Composites 4.0 :transformation numérique, production adaptative, nouveaux paradigmes
Composites 4.0 est une petite galaxie dans l'univers de l'Industrie 4.0, qui est la transformation numérique dans la façon dont les biens et services sont conçus, produits, livrés, exploités, entretenus et mis hors service. Pour la fabrication de composites, l'objectif est d'utiliser l'automatisation, les capteurs et les données, les communications 5G, les logiciels et d'autres technologies numériques en constante évolution pour rendre les produits et les processus plus efficaces, intelligents et adaptatifs.
Les fabricants de composites procèdent à cette transformation numérique le long d'un spectre. Les premières étapes comprennent l'inspection en ligne et des processus optimisés qui réduisent les déchets et les coûts tout en augmentant la qualité et le rendement des pièces. Des solutions plus avancées fonctionnent vers une production intelligente et autonome qui n'est pas seulement agile, mais répond et même anticipe l'évolution des marchés et des demandes des clients.
« Composites 4.0 n'est pas une fin, mais un outil », explique le Dr Michael Emonts, directeur général du AZL Aachen Center for Integrative Lightweight Production à l'Université RWTH Aachen (Aix-la-Chapelle, Allemagne), dont le projet iComposite 4.0 a démontré une chaîne de processus adaptative avec potentiel de réduction du coût d'un bac de plancher automobile de 50 à 64 %.
"Il y a une différence entre simplement rendre les choses numériques et la transformation numérique qui change réellement les processus derrière votre entreprise et ouvre de nouvelles opportunités et modèles commerciaux", affirme Christian Koppenberg, directeur général du producteur de pièces composites Dynexa (Laudenbach, Allemagne).
« Composites 4.0 n'utilise pas seulement des robots », affirme le Dr Michael Kupke, directeur du Centre de technologie de production légère du Centre aérospatial allemand (DLR) (ZLP, Augsbourg), qui a développé une cellule de travail équipée d'une intelligence artificielle [IA]. où les robots collaboratifs peuvent passer de la production de cloisons de pression arrière composites à des panneaux de fuselage sans reprogrammation ni recyclage. « C'est la technologie qui garantit que vous n'avez pas à enseigner aux robots, car il n'y a aucune analyse de rentabilisation pour cela. Composites 4.0, c'est bien plus qu'augmenter l'efficacité et réduire les coûts. C'est un changement dans la façon dont les entreprises envisagent et abordent la production qui déterminera quelles entreprises survivront et lesquelles ne survivront pas.
Préformage adaptatif, RTM
« L'idée du projet iComposite 4.0 était de créer des préformes à partir de mèches et de câbles rentables en combinant de la fibre de verre longue et sèche (25-30 millimètres) pulvérisée puis renforcée avec une grille de fibres de carbone unidirectionnelles (UD) via un placement automatisé des fibres (AFP) », explique Emonts. « Le démonstrateur choisi, un plancher arrière sous le véhicule, était auparavant fabriqué avec des textiles plus coûteux qui produisaient également plus de 60 % de déchets. »
La transformation Composites 4.0 a nécessité l'intégration des processus de pulvérisation de fibres, de dépôt de fibres et de moulage par transfert de résine (RTM) ultérieur afin qu'ils réagissent les uns aux autres et s'adaptent en fonction de la qualité de la pièce mesurée entre les étapes (Fig. 1). « Nous avons utilisé un système de vision industrielle d'Apodius GmbH [Aix-la-Chapelle, Allemagne] avec un capteur laser optique et un module de caméra pour caractériser la topologie de surface de la préforme pulvérisée », explique Emonts. « Apodius a adapté le logiciel pour analyser le pourcentage de fibres dans chaque direction. La gamme iComposite 4.0 a comparé cela à la conception numérique et a décidé si elle répondait aux exigences mécaniques. Si oui, il a appliqué la grille UD standard pour le renforcement. Si non, il a décidé où placer des couches de fibres UD supplémentaires. »
