Plus la fonderie de votre grand-père
Les fonderies continuent d'évoluer en adoptant des technologies innovantes et la sécurité au travail
Une fonderie est une installation industrielle où le métal est fondu et coulé dans des formes spécifiques en le versant dans un moule. Le processus lui-même est vieux de plusieurs siècles. Aujourd'hui, environ 90 % de tous les produits manufacturés dépendent des pièces moulées en métal pour les composants, les voitures et les camions étant le plus grand marché. L'aluminium, le fer et l'acier sont les alliages les plus couramment traités dans les fonderies.

Histoire des fonderies
Depuis des générations, l'humanité a trouvé des moyens innovants d'utiliser les matières premières trouvées dans la nature - le travail des métaux fait partie de la civilisation depuis l'Antiquité. Un large éventail d'artefacts ont été découverts par les archéologues, des objets de culte aux outils et armes de guerre. En fait, les époques de l'histoire humaine ont été nommées d'après les progrès de la technologie des métaux :l'âge du cuivre, l'âge du bronze et l'âge du fer. Le plus ancien moulage connu trouvé par les historiens est une hache en cuivre, qui a été découverte enterrée avec une momie d'environ 3300 av. J.-C.
La fonderie et le four sont originaires de Mésopotamie et des régions d'Irak et de Syrie. Les pièces moulées en argile et les foyers chauds travaillaient pour fondre et façonner le cuivre, l'or et l'argent. Ces fonderies primitives fondaient le cuivre et étaient capables de créer des formes plus complexes, mais ce n'est qu'avec l'introduction de l'étain que le travail des métaux a fait une avancée significative. L'ajout d'étain a abaissé la température à laquelle les deux métaux fondaient et formaient le bronze, le premier alliage.
Au fil des siècles et des générations successives, diverses techniques de travail et de moulage des métaux se sont développées et se sont perdues, alors que différentes civilisations ont émergé pour dominer le paysage culturel et technologique. C'est au Moyen Âge que les procédés de coulée du métal dans les fonderies ont été documentés pour la première fois. Vannoccio Biringuccio (1480-1539) est connu comme le "père de l'industrie de la fonderie" puisqu'il est devenu l'auteur du premier manuel sur les fonderies, à partir duquel la technologie a été développée plus avant.
La première fonderie officielle était connue sous le nom de "Canon Shop", qui a été construite à Moscou en 1479. L'industrie de la fonderie de métaux des XIVe et XVe siècles en Europe est devenue connue pour la production de cloches, de canons et de boulets de canon en bronze et en fer.
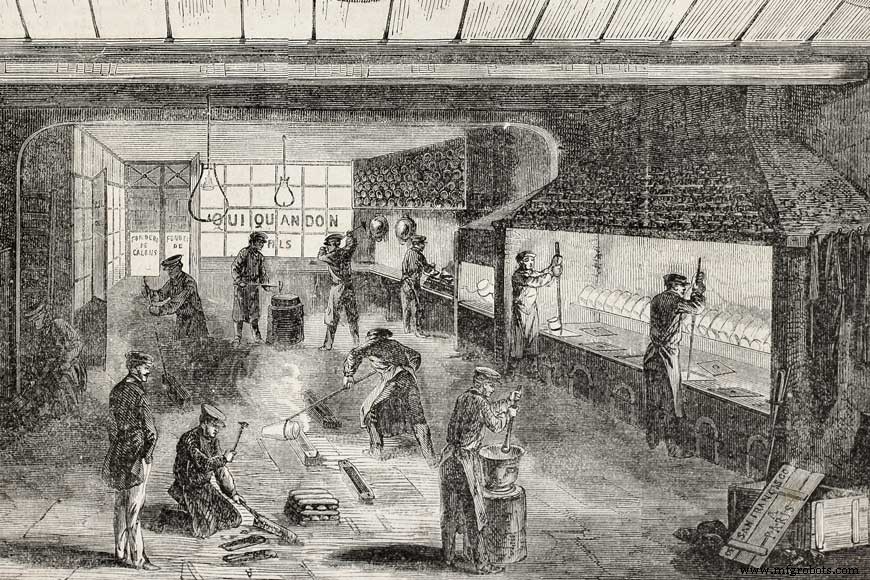
En Amérique du Nord, l'industrie de la coulée de métal s'est développée pour soutenir le progrès des colons à travers le Nouveau Monde. Des outils plus avancés et plus solides, des fers à cheval et des voies ferrées étaient nécessaires pour répondre à la demande des villes en développement.
