Nouveau préimprégné pour moulage par compression en RAPM
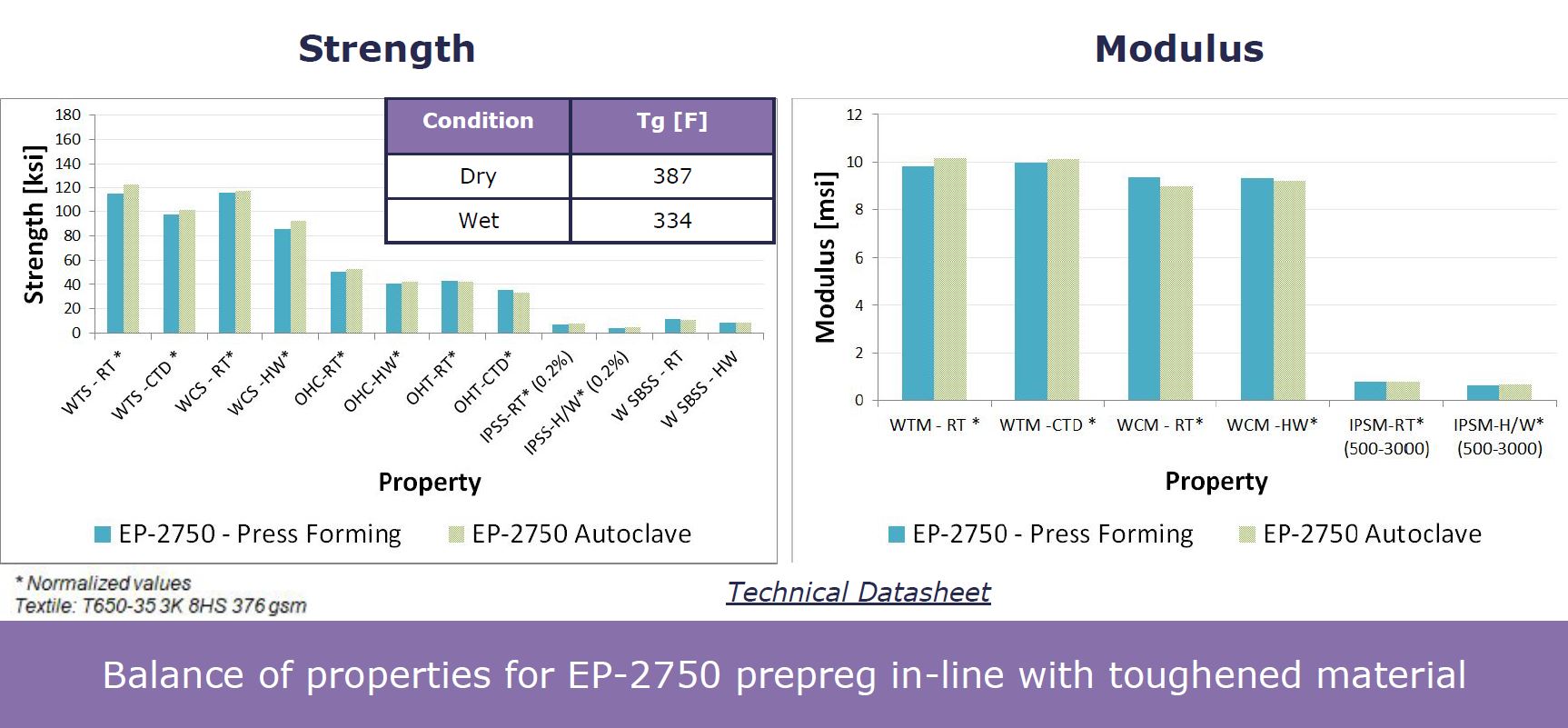
Le préimprégné en fibre de carbone/époxyde est le matériau de base pour les composites aérospatiaux depuis des décennies, car il offre des propriétés mécaniques élevées et une teneur précise en résine/fibre, ainsi qu'une facilité de manipulation pour le drapage et le durcissement en autoclave. Cependant, alors que les fabricants d'avions et de mobilité aérienne urbaine (UAM) explorent des taux de production plus élevés et des coûts inférieurs, le moulage par compression est attrayant, réduisant les temps de cycle et augmentant l'efficacité par rapport à l'autoclave. Dans sa forme la plus simple, le moulage par compression comprend le préchauffage du matériau de moulage, son placement dans une cavité d'outil ouverte et sa consolidation avec une pression hydraulique à température, pendant laquelle le matériau thermodurcissable liquide est converti en un solide. La pièce durcie est ensuite éjectée pour toutes les étapes de coupe et de finition requises.

La combinaison du moulage à la presse et du préimprégné offre non seulement un processus efficace et rapide avec les performances et la manipulation facile du préimprégné, mais évite également certaines des dynamiques de processus complexes de remplissage de renforts secs avec de la résine liquide lors de processus tels que l'infusion de résine et le moulage par transfert de résine (RTM). Pour les petites aérostructures en particulier, le moulage par presse préimprégné offre un potentiel de temps de cycle de <30 minutes tout en obtenant des pièces à géométrie complexe de haute qualité.
Solvay Composite Materials (Alpharetta, Géorgie, États-Unis) était un partenaire clé du programme RAPid high-Performance Manufacturing (RAPM) dirigé par The Boeing Co. (Chicago, Ill., États-Unis). RAPM est la partie « formage » du programme The Tailorable Feedstock and Forming (TFF) lancé par la Defense Advanced Research Projects Agency (DARPA, Arlington, Va., États-Unis) en 2015. Son objectif est de permettre des opérations rapides, à faible coût et agiles. fabrication de petites pièces composites de forme complexe et augmente la capacité des composites à concurrencer l'aluminium usiné dans les applications de défense.
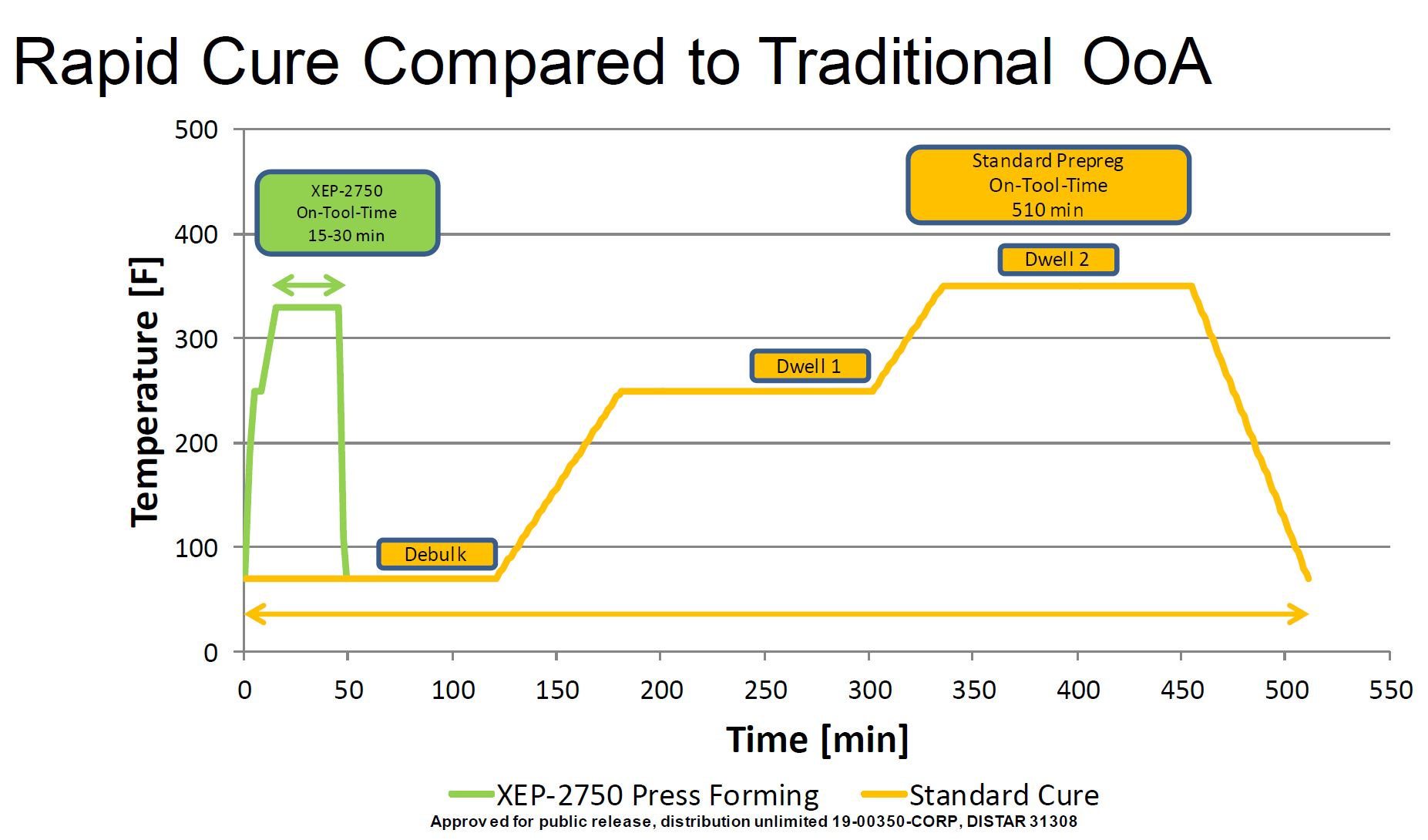
Fournisseur de longue date de Boeing pour les applications de défense, Solvay est également leader dans les solutions innovantes pour l'aérospatiale commerciale, telles que le préimprégné époxy hors autoclave (OOA) CYCOM 5320-1, ainsi que pour l'automobile, comme le temps takt de 1 minute, vinyle hybride SolvaLite 730 préimprégné.
