Cinq conseils de conception pour la coulée d'uréthane
La coulée d'uréthane est un processus de fabrication traditionnel polyvalent qui utilise un modèle maître imprimé en 3D et un moule en silicone pour créer des pièces en plastique d'utilisation finale. Pendant le processus de coulée d'uréthane, le modèle principal est placé à l'intérieur d'une boîte scellée, recouvert de silicone liquide, puis durci. Une fois le silicone durci, un fabricant le coupe en deux pour libérer le modèle principal - à ce stade, le moule en uréthane coulé est prêt à l'emploi.
Pour créer des pièces moulées en uréthane sur mesure, les ingénieurs versent de la résine de coulée d'uréthane - généralement un matériau en polyuréthane qui peut imiter les propriétés physiques du plastique utilisé dans le moulage par injection - dans le moule et le durcissent dans un four. La partie finale nécessite généralement peu ou pas de post-traitement.
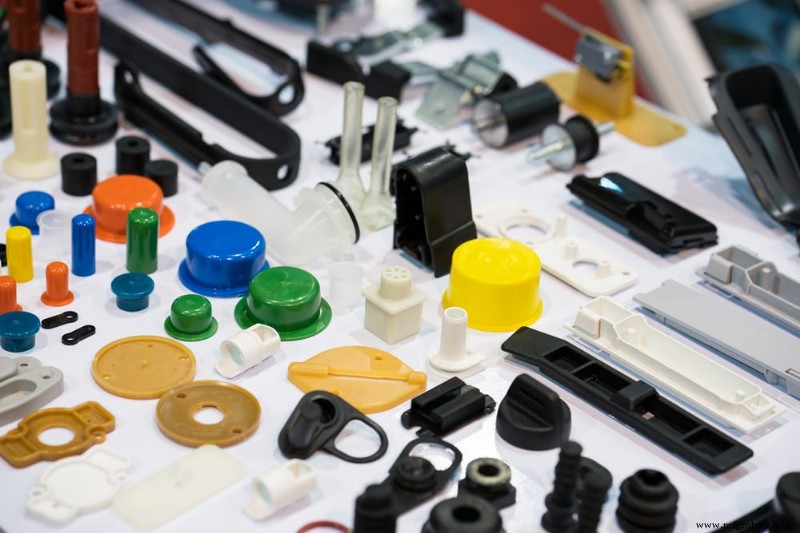
Moins cher et moins long que l'outillage dur, le moulage à l'uréthane est idéal pour le prototypage rapide et les séries de production à volume faible à moyen de constructions complexes. Pour tirer le meilleur parti de ce processus de fabrication, les équipes de produits doivent concevoir pour la fabricabilité et optimiser la conception des moules dès le début afin de rationaliser le processus de production et de maintenir les coûts bas. Voici cinq conseils de conception essentiels pour créer des pièces moulées en uréthane propres et fonctionnelles :
5 astuces de conception pour la coulée d'uréthane
1. Donnez une épaisseur de paroi uniforme
De nombreux ingénieurs préfèrent la coulée d'uréthane au moulage par injection car le premier procédé permet une plus grande variation d'épaisseur de paroi, mais il est toujours important de s'assurer qu'une conception de moule en uréthane donnée présente des parois uniformes. Des parois uniformes réduisent le risque de déformation pendant le durcissement, garantissent que le moule sera rempli complètement et avec précision et atténuent d'autres problèmes de conception.
Une épaisseur de paroi minimale de 0,040 po (1 mm) est recommandée, mais il existe des cas où les parois peuvent être aussi minces que 0,020 po (0,5 mm) dans de petites pièces. Pour les grandes pièces, l'épaisseur de la paroi doit toujours augmenter proportionnellement à la taille de la pièce pour garantir que les parois peuvent fournir un support adéquat.
2. Tenir compte du rétrécissement
Lorsque deux parois d'épaisseurs différentes se croisent dans une conception de moule en uréthane, un retrait peut se produire. Étant donné que les parois plus épaisses se solidifient plus lentement que les parois plus minces, la zone à laquelle elles sont attachées au niveau de la paroi nominale se rétrécit à mesure que la projection - une nervure ou un bossage - rétrécit. Cela provoque une zone en creux dans le mur nominal. Pour minimiser le rétrécissement et éviter les zones enfoncées, les ingénieurs doivent s'assurer que l'épaisseur des nervures se situe entre 50 % et 60 % des murs auxquels elles sont fixées.
