Sable de moulage - Propriétés, types, processus, QCM
Dans cet article, nous allons en savoir plus sur Qu'est-ce que le sable de moulage ,Propriétés du sable de moulage et types de sable de moulage .
Le principal matériau utilisé dans l'atelier de fonderie pour le moulage est le sable. En effet, il possède les propriétés indispensables à des fins de fonderie.
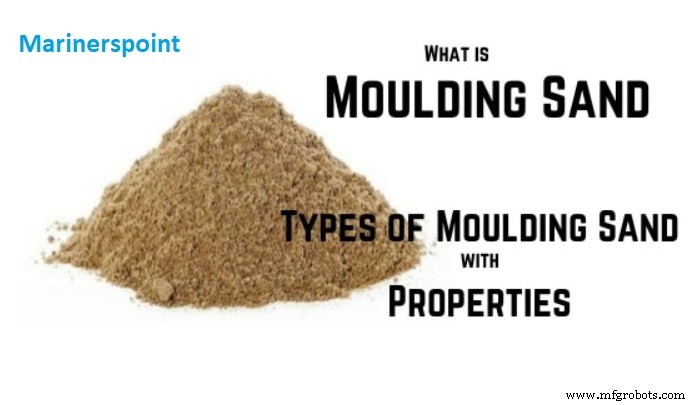
Sources
Tous les sables sont formés par la fragmentation des roches sous l'action de forces naturelles telles que le gel, le vent, la pluie, la chaleur et les courants d'eau. Les roches, cependant, sont très complexes dans leur composition, et les sables contiennent la plupart des éléments des roches dont ils sont des fragments. Pour cette raison, les sables de moulage dans différentes parties du monde varient considérablement. Aujourd'hui, le sable est obtenu à partir d'endroits qui étaient probablement autrefois des fonds et des rives de rivières et de dunes de sable.
En Inde, les sables de fonderie se trouvent dans la région de Damodar et Barakar, Santhal Pargana (Bihar), Batala (Gurdaspur, Punjab), Bhavnagar (Saurashtra), Londha (Maharashtra), Avadi et Veeriyambakam (Madras), Kanpur, Jabalpur, Rajkot, Guntur , à Ganges et bien d'autres endroits.
Principaux ingrédients
Les principaux ingrédients des sables de moulage sont :(1) grains de sable siliceux (2) argile (3) humidité et (4) matériaux divers.
La silice sous forme de quartz granuleux, lui-même un sable, est le principal constituant du sable de moulage. Le sable de silice contient de 80 à 90 % de dioxyde de silicium et se caractérise par une température de ramollissement et une stabilité thermique élevées.
C'est un produit de la décomposition de roches de quartz ou la décomposition du granit, qui est composé de quartz et de feldspath . Le feldspath, lorsqu'il se décompose, devient de l'argile (silicate d'aluminium hydraté). Cependant, les grains de sable de silice confèrent un caractère réfractaire, une résistivité chimique et une perméabilité au sable. Ils sont spécifiés en fonction de leur taille moyenne et de leur forme.
Argile est défini comme ces particules de sable (moins de 20 microns de diamètre) qui ne se déposent pas à une vitesse de 25 mm par minute, lorsqu'ils sont en suspension dans l'eau. L'argile est constituée de deux ingrédients : limon fin et vraie argile . Le limon fin est une sorte de matière étrangère ou de dépôt minéral et n'a aucun pouvoir de liaison.
C'est la vraie argile qui donne la force de liaison nécessaire au sable du moule, de sorte que le moule ne perde pas sa forme après le pilonnage. L'argile véritable est constituée d'agrégats extrêmement minuscules de particules cristallines, généralement en forme de flocons, appelées minéraux argileux. La plupart des sables de moulage pour différentes qualités de travail contiennent de 5 à 20 pour cent d'argile. L'humidité, en quantité requise, fournit l'action de liaison de l'argile.
Lorsque de l'eau est ajoutée à l'argile, elle pénètre dans le mélange et forme un microfilm qui recouvre la surface de particules d'argile en forme de flocons. La qualité de liaison de l'argile dépend de l'épaisseur maximale du film d'eau qu'elle peut maintenir. L'action de liaison est considérée comme meilleure si l'eau ajoutée est la quantité exacte requise pour former le film. D'autre part, l'action de liaison est réduite et le moule s'affaiblit si l'eau est en excès. L'eau doit être comprise entre 2 et 8 %.
Les matériaux divers que l'on trouve, en plus de la silice et de l'argile, dans le sable de moulage sont l'oxyde de fer, le calcaire, la magnésie, la soude et la potasse. Les impuretés doivent être inférieures à 2 %.
