Des kits faciles à utiliser permettent la réparation sur le terrain des structures composites
Les ponts déployables modulaires sont un atout clé dans les opérations tactiques militaires et la logistique, ainsi que pour la restauration des infrastructures de transport lors de catastrophes naturelles. La construction composite est à l'étude pour réduire le poids de ces ponts, ce qui à son tour réduit la charge sur les véhicules de transport et les mécanismes de lancement-récupération. Les composites offrent également la possibilité d'augmenter la capacité de charge et de prolonger la durée de vie par rapport aux ponts métalliques.
Le pont composite modulaire avancé (AMCB) en est un exemple, conçu et construit à l'aide de stratifiés époxy renforcés de fibres de carbone (Fig. 1) par Seemann Composites LLC (Gulfport, Mississippi, États-Unis) et Materials Sciences LLC (Horsham, Penn., États-Unis). ). Cependant, la capacité de réparer de telles structures sur le terrain a été un problème entravant l'adoption des composites.
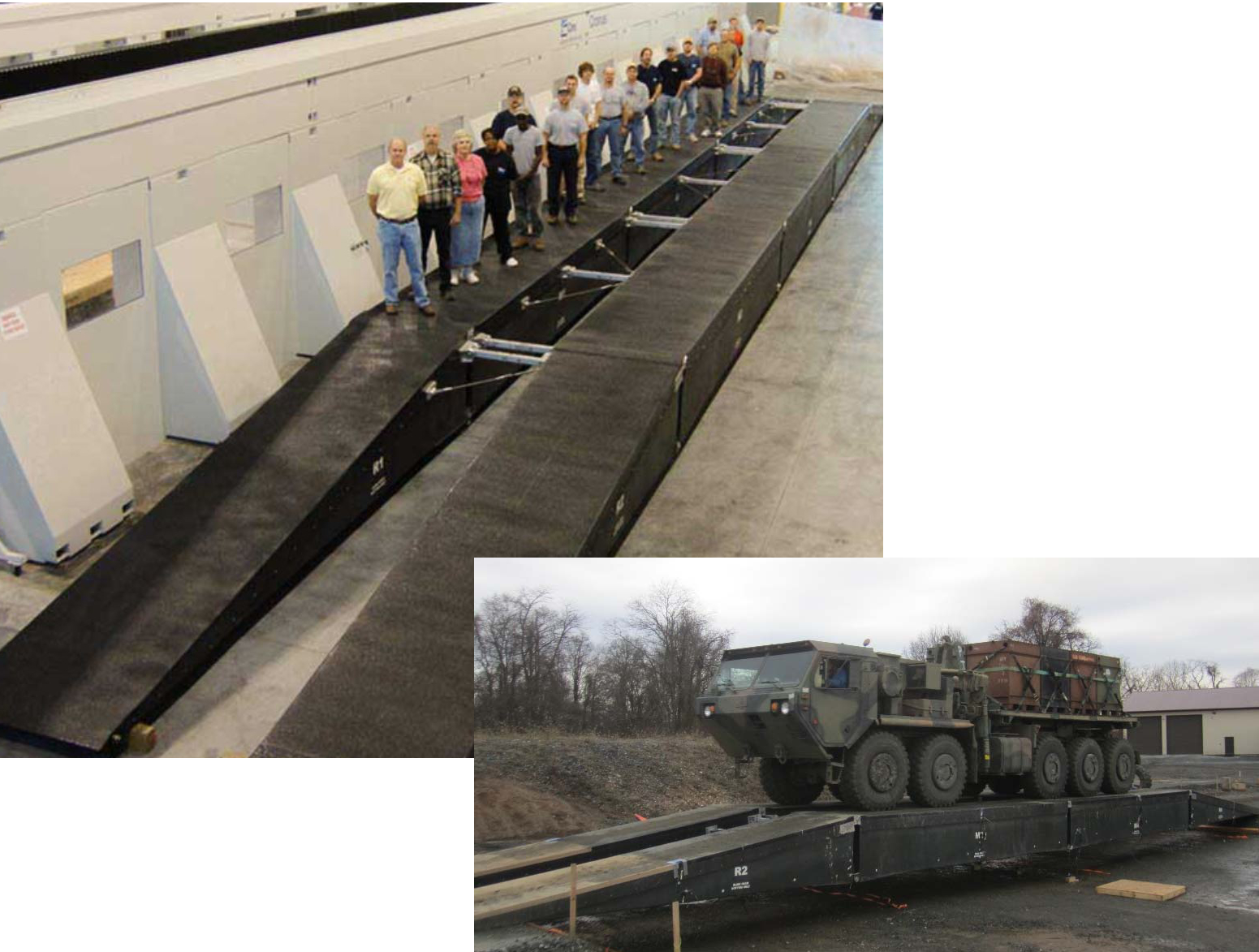
En 2016, Custom Technologies LLC (Millersville, Maryland, États-Unis) a reçu une subvention de phase I de Small Business Innovation Research (SBIR) financée par l'armée américaine pour développer une méthode de réparation pouvant être effectuée avec succès par des soldats sur le terrain. Sur la base de cette méthode, une subvention SBIR Phase II a été attribuée en 2018 pour démontrer de nouveaux matériaux et équipements fonctionnant sur batterie qui pourraient restaurer 90 % ou plus de la résistance d'origine de la structure, même lorsque la réparation de patch est effectuée par un novice sans formation préalable. . La faisabilité de la technologie a été établie en effectuant une série de tâches d'analyse, de sélection de matériaux, de fabrication d'échantillons d'essai et d'essais mécaniques, ainsi que des réparations à petite et à grande échelle.
Des ponts de navires fissurés aux ponts de pont
Le chercheur principal pour les deux phases du SBIR était Michael Bergen, fondateur et président de Custom Technologies LLC. Bergen a pris sa retraite du Naval Surface Warfare Center (NSWC) Carderock avec un mandat de 27 ans dans le département des structures et des matériaux, où il a géré le développement et l'application de technologies composites pour la flotte de la marine américaine. Le Dr Roger Crane a rejoint Custom Technologies en 2015 après avoir pris sa retraite de la marine américaine en 2011 avec 32 ans de service. Son expertise dans les composites comprend des publications techniques et des brevets couvrant des sujets tels que les nouveaux matériaux composites, la fabrication de prototypes, les méthodes d'assemblage, les composites multifonctionnels, la surveillance de la santé structurelle et la réparation des composites.
