Outillage additif hybride grand format :des moules plus légers, plus rapides et moins coûteux pour les grandes pièces
Depuis plus de trois décennies, l'aviation commerciale a de plus en plus adopté les matériaux composites. En fait, plus de la moitié des composants structurels critiques de plusieurs modèles d'avions commerciaux majeurs sont aujourd'hui des composites. À mesure que l'utilisation de ces matériaux a augmenté en termes de volume et de taille des pièces, il est devenu de plus en plus difficile de construire des outils - en particulier des outils abordables - pour prototyper et fabriquer plus rapidement ces pièces. Par exemple, les ailes de l'A350 XWB d'Airbus SE (Leiden, Pays-Bas) mesurent chacune 32 mètres de long sur 6 mètres de large et représentent certaines des plus grandes structures aéronautiques composites jamais produites.
« Il existe maintenant des technologies de fabrication tellement révolutionnaires sur le marché que nous pouvons nous attendre à de grandes étapes dans l'évolution de l'outillage, nous aidant à relever les défis auxquels nous sommes confrontés dans le développement de composants d'avions composites », note M. Pilar Muñoz Lopez, ingénieur en fabrication de composites chez Usine d'Airbus à Illescas, en Espagne. « Il est crucial pour nous d'étudier ces technologies, capacités et limitations afin que nous puissions être prêts pour l'avenir. »
Étant donné que l'outillage représente une proportion importante des coûts totaux du programme pour les pièces d'aérostructure, et étant donné la taille croissante de ces pièces, de nouvelles options d'outillage avec des coûts et des délais de livraison inférieurs sont nécessaires. Une étude intéressante sur l'outillage hybride, grand format et fabriqué de manière additive (LFAM) pour les pièces d'aérostructure de prototype et de production à faible volume a récemment été réalisée par Airbus, Northrop Grumman Aeronautics Systems - Aerospace Structures Business Unit (Clearfield, Utah, États-Unis) et l'Université du Dayton Research Institute (UDRI, Dayton, Ohio, États-Unis) avec des résultats encourageants.
Dompter les problèmes de dilatation thermique
La majorité des aérostructures en plastique renforcé de fibres de carbone (PRFC) sont produites à partir d'un préimprégné à matrice époxy. Pour mouler de telles pièces, l'outillage doit résister à des températures de durcissement au four ou à l'autoclave jusqu'à 180 °C/356 °F. De plus, étant donné le très faible coefficient de dilatation thermique (linéaire) du CFRP (CLTE ou CTE), il est essentiel de faire correspondre - aussi étroitement que possible - les outils et les matériaux de moulage CLTE à des températures ambiantes et élevées. Cela garantit que les moules conservent leurs dimensions afin que les pièces résultantes répondent également aux exigences dimensionnelles. Pour éviter toute déformation ou contrainte dans les structures finales, il est également important d'éviter d'utiliser un matériau d'outillage qui refroidit plus rapidement que le matériau de la pièce. En conséquence, les outils les plus couramment utilisés pour mouler de grandes aérostructures en CFRP sont fabriqués à partir de CFRP lui-même ou d'Invar, un alliage ferreux de nickel et de fer connu pour son faible CLTE. Les deux sont coûteux et peuvent avoir des délais de livraison importants. De plus, l'Invar est difficile et long à usiner et lourd à expédier. Alors que les outils en acier ou en aluminium peuvent réduire les coûts, leurs valeurs CLTE relativement plus élevées limitent leur utilisation dans de nombreuses applications, en particulier lors du moulage de pièces grandes ou longues.
De nombreuses études des secteurs public et privé ont évalué des outils fabriqués de manière additive imprimés dans des matériaux thermoplastiques et ont conclu qu'ils offrent potentiellement des avantages, notamment des coûts inférieurs et des délais de production plus courts pour produire des composites stratifiés thermodurcissables. Malheureusement, l'outillage LFAM à base de polymère présente des problèmes tels que la porosité de l'outil, qui peut entraîner une perte de vide importante aux températures/pressions de durcissement. La résolution de ce problème nécessite des retouches de remplissage d'outils supplémentaires et des revêtements de surface. Les valeurs CLTE hautement anisotropes représentent un défi encore plus important, en raison de l'alignement de la matière première dans le plan pendant l'extrusion/l'impression, ce qui peut entraîner des différences d'expansion/contraction 5 à 10 fois plus importantes sur l'axe Z que sur les axes d'impression X et Y. Cela rend difficile l'obtention de pièces dimensionnellement précises de manière répétable et reproductible, en particulier lorsque les pièces sont volumineuses, ont un rapport hauteur/largeur élevé et/ou présentent des surfaces complexes.
« Tous ceux qui s'intéressent à l'outillage additif se sont heurtés aux mêmes problèmes de porosité et de dilatation thermique incontrôlée avec peu de moyens efficaces de résoudre ces problèmes », explique Scott Huelskamp, chef d'équipe UDRI, développement de processus de fabrication avancés, Division des matériaux de structure. "Il y a beaucoup de gens qui veulent utiliser des outils de FA, mais ils attendent que quelqu'un résolve ces problèmes."
Compte tenu du potentiel de la FA pour réduire les coûts d'outillage et les délais, l'industrie a concentré des efforts considérables sur la résolution des problèmes d'expansion en explorant de nouveaux matériaux imprimables, des modifications du matériel d'impression et des approches de modélisation innovantes. Par exemple, certains groupes ont développé une « valeur de compensation » pour la conception d'outils de FA pour traiter les différentiels CLTE. Cependant, Huelskamp note que déterminer qui valeur de compensation à utiliser est difficile et sujette à erreur. En outre, de telles approches se sont révélées inefficaces pour les outils à cavité femelle et les outils dotés de fonctions de piégeage sur toute leur longueur qui créent des conditions de verrouillage de matrice capables d'endommager les pièces lors du cycle thermique dans l'outil.
"Il n'y a aucun facteur de compensation qui va résoudre ce genre de problème", ajoute-t-il. « À ce jour, aucune étude d'outillage AM n'a pleinement répondu au besoin de valeurs CTE isotropes basses à température élevée. Sans cette caractéristique, les tailles et géométries des outils seront toujours limitées, et les outils plus grands souffriront d'erreurs dimensionnelles plus élevées aux températures de durcissement. »
Dans le but d'essayer de nouvelles approches pour résoudre les problèmes d'outillage LFAM, un projet de 18 mois a été entrepris par plusieurs sociétés membres sous les auspices de l'Institute for Advanced Composites Manufacturing Innovation (IACMI, Knoxville, Tenn., États-Unis) et soutenu par les États-Unis. Département de l'énergie et de l'emploi Ohio (Columbus, Ohio). L'équipe était dirigée par l'UDRI et comprenait Airbus et Northrop Grumman. Ces organisations avaient déjà collaboré à d'autres recherches, à la fois à l'intérieur et à l'extérieur de l'IACMI, et connaissaient donc les capacités de chacune.
