Qu'est-ce que le moulage au sable ?
Comment former des moulages complexes avec des moules en sable
Moulage au sable est un processus qui utilise des moules en sable non réutilisables pour former des pièces moulées en métal. D'une part, le moulage est un processus de fabrication d'une simplicité trompeuse :quiconque a formé des châteaux sur la plage sait que le sable peut être utilisé pour créer des formes détaillées. Cependant, dans une fonderie, traitant de la chaleur du métal en fusion, de nombreux facteurs doivent être pris en compte pour réussir. Le moulage est utilisé pour fabriquer des composants métalliques de toutes tailles, allant de quelques onces à plusieurs tonnes. Des moules en sable peuvent être formés pour créer des pièces moulées avec des détails extérieurs fins, des noyaux intérieurs et d'autres formes. Presque tous les alliages métalliques peuvent être coulés au sable. Les creux sont faits dans du sable humidifié, remplis de métal en fusion et laissés refroidir.
Qu'est-ce que le sable de moulage ?
Le sable de moulage présente trois avantages importants par rapport aux autres matériaux de moulage :
- c'est peu coûteux,
- il est facilement recyclable, et
- il peut résister à des températures extrêmement élevées.
Le moulage au sable est l'un des rares procédés disponibles pour les métaux à haute température de fusion tels que les aciers, le nickel et le titane. En raison de sa flexibilité, de sa résistance à la chaleur et de son coût relativement faible, le moulage au sable est le procédé de moulage le plus largement utilisé.
Les pièces moulées sont produites en versant du métal liquide dans une cavité de moule. Pour qu'une coulée soit réussie, la cavité du moule doit conserver sa forme jusqu'à ce que le métal soit refroidi et complètement solidifié. Le sable pur se désagrège facilement, mais le sable de moulage contient un matériau de liaison qui augmente sa capacité à résister à la chaleur et à conserver sa forme.
Sable vert (un agrégat de sable, de charbon pulvérisé, d'argile de bentonite et d'eau) a traditionnellement été utilisé dans le moulage au sable, mais les systèmes de moulage à liaison chimique modernes deviennent de plus en plus populaires. Le sable de coulée le plus utilisé est la silice (SiO2 ).
Propriétés du sable de moulage
Force
La capacité du moule en sable à conserver sa forme géométrique dans des conditions de contraintes mécaniques.
Perméabilité
La capacité d'un moule en sable à permettre l'échappement des gaz et de la vapeur pendant le processus de coulée.
Teneur en humidité
La teneur en humidité affecte la résistance et la perméabilité d'un moule :un moule avec trop peu d'humidité peut se briser, tandis qu'un moule avec trop d'humidité peut entraîner l'emprisonnement de bulles de vapeur dans le moulage.
Fluxabilité
La capacité du sable à remplir de petites cavités dans le motif. Une fluidité élevée crée un moule plus précis et est donc utile pour les moulages détaillés.
Taille des grains
La taille des particules individuelles de sable.
Forme du grain
Cette propriété évalue la forme des grains de sable individuels en fonction de leur rondeur. Généralement, trois catégories de grains sont utilisées dans le sable de fonderie :
- Grain arrondi les sables offrent une force de liaison relativement faible, mais une bonne fluidité et une bonne finition de surface.
- Grains angulaires ont une plus grande force de liaison en raison de l'emboîtement, mais une fluidité et une perméabilité plus faibles que les sables à grains arrondis.
- Grains subangulaires sont la voie du milieu. Ils possèdent une meilleure résistance et une perméabilité inférieure par rapport aux grains arrondis, mais une résistance inférieure et une meilleure perméabilité que les grains anguleux.
Réductibilité
La capacité du mélange de sable à s'effondrer sous la force. Une plus grande capacité d'écrasement du moule permet au métal coulé de se rétracter librement à mesure qu'il se solidifie, sans risque de déchirure ou de fissuration à chaud.
Résistance réfractaire
Le moule ne doit pas fondre, brûler ou se fissurer lorsque du métal en fusion y est versé. La résistance réfractaire mesure la capacité du sable de moulage à résister à une chaleur extrême.
Réutilisabilité
La capacité du sable de moulage à être réutilisé (après le conditionnement du sable) pour produire d'autres moulages au sable lors d'opérations de fabrication ultérieures.
