PEEK contre PEKK contre PAEK et moulage par compression continue
Il s'agit d'un suivi de la récente série d'articles sur les composites thermoplastiques (TPC) que j'ai écrit (voir ci-dessous) ainsi que la fonctionnalité des rubans thermoplastiques que Jeff Sloan a écrit dans le numéro de février.
- Consolidation des aérostructures composites thermoplastiques en place, Partie 1
- Consolidation des aérostructures composites thermoplastiques en place, Partie 2
- Démonstrateurs composites thermoplastiques — Feuille de route de l'UE pour les futures cellules
- PEEK ou PEKK dans les futures aérostructures TPC ?
Les TPC volent à bord d'avions depuis les années 1990 et en structure primaire depuis 2010 — Gulfstream G650 comprend un gouvernail et un élévateur en fibre de carbone/sulfure de polyphénylène (PPS) produits par l'entreprise Fokker de GKN Aerospace (Redditch, Royaume-Uni) à l'aide du préimprégné Cetex de TenCate.
Je pense que parfois nous oublions l'expérience que nous avons déjà dans la technologie TPC. Dans le passé, nous avons demandé « pourquoi plus de TPC ne volent-ils pas dans des avions ? » Peut-être que maintenant, avec la préparation de Boeing pour le nouvel avion de milieu de gamme (NMA) et les progrès de l'industrie aéronautique européenne via Clean Sky 2 et d'autres programmes de développement, nous pourrions enfin voir une nouvelle série d'applications entrer en service.
En attendant, il existe déjà une chaîne d'approvisionnement étendue avec un éventail d'entreprises chevronnées. Ici, je vais toucher la base avec TenCate (récemment acquis par Toray), Teijin et Solvay. Chacun a un point de vue différent sur les polymères et les technologies de traitement qui offrent un potentiel.
TenCate — Le vétéran de TPC continue de faire progresser la technologie
TenCate revendique plus de 40 ans d'expérience dans le développement de composites thermoplastiques. C'est Cetex La marque est bien connue pour les stratifiés préimprégnés et préconsolidés (également appelés feuilles organiques), mais s'étend également aux composés de moulage en vrac (BMC) ainsi qu'aux rubans unidirectionnels (UD) et tissés. La société a une longue expérience avec la gamme complète de thermoplastiques (voir graphique ci-dessous), et a maintenant ajouté Low Melt Polyaryletherketone (LM PAEK ). Ces matériaux sont utilisés dans des applications prises en charge par les divisions aérospatiale et industrielle de TenCate, ainsi que dans des produits plus grand public tels que l'électronique grand public et les chaussures de sport via la division Performance Composites de l'entreprise.
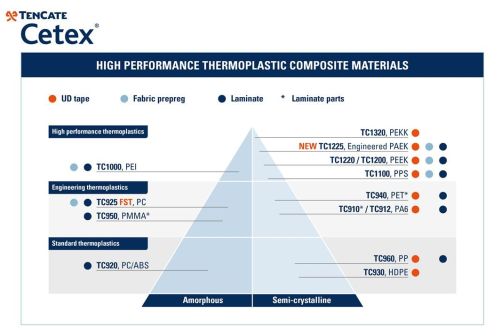

Les rubans thermoplastiques Cetex sont disponibles dans une grande variété de polymères matriciels allant d'une température de fusion inférieure/des performances inférieures à une température de fusion plus élevée/des performances supérieures.
SOURCE :TenCate (en haut), Tri-Mack Plastics Mfg. Corp . (bas)
avec PEEK, PAEK ajouté par CW.
Lors des interviews pour ma série sur les thermoplastiques consolidés in-situ, le Low Melt PAEK est apparu comme une alternative potentielle à la polyéthercétonecétone (PEKK) et à la polyétheréthercétone (PEEK) dans la quête d'un traitement plus rapide. Lorsque j'ai interrogé TenCate à ce sujet, le Dr Hans Luinge, directeur de la recherche et du développement de produits sur les composites thermoplastiques pour TenCate, a récapitulé la différence entre les températures de fusion :
- Ruban fibre de carbone TC1225 (CF)/LM PAEK 305 °C
- Ruban TC1320 CF/PEKK 340°C
- Ruban TC1200 CF/PEEK 350°C
Notez que les températures réelles utilisées lors du traitement de ces rubans composites peuvent être plus élevées, mais le TC1225 LM PAEK est toujours attrayant en raison de son point de fusion beaucoup plus bas.