Approche « de la force brute »
L'UDRI avait déjà une expérience considérable dans les études d'outillage AM et est un membre actif d'America Makes (Youngstown, Ohio, États-Unis), le consortium AM américain. De plus, l'institut avait effectué des recherches pour l'US Air Force impliquant des structures AM avec des supports métalliques, et a travaillé avec Cincinnati Inc. (Harrison, Ohio, États-Unis), producteur d'imprimantes de fabrication additive Big Area (BAAM), sur de l'outillage AM pur.
« Nous avions également travaillé avec des mélangeurs personnalisés sur de nouvelles matières premières pour les imprimantes 3D, mais rien de ce que nous faisions ne semblait faire beaucoup de progrès, et nous ne savions pas que quelqu'un d'autre avait plus de succès que nous », se souvient Huelskamp. « C’est à ce moment-là que nous avons eu l’idée d’aborder le problème différemment. Si nous ne pouvions pas changer le comportement des matériaux AM ou prédire ce comportement directement , alors peut-être pourrions-nous les forcer à se comporter comme nous le voulions indirectement . " Adoptant ce que Huelskamp appelle une approche de « force brute », l'UDRI a proposé une étude LFAM hybride qui produirait un outillage d'aérostructure en appliquant des méthodes conventionnelles Peaux de visage CFRP en composite thermoplastique Noyaux AM.
Les objectifs du projet étaient simples :trouver une méthode moins coûteuse et plus rapide pour fabriquer de gros outils pour les aérostructures. L'équipe a recherché une option qui réduisait les coûts de 50 % et a produit au moins 10 prototypes acceptables ou des pièces de production à faible volume pour les tests ultérieurs
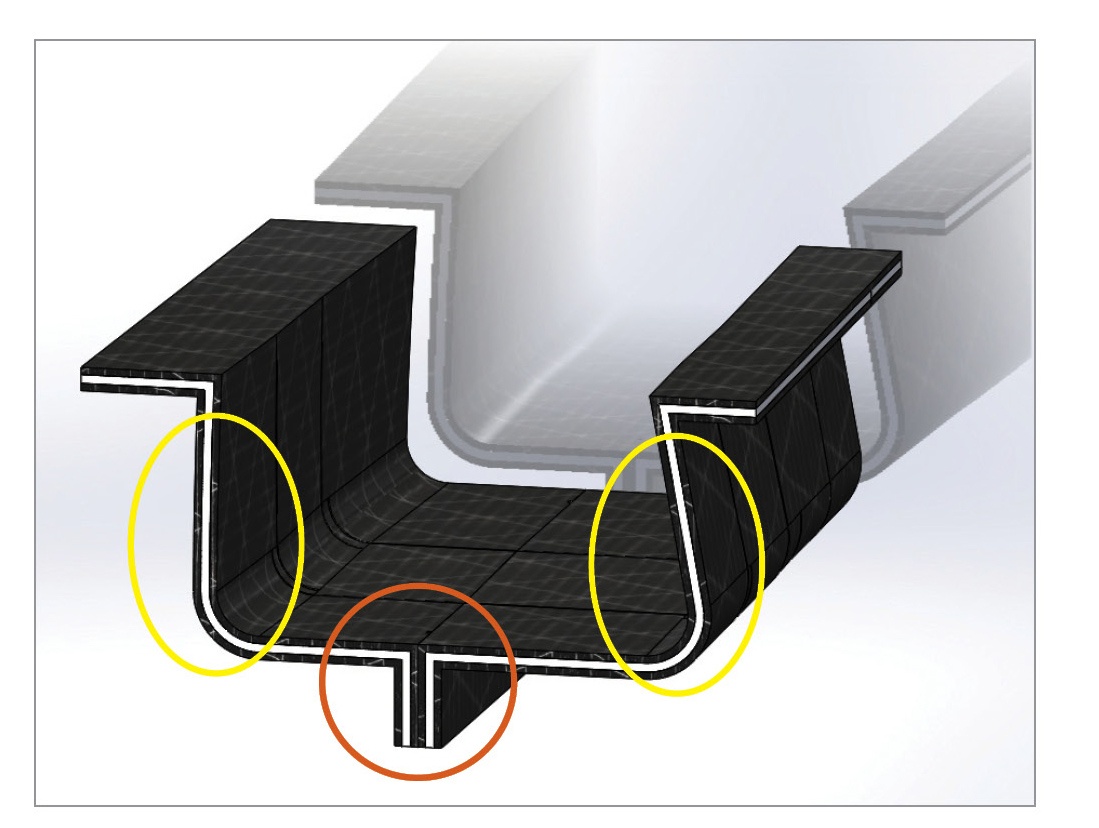
L'équipe a décidé d'utiliser une structure sandwich pour produire un outillage simple face pour une section d'un longeron d'aile générique en utilisant les données d'outils d'Airbus. À part la production d'outillage pour mouler uniquement une section du longeron en C à grande échelle - en raison des limitations d'espace à l'installation UDRI - aucun changement de conception majeur n'a été apporté.
Un outil femelle a été conçu pour garantir que la géométrie de la pièce critique a été formée à l'aide de surfaces usinées. Cet outil de capuchon de longeron avait un léger angle vers l'intérieur qui créait un dépouillement négatif et une condition de verrouillage de matrice, étant un outil monobloc. Cela a conduit les chercheurs à modifier la conception en un outil divisé qui a été scellé à l'aide de joints/cordstock. Pour atténuer les risques, l'équipe a commencé avec un outil sous-échelle de 0,6 mètre/2,0 pieds pour prouver le concept. Une fois que le processus de développement de l'outil et les pièces prototypes produites sur cet outil ont été testés et trouvés fonctionnels, l'équipe a construit un outil plus grand de 3,3 mètres/11 pieds de long pour mouler une plus grande section du longeron pour les tests de prototype.
