5 considérations de meulage pour améliorer la finition de surface
L'amélioration de l'état de surface peut se faire en ajustant un ou plusieurs de ces points :paramètres de fonctionnement, dressage des meules, granulométrie, débit de liquide de refroidissement et état de la machine.
Le meulage de production CNC de précision brille lorsque les pièces nécessitent des tolérances géométriques serrées et des finitions de surface de qualité. En règle générale, les finitions de surface dans la plage de 32 micropouces Ra à aussi peu que 4,0 micropouces Ra et mieux sont les nombres nécessaires à atteindre. Comparativement, une opération traditionnelle de fraisage ou de tournage peut atteindre une finition d'environ 125 micropouces à 32 micropouces Ra.
Si l'objectif est d'améliorer la finition de surface actuelle de 20 micropouces Ra à 17 micropouces Ra, alors simplement augmenter la vitesse de la roue et/ou réduire légèrement la vitesse d'avance peut suffire. Cependant, si une finition de surface plus fine est requise, ces cinq facteurs doivent être pris en compte.
1) Paramètres opérationnels de broyage
Le réglage des paramètres de meulage peut être la solution la plus simple et la plus rapide pour améliorer la finition de surface d'une pièce. Voici les paramètres clés et les actions recommandées pour le faire avec succès.
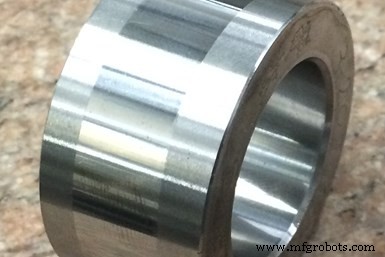
Avance lente/meulage de surface :
- Augmenter la vitesse des roues. C'est un bon point de départ. Cependant, assurez-vous que la roue est conçue pour fonctionner à la nouvelle vitesse. La vitesse de fonctionnement maximale (MOS) sera indiquée sur le côté de la roue.
- Réduire la vitesse d'alimentation.
- Réduire la profondeur de coupe.
- Augmentez le nombre de passes d'étincelles.
Meulage du diamètre extérieur (OD)/diamètre intérieur (ID) :
- Augmenter la vitesse des roues. Comme mentionné précédemment, la roue doit être conçue pour fonctionner à la nouvelle vitesse. La vitesse opérationnelle maximale sera indiquée sur le côté de la roue.
- Réduire la profondeur de coupe par tour.
- Réduire la vitesse de travail (tr/min) :il peut être nécessaire d'ajuster la vitesse d'alimentation pour maintenir la profondeur par tour.
- Augmenter le temps de séjour/d'étincelle.
- Utilisez l'oscillation (une pratique courante dans la rectification intérieure en plongée).
Aujourd'hui, de nombreuses rectifieuses sont équipées de contrôleurs de vitesse variable, de sorte que la modification de la vitesse de la meule peut être effectuée en modifiant simplement le programme CNC ou en ajustant le contrôleur de vitesse de broche. D'autres machines peuvent nécessiter un changement manuel des poulies et des courroies.
La réduction des vitesses d'avance peut également être effectuée en éditant le programme CNC ou en ajustant le contrôle de la vitesse d'avance. Cependant, cette approche peut augmenter le temps de cycle, ce qui n'est pas toujours une bonne option, en particulier dans une opération de production où le temps de cycle est critique. Dans les applications où le temps de cycle n'est pas critique, la réduction de la vitesse d'avance peut être une bonne option pour améliorer la finition de surface de la pièce.
Lorsque la vitesse de la meule est augmentée et que la profondeur de coupe et l'avance sont réduites, la meule peut s'émousser. Cela augmente les risques de dommages thermiques à la pièce et peut augmenter les forces de meulage. Par conséquent, il faut faire attention lors du réglage de ces paramètres pour ne pas introduire d'autres problèmes dans le processus.
2) Dressage de la meule
Les conditions de dressage des meules conventionnelles et superabrasives peuvent être modifiées pour aider à améliorer la finition de surface. Ceci est généralement accompli en ralentissant la vitesse de rotation de l'habillage et/ou en réduisant la profondeur par passe pendant l'habillage. La réduction de la profondeur de dressage rend l'action de dressage moins agressive et donne une face de meule plus lisse, ce qui améliore généralement la finition de surface de la pièce. La réduction de la vitesse de rotation de la robe réduit l'avance de la robe, qui est la distance parcourue par la roue en une rotation de la roue. Le fil de dressage peut être appliqué à n'importe quel processus de dressage où l'outil de dressage traverse la face de la meule. Cependant, le plomb de dressage ne s'applique pas aux opérations de pansement en plongée. L'ajustement du pas est un bon moyen d'améliorer l'état de surface des procédés existants.