Saugus Iron Works a été la première fonderie aux États-Unis et a été commandée en 1642 par des sidérurgistes européens. Établie à Lynn, dans le Massachusetts, elle est devenue le berceau de l'industrie sidérurgique américaine.
Développements dans la technologie de fonderie
Les procédés de fonderie évoluent en permanence pour améliorer la qualité des produits et l'efficacité de la production, et tirer parti des nouvelles technologies. Des percées dans le développement ont permis des avancées significatives dans le moulage des métaux à des moments clés de l'histoire de l'industrie.
Développements de fours
La migration du charbon vers le coke comme combustible pour les fonderies a été lancée par Abraham Darby. Son innovation en 1709 a conduit à une amélioration significative de l'efficacité et du coût, et a permis la construction de fours beaucoup plus grands qu'auparavant.
Cubilot four
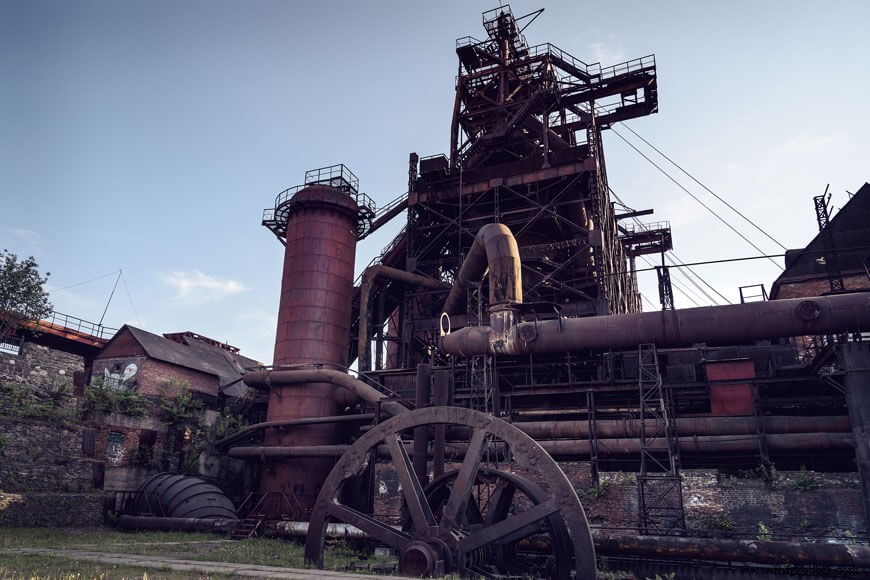
Le four à coupole a été développé en 1720 par le français René-Antoine Ferchault de Réaumur. La structure en forme de dôme a une ouverture pour alimenter la charge et des portes battantes à la base pour vider le four après l'arrêt. Un lit de coke supporte la charge de fondant de métal, de coke et de calcaire en fusion au-dessus des tuyères (ouvertures où l'air est fourni). Bien que le cubilot dominait autrefois le paysage de la fonderie, il a maintenant été largement remplacé par des fours à induction électrique et à arc électrique plus efficaces.
Processus creuset
Dans l'Angleterre du XVIIIe siècle, Benjamin Huntsman était l'entrepreneur à l'origine du développement du procédé du creuset. C'était le premier processus dans lequel l'acier pouvait être complètement fondu pour donner un produit uniforme après la coulée.
