Le contrôle connecté
Internet et l'informatique basée sur le cloud modifient la façon dont les fabricants exploitent les machines-outils CNC. Votre boutique est-elle prête ?
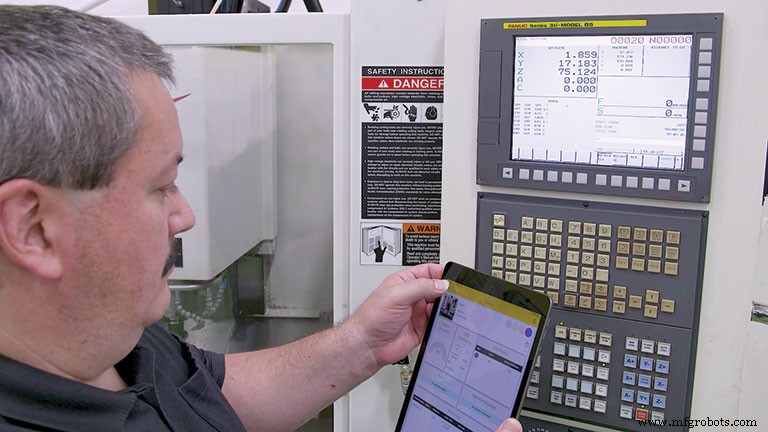
Les ports Ethernet ont commencé à apparaître sur les tours CNC et les centres d'usinage il y a plus de 20 ans. La norme de communication des machines-outils MTConnect a fait ses débuts officiels aux États-Unis lors de l'IMTS 2010 à Chicago. Les fabricants ont commencé à parler de cloud computing et d'Internet industriel des objets (IIoT) peu de temps après, des termes qui deviendront courants lorsque l'économiste allemand Klaus Schwab a publié un article en 2015 déclarant que le monde était entré dans une quatrième révolution industrielle.
Bienvenue en 2021. Il devrait maintenant être évident pour les propriétaires d'ateliers d'usinage, les programmeurs CNC et les ingénieurs de fabrication que l'industrie de l'usinage a considérablement changé au cours des deux dernières décennies. Les machines-outils CNC sont bien plus intelligentes qu'auparavant, capables de générer des quantités importantes de données sur tout ce qui se passe derrière la vitre. Les logiciels de fabrication sont également devenus plus intelligents, offrant une interopérabilité et des capacités basées sur le cloud dont on ne rêvait qu'au tournant du siècle.
Que toute cette magie technique soit une bonne chose ou non est à débattre. Certains pourraient dire que la vie dans l'atelier est déjà suffisamment difficile :qui a besoin de Big Data et de machines intelligentes alors qu'il y a à peine assez d'heures dans la journée pour sortir les pièces ? D'autres voient l'industrie 4.0 et tout ce qu'elle implique comme la voie à suivre pour les fabricants, et quiconque ne l'adopte pas sera bientôt en faillite.
Gagner des FOCAS
La vérité se trouve quelque part entre les deux. Paul Webster, directeur de F.A. Engineering chez FANUC America Corp., dont le siège est à Rochester Hills, Michigan, a noté que les machines-outils CNC étaient prêtes pour le réseau et Internet depuis avant l'an 2000. Les magasins qui choisissent d'ignorer cette capacité fonctionnent toujours très bien, merci, et continueront de le faire pour les années à venir. Et pourtant, rares sont ceux qui diraient que la connectivité des machines-outils et la plus grande visibilité sur les processus d'usinage ainsi activées ne sont jamais une mauvaise chose et peuvent faire la différence entre un travail rentable et un travail que vous oublieriez tout de suite.
"Nous avons introduit notre API FOCAS (interface de programmation d'application) au début des années 90, ainsi que des ports fibre optique puis Ethernet, donc connecter une CNC est facile depuis un certain temps maintenant", a-t-il déclaré. "Le plus difficile a toujours été de déterminer les données dont vous avez besoin et ce que vous allez en faire une fois que vous les aurez."