Il est préférable de calculer le taux de chevauchement du dressage (qui tient compte de la largeur du dresseur) lors du développement d'un nouveau processus ou du changement de type d'outil de dressage. Le taux de chevauchement est le nombre de fois qu'un point sur la face de la meule entre en contact avec la face du dresseur lorsque le dresseur se déplace sur la meule (tableau 1).
Le taux de recouvrement de dressage détermine l'état de surface de la face de la roue. Ceci, à son tour, détermine la rugosité de surface de la pièce. Lorsque le taux de chevauchement augmente, le dresseur frappe le même grain sur la meule plusieurs fois, créant une topographie fine sur la surface de la meule. Cela rend la face de la meule terne et fermée, ce qui donne une finition de surface plus fine sur la pièce.
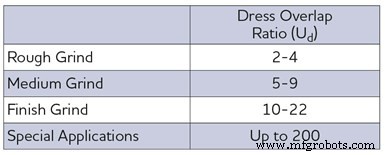
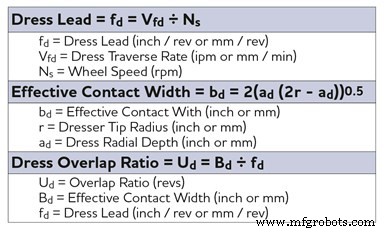
Il faut cependant veiller à ce que la face de la meule ne soit pas trop fermée après un dressage très fin. Une face de meule fermée peut entraîner une puissance de meulage plus élevée car la surface de la meule est terne et peut causer des dommages thermiques à la pièce. Le tableau 2 présente les équations permettant de déterminer le taux d'avance et de chevauchement.
3) Composition de la meule :taille du grain
La granulométrie de la meule a un effet direct sur la finition de surface. Plus la taille du grain est grande, plus la finition est grossière. Il est important de sélectionner la taille de grain correcte en fonction des exigences de finition de la pièce. Le tableau 3 montre les types de grains, les tailles et des suggestions pour diverses exigences de finition.
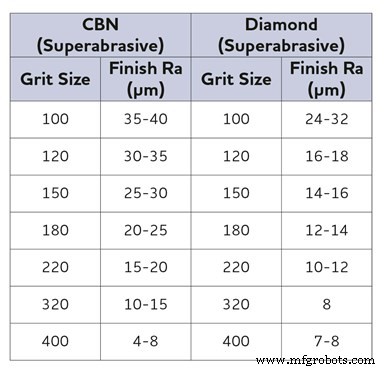
Avant de modifier la granulométrie, il est conseillé de dresser la meule avec des paramètres moins agressifs. La réduction de la taille des grains signifiera probablement que les taux d'alimentation devront être réduits et, par conséquent, les temps de cycle pourraient augmenter. Les tailles de grain plus petites ne peuvent pas enlever le matériau à un taux d'élimination aussi élevé que les tailles de grain plus grossières. En outre, des dommages thermiques peuvent être induits dans une pièce lors de l'utilisation de grains plus petits.
La composition d'une meule abrasive conventionnelle comprend le type et la taille de l'abrasif, la structure de la meule (espacement des grains), la nuance (dureté du liant) et le type de liant. La composition d'une meule superabrasive comprend le type et la taille de l'abrasif, la concentration de l'abrasif, ainsi que la qualité et le type de liant. Les abrasifs conventionnels comprennent l'oxyde d'aluminium, le carbure de silicium et l'abrasif céramique; et les superabrasifs comprennent le diamant et le nitrure de bore cubique (cBN).
Avant de commander une meule avec un grain plus petit, il est conseillé de contacter un fabricant/distributeur de meules pour trouver la meilleure composition de meule pour une application.
