Sable de fonderie
Comment faire du sable vert pour la coulée de métal
Le sable de moulage est au cœur du processus de moulage au sable. Il doit bien conserver une forme et capturer les détails fins d'un moulage, tout en étant suffisamment perméable pour permettre aux gaz de s'échapper. Sous la contrainte d'en retirer le motif de moulage, ou pendant qu'il est rempli, il ne peut pas s'effriter ou couler sur lui-même. Lorsqu'il est renversé, il ne doit pas perdre sa forme :les parties d'un moule doivent rester fidèles tout en étant serrées ensemble.
Dans la plupart des cas, le sable « vert » suffit à mettre en évidence ces propriétés. Le sable vert n'est pas appelé ainsi en raison de sa couleur - ces matériaux peuvent être d'une large gamme de couleurs en fonction de la composition et de l'utilisation. Au lieu de cela, il tire son nom parce qu'il est humide, comme le bois vert.
Les aspects mécaniques du sable sont mesurés avant d'être utilisés sur le sol de la fonderie. Des techniciens ou des ingénieurs de fonderie emballent des cylindres de sable et effectuent des tests. De plus en plus, ces tests sont effectués avec des appareils informatisés capables de nombreux points de précision.
La perméabilité au sable est la "puissance de ventilation" du matériau - la quantité de gaz qu'il permettra de s'échapper du moule. La résistance à la compression verte capture la quantité de compression que le sable peut supporter avant qu'il ne commence à s'effriter. La résistance au cisaillement vert mesure la résistance à la rupture structurelle sous contrainte de cisaillement :il s'agit d'une force qui produit une rupture par glissement parallèlement à sa direction. Les sables sont également testés pour leur résistance à sec, car ils perdent généralement de l'humidité au cours du remplissage. La résistance à chaud (comportement à des températures élevées) est également vérifiée. La chaleur élevée de la coulée fera-t-elle s'effondrer le moule ?
Plusieurs tests auxiliaires sont souvent effectués, y compris la teneur en humidité, la teneur en argile et l'examen de la granulométrie. Un ingénieur fondeur se verra confier le contrôle des propriétés du sable et pourra effectuer plusieurs ajustements au cours de la durée de vie du sable pour le maintenir en bon état de fonctionnement.
Le mélange spécial qui crée le sable de fonderie fournit le comportement nécessaire. L'ingrédient principal est un sable minéral avec une granulométrie constante. La taille du grain de sable va affecter la finition de la coulée, mais aussi parfois la perméabilité et la porosité du moule. Cet ingrédient seul ne suffit pas :un liant, généralement de l'argile, est ajouté et le mélange est humidifié avec de l'eau.
Les sables naturellement liés sont des mélanges de silice et d'argile extraits de la terre, bien que souvent avec quelques ajustements des proportions afin d'obtenir les bonnes propriétés du sable. Les sables naturellement liés sont utilisés dans les fonderies de fonte grise, de fonte ductile, de fonte malléable et de métaux non ferreux (à l'exception du magnésium). Les sables liés synthétiquement sont produits en combinant du sable sans argile avec des quantités précises d'argile ou de bentonite. Ils sont plus uniformes que les sables naturellement liés mais nécessitent un mélange et un contrôle plus minutieux. Les fonderies d'acier, les fonderies de fonte grise et de fonte malléable et les fonderies de magnésium utilisent ce type de sable. Pour les noyaux ou autres sables qui doivent suffisamment durcir pour être un objet pouvant être soulevé ou déplacé, un collage synthétique est généralement nécessaire.
Il existe un certain nombre d'options disponibles pour une fonderie lors du mélange d'une recette pour le moulage au sable.
Sables minéraux
Le mélange dans les fonderies est généralement composé de 75 à 85 % de sable, le reste étant de l'argile, de l'eau et d'autres additifs. Le sable peut être trouvé naturellement, généralement à partir d'un lac, ou peut être créé après l'extraction et la standardisation de minéraux sans argile.
Olivine
Traditionnellement, un sable d'olivine était utilisé pour la coulée des métaux dans les fonderies ferreuses et non ferreuses. Ce sable pouvait produire une finition fine en refroidissant rapidement le métal, et il créait un environnement très peu poussiéreux qui n'est pas dangereux à respirer. Il était considéré comme un sable de fonderie "indulgent", prenant bien les motifs et ne se dilatant pas à chaud, mais sa résistance à la traction n'est pas très élevée. Les sables siliceux ont toujours été préférés pour les noyaux. Certains sables d'olivine auraient une teinte vert très clair, mais c'est une coïncidence - comme tout le reste, il peut être "sec" ou "vert".