RAPM était une opportunité parfaite pour Solvay de tester et d'affiner son système expérimental XEP-2750, maintenant commercialisé sous le nom de CYCOM EP2750, qui a été développé pour faire le pont entre la production de composites pour l'aérospatiale et l'automobile. Ce blog - une barre latérale en ligne de l'article de mai 2020 "Révolutionner le paradigme des coûts des composites, partie 2 :Formage" - passe en revue ce développement ainsi que les processus de moulage par compression utilisés et ce que CYCOM EP2750 offre aux fabricants de composites pour l'aérospatiale et l'automobile.
Les références de ce blog incluent :
- « Fabrication de composants de production aérospatiale par presse à ressorts » par Timothy J. Luchini
1
, Alejandro J. Rodriguez
2
, Scott A. Rogers
2
, Aurèle Bras
3
, Adam Whysall
3
, Richard Russell
3
, Scott Lucas
2
, Gail L. Hahn
1
. Actes de la conférence SAMPE. Charlotte, Caroline du Nord, du 20 au 23 mai 2019.
- « Défis des géométries de pièces structurelles aérospatiales pour le moulage par compression à haut débit » par Aurele Bras
1
, Alejandro J. Rodriguez
2
, Richard Russell
1
, Timothy J. Luchini
3
, Travis Adams
3
, Adam Whysall
1
, Scott A. Rogers
2
, Scott Lucas
2
, Gail L. Hahn
3
. Society for the Advancement of Material and Process Engineering – North America.Actes de la conférence SAMPE. Seattle, WA, du 4 au 7 mai 2020. Society for the Advancement of Material and Process Engineering – Amérique du Nord.
- « Moulage rapide à hautes performances du préimprégné structurel xEP-2750 pour le moulage par compression » par Timothy J. Luchini 1 , Alejandro J. Rodriguez 2 , Scott A. Rogers 2 , Aurèle Bras 2 , Adam Whysall 2 , Richard Russell 2 , Scott Lucas 2 , Gail L. Hahn 1 . SAMPE 2019.
1 The Boeing Company, Saint Louis, MO 63134, 2 Solvay Composite Materials, Anaheim, Californie, États-Unis et 3 Matériaux composites Solvay, Heanor, Royaume-Uni
- Webinaire CompositesWorld :"Processus automobiles pour la fabrication de composites aérospatiaux à haut débit" par Alejandro Rodriguez, Solvay Composite Materials, Anaheim, Californie, États-Unis
Objectifs matériels et processus
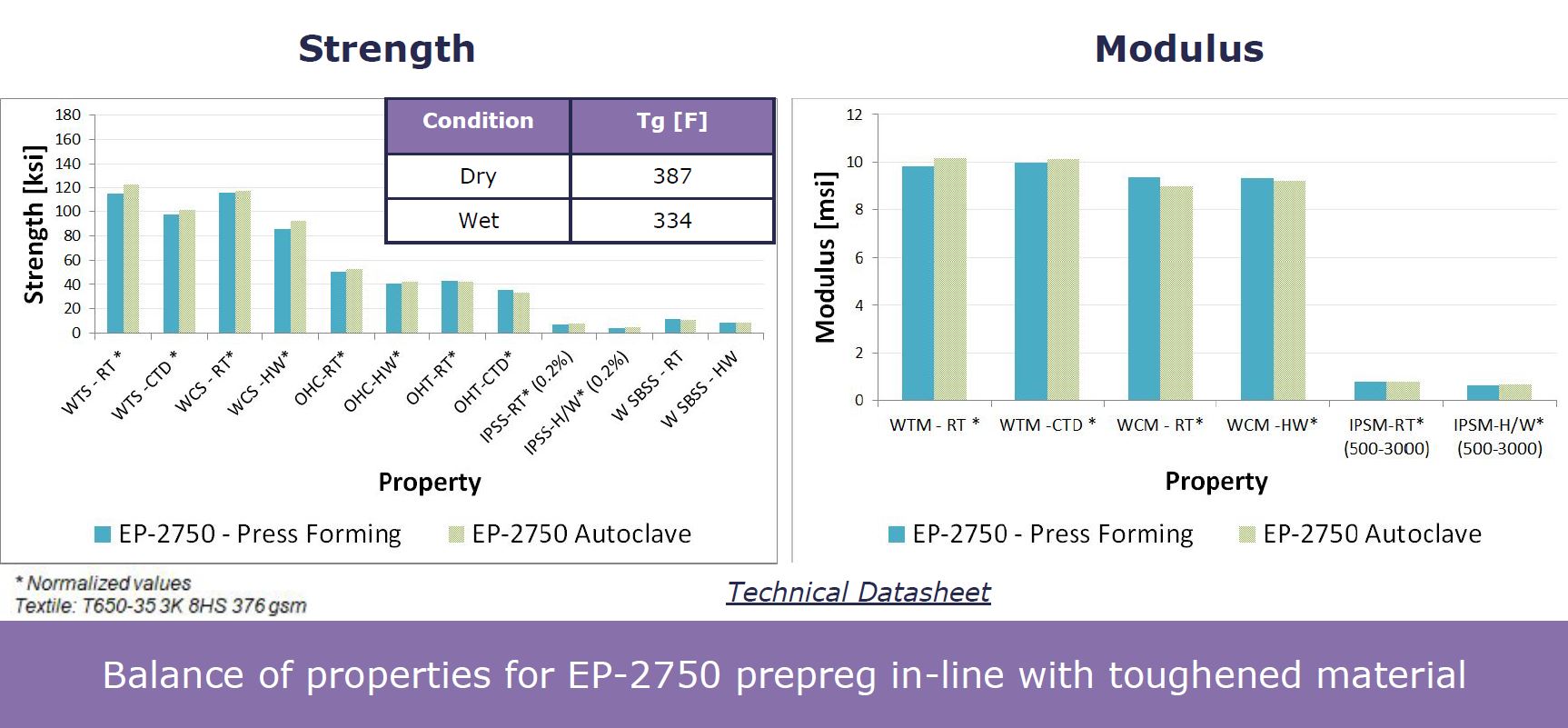
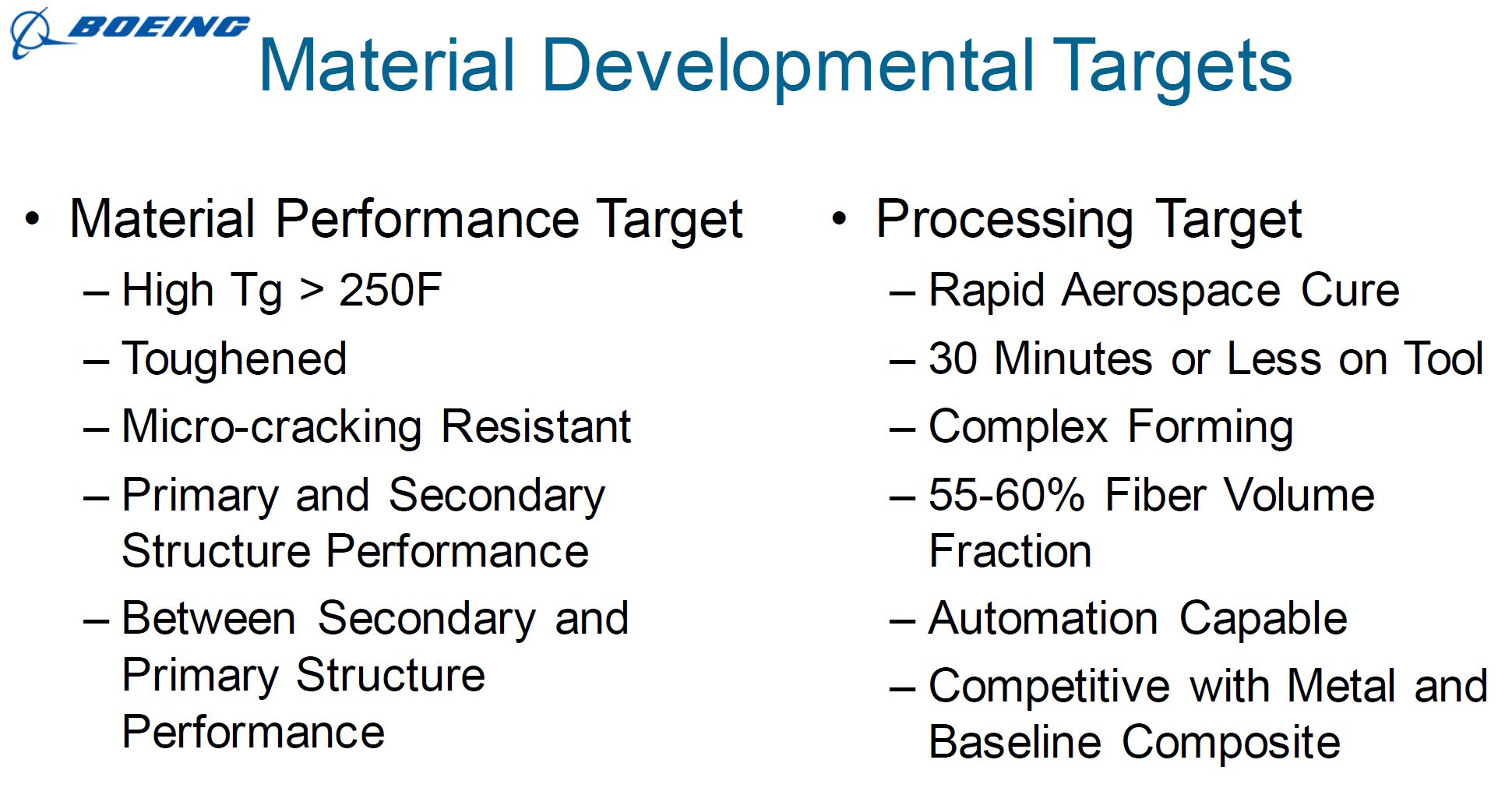
CYCOM EP2750 a été développé pour atteindre les objectifs de performance fixés par Boeing pour un époxyde durci pour l'aérospatiale, présentant un équilibre de température de transition vitreuse (Tg) jusqu'à 350 °F, de bonnes propriétés d'entaille - par exemple, compression à trou ouvert (OHC) et tension à trou ouvert (OHT) — et la résistance aux solvants. Cette nouvelle classe de préimprégnés est applicable aux aérostructures primaires et secondaires et est compatible avec de multiples renforts (par exemple, carbone et fibre de verre).