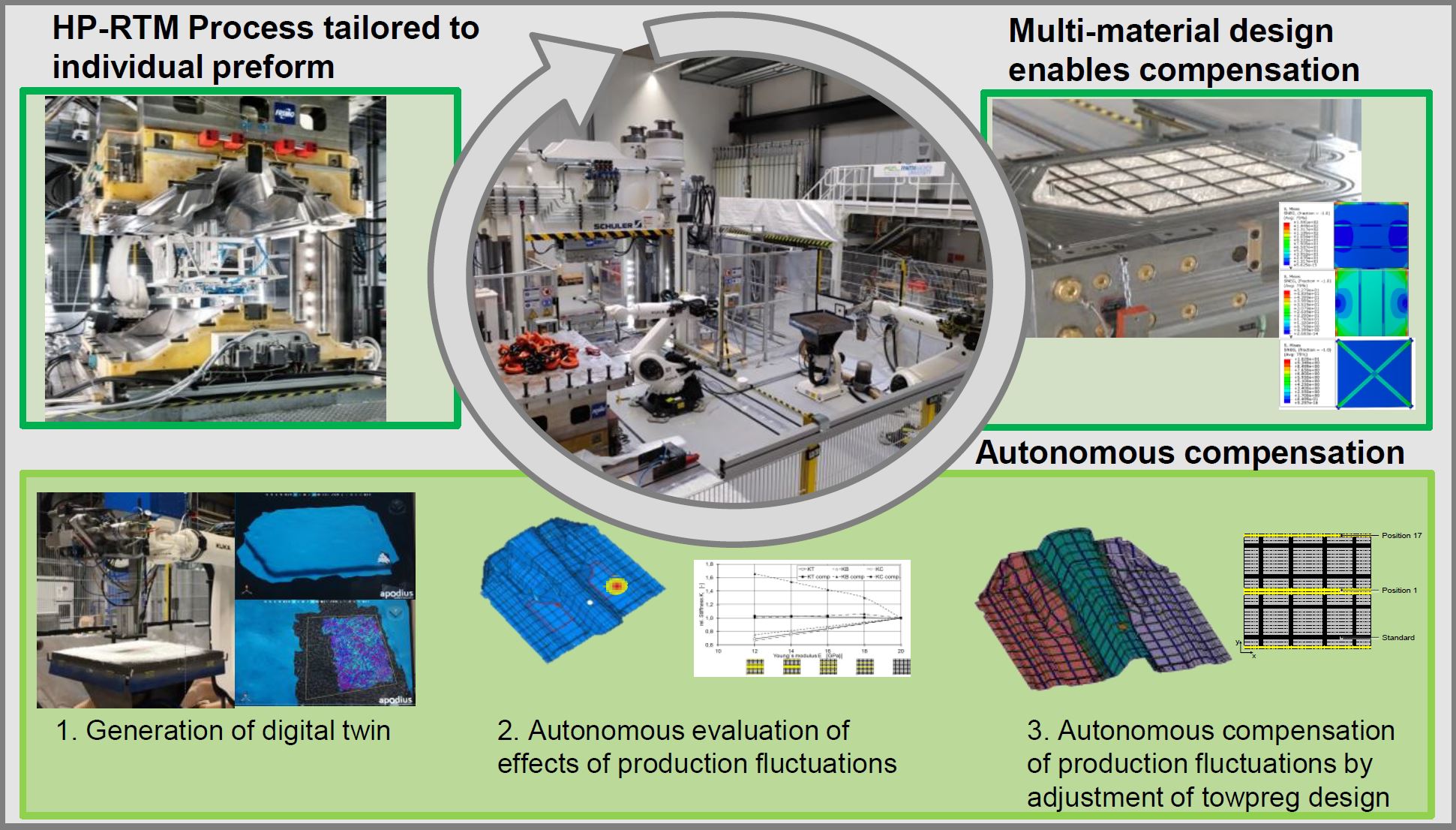
Cependant, ces couches UD supplémentaires peuvent entraîner un dépassement des tolérances de l'épaisseur et de la géométrie de la pièce. « Par conséquent, explique-t-il, nous avons combiné la ligne de préformage avec un procédé RTM adaptatif qui, si nécessaire, ajustait l'épaisseur de la pièce en augmentant la pression sur certaines parties de la presse. Cela aussi était automatisé, dans le but de remplacer l'intervention de l'opérateur de ligne, mais cela nécessitait une simulation des performances des pièces à l'aide de données de mesure et d'un logiciel FEA standard.
« Actuellement, la simulation des propriétés mécaniques de la pièce est effectuée hors ligne », explique Emonts. « Nous avons généré une base de données des variations de processus et de pièces, créé des algorithmes pour réagir à chaque variation et les avons validés via FEA. Ainsi, sur la base des variations mesurées par la ligne, les algorithmes lui ont ordonné d'effectuer une atténuation appropriée. Pour rendre la ligne adaptative in situ, la prochaine étape serait d'ajouter l'apprentissage automatique. » Pendant ce temps, AZL poursuit de nombreux projets Composite 4.0, notamment la production auto-optimisée de composites thermoplastiques hybrides et de pièces moulées par injection avec renforcement intégré des flans sur mesure à base de ruban.
Ailes en CFRP zéro défaut
Le projet ZAero (voir « Fabrication zéro défaut de pièces composites ») est un autre projet clé de Composites 4.0, qui a débuté en 2016. Il visait à augmenter la productivité des grandes structures en plastique renforcé de fibres de carbone (PRFC) telles que les ailes. Les défauts seraient réduits en utilisant une inspection en ligne automatisée avec un préimprégné AFP ou le placement automatisé de matériaux secs de Danobat (Elgoibar, Espagne) (ADMP, voir « Proving viability of dry fabrics, infusion for large aerostructures »). La surveillance du processus pendant l'infusion de résine ou le durcissement du préimprégné prédirait l'état de durcissement et réduirait la durée du cycle. Les données collectées sur les processus et les défauts ont été utilisées avec FEA pour prédire les performances des pièces. Cela a ensuite été entré dans un outil d'aide à la décision pour savoir comment traiter les défauts identifiés. Une simulation d'écoulement partiel pour les revêtements d'ailes CFRP a été développée qui, lorsqu'elle est introduite dans cet outil, a permis d'optimiser une stratégie de reprise (Fig. 2). Aujourd'hui, de nombreuses pièces de ce type sont retravaillées pendant la fabrication, mais seulement après le NDI. Les retouches antérieures et l'amélioration du contrôle des processus étaient en effet les objectifs du projet ZAero, ainsi que les catalyseurs de l'augmentation ciblée de 15 % du taux de production, de la réduction de 15 à 20 % de coût de production et 50 % de déchets en moins.
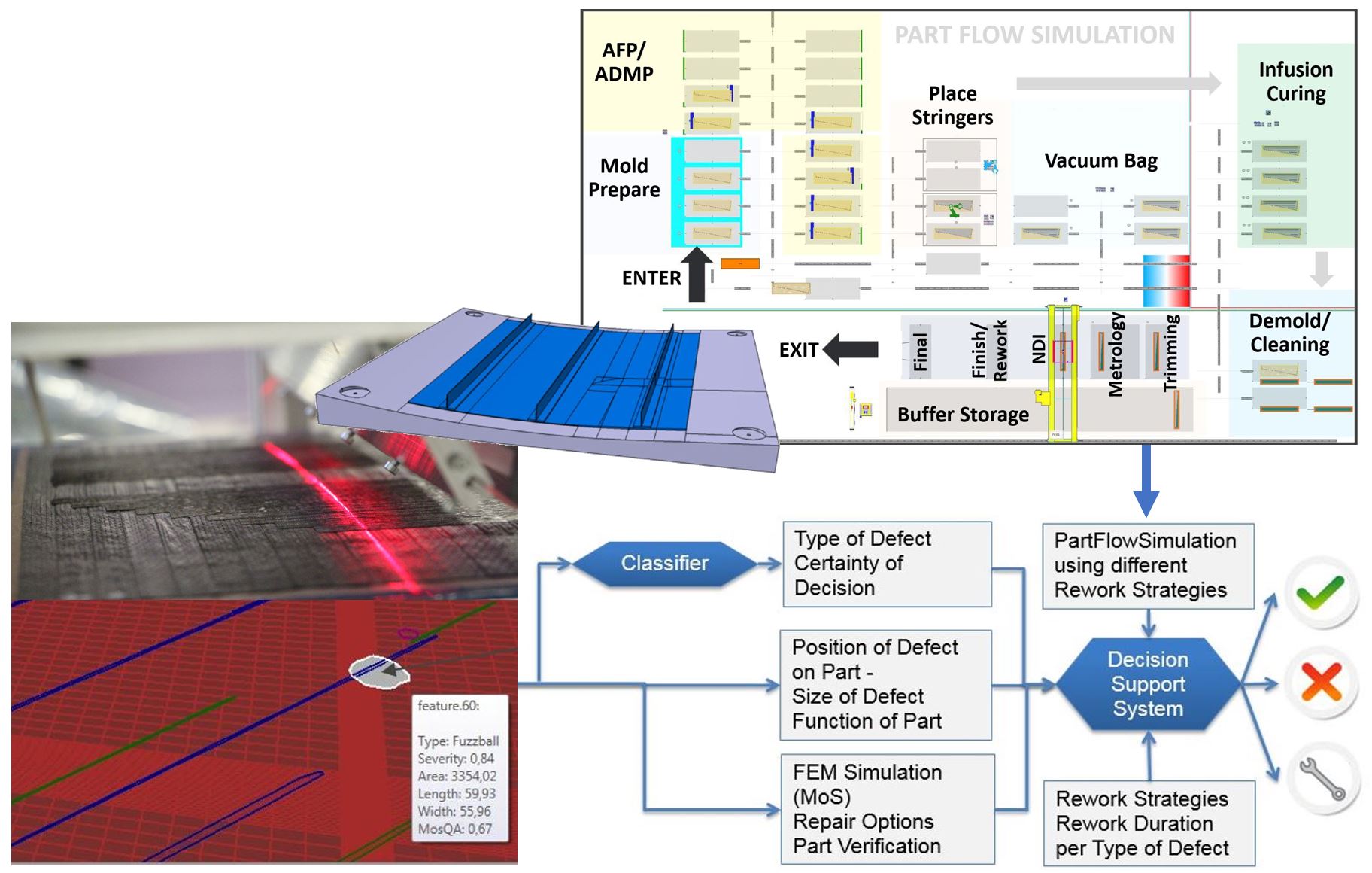
Lors de l'examen final de septembre 2019, le capteur AFP préimprégné développé par le chef de projet Profactor (Steyr, Autriche) a non seulement réalisé une inspection en ligne automatisée, mais pourrait également être utilisé pour corriger des pièces in situ. "Ce capteur peut détecter les défauts standard tels que les lacunes, les chevauchements, les FOD, les boules de fuzz et les câbles torsadés, ainsi que la coupe précoce et tardive de chaque câble", explique le Dr Christian Eitzinger, responsable de la vision industrielle chez Profactor. Un trait manquant peut être corrigé automatiquement avec le placement d'un trait supplémentaire précisément là où il a été omis. Cependant, la machine doit être arrêtée pour retirer les boules de poils ou un câble tordu. « Une base de données construite à l'aide de l'expérience 3D de Dassault Systèmes (Paris, France) pour CATIA nous permet de calculer les effets sur les performances de la pièce en fonction de la taille, de la forme et du type de défaut. Le traitement de tous les défauts d'un pli ne prend que quelques secondes. L'opérateur de la machine décide alors quels défauts peuvent être laissés et ce qui doit être retravaillé. »
