Moulage sous basse pression :un guide simple pour comprendre le processus
De son nom, le moulage sous pression à basse pression consiste à injecter le matériau fondu dans le moulage sous pression sous une basse pression bien contrôlée qui confère des avantages au processus. Par exemple, il permet la fabrication précise de roues à symétrie axiale, de sorte que l'industrie automobile est l'un des principaux utilisateurs du processus.
Avant de sous-traiter à un service de moulage sous pression, il est important de connaître vous-même le processus. Par conséquent, cet article présentera le moulage sous pression à basse pression, son fonctionnement, ses avantages et ses inconvénients, ainsi que d'autres alternatives que vous pourriez utiliser.
Qu'est-ce que le moulage sous pression à basse pression ?
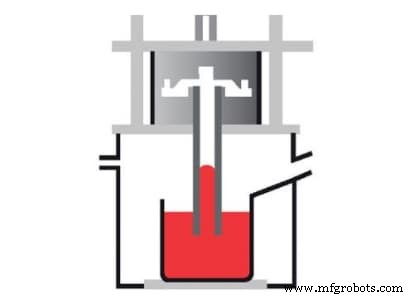
LPDC consiste à remplir un moule moulé sous pression avec du métal en fusion sous basse pression. Il est très précis en raison du remplissage constant de la cavité de la matrice pendant la phase de rétraction (solidification). Cela signifie qu'il compense la réduction de volume. D'autres attributs incluent la réduction de la formation d'oxyde et de la porosité et une consistance supérieure du métal fondu de haut en bas.
Comment fonctionne le moulage sous pression à basse pression ?
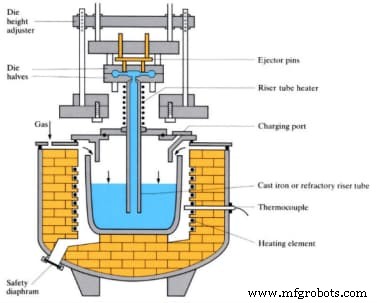
Le moulage sous pression à basse pression utilise une petite pression, généralement autour de 20 à 100 kPa (2,9 à 14,5 psi), au lieu de la gravité pour remplir une matrice. Contrairement au processus de moulage sous pression traditionnel, il a une configuration unique et utilise plusieurs équipements. Vous trouverez ci-dessous une illustration de la configuration et des équipements nécessaires.
Le processus commence par un four de fusion qui fait fondre les alliages métalliques et les amène à la température de coulée. Par exemple, l'aluminium a une température de coulée de 710-720 0 C.
Le métal fondu ira ensuite dans un four de maintien sous le moule, qui fonctionne comme un récipient tout en maintenant le liquide à la température de coulée.
La basse pression force le métal fondu à travers un tube de montée dans le moule. Le métal liquide se déplace sous une pression constante jusqu'à ce que le métal fondu se solidifie dans la cavité de la matrice.
Lors de la solidification, la pression est relâchée et le métal en fusion restant retourne à travers la colonne montante vers le four de maintien pour être recyclé. Enfin, le moulage sera facilement retiré une fois le moule refroidi.
Avantages de Moulage sous basse pression
Le LPDC présente de nombreux avantages, ce qui en fait une méthode de moulage sous pression applicable dans plusieurs industries. Vous trouverez ci-dessous quelques avantages du processus.
· Haute précision
Les pièces fabriquées à l'aide de ce procédé sont d'une grande précision. Cela est dû à la basse pression maintenue pendant la solidification. Par conséquent, il y a un remplissage continu de la cavité de la matrice, compensant le rétrécissement de volume à mesure que le métal fondu se solidifie. En raison de sa grande précision, c'est la meilleure méthode pour fabriquer des pièces à symétrie axiale telles que des roues.
· Il forme des moulages très purs
Les pièces moulées sont très pures en raison du peu ou pas de laitier responsable de l'impureté. Le faible niveau de laitier est dû à la configuration de la machine de coulée. Généralement, les scories se trouvent à la surface des métaux en fusion. Cependant, comme les colonnes montantes descendent dans le four de maintien, le métal liquide forcé dans la cavité ne contient pas de scories. D'où la coulée très pure. De plus, comme il s'agit d'un processus à basse pression, le risque que des scories pénètrent dans le moule est faible.
De plus, le processus ne conduit pas à l'oxydation du métal fondu en raison du processus de remplissage stable. La stabilité réduit ou élimine le culbutage, l'impact et les éclaboussures du métal en fusion pendant le processus. Par conséquent, il n'y a pas de formation de scories d'oxydation pouvant affecter la pureté des pièces moulées.
· Il a une bonne formabilité
Le remplissage à basse pression conduit à une bonne formabilité du fait de l'amélioration de la fluidité du métal liquide. Par conséquent, les pièces moulées fabriquées à l'aide de ce procédé ont un contour clair et une surface lisse. En général, le procédé est idéal pour fabriquer des pièces coulées aux géométries complexes en raison de sa grande formabilité.