« Cetex TC1225 LM PAEK a été introduit dans le TAPAS1 programme de développement, dans lequel nous avons été un participant clé », se souvient Luinge. Il utilise le polymère PAEK de Victrex, et il souligne que d'ici 2013 , le matériau TC1225 avait déjà été utilisé dans une structure d'avion de démonstration . Airbus Nantes a exposé un fuselage panneau avec renforts intégrés au salon du Bourget 2013. Il a été fabriqué à l'aide du ruban CF/LM PAEK fourni par TenCate, avec des éléments en oméga et en T assemblés à la presse qui ont été soudés à la peau, fabriqués avec un placement automatisé de fibres (AFP).
« Le PAEK à bas point de fusion fonctionne bien dans l'AFP, le formage de tampons et le soudage », déclare Scott Unger, directeur mondial de la technologie de TenCate. Mais avec la fonte inférieure température, ne sont pas les propriétés mécaniques pour LM PAEK inférieur à PEKK et PEEK ? Unger dit non, ils sont tous à peu près les mêmes . « PEEK, PEKK et LM PAEK sont tous de bons matériaux de structure et, du point de vue des coûts, le prix du TC1225 est compétitif par rapport au TC1200 CF/PEEK et est moins coûteux que le TC1320 PEKK. »
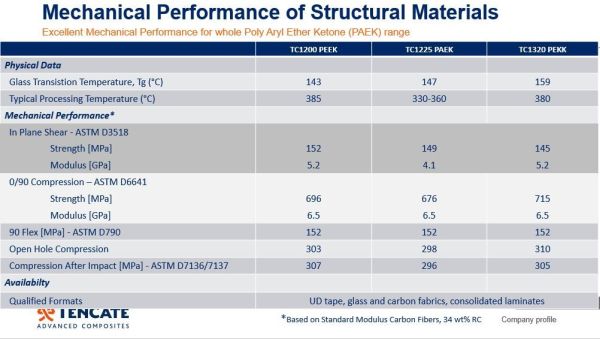
Le PAEK à bas point de fusion accélère la consolidation in situ
De plus, le TC1225 LM PAEK est prometteur pour la consolidation in situ, ce qui, selon Unger, « est potentiellement le Saint Graal. Mais ce que nous avons vu dans le passé, c'est que vos vitesses AFP doit être très lent pour parvenir à la consolidation in situ . " Il explique :« Vous ne pouvez pas atteindre la consolidation in situ sans utiliser un ruban qui démontre un niveau de vide bien inférieur à ce qui est finalement acceptable dans le stratifié ou la structure finale. Il existe deux facteurs clés :qualité du ruban et dans quelle mesure la résine de matrice et la fibre sont réparties dans le ruban UD. Unger affirme que les processus de fabrication de ruban UD de TenCate ont été conçus pour produire des niveaux de vide extrêmement bas pour permettre des processus tels que l'AFP rapide suivie par uniquement hors autoclave/sac sous vide Consolidation (OOA/VBO) ainsi que AFP consolidée in situ en une seule étape.
