Résines époxy retransformables, réparables et recyclables pour composites
Pour la plupart des structures composites aérospatiales, l'époxyde thermodurcissable a été la résine matricielle préférée en raison de ses propriétés mécaniques élevées, de son faible retrait au durcissement et de sa résistance à la température et à l'humidité, ce qui empêche la dégradation de l'environnement pendant le service. Ces avantages résultent de la structure moléculaire réticulée de l'époxyde formée pendant le durcissement. Cependant, cette chimie covalente thermodurcissable a également signifié que les composites époxy durcis traditionnels ne peuvent pas être facilement remoulés, remodelés ou dissous, ce qui rend le recyclage et la réparation plus difficiles.
Au cours de la dernière décennie, dynamique des chimies ont été développées dans lesquelles des liaisons covalentes sont échangées et réarrangées avec un stimulus tel que la chaleur. Appelés « résines réversibles », ces polymères sont thermodurcis propriétés inférieures à la température de transition vitreuse (Tg ), mais se comporte comme un thermoplastique à des températures élevées, telles que 80 °C au-dessus de Tg . CIDETEC (Donostia-San Sebastian, Espagne) est un organisme de recherche appliquée qui travaille sur de telles résines depuis 2013. Il a breveté des résines époxy et des composites thermo-mécaniquement retraités basés sur l'échange de disulfures aromatiques, ce qui permet le retraitement, la réparation et le recyclage. (technologie 3R) des composites durcis. Le CIDETEC dirige désormais 11 partenaires du projet Horizon2020 AIRPOXY pour faire mûrir cette technologie du niveau de maturité technologique (TRL) 3 au TRL 5.