Four à arc électrique
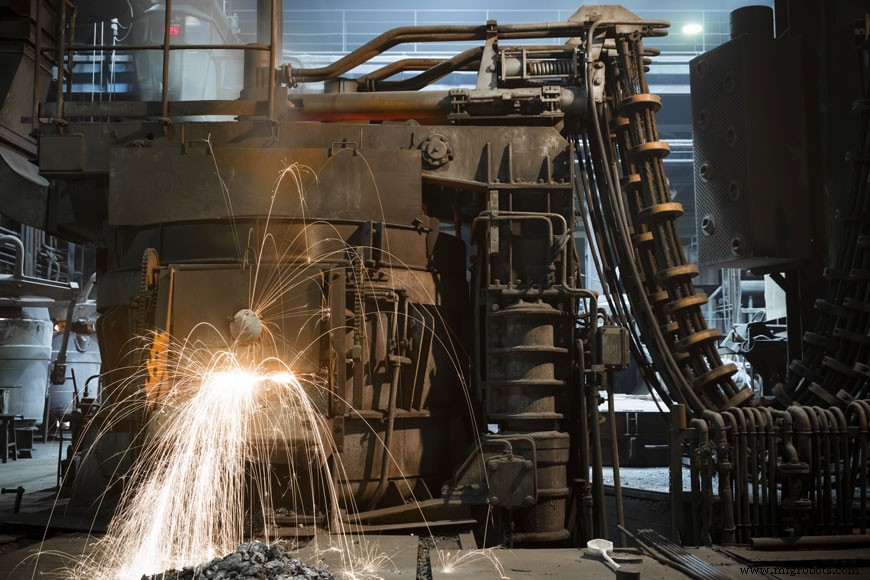
L'introduction de l'approvisionnement en électricité commerciale a contribué à l'invention des fours à arc électrique. Les électrodes en graphite créent l'arc électrique et fournissent le courant comme source d'énergie pour faire fondre le fer. Le premier four à arc électrique a été créé en 1900 par Paul Héroult de France. En 1907, une usine commerciale a été établie aux États-Unis. Ces fours sont plus économiques à des cadences de production plus faibles et peuvent fonctionner par intermittence, ce qui donne plus de flexibilité aux fonderies de métaux.
Four à induction électrique
Les fours à induction électrique utilisent un courant alternatif de haute puissance traversant une bobine pour induire des courants de Foucault dans le métal, générant ainsi de la chaleur, et se trouvent le plus souvent dans les fonderies de production aujourd'hui.
Développements de fonderie
Dans les temps anciens, la fonte des métaux se faisait dans des moules en argile. L'un des grands rois assyriens, Senacheribb, prétend avoir perfectionné la technique de coulée du bronze et du cuivre dans des moules en argile. Au fil du temps, les développements technologiques ont transformé le processus de moulage, du moulage au sable à la technologie électromagnétique.
Moulages au sable
Vannochio Birringucio, fondeur de la fin du XVe et du début du XVIe siècle, a écrit un livre sur toutes les formes de moulage et les travaux connexes. Le livre décrit l'utilisation des moulages au sable, la prochaine phase majeure de la technologie de moulage. Initialement, le sable était mélangé avec de l'argile comme agent liant afin que le moule conserve sa forme pendant la coulée, mais au fil du temps, de nouveaux types de sable et d'agents liants ont été développés.
Le sable vert est l'un des matériaux les plus couramment utilisés aujourd'hui. Historiquement, le sable vert était composé de sable siliceux, d'argile bentonite, d'eau et de charbon marin. Cependant, le charbon de mer n'est plus couramment utilisé aujourd'hui et a été remplacé par d'autres matériaux. Alors que le moulage au sable vert reste d'usage courant, les procédés « sans cuisson », à prise chimique ou à prise à froid deviennent prédominants dans les fonderies d'aujourd'hui.