« Notre bande est extrêmement cohérente avec 0 à 0,5 % de vides maximum ", déclare Winand Kok, directeur des services d'experts UE de TenCate. « Notre épaisseur de ruban est également très cohérent , c'est pourquoi nous pouvons obtenir des épaisseurs de plis très précises dans les stratifiés consolidés. Cette cohérence est également importante pour les procédés de soudage thermoplastique et la consolidation in situ. Unger revient sur la deuxième exigence qu'il a évoquée ci-dessus :« LM PAEK a beaucoup un meilleur débit contre PEKK et PEEK. Il peut également être traité à des vitesses plus élevées que PEKK et PEEK. »
Ce dernier point a été démontré dans une comparaison stratifié à stratifié . « Nous avons fabriqué des stratifiés CF/PEKK TC1320 à l'aide d'une machine AFP laser Coriolis au Centre de recherche sur les composites thermoplastiques (TPRC) à Twente, aux Pays-Bas », explique Unger, « à une vitesse rapide de 600 mm/s . Nous avons ensuite consolidé ce stratifié en utilisant un sac sous vide uniquement dans un four." Il a reconnu qu'il y avait de la porosité entre les plis en raison de la superposition rapide d'AFP, mais ces vides ont été comblés au cours de la deuxième étape de consolidation, illustrée sur les microphotographies du stratifié. « Nous avons également placé le matériau TC1320 en fibre à 200 mm/s et constaté que la porosité entre les plis n'était pas éliminé avec la vitesse plus lente. Nous avons ensuite réalisé un stratifié équivalent en utilisant la même machine AFP mais cette fois en utilisant TC1225 CF/LM PAEK bande sans aucune étape de consolidation OOA/VBO secondaire, c'est-à-dire une consolidation in situ complète via l'AFP. Nous avons atteint les mêmes propriétés de consolidation comme dans le panneau PEKK en 2 étapes. »
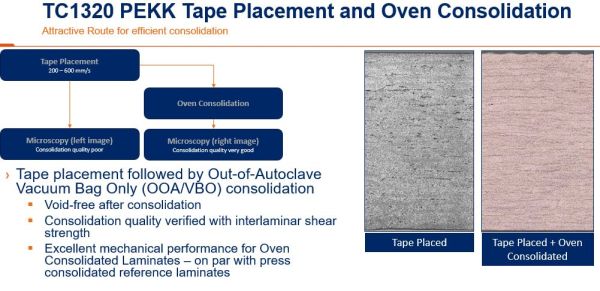

CF/PAEK fabriqué avec consolidation in-situ AFP (pas d'étape secondaire) a montré les mêmes propriétés de consolidation que CF/PEKK fabriqué avec AFP rapide + consolidation au four (en haut). SOURCE :TenCate
Unger note la vitesse AFP de 200 mm/s pour le consolidé in-situ Stratifié CF/PAEK est plus de deux fois celle revendiquée par Henri de Vries, scientifique principal, composites, au Département de technologie des structures du Centre aérospatial des Pays-Bas (NLR, Amsterdam), dans mon article, « Consolidating thermoplastique composite aerostructures in place, Part 2 » :
"Maintenant, nous regardons jusqu'où nous pouvons pousser la consolidation in-situ vitesse AFP tout en maintenant des niveaux de vide et des propriétés mécaniques acceptables dans le stratifié », explique Unger. « Nous avons beaucoup travaillé sur la pose d'un panneau TPC raidi à l'aide de processus automatisés. Maintenant, l'objectif est de construire le niveau de préparation technologique . " Kok dit que TenCate continue de le faire, en travaillant avec des partenaires de l'industrie, y compris des clients et des instituts de R&D. Un exemple était le pylône moteur réalisé avec TC1320 CF/PEKK Ruban adhésif exposé sur le stand de TenCate au JEC 2018. TenCate a travaillé à la fois avec le fabricant de coque de pylône NLR ainsi qu'avec Dutch Thermoplastic Components (DTC), qui a formé des nervures soudées à la coque en tant qu'éléments de renforcement. Bien que cette partie ait été fabriquée à l'aide de l'AFP puis consolidée dans un autoclave, Kok note :« Nous explorons également comment optimiser davantage les bandes pour une consolidation en 2 étapes en utilisant uniquement un ensachage sous vide dans un four au lieu d'un autoclave. »

Ruban Slit CF/LM PEKK, laminé réalisé à l'aide de la pose automatisée de ruban (ATL) et d'une nervure pressée, produit par DTC. SOURCE :www.composites.nl
Unger note que les produits CF/LM PAEK de TenCate utilisés dans le développement et la démonstration de structures d'avions primaires utilisent en effet à la fois de la fibre de carbone non dimensionnée ainsi que fibre de carbone avec dimensionnement . Il dit que même s'il y a cinq ans, il était peut-être rare de voir des rubans préimprégnés LM PAEK, PEKK et PEEK utilisant de la fibre de carbone avec encollage en raison des effets néfastes sur les propriétés mécaniques associées aux ensimages, ce n'est certainement plus le cas aujourd'hui.
Un dernier point soulignant le potentiel de LM PAEK est que le NIAR et la FAA sont en train de compléter la première base de données publique pour un matériau composite thermoplastique , en utilisant le TC1225 CF/LM PAEK de TenCate. La base de données doit être publiée au début de l'année prochaine, et ce matériau a été choisi en raison de ses propriétés mécaniques et de sa facilité de traitement.
