Comment nous avons utilisé l'impression 3D pour valider les conceptions de valve et le schéma de notre ventilateur mécanique d'urgence
Lorsque la pandémie de COVID-19 est devenue une grave préoccupation en Amérique du Nord au début de 2020, il y avait de nombreuses inconnues. Comment le COVID-19 s'est-il propagé ? Quels étaient les symptômes ? Le COVID-19 pouvait-il se propager en l'absence de symptômes ? Y a-t-il eu des séquelles durables ou des maladies dérivées ? Jusqu'où et à quelle vitesse la propagation se produirait-elle? Le port de masques aiderait-il à freiner la propagation ? Quand un vaccin serait-il prêt ?
Parmi toutes ces inconnues, cependant, un fait était certain - si la pandémie s'est propagée et les cas graves ont augmenté de façon exponentielle, les ventilateurs seraient cruciaux pour traiter correctement les patients. Une autre certitude :de nombreux pays, y compris le siège social de Protocase au Canada, ne disposaient pas d'un approvisionnement suffisant en ventilateurs pour un tel scénario.
Au début de la pandémie de COVID-19, le gouvernement fédéral a jugé Protocase essentiel, en raison de notre clientèle d'organisations travaillant dans l'innovation, la médecine, l'aérospatiale et la défense. Mais au-delà d'être ouvert et prêt à fabriquer des pièces et des boîtiers personnalisés pour nos clients afin qu'ils puissent continuer à innover et à développer de nouvelles technologies, l'équipe Protocase voulait faire sa part pour aider à faire face à la pandémie de COVID-19. Le projet? Construisez un ventilateur portable fonctionnel qui pourraient être rapidement fabriqués et assemblés.
Le défi
Après avoir contacté un groupe de professionnels de la santé, dont des médecins urgentistes, des inhalothérapeutes et autres, pour discuter des critères d'un ventilateur fonctionnel, notre équipe de recherche et développement a cartographié le système pneumatique. Une partie cruciale de la conception d'un ventilateur sont les valves, qui, fonctionnant en tandem avec des tuyaux de branchement, forment un circuit pour l'inspiration et l'expiration. L'équipe devait trouver trois types courants de vannes :un clapet anti-retour, un clapet anti-retour à pression réglable et un solénoïde.
Un problème :les vannes prêtes à l'achat étaient extrêmement demandées.
«Tout le monde sautait sur les versions de ces pièces qui conviendraient aux ventilateurs et à toutes les différentes solutions à la pandémie. Il y a eu des interruptions de la chaîne d'approvisionnement », explique Justin Lewis, ingénieur mécanique au sein de l'équipe R&D de Protocase. «Après avoir lutté un peu pour essayer de commander les vannes dont nous avons besoin, nous avons décidé de fabriquer les nôtres. Les vannes résultantes sont essentiellement la version de ces pièces que nous pouvions fabriquer rapidement avec ce que nous avions en interne sans avoir à gérer les délais. »
Les conceptions des vannes se sont rapidement concrétisées, car la conception globale (et les critères impératifs de la fonction d'une vanne) était déjà bien définie et établie.
« Fondamentalement, on nous a donné une liste de critères auxquels devaient répondre les médecins et les inhalothérapeutes que nous avons consultés », explique Jordan Rose, ingénieur R&D mécanique chez Protocase. "Sur la base de la conception pneumatique de l'ensemble du système, vous pouvez en quelque sorte déterminer les pressions auxquelles ces éléments doivent agir. C'est l'autre moitié des informations dont nous avions besoin pour continuer. Nous avons examiné comment fonctionne un clapet anti-retour, et à quelles pressions et débits ces éléments doivent-ils fonctionner, en utilisant les mathématiques que nous aurions apprises à l'école d'ingénieurs."
