Fabrication de structures périodiques 3D basées sur des nanoshells par processus de modélisation à l'aide de ZnO dérivé de la solution
Résumé
Les méthodes de fabrication d'une nanostructure périodique 3D avec des propriétés excellentes et uniques pour diverses applications, telles que les cristaux photoniques et phononiques, ont suscité un intérêt considérable. Des processus de modélisation utilisant des cristaux colloïdaux ont été proposés pour créer facilement des structures 3D à base de nanoshell sur une grande surface. Cependant, il existe des limitations techniques dans la conception structurelle, ce qui entraîne des difficultés pour la flexibilité structurelle. Ici, nous démontrons une combinaison de processus de nanostructuration et d'infiltration de champ de proximité utilisant du ZnO dérivé de la solution pour une structure périodique 3D à base de nanoshell avec une flexibilité structurelle et une contrôlabilité élevées. Un processus unique d'infiltration d'un matériau dérivé d'une solution dans un modèle polymère préparé par un processus de nanomotif de champ de proximité permet la fabrication d'une couche préformée qui fonctionne comme une couche protectrice pour le modèle et un cadre pour la structure inverse. Par la suite, ce processus montre la contrôlabilité de l'épaisseur des nanocoquilles et une amélioration significative du facteur de retrait de la hauteur de la structure (16 %) par rapport à ceux d'une méthode d'infiltration sans vide précédente (34 %). La méthode proposée offre une contrôlabilité et une flexibilité élevées dans la conception des tailles structurelles, conduisant à un développement ultérieur vers des structures 3D à base de nanoshell pour diverses applications, y compris les dispositifs énergétiques et les capteurs.
Contexte
Les nanostructures périodiques tridimensionnelles (3D) ont reçu beaucoup d'attention en raison de leurs propriétés excellentes et uniques. Le potentiel de cette technologie est un domaine en développement rapide qui est prometteur dans diverses applications, notamment les cristaux photoniques (PhC) [1,2,3], les cristaux phononiques (PnC) [4], les matériaux de batterie [5, 6] et les canaux microfluides [sept]. La recherche a montré que la périodicité structurelle peut être obtenue en utilisant diverses méthodes de fabrication [8,9,10,11] avec une contrôlabilité et une flexibilité élevées, qui sont des caractéristiques très importantes pour cette technologie. Le processus de création de modèles fournit une procédure simple par rapport aux approches ascendantes traditionnelles, utilisant une structure périodique 3D comme modèle composé de sphères colloïdales auto-assemblées ou d'un photopolymère suivi d'une infiltration de matériaux inorganiques et d'un retrait du modèle [9, 12, 13, 14 ,15,16,17,18,19]. Bien que des procédés sous vide avec dépôt de couche atomique (ALD) suivi d'un dépôt chimique en phase vapeur (CVD) aient été utilisés comme techniques d'infiltration, une surcouche en excès - qui se forme sur le modèle après l'infiltration - nécessitera une gravure ionique réactive (RIE) supplémentaire pour l'éliminer [ 9, 18, 19]. En revanche, un processus sans vide avec électrodéposition [7, 12, 20] et réaction sol-gel [13, 21, 22, 23] permet la création de fines structures inverses et a démontré les propriétés optiques des structures périodiques 3D résultantes composées de ZnO, Cu2 O et TiO2 [13, 20, 23]. De plus, les processus sans vide présentent les avantages d'une rentabilité et d'un temps de traitement plus court.
Le ZnO est un matériau semi-conducteur prometteur doté de propriétés optiques et électriques exceptionnelles. De plus, la stabilité chimique et thermique [24] fait du ZnO un excellent candidat pour diverses applications telles que les PhC, les capteurs et les électrodes transparentes [13, 14, 24]. De plus, le ZnO dopé à l'Al a également montré des performances élevées dans le domaine des dispositifs thermoélectriques sans avoir besoin d'éléments toxiques ou rares [25, 26].