Ces deux experts avaient déjà développé un procédé unique qui utilisait des composites pour réparer les fissures dans les superstructures en aluminium 5456 du croiseur lance-missiles de classe USS Ticonderoga CG-47. « Ce processus a été développé pour réduire la croissance des fissures et servir d'alternative abordable au remplacement d'une plaque de pont de 2 à 4 millions de dollars », explique Bergen. « Ainsi, nous avions démontré que nous savions comment effectuer des réparations en dehors du laboratoire et dans un environnement de service réel. Mais le défi était que les méthodes actuelles pour les moyens militaires ne sont pas très efficaces. Les options sont une réparation de doublage collé [essentiellement en collant une plaque sur la zone endommagée] ou la mise hors service de l'actif pour les réparations au niveau du dépôt (niveau D). Il y a tellement d'actifs laissés de côté parce qu'une réparation de niveau D est nécessaire. »
Ce qu'il faut, poursuit-il, « c'est une méthode qui puisse être exécutée par un soldat sans expérience dans les composites, en utilisant uniquement un kit et un manuel de réparation. Notre objectif était de rendre le processus facile :lire le manuel, évaluer les dommages et effectuer la réparation. Nous ne voulions pas de mélange de résines liquides car cela nécessite une mesure précise pour assurer un durcissement complet. Nous avions également besoin d'un système sans déchets HAZMAT à gérer une fois la réparation terminée. Et il devait être conditionné sous forme de kits pouvant être déployés par les réseaux déjà en place. »
Nouveaux matériaux de patch collés
Une solution que Custom Technologies a démontrée avec succès est un kit portable qui permet un patch composite collé, adapté à la taille des dommages - jusqu'à un maximum de 12 pouces carrés - à l'aide d'un adhésif époxy renforcé. Des démonstrations ont été réalisées sur des composites représentatifs du pont AMCB de 3 pouces d'épaisseur, qui comprend un noyau en balsa de 3 pouces d'épaisseur (densité de 15 livres par pied cube) avec des revêtements comprenant deux plis de Vectorply Corp. (Phenix City, Ala., US) C-LT 1100 carbone 0°/90° tissu cousu biaxial, un pli de fibre de carbone C-TLX 1900 0°/+45°/-45° triaxial et deux autres plis de C-LT 1100 pour un total de cinq plis. "Nous avons décidé que le kit utiliserait des patchs préfabriqués dans une superposition quasi-isotrope de multiaxiaux similaires afin que l'orientation du tissu ne soit pas un problème", explique Crane.
Le problème suivant était la matrice de résine pour les réparations par stratification. Pour éviter de mélanger des résines liquides, le patch utiliserait des préimprégnés. "Cependant, le défi pour ceux-ci est le stockage", explique Bergen. Pour développer une solution de patch stockable, Custom Technologies s'est associé à Sunrez Corp. (El Cajon, Californie, États-Unis) pour développer un préimprégné en fibre de verre/ester vinylique qui durcit en six minutes à l'aide de la lumière ultraviolette (UV). Il a également travaillé avec Gougeon Brothers (Bay City, Michigan, États-Unis), qui a suggéré d'utiliser un nouveau film de résine époxy flexible.
Les premières recherches avaient déjà démontré que l'époxy était la résine la plus appropriée pour un préimprégné en fibre de carbone - l'ester vinylique à séchage UV fonctionne très bien avec les fibres de verre translucides mais ne durcit pas sous les fibres de carbone bloquant la lumière. Basé sur le nouveau film de Gougeon Brothers, le préimprégné époxy final a démontré un durcissement d'une heure à 210°F/99°C avec une longue durée de conservation à température ambiante - aucun stockage à basse température n'est requis. La résine durcira également à des températures plus élevées, dit Bergen, par exemple à 350 °F/177 °C si une température de transition vitreuse plus élevée (Tg ) est requis. Les deux préimprégnés sont fournis dans le kit de réparation portable sous forme de couches de patch préimprégnées pré-imprégnées scellées dans des enveloppes en film plastique.
Étant donné que les kits de réparation peuvent être stockés pendant une période prolongée, Custom Technologies a dû effectuer une étude de durée de conservation. « Nous avons acheté quatre étuis en plastique dur – typiques du type que l'armée utilise pour l'expédition du matériel – et avons placé des échantillons d'adhésifs époxy et de préimprégné d'ester vinylique dans chacun d'eux », explique Bergen. Les boîtiers ont ensuite été placés à quatre endroits différents pour être testés :sur le toit de l'installation de Gougeon Brothers dans le Michigan, sur le toit d'un aéroport du Maryland, à l'extérieur dans une installation de la vallée de Yucca (désert de Californie) et dans un laboratoire d'essais de corrosion en plein air. dans le sud de la Floride. Tous les cas avaient des enregistreurs de données, note Bergen, « et nous prélevions des données et des échantillons de matériaux tous les trois mois pour évaluation. Une température maximale de 140 °F a été enregistrée par les boîtes en Floride et en Californie, ce qui est un véritable défi pour la plupart des résines de réparation. De plus, Gougeon Brothers a testé en interne la nouvelle résine époxy pure. « Des échantillons conservés pendant des mois dans un four à 120 °F ont commencé à polymériser », explique Bergen. "Cependant, pour les échantillons correspondants maintenus à 110 ° F, la chimie de la résine n'a progressé que d'une petite quantité."
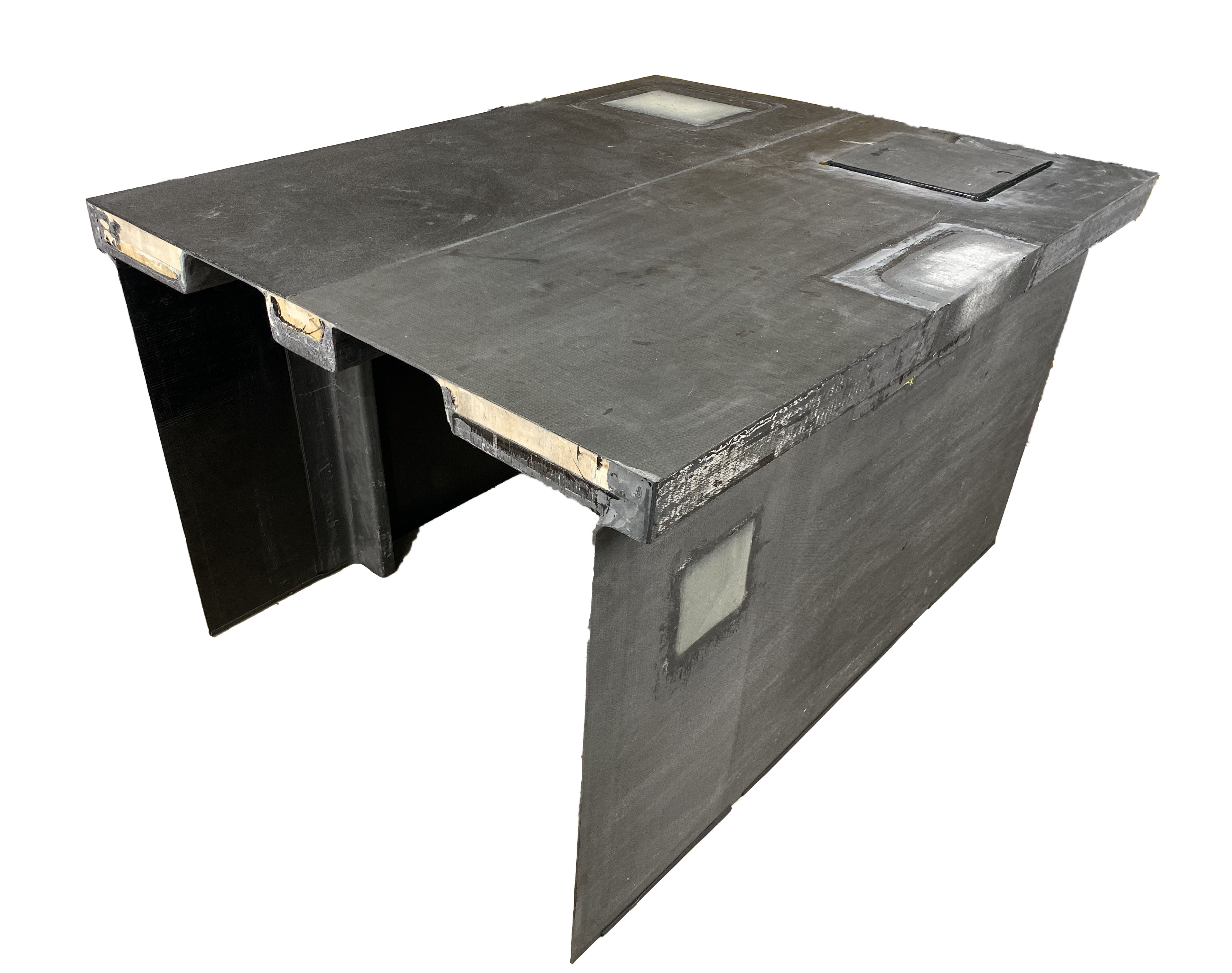
Test de réparation
Pour démontrer la technologie de réparation, des stratifiés représentatifs ont dû être fabriqués, endommagés puis réparés. « Dans la phase I du projet, nous avons d'abord travaillé avec des poutres à petite échelle de 4 x 48 pouces et des tests de flexion en quatre points pour évaluer la viabilité de notre processus de réparation », explique Crane. « Nous sommes ensuite passés à des panneaux de 12 x 48 pouces dans le projet de phase II, en appliquant une charge pour créer un état de contrainte biaxial à la défaillance, puis nous avons évalué les performances de réparation. Dans le projet de phase II, nous avons également terminé les réparations d'un modèle de l'AMCB que nous avions construit. »
Les panneaux de test utilisés pour démontrer les performances de réparation ont été fabriqués en utilisant le même pedigree en stratifié et en noyau que l'AMCB construit par Seemann Composites, dit Bergen, "mais nous avons réduit l'épaisseur de la feuille de face de 0,375 pouce à 0,175 pouce, sur la base des axes parallèles théorème. Cette approche, ainsi que des éléments supplémentaires de la théorie des poutres et de la théorie classique des stratifiés [CLT], a été utilisée pour relier le moment d'inertie et la rigidité effective de l'AMCB à grande échelle à des articles de démonstration de taille réduite plus faciles à manipuler et plus rentables. Nous avons ensuite utilisé des modèles d'analyse par éléments finis [FEA] développés par XCraft Inc. (Boston, Mass., États-Unis) pour affiner la conception des réparations structurelles. Les tissus en fibre de carbone pour les panneaux de test et le modèle AMCB ont été achetés auprès de Vectorply et le noyau en balsa a été fourni par Core Composites (Bristol, R.I., États-Unis).