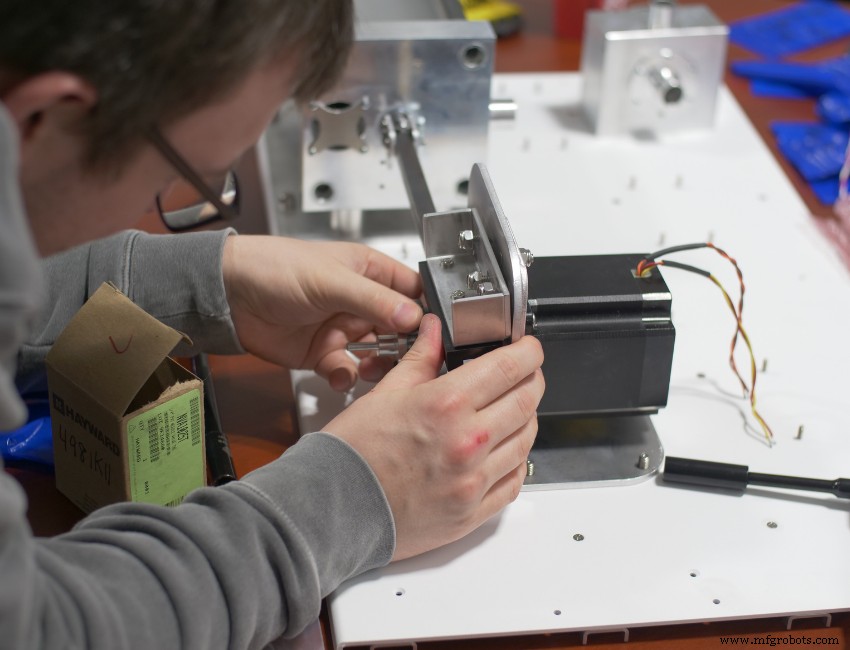
"C'est du Lego industriel. Il s'agit de voir l'ensemble, construit à partir de ces blocs de base », explique Lewis. "Ce sont les blocs de base - nous devons juste les construire et les assembler dans le bon ordre afin qu'ils atteignent tous l'objectif."
Une fois les conceptions de vannes bien établies, ainsi que les exigences de pression et de débit définies, l'équipe s'est mise à travailler sur la construction des prototypes initiaux. Pour cette tâche, l'impression 3D était la première étape logique, car elle validerait les dimensions et vérifierait les calculs de pression et de débit.
"Étant donné que le processus d'usinage est considérablement plus long, il est important d'imprimer d'abord les pièces en 3D pour confirmer les spécifications", déclare Rose.
"L'impression 3D a validé l'ensemble du schéma", dit Lewis. "Cela nous a permis de tout assembler et de dire :"D'accord, ça marche", avant d'investir tout le temps et l'argent nécessaires pour fabriquer les pièces usinées appropriées."
L'équipe a effectué quelques itérations d'impression 3D du clapet anti-retour et du clapet anti-retour réglable, en essayant de rationaliser autant que possible la conception et de s'assurer qu'elle fonctionnait correctement. Par exemple, dans une première conception du clapet anti-retour réglable, le clapet avait un cercle et un bossage d'un côté.
"La raison pour laquelle j'ai fait cela était de voir quel type de soutien était nécessaire pour ce patron circulaire. Sinon, vous devrez peut-être le soutenir en dessous », explique Rose. "Je voulais essayer d'éviter tout problème de surface qui pourrait exister afin que le tuyau qui se trouvait dans le système pneumatique s'adapte correctement. Finalement, nous sommes passés à une forme de tube droit qui fonctionnait bien."
