Suppression des obstacles à l'optimisation des processus de broyage nouvellement installés
En règle générale, les nouvelles lignes à volume élevé produisant des pièces complexes qui incluent des processus de meulage, tels que des aubes et des aubes de moteur automobile ou de moteur aéronautique, passent par différentes étapes, de l'achat de la machine à la production réelle, comme indiqué dans la figure 1. Si ces lignes incluent un processus considéré comme "risque élevé " il sera programmé avec un "temps de développement" dans le cadre de l'évaluation et de l'achat de la capacité du broyeur (étapes 4 et 5) par des tests et des améliorations. Il s'agit d'une stratégie efficace qui réduit considérablement les problèmes associés au lancement du programme, mais qui peut prendre du temps et coûter cher ; très souvent, des échantillons de pièces peuvent même ne pas être disponibles ou sont des prototypes sujets à d'autres modifications de conception. Dans de tels cas ou pour des conceptions de composants différentes, mais pas radicalement différent à partir de conceptions existantes, le "temps d'optimisation" est rarement planifié avant la qualification réelle de la machine.
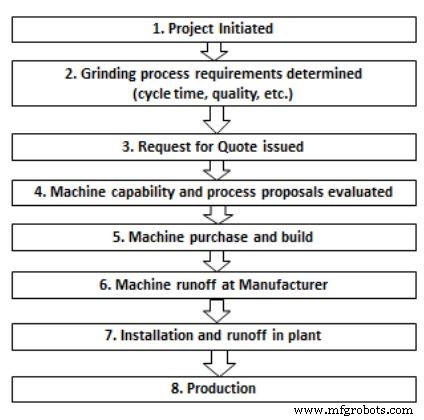
Lorsque les machines sont qualifiées et installées avec "non radical ” processus, l'accent est mis sur la qualité des pièces et le temps de cycle. Les spécifications des roues peuvent être sélectionnées pour garantir la meilleure qualité au milieu des incertitudes de la nouvelle conception de la pièce et de leur impact sur le maintien des tolérances de la pièce à des spécifications CpK souvent plus strictes que celles requises pour la production. De plus, en raison du coût ou de la disponibilité, seules 50 ou 100 pièces sont souvent fournies pour la qualification, ce qui rend discutable la mise en place d'un processus stable à long terme. Il n'y a généralement pas beaucoup de temps ou de composants pour optimiser le coût de l'outillage ou de l'abrasif par pièce. Après l'installation, dans de nombreux cas, une attitude "si ce n'est pas cassé, ne le répare pas" prend le dessus et les processus sont bloqués. L'optimisation est rarement tentée.
Il est donc très important que « l'étape supplémentaire » d'optimisation soit considérée comme un « audit » final du processus. La plupart du temps, cette étape peut être simplement une « mise au point » du processus de sorte qu'une requalification de l'ensemble du processus n'est pas nécessaire, mais parfois des opportunités suffisamment importantes peuvent être découvertes, ce qui justifierait des modifications majeures du cycle et/ou des spécifications de la roue. Une analyse coûts/avantages serait effectuée pour déterminer si un changement de processus plus substantiel devrait être fait.
Il existe plusieurs raisons pour lesquelles le manque de "temps d'optimisation" peut entraîner des processus sous-optimaux :
- Les cycles peuvent fonctionner de manière acceptable dans la machine mais ne pas être "compatibles avec les roues". c'est-à-dire que la durée de vie de la roue peut être moins qu'optimale
- La technologie des roues évolue. Les estimations faites sur la technologie existante peuvent ne pas être optimales pour la nouvelle technologie
- Des variations subtiles dans la configuration des pièces, la conception de la machine et les exigences de qualité rendent l'optimisation des processus très difficile en dehors de la chaîne de production. En effet, la chaîne de production fournit de nombreuses pièces et un environnement avec de réelles variations et métrologie. Ces deux qualités permettent de tester la "robustesse" du processus "optimisé".