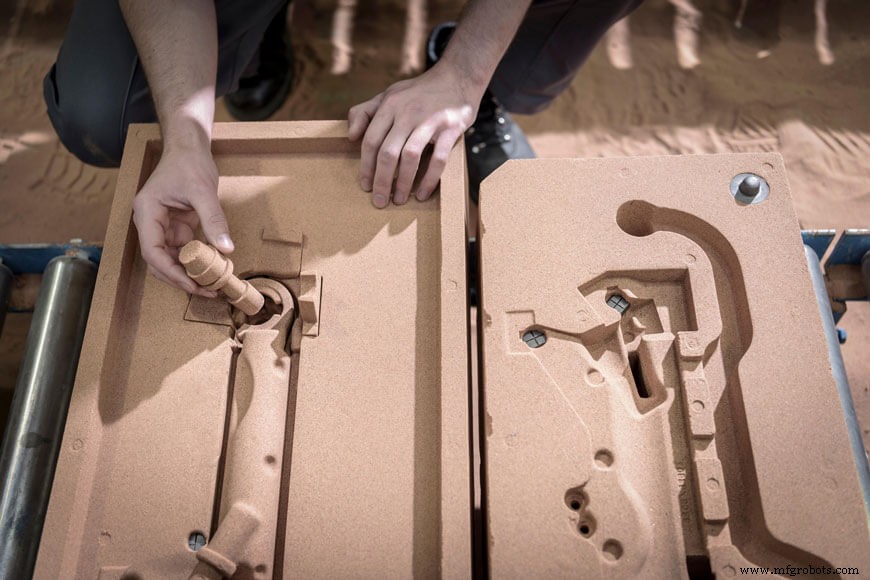
Moulage sous pression
Le moulage sous pression et le moulage de précision sont des techniques modernes utilisant des matériaux nouvellement disponibles pour améliorer la qualité de la finition du moulage et le coût de production. Le moulage sous pression se caractérise par le forçage du métal en fusion sous haute pression dans une cavité de moule. Une machine à chambre chaude ou froide est utilisée selon le type de métal coulé. Les moulages sous pression sont connus pour fournir une bonne finition de surface et une cohérence dimensionnelle.
Diffusion continue
L'avancée la plus significative dans le processus de coulée a peut-être été l'introduction de la machine de coulée continue. Le métal en fusion est versé dans un moule et retiré lentement pour créer des longueurs continues de métal solidifié. Le principal avantage de cette méthode de coulée d'acier au carbone est l'élimination de certaines des étapes de traitement en aval. Ces produits semi-finis peuvent être plus facilement transformés en produits finis par laminage.
Moules permanents
Au 21e siècle, les processus de moulage ont fait un autre bond en avant grâce à l'introduction de la technologie électromagnétique. Une bobine d'induction est enroulée autour d'un moule refroidi à l'eau avec un courant alternatif générant des champs électromagnétiques.
Ces champs électromagnétiques traversent le métal en refroidissement, provoquant la formation de courants de Foucault dans le métal en fusion, ce qui entraîne deux résultats positifs :
- Le contact entre le métal de refroidissement et la surface du moule est "doux" donnant une meilleure qualité de finition. Dans la coulée standard refroidie à l'eau, une peau épaisse de microstructure grossière se forme en raison du contact "dur" avec le moule. Cette peau est broyée avant le laminage, ce qui entraîne un gaspillage important de produit et une augmentation des coûts.
- L'homogénéité du métal est grandement améliorée avec une réduction des ségrégations aux joints de grains.
Développements de qualité
Sir Henry Bessemer a été l'innovateur à l'origine de nouvelles techniques pour éliminer le carbone et l'excès d'oxygène de l'acier fondu qui ont abouti à l'invention du convertisseur. Bessemer a découvert que le soufflage d'oxygène à travers le métal en fusion provoquait une réaction avec le carbone et le silicium dans le matériau, éliminant les impuretés mais chauffant également le matériau pour faciliter le coulage.