CYCOM EP2750 a également été développé avec la possibilité d'augmenter la production à l'aide d'une manipulation automatisée et d'un moulage par compression. Cela comprend un temps de durcissement sur outil de 15 à 30 minutes à 330-370 °F, avec une post-polymérisation d'une heure à 350 °F. Ce temps de cycle de 30 minutes ou moins permet un volume de production annuel de 10 000 pièces par outil.
Solvay a utilisé deux variantes de moulage par compression au cours du programme RAPM :le moulage à ressort et le formage à double diaphragme (DDF). Les deux utilisent le principe de tenir un flan plat et de le faire passer à travers une étape de préchauffage infrarouge (IR) avant de le transporter dans une cavité d'outil en métal assortie. La presse ferme ensuite le moule en acier selon un programme automatisé et applique une pression complète sur le préimprégné pendant le temps restant sur l'outil.
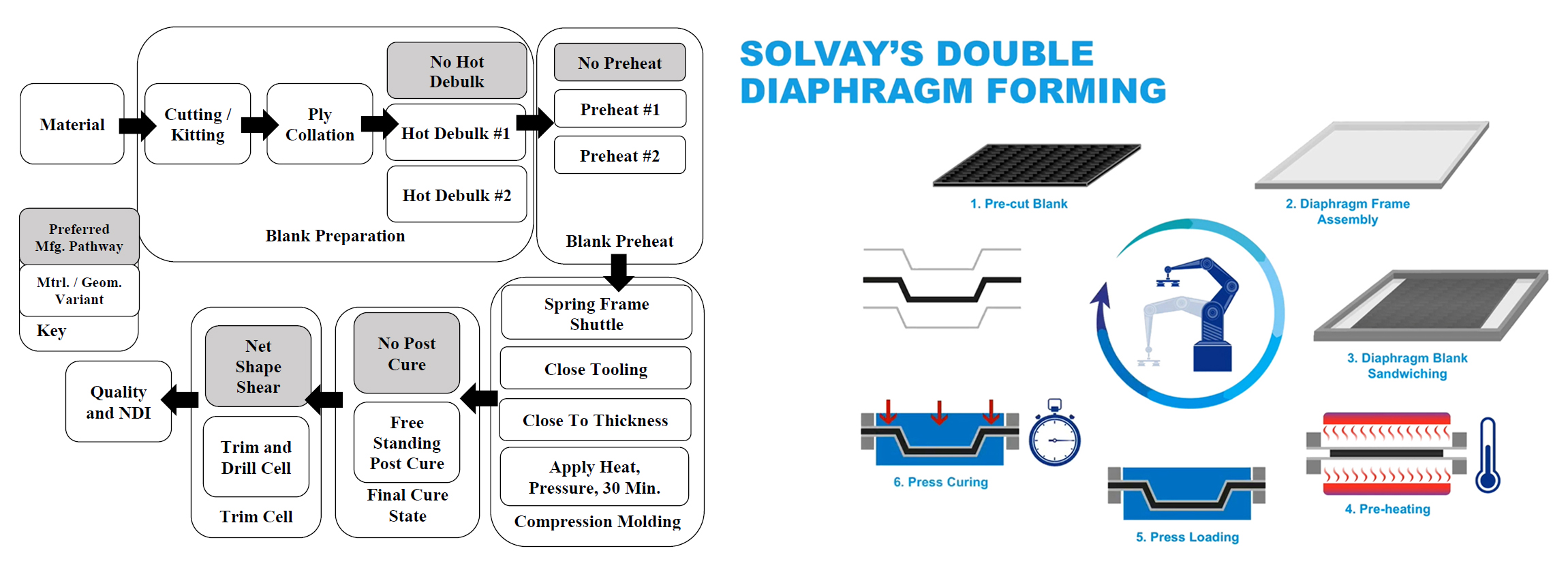
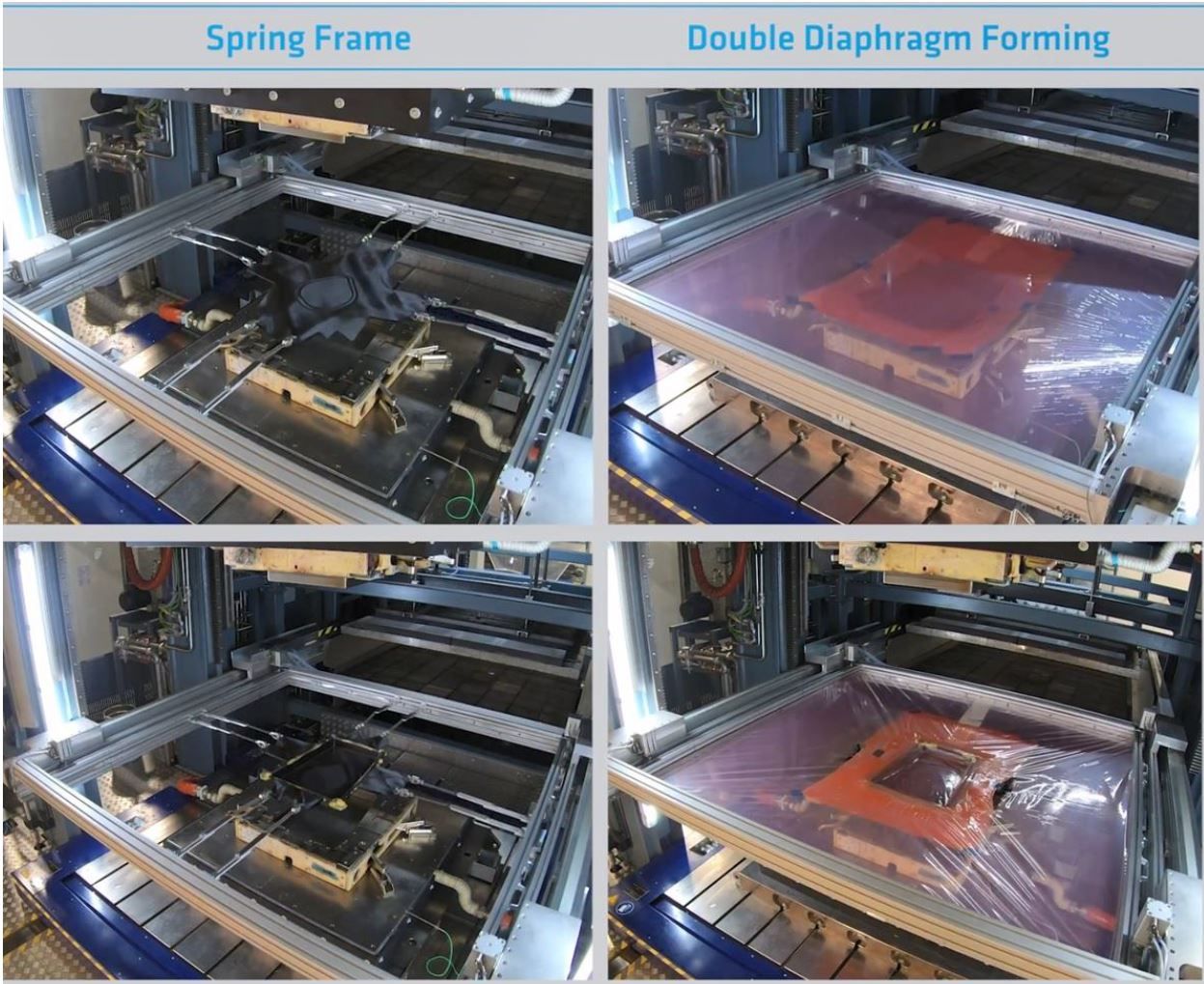
Le moulage à ressort et le DDF utilisent tous deux des outils métalliques assortis et offrent une approche d'entrée et de sortie à chaud, éliminant ainsi la chaleur et le refroidissement de l'outil, pour une production à cadence élevée. Les deux ont été utilisés pour mouler avec succès plusieurs types de pièces à géométrie complexe avec des rembourrages, des brides verticales et des variations d'épaisseur de 3,8 à 8,9 millimètres. Ces pièces ont été fabriquées au centre d'application de Solvay à Heanor, au Royaume-Uni. Bien qu'elles ne soient pas disponibles pendant le RAPM, Heanor dispose désormais d'une ligne de moulage par compression entièrement automatisée, du rouleau préimprégné à la pièce moulée, atteignant des temps de cycle de 15 à 60 minutes pour les pièces aérospatiales fabriquées avec EP2750 et takt temps de 3 minutes ou moins pour les petites et moyennes pièces utilisant des préimprégnés automobiles. Solvay voit de nombreux avantages dans le processus DDF, notamment :
- Suppression de l'étape de préformage – ébauche 2D à pièce 3D
- Aucun démoulage ni nettoyage requis
- Réduction des matériaux auxiliaires (par exemple, reniflard, purgeur, ensachage, ruban adhésif) par rapport à l'autoclave
- Amélioration du moulage de l'achat à la volée par rapport au moulage du cadre à ressort, car moins de matériau en excès est nécessaire pour fixer les pinces à ressort.