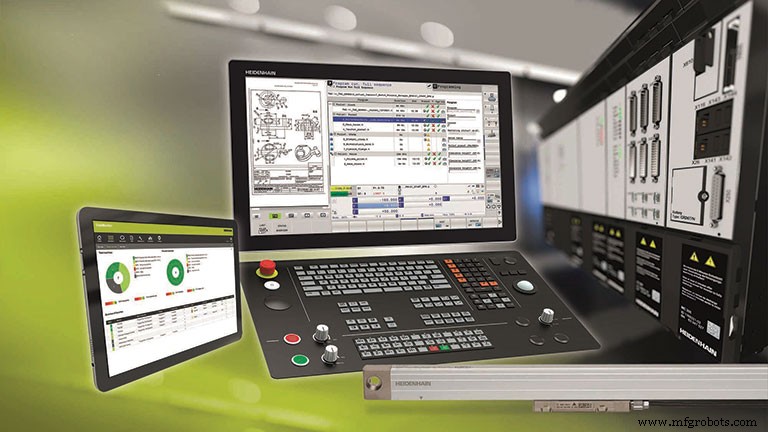
Ces données comprennent les historiques d'alarmes, les paramètres de vitesse d'avance et de broyage de la broche, les températures du servomoteur et de la broche, la consommation d'énergie, les variables macro, et bien plus encore, qui peuvent toutes être extraites de la machine-outil de manière continue et automatique. Ajoutez à cela diverses entrées fournies par l'opérateur - numéro de travail, état de production, consommation d'outils de coupe et même des informations sur la qualité des pièces - et obtenir une image complète des activités de l'atelier ne devient pas plus difficile que de jeter un coup d'œil sur le tableau de bord de n'importe quel logiciel de surveillance qui recueille ces données. .
Dans le cas de FANUC, il s'agit de MT-LINKi, une plate-forme d'analyse indépendante de la marque capable de surveiller plus de 1 000 machines-outils CNC à la fois, ainsi que de FASData, un programme de surveillance de la production. D'autres constructeurs de commandes proposent des solutions similaires, tout comme de nombreux constructeurs de machines-outils, fournisseurs d'outils de coupe et développeurs de logiciels tiers. Tous fournissent les moyens de rassembler ce qui est certes une montagne de données et de le présenter d'une manière qui a du sens pour les humains, leur donnant la capacité de réagir aux tendances et aux problèmes potentiels bien avant qu'ils ne puissent avoir un impact négatif sur les niveaux de production.
L'énigme du cloud
La question devient alors quel est le meilleur endroit pour stocker ces données et héberger le logiciel utilisé pour les analyser ? Les deux doivent-ils être situés dans le cloud dans une installation d'hébergement hors site et gérés par des spécialistes du matériel et des logiciels dédiés ? Ou une installation « sur site » est-elle plus appropriée, en utilisant les talents informatiques internes de la boutique ?
Webster et les autres personnes interrogées pour cet article ont largement convenu que, bien que la première soit souvent l'approche la plus sûre et la plus rentable, de nombreux ateliers restent réticents à l'idée que les programmes de pièces et les données de production quittent leur usine. Il en va de même pour Gisbert Ledvon, directeur du développement commercial pour les machines-outils chez Heidenhain Corp, basé à Schaumburg, dans l'Illinois. Il a noté que les clients peuvent installer le logiciel StateMonitor de l'entreprise où ils le souhaitent, mais encourage les installations sur site dans la mesure du possible.
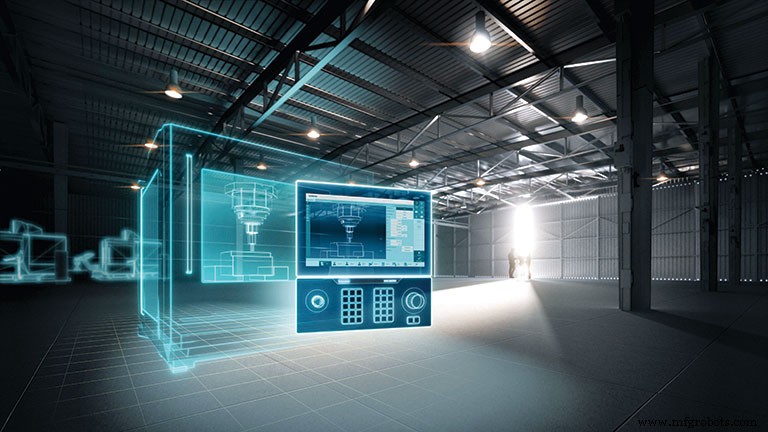
"Notre philosophie est que les clients doivent protéger leur propriété intellectuelle, et pour nous, cela signifie connecter leurs machines-outils et leurs systèmes logiciels à un réseau d'entreprise correctement sécurisé", a-t-il déclaré. "Il y a eu de nombreux cas où des magasins ont été piratés et forcés de payer des rançons. Certes, ces attaques sont généralement réalisées par e-mail et non par le contrôle de la machine-outil, mais c'est néanmoins une préoccupation. C'est pourquoi la NTMA (National Tooling and Machining Association) a commencé à proposer des séminaires montrant aux fabricants comment ils peuvent se protéger contre ces types de cybercriminalité."