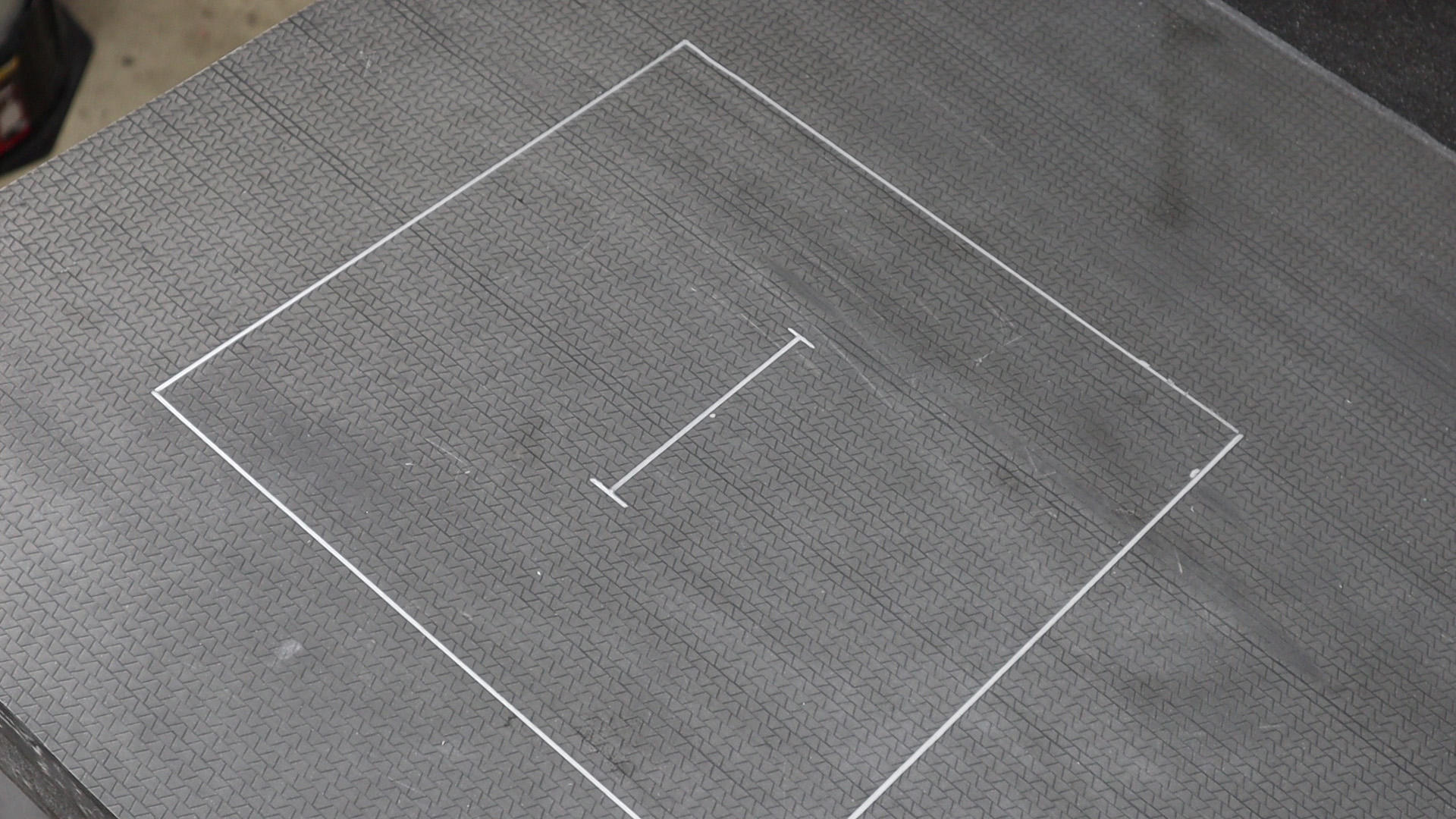
Étape 1. Ce panneau de test montre le diamètre du trou de 3 pouces pour simuler les dommages marqués au centre ainsi que le périmètre de réparation. Crédit photo pour toutes les étapes :Custom Technologies LLC.