Pendant ce temps, les matériaux artificiellement nanostructurés ont attiré une attention considérable en tant que moyen de fabriquer des nanostructures aux propriétés uniques. Par exemple, Biswas et al. ont suggéré qu'une architecture hiérarchique 3D avec des micro- et nanostructures contribue fortement à une réduction de la conductivité thermique conduisant à une amélioration significative des performances thermoélectriques [27]. Cela indique qu'une méthode de fabrication avec une polyvalence et une simplicité remarquables est hautement souhaitable pour la préparation d'architectures hiérarchiques 3D bien ordonnées, afin d'améliorer et de gérer diverses caractéristiques des matériaux. Parmi les architectures, une architecture hiérarchique constituée de structures nanoshell fabriquées par le processus de modélisation [28,29,30,31] a fait l'objet d'une attention particulière en raison du rapport surface/volume extrêmement élevé contrairement aux structures inverses traditionnelles. Cependant, la technique ALD nécessite des pompes à vide à forte consommation énergétique et des équipements coûteux; qui sont tous deux nécessaires au processus d'infiltration pour créer une structure périodique 3D à base de nanoshell [28, 29]. Par conséquent, l'infiltration à l'aide de procédés sans vide présente la difficulté technique d'obtenir la contrôlabilité de l'épaisseur des nanocoques, car elle infiltre de manière dense un matériau dérivé de la solution dans un modèle 3D pour créer des cadres monolithiques pour une structure inverse autoportante [20, 23, 31]. À ce jour, ce domaine émergent manque de rapports substantiels sur les méthodes de fabrication de structures périodiques 3D à base de nanoshell utilisant un processus cohérent sans vide.
Dans cet article, nous démontrons une combinaison d'un processus de nanopatterning de champ de proximité (PnP) [32,33,34,35,36] et d'un processus d'infiltration avec du ZnO dérivé de la solution, afin de créer une structure périodique 3D à base de nanoshell. PnP est une méthode pour former des structures périodiques polymères 3D utilisant une distribution d'intensité 3D de la lumière dans un photopolymère, générée par le passage de la lumière à travers un masque de déphasage avec des motifs en relief périodiques. Ce processus a une grande flexibilité dans la conception des tailles structurelles en modifiant le motif en relief car la distribution d'intensité dépend fortement de sa conception. Ainsi, ce processus peut résoudre les problèmes de modélisation du processus d'auto-assemblage colloïdal tels que la difficulté de modification structurelle et la non-uniformité causée par des défauts [30]. Le but de cette étude est de fabriquer une architecture hiérarchique 3D basée sur des nanoshells par une méthode cohérente sans vide utilisant du ZnO dérivé de la solution. De plus, cette étude a évalué les facteurs de retrait des structures périodiques 3D ZnO fabriquées par le processus de modélisation polymère.
Méthodes
Préparation d'un modèle polymère 3D par PnP
Un verre de couverture (épaisseur 0,16-0,19 mm) nettoyé avec un plasma d'oxygène pendant 2 min a été utilisé comme substrat. Un film bicouche a été préparé sur le substrat pour empêcher le délaminage de la membrane nanostructurée pendant le processus de développement. Des informations détaillées sur les procédures pour les modèles polymères 3D sont décrites dans la littérature [28, 32, 33, 37]. Tout d'abord, une résine photosensible à tons négatifs (SU-8, MicroChem) exposée par inondation à la lumière UV a été formée sur le substrat en tant que couche d'adhérence (<2 μm). Le film de résine photosensible d'une épaisseur de 10 μm a ensuite été déposé par centrifugation (2000 rpm pendant 30 s) sur la couche d'adhérence. Le film bicouche préparé pour le substrat a ensuite été cuit doucement (95 °C pendant 10 min) sur une plaque chauffante. Le masque de déphasage utilisé dans cette étude a été fabriqué à partir de poly(diméthylsiloxane) (PDMS) (VDT-731, HMS-301, Gelest), qui a un motif en relief carré composé de cylindres (périodicité 600 nm, diamètre 480 nm, profondeur du relief 420 nm). Le masque de déphasage PDMS a été directement mis en contact avec une surface supérieure du film photorésistant pendant l'irradiation UV. Après irradiation UV (longueur d'onde 355 nm) à travers le masque de déphasage à l'aide d'un laser Nd:YAG (Awave355-300mW40K, Advanced Optowave) avec un extenseur de faisceau et un collimateur, l'échantillon a été cuit après exposition (65 °C pendant 7 min ) sur une plaque chauffante. Les régions non exposées ont ensuite été éliminées à l'aide d'acétate d'éther méthylique de propylène glycol (PGMEA) (révélateur SU-8, MicroChem) suivi d'un rinçage à l'éthanol afin d'obtenir un modèle polymère 3D [32,33,34,35,36].