· Cristallisation
Étant donné que la coulée se solidifie sous pression, elle peut cristalliser et former une structure compacte. Par conséquent, les pièces moulées réalisées via le procédé sont solides et conviennent à la fabrication de pièces nécessitant de bonnes valeurs de résistance.
Inconvénients de Moulage sous basse pression
Bien que le processus de moulage sous pression à basse pression soit idéal pour obtenir des résultats précis, il présente également des inconvénients.
· Cycle de diffusion plus lent
Un inconvénient est qu'il a un cycle plus lent en raison de la basse pression. Par conséquent, le nombre de pièces pouvant être fabriquées est faible et les pièces ont un coût élevé.
· Pièce métallique érodée
Pièce moulée en aluminium érodée forme peut se produire en raison de la partie métallique de l'équipement entrant en contact avec le métal en fusion. Cela peut entraîner des coûts de maintenance élevés, en particulier dans les grandes installations de fabrication. De plus, les constituants de la partie métallique de l'équipement peuvent pénétrer dans le métal liquide, affectant les performances.
· Ne convient pas à la fabrication de pièces à parois minces
L'épaisseur de paroi minimale des pièces moulées que vous pouvez réaliser en utilisant le procédé est d'environ 3 mm. Par conséquent, il ne convient pas à la fabrication de pièces à parois minces que le moulage sous haute pression.
RapidDirect :Votre partenaire de moulage sous pression basse pression
Le processus de coulée à basse pression devrait figurer en tête de votre liste si votre projet nécessite une précision, une coulée pure et des propriétés de matériau exceptionnelles. Même s'il a un cycle de coulée lent, choisir le processus parfait pour votre projet nécessite de l'expérience et des connaissances. Il est donc bon d'obtenir des conseils d'experts dès le début.
Contactez RapidDirect pour vous aider avec vos besoins de fabrication. Nous offrons des services de moulage sous pression à basse pression et un large éventail d'autres services de fabrication, y compris l'usinage CNC, l'impression 3D et la fabrication de tôles qui peuvent répondre à vos exigences avec notre puissante équipe d'ingénierie et nos usines.
Vous pouvez demander un devis dès aujourd'hui en téléchargeant vos fichiers de conception ou consulter notre guide du moulage sous pression, qui fournit des informations plus détaillées sur la technique de moulage sous pression, y compris son processus, ses matériaux, sa finition de surface, ses applications et ses coûts.
Moulage sous pression à basse pression contre moulage sous pression à haute pression
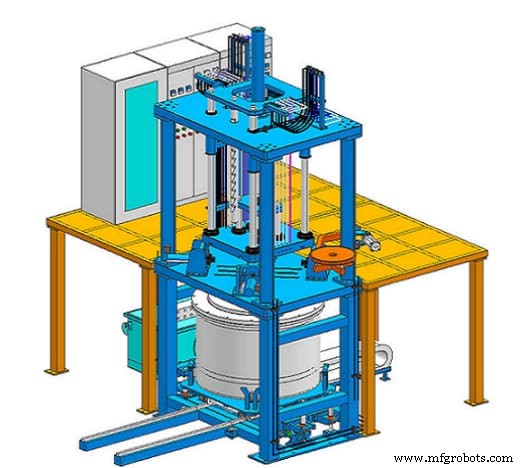
Le moulage sous pression basse et haute pression est applicable dans différents scénarios en fonction de la complexité du composant, du nombre de pièces et du budget de fabrication. Vous trouverez ci-dessous une clarification sur les différences entre les deux et les avantages du moulage sous pression à basse pression par rapport au moulage sous pression à haute pression.
· Temps de cycle
La plage de pression de coulée sous pression à basse pression est d'environ 0,7 bar à 1 bar. D'autre part, le moulage sous haute pression implique une haute pression (souvent supérieure à 1000 bars).
En conséquence, le moulage sous pression à basse pression a un temps de cycle inférieur à celui du moulage sous pression à haute pression. Cela se voit dans le fait que ce dernier est responsable d'environ 50 % des pièces moulées en métaux légers devant les 20 % de la basse pression.
· Résistance de la pièce
Les pièces fabriquées à partir de coulée à basse pression ont des valeurs de résistance élevées car la solidification se produit sous une pression constante pendant une longue période pour former une structure compacte et dense. Les pièces fabriquées à haute pression ont également une bonne valeur de résistance. Cependant, vous ne pouvez pas comparer leur résistance à des pièces fabriquées à basse pression car la pression est élevée et le temps est rapide.
· Qualité du casting
Les moulages à basse pression ont une qualité supérieure à celle des moulages à haute pression. Cela est dû à la réduction de volume due au retrait complétée par une injection constante de métal en fusion dans la cavité de la matrice jusqu'à la solidification.
De plus, ces pièces moulées sont plus pures en raison de la moindre quantité de scories présentes et elles n'ont pas de pores. Ceci est différent des moulages à haute pression, qui peuvent avoir des pores en raison de la haute pression, et les scories sont injectables dans la cavité de la matrice.