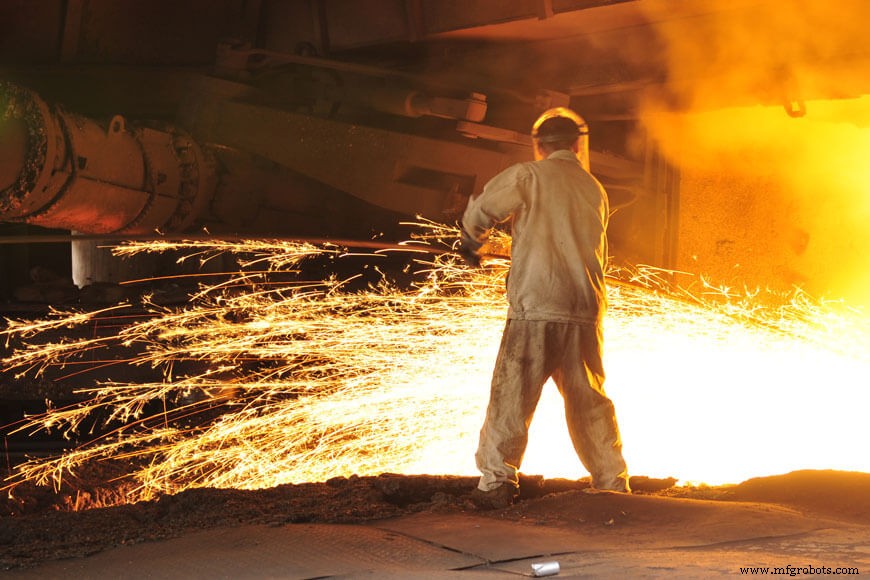
Les convertisseurs sont maintenant utilisés pour des degrés fins de contrôle de la qualité en définissant des ratios précis de teneur en carbone et en ajoutant des alliages et d'autres additifs pour les propriétés spécifiques du produit requises. Dans un four à arc électrique, de l'oxygène peut être injecté dans le bain pour "brûler" le carbone et de nombreux autres éléments et impuretés. Cela rend le bain initial aussi propre que possible et permet à la fonderie d'allier la masse fondue à la teneur parfaite. Dans la fusion par induction, la fonderie ne peut commencer qu'avec un bain créé à partir de l'alimentation ou de la ferraille fondue. Le contenu chimique de la ferraille doit correspondre à la chimie du bain que la fonderie utilise initialement.
Développements mesure et contrôle
Couplé aux progrès des méthodes de production, il y a eu des progrès dans les méthodes d'essai en laboratoire du métal en fusion alors que la fabrication est toujours en cours. Des échantillons peuvent être prélevés dans des convertisseurs et analysés à l'aide de spectromètres ou d'analyses par fluorescence X. Cette rétroaction en temps réel de la composition chimique crée une opportunité pour les fabricants de faire des ajustements avant de couler, ce qui permet d'économiser du temps et des ressources précieux en raison des retouches.
Bien qu'un opérateur expérimenté puisse détecter à l'œil nu les défauts de surface et les défauts potentiels du produit coulé, l'amélioration des méthodes de contrôle non destructif a donné aux clients une plus grande sécurité dans l'intégrité du produit :
- Le colorant pénétrant et la poudre fluorescente peuvent être mis en suspension dans de l'huile pénétrante et appliqués sur la surface du moulage fini. Les fissures et les défauts de surface sont immédiatement visibles lors de l'application du révélateur ou en présence de lumière ultraviolette.
- L'inspection radiographique est la méthode la plus efficace pour identifier les trous internes, les fissures ou les inclusions. Le plâtre est exposé au rayonnement d'un tube à rayons X et l'image créée sur le film radiographique indique les changements de densité du moulage. L'avantage de cette méthode est que la radiographie sert d'enregistrement permanent, qui peut accompagner le produit tout au long de son cycle de vie pour le contrôle de la qualité et de la sécurité.
- L'inspection par ressuage liquide (LPI) peut détecter de minuscules fissures, pores ou autres imperfections de surface dans les pièces moulées ferreuses et non ferreuses qui sont difficiles à voir à l'œil nu. LPI utilise une solution d'huile colorante colorée sur la surface de la pièce moulée qui se retrouve dans les défauts de surface. Une fois qu'un révélateur spécial est appliqué, les défauts deviennent clairement visibles.
- L'inspection des particules magnétiques (MPI) aide à identifier l'emplacement des discontinuités de surface dans les métaux ferreux. Cela peut également indiquer des défauts sous la surface si la force de magnétisation est suffisante pour produire un champ de fuite à la surface. Dans ce test, un flux magnétique est induit dans un matériau ferromagnétique. Toute discontinuité abrupte dans son trajet se traduit par un champ de fuite de flux local. Si des particules finement divisées de matériau ferromagnétique sont amenées à proximité, elles offrent un chemin à faible réluctance vers le champ de fuite et prennent une position qui délimite approximativement ses limites effectives. La pièce moulée à inspecter est magnétisée et sa surface saupoudrée de poudre magnétique. Un courant d'air à faible vitesse expulse l'excès de poudre, laissant le défaut délimité par les particules de poudre restantes. La poudre peut être appliquée pendant que le courant magnétisant circule (méthode continue) ou après que le courant est coupé (méthode résiduelle). Il peut être appliqué sec ou en suspension, dans un distillat léger de pétrole similaire au kérosène.