Lancé en septembre 2018, ce projet de 42 mois fera progresser les processus de thermoformage des composites 3R pour une production en grand volume, une réparation et un assemblage rentables des composites 3R par soudage thermodurcissable et une meilleure liaison adhésive. Ces technologies seront présentées dans deux démonstrateurs aérospatiaux :une section de capot de soufflante en composite avec peau moulée par transfert de résine (RTM) et raidisseur transversal collé à un raidisseur longitudinal thermoformé; et une section de bord d'attaque d'aile avec des nervures thermoformées soudées à une peau réalisée en utilisant le même RTM qualifié (SQRTM). CIDETEC explore également le recyclage des matériaux et pièces composites 3R et évalue les avantages de cette technologie par rapport aux composites traditionnels à l'aide des méthodologies d'évaluation du cycle de vie (ACV) et du coût du cycle de vie (LCC).
Vitrimère époxy 3R
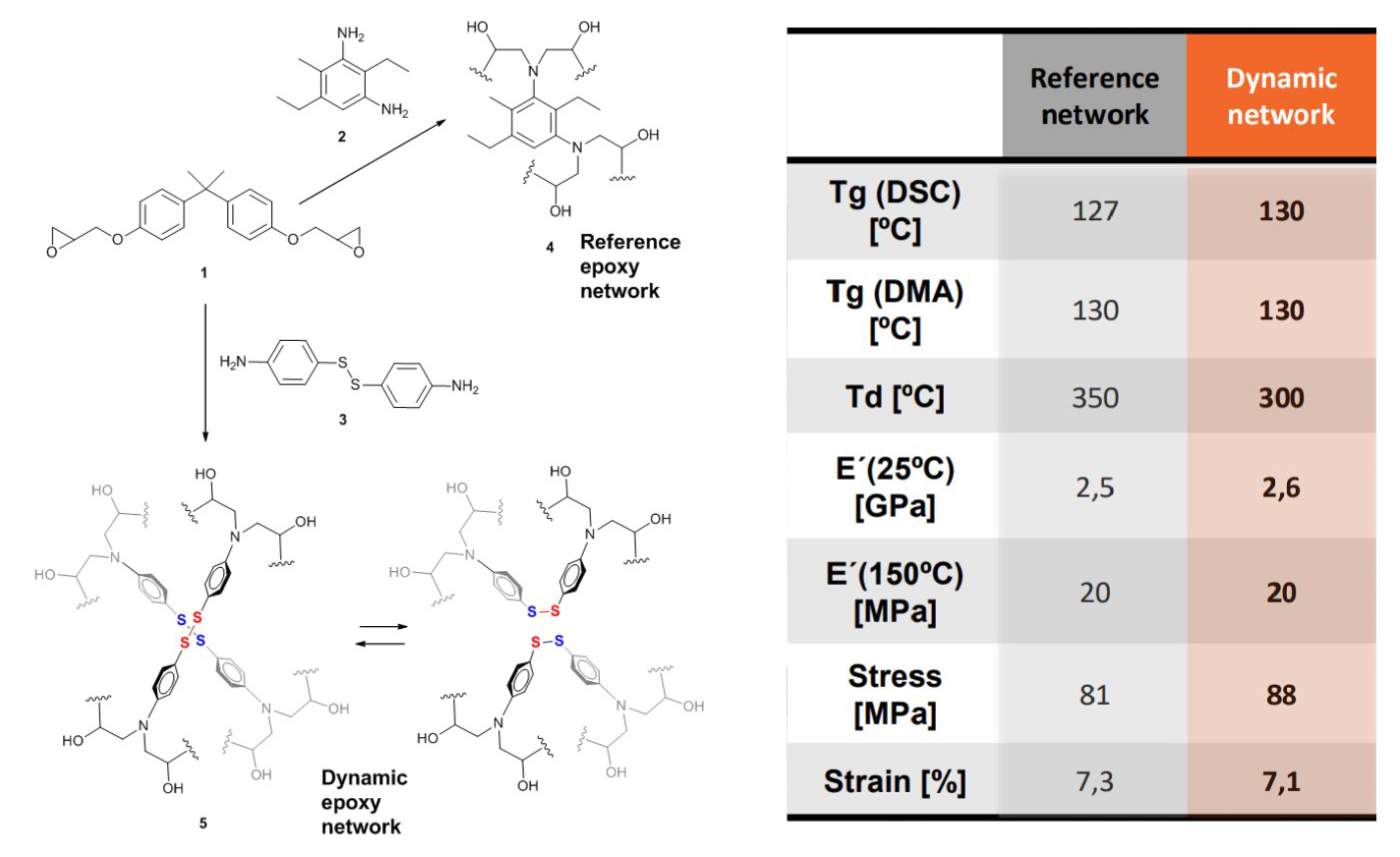
« La chimie dynamique peut être classée en deux types :dissociative et associative », explique Alaitz Rekondo, responsable Polymères et Composites au CIDETEC. Elle note qu'avec la chimie dissociative, les liaisons croisées sont rompues. « Les matériaux perdront ainsi leur intégrité avec le thermoformage et le recyclage en raison des liaisons rompues. » CW a écrit sur ce type de chimie via la résine réticulée thermoréversible d'Evonik (Essen, Allemagne) basée sur les réactions de Diels-Alder et le durcisseur époxy Recyclamine de Connora, qui permet le clivage des réticulations. Ceci est réalisé en immergeant les composites Recyclamine dans un solvant à faible pH à température élevée, en convertissant la résine en un époxy thermoplastique tout en libérant le renfort de fibre continu afin que la résine et la fibre puissent être réutilisées. A noter, la Recyclamine a été acquise en 2019 par Aditya Birla Chemicals (Mumbai, Inde) et est désormais utilisée dans les résines époxy recyclables Epotec.