Classement
Types de sables de moulage :ils peuvent être classés généralement en trois types différents :(1) sables de moulage naturels , (2) sables synthétiques ou riches en silice , et (3) sables spéciaux .
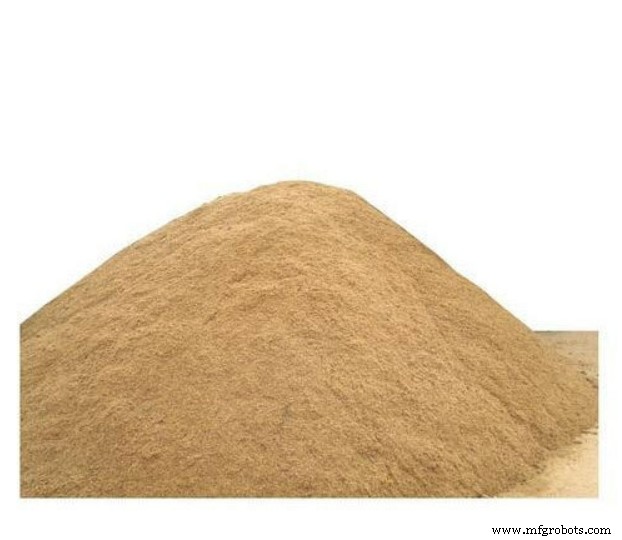
1. Sables de moulage naturels
Sables de moulage naturels , appelés sables verts, sont prélevés dans le lit des rivières ou sont creusés dans des fosses. Ils possèdent une quantité appréciable d'argile qui agit comme un lien entre les grains de sable et sont utilisés tels quels avec de l'eau ajoutée. La quantité et le type de minéral argileux présent affectent la résistance, la ténacité et la réfractarité du sable.
Ceux-ci sont également obtenus par concassage et broyage de grès jaune tendre, de roches carbonifères, etc. Au cours de l'opération de broyage, les agrégats d'argile se décomposent et les particules d'argile se répartissent uniformément sur les grains de sable. La forme du grain de ces sables doit être sous-anguleuse à ronde.
En raison de leur facilité de disponibilité, de leur faible coût et de leur grande flexibilité de fonctionnement, les sables de moulage naturels sont utilisés pour la plupart des moulages légers ferreux et non ferreux. Les exigences de ces sables sont satisfaites par IS :3343-1965 , qui les a classés en trois grades A , B et C , en fonction de leur teneur en argile et de leur température de frittage.
2. Sables synthétiques
Sables synthétiques sont essentiellement des sables riches en silice contenant peu (moins de 2 %) ou pas de liant (argile) sous forme naturelle. Ils se présentent sous forme de dépôts meubles ou mal consolidés d'origine sédimentaire, de dunes soufflées vers l'intérieur depuis la côte ou de dépôts accumulés dans les estuaires et les rivières le long de la côte.
Ils sont également fabriqués en fonderie en écrasant d'abord des grès de quartzite, puis en les lavant et en les calibrant pour obtenir une qualité de sable de forme et de distribution de grain requises. La résistance et les propriétés de liaison souhaitées de ces sables sont développées par des ajouts séparés tels que la bentonite, l'eau et d'autres matériaux.
Cela permet une plus grande flexibilité dans le contenu des propriétés telles que la résistance à l'état vert et à sec, les perméabilités et d'autres qui peuvent être facilement modifiées à volonté. En effet, les sables synthétiques sont donc plus chers que les sables naturels.
IS :1987-1974 couvre les exigences du sable à haute teneur en silice pour une utilisation dans les fonderies et le classe en trois grades en fonction de la teneur en silice .
3. Sables spéciaux
Sables spéciaux sont idéales pour obtenir des caractéristiques spéciales, qui ne sont pas habituellement obtenues dans d'autres sables. Le zircon, l'olivine, la chamotte, la chromite et la magnésite chromée sont souvent utilisés comme sables spéciaux. Les sables de zircon conviennent aux noyaux des moulages en laiton et en bronze. Certaines fonderies utilisent du sable d'olivine pour les moulages non ferreux de nature complexe. La chamotte est précieuse pour les pièces moulées en acier lourd.
Les sables de chromite et de chrome-magnésite sont particulièrement utiles lorsque la tendance au refroidissement doit être augmentée pour contrôler la solidification. Ils conviennent également comme matériaux de revêtement dans les moules pour les pièces moulées en acier.
Types de sable de moulage
Les sables à mouler peuvent encore être classés, selon leur usage, en nombre de variétés. Ceux-ci sont décrits ci-dessous.