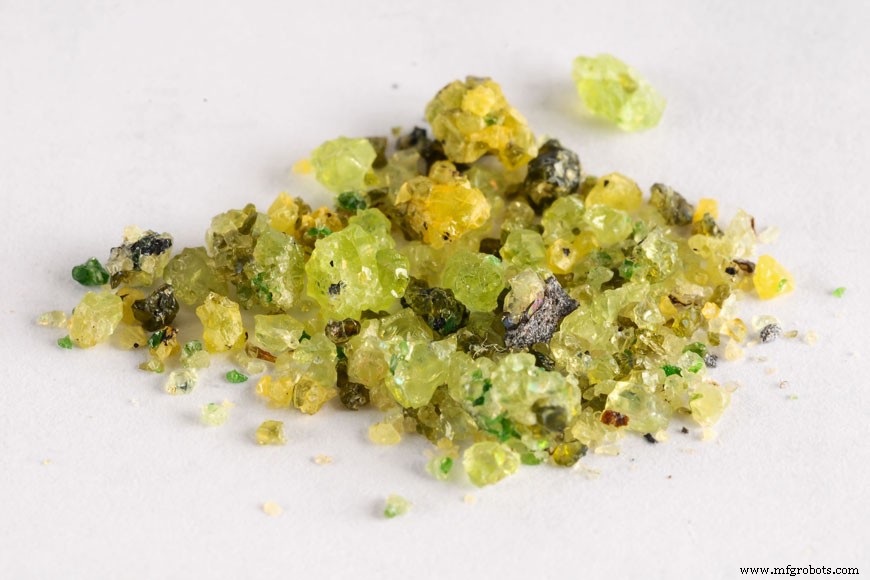
Les sables d'olivine ne sont plus exploités aux États-Unis, donc, du moins en Amérique du Nord, ce n'est plus la principale source de sable de fonderie.
Silice
Les fonderies ferreuses (celles qui traitent le fer et l'acier) utilisent généralement du sable de silice, parfois appelé sable de quartz. Le sable de silice est utilisé depuis longtemps dans la fabrication de noyaux, donc le passage à l'utilisation du même agrégat tout au long du processus de coulée a facilité le processus de gestion des fournitures de fonderie.
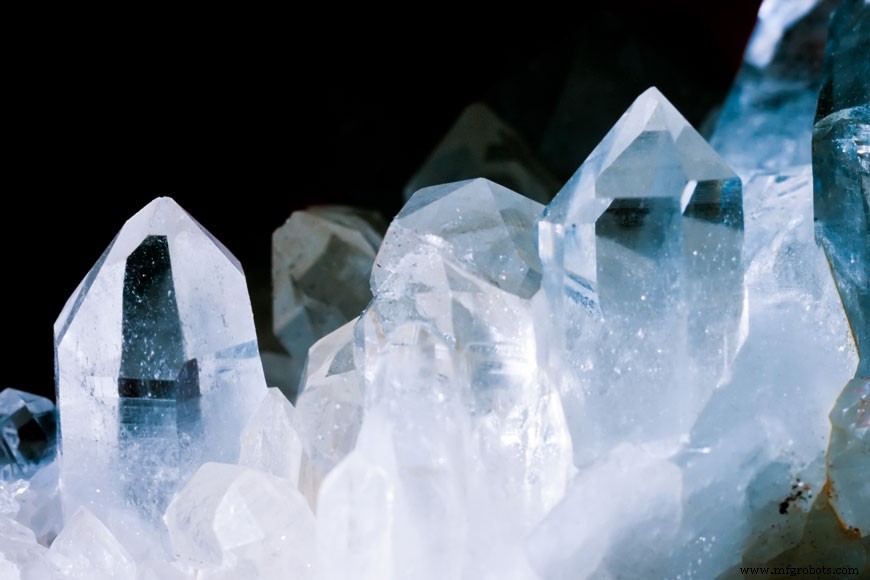
Les fonderies utilisant ce produit prennent quelques précautions mineures supplémentaires contre la silicose, qui est une maladie qui peut se former dans les poumons de ceux qui ont respiré beaucoup de particules de silice. Parfois, des respirateurs ou des masques filtrants sont utilisés.
Argile dans du sable vert
Le sable vert est généralement composé à 10% d'argile bentonite. Au niveau moléculaire, cette argile contient un mélange absorbant de silice et d'aluminium, et contient généralement aussi du potassium, du sodium ou du calcium. La bentonite calcique est l'argile la plus couramment utilisée dans le processus de coulée verte.