L'imprégnation complète ou partielle maintient la pression
Les caractéristiques de l'EP2750 qui facilitent le moulage par compression incluent sa faible adhérence pour une manipulation automatisée de la prise et de la place et sa nature entièrement imprégnée par rapport au CYCOM 5320-1, qui est partiellement imprégné pour faciliter la respiration des bords, nécessaire pour les stratifiés sans vide utilisant le traitement OOA. Le moulage par compression, cependant, exploite un écoulement de résine forcé très rapide en raison des pressions plus élevées appliquées - par exemple, jusqu'à 350 psi (maximum typique pour EP2750) par rapport à 35 psi courant dans le traitement en autoclave et 14,7 psi dans le traitement OOA sous vide uniquement.
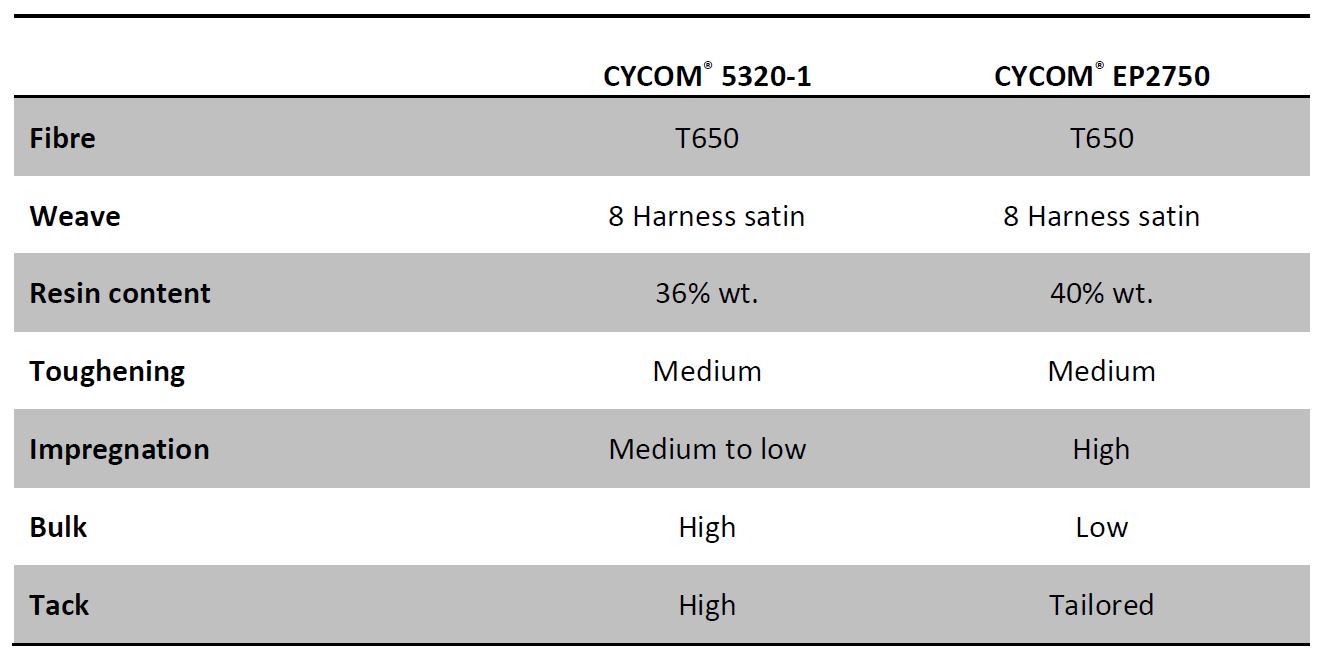
Le fait d'avoir un préimprégné plus complètement imprégné, même si la teneur en résine n'est que légèrement supérieure — 40 % dans le CYCOM EP2750 contre 36 % dans le CYCOM 5320-1 — maintient la pression hydrostatique pendant le compactage et le durcissement dans la cavité de l'outil en métal correspondant, ce qui réduit le risque de zones sèches, épaisseurs de pièces durcies (CPT) irrégulières, plis et autres défauts tout en garantissant une bonne qualité de surface.
Notamment, Solvay a développé un film transformateur breveté pour augmenter la pression hydrostatique lors de l'utilisation du préimprégné CYCOM 5320-1 à faible teneur en résine. Appliqué à la superposition de pièces avant le moulage par compression, le Transformer Film augmente la teneur en résine et a aidé à amener le CPT aux exigences des essais de moulage de pièces RAPM.
Essais de moulage de pièces RAPM
Comme expliqué dans l'article de fond de CW de mai 2020, CYCOM EP2750 était l'un des principaux matériaux testés dans la piste préimprégnée thermodurcissable de RAPM. Pièces Pathfinder testées dans la phase initiale de fabrication et de développement incluses
Panneaux d'accès perlés TS-RAPM-001 et -009, nervure TS-RAPM-002 et profilé en C incurvé TS-RAPM-003. Les pièces ont été conçues chez Boeing (plusieurs sites dans le monde), l'outillage a été fabriqué chez C-Con GmbH (Munich, Allemagne), les pièces ont été fabriquées au Centre d'applications de Solvay à Heanor, Royaume-Uni et ont ensuite été testées chez Solvay Anaheim, Californie, États-Unis et Boeing St. Louis, Missouri, États-Unis