Pourtant, il arrive parfois que des pièces moulées en uréthane rétrécissent pour des raisons autres qu'un défaut de conception du moule en uréthane. Les dimensions finales d'une pièce moulée en uréthane dépendent de la précision du modèle principal et du moule, de la géométrie de la pièce, ainsi que des matériaux de moulage en uréthane. Un taux de retrait de 0,15 % est considéré comme acceptable, mais les ingénieurs doivent revoir la conception de leur moule en uréthane si le taux de retrait dépasse ce seuil.
3. Employez des côtes
L'ajout de nervures à une conception de moule en uréthane peut augmenter la résistance et la rigidité de la pièce d'extrémité sans ajouter d'épaisseur. Pour utiliser correctement les nervures, les ingénieurs doivent respecter les consignes suivantes :
Hauteur
Des nervures plus longues fournissent un meilleur renforcement, mais le coulage d'une longue nervure peut rendre la pièce difficile à mouler. Pour cette raison, une nervure ne doit pas dépasser une hauteur égale à trois fois son épaisseur. Pour éviter complètement le problème de hauteur, les ingénieurs peuvent utiliser plusieurs nervures courtes au lieu d'une nervure longue pour augmenter la rigidité de la pièce.
Largeur
La largeur de la nervure à l'intersection de la pièce doit être de 40 % à 60 % de l'épaisseur de la pièce. Si un rayon de congé est inclus dans la conception, il doit être d'au moins 25 % de l'épaisseur de la pièce. Ces paramètres aident à rendre la nervure aussi solide que possible.
Angle de dépouille
Les ingénieurs doivent rédiger une nervure conçue pour réduire la possibilité de naufrage. Les angles de dépouille de chaque côté doivent être compris entre 0,25 et 0,5 degrés et l'angle de dépouille de chaque côté doit être égal. Pour les surfaces texturées, ajoutez une dépouille supplémentaire de 1,0 degré pour chaque profondeur de texture de 0,025 (0,001 pouce).
Espacement
Les ingénieurs doivent placer les nervures consécutives à au moins deux fois l'épaisseur les unes des autres pour répartir uniformément le poids de la pièce sur toutes les nervures.
Orientation
L'orientation des nervures détermine comment et où la pièce subit des contraintes. Les ingénieurs doivent donc veiller à disposer les nervures de manière à maximiser la rigidité en flexion de la pièce. Si les nervures sont placées dans la mauvaise position, elles n'auront aucun impact positif sur la résistance de la pièce.
Les équipes de produits doivent également être conscientes des intersections et de l'enfoncement lorsqu'elles travaillent avec des nervures. Au point d'intersection d'une nervure avec la pièce, une nervure lourde peut faire plonger la pièce. Pour éviter l'affaissement à l'intersection des nervures, les ingénieurs peuvent utiliser des congés pour atténuer la contrainte sur la surface de la pièce et réduire l'affaissement du côté opposé de la pièce. Les rayons des congés doivent être au moins au quart de l'épaisseur de la pièce. De plus, le carottage ou l'allégement de la pièce réduit la quantité de matériau utilisé et aide à maintenir une épaisseur de paroi uniforme dans toute la pièce.
Les nervures peuvent considérablement améliorer les performances d'une pièce finale, mais les ingénieurs et les équipes de produits ne doivent pas s'emballer. Les nervures ne sont utiles que lorsque la pièce nécessite un renforcement supplémentaire. Dans les situations où ce n'est pas le cas, les nervures sont souvent mal placées et n'améliorent guère la résistance ou la rigidité de la pièce. De plus, des nervures inutiles augmentent le poids et le prix de la pièce, causent des problèmes de moulage et contribuent au gaspillage de matière. Les ingénieurs et les équipes de produits doivent garder ces considérations à l'esprit lorsqu'ils décident si la conception de leur moule en uréthane nécessite ou non une nervure.
4. Tenez compte des courants d'air et des contre-dépouilles
Les courants d'air et les contre-dépouilles ne sont pas un problème avec la coulée d'uréthane car le silicone liquide peut prendre la forme de n'importe quel moule. Cependant, si un ingénieur utilise la coulée d'uréthane pour construire un prototype qui sera éventuellement fabriqué à l'aide d'un processus différent, comme le moulage par injection, il doit créer la conception prévue pour la production finale. Cela pourrait inclure l'incorporation de brouillons et de contre-dépouilles. Les longues caractéristiques sans tirant d'eau présentent un léger risque de rupture de pièce lors de l'extraction de la pièce du moule, donc un léger angle peut être utile, en particulier pour les grandes séries de production.