Cependant, les résines 3R de CIDETEC sont différentes. « Notre chimie est associative , de sorte que les liaisons croisées ne sont jamais rompues », note Rekondo. « Nos résines sont des vitrimères. CW a introduit les vitrimères dans l'article de Jeff Sloan de 2020 sur Mallinda (Denver, Colorado, États-Unis). « Ainsi, les résines se comportent comme un thermoplastique pendant tout le traitement », explique-t-elle, « en raison de l'échange dynamique lors du chauffage – pour nous, cela se produit dans les liaisons disulfure aromatiques – mais les résines restent toujours thermodurcissables. Contrairement à de nombreux vitrimères, les résines 3R ne nécessitent pas de catalyseurs. Mais nous pouvons utiliser des catalyseurs, si nécessaire, pour répondre aux différentes exigences des cycles de durcissement rapide/snap-cure ou de durcissement à température ambiante. »
CIDETEC a commencé ses recherches sur les vitrimères avec des matériaux élastomères souples à la recherche de propriétés d'auto-cicatrisation. « Nous utilisions un durcisseur dynamique disponible dans le commerce, puis nous nous sommes rendu compte qu'il s'agissait également d'un durcisseur pour les époxydes », explique Rekondo. Les formulations initiales de résine époxy 3R de qualité industrielle ont montré des propriétés comparables aux époxydes aérospatiaux actuels (Fig. 1). « Vu le grand potentiel des résines retraitement et recyclables pour l'aérospatiale, c'est maintenant l'un de nos principaux domaines de recherche. »
Nerea Markaide, coordinatrice du projet AIRPOXY au CIDETEC, explique que le potentiel est en effet grand :le thermoformage 3R permet une production de composites en grand volume qui est nettement plus rapide et moins chère qu'un autoclave, la réparation 3R est 50 % moins chère que les méthodes actuelles de patch composite collé, 3R le soudage réduit les coûts d'assemblage de 55 % par rapport au collage actuel et le collage 3R est plus robuste que les méthodes actuelles. À terme, CIDETEC envisage une famille de résines et d'adhésifs 3R pour améliorer le coût et la durabilité de la production d'aérostructures composites.
Préimprégné, RTM et thermoformage
Le CIDETEC, en charge de la formulation de la résine 3R de qualité aérospatiale, a identifié la meilleure formulation de résine pour des essais de démonstration. Ce système pour infusion de résine ou RTM a un Tg de 170°C sec/150°C humide, une viscosité de 200 centipoises à 70°C et une faible absorption d'humidité (2-3%). Il peut être formulé comme un système à un ou deux composants avec un durcissement typique d'une heure à 130°C et un post-durcissement de 30 minutes à 180°C.
CIDETEC a utilisé cette formulation de résine 3R pour imprégner le tissu satiné à cinq harnais (5HS) de Chomarat (Le Cheylard, France) fabriqué avec de la fibre de carbone à module intermédiaire dans un processus de préimprégnation en continu. Ce préimprégné a ensuite été utilisé par le Leibniz-Institut für Verbundwerkstoffe (IVW, Kaiserslautern, Allemagne) pour fabriquer des stratifiés 3R multicouches plats et de forme 3D par moulage par compression continue (CCM).
Des stratifiés 3R ont également été fabriqués à l'aide de RTM pour infuser des tissus 5HS et unidirectionnels (UD) en utilisant des paramètres de processus optimisés pour la résine 3R par Eurecat (Barcelone, Espagne). Ingeniería y Desarrollos en Composites (IDEC, Araba, Espagne) démontrera la production de RTM dans un environnement industriel en utilisant la même résine pendant qu'elle commence les essais pour produire la peau RTM et le raidisseur transversal pour le démonstrateur de sous-composant de capot de soufflante de 0,5 mètre x 0,5 mètre.
Pendant ce temps, Coexpair (Namen, Belgique) et Sonaca (Charleroi, Belgique) combineront Hexcel (Stamford, Connecticut, États-Unis) HexPly 8552 préimprégné époxy durci avec un film de résine 3R - qui permettra le soudage (voir ci-dessous) - pour produire le nez incurvé structure pour le démonstrateur de sous-composant de bord d'attaque de 1 mètre de long utilisant le même processus RTM qualifié (SQRTM) (voir « SQRTM permet des pièces en forme de filet »).