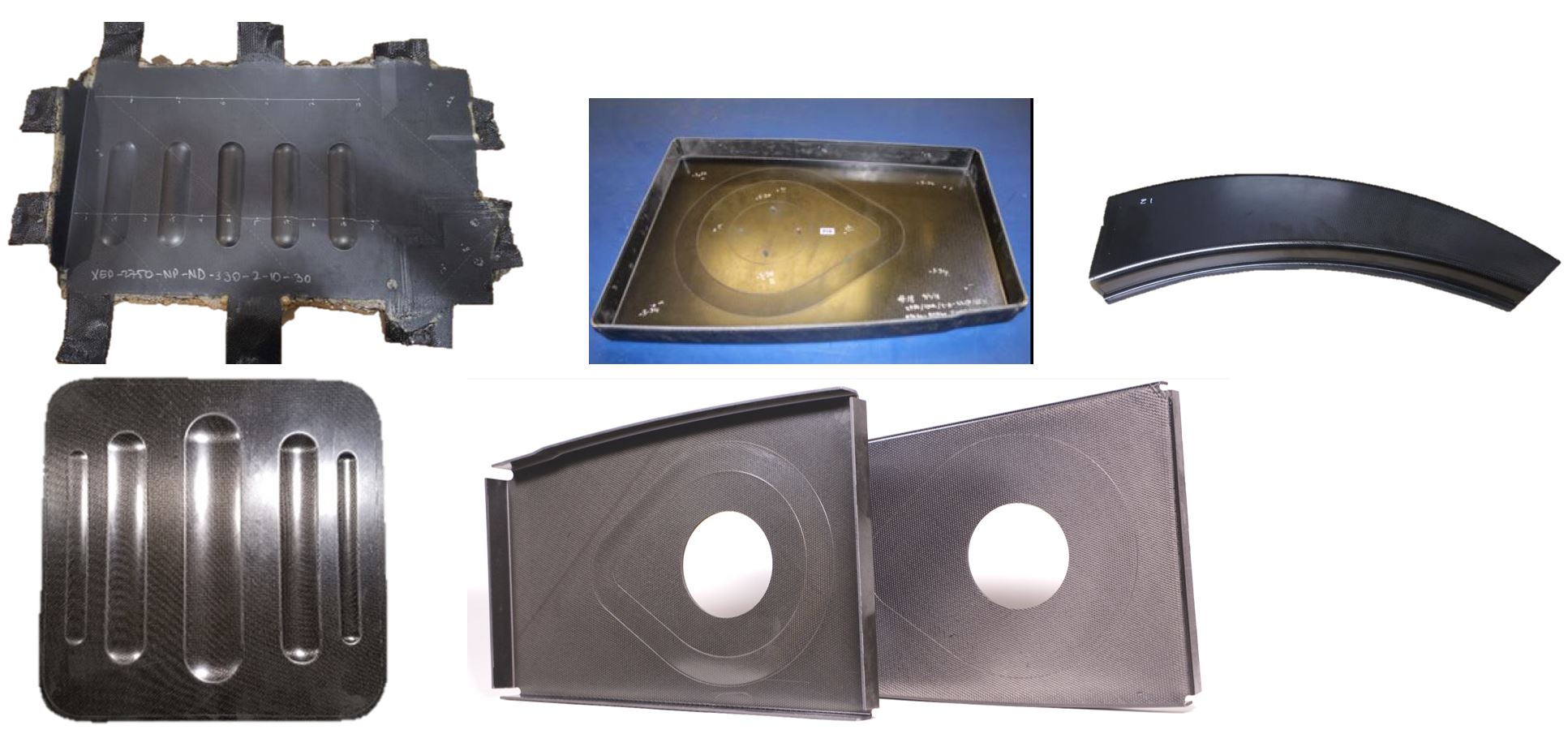
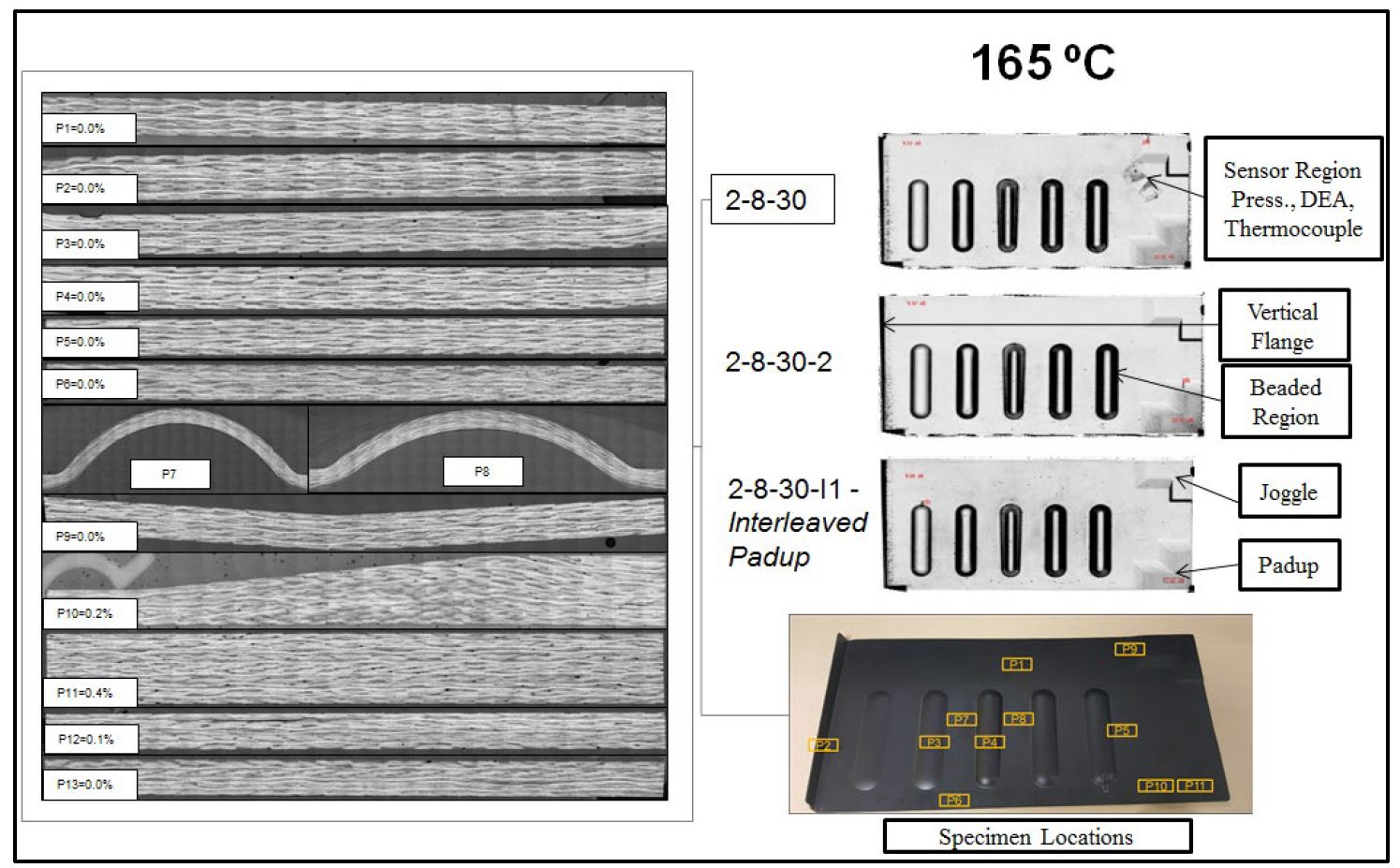

La qualité de la surface a été évaluée à l'aide d'une inspection non destructive (NDI) et des panneaux sélectionnés ont été coupés pour la porosité, le cisaillement court, la fraction volumique des fibres, la teneur en résine, le degré de durcissement et la température de transition vitreuse.
Des niveaux de porosité inférieurs à 0,5 % ont été facilement atteints, attribués aux pressions de consolidation élevées du moulage par compression. Bien que les paramètres du processus aient dû être optimisés pour chaque partie différente, une fois verrouillé, le processus s'est avéré être reproductible.
Panneau perlé TS-RAPM-009
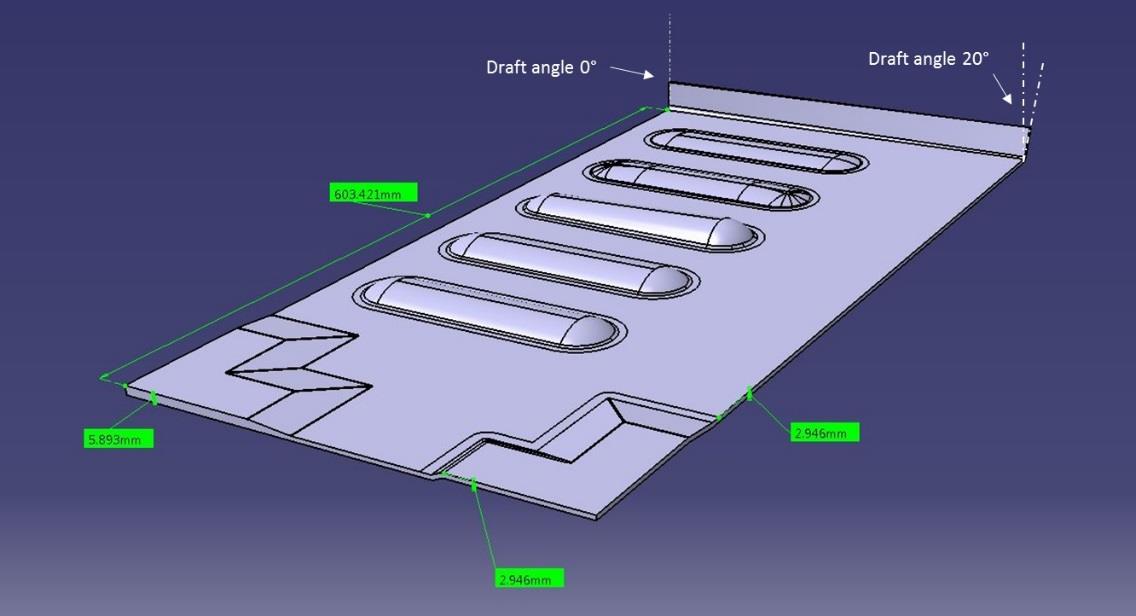
Cette partie plate de 600 millimètres de long comportait des billes parallèles de différentes géométries. L'épaisseur est passée de 3 à 6 millimètres dans un coin (pad-up) tandis que le coin opposé présentait un joggle d'épaisseur constante. Le bord opposé comprenait une aile verticale avec un angle de dépouille qui variait linéairement de 0° à 20°.
Dérapage des pad-ups
Les premiers essais ont été effectués avec des pads empilés sur la surface du drapage. Cependant, étant donné que les couches de remplissage étaient situées près du bord de la pièce, il était possible qu'elles soient expulsées de la pièce, entraînant une zone de basse pression pendant le durcissement et la porosité. La solution consistait à intercaler les plis de rembourrage à l'intérieur de la pile de stratifiés. Le risque de glissement et de porosité n'a pas été observé dans les parties ultérieures où les rembourrages étaient situés loin des bords et efficacement verrouillés par le matériau environnant.
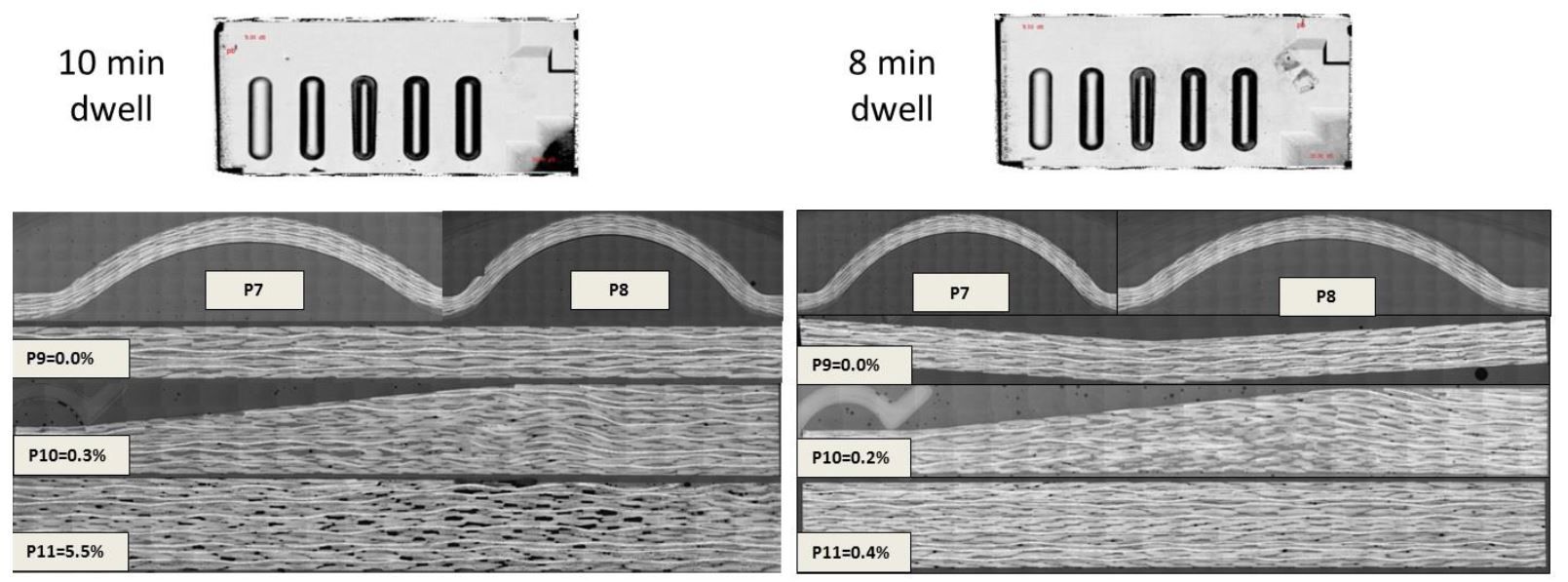
Porosité avec temps de séjour
Une porosité accrue a également été observée si le temps de séjour était trop long. Les panneaux perlés fabriqués avec un séjour de 8 minutes avaient une teneur en vides inférieure à ceux fabriqués avec un séjour de 10 minutes. Cela était particulièrement vrai dans la zone de remplissage, où la teneur en vides était de 5,5 % pour la temporisation de 10 minutes et de 0,4 % pour la temporisation de 8 minutes. La temporisation plus courte maintient un flux de résine élevé, mouillant efficacement les fibres et maintenant la pression dans la cavité de l'outil pendant le durcissement.