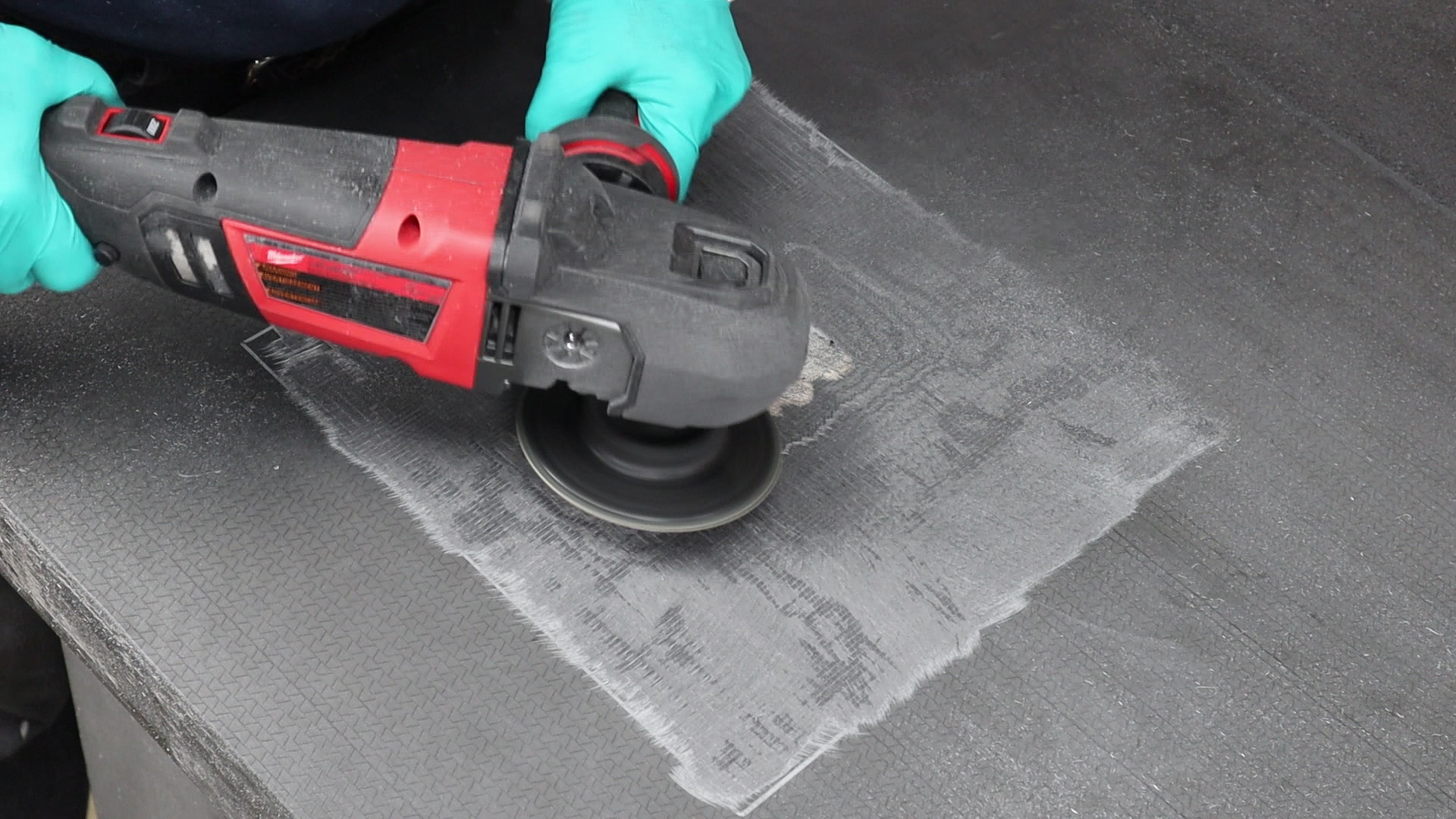
Étape 2. Une meuleuse à main alimentée par batterie est utilisée pour enlever le matériel endommagé et écharpe un cône 12:1 pour recevoir le patch de réparation.
« Nous voulions simuler un degré de dommage plus élevé dans les panneaux d'essai que ce qui est susceptible d'être observé sur les tabliers de pont sur le terrain », explique Bergen. « Donc, notre approche consistait à utiliser une scie cloche pour faire un trou de 3 pouces de diamètre. Nous avons ensuite retiré le bouchon du matériau endommagé et effectué un foulard 12:1 à l'aide d'un broyeur pneumatique portatif. »
Pour la réparation en fibre de carbone/époxy, explique Crane, une fois le matériau de la feuille de revêtement « endommagé » retiré et le foulard approprié appliqué, le préimprégné a été coupé en largeur et en longueur pour correspondre à la conicité de la zone endommagée. « Pour nos panneaux d'essai, cela nécessitait quatre couches de préimprégné qui ont permis au matériau de réparation d'être égal à la partie supérieure de la feuille de face en carbone d'origine non endommagée. Après cela, trois surcouches du préimprégné carbone/époxy ont été centrées sur cette section de réparation. Chaque pli successif s'étendait de 1 pouce sur tous les côtés du pli ci-dessous, ce qui a permis un transfert progressif de la charge du « bon » matériau environnant vers la zone réparée. Le temps total pour effectuer cette réparation - y compris la préparation de la zone de réparation, la découpe et la mise en place du matériau de réparation et l'application de la procédure de durcissement - était d'environ 2,5 heures.
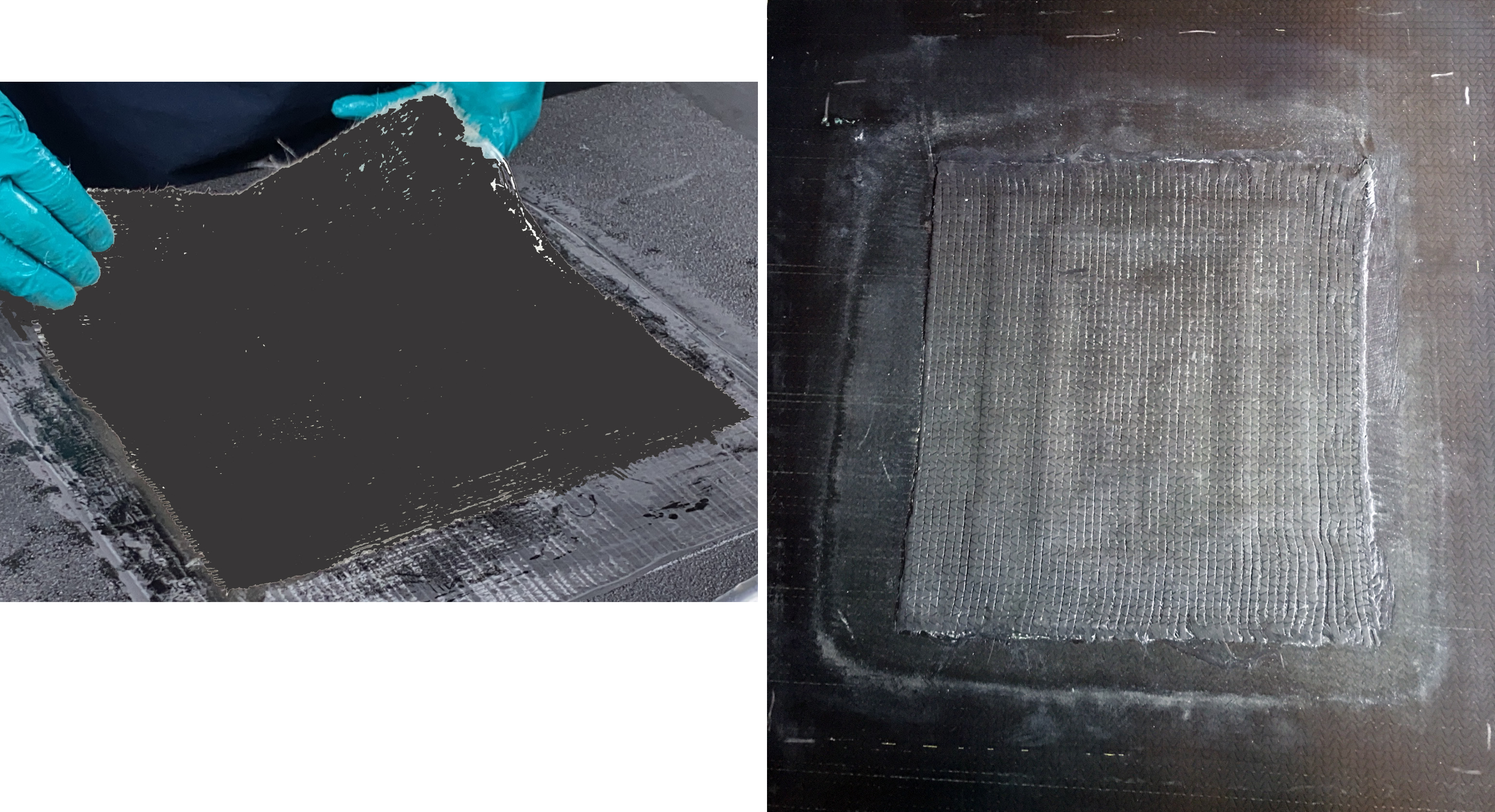
Même si la réparation carbone/époxy est simple et rapide, l'équipe a reconnu le besoin d'une solution encore plus rapide qui pourrait restaurer les performances. Cela a conduit à l'exploration du préimprégné durci aux ultraviolets (UV). « L'intérêt pour la résine vinylester Sunrez était basé sur l'expérience antérieure de la Marine avec Mark Livesay, qui a fondé la société », explique Bergen. « Nous avons commencé par fournir à Sunrez un tissu de verre quasi-isotrope à préimprégner avec son ester vinylique et avons évalué le profil de durcissement dans des conditions variées. De plus, sachant que la résine vinylester ne fournit pas des propriétés de liaison secondaire aussi appropriées que l'époxyde, un effort supplémentaire a été fait pour évaluer divers agents de couplage de la ligne de liaison et en qualifier un pour cette application. »
Un autre problème était que la fibre de verre n'offrait pas les mêmes propriétés mécaniques que la fibre de carbone. « Cela a été résolu en utilisant une couche supplémentaire de verre/ester vinylique par rapport au patch carbone/époxy », explique Crane. « La raison pour laquelle une seule couche supplémentaire était nécessaire était que le matériau en verre était un tissu plus lourd. » Il en a résulté un patch approprié qui a pu être appliqué puis durci en six minutes, même à des températures très froides/gelées à l'intérieur du champ sans avoir besoin de fournir de la chaleur. Crane note que cette réparation pourrait être effectuée en une heure.