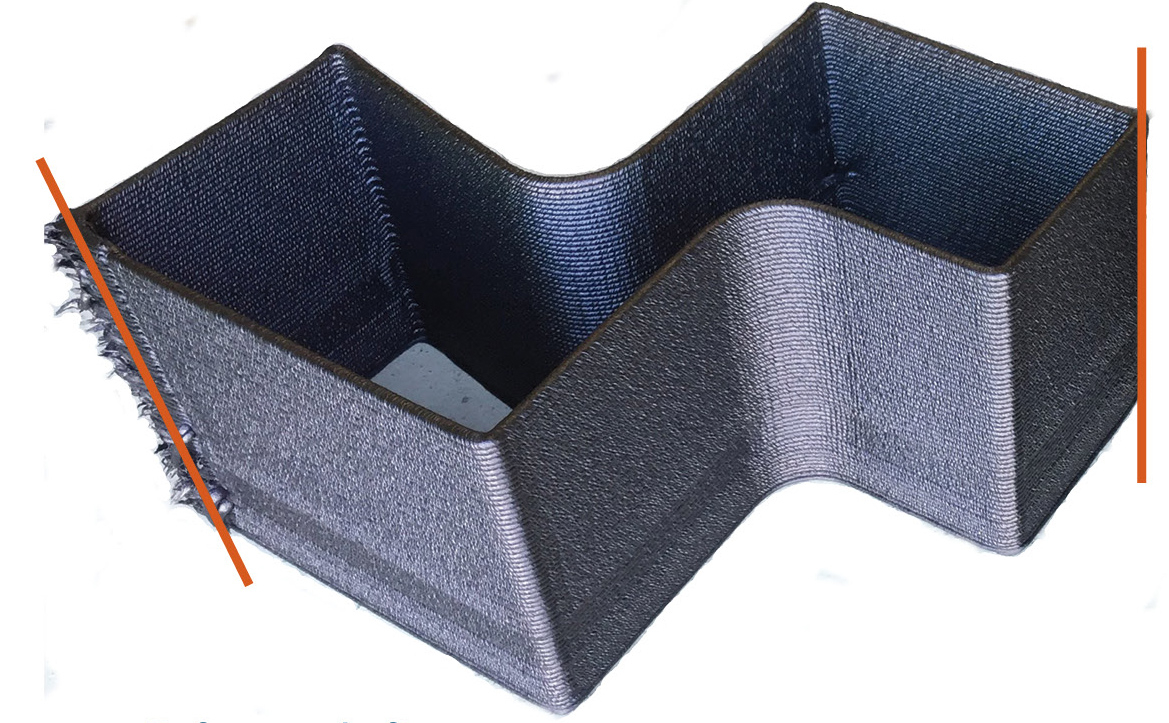
Étant donné que l'outillage CFRP a une valeur CLTE si faible, qu'il est plus léger que l'Invar et que l'outil était destiné aux prototypes/pièces de production à faible volume, l'équipe a décidé d'utiliser des peaux de face CFRP pour contraindre le noyau AM. Les peaux ont été fabriquées avec un préimprégné d'outillage époxy Hextool M81 de Hexcel (Corp., Stamford, Connecticut, États-Unis).
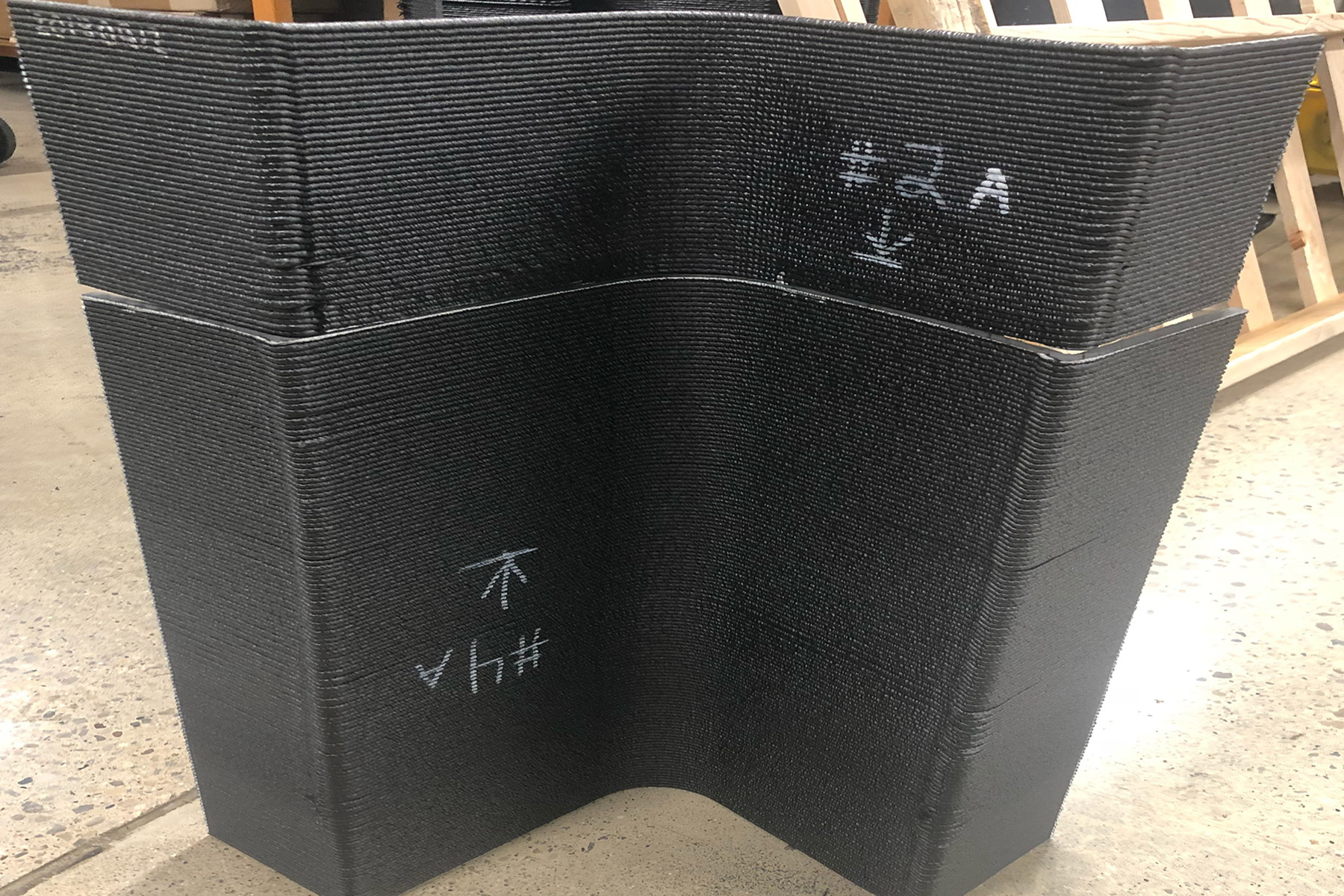
L'image du haut montre une section de la moitié droite de la sous-échelle, l'outil imprimé BAAM avec des lignes rouges indiquant les lignes de coupe après l'impression. L'image du bas montre la moitié droite de l'outil après le collage des sections. Crédit photo :Institut de recherche de l'Université de Dayton.
Le format du matériau était un tapis de 2 000 grammes par mètre carré/59 onces par mètre carré de fibre de carbone hachée imprégnée d'époxy durci Hexcel 8552. Ce matériau est souvent utilisé pour l'outillage composite en raison de ses propriétés presque isotropes, qui permettent un usinage post-moulage sans mouvement de l'outil qui pourrait autrement être causé par la relaxation des contraintes résiduelles.
Étant donné que le noyau serait imprimé sur une imprimante Cincinnati Inc. BAAM 1000 chez Additive Engineering Solutions (Akron, Ohio, États-Unis), et étant donné que UDRI et Cincinnati avaient une expérience significative du travail avec le polyétherimide thermoplastique à haute température (PEI), ils ont sélectionné PEI renforcé à 20 % de fibres de carbone courtes (Thermocomp EX004EXAR1 Ultem) de SABIC (Riyad, Arabie saoudite) pour imprimer un noyau de forme proche du filet. (La présence de fibres de carbone stabilise le polymère pendant l'impression et l'empêche de s'affaisser; dans la structure finie, les fibres réduisent le CLTE dans le sens de l'impression.) Pour maintenir les coûts bas, le noyau a fonctionné comme le maître d'outillage et les peaux de visage ont été laminées directement au noyau sans adhésif, mais avec quelques modifications à la surface du noyau qui est couverte par la propriété intellectuelle (PI) développée au cours du projet. Cette approche était efficace, sans délaminage même après plusieurs cycles thermiques.