La temporisation plus longue a permis au débit de résine et à la pression de diminuer, en particulier dans la zone de remplissage, en raison de sa proximité avec le bord de la cavité de l'outil, qui n'avait pas de bord de cisaillement ou de réduction de section. Ainsi, la pression dans la cavité de l'outil a diminué au bord de la pièce, en particulier dans les régions plus épaisses où la section transversale était plus grande. L'absence de pression ici exacerbe également le risque de glissement des nappes de rembourrage. « Lors de la conception de l'outillage, une réduction de la section autour de la cavité de l'outil aidera à créer et à maintenir la pression, en particulier pour les pièces d'épaisseurs variables », explique Gail Hahn, chercheuse chez Boeing et chercheuse principale du projet RAPM. « Vous devez présenter une forme de pincement ou d'étanchéité afin d'encourager un état de pression hydrostatique dans la cavité. »
Côte TS-RAPM-002
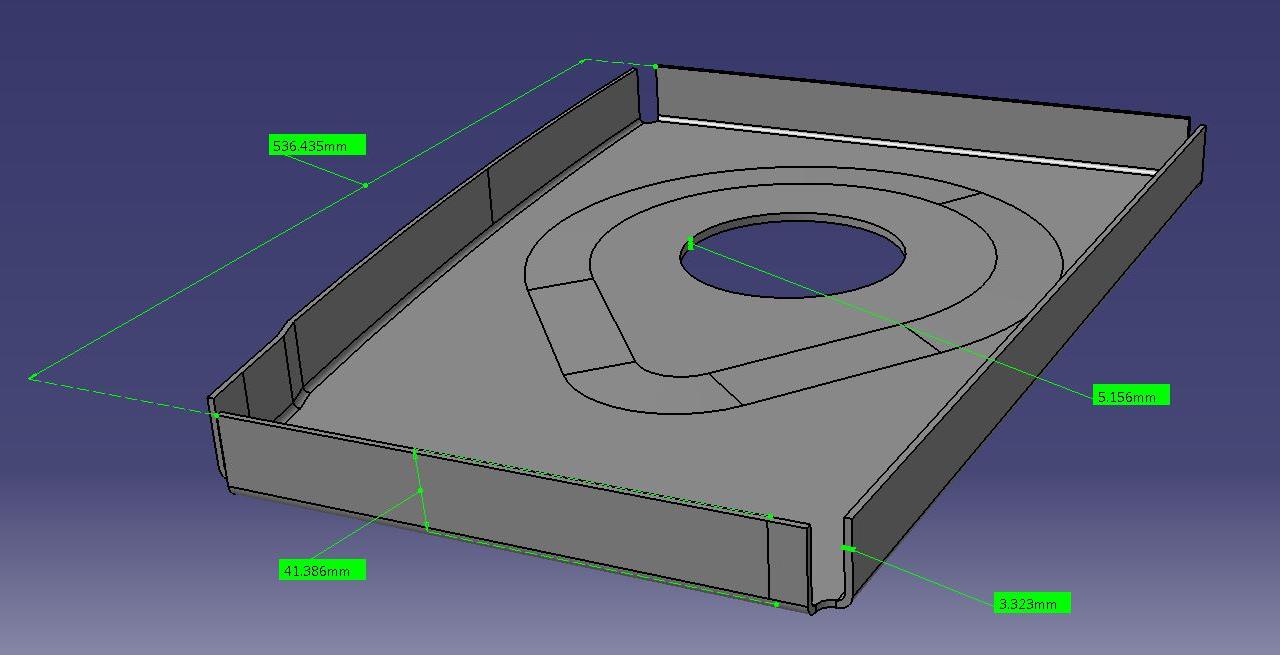
Une fois les paramètres de traitement établis pour les panneaux perlés TS-RAPM-009, le processus a été répété pour la nervure TS-RAPM-002, qui mesurait 540 millimètres sur son bord le plus long. La nervure a accumulé une épaisseur au centre de 3,3 à 5,2 millimètres et la profondeur de l'étirage était de 42 millimètres sur la partie finale coupée. Les quatre bords comportaient des rebords verticaux. Notez qu'un angle de compensation de ressort a été déterminé lors des essais de panneaux de bourrelet et a ensuite été appliqué à la géométrie de l'outil de la nervure. Les essais de panneaux perlés ont également conduit à une capacité de tension plus élevée et à une modularité de l'emplacement du ressort sur le cadre à ressort.
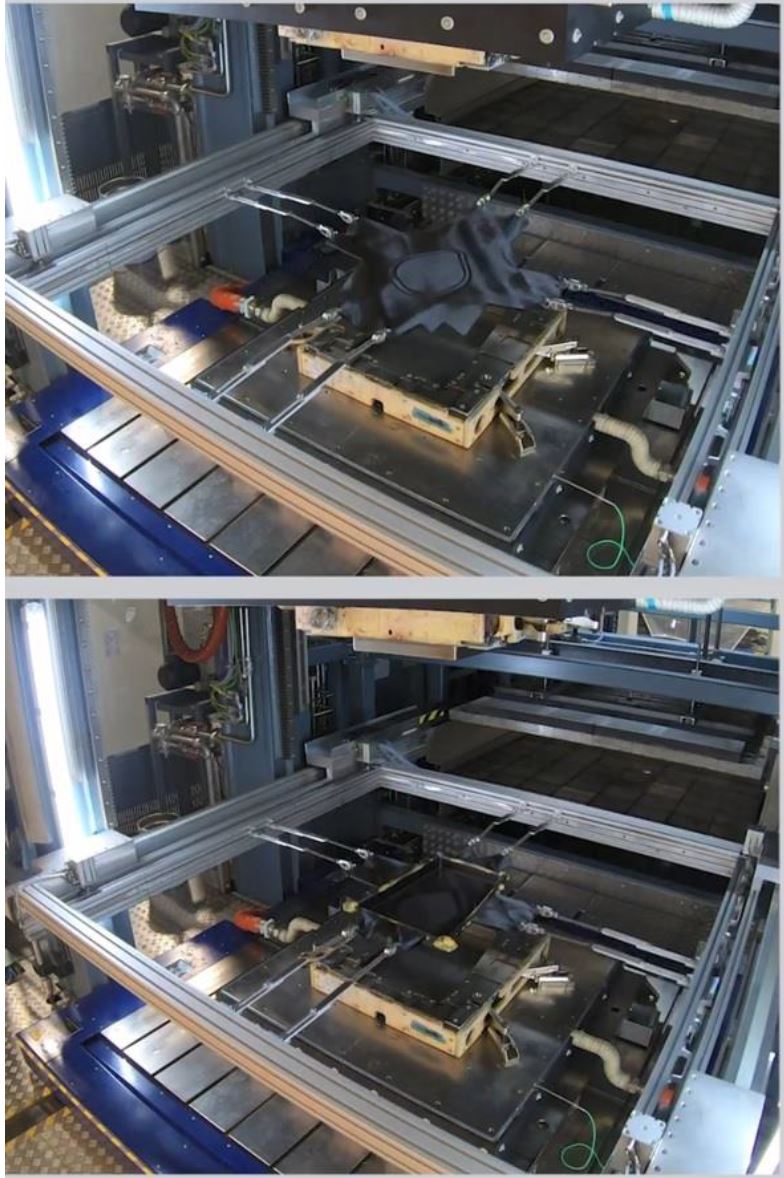
Excès de matériel pour les pinces
Les nervures ont été fabriquées à l'aide de moulures à ressort et de DDF. En raison de l'emboutissage profond de la nervure, un excès de matériau était nécessaire pour fixer les pinces à ressort, mais cela pouvait être réduit lors de l'utilisation du DDF. Un autre problème était que la conception de l'outil limitait l'espace pour les pinces à ressort à proximité immédiate de la cavité de l'outil.
Variations du CPT
L'épaisseur de pli durci (CPT) était plus élevée sur les parties plates de la nervure que sur ses bords verticaux. Il a été estimé que la géométrie de la pièce maintenait la résine dans la zone plate centrale, notant que les brides verticales agissaient comme un joint en résine. Cela a aidé au compactage et à la finition des pièces dans la zone plate centrale. Cependant, les brides verticales ont souffert d'un fort cisaillement lors de la fermeture de l'outil, ce qui a provoqué une rugosité de surface mais pas de porosité (voir les données de porosité ci-dessous). CYCOM EP2750, un matériau moins volumineux, a contribué à atténuer cet effet - sa plus faible épaisseur a diminué le cisaillement.
Variations de l'épaisseur de la bande avec la teneur en résine préimprégnée
Les études de qualité ont montré des côtes reproductibles avec une porosité <0,1 % et un plissement/ondulation minimal des fibres. Cependant, alors qu'il était supposé que la variation de l'épaisseur de la pièce serait minimisée avec un traitement de moule adapté, l'examen des paramètres de traitement du matériau et de la pièce finie CPT a montré que si l'espace d'outillage dans les ailes verticales de la nervure était fixe et cohérent, l'épaisseur de l'âme pouvait varier en fonction de la teneur en résine préimprégnée (moins de +/- 2 %) et du processus - CPT pourrait varier entre les semelles et l'âme, car la résine pouvait migrer à l'intérieur de la cavité.