Pour la surveillance et le contrôle du processus d'infusion, Airbus (Toulouse, France) a travaillé par l'intermédiaire de sa filiale InFactory Solutions (Taufkirchen, Allemagne) pour développer trois capteurs qui mesurent la température, l'état de durcissement et le front d'écoulement de la résine (voir « Capteurs pour la surveillance du front d'écoulement de la résine ». ) « Nous les avons intégrés à CATIA 3D Experience et avons montré que les données peuvent être acquises de manière fiable et ajoutées au fil numérique de chaque pièce », explique Eitzinger. (Voir l'encadré en ligne « Composites 4.0 : fil numérique contre le jumeau numérique ».)
Le dernier des démonstrateurs en trois parties était une sous-section de couverture d'aile supérieure avec trois longerons (voir l'encadré en ligne « mise à jour du projet ZAero »). Pour cette partie, l'outil d'aide à la décision de Profactor a été présenté en direct chez le partenaire FIDAMC (Madrid, Espagne), connecté à la simulation de flux de pièces - basée sur le logiciel Siemens PLM (Plano, Texas, États-Unis) Tecnomatix Plant Simulation - fonctionnant sur le serveur de Profactor en Autriche. En plus de créer une base de données de défauts, ZAero a mené des expériences d'apprentissage automatique. Des modèles informatiques génératifs conçus manuellement, combinés à des réseaux de neurones profonds détectés et classés, permettent d'obtenir un taux de classification correcte de 95 % des différentes régions (écart, chevauchement, remorquage, boule de fuzz) dans les données de surveillance ADMP réelles, même lorsque Les données sur les défauts créées artificiellement ont été utilisées pour la formation en profondeur du réseau (de la même manière que les systèmes de test par ultrasons sont calibrés sur une gamme de défauts délibérés).
"Nous allons certainement poursuivre une sorte de phase suivante", a déclaré Eitzinger. Pendant ce temps, Profactor commercialise des capteurs modulaires pour l'orientation des fibres et les défauts lors de la superposition automatisée. InFactory Solutions propose également ses capteurs AFP et d'infusion de résine, et les partenaires de placement de fibres Danobat et MTorres (Torres de Elorz, Navarre, Espagne) vendent désormais leurs équipements avec inspection en ligne intégrée.
Parcours de transformation numérique de Dynexa
Dynexa est un fabricant de pièces composites spécialisé dans les tubes et arbres en CFRP. « Nous avons toujours essayé de tout numériser », explique le directeur général Koppenberg. « Nous nous sommes déjà débarrassés des processus manuels et analogiques, en intégrant tout principalement dans notre système ERP [enterprise resource planning]. Mais comment faisons-nous cela dans la fabrication? Nous avons compris que tout ce que nous mettons dans un protocole ou une procédure de travail est un code, et c'est une base pour la transformation numérique. Mais où est-il stocké ? Sur un serveur local, dans le cloud ou au sein de la machine ? Nous demanderions à cinq personnes et obtiendrions sept réponses sur ce que nous devrions faire. (Voir l'encadré en ligne, « Composites 4.0 :Par où commencer ? »)
Heureusement, le gouvernement allemand avait mis en place un programme permettant aux universités de fournir des conseils gratuits sur l'Industrie 4.0 aux petites et moyennes entreprises (PME). Dynexa a commencé à travailler avec le centre de compétences « Mittelstand (SME) 4.0 » de Darmstadt. "Ils ont dit de ne pas s'inquiéter de l'architecture numérique mais de se pencher davantage sur ce que vous devez mesurer et comment le faire", se souvient Koppenberg. "Nous avons choisi un processus qui impliquait une mesure manuelle importante, où nous savions que nous avions des problèmes de qualité, de temps et de coût."