Les deux systèmes de patch ont été démontrés et testés. Pour chaque réparation, la zone à endommager a été marquée (étape 1), créée avec la scie cloche puis enlevée à l'aide d'une meuleuse à main à batterie (étape 2). La zone de réparation a ensuite été réduite à un cône de 12:1. La surface éraflée a été nettoyée avec des tampons imbibés d'alcool (étape 3). Ensuite, le patch de réparation a été découpé sur mesure, positionné sur la surface nettoyée (étape 4) et consolidé avec un rouleau pour éliminer les bulles d'air. Pour le préimprégné en fibre de verre/ester vinylique durcissant aux UV, une couche pelable a ensuite été placée sur la zone de réparation et le patch a été durci à l'aide d'une lumière UV sans fil pendant six minutes (étape 5). Pour le préimprégné en fibre de carbone/époxy, la zone de réparation a été mise sous vide et durcie à l'aide d'un dispositif de liaison à chaud préprogrammé à un bouton fonctionnant sur batterie pendant une heure à 210 °F/99 °C.
Étapes de réparation
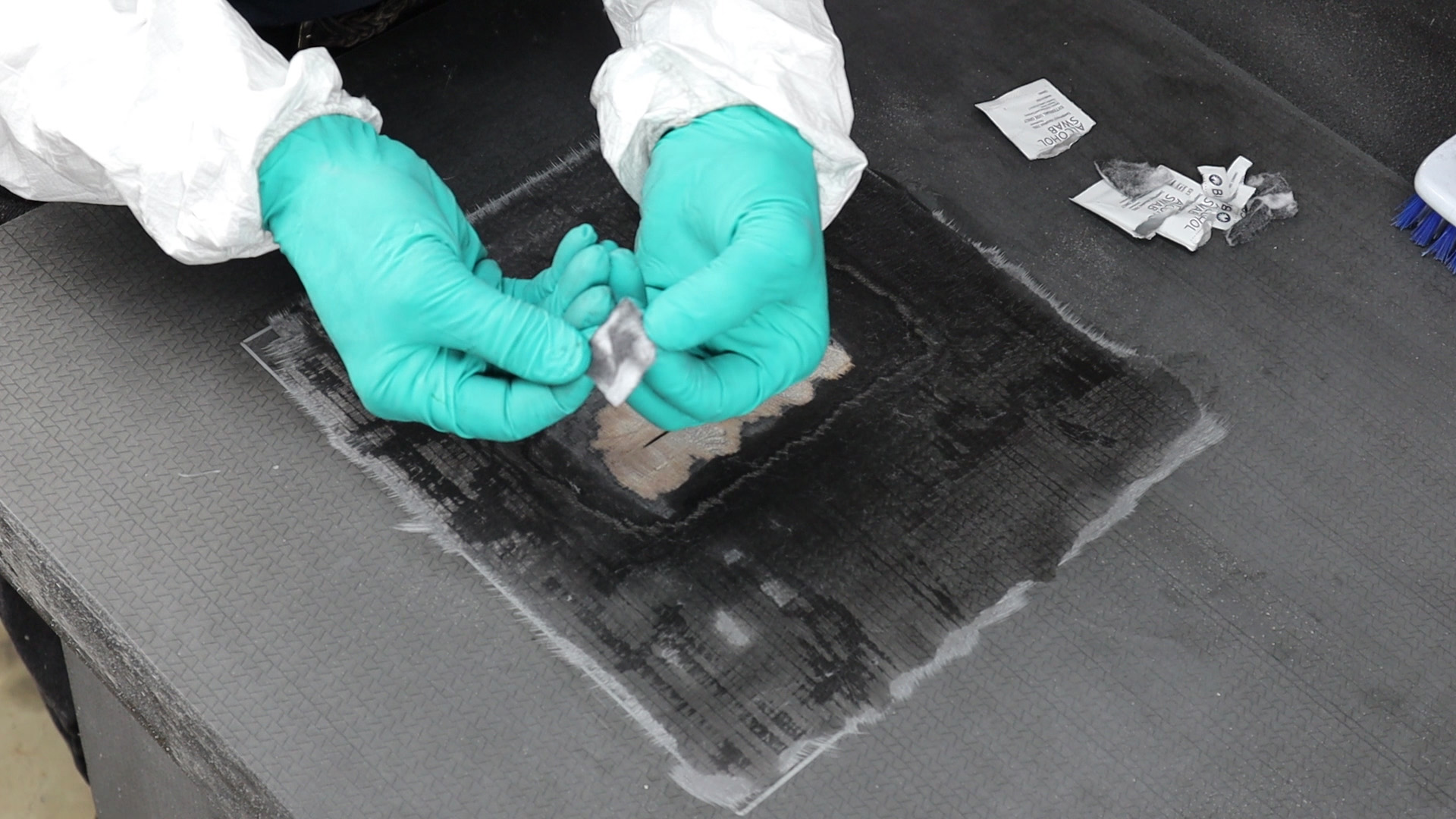
Étape 3. La zone de réparation préparée est ensuite nettoyée avec une lingette solvantée à l'aide de tampons d'alcool jetables.