Exemples :
Le cycle de meulage illustré à la figure 2 a été expédié par l'OEM installé dans une usine et est actuellement en production. Ce cycle fonctionne bien et produit des pièces acceptables, mais il n'est pas "compatible avec les roues".
L'"inconvivialité" de la roue de ce cycle est due à la forte pointe (puissance/force) au début du cycle. L'usure de la meule est proportionnelle au carré de la force de meulage, des forces élevées entraîneront une usure rapide de la meule. Dans ce cas, réduire l'avance rapide et augmenter l'avance moyenne prolongerait la durée de vie de la meule tout en maintenant le temps de cycle et la qualité des pièces.
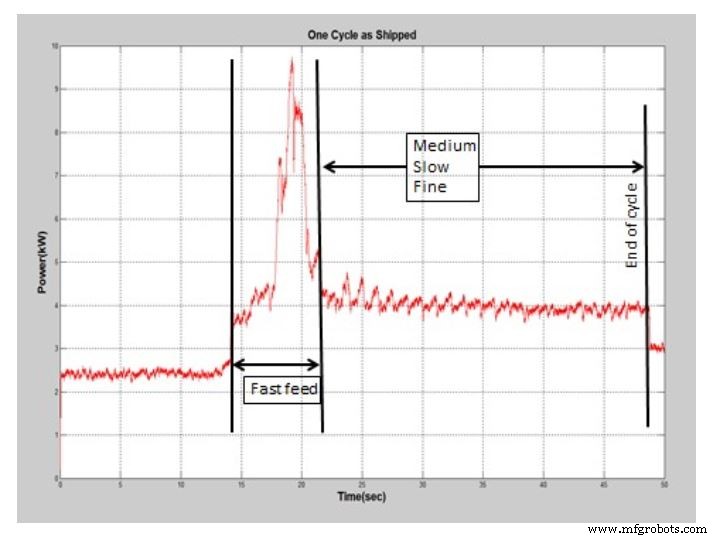
Un cycle dans le processus d'optimisation
Dans un cas inhabituel récent, le fabricant a accepté de procéder à une optimisation "in situ" du processus de broyage. Initialement, le cycle de meulage a été modifié pour le rendre plus "convivial pour les meules", comme indiqué ci-dessus. Dans ce cas, le cycle le plus convivial était également d'environ 5 secondes plus court que le cycle initial.
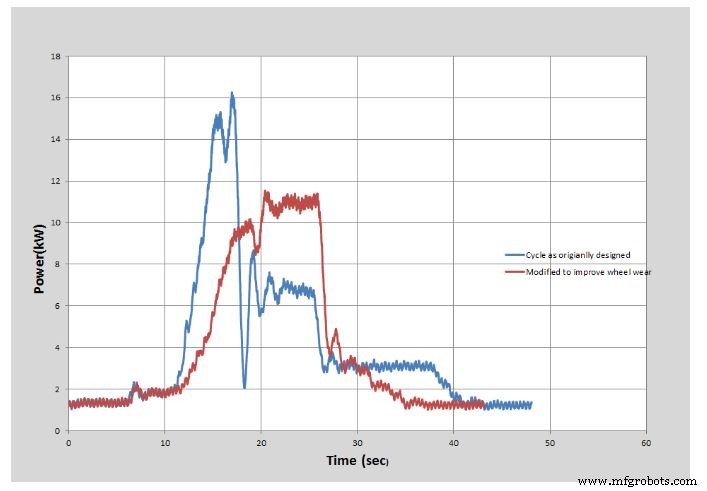
Après avoir exécuté le cycle modifié pendant plusieurs semaines pour valider la qualité continue des pièces, le nombre de pièces par dressage a été augmenté de 8 à 20 et la profondeur de dressage a été réduite de 0,03 mm à 0,02 mm. Ce processus a maintenant fonctionné pendant environ 6 semaines sans changement significatif de la qualité des pièces. Le résumé des économies de coûts par an est présenté ci-dessous.