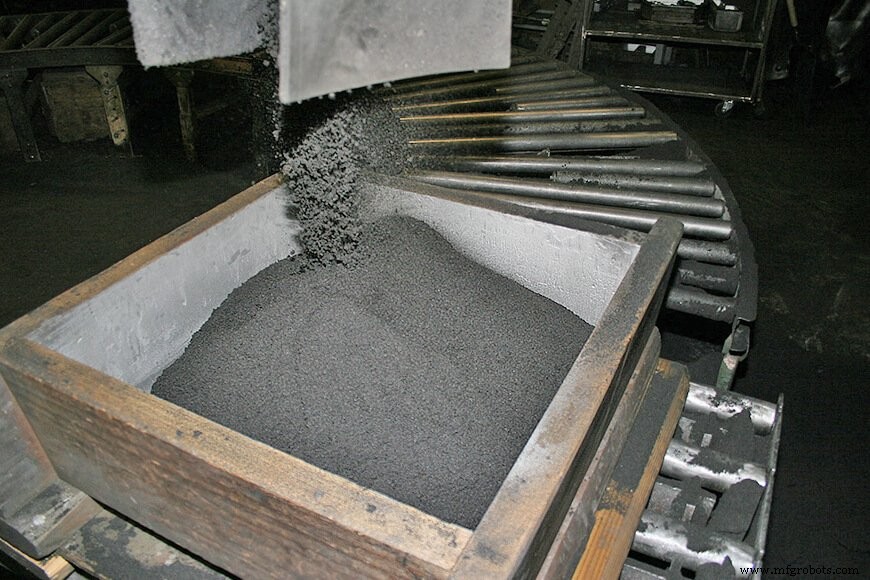
De nombreuses propriétés du sable de moulage dépendent de la granulométrie et de la répartition des particules de sable :une petite granulométrie améliore la résistance du moule, mais une grande granulométrie est plus perméable. Le sable à grain fin donne aux pièces moulées une bonne finition de surface, mais possède une faible perméabilité, tandis que le sable à grain grossier fournit le contraire.
Additifs spéciaux ou liants peut être ajouté à l'agrégat de base de sable, d'argile et d'eau pour augmenter la cohésion. Ces liants peuvent être organiques ou inorganiques. Les liants courants comprennent les céréales, le brai moulu, le charbon marin, la gilsonite, le mazout, la farine de bois, la farine de silice, l'oxyde de fer, la perlite, la mélasse, la dextrine et des matériaux exclusifs.
Trouver la combinaison parfaite n'est pas facile. Certaines propriétés d'un agrégat de sable sont contradictoires :un sable de moulage avec une plus grande aptitude à l'écrasement a moins de résistance, et un autre avec une plus grande résistance a moins d'aptitude à l'écrasement. Des compromis sont souvent nécessaires pour parvenir à un compromis qui offre des propriétés appropriées pour la pièce spécifique et l'application de fonderie. Le contrôle précis des propriétés du sable de moulage est si essentiel que les laboratoires de sable sont devenus un ajout courant aux fonderies modernes.
Parties d'un moule de moulage au sable
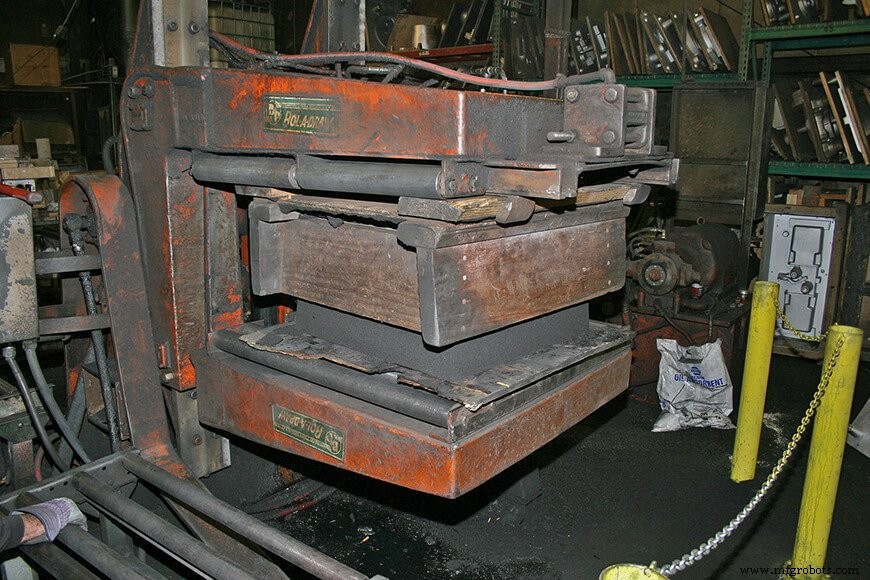
Une coulée de métal est façonnée par le moule utilisé pour la produire - un bon moule est une condition préalable à une bonne coulée. Les moules ont plusieurs parties qui fonctionnent ensemble pour influencer le produit final.