Inspection des particules magnétiques
L'inspection par particules magnétiques (MPI) est un type de test non destructif qui utilise le flux magnétique pour déterminer les défauts de surface. Regardez un ouvrier effectuer des tests non destructifs sur une soudure pétrolière et gazière.
- Les tests par ultrasons (UT) identifient les défauts internes par le son en utilisant une énergie acoustique à haute fréquence qui est transmise dans un moulage. L'UT permet d'étudier la section transversale d'un moulage et est donc considérée comme une méthode d'inspection volumétrique. L'énergie acoustique à haute fréquence traverse le moulage jusqu'à ce qu'elle touche la surface, l'interface ou le défaut opposé. L'interface ou le défaut reflète des parties de l'énergie qui sont collectées dans une unité de réception et affichées pour que l'analyste puisse les voir. Le modèle de déviation d'énergie peut indiquer l'emplacement et la taille d'un défaut interne, ainsi que l'épaisseur de paroi et le nombre de nodules de fonte ductile. L'UT nécessite des connaissances et de l'expérience pour une interprétation précise des résultats, ce qui augmente le coût de l'inspection.
Évolution de la sécurité
Travailler dans une fonderie est un métier dangereux. Il existe de nombreux risques chimiques, mécaniques et thermiques qui doivent être contrôlés afin d'éliminer les risques potentiels pour les travailleurs.
L'un des principaux domaines qui a amélioré la sécurité des travailleurs est la mécanisation de l'industrie.
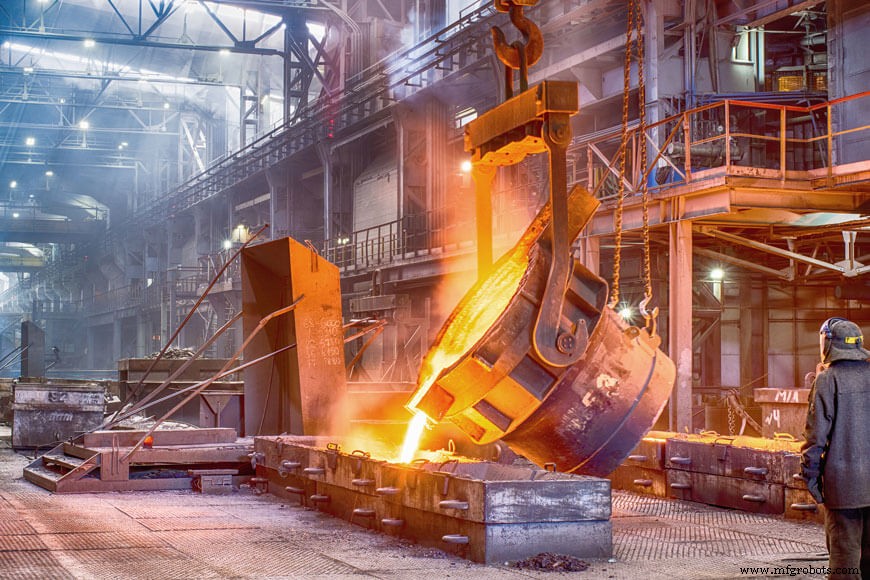
Auparavant, les poches étaient malmenées, ramassées et déplacées sur le site de la fonderie. Des poches à engrenages ont ensuite été introduites, ce qui a permis à un opérateur de faire fonctionner et de contrôler la poche à distance plutôt que de se tenir à côté du récipient de métal en fusion. Des grues ont été introduites pour soulever les poches de coulée en position pour le coulage, mais le bruit de l'environnement de production et les contraintes de ligne de vue signifiaient toujours que les grutiers étaient susceptibles de provoquer des incidents. Les grues de processus sont le dernier développement où les poches de coulée fonctionnent sur des pistes prédéfinies avec des ascenseurs, éliminant ainsi le risque qu'un opérateur se trouve sur le chemin de la poche en mouvement dans des conditions de fonctionnement normales.