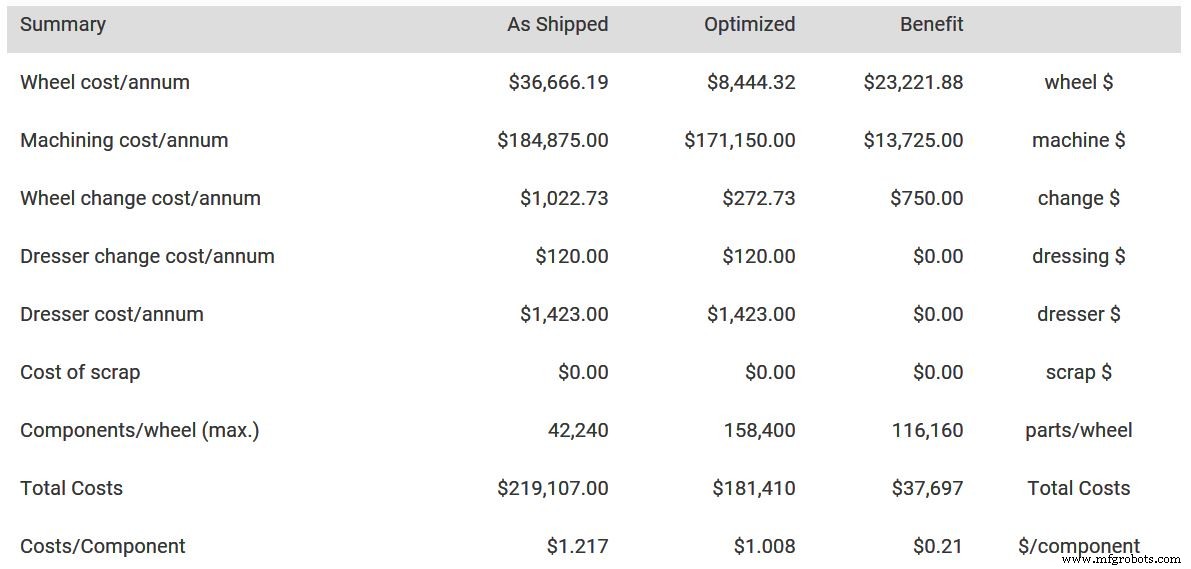
Stratégie d'optimisation
La solution, comme illustré dans le deuxième exemple, consiste à planifier le temps et les pièces dans les premières étapes de la production (entre les étapes 7 et 8 de la figure 1) pour travailler sur l'optimisation des processus avec le constructeur de la machine et l'équipe d'ingénierie d'application d'outillage/abrasifs. . À tout le moins, un équipement de surveillance de l'alimentation doit être utilisé pendant cette phase pour aider à l'évaluation et au développement du cycle. Avec cette étape supplémentaire, la stabilité du processus peut être surveillée sur des séries de pièces plus longues, ce qui peut mettre en lumière des problèmes et/ou présenter des opportunités d'amélioration.
Le gain potentiel de cette étape est important, car les améliorations/économies réalisées à ce stade seront en place tout au long du cycle de vie du projet.
Précédemment présenté sur Norton Abrasives
Achetez notre sélection de roues de grille Norton sur MSCdirect.com.
Technologie industrielle
- Création de normes et de processus opérationnels
- Airbus présente l'usine du futur
- Modes de défaillance des processus de fiabilité des équipements
- Optimisation des opérations de fabrication dans votre atelier
- Meules :fabrication et qualité | Secteurs | Métallurgie
- Qu'est-ce que le rodage ? - Définition, processus et outils
- Comment mettre en œuvre la gestion des processus métier
- Services de meulage de surface :processus et précision
- Fondamentaux du meulage OD