Fabrication condensée
Dans la fabrication conventionnelle d'outillage CFRP d'aérostructure, un maître à faible coût est d'abord créé. Cela implique généralement de coller ensemble des blocs de planche à outils dans un four ou un autoclave, puis d'usiner la structure monolithique à la géométrie de la pièce souhaitée. Le matériau d'outillage est ensuite mis en place, ensaché et durci sur le maître dans un autoclave. Après le démoulage et le nettoyage, une structure de support est collée à l'outil et la surface de l'outillage est à nouveau usinée pour assurer une bonne tolérance géométrique et un bon état de surface.
Avec l'outillage de FA hybride, l'équipe a développé un processus de fabrication condensé pour réduire les délais et les coûts. Tout d'abord, un noyau de forme proche du filet (tool master) a été imprimé en 3D (en fibre de carbone courte/PEI). Ensuite, le préimprégné d'outillage CFRP a été directement laminé sur les deux côtés du noyau (avec des réductions à chaud entre les plis un, quatre et sept selon les recommandations du fournisseur). La structure entière a ensuite été mise sous vide et durcie à l'autoclave.
Procédé de fabrication condensé pour l'outil de longeron en C de sous-échelle.
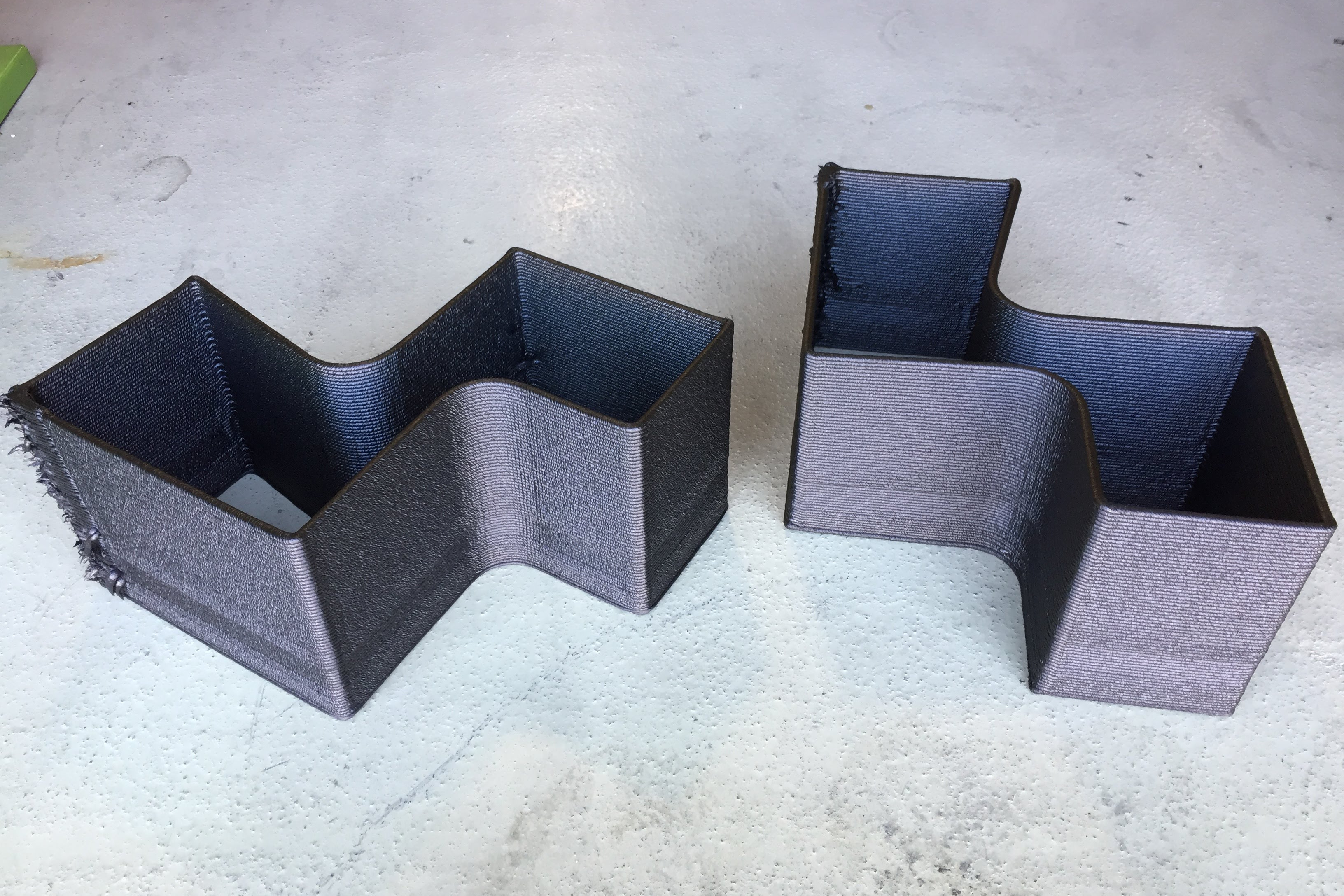
Étape 2 :Découpez l'imprimé BAAM au milieu et dans les moitiés gauche et droite.