Fabrication d'une structure 3D à base de nanoshell
La figure 1 montre un diagramme schématique de la procédure utilisant le processus d'infiltration avec du ZnO dérivé de la solution pour les structures périodiques 3D à base de nanoshell. Une solution de précurseur de ZnO (2,0 M) composée d'un matériau de décomposition organique métallique (MOD) (SYM-Zn20, Kojundo Chemical Lab.) a été utilisée comme matériau d'infiltration. Initialement, quelques gouttes de la solution de précurseur ont été déposées de manière à recouvrir toute la surface supérieure du modèle polymère 3D préparé par PnP. L'échantillon a ensuite été déposé par centrifugation à 2000 tr/min pendant 20 s pour obtenir l'uniformité de l'alimentation en solution. Ensuite, un dégazage sous vide a été effectué pour faciliter la pénétration dans le fond du gabarit, tel qu'il est couramment utilisé dans la fabrication de cellules solaires à colorant (DSSC) [38, 39]. La pré-cuisson a finalement été réalisée dans un four électrique (FO310, Yamato Scientific) à 2 20°C pendant 1 h en atmosphère d'oxygène (débit 14 L/min). La condition de température utilisée sur l'état de gel du précurseur de ZnO a été déterminée en référence à notre étude précédente [40]. De plus, la procédure allant du revêtement par centrifugation à la pré-cuisson a été effectuée plusieurs fois afin d'examiner la dépendance du nombre de cycles du processus d'infiltration sur les propriétés structurelles résultantes.
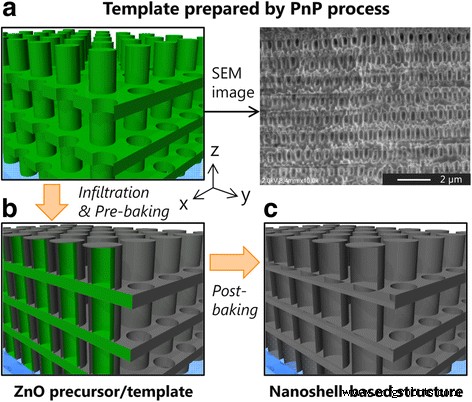
Diagramme schématique de la procédure utilisant le processus d'infiltration avec du ZnO dérivé de la solution pour les structures 3D à base de nanoshell. un Préparation du modèle par processus PnP. b Infiltration de la solution précurseur de ZnO dans le gabarit et pré-cuisson plusieurs fois, et c Post-cuisson pour la suppression du modèle
Pour obtenir une structure 3D ZnO en utilisant le processus de création de modèles, le retrait du modèle est nécessaire après le processus d'infiltration. De plus, en raison d'un traitement thermique insuffisant, l'élimination du précurseur de ZnO restant qui s'est infiltré dans le gabarit est également nécessaire. Ainsi, la post-cuisson a un double objectif :en premier lieu, retirer le gabarit et, par conséquent, contribuer à la pyrolyse du précurseur pour servir de préparation au ZnO. Dans cette optique, la post-cuisson a été effectuée sur le gabarit infiltré de précurseur à 410 °C pendant 4 h en atmosphère d'oxygène [19]. Nos recherches antérieures ont montré que la température de pyrolyse du précurseur est supérieure à 360 °C [40]. Comme mentionné ci-dessus, cette procédure a deux processus de cuisson différents car la post-cuisson à des températures supérieures à 400 °C après infiltration sans pré-cuisson provoque un effondrement structurel (Fichier supplémentaire 1 :Figure S1a, b).