La cavité du moule est façonnée par le motif , un modèle grandeur nature de la pièce qui s'imprime dans le moule en sable. Certaines surfaces internes ne sont pas incluses dans le motif et seront plutôt créées par des noyaux séparés.
Un noyau est une forme de sable insérée dans le moule pour façonner l'intérieur de la coulée, y compris des caractéristiques telles que des trous ou des passages. Les noyaux sont généralement fabriqués à partir de sable de moulage afin qu'ils puissent être secoués hors du moulage. Une impression de base est une région ajoutée au motif, au noyau ou au moule pour localiser et soutenir le noyau dans le moule.
Un support de base supplémentaire est fourni par les chaplets – de petites pièces métalliques fixées entre le noyau et la surface de la cavité. Afin de maintenir ce support, les chapelets doivent être composés d'un métal ayant une température de fusion identique ou supérieure à celle du métal coulé. Après solidification, les chapelets auront été emboîtés à l'intérieur du moulage.
Les noyaux de sable peuvent être produits en utilisant plusieurs des mêmes méthodes que les moules en sable :comme les moules sont façonnés par un motif, les noyaux de sable sont façonnés par une boîte à noyau; ils ressemblent à un dé et peuvent être en bois, en plastique ou en métal. Les boîtes à noyaux peuvent également contenir plusieurs cavités pour produire plusieurs noyaux identiques.
Une contremarche est un vide supplémentaire dans le moule conçu pour contenir l'excès de métal. Il empêche la formation de vides de retrait dans la pièce moulée principale en alimentant le métal en fusion dans la cavité du moule au fur et à mesure qu'il se solidifie et se rétracte.
L'ensemble du moule en sable est contenu dans une boîte appelée flacon . Dans un moule en deux parties, typique des moulages au sable, la moitié supérieure (contenant la moitié supérieure du modèle, du flacon et du noyau) est appelée chape . La moitié inférieure s'appelle le glisser . La ligne de séparation est la ligne ou la surface qui sépare le grugeage et la traînée.
Comment faire un moulage au sable
Le moulage au sable comprend quatre étapes de base :assembler le moule en sable, verser le métal liquide dans le moule, laisser refroidir le métal, puis casser le sable et retirer le moulage. Bien sûr, le processus est plus complexe qu'il n'y paraît.
La première étape de l'assemblage du moule consiste à remplir partiellement la traînée de sable. Le motif, l'impression du noyau, les noyaux et le système de déclenchement sont placés près de la ligne de séparation. La chape est ensuite assemblée à la drague. Du sable supplémentaire est versé sur la moitié de la chape jusqu'à ce que le motif, le noyau et le système de porte soient recouverts, puis le sable est compacté par vibration ou par des moyens mécaniques. L'excès de sable est enlevé à l'aide d'une barre à araser.
Maintenant que le moule est formé, la chape est retirée de la traînée afin que le motif puisse être extrait du moule.
L'extraction du modèle est effectuée avec soin pour éviter de casser ou de déformer la cavité de moule nouvellement formée. Ceci est facilité par la conception d'un projet :un cône vertical perpendiculaire au plan de joint. La conicité du tirant d'eau est généralement d'au moins 1°. Plus la surface du motif est rugueuse, plus l'ébauche à fournir est importante.
Avant de pouvoir être rempli de métal liquide, le moule complet doit être préparé; la cavité du moule est souvent lubrifiée avec des lavages de moule pour faciliter le retrait de la coulée. Ensuite, les noyaux sont positionnés, des matériaux de moule supplémentaires tels qu'une corde de chape sont ajoutés pour aider à prévenir les faux-ronds, et les moitiés de moule sont fermées et solidement serrées ensemble ; les sections de chape et de traînée maintiennent un alignement correct à l'aide de broches et de guides.
Les moitiés de moule doivent rester sécurisées afin que le métal liquide ne puisse pas fuir à travers la ligne de séparation. Avant de couler des moules sans flacon, des vestes de coulée en bois ou en métal sont souvent placés autour du moule et des poids sont placés sur le dessus pour empêcher la chape de se soulever.
Le métal en fusion pénètre dans la cavité du moule par un système de porte :le métal en fusion est versé dans un moule via le gobelet verseur , continue dans la grappe (la partie verticale du système de vanne), puis à travers les glissières (parties horizontales). Les gaz accumulés et l'air déplacé s'échappent par les ventilations . Les multiples points où le métal est introduit dans la cavité du moule à partir des canaux sont appelés les portes .