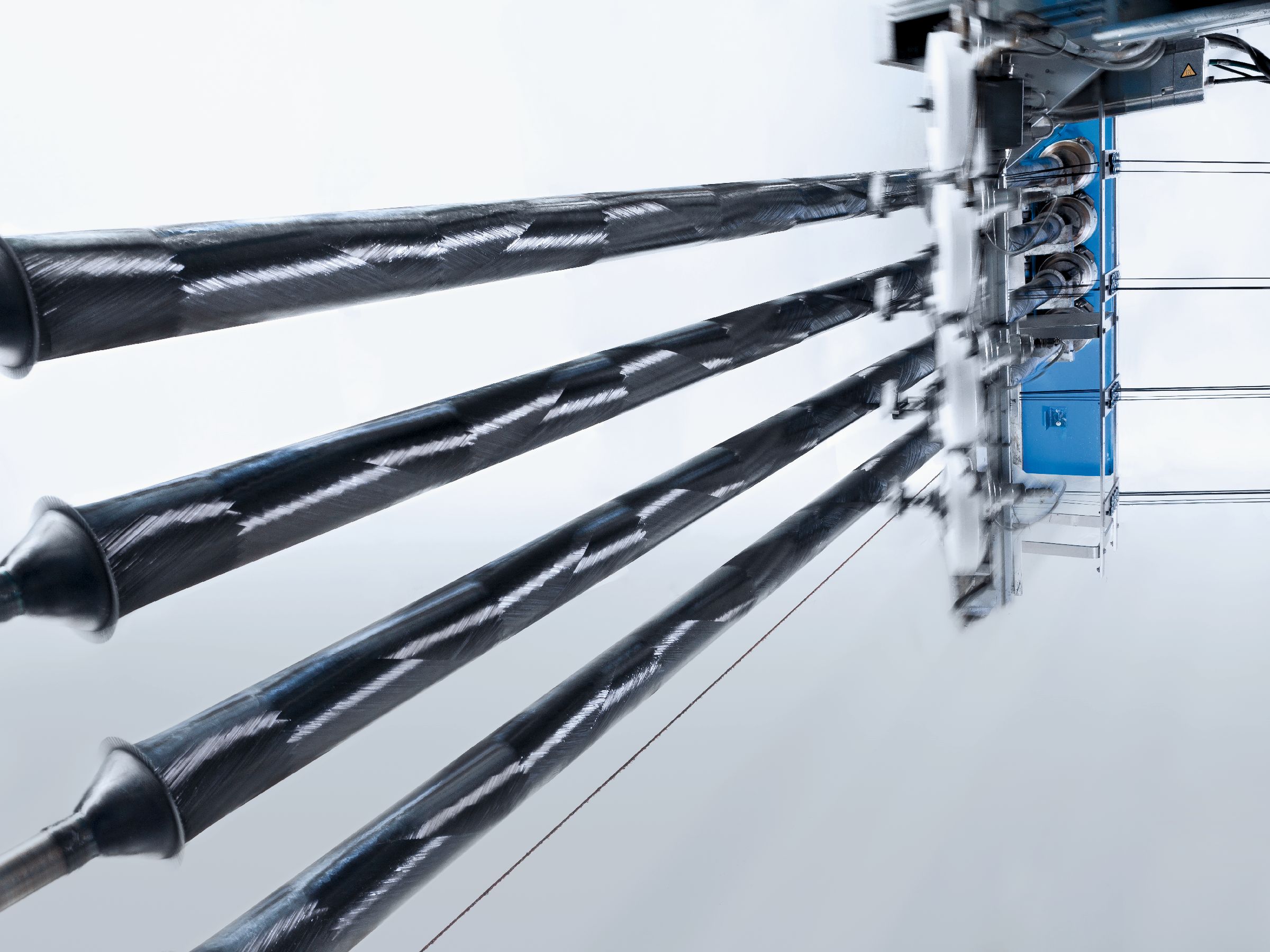
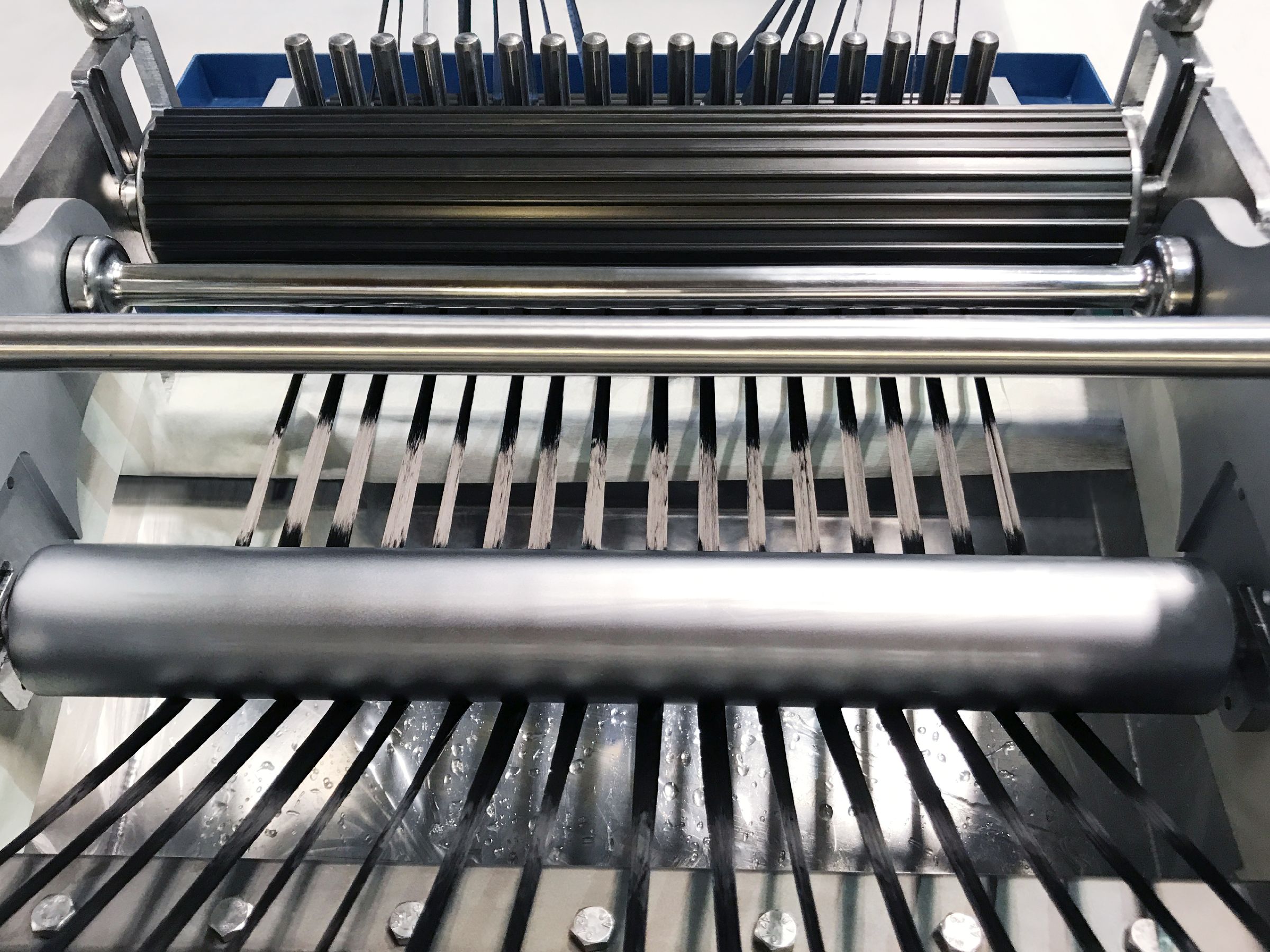
Dynexa utilise un processus d'enroulement filamentaire humide (voir « Arbre de sortie composite prêt pour le terrain d'essai automobile.) » Une étape clé est le ramassage de la résine, où la fibre sèche est acheminée sur un rouleau de compactage qui sort du bain de résine. Une racle est posée contre le rouleau de compactage qui détermine la quantité de résine à combiner avec le filament sec avant qu'il ne soit enroulé. "Si nous ramassons trop de résine, nous pouvons dépasser le diamètre du tube spécifié", explique Koppenberg, "mais avec trop peu de résine, nous risquons de tomber en dessous du diamètre minimum autorisé."
« Sans mesure, vous ne connaissez le diamètre final qu'après durcissement, lorsque toute la valeur a été investie », précise-t-il. « Ainsi, l'opérateur doit arrêter la machine, mesurer la pièce, la noter puis redémarrer. Grâce à des années d'expérience, nous savons quelle doit être l'épaisseur du stratifié à chaque étape du bobinage. Ainsi, l'opérateur compare la mesure et ajuste la racle pour corriger le prélèvement de résine si nécessaire, mais cela est très manuel et repose sur les compétences et l'expérience de l'opérateur. »
Pour numériser cela, Dynexa s'est entretenu avec une myriade de fabricants de lasers et d'appareils photo. « Ils disaient : « nous avons la solution », mais personne n'a pu la faire fonctionner », note Koppenberg. L'équipe de l'Université de Darmstadt, cependant, a permis l'utilisation d'une caméra en déterminant les corrections