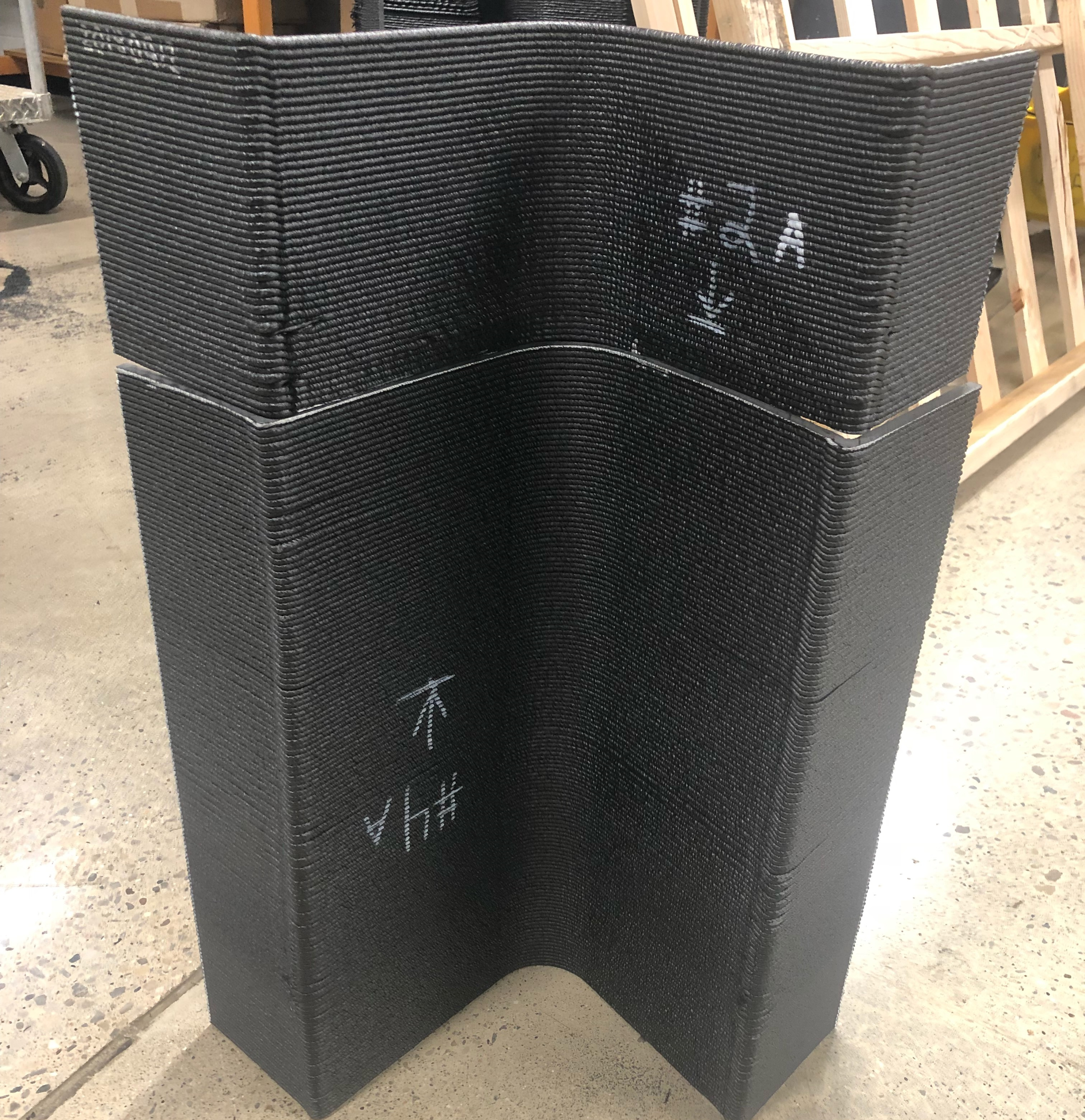
Étape 3 :Collez l'impression BAAM pour obtenir la longueur requise et laissez durcir.
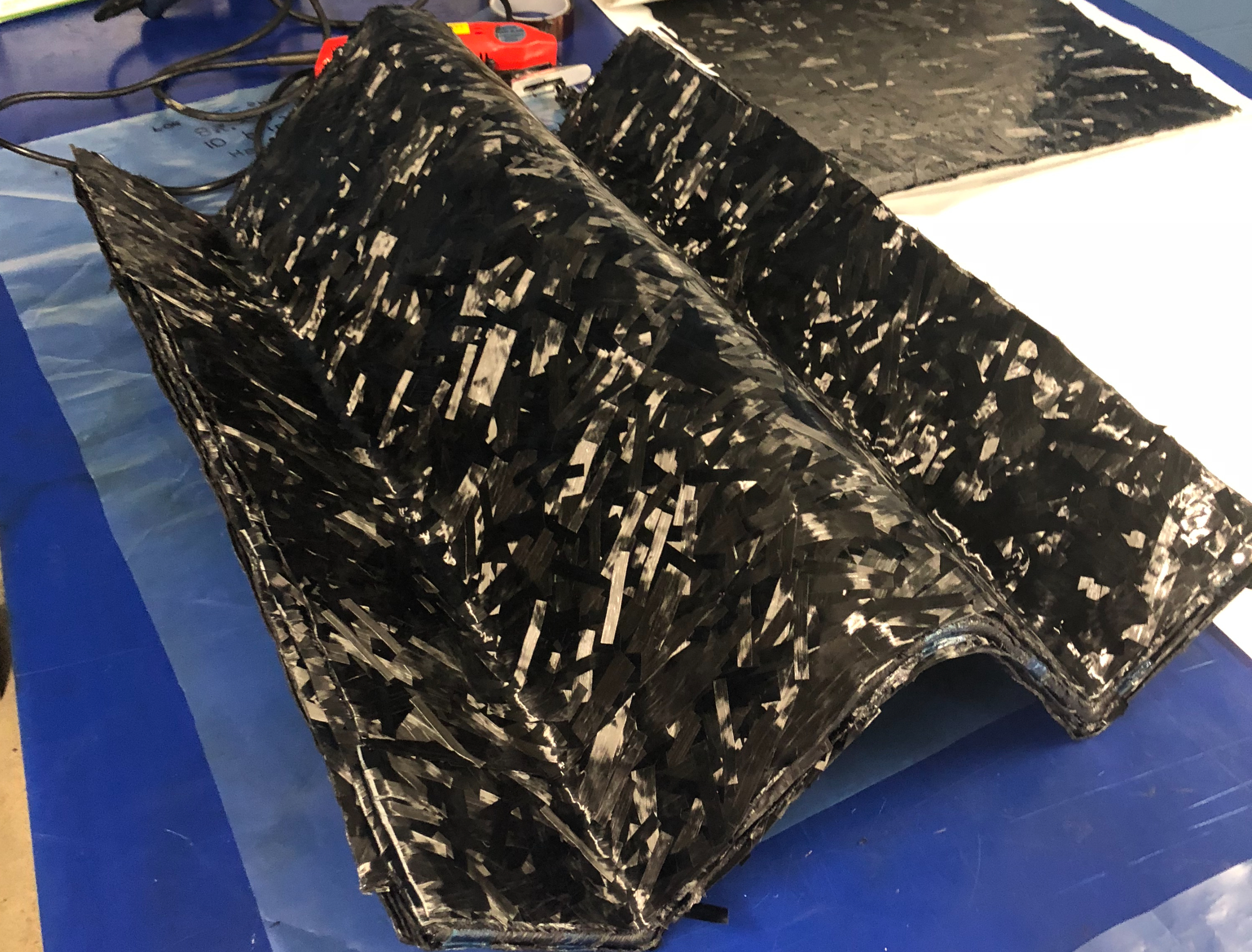
Étape 4 :Laminé préimprégné de l'outillage sur les deux côtés du noyau avec des démoulages à chaud selon les instructions du fabricant.