Moulure au sable vert
C'est un mélange de sable de silice avec 18 à 30 pour cent d'argile, ayant un total d'eau de 6 à 8 pour cent. L'argile et l'eau fournissent le lien pour le sable vert. Il est fin, doux, léger et poreux. Étant humide, lorsqu'il est pressé dans la main, il conserve la forme qui lui donne l'impression sous la pression. Les moules préparés dans ce sable sont appelés moules à sable vert.
Moulage au sable sec
Le sable vert qui a été séché ou cuit après la fabrication du moule est appelé sable sec. Ils conviennent aux gros moulages. Les moules préparés dans ce sable sont appelés moules à sable sec.
Limon Sable
Le sable limoneux est riche en argile, jusqu'à 50 % environ, et sèche dur. Ceci est particulièrement utilisé pour le moulage de limon, généralement pour les gros moulages.
Face au sable
Le sable de parement forme la face du moule. Il est utilisé directement à côté de la surface du modèle et il entre en contact avec le métal en fusion lorsque le moule est coulé. Par conséquent, il est soumis aux conditions les plus sévères et doit donc posséder une résistance et une réfractarité élevées.
Il est composé de sable de silice et d'argile, sans ajout de sable usagé. Différentes formes de carbone sont utilisées pour empêcher le métal de brûler dans le sable. Ils sont parfois mélangés avec 6 à 15 fois plus de sable de moulage fin pour faire des parements.
La couche de sable de parement dans un moule varie généralement de 20 à 30 mm. De 10 à 15 % de la quantité totale de sable de moulage utilisé dans la fonderie est du sable de parement. Un mélange de sable de revêtement pour le moulage au sable vert de la fonte peut être composé de 25 % de sable frais et spécialement préparé, de 70 % de sable ancien et de 5 % de charbon marin.
Envers Sable
Le sable de support ou le sable de sol est utilisé pour soutenir le sable de parement et pour remplir tout le volume du ballon. Le vieux sable de moulage utilisé à plusieurs reprises est principalement utilisé à cette fin.
Le sable de support est parfois appelé sable noir en raison du fait que le vieux sable de moulage utilisé à plusieurs reprises est de couleur noire en raison de l'ajout de poussière de charbon et de la combustion au contact du métal en fusion.
Système Sable
Dans les fonderies mécaniques où le moulage à la machine est utilisé, un soi-disant sable de système est utilisé pour remplir tout le ballon. Dans les unités mécaniques de préparation et de manutention du sable, aucun sable de parement n'est utilisé. Le sable utilisé est nettoyé et réactivé par l'ajout de liants d'eau et d'additifs spéciaux. C'est ce qu'on appelle le sable système. Étant donné que tout le moule est constitué de ce système de sable, la résistance, la perméabilité et la réfractarité du sable doivent être supérieures à celles du sable de support.
Séparer le sable
Le sable de séparation est utilisé pour empêcher le sable vert de coller au motif et également pour permettre au sable sur la surface de séparation de la chape et de se séparer sans s'accrocher. Il s'agit de sable de silice propre et sans argile qui a la même fonction que la poussière de séparation.
Noyau Sable
Le sable utilisé pour fabriquer les noyaux est appelé sable à noyau, parfois appelé sable bitumineux. Il s'agit de sable de silice mélangé à de l'huile de noyau composée d'huile de lin, de résine, d'huile minérale légère et d'autres matériaux liants. Le brai ou les farines et l'eau peuvent être utilisés dans de gros noyaux pour des raisons d'économie.
Propriétés du sable de moulage
Quelles sont les propriétés du sable de moulage ?
Un bon sable de moulage doit posséder six propriétés. Propriétés du sable de moulage sont :il doit avoir une porosité, une fluidité, une aptitude à l'écrasement, une adhésivité, une cohésion ou une résistance et un caractère réfractaire.
- Porosité :- La propriété la plus importante du sable de moulage est la porosité, également connue sous le nom de perméabilité. Il fait référence à la capacité du sable de moulage à laisser passer les gaz. Lors du coulage du métal en fusion dans la cavité de sable, des gaz et de la vapeur sont produits. Cette propriété est affectée non seulement par la forme et la taille des particules de sable, mais également par la quantité d'argile, de liant et d'humidité dans le mélange.
- Fluxabilité :- La capacité du sable à combler de petits vides dans le motif. Une fluidité élevée produit un moule plus précis et est donc utile pour les moulages détaillés.