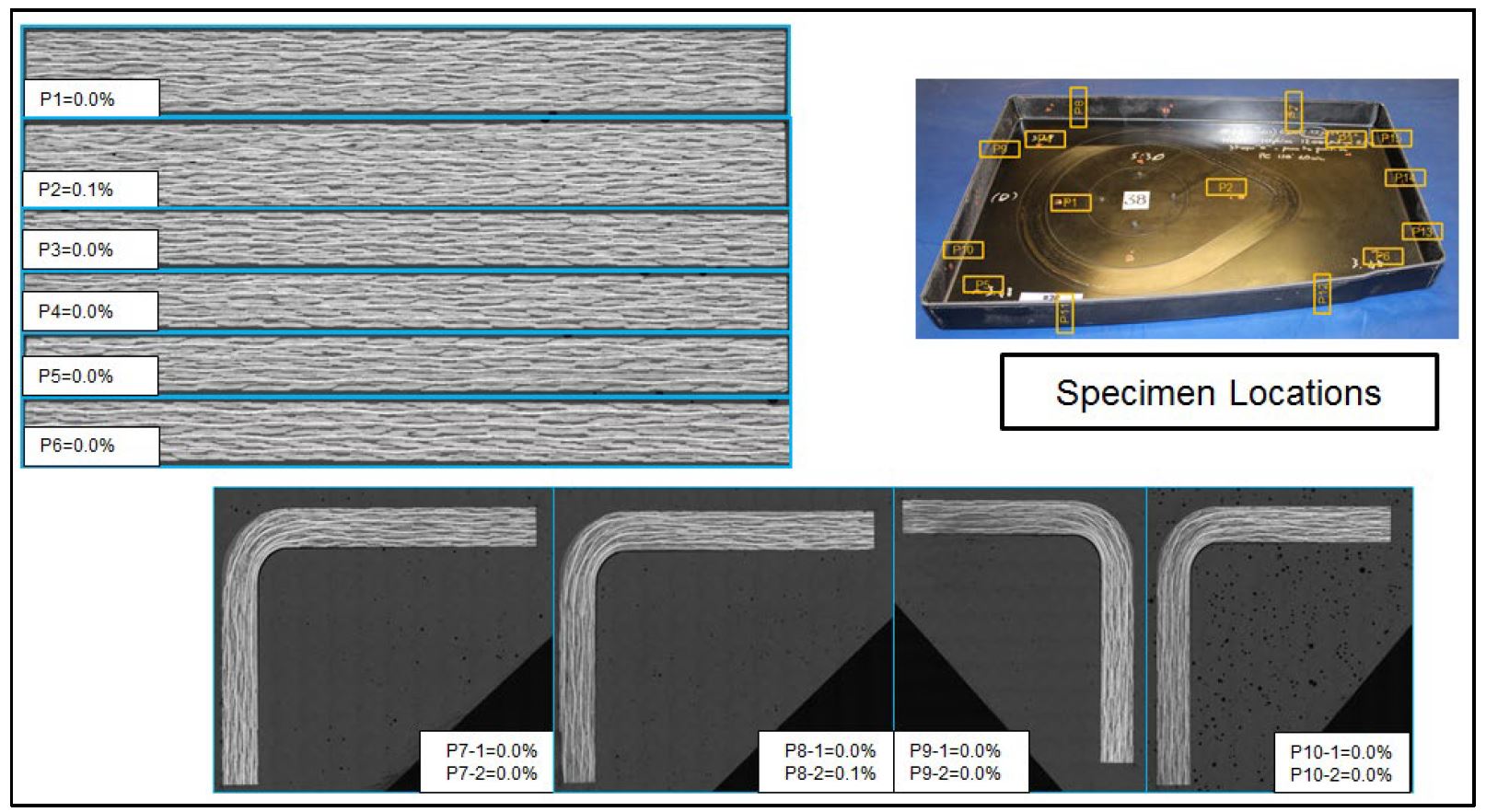
TS-RAPM-003 canal C incurvé
Cette pièce mesurait 640 millimètres de long avec une section en U de 40 millimètres de profondeur sur la pièce finale taillée. Le rayon intérieur de la section était plus grand que le rayon extérieur, et l'épaisseur est passée de 6,6 millimètres dans la section étroite à 8,8 millimètres à l'extrémité large. En raison de son épaisseur, la partie du canal C était sensiblement plus lourde que les parties précédentes discutées. Par conséquent, le cadre à ressorts nécessitait plus de points de fixation qu'avec les pièces précédentes.
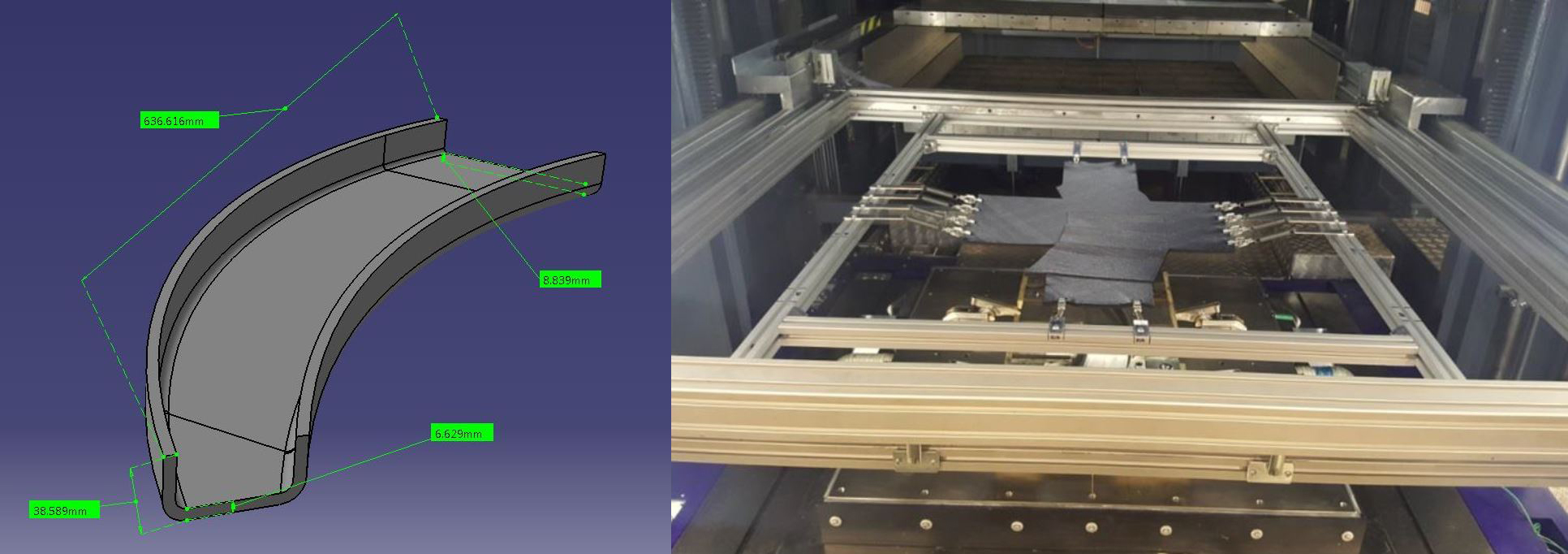
Double palier pour maintenir la pression dans les pièces épaisses
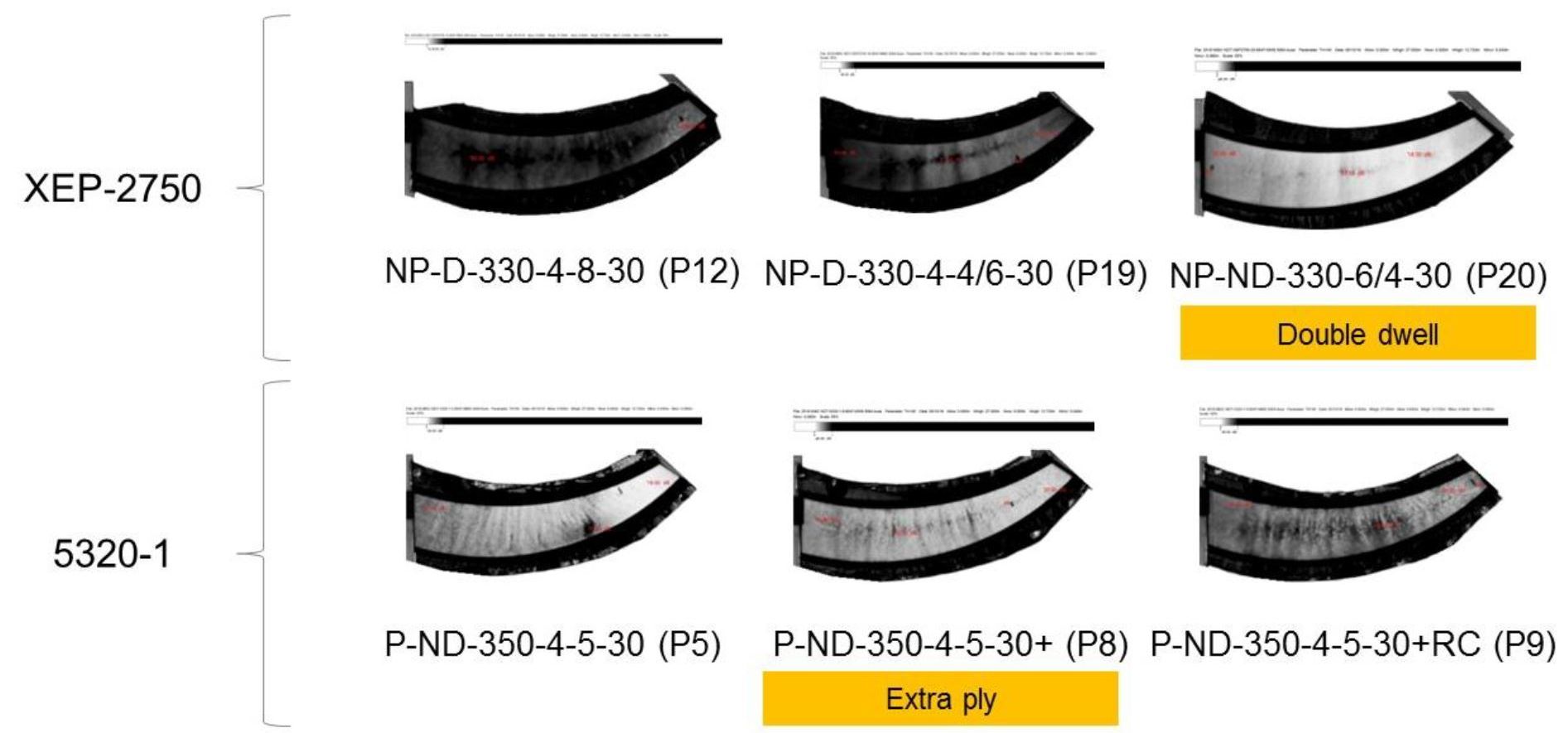
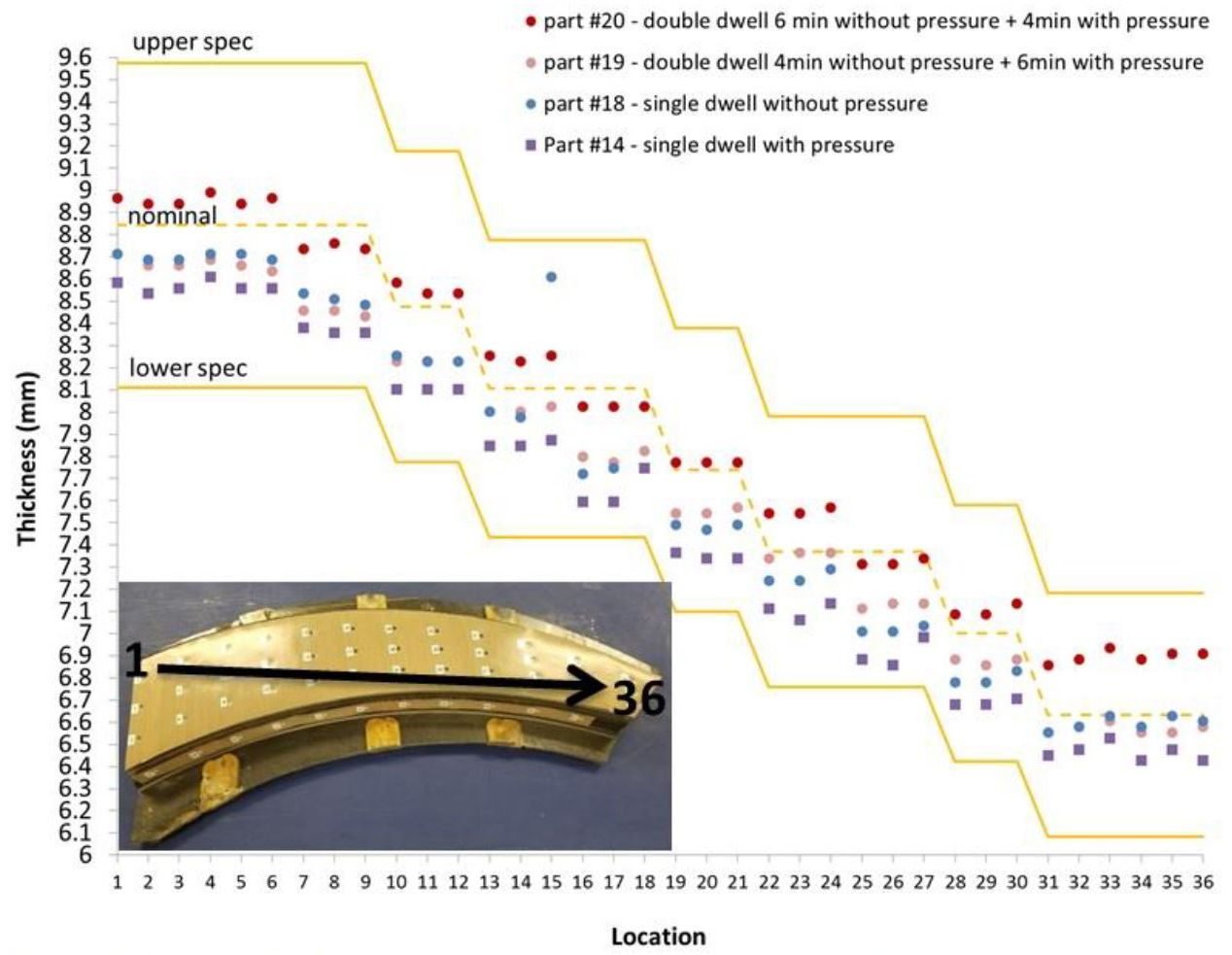
Les C-scans des pièces moulées mettent en évidence un pli se propageant du rayon intérieur au rayon extérieur pour les pièces utilisant des flans préconsolidés. L'échelle de gris indique que les rides sont également porteuses de porosité.
Ces rides et porosités ont été supprimées pour les pièces préimprégnées CYCOM EP2750 en utilisant un « double dwell » traiter. Cela consiste à appliquer une certaine pression pendant le séjour immédiatement après l'augmentation de la viscosité du matériau. « Cela a été déterminé à l'aide des données fournies par la presse et les outils lors du développement du processus », explique Hahn. « Fondamentalement, il y a deux étapes d'augmentation progressive de la pression avant l'application complète de la pression. En conséquence, le profil pression/temps a une forme similaire au profil de viscosité de la résine. Un séjour initial à l'épaisseur apparente est utilisé pour augmenter la viscosité de la résine afin d'éviter un amincissement de la charge de matériau [ébauche ou préforme]. Si la charge est d'épaisseur importante, deux paliers sont utilisés pour éviter la perte de pression due au retrait de la résine. Le premier palier est à un écart de X, et le second à un écart de Y, avec Y
La figure 18 ci-dessus montre l'effet du double séjour sur l'épaisseur de la pièce du canal C. L'adaptation de la pression à la viscosité de la résine a permis de retenir davantage de résine dans la pièce, ce qui a mouillé les fibres pour une faible porosité et une épaisseur de construction pour atteindre la distorsion nominale requise tout en maintenant une faible distorsion des fibres. Cependant, l'équipe RAPM a souligné que ce processus de double séjour n'est favorisé que pour les pièces plus épaisses, notant qu'il peut induire des irrégularités CPT dans des pièces d'épaisseurs variables.
Les essais de pièces RAPM discutés ici ont apporté des connaissances sur la fabrication à haute cadence de pièces structurelles aérospatiales à l'aide du moulage par compression préimprégné. Les leçons apprises incluent :