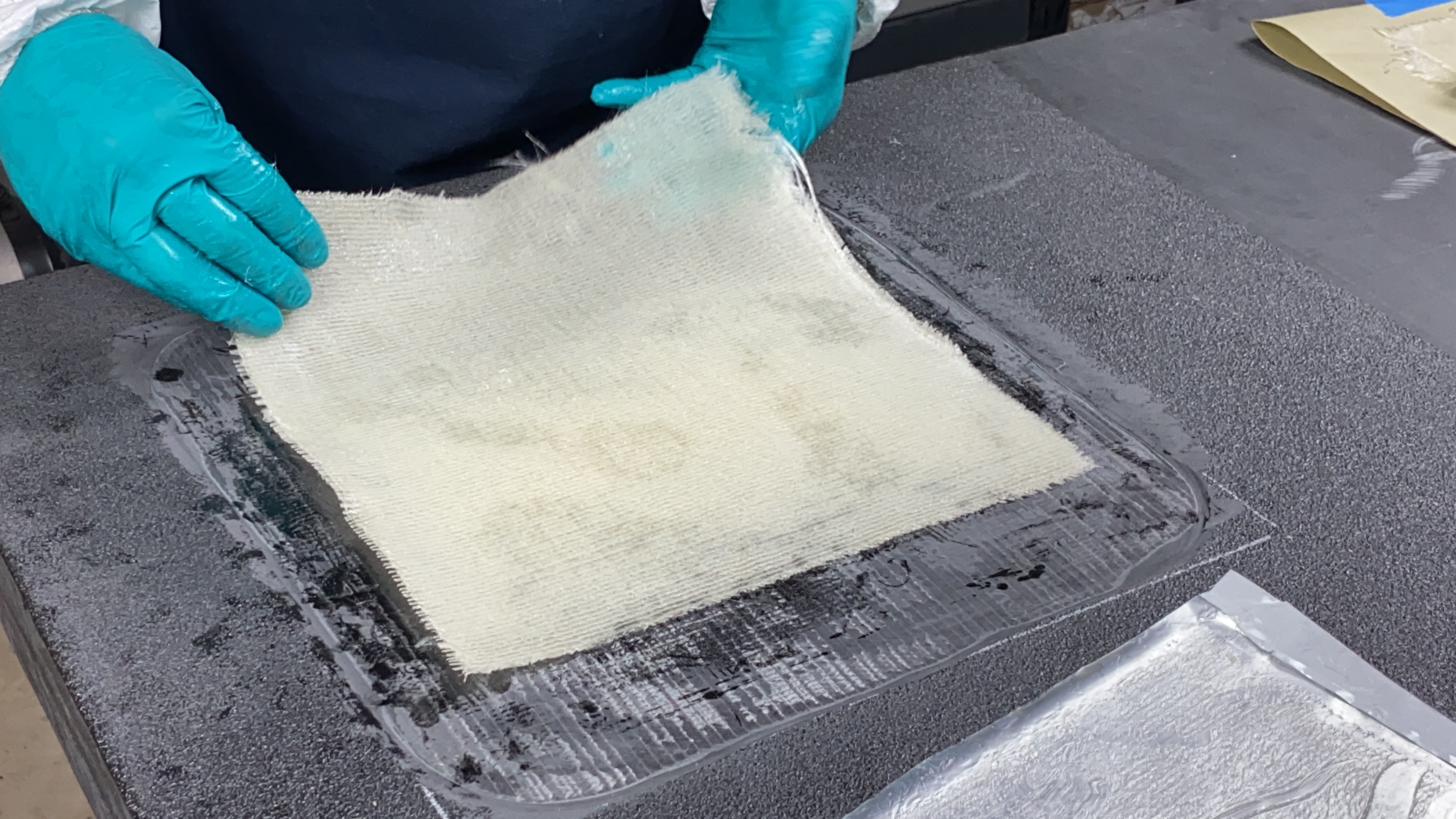
Étape 4. Le patch de réparation en fibre de verre/ester vinylique est coupé à la bonne taille et positionné sur la zone de réparation.
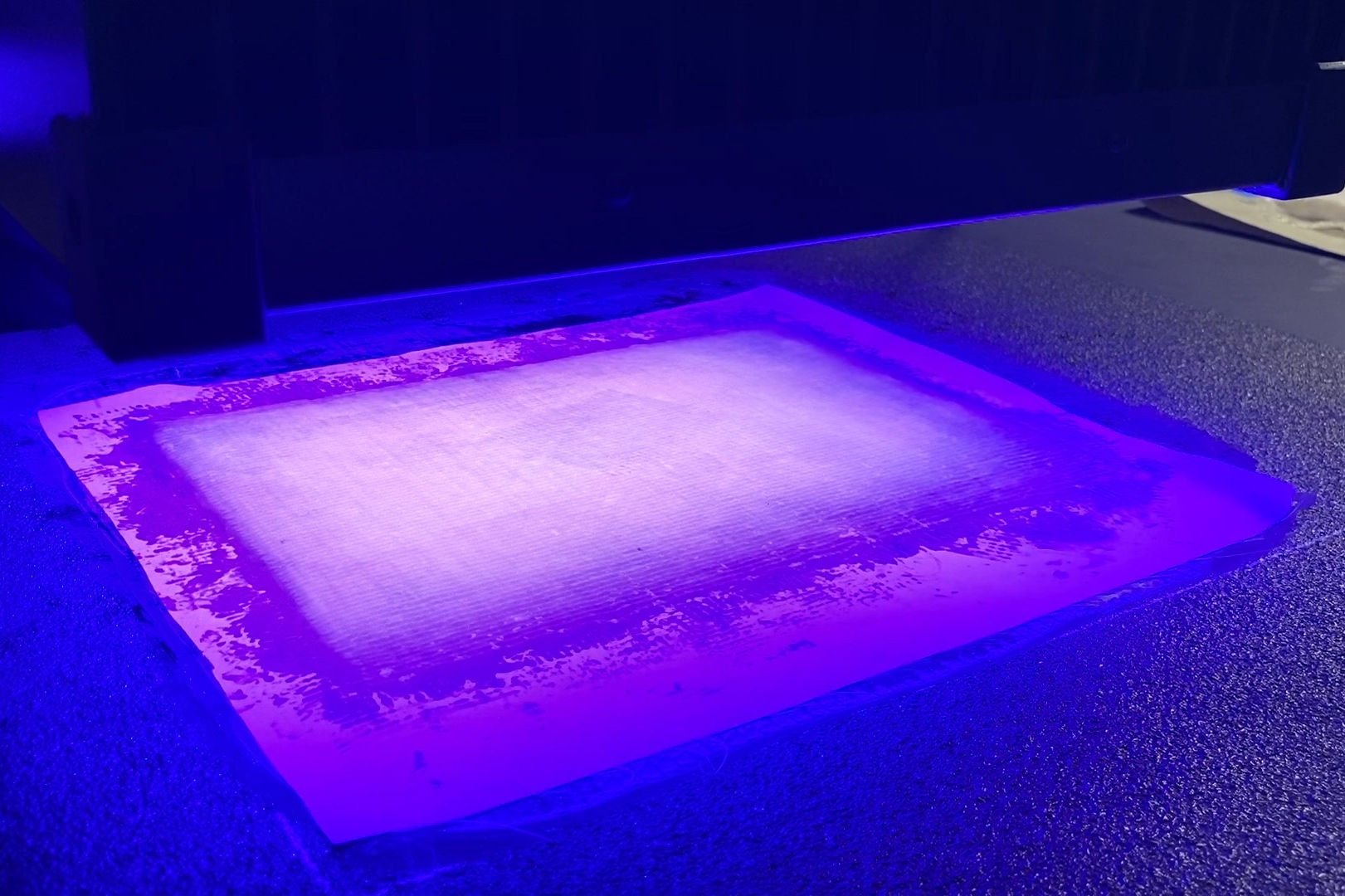
Étape 5. Après avoir placé une couche pelable sur la zone de réparation, le patch de réparation est polymérisé à l'aide d'une lampe UV sans fil pendant six minutes.