Une fois la pièce coulée refroidie, elle est extraite du moule en sable. Le processus d'élimination du sable des pièces moulées est appelé shakeout . Le moulage peut être retiré manuellement ou par des machines automatisées. Les tables d'agitation et les culbuteurs rotatifs sont couramment utilisés.
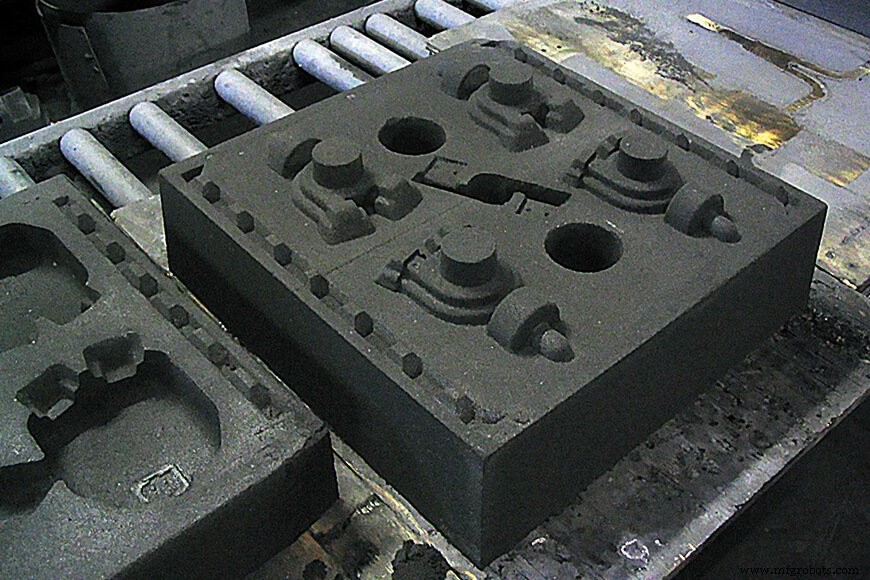
Il existe des variantes à ce processus de base en fonction du modèle, du type de flacon et du niveau de mécanisation :
- Moulure de banc est préféré pour les petits travaux. L'ensemble de l'opération s'effectue sur un banc de hauteur convenable.
- Moulure de sol est utilisé pour les travaux de taille moyenne et grande. Comme son nom l'indique, le moule est posé sur le sol avant le coulage.
- Moulage mécanique est utilisé pour la production de masse. Le moulage à la machine permet d'économiser du travail et offre une précision et une uniformité supérieures, ce qui permet de maintenir des tolérances dans des limites étroites à un rythme rapide. Les principales opérations effectuées par les machines de moulage sont le pilonnage du sable de moulage, le roulage sur le moule, la formation de la porte, le frappement du modèle et son retrait.
Recyclage du sable de moulage
Une fois que le sable a été secoué d'une coulée complète, les morceaux sont refroidis et broyés. Toutes les particules et granulés métalliques sont éliminés, souvent à l'aide d'un champ magnétique. Tous les sables et constituants sont criblés avec des agitateurs, des cribles rotatifs ou des cribles vibrants. Le sable nettoyé peut ensuite être réintroduit au début du cycle de production du sable de moulage.
Les sables de moulage sont préparés dans des broyeurs, qui mélangent le sable, l'agent de liaison et l'eau. Les aérateurs sont utilisés conjointement pour détacher le sable afin de le rendre plus propice au moulage.
Le sable préparé est livré au sol de moulage, généralement par des camions à godet ou par des convoyeurs à bande, où il est façonné en moules; les moules peuvent être posés au sol ou amenés par des convoyeurs à un poste de coulée. Après le coulage, les moulages sont retirés du sable adhérant à une station de décochage. Le sable utilisé, à son tour, est renvoyé dans les bacs de stockage par un convoyeur à bande ou par d'autres moyens.
Le sable de moulage est généralement recyclé et réutilisé dans de nombreux cycles de production. Selon les estimations de l'industrie, environ 100 millions de tonnes de sable sont utilisées chaque année dans la production. De ce nombre, seulement quatre à sept millions de tonnes sont jetées, et même ce sable est souvent recyclé par d'autres industries.