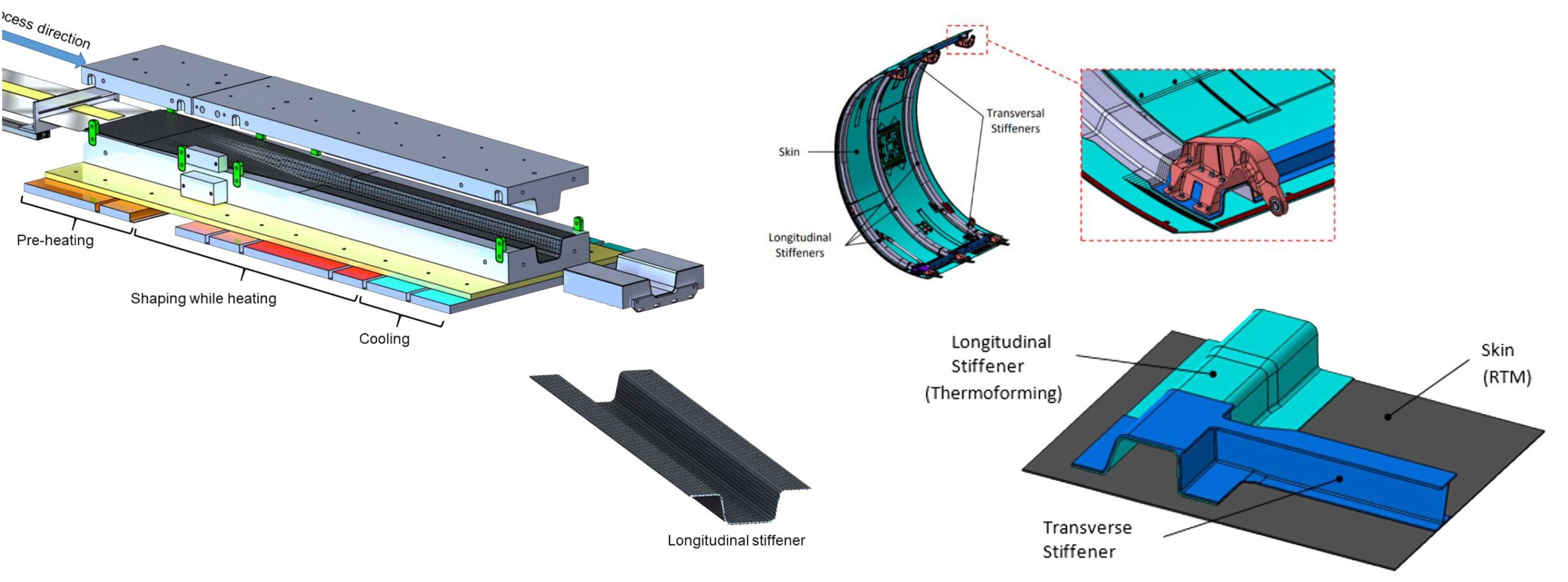
Fig. 2. Démonstrateur de sous-composant de capot de ventilateur
IDEC supervisera le collage des raidisseurs stratifiés 3R et de la peau à l'aide d'un film adhésif 3R. IDEC réalisera la peau et le raidisseur transversal en RTM tandis qu'EireComposites réalisera le raidisseur longitudinal en CCM. Crédit photo :IVW (gauche et en bas à droite) et IDEC (en haut à droite)
Les laminés préimprégnés et RTM flat 3R ont également été utilisés pour démontrer le thermoformage. Les simulations utilisées étaient basées sur des modèles microscopiques et macroscopiques d'éléments finis (FEM) développés par Altair Engineering (Antony, France), le moulage par compression discontinue optimisé IVW (DCM ou emboutissage) et les procédés CCM pour les matériaux 3R. EireComposites (comté de Galway, Irlande) utilise le DCM pour produire les nervures et les raidisseurs longitudinaux des démonstrateurs tandis qu'IVW produit les raidisseurs longitudinaux à l'aide du CCM. Les deux procédés utilisent une pression d'environ 20 bars tout en chauffant à environ 210°C, suivi d'un refroidissement de la pièce dans le moule fermé (Fig. 2). Les tests menés par Eurecat ont montré que les pièces composites thermoformées 3R répondent aux exigences typiques des aérocomposites, y compris une teneur en vide inférieure à 2 %. Il a également constaté que la résistance au cisaillement interlaminaire (ILSS) pour les stratifiés thermoformés avec 5HS était d'environ 80 % (43 MPa) de celle des pièces RTM (54 MPa).