Caractérisation
Les morphologies des structures périodiques 3D fabriquées par PnP et l'infiltration de ZnO dérivé de la solution ont été observées par microscopie électronique à balayage (MEB) (SU-6600, Hitachi). Nous avons évalué la périodicité structurelle, la qualité et l'uniformité des structures obtenues pour chaque étape de fabrication par des images SEM en coupe transversale. De plus, les facteurs de retrait sont estimés par des mesures des différences de taille structurelle entre les structures de ZnO résultantes et les modèles préparés par PnP. De plus, une analyse par spectrométrie de rayons X à dispersion d'énergie (EDX) a été menée pour confirmer la suppression du modèle et pour identifier un rapport de composition de ZnO dérivé de la solution, en utilisant le même appareil avec une tension d'accélération de 5,0 kV. Pour mesurer les spectres de réflectance du modèle polymère et de la structure périodique 3D à base de nanoshell, la spectroscopie UV-Vis (V-570, JASCO) a été utilisée. De plus, l'énergie de la bande interdite du ZnO dérivé de la solution a été estimée expérimentalement en mesurant le spectre de transmission.
Résultats et discussion
Les tailles structurelles dans les structures 3D ZnO obtenues par des processus de modélisation dépendent fortement des tailles du modèle principal. La périodicité répétée dans la direction hors plan (z axe) dans les structures, appelée distance de Talbot (Z T ), préparé par PnP peut être calculé en utilisant la formule suivante [41].
$$ {Z}_{\mathrm{T}}=\frac{\raisebox{1ex}{${\lambda}_0$}\!\left/ \!\raisebox{-1ex}{${n}_ {\mathrm{m}}$}\right.}{1-\sqrt{1-{\left(\frac{\lambda_0}{n_{\mathrm{m}}\cdot p}\right)}^2 }} $$La formule est composée d'une lumière d'irradiation avec une longueur d'onde dans l'espace libre λ 0 , l'indice de réfraction du milieu n m , et la périodicité du motif en relief p . Dans cette étude, la distance idéale de Talbot a été calculée en utilisant la formule avec les paramètres :λ 0 = 355 nm, n m = 1,66, et p = 600 nm. Le tableau 1 montre les distances Talbot de la valeur théorique et d'une valeur mesurée à partir du modèle SU-8 préparé.
Il a été constaté que la distance Talbot dans le modèle a diminué de 29,2 % par rapport à la valeur théorique. De même, des études antérieures ont rapporté que le rétrécissement des nanostructures SU-8 s'est produit même dans différentes tailles de caractéristiques au cours du processus de développement [35, 42]. Ainsi, lors de la fabrication de structures 3D précises et précises, il est important de prendre en compte le facteur de retrait.
La figure 2 présente les images SEM en coupe transversale des structures 3D précurseur/polymère de ZnO fabriquées par le processus d'infiltration avec différents nombres de cycles de un à six. Comme le montrent les images SEM, le précurseur de ZnO précuit était uniformément réparti sur toute la surface du modèle dans tous les nombres de cycles, suggérant un revêtement conforme sans distorsions ni défauts significatifs. Il y avait une différence nette entre les résultats avec et sans infiltration de précurseur avant le processus de pré-cuisson. Un effondrement structurel a été confirmé après pré-cuisson à 220°C sans ZnO pré-enduit (Fichier supplémentaire 1 :Figure S1c). Il est évident que le précurseur de ZnO pré-revêtu joue un rôle de couche protectrice pour empêcher un effondrement structurel causé par le rétrécissement de la matrice SU-8 pendant le recuit malgré un cycle du processus d'infiltration. De plus, le précurseur de ZnO pré-revêtu est devenu plus épais en augmentant le nombre de cycles du processus d'infiltration et six cycles ont suffi pour remplir complètement le modèle polymère 3D avec le précurseur de ZnO précuit. Plus important encore, nous avons démontré des structures 3D précurseur/polymère de ZnO avec le même facteur de remplissage du précurseur pré-revêtu de bas en haut. Dans cet article, le facteur de remplissage représente la proportion du précurseur infiltré par rapport au volume du modèle polymère après le processus d'infiltration. Jusqu'à présent, des méthodes sol-gel et d'électrodéposition ont été utilisées pour une infiltration uniforme de matériaux inorganiques dans un modèle 3D. Cependant, ces méthodes nécessitent une infiltration à haute densité pour obtenir des structures inverses monolithiques et autoportantes après le retrait du gabarit. De plus, les matériaux pour une structure inverse proviennent du côté électrode, ce qui conduit à un gradient de distribution dans la structure, notamment dans cette dernière méthode. Par conséquent, il y a eu peu de rapports sur une fabrication de structures inverses 3D à base de nanoshell utilisant un processus sans vide avec contrôlabilité de l'épaisseur. En revanche, nous avons obtenu une infiltration uniforme avec un facteur de remplissage relativement faible par le processus proposé et démontré avec succès la contrôlabilité pour une épaisseur du précurseur pré-revêtu par le processus d'infiltration.