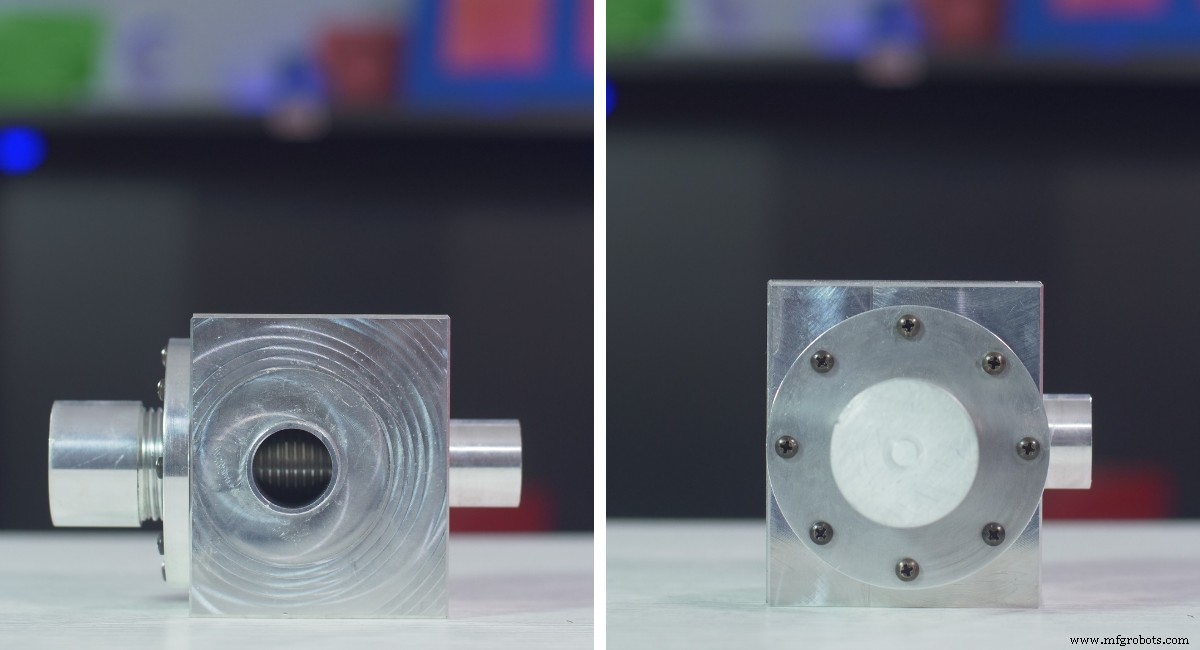
"La théorie générale était bonne dès le départ, il s'agissait davantage de sceller correctement, de s'assurer que nous avions les bons ressorts", explique Lewis.
La seule vanne qui n'a pas été imprimée en 3D en tant que prototype initial était le solénoïde pneumatique - pour une bonne raison.
"Cela a l'air simple de l'extérieur, car ce n'est qu'un gros bloc de métal, mais à l'intérieur, il y a beaucoup de chambres différentes", explique Rose. "Ce n'est pas quelque chose qu'il serait possible d'imprimer en 3D."
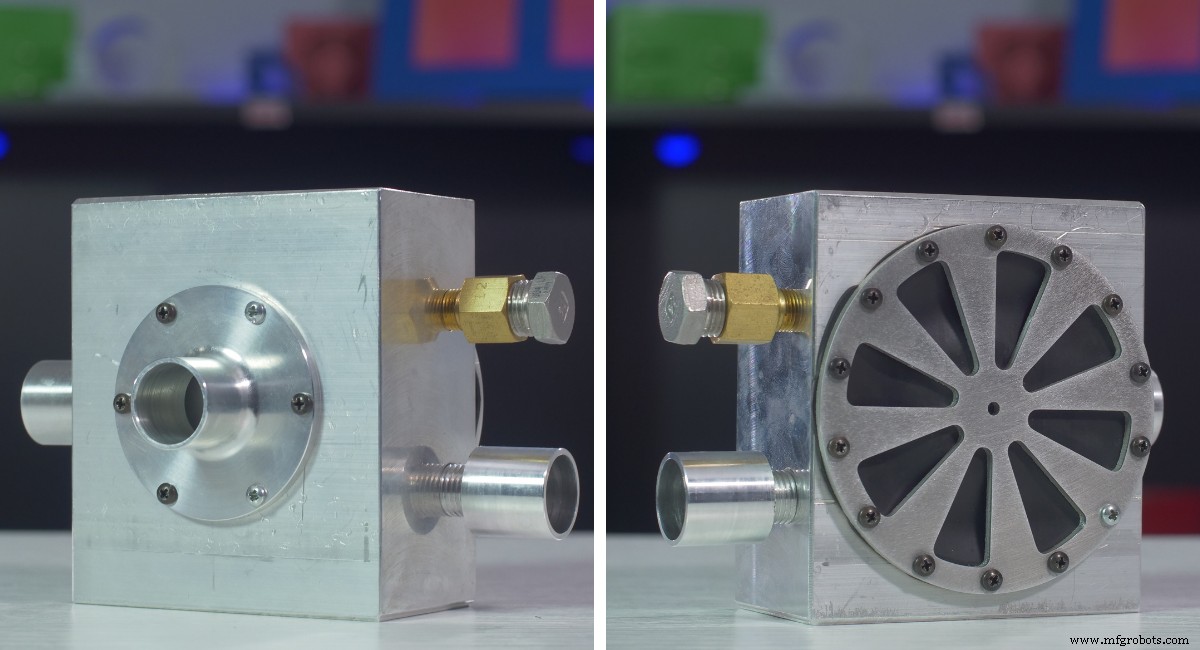
"Avec l'impression 3D, il peut être plus difficile d'obtenir un joint d'arbre sur ce type de matériau", explique Lewis. "En fraisant le solénoïde, nous avons pu l'usiner avec une belle finition et y placer un arbre ajusté pour que tout soit correctement scellé."
