Les porte-outils fournissent le lien vital à la productivité de l'usinage
Des machines-outils précises et des outils de coupe avancés offrent ensemble une productivité de coupe de métal exceptionnelle. Cependant, le lien entre l'outil de coupe et la broche de la machine – le porte-outil – est crucial pour atteindre pleinement cette productivité. Les fabricants d'outils proposent une grande variété de styles de porte-outils, chacun étant conçu pour des performances optimales dans certaines applications d'usinage. Un atelier d'usinage doit donc baser son choix de porte-outils sur ses opérations spécifiques ainsi que sur les pièces qu'il produit. Néanmoins, alors que les ateliers cherchent à acquérir la technologie de machine et les matériaux d'outils de coupe les plus avancés, ils accordent souvent peu d'importance à la sélection, à l'application et à l'entretien des porte-outils qui correspondent le mieux à leurs besoins de production spécifiques.
Tous les détenteurs ne sont pas créés égaux
Aucune méthode de serrage d'outil n'est appropriée pour toutes les applications possibles. Un porte-outil conçu pour effectuer des opérations de finition à grande vitesse manquera généralement de la rigidité et de la résistance nécessaires pour être efficace, par exemple, dans l'ébauche profonde de pièces moulées brutes. À l'inverse, un porte-outil destiné à l'usinage d'ébauche manquera généralement des qualités d'équilibre qui lui permettraient de fonctionner sans à-coups à des vitesses élevées dans les opérations de finition. De plus, la conception robuste et l'encombrement d'un porte-outil d'ébauche peuvent limiter son accès aux fonctions de pièces fines ou profondes. Les matières à usiner dures nécessitent des porte-outils dotés d'une résistance et d'une rigidité accrues. Les capacités d'un porte-outil à amortir les vibrations et à fournir du liquide de refroidissement sont également des critères de sélection importants.
L'utilisation d'un porte-outil inapproprié peut entraîner des erreurs dimensionnelles et des pièces mises au rebut, ainsi qu'une usure excessive des broches de la machine-outil, une durée de vie plus courte de l'outil et une augmentation des bris d'outil. Dans les travaux non critiques, un porte-outil à prix avantageux peut produire des résultats satisfaisants. Mais dans les opérations où la précision reproductible est obligatoire - et en particulier lorsque la mise au rebut d'une pièce coûteuse réduira les marges bénéficiaires des pièces - l'investissement dans des porte-outils de haute qualité axés sur l'application offre une assurance à faible coût contre de telles pertes imprévues.
Pour certains responsables d'atelier, les versions longues des porte-outils utilisés dans une gamme d'applications constituent une stratégie de réduction des coûts valable. Cependant, toujours utiliser le porte-outil le plus court possible maximisera la rigidité, minimisera les vibrations dégradant la surface et préservera la durée de vie de l'outil.
Les porte-outils représentent moins de deux pour cent des coûts de production totaux. Même la réduction de moitié de ce coût produit des économies négligeables, tandis qu'une pièce mise au rebut ou un outil cassé a un effet financier mesurable. Les outils et supports haut de gamme peuvent augmenter les taux de production de coupe de métal pour un retour immédiat sur l'investissement en outillage. Particulièrement dans des industries telles que la fabrication de composants aérospatiaux où la stabilité du processus d'usinage est primordiale, de nombreux fabricants se concentrent avant tout sur l'acquisition d'outils haut de gamme pour éviter de produire des pièces défectueuses et de perdre du temps dans les activités de dépannage et les arrêts de production. Les fabricants aérospatiaux prennent généralement beaucoup de temps pour valider les nouveaux concepts de support avant de les certifier pour la production.
Les facteurs de la pièce influencent la sélection du porte-outil
Les facteurs influençant la sélection du porte-outil incluent l'usinabilité du matériau de la pièce dans chaque travail ainsi que la configuration de la pièce finale, qui peut déterminer les dimensions du porte-outil nécessaires pour atteindre certains contours et/ou caractéristiques. Cependant, les porte-outils doivent être aussi simples et faciles à utiliser que possible afin de minimiser les risques d'erreur de l'opérateur.
Quelle que soit la technologie de porte-outil appliquée, la rigidité d'une machine-outil, la puissance de la broche et sa capacité à générer des tolérances serrées dicteront les opérations réalisables. Par exemple, essayer de produire des tolérances à l'échelle du micron sur une machine usée est une perte de temps.
Les éléments de base d'une machine-outil jouent un rôle clé - une machine rapide avec des guidages linéaires tirera le meilleur parti des porte-outils conçus pour une application à grande vitesse, tandis que les machines avec des guidages en caisson offrent un support pour l'usinage lourd. Une machine multitâche exploitera pleinement les capacités des porte-outils capables d'accomplir à la fois des opérations de tournage et de fraisage/perçage.
La stratégie d'usinage utilisée guidera également la sélection des porte-outils. Par exemple, les ateliers peuvent choisir des outils pour maximiser la productivité dans les opérations de coupe à grande vitesse (HSC) impliquant des profondeurs de coupe plus légères, ou dans des situations de coupe à haute performance (HPC) qui se concentrent sur la génération de taux d'enlèvement de métal élevés sur des machines avec une puissance adéquate mais une capacité de vitesse limitée. .