4) Livraison de liquide de refroidissement
Si l'apport de liquide de refroidissement est insuffisant, des copeaux de meulage peuvent être réintroduits dans la zone de meulage. Les copeaux peuvent provoquer des rayures sur la pièce, ce qui est souvent le cas lors du meulage ID. Il est essentiel de s'assurer que la buse de liquide de refroidissement est correctement dirigée vers la zone de meulage et qu'il y a un débit et une pression de liquide de refroidissement suffisants pour évacuer les copeaux de la zone. Le ciblage précis de toute la zone de meulage peut être essentiel pour obtenir une finition de surface homogène sur toute la pièce. Dans certains processus à taux d'enlèvement élevé, il peut être nécessaire d'ajuster la pression du liquide de refroidissement pour qu'elle corresponde à la vitesse de la meule afin d'éviter de brûler la pièce. Cela aide également à éliminer les copeaux de la zone de broyage.
Les copeaux peuvent également coller à la meule, dans certains cas. Cela peut se produire lors d'un meulage plus agressif ou lors du meulage de certains métaux qui ont tendance à coller à la meule. Dans ces applications, il peut être nécessaire d'implémenter des buses d'épuration. Les buses d'épuration sont généralement des dispositifs à haute pression (500-1 000 psi) et à faible débit qui sont ciblés après la zone de meulage pour éliminer les copeaux de la structure de la meule.