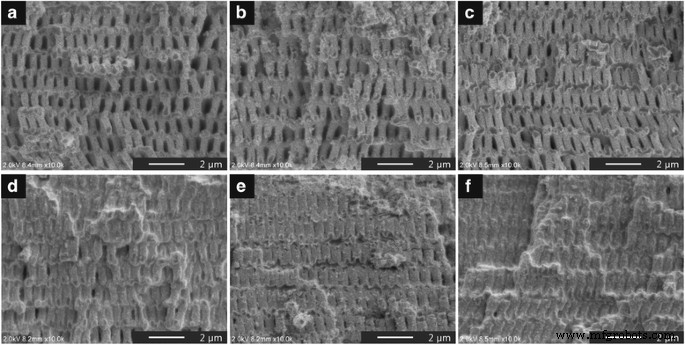
Images SEM en coupe des structures 3D précurseurs/polymères de ZnO. Le processus d'infiltration a été mené avec différents nombres de cycles de un à six (a –f )
Un processus de cuisson supplémentaire est nécessaire pour obtenir une structure inverse de ZnO 3D en raison d'une température insuffisante car il y a encore un solvant résiduel dans le ZnO pré-revêtu pour éliminer le modèle polymère lors de la pré-cuisson. Ainsi, la post-cuisson à 410 °C pendant 4 h a été effectuée avec un four électrique sous atmosphère d'oxygène pour l'élimination du gabarit et la pyrolyse pour que le précurseur de ZnO pré-revêtu se produise en même temps. La figure 3 indique les images SEM en coupe transversale des structures inverses 3D résultantes après la post-cuisson. En conséquence, nous avons obtenu des structures inverses 3D avec des pores dans tous les cas où le nombre de cycles du processus d'infiltration a été fixé de un à six. Cependant, les structures inverses 3D qui ont infiltré le précurseur d'un à trois cycles ont montré des distorsions structurelles, des défauts et un raccourcissement significatif dans la direction hors du plan. Nous considérons que ce raccourcissement du film nanostructuré est causé par une déformation du précurseur pré-enrobé le long du gabarit avec un retrait résultant du retrait lors du processus de post-cuisson. Plus important encore, la structure infiltrée à un cycle possédait des architectures à gradient périodique avec des structures plus petites dans la partie inférieure vers le côté supérieur dans une direction hors du plan. Cela peut être attribué à deux raisons :(i) L'élimination du gabarit a été initiée plus tôt dans la partie inférieure que dans la partie supérieure avant la solidification du ZnO ; (ii) la partie inférieure de la structure inverse s'est déformée en compression sous son propre poids après retrait du gabarit. Ces suggestions sont cohérentes avec les résultats d'études de processus de modèle précédentes utilisant SU-8 pour obtenir des motifs inverses 2D à base de nanoshell [43, 44], qui ont signalé que les caractéristiques structurelles inverses 2D peuvent être modifiées en fonction d'une charge intentionnelle et de la façon dont le le modèle a été retiré pendant le processus de cuisson. Dans cette étude, nous avons également pu observer une déformation de la structure inverse 3D au niveau des zones de connexion avec une épaisseur plus fine des couches inverses post-cuites. On le voit d'ailleurs dans le cas de la structure de l'infiltration conduite à un cycle (Fichier complémentaire 1 :Figure S2). Ce résultat suggère la possibilité que la condition post-cuisson plus détaillée (c.