Un faux-rond faible et reproductible peut aider à assurer un engagement constant de l'outil et ainsi réduire les vibrations et maximiser la durée de vie de l'outil. L'équilibre est crucial, et un porte-outil de haute qualité doit être parfaitement équilibré à une qualité G2,5-25000 RPM (1 g.mm). Les ateliers d'usinage peuvent effectuer leurs propres recherches et consulter leurs fournisseurs d'outillage pour déterminer le ou les systèmes de porte-outils qui répondront de manière rentable à leurs besoins de production.
Chaque titulaire a sa niche
Qu'ils soient simples Weldon, pinces, thermorétractables, de type mécanique ou hydraulique, les porte-outils doivent également être adaptés à des exigences opérationnelles spécifiques. Les porte-fraises simples pour outils à queue Weldon, par exemple, sont rigides, faciles à utiliser, peuvent transmettre un couple élevé et offrent un serrage sûr et solide avec une forte action anti-arrachement. Ils sont bien adaptés à l'ébauche lourde mais manquent de concentricité précise. En général, ils sont intrinsèquement déséquilibrés et ne s'appliquent pas de manière productive aux applications utilisant des vitesses de rotation élevées.
Les mandrins à pinces et les pinces interchangeables sont la forme la plus courante de technologie de maintien d'outils ronds. Les styles ER économiques sont disponibles dans une large gamme de tailles et offrent une adhérence suffisante pour des opérations de fraisage et de perçage légères et fiables. Les porte-pinces ER haute précision présentent un faible faux-rond (<5 μm à la pointe de l'outil) et une conception symétrique qui peut être équilibrée pour les opérations à grande vitesse, et des versions renforcées sont disponibles pour l'usinage intensif. Les porte-outils ER facilitent le changement rapide et peuvent s'adapter à une gamme de diamètres d'outils.
Les porte-outils thermorétractables offrent une force de serrage élevée, une concentricité de 3 μm à 3xD et d'excellentes qualités d'équilibrage. Leurs petites configurations de nez simples offrent un bon accès aux caractéristiques des pièces étroites.
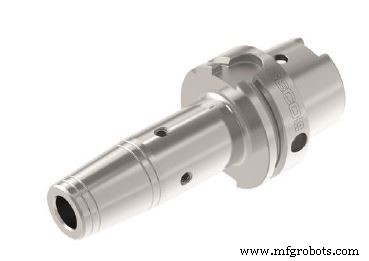
Les versions renforcées peuvent effectuer un fraisage modéré à lourd, mais la force de préhension dépend des tolérances ID de la tige et du porte-outil. Les outils de frettage nécessitent l'achat d'une unité de chauffage spéciale, et le processus de chauffage/refroidissement prend plus de temps d'installation qu'un simple changement de pinces.
Les mandrins de fraisage mécaniques offrent une force de préhension élevée et une rigidité radiale élevée grâce à plusieurs rangées de roulements à aiguilles. La conception permet un fraisage lourd et des changements d'outils rapides, mais le faux-rond peut être supérieur à celui des systèmes de pinces. Les mandrins mécaniques sont généralement plus grands que les autres styles de porte-outils, ce qui peut restreindre l'accès de l'outil à certaines fonctionnalités de la pièce.
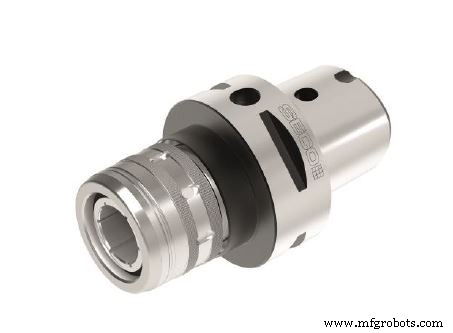
Les mandrins hydrauliques qui utilisent la pression d'huile pour générer une force de serrage ont moins d'éléments internes que les mandrins mécaniques et, par conséquent, ont un profil comparativement plus mince. Les mandrins hydrauliques présentent un faible faux-rond et sont efficaces pour l'alésage, le perçage et le fraisage léger à des vitesses de broche élevées, mais sont sensibles aux fortes charges radiales.
Tout aussi important que la façon dont un support sécurise un outil de coupe est aussi la façon dont il se monte sur une broche de machine-outil. La broche ou l'extrémité conique d'un porte-outil détermine la capacité de transfert de couple et établit la précision de centrage de l'outil. Les cônes d'outils traditionnels BT, DIN et CAT sont efficaces sur les petites machines, mais peuvent être limités en termes de capacité à grande vitesse. Les versions qui fournissent un contact à la fois sur le cône et la face du support offrent une rigidité et une précision accrues, en particulier dans les situations de long porte-à-faux. Des tailles de cône plus grandes sont nécessaires pour transmettre de manière fiable un couple plus élevé. Un porte-outil HSK-E32, par exemple, ne peut pas remplacer un HSK-A125A dans une situation d'usinage lourd.