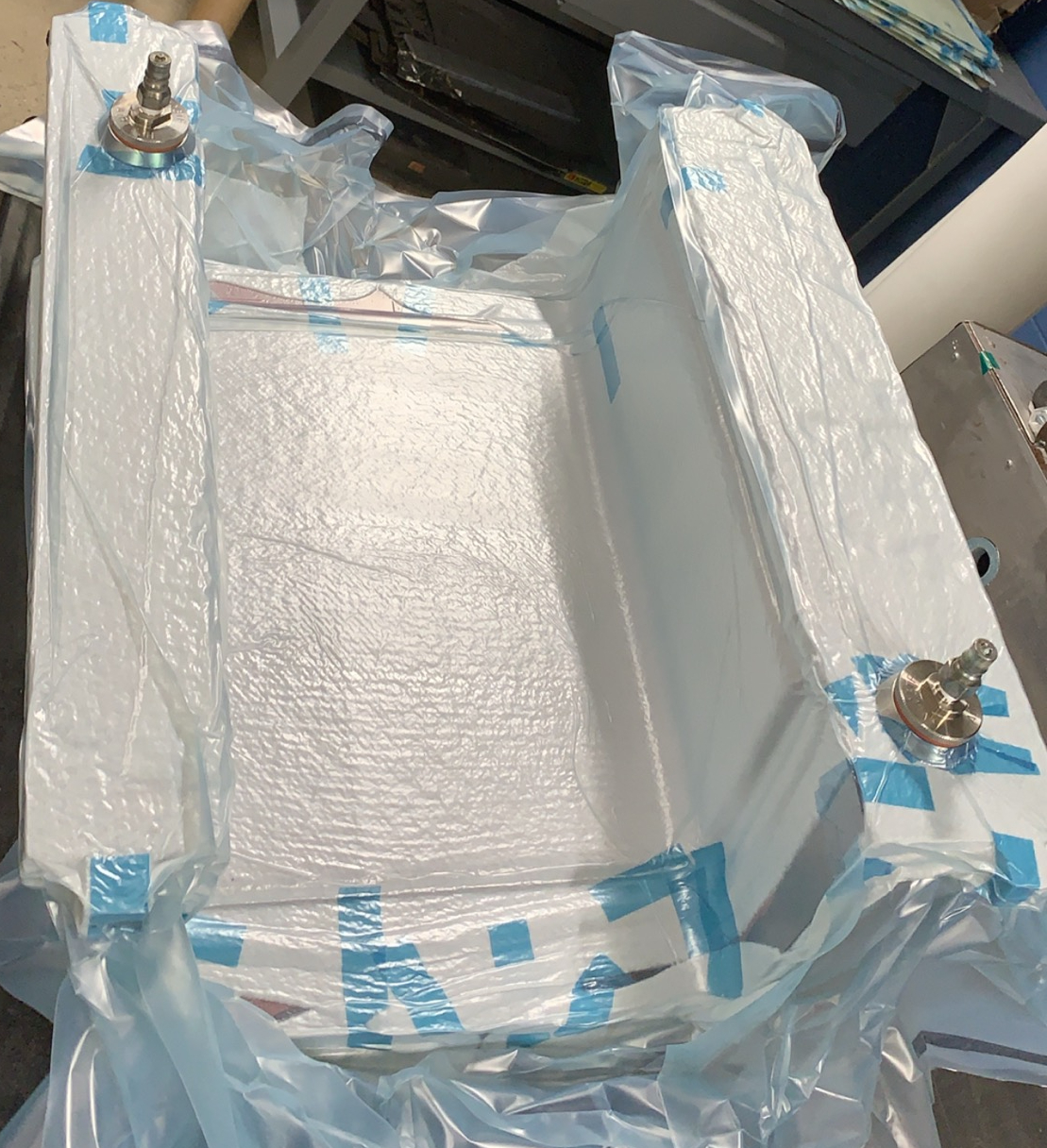
Étape 5 :Sac sous vide et durcissement en autoclave.
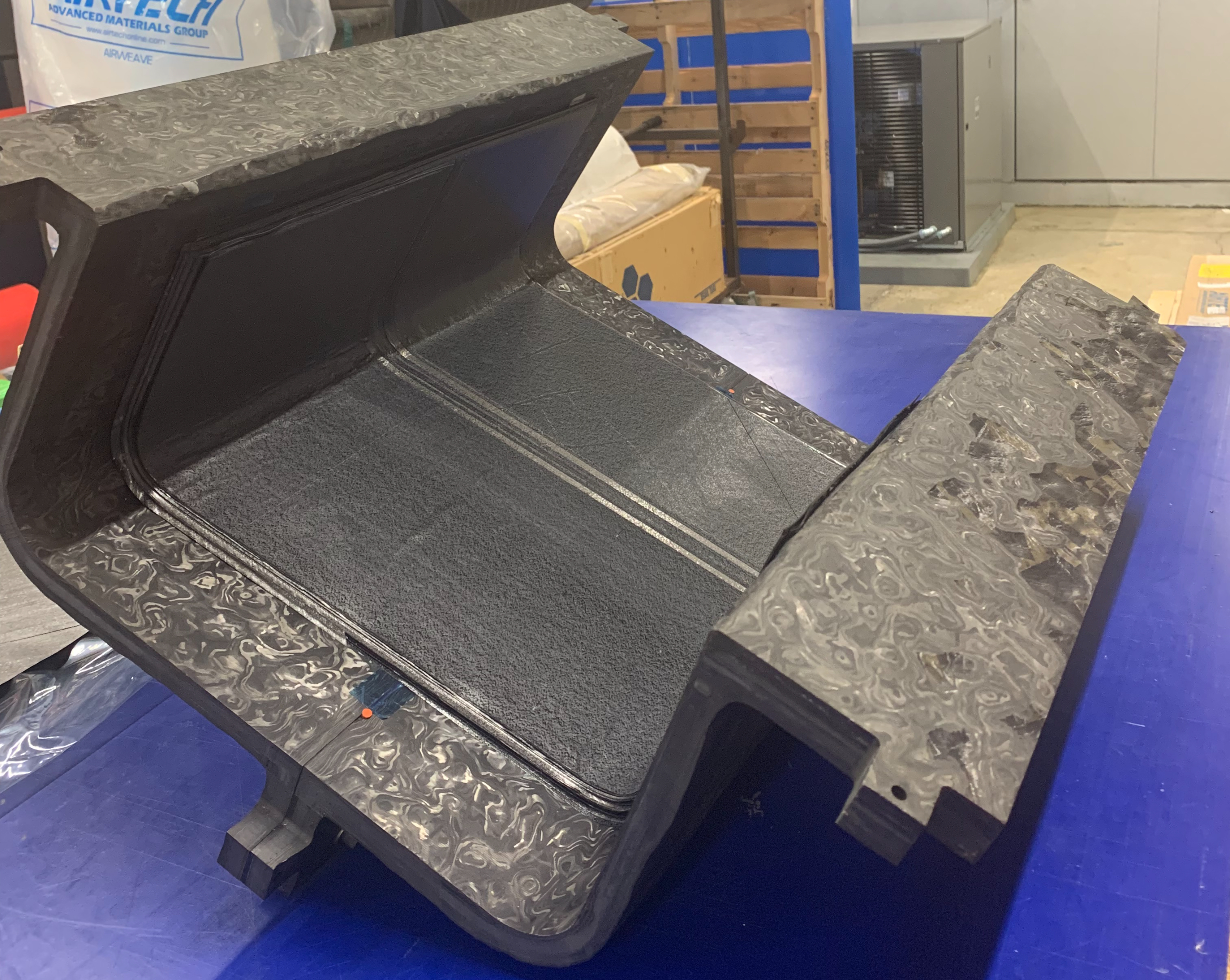
Étape 6 :Outil durci à la machine pour obtenir les dimensions finales et la finition de surface.