Images SEM en coupe des structures inverses 3D résultantes après post-cuisson. Le processus d'infiltration a été mené avec différents nombres de cycles de un à six (a –f )
Nous avons démontré la fabrication de structures périodiques 3D à base de nanoshell avec des distorsions structurelles et des défauts relativement faibles en utilisant une infiltration à quatre cycles. Par la suite, la structure fabriquée à partir d'une infiltration à six cycles possédait la périodicité structurelle la plus ordonnée. La figure 4 montre les images SEM en coupe avec un grossissement plus élevé des structures inverses 3D (Fig. 3d–f). Par conséquent, les épaisseurs de nanoshell dans les structures inverses 3D avec une infiltration de quatre à six cycles étaient respectivement <85, <100 et <125 nm. Ces résultats indiquent qu'une augmentation progressive de la quantité de précurseur infiltré en augmentant le nombre de cycles du processus d'infiltration a contribué à la préformation du cadre monolithique et à une structure inverse 3D résultante avec une périodicité bien ordonnée dérivée du modèle. Généralement, l'infiltration à haute densité est une condition préalable pour qu'une structure 3D autoportante conserve sa périodicité dans le processus sans vide, formant ainsi une structure résultante avec un facteur de remplissage spécifié en fonction du modèle. En revanche, nous avons démontré avec succès la fabrication de structures périodiques 3D à base de nanoshell grâce à la préformation d'un précurseur précuit qui fonctionne comme une couche protectrice pour le modèle SU-8 et un cadre monolithique pour une structure inverse également. Fait intéressant, ce processus ne fournit aucune superposition excessive sur le modèle pendant le processus d'infiltration, ce qui empêche la solution de précurseur de pénétrer dans le modèle. Étant donné que les structures 3D à base de nanoshell se sont infiltrées uniformément, le précurseur de ZnO de la partie inférieure à la partie supérieure a été obtenu via une infiltration séquentielle cycle par cycle (Fichier supplémentaire 1 :Figure S3). Jusqu'à présent, la contrôlabilité de l'épaisseur de la structure nanoshell obtenue par le processus d'infiltration proposé est inférieure à une méthode utilisant la technique ALD, qui montre sa capacité à fournir une précision au niveau atomique et des surfaces uniformes. Bien que cette limitation puisse réduire le domaine d'application, ce problème pourrait être amélioré par de nouveaux progrès de notre procédé avec des conditions d'infiltration optimales. De plus, notre processus est un processus sans vide basé sur une solution rentable qui nous donne un impact élevé par rapport à un processus sous vide tel que ALD, car le processus sous vide entraîne une fabrication coûteuse ainsi qu'un long temps de traitement.
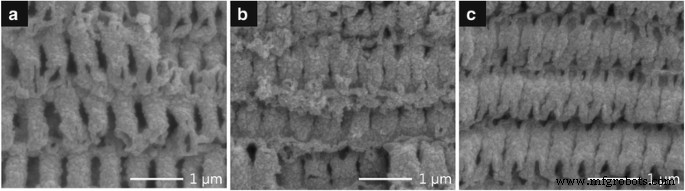
Images SEM en coupe avec un grossissement plus élevé des structures inverses 3D à base de nanoshell. Le processus d'infiltration a été mené avec différents nombres de cycles de quatre à six (a –c )
Nous avons effectué une analyse EDX pour vérifier si le modèle SU-8 a été retiré et pour identifier un rapport de composition de ZnO dérivé de la solution après une post-cuisson à 410 °C pendant 4 h. Une analyse EDX avec une tension d'accélération de 5,0 kV a été réalisée sur les structures transversales pour les échantillons soumis à avant et après la post-cuisson (Fichier supplémentaire 1 :Figure S4). Dans cette mesure, nous avons pu identifier des pics de ZnLα (1,025 keV), OKα (0,531 keV) et CKα (0,283 keV) dérivés d'un modèle SU-8 et d'un ZnO dérivé de la solution des spectres EDX obtenus. La figure 5 illustre les différences dans la quantité de carbone et le rapport de composition du zinc et de l'oxygène, respectivement. Ce sont les valeurs moyennes calculées à partir de huit résultats détectés à différents points d'observation pour les deux échantillons. Il est évident que la quantité de carbone a été considérablement réduite de 47,8 à 3,5 % grâce à la post-cuisson, comme le montre la Fig. 5a, ce qui signifie que le processus de post-cuisson a été efficace pour l'élimination du modèle et la pyrolyse du précurseur de ZnO pré-revêtu. en même temps. La variation de la quantité de carbone dans l'échantillon avant post-cuisson résulte du fait qu'il y avait une différence dans la zone exposée du gabarit en fonction de l'emplacement. La figure 5b a révélé que le rapport de composition du ZnO dérivé de la solution après la post-cuisson était de 58,3:41,7 (Zn:O), ce qui est presque le même que la valeur des nanotiges de ZnO fabriquées par des procédés sans vide tels que le dépôt de bain chimique ( CBD) [45] et méthode hydrothermale [46].