Malgré cela, Ledvon admet que le cloud est une tendance technologique qui ne fera que prendre de l'ampleur. Ce qu'il faut pour atténuer les risques associés, ce sont de bonnes pratiques d'entretien informatique. Installez un pare-feu robuste entre le réseau du magasin et le monde extérieur. Évitez les connexions directes CNC-cloud en téléchargeant des fichiers externes, des logiciels et des correctifs sur un serveur interne sécurisé, puis vérifiez-les avec un logiciel antivirus avant leur distribution. Formez tous les utilisateurs d'ordinateurs à gérer les mots de passe, à repérer les e-mails et les sites Web malveillants et à protéger les informations de l'entreprise. La liste continue.
"Étant donné que le contrôle est le centre névralgique de toute machine-outil, je ne pense pas que la commodité de l'accès au cloud vaille le risque d'une exposition à Internet", a déclaré Ledvon. « Cependant, rien de tout cela n'empêche les fabricants de mettre en œuvre une stratégie Industrie 4.0. Par tous les moyens, ils devraient mettre en réseau leurs machines-outils et commencer à collecter des données à analyser. Cela leur donnera les informations nécessaires pour configurer les machines plus rapidement, réduire les temps de cycle, maximiser la durée de vie des outils et bénéficier de tous les autres avantages offerts par les commandes CNC et les systèmes logiciels d'aujourd'hui. »
Talent natif
Un autre composant de l'Industrie 4.0 est le jumeau numérique, qui dans ce cas fait référence à une représentation virtuelle mais très précise et complète d'une machine-outil CNC. Selon Vivek Furtado, responsable de la numérisation des machines-outils pour Siemens Industry Inc., Elk Grove Village, Illinois, les jumeaux numériques rationalisent la conception et le déploiement des machines CNC, ce qui rend les fabricants plus efficaces.
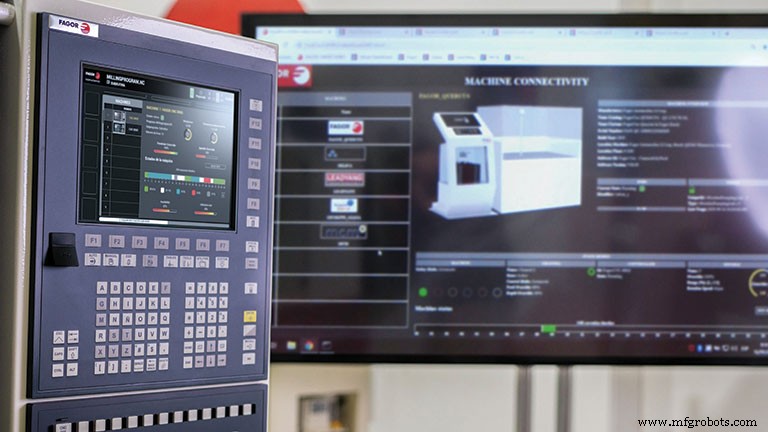
"Notre contrôleur SINUMERIK One est connu comme un natif numérique, en ce sens qu'il a été conçu à partir de zéro pour prendre en charge le jumeau numérique et d'autres technologies habilitantes", a-t-il déclaré. « Il offre aux fabricants de machines-outils à commande numérique la possibilité de créer une version virtuelle d'un tour ou d'un centre d'usinage contenant l'ensemble de sa cinématique et de ses caractéristiques de fonctionnement. Cela réduit considérablement le temps d'ingénierie et les coûts de développement, et garantit que le produit répondra aux besoins des utilisateurs finaux."
Les contrôleurs numériques à capacité jumelle servent à d'autres fins. Ils accélèrent la formation des nouveaux employés et réduisent le risque de planter une machine-outil coûteuse. Ils permettent aux estimateurs de citer les travaux avec plus de précision, aux ingénieurs de développer des processus de fabrication optimisés et aux programmeurs CNC de valider le code G et la sélection des outils de coupe avant d'envoyer le travail à l'atelier. Une fois là, ils facilitent le fonctionnement de la machine-outil avec des graphismes améliorés et une plus grande convivialité.
