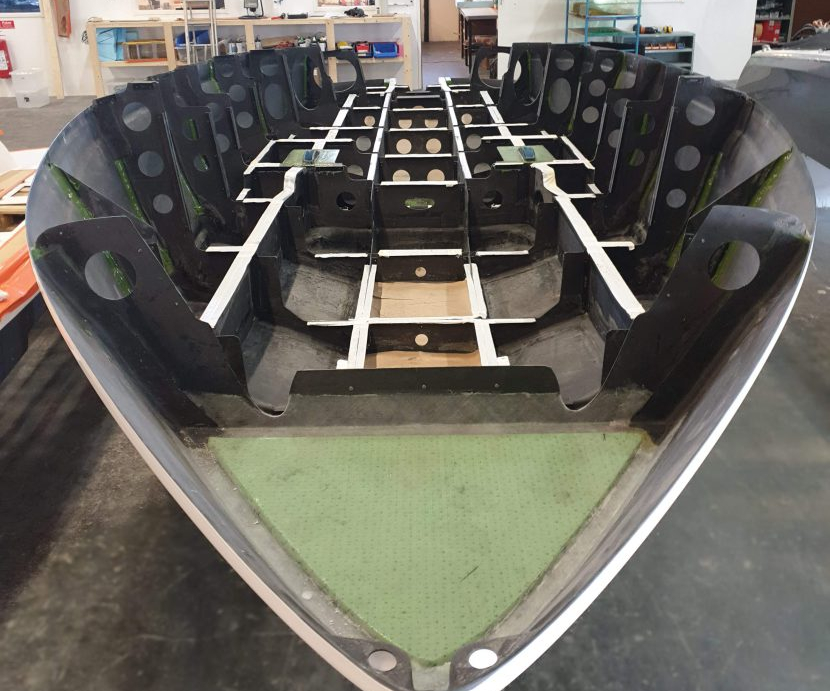
L'intérieur de Seven La coque de montre les longerons et les nervures qui sont découpés dans des stratifiés composites fibre de carbone/époxy, puis collés en place avec des attaches adhésives et mécaniques. Cette architecture permet à Candela Boats d'assembler rapidement des coques et offre une flexibilité pour s'adapter aux changements de conception. Origine | Candela Bateaux
Premièrement, dit-il, nous « n'avons besoin que de la forme en V pour percer les vagues ». Il protège également les foils lorsque le bateau ne foile pas. Deuxièmement, aplatir la moitié de la coque simplifie la fabrication et économise beaucoup de poids. Troisièmement, dit-il, le fond plat rend le bateau incroyablement stable au quai pour l'embarquement et le débarquement. « C'est comme une péniche », note-t-il.
À l'intérieur de la coque, cependant, c'est là que Candela a travaillé pour fabriquer le Seven non seulement structurellement sain, mais adaptable à une fabrication efficace et relativement élevée. Hällestrand dit que la coque est de conception comparable à un fuselage d'avion - une peau entourant un réseau de longerons et de nervures. Comme le foil, la coque est infusée, utilisant la même fibre de carbone UD et l'époxy SR1710, fabriquée sur un outillage composite également fabriqué avec du SR1710. L'épaisseur de la coque sous la ligne de flottaison est de 3 millimètres; l'épaisseur de la coque au-dessus de la ligne de flottaison est de 2 millimètres.
Marc Denjean, directeur des exportations chez Sicomin, explique que le SR1710 est un système époxy performant qui offre « des propriétés mécaniques bien au-dessus de la moyenne ». Sicomin fournit également un apprêt époxy à haut pouvoir garnissant dans le moule, ce qui signifie que la coque est démoulée prête à être peinte.
Pour construire les longerons et les nervures, Candela commence avec des panneaux infusés de fibre de carbone/époxy stratifié solide de 3 millimètres d'épaisseur, puis les usine CNC pour les mettre en forme, en fonction de l'endroit où le stratifié est placé dans la coque. Pour construire la structure de la coque - longerons et nervures - ces formes découpées sont ensuite assemblées et attachées les unes aux autres et à la coque avec un collage et des attaches mécaniques.