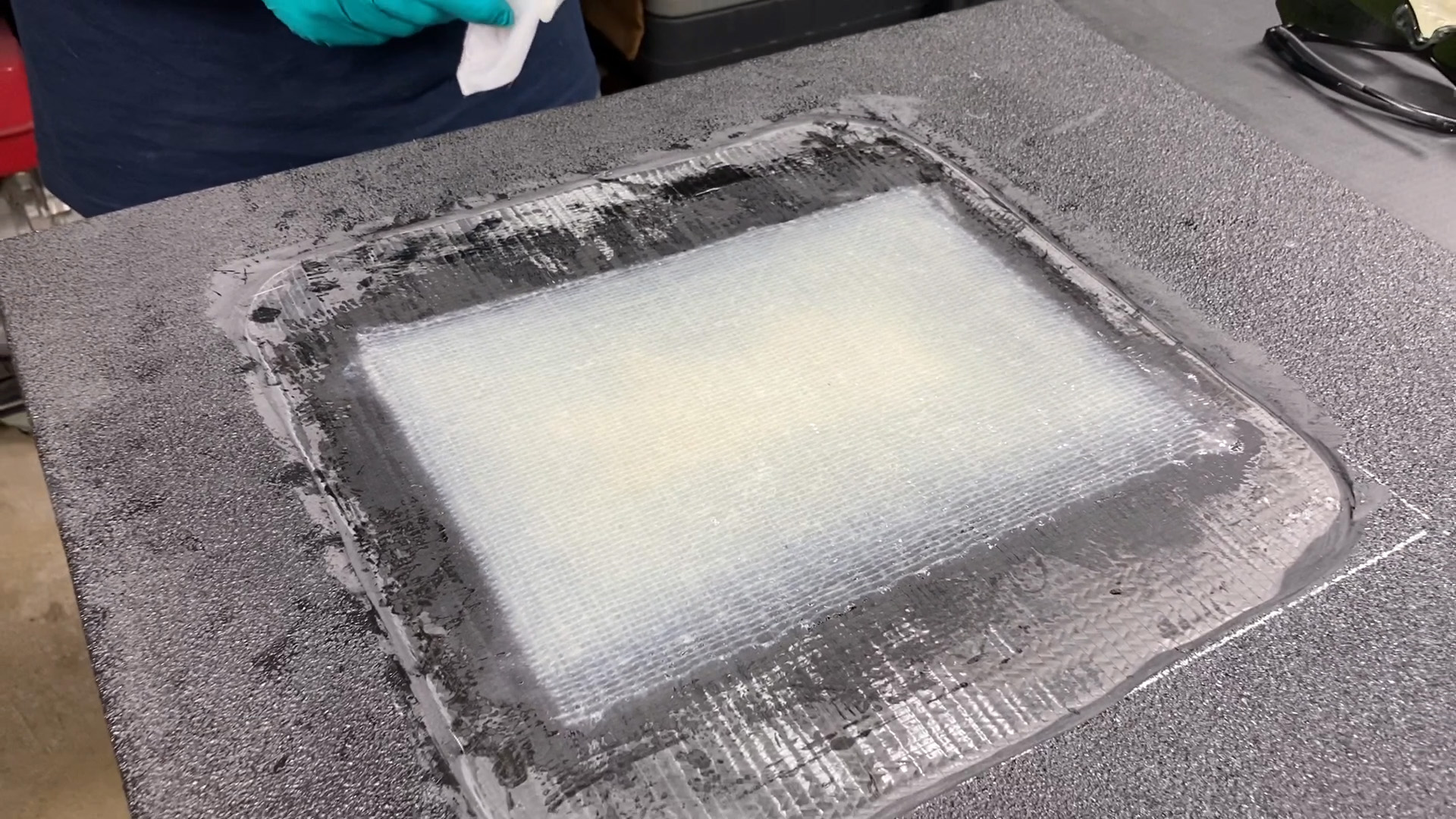
Étape 6. Réparation de patch préimprégné en fibre de verre/ester vinylique durcie aux UV.
Précédent Suivant« Nous avons ensuite effectué des tests pour évaluer la liaison adhésive du patch et sa capacité à restaurer la capacité de charge de la structure », explique Bergen. « Au cours de la phase 1, nous devions démontrer la facilité d'application et la capacité à restaurer au moins 75 % de résistance. Cela a été accompli sur les poutres en fibre de carbone/époxy et balsa de 4 x 48 pouces en flexion en quatre points après la réparation de dommages simulés. Le projet de la phase 2 utilisait des panneaux de 12 x 48 pouces et devait montrer une exigence de résistance supérieure à 90 % sous une charge de contrainte complexe. Nous avons satisfait à toutes ces exigences et avons ensuite filmé les méthodes de réparation sur le modèle AMCB pour fournir une référence visuelle sur la façon d'utiliser les techniques et l'équipement sur le terrain. »
Réussite des novices, futures applications
Un aspect clé du projet était de prouver qu'un novice pouvait facilement effectuer la réparation. Pour ce faire, Bergen a eu une idée :« J'avais promis une démonstration à nos deux points de contact techniques à l'Armée :le Dr Bernard Sia et Ashley Genna. Lors de l'examen final du projet de phase I, j'ai demandé à Ashley, qui n'avait aucune expérience de réparation préalable, d'effectuer la réparation. À l'aide des kits et du manuel que nous avons fournis, elle a appliqué le patch et terminé la réparation sans aucun problème. »
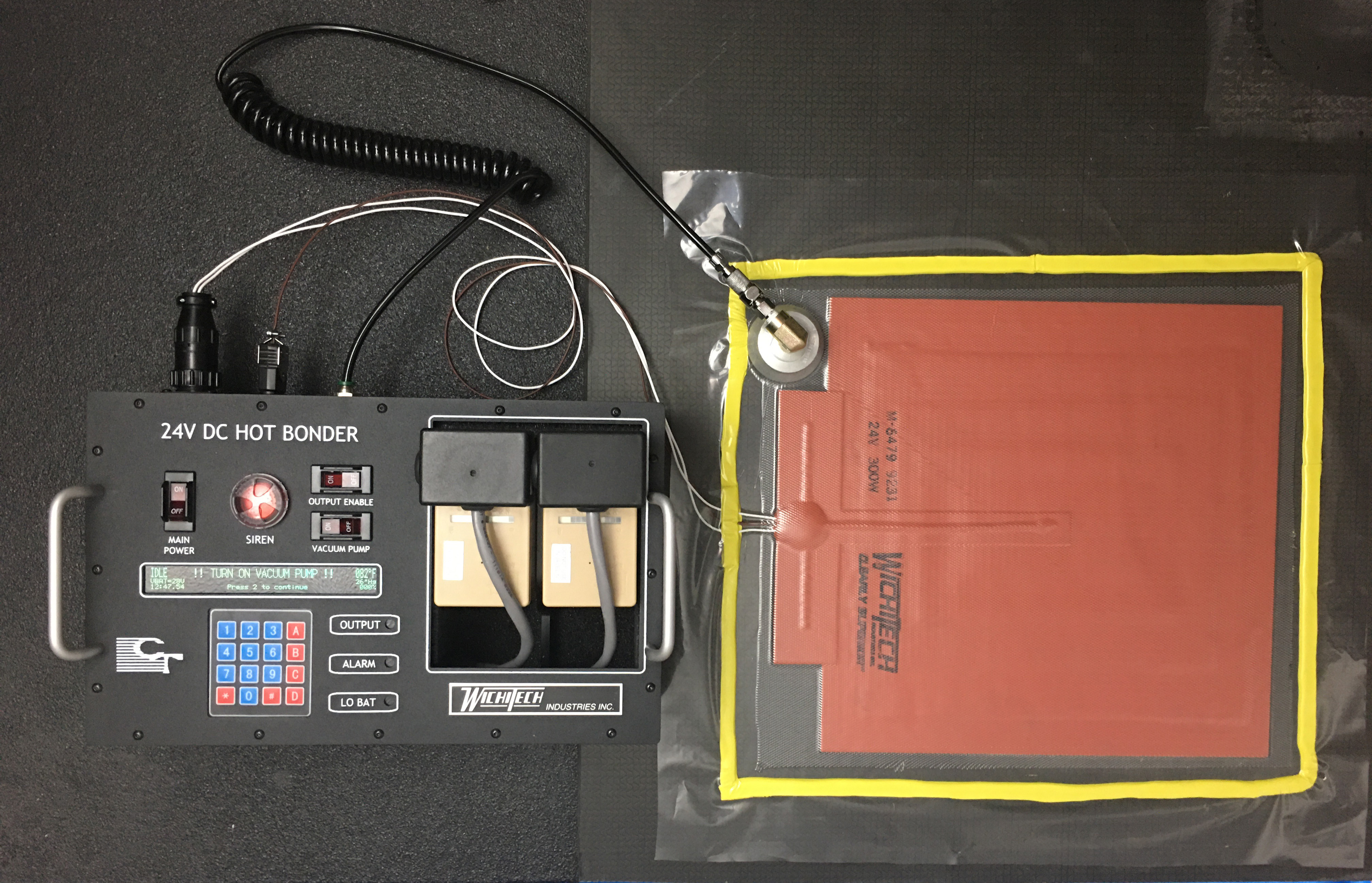