Cependant, il est peu probable que les buses de récurage soient la solution pour le meulage ID, en raison de la quantité limitée d'espace dans l'alésage de la pièce. Le liquide de refroidissement doit être utilisé dans ces cas. Cependant, pour le diamètre extérieur et le meulage par fluage/surface, des buses de récurage peuvent souvent être mises en œuvre sans interférer avec la pièce ou les fixations.
Une mauvaise filtration du liquide de refroidissement peut également affecter négativement la finition de surface et/ou provoquer des rayures sur la surface de la pièce. Si les particules ne sont pas filtrées, elles peuvent être renvoyées dans la zone de broyage avec le liquide de refroidissement. Lorsque le filtrage est soupçonné d'être la cause de rayures et d'une mauvaise finition, un filtre micron plus petit peut devoir être utilisé. Une règle générale pour le meulage au carbure, par exemple, consiste à utiliser un filtre qui filtrera les particules, au minimum, supérieures à 10 % de la taille du grain de la meule (voir tableau 4).
Développer Développer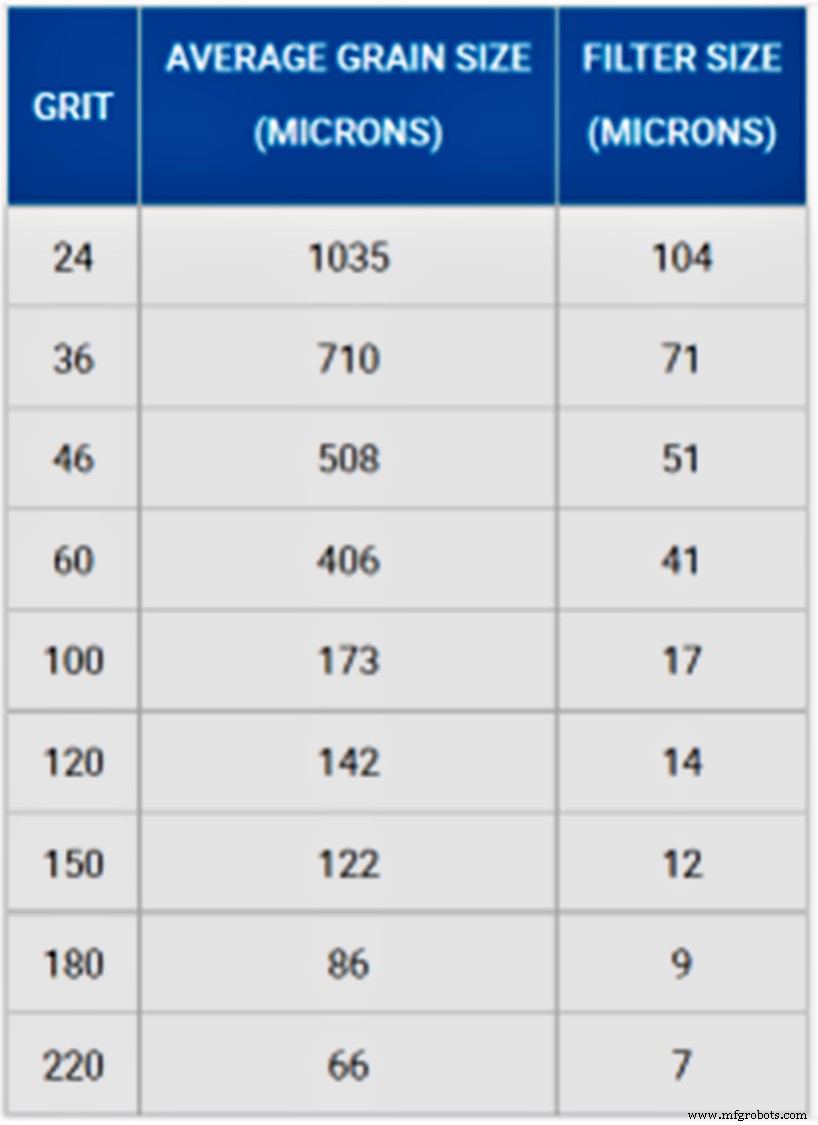
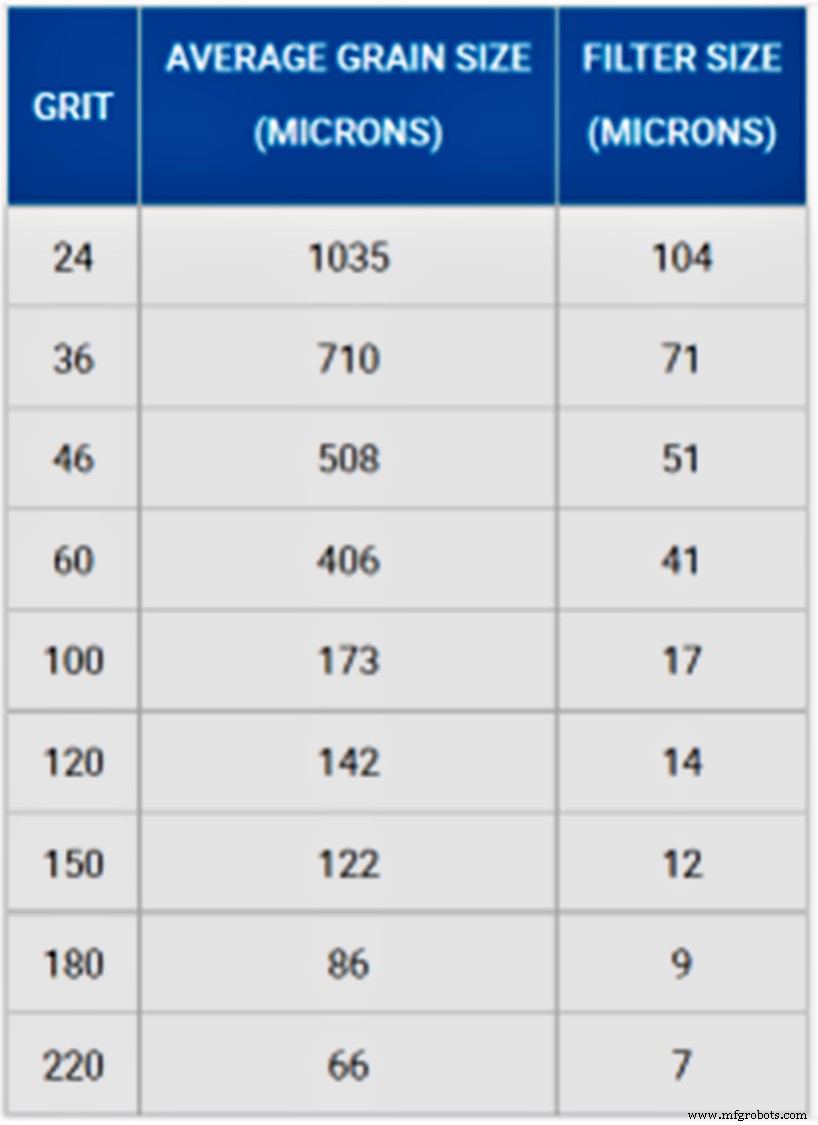
Le type de liquide de refroidissement peut également influencer la finition de surface, généralement en raison de l'impact du pouvoir lubrifiant sur l'usure des roues. Le liquide de refroidissement à l'huile simple favorise généralement une usure plus faible des roues et, par conséquent, une finition de surface plus uniforme.