Teijin — Un producteur de longue date de CF passe aux TPC
Le producteur de fibre de carbone (CF) Toho Tenax Co. Ltd. (Tokyo, Japon) est désormais renommé à l'échelle mondiale Teijin Carbon, avec trois filiales principales :
- Teijin Carbon Europe
- Teijin Carbon America
- Teijin Carbon Singapour.
Le nom du produit reste Tenax.
« Nous avons passé beaucoup de temps à développer des thermoplastiques il y a 15 à 20 ans », explique Jean-Philippe Canart, auparavant chef de produit semi-produits thermoplastiques pour Toho Tenax Europe et maintenant ingénieur de marché aérospatial pour Teijin Carbon America. « L'une de nos stratégies consistait à développer un ruban thermoplastique unidirectionnel (UD) , que nous avons introduit en 2013 . "
Canart explique les éléments constitutifs de ce développement :« L'une de nos technologies de base est le encollage thermoplastique pour CF , ce qui facilite le traitement de la bande. L'encollage standard CF doit être supprimé en raison des températures de traitement élevées requises pour les thermoplastiques. En plus de la résistance à la température, l'encollage thermoplastique offre également des performances supplémentaires avec une adhérence fibre-matrice dans le composite fini. L'une de nos plus grandes lignes en Europe produit 1 700 tonnes/an de CF équipées du dimensionnement TP. À partir de là, nous avons développé bande UD avec PEEK, PEKK et PPS matrices thermoplastiques pour une utilisation principalement dans des applications aérospatiales, mais nous travaillons également sur des applications pétrolières et gazières et industrielles. »
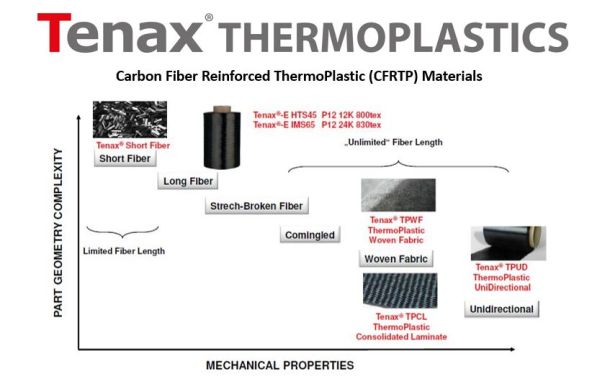
SOURCE :Teijin .
Canart dit que le premier objectif de Teijin avec TPC était le formage à la presse (estampage) de clips et de supports pour l'Airbus A350, à l'aide de tissu CF enduit de PEEK :« Ce fut la première grande vague d'applications aérospatiales. Nous voyons maintenant cela se déplacer vers des pièces plus grandes et plus structurelles produites avec un mélange de stratifiés AFP suivis d'une consolidation par emboutissage. » Canart reconnaît que la consolidation in-situ (ISC) est en développement depuis des décennies, mais soutient que « nous ne la considérons pas encore comme mature. Nous soutenons les projets de R&D et les instituts en développement. Il dit que l'ISC est possible, « mais la question est de savoir à quelle vitesse pouvez-vous fabriquer des pièces ? Et quelle est la robustesse du processus ? » Il pense qu'il faudra 2025-2030 avant que les pièces ISC soient en production pour les cellules commerciales . En attendant, Teijin envisage une expansion des bandes TPC pour les lignes de production en 2 étapes, AFP + emboutissage. « Nous avons déjà investi dans notre ligne de ruban européenne et prenons également en charge de nouvelles capacités de processus telles que le moulage par compression en continu (CCM) . La chaîne d'approvisionnement s'agrandit."