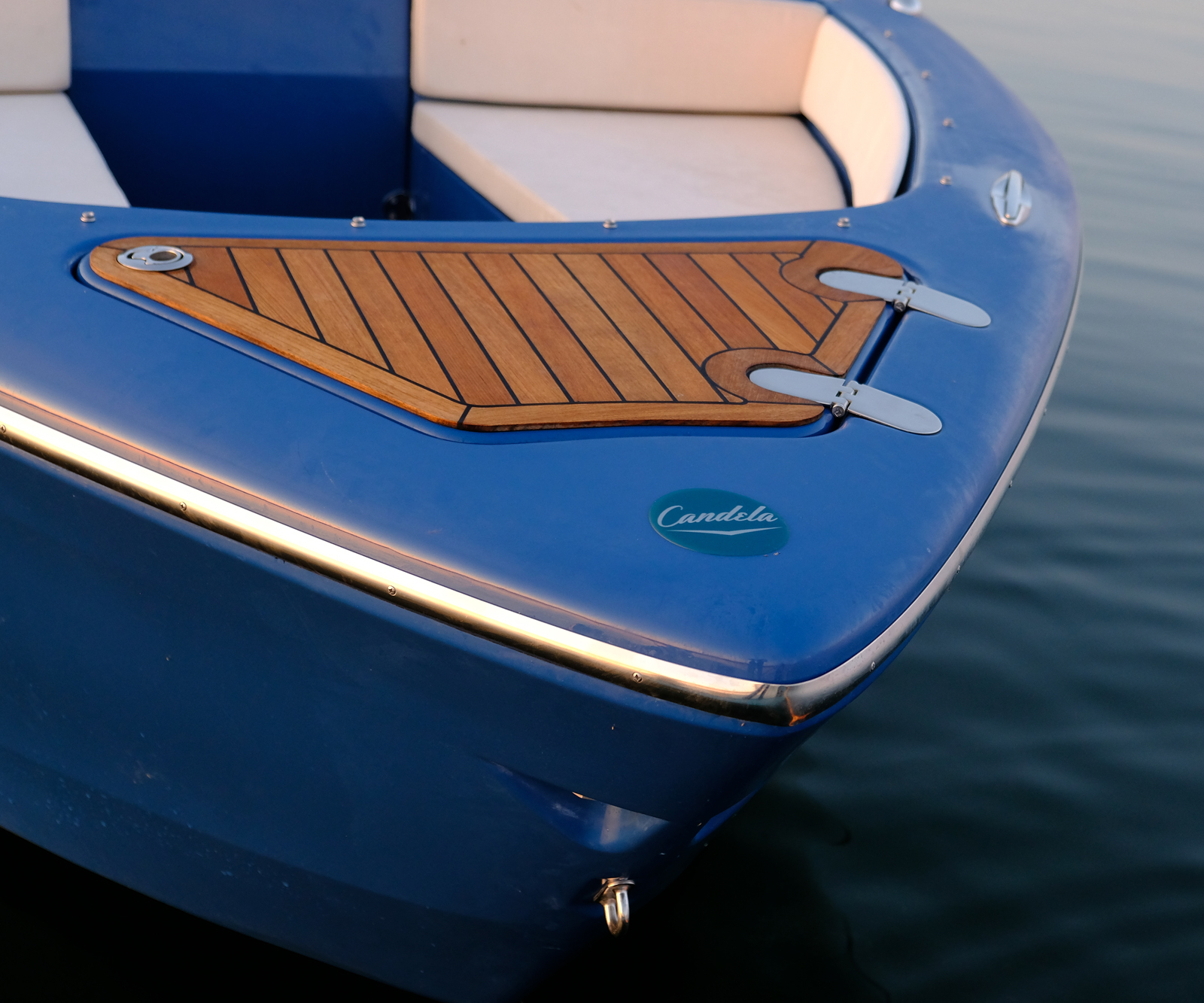
La batterie du Seven est situé dans la partie avant de la coque, pour fournir l'équilibre indispensable lorsque le bateau est en mode foil.
Origine | Candela Bateaux
Selon Hasselskog, ce processus de conception/fabrication par découpe et assemblage de stratifié s'est avéré très efficace et permet à Candela Boats de construire la structure de la coque en seulement 40 heures. Il permet également à l'entreprise d'ajuster facilement les structures internes pour concevoir des changements sans les dépenses et le temps requis pour modifier les moules. "Il est facile de faire évoluer, d'apporter des modifications ou de créer une nouvelle structure simplement en changeant le code d'usinage", dit-il.
L'essentiel
Conformément à la vision originale de Hasselskog, l'efficacité du Seven est difficile à battre - il est 4 à 5 fois plus économe en énergie qu'un bateau planant à essence comparable et convertit 90 % de son énergie chimique en énergie mécanique. De plus, le coût de possession du Seven , selon Candela, est 95% moins qu'un bateau planant à essence.
La société a 190 commandes pour le Seven, et il prévoit d'assembler 40 bateaux en 2020. Hasselskog dit qu'actuellement Candela est uniquement un concepteur et un assembleur de bateaux. La fabrication des structures composites est effectuée par des tiers, mais Hasselskog dit que Candela peut apporter ce travail en interne car elle cherche à optimiser les processus de fabrication et, en fin de compte, à réduire l'empreinte carbone de l'entreprise. « Nous devons réduire nos coûts, ce qui signifie une fabrication plus efficace », déclare Hasselskog. "Nous n'en sommes pas encore là, mais nous allons dans la bonne direction."
Résine
- CompositesWorld SourceBook 2022
- Composites Evolution présente des préimprégnés hautes performances, de nouveaux rubans UD thermoplastiques
- Dépannage du thermoformage des composites thermoplastiques
- L'évolution des composites additifs
- Composites thermoplastiques :support de pare-chocs structurel
- Des kits faciles à utiliser permettent la réparation sur le terrain des structures composites
- UMaine Composites Center reçoit 500 000 $ pour aider les constructeurs de bateaux à intégrer la technologie d'impression 3D
- Soudage de composites thermoplastiques
- Composites hautes performances en Israël