L'argile bentonite est extraite et nettoyée avant d'être utilisée dans une variété d'applications. Bien qu'elle ait de nombreuses utilisations dans la fabrication et la construction, les utilisations les plus courantes de la bentonite sont dans la litière pour chat et les produits cosmétiques comme les masques faciaux, où elle est utilisée pour ses propriétés absorbantes.
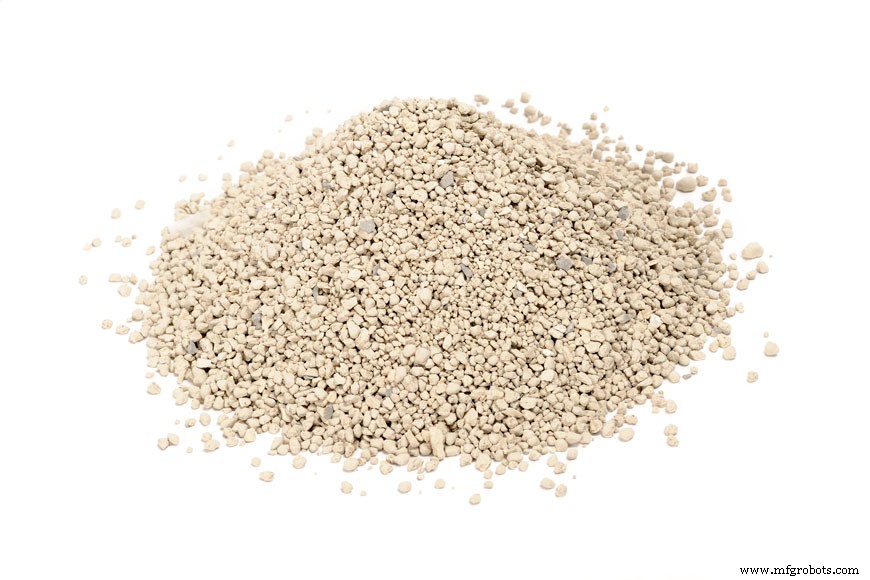
Autres additifs pour le moulage au sable vert
L'humidité est un élément important dans tous les moulages au sable vert. L'eau est généralement ajoutée à raison de 2 à 5 % du poids du mélange. Les liaisons hydrostatiques entre les molécules d'eau renforcent le sable :ce sont ces liaisons qui construisent les châteaux de sable à partir du sable humide sur la plage, et les mêmes forces sont à l'œuvre dans la fonderie. C'est l'eau qui augmente la capacité du sable vert à supporter les contraintes de cisaillement et la compression.
Des additifs spéciaux peuvent être utilisés en plus du sable, de l'argile et de l'eau de base. Ceux-ci comprennent les céréales, le brai moulu, le charbon de mer, la gilsonite, le mazout, la farine de bois, la farine de silice, l'oxyde de fer, la perlite, la mélasse, la dextrine et des matériaux exclusifs. Tout cela sert à modifier les propriétés spécifiques du sable pour donner les résultats souhaités.
Les sables de parement, pour donner une meilleure surface à la coulée, sont utilisés pour les coulées de fonte grise, de fonte malléable, d'acier et de magnésium. Les sables de fer contiennent généralement du charbon de mer, un charbon finement broyé qui empêche le sable d'adhérer à la coulée en générant un film de gaz au contact du métal chaud. Pour les fonderies utilisant du charbon de mer dans tous leurs sables, le mélange tourne autour de 5% de poussière de charbon. Gilsonite sert le même objectif, en ce sens qu'il produit des gaz pour empêcher le sable de coller ou les trous d'épingle liés à l'azote.
Les revêtements en acier peuvent contenir de la farine de silice ou un autre matériau très fin hautement réfractaire pour former une surface dense dans laquelle le métal ne peut pas facilement pénétrer. Le sable d'olivine était également utilisé pour les pièces moulées en acier au manganèse, car la combinaison de sable d'olivine et de manganèse offrait une bonne finition.
Les lavages de moules sont des revêtements appliqués sur la surface du moule ou du noyau pour améliorer la finition de la coulée. Ils sont appliqués humides ou secs. La pratique habituelle consiste à brosser ou pulvériser les lavages de moules humides et à brosser ou frotter sur les secs. La farine de graphite ou de silice mélangée à de l'argile et de l'eau de mélasse est fréquemment utilisée. Les lavages sont généralement mélangés avec des solutions de solvants à base d'eau ou d'alcool. Les solutions à base d'alcool peuvent être allumées avec une flamme, enflammant l'alcool et durcissant instantanément le moule. Les solutions à base d'eau nécessitent un temps de séchage au four, pendant lequel le lavage prend et l'excès d'humidité est éliminé.