Collage, soudage, SHM et réparation
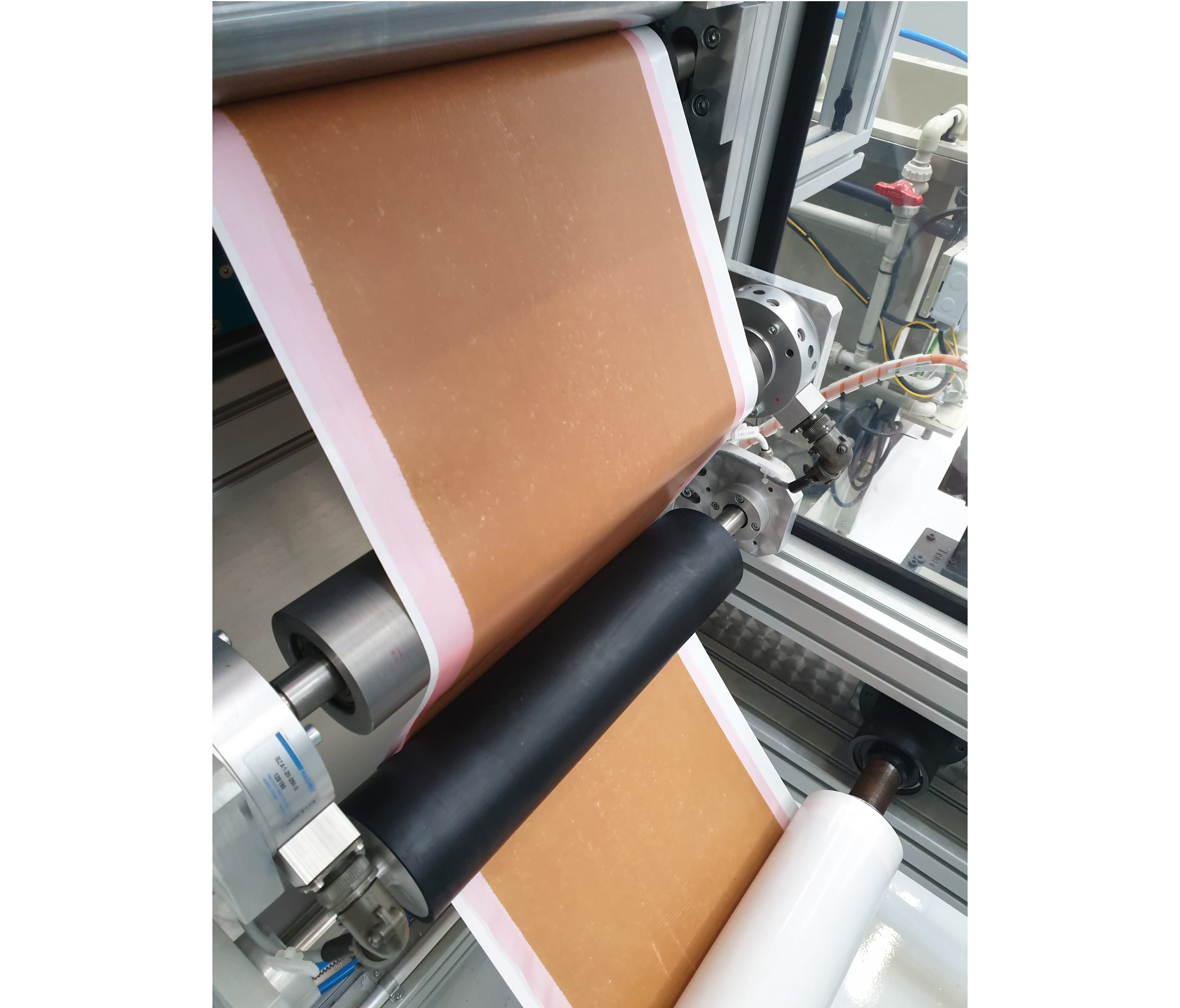
CIDETEC a reformulé la résine 3R pour l'optimiser pour le collage et a produit les premiers films adhésifs 3R en février 2020. le remaniement du pont disulfure, ce qui améliore l'intégrité du joint. IDEC supervisera le collage des raidisseurs et de la peau à l'aide d'un film adhésif 3R pour produire le démonstrateur de sous-composant de capot de soufflante (Fig. 2).