L'avenir des fonderies
Tendances technologiques futures
L'efficacité est la principale motivation des avancées technologiques dans les fonderies. L'accent est mis sur la réduction de la consommation d'énergie en raison de l'accent mis sur la fabrication durable, ainsi que sur la réduction des coûts associée. Une main-d'œuvre réduite dans les fonderies réduira également le risque de blessures et optimisera la production.
Les améliorations de l'automatisation et un mouvement vers les simulations informatiques, telles que les logiciels de simulation de solidification, réduiront la dépendance de l'industrie de la fonderie vis-à-vis de la main-d'œuvre et amélioreront la précision et l'efficacité. La simulation de procédés assistée par ordinateur offre des modèles de procédés qui sont maintenant suffisamment matures. Cela permet aux ingénieurs de fonderie d'utiliser le monde virtuel pour se préparer au monde réel, minimisant ainsi le nombre d'itérations d'essai.
La machine à mesurer tridimensionnelle (MMT) apporte un nouveau niveau de mesure de précision à l'atelier de l'industrie de l'usinage. L'inspection des trous, des fentes, des pièces soudées et des déformations peut être effectuée rapidement, ce qui réduit considérablement le temps de cycle. Les données numérisées sont ensuite combinées avec les résultats tactiles dans des rapports graphiques pour une interprétation facile. Le CMM est une force motrice pour augmenter la productivité et fournir des informations pratiques.
Tendances futures du marché
Le marché de la fonderie a été dominé au cours de la dernière décennie par la consolidation en grands conglomérats. Les économies d'échelle sont un moteur clé de cette tendance et se poursuivront probablement dans un avenir prévisible. Les opérations plus petites et moins efficaces continueront de fermer en raison de la compétitivité du marché.
Tendances futures en matière d'environnement et de sécurité
Le recyclage des métaux est l'une des réussites du développement durable, mais il reste nécessaire de développer l'utilisation durable d'autres produits impliqués dans le processus de moulage des métaux. De nouvelles façons d'utiliser les scories et les sables de moule épuisés continueront d'être identifiées et explorées pour suivre les progrès constants de la réglementation contre l'élimination des déchets.
Les progrès rapides de la technologie robotique ont ouvert des portes pour réduire l'exposition des humains à des situations dangereuses. Les innovateurs en technologie robotique pour les environnements industriels développent des cellules de travail robotisées entièrement automatisées et ne nécessitant aucune intervention humaine sur le chantier.
Les fonderies et leur évolution continue
La coulée de métal fait partie de la société humaine depuis l'Antiquité et son utilisation et ses progrès ne font que croître de jour en jour.
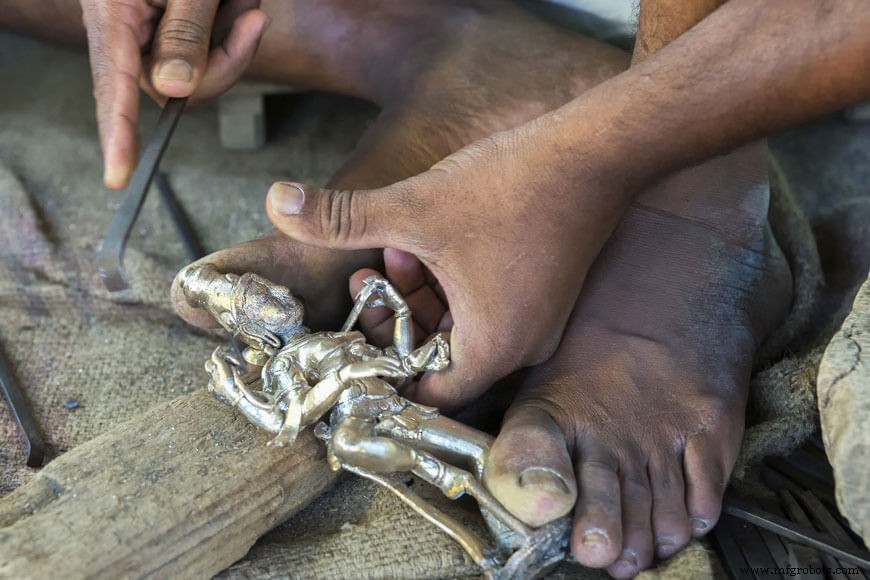
Aujourd'hui, les produits en métal coulé affectent nos vies de multiples façons. Les pièces automobiles, les ustensiles de cuisine, les outils et de nombreux autres produits d'usage quotidien sont tous issus des processus de fabrication des fonderies.