nécessaires en raison de certains facteurs physiques, tels que la réflexion de la lumière sur la surface humide. "Maintenant, nous avons le bobinoir connecté à l'appareil de mesure, qui fonctionne de manière très standardisée", ajoute-t-il.
L'équipe a développé une base de données de tables de correction et d'algorithmes de décision qui permet à la machine d'enroulement filamentaire de savoir quelle doit être la cible pour chaque étape du tube spécifique en cours d'enroulement. "Si l'entrée de l'appareil de mesure montre que la prise de résine n'est pas là où elle devrait être", explique Koppenberg, "la machine d'enroulement filamentaire réagit en ajustant la racle pour la ramener aux spécifications sans arrêter l'enroulement pour mesurer."
Chaque bobineuse dispose désormais du système de mesure numérique, et une carte ethernet. « La partie la plus chère a été d'installer et d'acheminer les câbles jusqu'au serveur », ironise Koppenberg, « mais maintenant nous pouvons parler à chaque machine et collecter toutes les données. » Et il y a un autre avantage. « Avant, les opérateurs programmaient sur les machines, mais une fois que nous les avons connectés au serveur, nous pouvons programmer sur n'importe quel ordinateur de bureau ou portable. Cela a encore réduit les temps d'arrêt et supprimé un autre goulot d'étranglement de la production. »
Cette première étape numérique a permis à Dynexa d'améliorer le contrôle, la qualité et l'efficacité de ses processus, lui permettant ainsi de devenir plus rentable. Cela a également stimulé une nouvelle transformation.