La chimie dynamique des résines 3R permet également la création de liaisons covalentes entre deux stratifiés composites 3R lorsqu'ils sont assemblés à l'aide de chaleur et de pression - décrit par CIDETEC comme un soudage thermodurcissable. Ceci sera utilisé par EireComposites pour joindre les nervures en stratifié 3R estampées au nez SQRTM pour le démonstrateur de bord d'attaque de l'aile (Fig. 3). Des paramètres de soudage optimisés ont été développés par IVW pour les stratifiés 3R. Notamment, le nez SQRTM réalisé avec le préimprégné commercial intègre un film de résine 3R supplémentaire en surface pour permettre le soudage des deux nappes. « Le procédé pour effectuer le soudage au niveau d'un démonstrateur est actuellement à l'étude », note Rekondo.
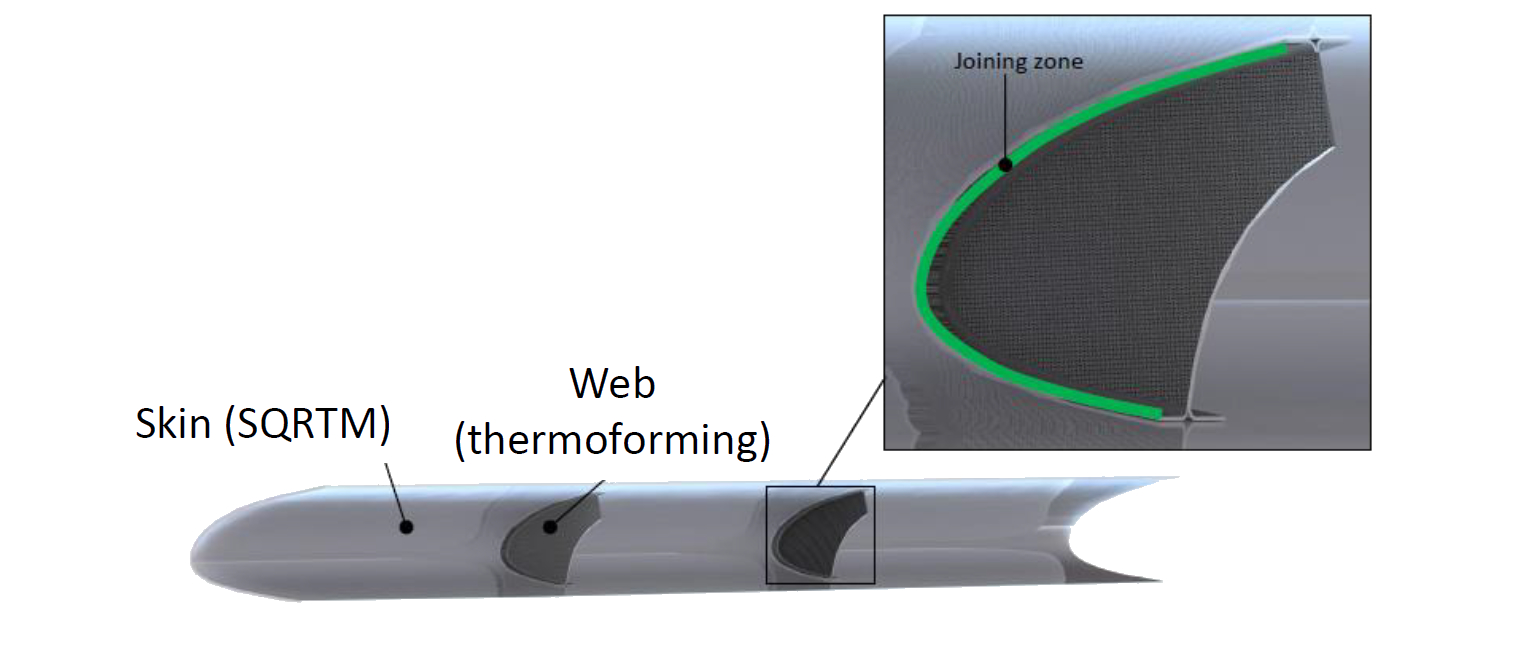
Dans le lot de travaux 4 – Surveillance de l'état de la structure (SHM) et réparation, IVW a étudié la réparabilité des défauts, tels que les délaminations et les joints de soudure détachés dans les composites 3R. L'équipe a réparé les délaminages en chauffant la zone défectueuse à la température de réparation de 220 °C et en appliquant une pression de consolidation constante de 20 bars tout en maintenant la température constante.
Le laboratoire Composites and Smart Materials (CSML) de l'Université d'Ioannina (Ioannina, Grèce) a évalué cette technique de réparation comme réussie à l'aide d'essais mécaniques ainsi que de diverses techniques d'évaluation