Soutenir la production de masse de TPC — CCM
Moulage par compression continue (CCM) est un procédé dont j'ai parlé en 2010 :« le moulage par compression de qualité aérospatiale ». Il est déposé sous le nom de X-CCM par Performance Polymer Compositesxperion (Markdorf, Allemagne), la société qui a initialement développé et commercialisé le processus il y a plus de deux décennies. X-CCM propose des stratifiés composites thermoplastiques de haute qualité utilisant un processus rapide et quasi continu. « Nous travaillons avec xperion en tant que fournisseur de matériaux », explique Canart. « Il s'agit d'une technologie mature , utilisé pendant de nombreuses années à la fois par Airbus et Boeing . Maintenant, il est en pleine croissance, utilisé pour produire des stratifiés consolidés façonnés. Le CCM est excellent pour le coût, mais la section transversale doit rester constante. »
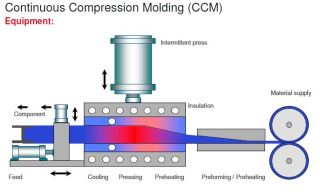
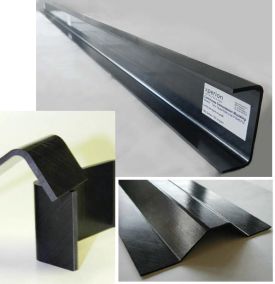
Teijin soutient la croissance des bandes TPC- basé sur des processus de fabrication de pièces comme le moulage par compression continue (CCM) commercialisé par xperion PPC.
SOURCE :Teijin, SAMPE Seattle 2014.
Selon Laurens de la Ossa, directeur des ventes senior pour xperion PPC, « Notre processus X-CCM est maintenant plus avancé, capable de produire des formes plus complexes, y compris des profils asymétriques comme les profils en T et en J . " Il ajoute que le processus peut produire des stratifiés TPC consolidés jusqu'à 24 pouces de largeur. « Nous faisons partie de toute une infrastructure technologique qui évolue vers la production de masse de composites thermoplastiques . Nous avons un processus très élégant pour les pièces TPC consolidées - il n'y a pas d'ensachage sous vide, et nous pouvons traiter des laminés épais de 60 plis et au-delà , 8-10 mm d'épaisseur."
Quel type de pièces X-CCM cible-t-il ? « Les longerons intérieurs du fuselage, les poutres de plancher et autres cadres autour du plancher ou du plafond, les composants structurels et les applications semi-structurelles qui exigent les performances matérielles les plus élevées », explique de la Ossa. « D'ici 2025 , lorsque les nouvelles plates-formes d'avions commenceront à entrer en production, nous atteindrons 6 à 10 fois le volume de matériel annuellement juste pour fournir ce à quoi nous avons répondu avec des devis à ce jour.
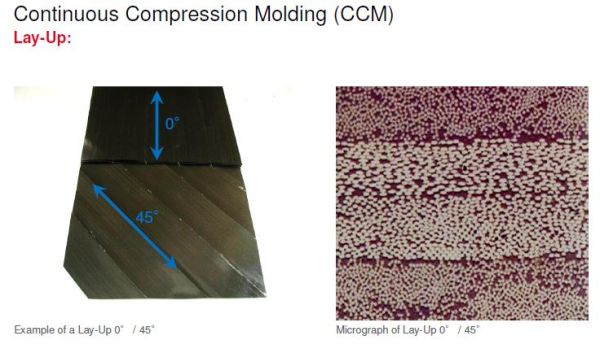
SOURCE :Teijin , SAMPE Seattle 2014
Dans le cadre de cette poussée continue vers une production en volume plus élevé, Teijin se concentre sur la réduction du coût du matériel de bande et l'augmentation de la capacité , dit Canart. Qu'en est-il des demandes de l'industrie pour du ruban plus épais ? Plus précisément, de Vries chez NLR avait déclaré :
« Nous avons déjà développé des rubans avec un grammage de fibre allant de 145 à 200 g/m 2 », répond Canart. « Avec ces produits, une épaisseur de 0,18 mm est déjà tout à fait standard pour nous. Nous avons modifié nos lignes pour cette épaisseur et aussi jusqu'à 0,20 mm, donc je pense que même 0,25 mm ne serait pas un grand saut. »
Et qu'en est-il de la qualité de la bande ? "Nous pensons que tous les rubans doivent être modifiés pour des pièces de meilleure qualité à des vitesses plus rapides", explique Canart. « La teneur en résine peut ne pas correspondre à ce que nécessite la consolidation in situ et la distribution de la résine dans le ruban peut également devoir être optimisée. Le temps et la vitesse de fusion sont si différents pour les différentes résines et procédés. Nous soutenons la poursuite du développement dans divers domaines, notamment les systèmes polymères et l'architecture du ruban , y compris la surface. »
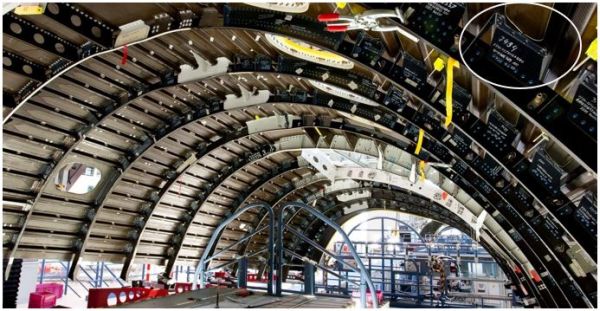
Fuselage de l'Airbus A350 clip fabriqué à partir de stratifiés thermoplastiques TenCate Cetex C/PPS utilisant le tissu tissé thermoplastique Tenax (TPWF). SOURCE :Teijin, Premium Aerotec Group.