Processus et méthodes de moulage au sable
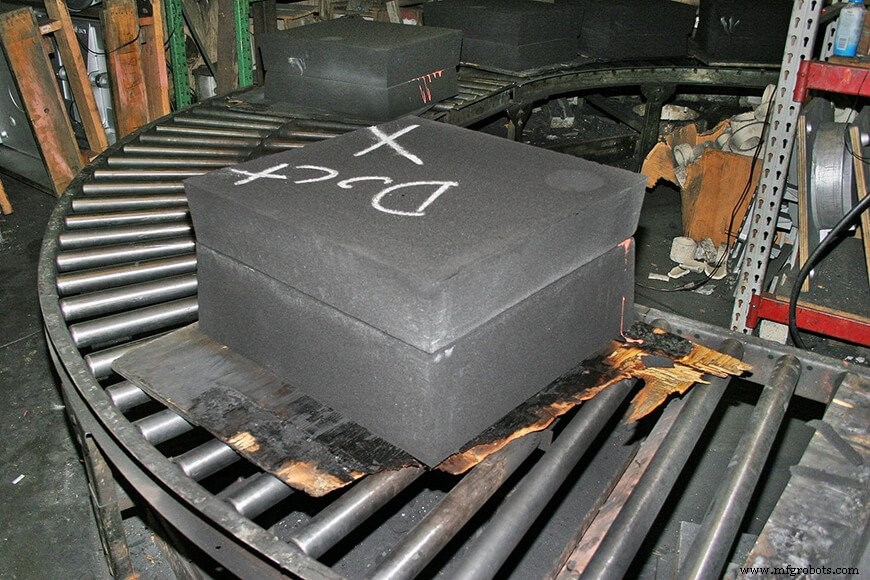
Moules de sable vert
Un mélange de sable vert typique contient 89 % de sable, 4 % d'eau et 7 % d'argile. Le sable vert est un favori de l'industrie en raison de son faible coût et de ses performances globales solides. Le "vert" dans le sable vert fait référence à la teneur en humidité présente dans le mélange lors de la coulée.
Les moules en sable vert ont une résistance suffisante pour la plupart des applications de moulage en sable. Ils offrent également une bonne capacité de pliage, de perméabilité et de réutilisation. Les principales difficultés proviennent de la teneur en humidité. Trop d'humidité peut provoquer des défauts dans le moulage, la tolérance à l'humidité dépendant du métal coulé.
Processus de prise à froid
Parfois, des liants non traditionnels sont utilisés dans le moulage au sable industriel. Les liants de coulée conventionnels nécessitent de la chaleur pour durcir, tandis que ces liants alternatifs se lient chimiquement à température ambiante lorsqu'ils sont mélangés avec du sable - d'où le terme processus de prise à froid. Techniquement avancés, ces procédés de moulage au sable relativement récents gagnent en popularité. Les processus de prise à froid sont plus coûteux que les moules en sable vert, mais ils produisent des pièces moulées avec une précision dimensionnelle exceptionnelle.
Moulage de coque
Le moulage en coquille est une invention relativement récente dans les techniques de moulage pour la production de masse et la finition lisse; il a été utilisé pour la première fois par l'Allemagne pendant la Seconde Guerre mondiale. Le matériau de moulage est un mélange de sable de silice sec et fin avec une teneur minimale en argile et de 3 à 8 % de résine thermodurcissable (phénol formaldéhyde ou graisse de silicone). Lorsque le mélange de moulage tombe sur la plaque-modèle chauffée, une coque dure d'environ 6 mm d'épaisseur se forme. Afin de durcir complètement la coquille, elle doit être chauffée à 440 à 650 °F (230 à 350 t) pendant plusieurs minutes.
Services de casting personnalisés
Reliance Foundry travaille en collaboration avec les clients pour concevoir le modèle et la méthode de moulage pour chaque moulage personnalisé. Demandez un devis pour obtenir plus d'informations sur la façon dont notre service de moulage peut répondre aux exigences de votre projet.
Articles connexes
- Guide de casting détaillé :série La vie d'un casting
- Société américaine de fonderie. "Processus de moulage au sable".
Crédits images
- Remplissage de la boîte de moule :OKFoundry, CC BY 2.0, via Flickr
- Cope tirée d'une boîte à moules :OKFoundry, CC BY 2.0, via Flickr
- Moule à sable ouvert :OKFoundry, CC BY 2.0, via Flickr
- Moule fermé :OKFoundry, CC BY 2.0, via Flickr
Processus de fabrication
- Qu'est-ce que le moulage de moules non consommables ?
- Qu'est-ce que le sable tranchant ?
- Qu'est-ce qu'un écran de sable ?
- Sable vert vs moulage au sable résine
- Moulage au sable vs forgeage
- Qu'est-ce que le moulage au sable ?
- Types d'équipement de moulage au sable
- Introduction à la terminologie du moulage au sable
- Qu'est-ce que le casting CI ?