Au fil des siècles, la technologie a fait des progrès spectaculaires pour améliorer la cohérence et le contrôle de la qualité des produits en métal coulé, tout en améliorant la sécurité au travail des travailleurs et en réduisant les coûts grâce à une plus grande efficacité. Une étude de l'histoire des fonderies révèle des entrepreneurs, des ingénieurs, des innovateurs et des solutionneurs de problèmes exceptionnels qui ont chacun joué un rôle dans le développement de cette industrie.
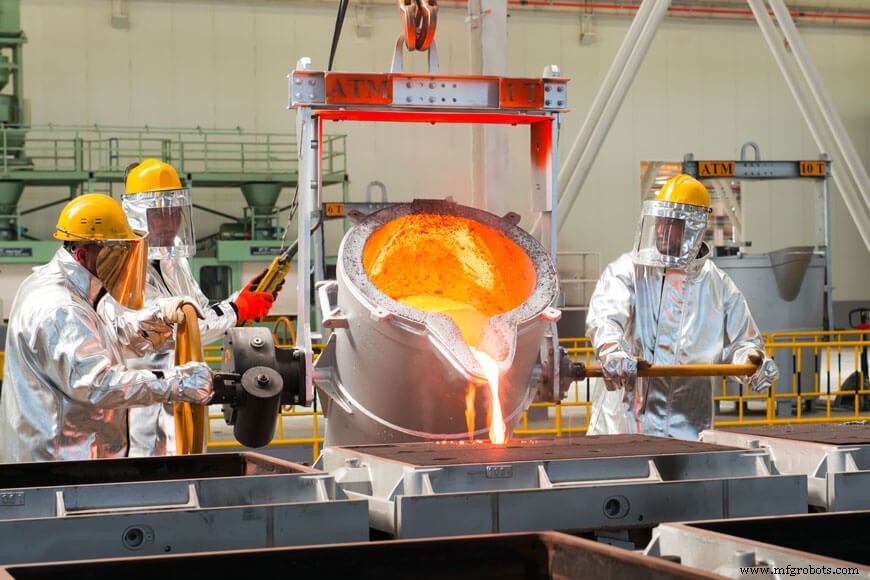
Les pressions économiques du marché mondial continuent de créer un environnement qui récompense l'innovation, la cohérence et l'efficacité. Les prochaines décennies ne manqueront pas de produire de nouvelles technologies passionnantes telles que l'utilisation des mégadonnées et de la robotique, et de nouveaux modèles commerciaux par le biais de fusions et de mises à niveau. Les tendances mondiales en faveur de la fabrication durable continueront d'entraîner des améliorations environnementales et de sécurité dans l'industrie, ce qui profitera aux travailleurs et aux communautés.
Références
- Pièces moulées industrielles en métal. « Histoire de la fonte des métaux »
- Le dictionnaire gratuit. "Industrie de la fonderie"
- Fonderie Waupaca. "Historique de la fonte des métaux"
- Service des parcs nationaux des États-Unis. "Lieu historique national de Saugus Iron Works"
- Encyclopédie Britannica. "Four cubilot"
- La Fondation américaine pour les études syriaques. "Le contexte de l'invention dans le monde antique"
- L'institut du fer et de l'acier du Japon. "Technologie sidérurgique depuis 100 ans"
- Société américaine de fonderie. "Les castings dans notre monde"
- Technologies des métaux. "Histoire de la fonderie métallique"
- AMAG. "La technologie EMC améliore la qualité et la rentabilité"
- T. P. Moulages. "Industrie de la fonderie :bref historique et définition"
Processus de fabrication
- Guillotine
- Silicium
- Charnières pour vos armoires en tôle
- 5 façons d'améliorer vos pièces de tôlerie
- 5 façons de rendre vos pièces métalliques résistantes à la corrosion
- Votre guide du processus de cisaillement de la fabrication des métaux
- 5 questions importantes à poser à votre fournisseur de métal
- Comment prévenir la corrosion dans votre équipement métallique
- Comment utiliser votre perceuse pour percer le métal