Précédent SuivantUne bonne adhérence a été obtenue entre le noyau PEI et les peaux époxy pendant le durcissement du stratifié, de sorte que l'adhésif n'était pas nécessaire. Non seulement les peaux CFRP sont non poreuses et plus durables que le noyau AM, mais elles contraignent également physiquement le mouvement du noyau pendant les excursions de température en raison de leurs valeurs CLTE beaucoup plus basses. Une seule cure et une seule opération d'usinage — deux dépenses majeures au cours des traditionnelles production d'outils - étaient nécessaires pour obtenir les dimensions finales et la finition de surface. De plus, aucun support n'était nécessaire, en raison de la structure en sandwich et de la forme de l'outil, qui comprenait des brides de retour en haut du moule pour la rigidité latérale et un joint boulonné au centre du moule pour la rigidité verticale - éliminant ainsi une opération de collage.
Défis initiaux
Les chercheurs ont été confrontés à plusieurs défis gérables avec le nouveau processus.
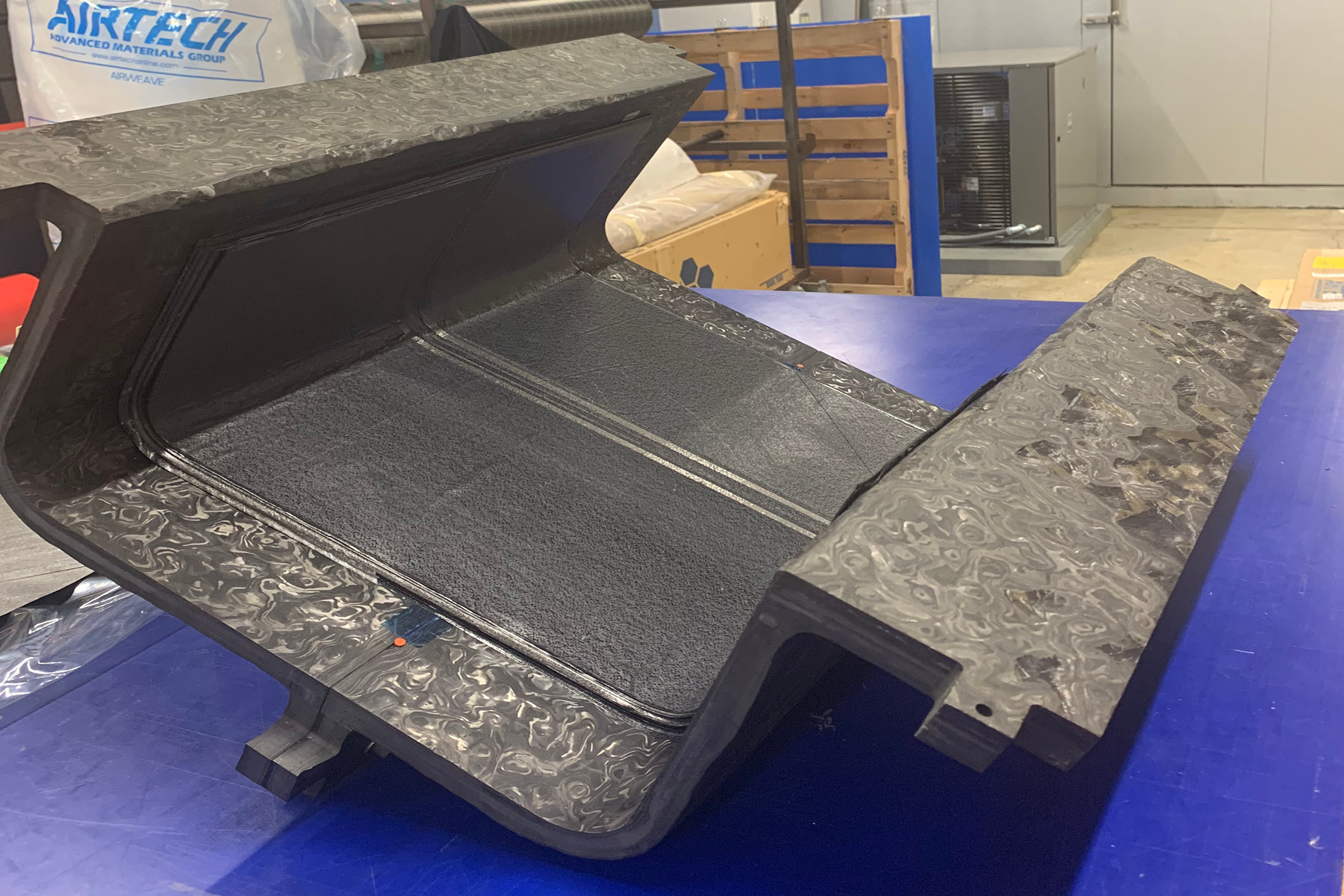
Pour faciliter la fabrication sur le BAAM, la direction de fabrication préférée pour le noyau était l'impression de la section transversale sous forme de construction verticale. Ce n'était pas un problème pour l'outil de 0,6 mètre; cependant, pour le plus grand outil, 3,3 mètres dépassaient ce que le BAAM 1000 pouvait imprimer verticalement. En raison des limitations de l'espace d'impression de l'axe Z de l'imprimante, les chercheurs ont choisi de réduire de moitié les deux outils de sous-échelle sur leur longueur, puis de les diviser à nouveau en sections gauche et droite (pour résoudre les problèmes de contre-dépouille du longeron et faciliter le démoulage).