non destructive (NDE), notamment les ultrasons multiéléments, la thermographie infrarouge, l'émission acoustique, la spectroscopie d'impédance et méthode de changement de résistance électrique (ERCM). Cette méthodologie NDE multiplateforme innovante a fourni une détection approfondie des dommages et des informations clés sur l'évolution du processus d'endommagement.
En termes d'efficacité de réparation, d'après les tests ILSS, les composites 3R ont montré une récupération de 72 % de leurs propriétés mécaniques initiales après réparation et une récupération de ≈ 90 % dans les tests d'impact à faible vitesse à 9 et 15 joules d'énergie d'impact.
Recyclage et AIRPOXY 2
Bien que le recyclage ne soit pas abordé dans le projet AIRPOXY, CIDETEC a démontré que les déchets peuvent être broyés et remoulés, par exemple, en utilisant le moulage par compression à 210°C. Cependant, à l'instar du processus utilisé par Connora, les stratifiés 3R peuvent également être immergés dans une solution contenant un agent réducteur doux qui, comme l'explique Rekondo, « perturbe le réseau dynamique et dissout donc la résine, lui permettant d'être précipitée et récupérée comme une poudre. Elle note que ce processus de dissolution peut être accéléré en chauffant à des températures allant jusqu'à 100°C. « La poudre pourrait ensuite être réutilisée pour une deuxième application de composites, mais celle-ci est toujours en cours de recherche », explique Rekondo.