Le solénoïde pneumatique comprend tous les aspects de la fabrication sur mesure de Protocase, avec des pièces de tour CNC, des pièces fraisées, des pièces en tôle, une pièce imprimée en 3D, ainsi que du matériau de joint. Au lieu de découper le matériau du joint en caoutchouc en un joint typique, l'équipe a découpé le caoutchouc en cercle à l'aide d'un routeur CNC pour créer une vessie de clapet anti-retour.
Regarder en arrière - et regarder vers l'avant
En fin de compte, commencer par l'impression 3D a été extrêmement bénéfique pour s'assurer que les pièces industrielles Lego s'emboîteraient et fonctionneraient comme le schéma présenté, sans prendre un temps précieux et crucial pour l'usinage CNC de toutes les pièces.
"C'est juste agréable de savoir que vous allez dans la bonne direction. Vous avez le schéma, vous assemblez le tout, puis vous vous dites :« Oh, attendez, tout est mal agencé. » Il y a eu des moments où nous avons fait des ajustements à la façon dont l'ensemble du système était agencé », explique Lewis. "Vous ne voulez pas dépenser beaucoup d'argent et de temps sur des blocs usinés pour le faire. Ces pièces imprimées en 3D fuyaient un peu, mais nous savions que l'ensemble du système fonctionnait, de sorte que nous pouvions investir en toute confiance dans la phase suivante."
Même la version finale des vannes usinées CNC n'est peut-être pas la plus simple et est peut-être maladroite par rapport aux homologues prêtes à l'achat sur le marché, mais il y a une raison à cela, dit Rose.
« Nous les avons conçus pour qu'ils soient bien dans nos capacités, car si jamais nous devions aller en usiner 2 000 d'entre eux, nous pourrions les faire rapidement », explique-t-il. "Nous avons activement essayé de ne rien concevoir d'extraordinaire ni de repousser les limites de notre usinage."

Comme pour tout prototype ou développement d'un produit, il peut être utile de réfléchir à ce qui s'est bien passé et à ce qui pourrait être amélioré. Dans l'ensemble, Rose et Lewis ont convenu que le projet restait sur des bases solides grâce à la fabrication agile disponible au bout de leurs doigts pour tester les dispositions et confirmer les spécifications sans aucun délai.
Avec le recul, cependant, ils voient les avantages d'utiliser un système électrique pour le ventilateur. Un système avec un système électrique peut être activé lorsque vous en avez besoin et désactivé lorsque vous en avez besoin à l'aide du logiciel. Un système pneumatique, en revanche, a un système de vide qui peut être difficile.
"Ce solénoïde pneumatique, c'est comme jouer d'un instrument de musique", explique Lewis. "C'est formidable si vous pouvez le faire régler à la sortie, mais si quelque chose change, vous ne voulez pas avoir quelqu'un à l'hôpital qui sait vraiment comment faire fonctionner la machine. Idéalement, vous voulez quelqu'un qui peut régler le bouton facilement. En ce qui concerne quelque chose en interne que nous pourrions faire rapidement, le système que nous avons conçu et construit est excellent, mais ce que nous avons appris depuis mars, c'est que les lignes d'alimentation sont quelque peu revenues à la normale et nous aurions peut-être pu opter pour un système électrique ."
"À l'époque, c'était la seule chose que nous ne pouvions pas obtenir - un solénoïde électrique", ajoute Rose. « Tout le monde était paniqué. Maintenant, ils sont beaucoup plus faciles à trouver.