Changement de paradigmes pour les composites
« Nous sommes dans un processus par étapes visant à fournir un nouvel écosystème à nos clients », déclare Matthias Bruckhoff, directeur des ventes et du marketing de Dynexa. Il donne un exemple :« Sur Amazon, vous pouvez voir ce que vous avez acheté et quand, ainsi que de nouveaux produits suggérés. Nous avions l'habitude de prendre les exigences des clients et de répondre en quelques jours à l'aide de nos outils de calcul et d'ingénierie. Maintenant, ce sera en ligne. Nos clients examineront les produits et calculeront ce dont ils ont besoin, leur coût et leur livraison en quelques minutes. Ce n'est pas nouveau, mais c'est l'est pour notre industrie. Tout comme nous avons libéré nos opérateurs de machines pour qu'ils se concentrent sur davantage de machines et de tâches de plus haut niveau, nous allons maintenant libérer notre équipe d'ingénieurs pour qu'elle se concentre sur des produits plus spécialisés et sophistiqués. »
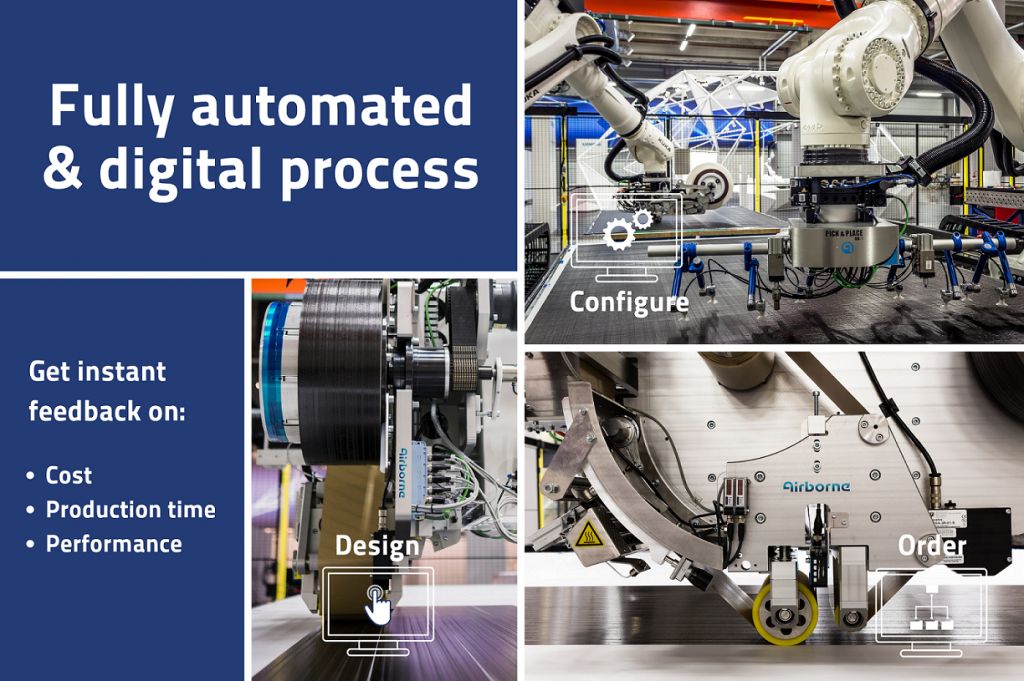
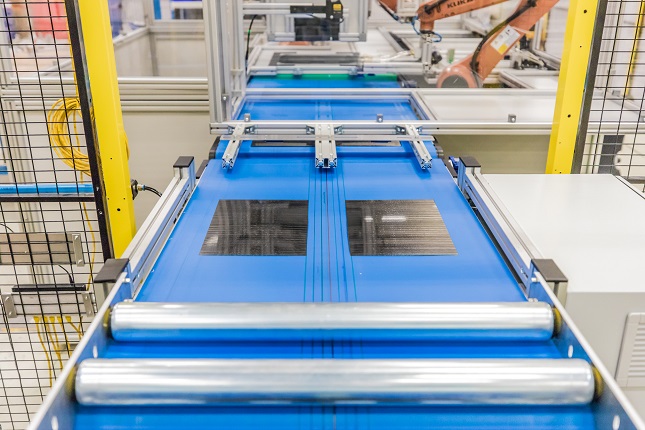
Airborne (La Haye, Pays-Bas) a lancé son portail de fabrication à la demande pour la fabrication automatisée de composites en septembre 2019 (voir « Airborne lance un portail d'impression composite »). À l'aide de cet outil, les clients saisissent les conceptions dans la plate-forme Web. Le système crée ensuite le code machine à la volée et détermine la durée et le coût de production. Les produits peuvent ensuite être personnalisés et, une fois commandés, fabriqués dans une cellule de fabrication automatisée. Le portail a été lancé à l'aide de la cellule de stratification automatisée (ALC) d'Airborne pour traiter le préimprégné thermodurcissable. Elle sera étendue à d'autres procédés, par exemple la ligne de production de composites thermoplastiques (TPC) à grand volume développée pour la business unit Spécialités de SABIC (Riyad, Arabie Saoudite).
« Ce portail est un élément clé de la façon dont nous voyons l'avenir numérique de la fabrication de composites », déclare Marcus Kremers, directeur de la technologie chez Airborne. « Il y a cinq ans, nous sommes passés d'un modèle commercial de fabrication de pièces à une aide aux clients avec l'automatisation et la numérisation. Nous développons un portefeuille de solutions qui permettent aux clients de construire facilement avec des composites. » Ce portefeuille comprend l'ALC, l'enrobage en nid d'abeille automatisé, le kit de plis automatisé et la ligne à haut volume utilisant des bandes TPC, surnommée la ligne de fabrication de composites numériques (DCML) par SABIC et Falcon par Airborne. Ce dernier est un exemple des solutions sur mesure d'Airborne. "Nous intégrons nos connaissances en matière de fabrication de matériaux composites et de pièces dans ces systèmes automatisés afin que les clients n'aient pas besoin d'être des spécialistes", déclare Kremers.