5. ÉTAT DE LA MACHINE
Des facteurs liés à la rectifieuse peuvent affecter la finition de surface de la pièce. Ceux-ci incluent :
Équilibrage de l'ensemble roue/moyeu : Si l'ensemble de meule n'est pas équilibré à un niveau acceptable, cela peut entraîner un broutage et/ou une mauvaise finition de surface. L'équilibrage peut être effectué à l'aide d'un équipement tel qu'un équilibreur statique, un équilibreur dynamique/manuel ou un équilibreur automatique monté sur la machine. La précision de la pièce à usiner et la finition de surface requises détermineront le type d'équipement à utiliser.
Les systèmes d'équilibrage automatique montés directement sur la broche porte-meule constituent la meilleure option d'équilibrage. Ce système déplace automatiquement les poids dans un moyeu pour contrer le déséquilibre roue/moyeu. Les équilibreurs automatiques sont limités aux machines de plus grande taille telles que les machines à alimentation lente et de type OD et ne sont donc pas pratiques pour les roues de petit diamètre.
La deuxième meilleure méthode d'équilibrage est le système d'équilibrage de type dynamique/manuel, qui peut être utilisé sur tous les types de machines. Il équilibre l'ensemble roue/moyeu directement sur la machine mais nécessite le déplacement manuel des masselottes d'équilibrage.
Enfin, l'équilibrage statique, qui s'effectue hors machine, a ses limites quant aux niveaux d'équilibrage qu'il peut atteindre. Cependant, c'est mieux que de ne pas équilibrer et, dans certaines applications, cela fonctionne bien.
Cela dit, toutes les roues ne nécessitent pas d'équilibrage. Certaines petites roues qui ont une faible masse n'ont pas le poids nécessaire pour créer un déséquilibre problématique. Ainsi, à moins que ces petites roues ne tournent à des vitesses très élevées ou si la machine/le système (fourreau) n'est pas rigide, l'équilibrage n'est pas nécessaire. De plus, les meules utilisées pour des applications de moindre précision ou d'ébauche peuvent ne pas nécessiter d'équilibrage.
Ridité de la machine : Une mauvaise rigidité de la machine peut entraîner une mauvaise qualité de la pièce. Au fil du temps, les roulements de broche peuvent s'user et se desserrer. Les roulements peuvent également être endommagés si la machine a été écrasée. Dans la mesure du possible, les roulements de broche doivent être vérifiés périodiquement ou en continu à l'aide d'un équipement d'analyse des vibrations. Cet équipement est un excellent outil pour aider à prévoir les problèmes imminents avec les roulements de broche qui pourraient entraîner une mauvaise qualité de la pièce. De mauvaises méthodes de montage et de serrage peuvent également entraîner des vibrations ou une déviation et, finalement, une mauvaise finition de surface.
Système d'habillage : Le dressage correct de la meule est essentiel pour obtenir une bonne finition de surface, c'est pourquoi le système de dressage doit être en bon état. Les outils fixes doivent être remplacés s'ils sont endommagés ou usés. Les outils rotatifs tels que la broche de meulage doivent être vérifiés pour détecter toute vibration, faux-rond et mouvement excessifs.
Entretien des machines-outils : Il est essentiel de suivre les instructions du fournisseur de la machine-outil pour la lubrification programmée de la machine, la surveillance de la qualité de l'air comprimé, la fréquence de changement de filtre, etc. Les moyeux de roue et les arbres doivent être inspectés pour détecter les dommages, ainsi que les fixations, les appuis fixes, les centres de la poupée mobile, etc. L'inspection de ces composants de la machine doit faire partie de la routine quotidienne de maintenance préventive d'un atelier.
En plus de la maintenance régulière, de nombreuses entreprises mettent désormais en œuvre des programmes de maintenance tels que la surveillance basée sur l'état (CBM), dans laquelle la machine est surveillée par des capteurs, tels que des accéléromètres, des jauges de température, des manomètres, etc. Cette maintenance prédictive utilise les données collectées par les capteurs pour établir des tendances, prévoir les pannes et aider à déterminer quand des composants tels que les roulements doivent être changés.
Précédemment présenté sur le blog de Norton.
Technologie industrielle
- Théorie de la meule | Métaux | Secteurs | Métallurgie
- Types de finitions de surface pour les produits moulés
- Du début à la fin :les bases de la mesure de surface
- Jauges de finition de surface personnalisées pour les endroits difficiles d'accès
- Finition de surface de moulage de précision
- Meulage de surface à l'ancienne
- Introduction à la rectifieuse plane PLC
- Qu'est-ce qu'une finition de surface d'usinage standard ?
- 9 conseils pour éviter les problèmes de finition de surface de dernière minute