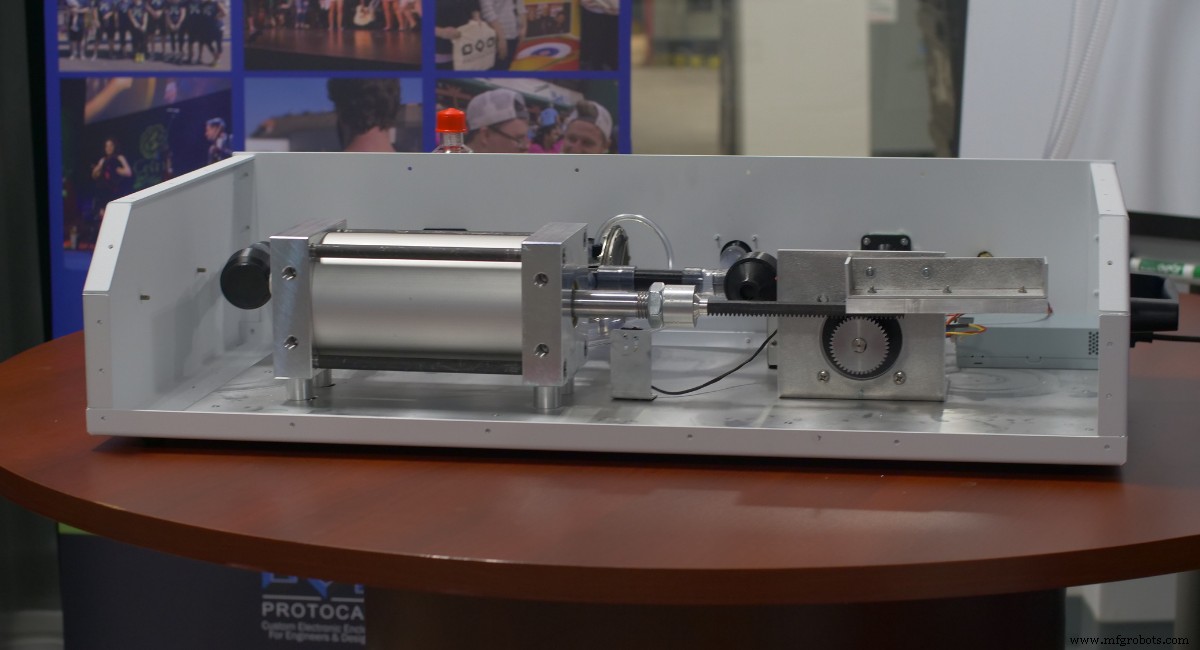
En regardant la situation dans son ensemble, le projet de ventilateur, y compris la conception et la fabrication des trois valves, a contribué à façonner le travail de l'équipe R&D de Protocase.
«Lorsque ce projet a été lancé, il semblait être une urgence mondiale. Nous avons laissé tomber tout le reste et un groupe d'entre nous s'est tous réunis », explique Rose. "Ce que nous avons réalisé, en faisant ce projet, c'est que nous pouvions arrêter nos autres projets pour nous concentrer sur une ou deux choses seulement, et vraiment réduire les choses."
Au lieu de trop se disperser ou de s'isoler du travail de l'autre, le groupe de recherche et développement se concentre désormais sur le fonctionnement en équipe.
« Nous avons des objectifs spécifiques sur lesquels nous pouvons tous travailler ensemble et nous pouvons mettre nos ressources en commun », explique Lewis. "Cela a juste changé la façon dont tout le monde travaille sur des projets, nous traitons presque chaque projet maintenant comme une sorte d'urgence. Ce projet a été le catalyseur de nombreuses améliorations au sein de notre département R&D."
Technologie industrielle
- Comment préparer la chaîne du froid pour les demandes de vaccins COVID-19
- Comment la logistique des beaux-arts change le marché de l'art pour de bon
- Comment se préparer à la prochaine interruption de la chaîne d'approvisionnement
- Comment garantir la préparation aux urgences dans l'entrepôt
- Quels sont les avantages de l'impression 3D pour les fabricants de métaux ?
- Quatre opportunités émergentes pour l'industrie de l'aluminium
- Qu'est-ce qu'AutoCAD ? Comment ça marche et à quoi ça sert
- Quelques outillages de mesure nécessaires à l'usinage de pièces mécaniques
- Qu'est-ce qu'une balise RFID ? Découvrez comment fonctionnent les étiquettes RFID, à quoi elles servent et certains des inconvénients de la technologie RFID