Solvay — marché à la fois du PEEK et du PEKK
Les produits thermoplastiques haute performance de Solvay pour les composites incluent Ketaspire PEEK , Novaspire PEKK , Radel polyphénylsulfone (PPSU ) et le sulfure de polyphénylène Ryton (PPS ). Dans une déclaration soumise par Solvay, la société affirme que ces polymères sont produits à des échelles industrielles qui permettra d'envisager des applications composites aérospatiales à grand volume et peut être utilisé pour produire un préimprégné de haute qualité .
Solvay fournit actuellement Unitape APC préimprégnés avec des polymères PEEK et PEKK, avec des tarifs principalement différenciés par le coût de la fibre sélectionnée plutôt que le polymère lorsqu'ils sont produits et utilisés à des volumes élevés. Par conséquent, il pense que la sélection de la matrice thermoplastique à utiliser pour une application donnée sera conduite par les préférences du client . Les facteurs affectant ce choix incluent les performances de température, les performances mécaniques, le traitement de fabrication des pièces, la disponibilité de la base de données de matériaux et l'expérience de la main-d'œuvre, pour n'en nommer que quelques-uns. Le point de vue de Solvay est que le PEKK et le PEEK répondent à un besoin sur le marché et qu'elle est en mesure d'offrir des préimprégnés renforcés de fibres de haute qualité et à prix comparable, indépendamment du polymère sélectionné.
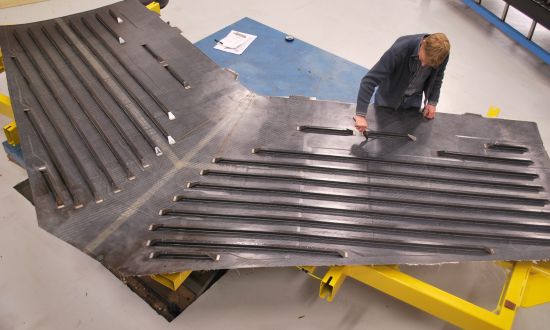
Queue horizontale de l'avion démonstrateur fabriqué par GKN Fokker utilisant
Solvay APC(PEKK-FC)/AS4D. SOURCE :GKN Fokker.
Ainsi, pour les thermoplastiques, comme pour tous les autres composites, les choix de matériaux et de procédés ne sont pas limités. En fait, ils semblent s'étendre. Lequel prendra l'ascendant dans la future production d'avions ? Cela reste à voir. CW continuera à regarder et à rapporter ce que nous voyons.
Résine
- Qu'est-ce que le moulage par compression et comment ça marche ?
- Moulage par compression :comment ça marche
- PEEK à haute viscosité pour le moulage par injection et l'extrusion
- Partenaire Victrex et Bond pour l'impression 3D de pièces PAEK
- Thermoplastiques surmoulés thermodurcissables, cycle de 2 minutes, une cellule
- Les bandes continues, D-LFT se rencontrent dans un nouveau processus de moulage par compression
- TPAC et TPRC développent un procédé de recyclage des composites thermoplastiques
- EconCore s'associe à MEAF sur les noyaux en nid d'abeille thermoplastique continu
- La société RTP développe des composés thermoplastiques légers et résistants