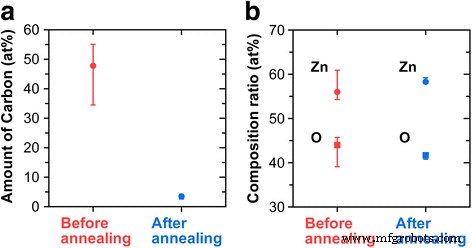
Différences de la quantité de carbone et du rapport de composition de ZnO avant et après post-cuisson. Le a quantité de carbone et b rapport de composition de ZnO obtenu par analyse EDX. Ce sont les valeurs moyennes calculées à partir de huit résultats détectés dans différents points d'observation pour les deux échantillons
Afin d'évaluer le facteur de retrait de la structure inverse 3D ZnO avec l'infiltration à six cycles dans le processus de création de modèles, la hauteur et la périodicité de la structure dans la direction dans le plan du modèle et la structure inverse illustrée sur la figure 6a ont été mesurées à partir de les images SEM en coupe. Nous avons créé des histogrammes représentant les valeurs mesurées de ses tailles structurelles (Fig. 6b) et résumé les valeurs moyennes et les facteurs de retrait calculés dans le tableau 2.
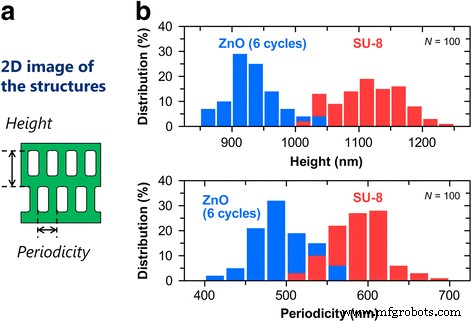
Structure d'image 2D et histogrammes qui représentent les valeurs mesurées des tailles structurelles. un Diagramme schématique de la hauteur et de la périodicité de la structure 2D dans la direction dans le plan des structures et (b ) des histogrammes qui représentent les valeurs mesurées des tailles structurelles pour le gabarit et la structure inverse pour ZnO et SU-8
D'après ces résultats, les facteurs de retrait de la hauteur de la structure et de la périodicité de la direction dans le plan étaient d'environ 16 % pour les deux tailles. Dans ce processus de modélisation, nous pensons que le rétrécissement du ZnO dérivé de la solution lui-même n'a pas contribué de manière dominante au rétrécissement de la structure 3D résultante, car les caractéristiques structurelles dépendent fortement du modèle SU-8 qui fonctionne comme cadre de départ. Par conséquent, cela indique que le rétrécissement de ZnO dérivé de la solution a un effet sur l'épaisseur des nanocoquilles de ZnO et n'affecte pas la périodicité de la direction dans le plan pour la structure résultante. Ainsi, lors de la fabrication de structures 3D précises et précises, il est important de prendre en compte le facteur de retrait. Nous avons comparé le facteur de retrait de la hauteur de la structure dans cette étude à celui d'une étude similaire [23] utilisant un gabarit polymère et TiO2 précurseur. Nous avons découvert que notre procédé proposé montre une amélioration du facteur de retrait de la hauteur de la structure de 34 % [23] à 16 %. Cette amélioration implique que le précurseur de ZnO pré-revêtu joue un rôle important en tant que cadre pour la structure inverse pendant la post-cuisson.