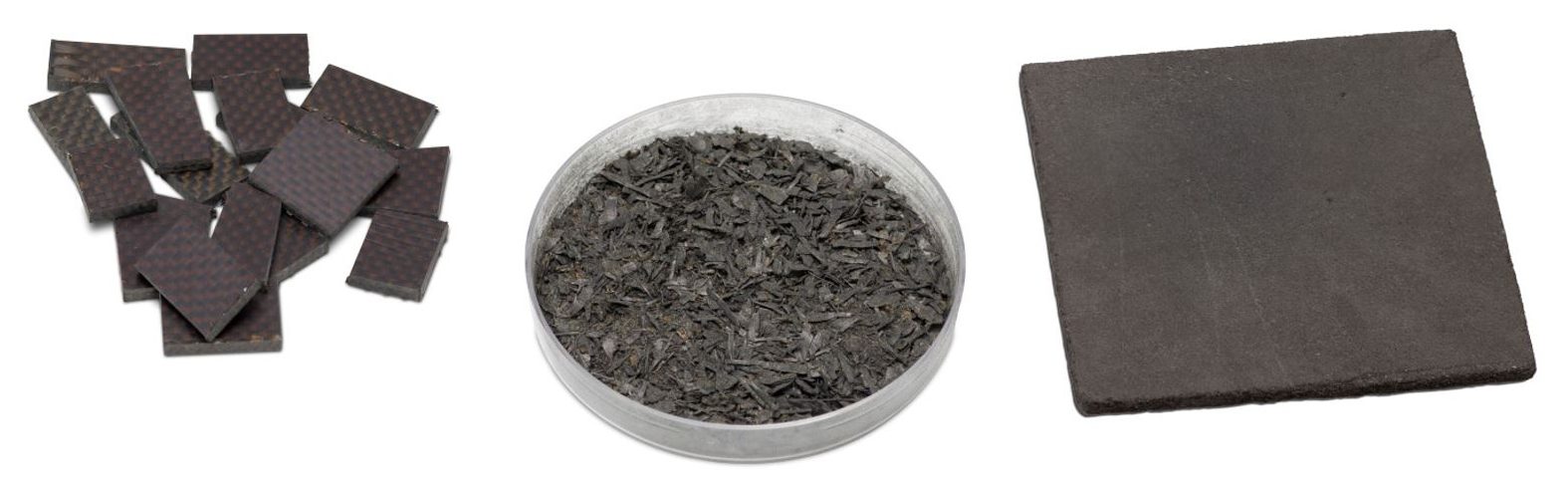
« Pour le recyclage des rebuts, nous pensons que deux à trois cycles seront possibles », poursuit-elle. « Mais pour les applications réelles en fin de vie, il y aura toujours une altération de la pièce et d'autres dégradations du matériau après avoir été en service pendant de nombreuses années. Dans ces cas, nous pensons qu'un seul recyclage sera possible. La deuxième application du matériau sera OK, mais probablement pas une troisième. Cela fait partie de ce que nous testons actuellement, d'abord pour les résines 3R de qualité industrielle, alors que nous terminons la caractérisation complète des matériaux 3R. »
Les deux démonstrateurs seront également achevés cette année, précise Markaide. «Nous procéderons ensuite à des tests mécaniques de ceux-ci, y compris des évaluations des dommages et des réparations. Notre objectif est d'atteindre le TRL 5 d'ici 2022. » Et maintenant quoi? « Nous prévoyons d'avoir un autre projet, AIRPOXY Part II », dit-elle, « pour poursuivre l'optimisation du traitement et poursuivre la caractérisation mécanique, ainsi que la validation et la certification des matériaux et des procédés. Nous aurons besoin d'un deuxième projet pour pousser la technologie sur le marché. »
La capacité de thermoformer et de souder des pièces aérospatiales en époxy semble une technologie pratiquement conçue pour la mobilité aérienne urbaine. "Nous devons maintenant réfléchir à la manière de fournir ce dont ces secteurs auront besoin", ajoute Markaide, notant qu'une feuille de route pour la commercialisation sera en effet l'un des livrables d'AIRPOXY Partie I. "Le recyclage est également une solution nécessaire qui n'est pas encore requise pour composites, mais ce sera dans le futur. Nous voulons être prêts."
Résine
- Prix en hausse pour les principaux volumes de résines
- Résines à base de PHA pour films soufflés, moulage par injection et thermoformage
- Résine pour le travail du bois et époxy
- Composites de graphène et polymères pour applications de supercondensateurs :une revue
- Sicomin fournit des résines époxy pour le concept de voiture volante ENATA Aerospace
- Hexion présente une solution époxy à deux composants pour la production de composites aérospatiaux
- AMRC et Prodrive s'associent pour faire progresser la fabrication de composants composites recyclables
- L'additif PES augmente la résistance à la rupture et aux microfissures dans les composites époxy
- Le consortium des composites thermoplastiques vise une production à haut volume pour l'automobile et l'aérospatiale