Préparation et manipulation du sable
Le sable est préparé dans des broyeurs, qui combinent le sable, l'agent de liaison et l'eau. Ces broyeurs ne se contentent pas de remuer les différents éléments du sable de fonderie. Au lieu de cela, une pression est nécessaire pour enrober uniformément chaque grain de sable avec de l'argile ou un autre matériau de liaison. Des aérateurs sont ensuite utilisés pour détacher à nouveau le sable afin de le rendre plus apte au moulage.
Des fraises à sable qui fonctionnent sur un tas sur le sol de la fonderie peuvent être utilisées à la place des meules. La livraison du sable sur le fond de moulage peut se faire au moyen de camions à benne basculante ou à godets ou par des convoyeurs à bande.
Au cours du processus de coulée, le sable est formé dans des moules qui peuvent être placés sur le sol ou livrés par des convoyeurs à une station de coulée. Après le coulage, les moulages sont secoués hors du sable. Le sable utilisé, à son tour, est renvoyé dans les bacs de stockage par un convoyeur à bande ou par d'autres moyens.
Recyclage du sable de fonderie
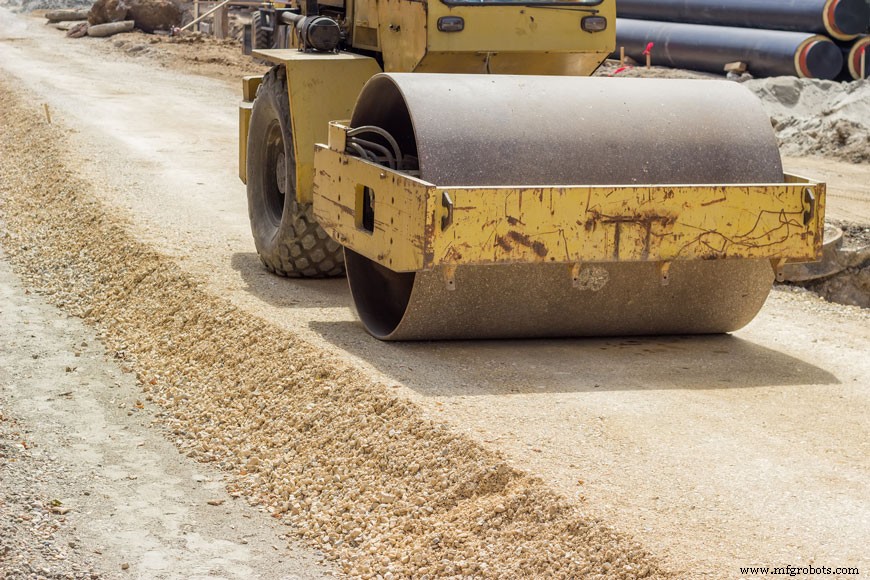
Le sable de fonderie peut être utilisé plusieurs fois avant d'être usé et ne peut pas être réhabilité. Ce sable était autrefois mis en décharge, mais sa réutilisation et son recyclage sont devenus un point d'intérêt. L'EPA suggère que le sable de fonderie usagé provenant du processus de moulage peut être utilisé en toute sécurité dans les sols, à la fois le terreau et la terre végétale fabriquée. Il peut également être utilisé comme couche de fondation pour les routes ou comme agrégat utilisé dans la fabrication du ciment.
Une recette simple avec de nombreuses variantes
Pour verdir du sable à la maison, il suffit de sable, d'argile et d'eau. La litière pour chat en argile agglomérante est une source bon marché de bentonite, mais elle nécessite un broyage fin avant d'être ajoutée :la bentonite finement broyée est une source plus coûteuse vendue comme produit de beauté. Le sable de silice finement broyé est disponible dans la plupart des quincailleries. 9 parties de silice pour 1 partie de bentonite, plus de l'eau juste pour la rendre humide, est un rapport facile à retenir. Le mélange doit être très minutieux et inclure beaucoup de pressage, de pressage et de maculage, pour enrober chaque grain de sable d'une couche d'argile.
Cette recette peut être utilisée pour le moulage de sable grossier ou pour les meilleurs châteaux de sable du quartier !
Previous Post:PatternmakingMetal Casting ProcessNext Post:CoreMaking
Processus de fabrication
- Qu'est-ce que le sable tranchant ?
- Qu'est-ce qu'un écran de sable ?
- Moulage au sable contre coulée centrifuge
- Moulage au sable vs forgeage
- Qu'est-ce que le moulage au sable ?
- AMPCOLOY® 83 Pièces coulées au sable
- AMPCO® 21 Moulages au sable
- AMPCO® 18.23 Moulages au sable
- Pièces moulées en sable AMPCO® M4