5. Inclure un espacement suffisant entre les lettres et les logos
Avec la coulée d'uréthane, il est facile pour les concepteurs de mouler des lettres et des logos en relief ou en retrait de haute qualité dans des pièces moulées en uréthane personnalisées. Pour s'assurer que les lettres sont aussi belles et lisibles que possible, les concepteurs doivent garder à l'esprit la hauteur ou la profondeur de l'élément, la largeur de l'élément, les rayons sur l'élément et l'espace entre les éléments.
Les équipes de produits doivent laisser au moins 0,050" entre les fonctionnalités, bien que cela puisse varier en fonction des particularités de la conception. Tous les rayons doivent être au moins égaux à la moitié de la hauteur de l'élément, mais des rayons plus grands sont encore meilleurs. Enfin, la largeur de tous les logos ou lettres doit être le double de leur hauteur.
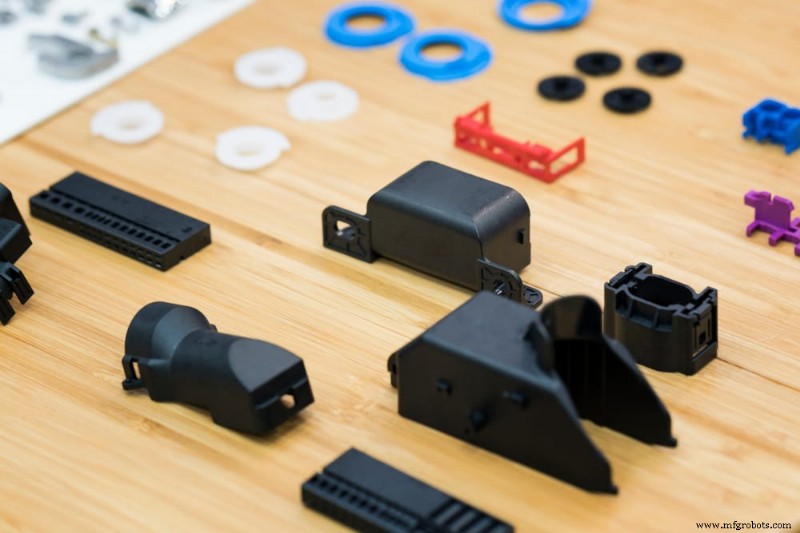
Optimisez vos pièces moulées en uréthane
Avec la coulée d'uréthane et la conception pour la fabricabilité, quelques petites modifications de conception suffisent. Les ingénieurs et les concepteurs doivent chercher à maintenir des épaisseurs de paroi uniformes, tenir compte du retrait et s'assurer qu'ils utilisent efficacement les nervures. Les équipes produit peuvent optimiser davantage la fabricabilité en créant des conceptions telles qu'elles sont destinées à la production finale et en s'assurant qu'elles laissent suffisamment d'espace entre les lettres et les logos pour améliorer l'esthétique.
Un partenaire de fabrication expérimenté comme Fast Radius peut aider les équipes produit à simplifier la conception pour la fabricabilité. Nous sommes passionnés par le développement de produits que l'on croyait autrefois impossibles à fabriquer, et nous mettons un point d'honneur à suivre les dernières technologies de conception numérique.
Les équipes de produits qui cherchent à développer une application révolutionnaire ou à optimiser une conception de moule en uréthane existante peuvent bénéficier des années d'expérience de notre équipe de conception dans les processus de fabrication. Contactez-nous dès aujourd'hui pour commencer à créer vos pièces moulées en uréthane personnalisées.
Pour plus de conseils de conception et d'informations sur la coulée d'uréthane, consultez les articles connexes dans le centre d'apprentissage Fast Radius.
Prêt à fabriquer vos pièces avec Fast Radius ?
Commencez votre devisTechnologie industrielle
- Cinq conseils pour optimiser les chaînes d'approvisionnement des soins de santé
- Cinq conseils pour créer un processus d'intégration de fournisseur efficace
- Expédition depuis le magasin le même jour ? Cinq conseils pour une livraison plus rapide
- 5 conseils pour la conception de tôlerie
- 6 conseils pour optimiser votre conception pour un projet de fabrication métallique
- 5 conseils de conception pour RIM
- Conseils de conception de moulage en polyuréthane
- 5 conseils pour la conception de circuits automobiles afin de vaincre les EMI
- Conseils de conception pour le moulage par injection