Un autre développement clé est le système de durcissement alimenté par batterie (Fig. 2). « Avec la réparation sur le terrain, vous n'avez que la puissance de la batterie », note Bergen. « Tous les équipements de traitement de notre kit de réparation développé sont sans fil. » Cela inclut le hot bonder alimenté par batterie que Custom Technologies a développé avec le fournisseur de hot bonder WichiTech Industries Inc. (Randallstown, Maryland, États-Unis). "Ce thermocolleur alimenté par batterie est préprogrammé pour terminer le durcissement, de sorte que le novice n'a pas besoin de programmer pour le cycle de durcissement", explique Crane. "Ils appuient simplement sur le bouton et cela complète la rampe et le trempage appropriés." Les batteries actuellement utilisées durent un an avant de devoir être rechargées.
Le projet de phase II étant maintenant terminé, Custom Technologies prépare une proposition d'amélioration de suivi et recueille des lettres d'intérêt et de soutien. « Notre objectif est de faire évoluer cette technologie jusqu'à TRL 8 et de la diffuser sur le terrain », déclare Bergen. « Nous voyons également un potentiel pour les applications non militaires. »
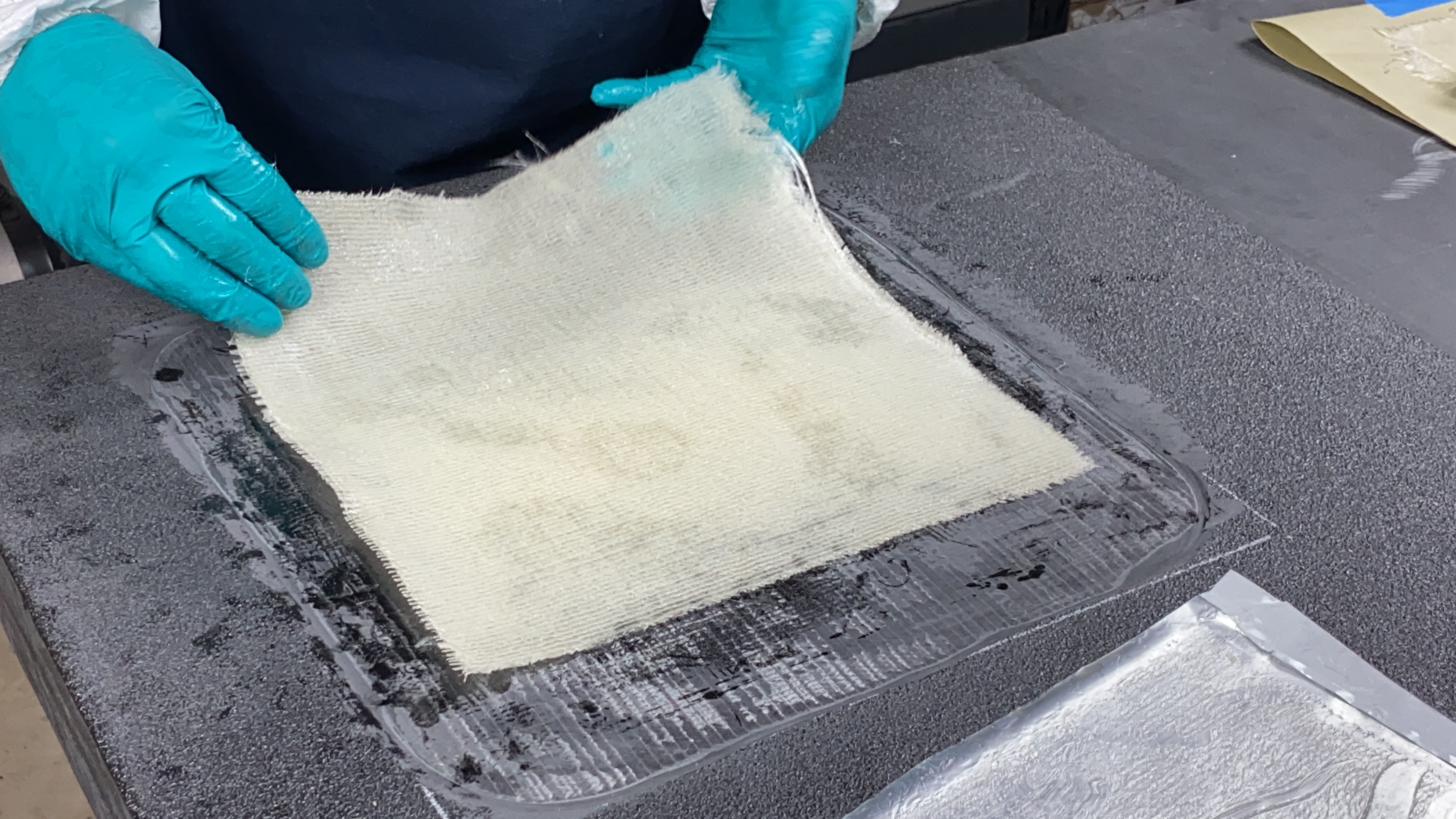
Résine
- 3 applications d'ingénierie des composites thermodurcissables les plus courantes
- Fabrication de composites :la fabrication de matériaux composites
- Les structures thermoplastiques sont au cœur de la présence d'Engel à China Composites Expo
- Développement de structures composites isogrilles utilisant une technologie de dépôt innovante
- La recherche AFRL fait progresser les composites CF/époxy imprimables en 3D
- Hexcel s'associe à Lavoisier Composites, Arkema
- AMRC et Prodrive s'associent pour faire progresser la fabrication de composants composites recyclables
- TenCate célèbre l'assemblage d'un consortium de composites thermoplastiques au Brésil
- Matériaux composites :où les trouver au NPE2018