Toute personne disposant d'un système de FAO ou d'un logiciel PLM haut de gamme pourrait dire qu'elle peut accomplir la plupart de ces tâches sans une commande CNC avancée. Et bien qu'il soit indéniable que les capacités de ces plates-formes logicielles et d'autres ont considérablement augmenté ces dernières années, les machines-outils qui participent au fil numérique fournissent aux ateliers d'usinage un outil important, qui améliore l'échange de données et boucle la boucle sur l'interopérabilité.
S'adapter et surmonter
Mis à part le jumelage numérique, Furtado a suggéré que les contrôleurs CNC deviennent beaucoup plus intelligents et conviviaux, avec des fonctions et des caractéristiques que tout utilisateur de smartphone reconnaîtra. "La plupart d'entre nous se souviennent que nous utilisions autrefois nos téléphones pour appeler les gens", a-t-il déclaré. « Aujourd'hui, ils vous permettent de surveiller votre santé, de rechercher des informations, de passer des commandes de produits, etc. Les nouvelles générations de contrôleurs offrent des fonctionnalités similaires. Ils sont capables de traiter les informations et de préparer les données de manière à ce qu'elles soient utilisées plus efficacement par leurs opérateurs humains ou par d'autres systèmes."
Cette intelligence s'étend également au processus d'usinage. Siemens, FANUC et des fournisseurs de solutions tiers tels que Caron Engineering offrent des capacités de contrôle adaptatif qui surveillent en permanence les charges de broche et d'axe, les vibrations de la machine et des facteurs similaires qui affectent la durée de vie de l'outil de coupe et la qualité des pièces. Ces systèmes intelligents ajustent ensuite les paramètres d'usinage en temps réel, optimisant l'enlèvement de matière et éliminant les problèmes potentiels.
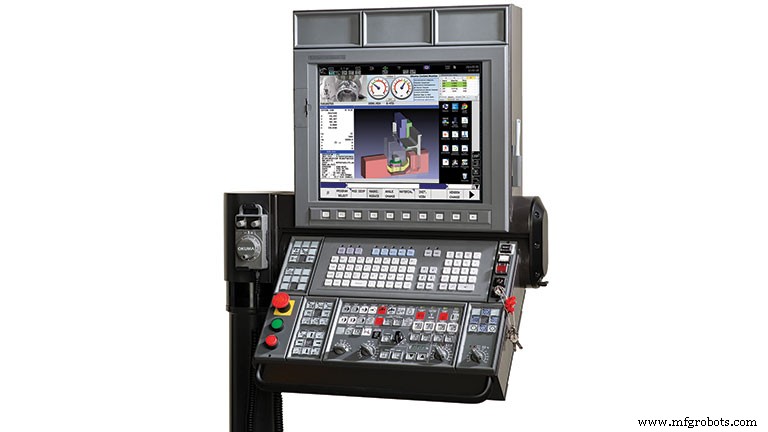
Fagor Automation Corp., Elk Grove Village, Illinois, est un autre fournisseur de contrôle qui vise le prix de l'industrie 4.0. Harsh Bibra, directeur général pour l'Amérique du Nord chez Fagor, a expliqué que son contrôle ARFS (Adaptive Real-time Feed and Speed) fait tout cela et plus encore, mais a noté que ce type de technologie basée sur des capteurs peut également être utilisé pour la maintenance prédictive.
"Nous proposons également notre pack de connectivité i4.0", a-t-il déclaré. "Cela permet aux utilisateurs de collecter des données d'usinage, bien sûr, mais aussi d'envoyer des alertes basées sur des conditions, de régler la machine-outil et de mettre à jour son micrologiciel, de modifier les paramètres, etc., le tout à partir d'un appareil mobile ou d'un ordinateur distant."
Le plus gros goulot d'étranglement
Bibra voit de grands changements à venir. Outre l'utilisation accrue de capteurs et d'accéléromètres compatibles IIoT dans les machines-outils, ainsi que des contrôleurs plus intelligents, les usines elles-mêmes deviendront plus intelligentes. L'intelligence artificielle (IA), bien au-delà des capacités d'adaptation que nous venons de mentionner, deviendra prédominante, ouvrant les portes à la prise de décision automatisée nécessaire à une fabrication en panne généralisée.