Le choix du style conique du support est souvent déterminé par les préférences régionales. HSK est apparu en Allemagne au milieu des années 1990 lorsque les machines 5 axes ont gagné en popularité. Les cônes CAT sont principalement utilisés aux États-Unis, tandis qu'en Asie, les queues BT sont populaires, souvent dans les versions à contact conique/face.
HSK est très courant pour l'usinage 5 axes. Les connexions PSC (système de serrage polygonal :Capto) et KM sont principalement utilisées sur les machines multitâches et sont désormais aux normes ISO. KM et Capto sont également des systèmes modulaires, permettant l'assemblage d'outils spécifiques de différentes longueurs en empilant des extensions ou des réducteurs. Les styles de porte-outils qui permettent de tourner, de fraiser ou de percer des pièces dans un seul montage gagnent en popularité à mesure que les machines multitâches sont de plus en plus utilisées.
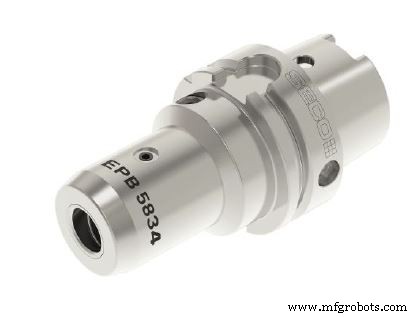
Bien qu'il existe des systèmes de porte-outils exclusifs qui utilisent des supports et des pinces uniques de manière innovante pour obtenir des résultats impressionnants, un atelier doit calculer leurs avantages. Ces systèmes impliquent généralement des coûts plus élevés et un choix d'outils limité provenant d'un seul fournisseur.
Coût et autres considérations
Bien que le coût de base d'un porte-outil de type hydraulique ou mécanique soit plus élevé que celui d'un porte-pince ou d'un porte-outil à fretter, d'autres facteurs entrent en jeu, tels que le coût du système de chauffage par frettage et le temps nécessaire pour changer d'outil. Il est également nécessaire d'avoir un support à ajustement serré pour s'adapter à chaque diamètre d'outil, par rapport à l'adaptation de différents diamètres en changeant simplement les pinces dans un système de support de mandrin à pince.
Les opérateurs de machines et le personnel de maintenance des outils jouent également un rôle important dans la réussite de l'application des porte-outils. Comme pour les machines-outils et autres équipements de fabrication, les porte-outils nécessitent une utilisation et un entretien corrects pour maximiser leurs avantages et les utiliser à leur plein potentiel. Par exemple, l'opérateur doit insérer la tige de l'outil dans le support sur toute sa longueur, car une mauvaise assise entraînera une vibration destructrice de précision ou même une éjection de l'outil. Le respect des spécifications d'assemblage de l'outil est essentiel. Les opérateurs ne doivent pas utiliser une poignée d'extension pour appliquer un couple excessif lors du serrage d'un mandrin, ce qui tord le collet et entraîne un outil mal aligné.
L'entretien des outils est également important mais souvent ignoré. Les opérateurs doivent toujours nettoyer les supports avant utilisation et inspecter également la broche de la machine-outil. Les supports doivent être stockés propres et secs, avec des capuchons pour protéger le cône de l'outil. La pression du fluide des mandrins hydrauliques doit être vérifiée régulièrement.
Conclusion
Les ateliers d'usinage doivent reconnaître l'importance des porte-outils dans le système d'usinage et apprendre comment associer correctement le bon porte-outil à leurs machines-outils, stratégies d'usinage et pièces à usiner spécifiques peut augmenter la productivité et réduire les coûts. Dans le même temps, les fabricants de porte-outils proposent des sélections plus complètes de porte-outils (voir encadré) conçu pour répondre aux besoins opérationnels individuels.
Les améliorations futures vont au-delà du matériel de support lui-même. La gestion des outils à l'aide de logiciels et d'étiquettes RFID est un élément de la fabrication basée sur les données et devient de plus en plus courante. Les progrès de la technologie des porte-outils incluent des porte-outils équipés de capteurs qui permettent de surveiller les forces sur le porte-outil en temps réel. Les données collectées permettent un réglage en cours de processus des paramètres d'usinage soit par l'opérateur, soit même automatiquement via l'intelligence artificielle (IA) en lien avec l'unité de contrôle de la machine. Ces nouvelles technologies et d'autres encore renforceront les contributions productives des porte-outils dans les opérations d'usinage.
Technologie industrielle
- L'histoire de la fraiseuse :un équipement d'usinage qui a parcouru un long chemin
- Les principales différences entre l'usinage 3 axes et 5 axes
- Déséquilibre :le problème caché que les ateliers d'usinage doivent résoudre
- Usinage du titane :trouver les bons outils de fraisage pour les superalliages
- Mettre l'inspection de surface entre les mains de l'opérateur de la machine-outil
- Leçons d'usinage haute performance :n'oubliez pas les porte-outils
- L'importance des liquides de refroidissement dans l'usinage
- Opérations d'usinage CNC :un processus vital dans la fabrication
- Le cœur des machines-outils :les broches de machines-outils.