Airborne a trois modèles commerciaux :acheter l'automatisation, la louer ou la laisser à Airborne pour qu'elle fonctionne via la fabrication en tant que service (MaaS). Les cellules automatisées aéroportées disposent de capteurs et de systèmes d'inspection en ligne qui génèrent des alertes basées sur une base de données de défauts et de tolérances définies par le client. « La gamme Falcon a des tolérances très faibles pour les défauts de qualité visuelle », note Kremers, « mais notre automatisation pour l'aérospatiale est davantage axée sur les tolérances structurelles. Nous améliorons également continuellement nos technologies pour qu'elles soient autodidactes et auto-adaptatives. Par exemple, notre prochaine version de logiciel pour la pose de bandes ALC aura la capacité d'identifier les défauts et de modifier le programme de production à la volée. »
À plus long terme, la vision est d'étendre le portail à la demande pour collecter la capacité de production de pièces composites répartie entre plusieurs entreprises et régions. Kremers cite Protolabs (Maple Plains, Minn., États-Unis), qui fournit des prototypes moulés par injection, en tôle, usinés CNC ou imprimés en 3D à la demande en moins d'une journée. De même, l'application en ligne de Plyable (Oxford, Royaume-Uni) fournit des moules pour la fabrication de composites, proposant des matériaux allant du panneau de polyuréthane à l'acier, en passant par les outils composites et imprimés en 3D. « C'est une façon différente d'organiser la chaîne de valeur », déclare Kremers. « Nous fabriquons les machines et les logiciels qui rendront cela possible pour les pièces composites. »
AZL Aachen poursuit également cet objectif avec sa machine de consolidation ultra-rapide, développée pour produire des stratifiés TPC multicouches en moins de cinq secondes. Commercialisé en 2019, il utilise des applicateurs AFP robotisés et assistés par laser de Conbility (Aix-la-Chapelle, Allemagne) et des rubans UD de 25 millimètres de large ainsi qu'un principe de flux de pièces - à la pointe de la technologie dans l'industrie de l'impression à grande vitesse - pour produire des stratifiés TPC, simplement collés ou entièrement consolidés, dans une variété d'épaisseurs, avec des renforts locaux. "Notre vision est de fournir des machines évolutives qui permettront des plates-formes en ligne", explique Emonts. « Les lignes peuvent avoir plusieurs stations, chacune avec plusieurs applicateurs AFP. Le client entrera les exigences et obtiendra des options pour le livret, le coût et la livraison. Une fois finalisé, ce sont les applicateurs qui communiquent entre eux pour organiser la production, pas l'opérateur. Il s'agit d'une production totalement intelligente de composites sur mesure. »
Automatiser l'automatisation
L'objectif principal de la ZLP est la production automatisée de structures CFRP. « L'automatisation d'une seule pièce ou d'un programme est difficile à justifier », note Florian Krebs, chef d'équipe ZLP pour l'automatisation flexible. « Cependant, si vous passez des machines spécifiques à une tâche à une plate-forme d'automatisation reconfigurable sans pratiquement aucune configuration supplémentaire, vous disposez désormais d'une solution d'entreprise. Plus la plate-forme est flexible, plus le retour sur investissement est rapide. »
La cellule de travail montrée dans les images d'ouverture a été conçue dans le cadre du projet ZLP PROTEC NSR pour construire une famille de pièces qui suit le même itinéraire de processus :drapage pick-and-place de tissus secs non frisés et infusion de résine (voir la barre latérale en ligne « Non analyse de rentabilisation pour l'enseignement des robots »). « Ce procédé a été conçu pour la cloison de pression arrière de l'Airbus A350, mais vous pouvez également réaliser un panneau de fuselage ou un capot d'aile sur cette ligne car les étapes sont similaires », explique Krebs.
« Réaliser des plates-formes d'automatisation flexibles nécessite certaines briques technologiques, notamment des algorithmes pour les robots, ainsi que des capteurs et la façon de comprendre les données qu'ils produisent », explique Kupke. "Par exemple, la ligne de production PROTEC NSR est conçue pour une modularité maximale - tous les modules sont interconnectés les uns aux autres pour démontrer un système d'auto-configuration, de correction et d'optimisation, évolutif en taille et en complexité."
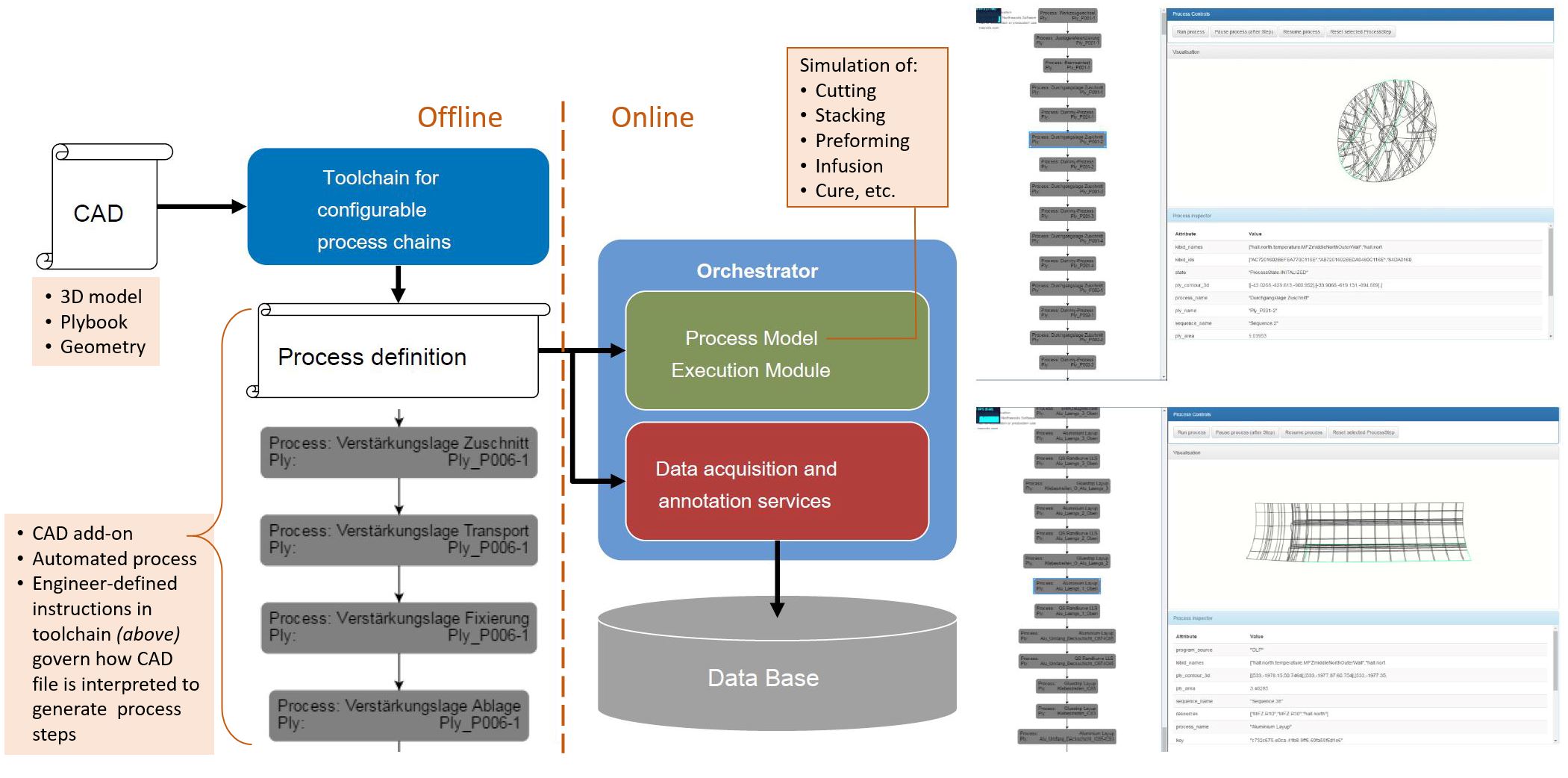
Il explique les modules comme le montre la figure 5, qui incluent le modèle CAO, la définition du processus, le modèle de processus qui permet la simulation et l'exécution du processus, le module d'exécution de la fabrication, les capteurs pour acquérir des données, le logiciel pour annoter les données et la base de données pour le stockage.