Tout cela va littéralement s'accélérer compte tenu du développement et du déploiement ultérieur des réseaux cellulaires 5G, a suggéré Bibra. Ceux-ci augmenteront non seulement la bande passante Internet et réduiront la latence, mais atténueront peut-être les craintes de piratage mentionnées précédemment. "Les commandes du futur seront équipées de la 5G, et les données qu'elles génèrent pourront ensuite être envoyées sans fil à des vitesses allant jusqu'à 10 gigabits par seconde (Gbit/s) vers des appareils dits périphériques", a-t-il déclaré. "Nous prévoyons que d'ici quelques années, cette technologie transformera fondamentalement la façon dont les fabricants collectent les informations de l'atelier."
L'inconvénient de l'industrie 4.0 est le manque de travailleurs qualifiés capables de comprendre et de travailler avec une technologie de pointe. Bibra a déclaré qu'un recyclage sera nécessaire à mesure que les fabricants deviendront plus avertis en matière de technologie. Cependant, toute préoccupation concernant les connaissances tribales et la perte d'expérience due à l'attrition et à la retraite des employés devrait devenir de l'histoire ancienne.
Visiter le magasin
Jim Kosmala, vice-président de l'ingénierie et de la technologie chez Okuma America Corp., Charlotte, N.C., attribue une grande partie de la connectivité accrue d'aujourd'hui à l'utilisation de commandes basées sur PC. "Beaucoup de gens oublient qu'Okuma n'est pas seulement un constructeur de machines-outils, mais fabrique également ses propres systèmes d'asservissement et contrôleurs. Ceux-ci fonctionnent sous Microsoft Windows et utilisent une puce Intel, qui offrent toutes deux une connectivité facile. »
Les commandes sur PC facilitent également l'installation de divers logiciels sur la commande - au début de la pandémie de COVID, par exemple, les clients d'Okuma pouvaient collaborer avec d'autres en utilisant Microsoft Teams, en partageant des écrans ou en donnant à d'autres le contrôle à distance selon les besoins. "C'est toute l'idée derrière notre App Store", a déclaré Kosmala. « Les utilisateurs peuvent télécharger et installer tout ce dont ils ont besoin directement sur le contrôle OSP, éliminant ainsi le besoin d'un PC séparé. Cela représente des possibilités entièrement nouvelles de collaboration et de connectivité."
L'une de ces applications est Okuma's Connect Plan, qui permet aux utilisateurs de surveiller les machines-outils CNC et de collecter des données opérationnelles. Il fonctionne avec la plupart des marques ou millésimes de machines-outils ainsi qu'avec des robots et d'autres formes d'automatisation. Selon Kosmala, cependant, Connect Plan utilise un algorithme d'intelligence artificielle pour examiner les informations disponibles et identifier les tendances qu'un humain pourrait manquer.
Prenons l'exemple du responsable d'un service de tournage, qui s'aperçoit après des semaines d'examen des rapports de collecte de données et des tableaux de bord qu'un certain tour démarre toujours avec 10 minutes de retard chaque matin à cause de l'habitude du café de l'opérateur, ou que la température de la broche sur la meuleuse la plus proche du le service d'expédition tombe à chaque fois qu'il ouvre la porte de chargement. Kosmala a expliqué que l'IA détecte ces tendances beaucoup plus rapidement qu'un humain, ce qui donne aux superviseurs la possibilité de résoudre plus rapidement les problèmes potentiels. De plus, ces informations sont stockées dans une base de données, de sorte que lorsque le superviseur quitte l'entreprise, il n'y a aucune perte de connaissances.
"Deming nous a dit que sans données, vous n'êtes qu'une autre personne avec une opinion", a déclaré Kosmala. « L'IIoT et l'industrie 4.0 consistent à collecter ces données et à les utiliser, pour finalement les transformer en connaissances. C'est la première étape pour quiconque dans ce voyage. Nous avons maintenant des conférences virtuelles et la possibilité de vérifier l'état de la machine ou les niveaux de production de n'importe où, et l'accès à des outils à distance qui simplifient l'automatisation. Si vous pouvez le faire sans avoir à entrer dans l'usine, tant mieux. Il s'agit d'augmenter l'efficacité et la disponibilité de la machine, deux choses qui sont plus facilement accomplies à l'aide de contrôleurs CNC modernes. »
Système de contrôle d'automatisation
- Que dois-je faire avec les données ? !
- Démocratiser l'IoT
- L'avenir des centres de données
- Les bases des panneaux de commande électriques
- Apprentissage automatique sur le terrain
- Intégration industrielle de l'Internet des objets
- Le Cloud dans l'IoT
- Au bord de la gloire :permettre une nouvelle ère des machines Internet
- Le décodeur permet la surveillance connectée des données de chaque machine