RAPM a montré que le moulage par compression préimprégné peut produire des structures de haute qualité de qualité aérospatiale tout en réduisant le temps de cycle et la main-d'œuvre. Cela permet aux composites de mieux rivaliser dans les études commerciales pour les applications aérospatiales tout en offrant des économies de poids et des performances de composants accrues (par exemple, résistance à la corrosion, à la fissuration et à la fatigue, etc.).
Solvay et Boeing ont travaillé ensemble pour affiner le nouveau système de préimprégné EP2750, démontrant des temps de cycle jusqu'à 20 minutes, grâce à une combinaison de chimie des matériaux, de connaissances en matière de préimprégné et de processus et d'automatisation.
En plus des parties de développement de fabrication décrites ci-dessus, RAPM a également produit plusieurs parties de défi et de transition, destinées à défier développements initiaux et transition candidats ayant le potentiel de gagner contre l'aluminium usiné dans les applications de défense. Ceux-ci incluent :
Les résultats et les enseignements tirés de ces essais de pièces et d'autres études de caractéristiques de fabrication RAPM seront publiés en 2020/2021.
Solvay a également illustré les performances de l'EP2750 dans les pièces automobiles, telles qu'un montant B de 36 x 16 x 2 pouces avec une épaisseur de 0,0725 pouces, comprenant 5 plis de fibre de carbone Solvay THORNEL T650-35 module standard 3K dans un 376 Grammes/mètre carré tissu satiné à 8 harnais. Cette pièce a été réalisée chez Solvay Heanor, Royaume-Uni, à l'aide de DDF. Par rapport au préimprégné standard autoclavé, la combinaison de CYCOM EP2750 et DDF offre une réduction de 60 % du temps de cycle et de 85 % du temps takt (temps entre le démarrage d'une pièce et la pièce suivante sur une ligne de production, c'est-à-dire le temps d'impulsion de la ligne) .
Leçons apprises du RAPM et essais de pièces supplémentaires
Essais de pièces automobiles Solvay
Résine
- Moulage par compression vs moulage par injection :quelle est la différence ?
- Moulage par compression :comment ça marche
- Moulage par compression et moulage par fonte :avantages et inconvénients
- Agent de purge hautement efficace pour les polyoléfines de moulage par soufflage
- PEEK à haute viscosité pour le moulage par injection et l'extrusion
- Convoyeur personnalisé pour le moulage de préformes
- Troisième brevet délivré pour un préimprégné thermoplastique souple
- Préimprégné aérospatial Toray optimisé pour le moulage sous pression sous vide
- Les bandes continues, D-LFT se rencontrent dans un nouveau processus de moulage par compression