« Sur le côté gauche de ce diagramme, vous faites un plan. Le module d'exécution met ensuite en œuvre ce plan », explique Kupke. « Au cours des étapes du processus, nous acquérons des données de toutes les machines et processus impliqués, par exemple, le cutter, les robots, le bâtiment (température, pression, humidité), les caméras lors du pick-and-place, etc. Nous analysons les données en temps réel pendant le processus et annoter également les données collectées automatiquement avec des métadonnées pour les alimenter dans la base de données, qui constitue la base du jumeau numérique du processus. Le point le plus important du jumeau numérique est d'avoir un référentiel central, une source de vérité. Le modèle CAO et la définition de processus de chaque pièce font partie de sa source unique de vérité. »
Avec ces modules en place, la ligne fonctionne de manière autonome par simple pression d'un bouton. À partir du modèle CAO, du plan de production et des caméras, les robots déduisent quelle pièce coupée vient ensuite et la recherchent sur la table (par exemple, à partir de 100 autres pièces coupées). "Ils décident comment configurer les pinces pour le ramasser et le déposer dans l'outillage, et savent où le placer." Sur la base du plan de production, les robots déterminent chaque chemin de début/fin pour toutes les étapes du processus et savent quand chacun est terminé. "Habituellement, ces chemins sont enseignés par un humain", note Kupke. « Mais dans notre système, chaque chemin est défini automatiquement, sans collision et en temps réel. Si vous modifiez le modèle CAO ou la définition du processus, les robots s'adapteront sans aucun effort pédagogique supplémentaire. Mais que se passe-t-il si vous changez complètement la pièce ? Avec ce type d'automatisation, vous pouvez effectuer ce changement très rapidement. C'est la voie vers une production flexible. Notre rôle chez ZLP est d'ouvrir cette voie en développant des briques technologiques et en les reliant entre elles. »
Opportunité et ontologie
La pandémie de COVID-19 a mis en évidence la valeur de la production flexible. Il a également créé un environnement commercial de plus en plus imprévisible. « Au cours des deux ou trois dernières années, tout est devenu plus volatile », note Bruckhoff de Dynexa. « Nos clients veulent des réponses très rapides, afin de répondre à leur client. En proposant notre nouvel écosystème en ligne, nous rendons l'ensemble de la chaîne d'approvisionnement plus compétitif. »
Ceci est bien reconnu par l'industrie aéronautique. « Nous avons besoin d'une base numérique pour les lignes de production et les sites entiers qui permettent une intégration à la fois horizontale et verticale », déclare Marc Fette, président de la division technique Technologies aérospatiales du VDI - l'Association allemande des ingénieurs et COO du Composite Technology Center (CTC, Stade, Allemagne), filiale R&T d'Airbus. Les projets CTC dans Composites 4.0 incluent le suivi des matériaux et des actifs, des robots collaboratifs, des chaînes de processus avancées, etc. Mais Fette souligne la nécessité d'une ontologie - une terminologie et un protocole commun pour la communication numérique et l'échange de données. (Voir l'encadré en ligne « Architecture et ontologie des composites 4.0 ».)
« Vous avez besoin d'une mise en réseau globale pour toutes les machines et tous les systèmes de production d'une usine donnée », explique-t-il, « mais cela doit également s'étendre à l'ensemble de la chaîne de création de valeur, y compris des disciplines telles que l'ingénierie, l'approvisionnement, la logistique et la certification des matériaux et des processus. , d'un côté. D'autre part, toutes les parties prenantes, telles que les fournisseurs, doivent être prises en compte et impliquées dans ce processus de changement. Nous voyons beaucoup de projets pilotes, mais quand vous regardez en détail, il y a toujours un manque de stratégie pour une approche holistique par entreprise ou chaîne de production. »
Il poursuit :« Nous avons un très grand réseau mondial de fournisseurs et ils ont les mêmes exigences pour fonctionner comme une chaîne d'approvisionnement connectée numériquement. La plupart de nos fournisseurs sont des PME travaillant pour les deux avionneurs, Airbus et Boeing. S'il n'y a pas de discussion sur une norme commune, vous transmettez ces défis aux fournisseurs. Ils ne peuvent très probablement pas se permettre de se conformer à deux ensembles de normes différentes pour toutes leurs machines, y compris la documentation, l'évaluation des données, la cybersécurité, etc. »
Fette admet qu'il s'agit de grandes idées et affirme que les constructeurs d'avions élaborent des plans pour relever ces défis. "Mais il y a de nombreux obstacles comme celui-ci, et c'est vraiment complexe, impliquant non seulement la technologie mais aussi des problèmes sociaux, économiques, ergonomiques et juridiques - c'est un processus de changement mental. Nous n'en sommes qu'au début. Mais pour réussir, nous devons comprendre que ces nouveaux systèmes reposent sur des personnes et que ces personnes doivent être présentes, pas seulement chez les OEM, mais dans l'ensemble du réseau mondial. »
« Les marchés sont de plus en plus fragmentés dans toutes les industries et tout le monde est confronté à un changement de paradigme », note Krebs de ZLP. "Beaucoup de gens ne voient pas cela comme une opportunité", ajoute Kupke, également de ZLP. Mais ceux qui voient cette opportunité envisagent un accès démocratisé aux composites permis par Composites 4.0, et avec cela, un marché beaucoup plus large, y compris des applications que nous commençons seulement à concevoir.
Résine
- Optimisation de la transformation numérique dans la fabrication CPG
- La stratégie de transformation numérique exige une nouvelle approche des talents
- La transformation numérique basée sur les données propulse Airbus vers de nouveaux sommets
- Comment la nouvelle ère de la transformation numérique change-t-elle le secteur des services publics ?
- Evonik va construire une nouvelle usine de production PA12
- Planifier pour réussir la transformation numérique
- Qu'est-ce que la transformation numérique dans la fabrication ?
- 7 moteurs de la transformation numérique
- Défis de la transformation numérique dans le secteur manufacturier