Les spectres de réflectance du modèle polymère et de la structure 3D ZnO à base de nanoshell mesurés par spectroscopie UV-Vis (Fichier supplémentaire 1 :Figure S5). Les pics de réflectance du modèle et de la structure 3D ZnO ont été obtenus à des longueurs d'onde de 410 et 450 nm, respectivement. Bien qu'il n'y ait pas de pic de réflectance qui implique une création de bande interdite photonique, le pic de réflectance similaire à celui du modèle - qui peut atteindre 62% - a été observé. Nous avons également évalué la bande interdite électronique du ZnO fabriqué par notre processus de modélisation proposé à partir d'un spectre de transmission mesuré, afin de vérifier si le ZnO a été préparé sous l'aspect d'une propriété optique. En conséquence, la bande interdite électronique de ZnO qui constitue une structure 3D à base de nanoshell s'est avérée être de 3,0 eV, ce qui a été déterminé à partir de (αhν ) 2 vs énergie photonique (hν ) graphique (Fichier supplémentaire 1 :Figure S6). Cette valeur de la bande interdite s'accorde bien avec celle des nanotiges de ZnO fabriquées par la méthode CBD [47].
Conclusions
Nous avons réalisé avec succès une combinaison de processus de nanostructuration et d'infiltration de champ de proximité en utilisant du ZnO dérivé de la solution pour une structure périodique 3D basée sur des nanoshells avec une flexibilité structurelle et une contrôlabilité. Un nouveau processus d'infiltration sans modèles colloïdaux défectueux a abouti à des structures nanoshell 3D, comparables aux structures formées à partir d'un processus ALD lent et coûteux. Notre étude a révélé l'effet du nombre de cycles du processus d'infiltration sur les défauts structurels et la taille des structures 3D ZnO résultantes. Nous avons démontré qu'un processus d'infiltration unique est utile dans la création d'une couche préformée qui fonctionne comme une couche protectrice pour le modèle et le cadre pour la structure inverse au lieu du processus ALD. L'analyse EDX a montré une diminution drastique de la quantité de carbone dans la structure après la post-cuisson, indiquant l'élimination simultanée du modèle et la pyrolyse du précurseur de ZnO pré-revêtu. Nous avons également réussi à améliorer considérablement le facteur de retrait de la hauteur de la structure par rapport aux précédents procédés d'infiltration sans vide. De plus, la mesure optique des structures 3D de ZnO a clarifié la bande interdite de ZnO expérimentalement à partir du spectre de transmission. La structure périodique 3D à base de nanoshell et notre processus proposé avec une contrôlabilité et une flexibilité élevées dans la conception des tailles structurelles ont le potentiel d'être utilisés pour le développement ultérieur de diverses applications, y compris les dispositifs énergétiques et les capteurs.
Abréviations
- 3D :
-
Tridimensionnel
- ALD :
-
Dépôt de couche atomique
- CBD :
-
Dépôt en bain chimique
- CVD :
-
Dépôt chimique en phase vapeur
- DSSC :
-
Cellules solaires à colorant
- EDX :
-
Spectrométrie à rayons X à dispersion d'énergie
- MOD :
-
Décomposition organique métallique
- PDMS :
-
Polydiméthylsiloxane
- PhC :
-
Cristal photonique
- PnC :
-
Cristal phononique
- PnP :
-
Nanomotif de champ de proximité
- RIE :
-
Gravure ionique réactive
- SEM :
-
Microscopie électronique à balayage
Nanomatériaux
- Découpe :un cours accéléré sur ce processus de fabrication
- Utilisation de technologies sans eau dans le processus de teinture
- Blog :Comprendre le processus de fabrication du PDMS
- Qu'est-ce que le processus de fabrication de tôles ?
- Quel est le processus de fabrication de tôles ?
- 9 avantages de l'utilisation du revêtement en poudre dans la fabrication de métaux
- Utiliser une imprimante 3D pour améliorer votre processus de fabrication - Vidéo
- Votre guide du processus de cisaillement de la fabrication des métaux
- 7 avantages de l'utilisation des revêtements en poudre dans la fabrication