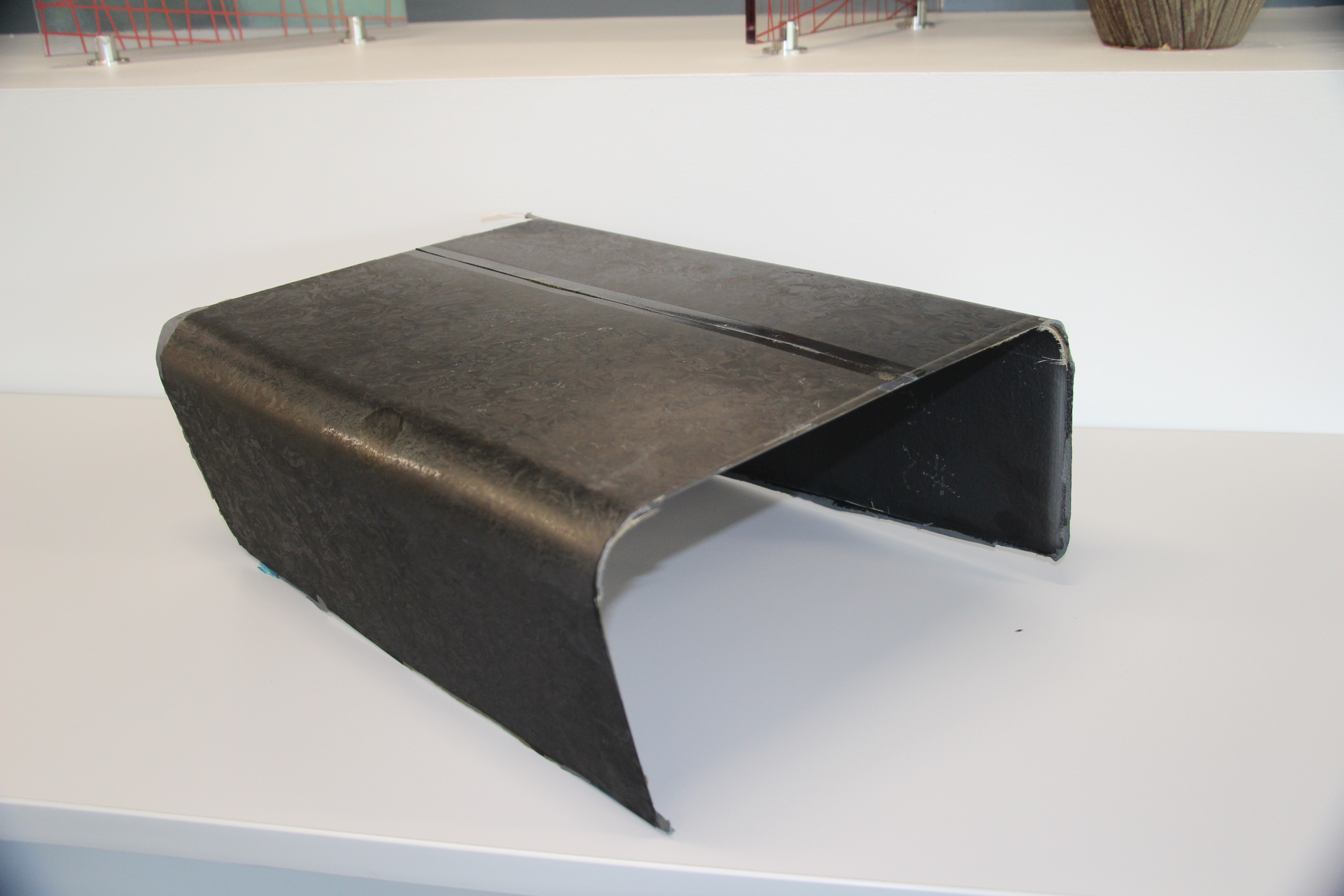
Pour augmenter l'efficacité de l'impression, les sections d'outils ont été imprimées dos à dos, puis coupées en morceaux à droite et à gauche. Pour atteindre la longueur de 3,3 mètres, les deux sections de droite ont été collées ensemble, suivies des deux sections de gauche à l'aide de l'adhésif époxy Loctite EA9394 de Henkel Corp. (Rocky Hill, Connecticut, États-Unis). L'équipe a laissé le noyau AM non usiné, estimant que c'était essentiel pour obtenir de faibles coûts d'outillage et des délais d'exécution courts, ainsi que pour créer un verrouillage mécanique entre le noyau AM et les peaux CFRP de chaque côté. La face arrière de chaque moitié d'outil a été stratifiée avec cinq plis de préimprégné tandis que la face avant a été stratifiée avec neuf plis pour fournir un matériau supplémentaire qui pourrait être retiré pendant l'usinage post-durcissement.
Résultats préliminaires
En plus de contrôler le CLTE du noyau AM, le préimprégné a fourni une surface sans piqûres qui a maintenu l'intégrité du vide sans avoir besoin de mastic/revêtement. Cette approche a connu un tel succès qu'elle a permis l'utilisation d'une conception d'outil en plusieurs pièces scellée avec un joint, ce qui, selon les chercheurs, n'avait pas encore été démontré dans l'outillage AM utilisé à haute température. De plus, la masse de l'outil a été considérablement réduite ; l'outil de sous-échelle correspondait à un tiers du poids calculé pour une conception Invar comparable. Non seulement les outils CFRP plus légers sont plus faciles à manipuler et à stocker sur des racks, mais ils nécessitent également des cycles de chauffage/refroidissement de l'autoclave plus courts. Sur un outil pour mouler le longeron en C à grande échelle, cet avantage de poids pourrait faire la différence entre être inférieur ou supérieur aux limites de poids du portique/grue dans certains espaces de fabrication.
Il est important de noter que le coût de l'outil hybride de 0,6 mètre a été calculé lors de la fabrication, à l'aide des taux de main-d'œuvre standard de l'industrie, à 24 136 USD, avec une répartition d'environ 50/50 entre les coûts d'usinage et les coûts d'impression/laminage. En revanche, un outil Invar identique a été coté à 46 775 USD, soit une économie de près de 50 %. Les coûts de l'outil de 3,3 mètres ne sont pas complets, mais devraient générer environ 30 % d'économies sur une base coût/longueur unitaire, car les coûts de matériau/d'impression évoluent de manière linéaire, mais les coûts d'usinage bénéficient d'une économie d'échelle qui réduit son impact. L'approche hybride a produit des outils qui répondaient aux exigences de performance opérationnelle d'Airbus et de Northrop Grumman et est considérée comme une alternative viable à l'Invar pour un outillage de prototype rapide ou à faible utilisation. L'étude de la durée de vie de l'outil ne faisait pas partie de cette étude, mais s'étendrait probablement considérablement au-delà des 12 cycles qui ont été démontrés.
Le programme a été prolongé de 18 à 30 mois, mais il reste encore des domaines dans lesquels des études supplémentaires sont nécessaires, comme la compréhension de la différence entre la géométrie finale du noyau telle qu'imprimée et celle prédite dans les modèles CAE. L'équipe souhaite également améliorer la précision prédictive afin que suffisamment de plis soient ajoutés dans les zones critiques pour s'assurer qu'il n'y a pas de perforation pendant l'usinage. Néanmoins, l'équipe a considéré qu'il s'agissait d'un projet réussi avec des opportunités considérables pour les futurs outils LFAM.
« Northrop Grumman est impatient de construire une pièce de démonstration de longeron de 3 mètres à l'aide de l'outil hybride de 3,3 mètres de long construit par UDRI et de notre propre processus automatisé de formation de raidisseurs (ASF) pour évaluer la durabilité et la stabilité dimensionnelle de l'outil », ajoute Vern Benson, membre technique de Northrop Grumman.
Résine
- Evonik, développe des solutions additives pour développer des matériaux d'impression 3D pour le processus STEP
- Henkel propose une plate-forme de matériaux pour la fabrication additive
- Essentium et Lehvoss s'associent pour développer des matériaux pour la fabrication additive
- Nouveau nylon 6 thermostabilisé pour les groupes motopropulseurs hybrides et électriques
- Trelleborg annonce un nouveau distributeur pour les matériaux d'outillage
- UAMMI, Impossible Objects fabrique des pièces composites pour l'U.S. Air Force
- Partenaire Victrex et Bond pour l'impression 3D de pièces PAEK
- AeroLas explore une nouvelle technologie de filage pour le fil hybride thermoplastique
- Conseils pour les moules d'impression 3D