· Coût
Le moulage sous pression à haute pression entraîne un coût d'exploitation et d'investissement plus élevé que le moulage sous pression à basse pression en raison des machines requises. Cependant, il a un coût de pièce inférieur en raison de son temps de cycle rapide.
· Épaisseur
La coulée basse pression est la méthode idéale pour réaliser des pièces épaisses. Cependant, il est inadapté aux pièces à paroi mince (ne convient pas aux épaisseurs inférieures à 3 mm). D'autre part, la coulée à haute pression peut produire des pièces à paroi mince (moins de 0,40 mm).
Alternatives à Moulage sous basse pression
Bien qu'elle présente de nombreux avantages, certaines conditions peuvent limiter l'utilisation de la coulée basse pression. Par conséquent, nous avons introduit plusieurs alternatives au processus et comment elles se comparent au processus de coulée à basse pression.
· Moulage par gravité
La coulée sous pression par gravité, également connue sous le nom de processus de coulée en moule permanent, est un processus consistant à remplir le métal en fusion dans le moule par gravité. Il convient aux alliages de matériaux non ferreux tels que l'aluminium, le cuivre, le magnésium et le zinc.
L'un des avantages de la coulée par gravité par rapport à la coulée à basse pression est sa large gamme de matériaux compatibles. Ceci est différent de ce dernier étant plus populaire pour travailler avec des alliages d'aluminium. D'où le nom de "moulage sous pression d'aluminium à basse pression".
· Casting d'investissement
Le moulage à modèle perdu ou moulage de précision est basé sur un ancien procédé appelé moulage à la cire perdue. Le processus consiste à créer un motif en cire ayant la forme du produit final via des processus tels que le moulage par injection ou impression 3D .
La cire est trempée dans une pâte céramique d'épaisseur contrôlée pour former un moule. Lors de la solidification de la cire, le moule est préchauffé et la cire retirée pour créer un boîtier métallique. Le métal fondu peut ensuite être injecté dans le moule, et les procédures appropriées suivent
Le moulage à modèle perdu est plus précis que les moulages à basse pression car le modèle de cire provient de processus de fabrication précis tels que l'impression 3D. De plus, la céramique ne se dilate pas.
· Moulage au sable
Le moulage au sable est le procédé de moulage de métal le plus couramment utilisé dans les usines spécialisées appelées fonderies. Le processus traditionnel consiste à fabriquer un moule avec du sable, de l'argile et de l'eau, à le remplir de métal en fusion et à casser le moule à la fin. Le moulage sous pression contre le moulage au sable La comparaison est principalement basée sur le type de métal avec lequel vous travaillez. Le moulage au sable l'emporte sur le moulage à basse pression lorsque vous souhaitez travailler avec un métal à haute température.
Conclusion
Le moulage sous pression à basse pression consiste à injecter du métal en fusion (principalement de l'aluminium) dans la matrice avec une surpression relativement faible. Le processus a un temps de cycle court. De plus, il est très précis pour la fabrication de pièces moulées avec des géométries complexes et fournit une coulée pure avec des propriétés matérielles exceptionnelles, ce qui en fait un processus de pointe dans de nombreuses industries. Cet article a présenté son fonctionnement, ses avantages et ses inconvénients, ainsi que d'autres alternatives que vous pourriez utiliser.
Avez-vous des questions sur le processus? Veuillez contacter RapidDirect. Vous pouvez également télécharger votre conception pour obtenir un devis aujourd'hui et découvrir comment nous pouvons répondre à vos besoins en matière de moulage sous pression.
FAQ
Pourquoi l'aluminium est-il bon pour le moulage sous pression ?L'aluminium est le matériau le plus courant pour le moulage sous pression en raison de sa légèreté. Même s'il est léger, le moulage d'aluminium a une résistance à la traction élevée. En outre, il existe davantage d'options de finition de surface pour la coulée d'aluminium. Par conséquent, ils sont plus esthétiquement matériels que les autres matériaux non ferreux.
Quels sont les types de moulage sous pression ?
Il existe deux types de moulage sous pression :le moulage sous haute pression et le moulage sous pression à basse pression. Les deux processus sont similaires dans la configuration. Cependant, ils diffèrent par leur processus et leurs propriétés. Par conséquent, ils sont applicables dans différents scénarios.
La coulée à haute pression a une application plus large en raison des cycles de coulée élevés. Cependant, la coulée à basse pression est plus précise et adaptée à la fabrication de pièces à symétrie axiale.
Technologie industrielle
- Les avantages et les inconvénients du moulage sous pression
- Présentation rapide du processus de casting
- Qu'est-ce que le processus de forgeage des brides
- Moulage de précision et moulage sous pression :quelles sont les différences ?
- Moulage au sable et moulage sous pression :quelles sont les différences ?
- Comprendre le processus de fabrication de coques du moulage à modèle perdu
- Introduction au procédé de moulage de précision en acier inoxydable
- Quand choisir le processus de moulage au sable de résine
- La simplicité du moulage par gravité