- Réductibilité :- La capacité du mélange de sable à s'effondrer sous la force. Une plus grande capacité d'écrasement du moule permet au métal coulé de se rétracter librement au fur et à mesure qu'il se solidifie, évitant ainsi les déchirures ou les fissures à chaud.
- Adhésivité :- L'adhésivité est la propriété du sable qui fait adhérer les particules de sable aux parois de la boîte de moulage. L'adhérence du sable permet un bon soulèvement de la chape avec le sable.
- Cohésion :- La cohésion du sable est la capacité de ses particules à rester ensemble. C'est la résistance à la traction du sable de moulage. Cette propriété est essentielle pour conserver les formes complexes du moule. Une résistance inadéquate peut entraîner l'effondrement des particules du moule lors de la manipulation, du retournement ou de la fermeture. L'ajout d'argile et de bentonite améliore la cohésion.
- Réfractarité :- Le caractère réfractaire du sable fait référence à sa capacité à résister à des températures élevées de métal en fusion sans fusion ni ramollissement. Les sables de moulage peu réfractaires peuvent s'enflammer lorsque du métal en fusion est versé dans le moule. Les moules en sable doivent généralement pouvoir résister à des températures allant jusqu'à 1 650 °C.
- Force :- La résistance du support qui a été séché ou cuit est appelée résistance à sec. Il doit alors avoir la force de résister aux forces érosives qui vous font fondre le métal et conserver sa forme.
Processus de moulage au sable
Moulage au sable , également connu sous le nom de moulage au sable ou processus de moulage au sable , est un procédé de fabrication basé sur la coulée qui utilise un moule en sable. Des objets métalliques et des composants de différentes tailles et formes en sont fabriqués. Pour mettre sa prévalence en perspective, le moulage au sable représente plus de 60% de tous les moulages métalliques. Les six phases principales du moulage au sable sont décrites en détail ci-dessous.
Étape 1 :Mettez le motif du moule dans le sable
La mise en place du modèle de moule dans le sable est la première étape du moulage au sable. Le moule a un impact direct sur la taille et la forme de la pièce moulée. En conséquence, les fabricants doivent développer de nouveaux moules afin de produire des articles et des composants métalliques dans des tailles et des formes spécifiées.
Étape 2 :Établir un système de contrôle
Un système de porte est utilisé dans presque tous les processus de moulage, et le moulage au sable ne fait pas exception. Il canalise le moule fondu dans la cavité du moule à l'aide d'un gobelet verseur et de tunnels ou de "portes" vers le moule. Les entreprises de fabrication mettront en place un système de porte comme celui-ci après avoir défini la conception du moule dans le sable.
Étape 3 :le motif de la moisissure doit être supprimé
Les entreprises de fabrication peuvent ensuite retirer le modèle de moule du sable après la mise en place du système de porte. À ce moment, le modèle de moule n'est pas pertinent. Le sable prend la forme du motif du moule lorsqu'il est placé à l'intérieur. En conséquence, il est possible de supprimer le motif du moule.
Étape 4 :Verser le métal en fusion dans la cavité du moule
Il est maintenant temps de verser le métal en fusion dans la cavité du moule. Le fer, l'acier, l'aluminium, le bronze, le magnésium, le zinc et l'étain ne sont que quelques-uns des métaux et alliages pouvant être coulés dans le sable. Les organisations de fabrication peuvent avoir besoin de chauffer des métaux ou des alliages jusqu'à 3 000 degrés Fahrenheit, selon le métal ou l'alliage exact utilisé. Le métal ou l'alliage est versé dans la cavité du moule une fois qu'il est passé d'un état solide à un état liquide.
Étape 5 :Attendez que le métal refroidisse
Les entreprises manufacturières doivent attendre que le métal en fusion refroidisse une fois qu'il a été placé dans le trou du moule. Encore une fois, différents types de métaux nécessitent des temps de refroidissement variés. Le métal en fusion se refroidira et passera d'une forme liquide à une forme solide.
Étape 6 :Ouvrir le moule pour retirer le moulage métallique
L'ouverture du moule pour extraire le moulage de métal nouvellement généré est la sixième et dernière étape du moulage au sable. Les modèles de moules sont généralement réutilisables, mais les moules eux-mêmes ne le sont pas. Par conséquent, chaque fois qu'une entreprise de fabrication souhaite fabriquer un nouveau produit ou composant métallique en utilisant le moulage au sable, elle doit développer un nouveau moule.
Effondrement du sable de moulage
Effondrement du sable de moulage fait référence à la capacité du sable à être facilement retiré du moulage une fois qu'il s'est solidifié. Les sables à faible affaissement adhéreront avec ténacité à la coulée. Un sable peu compressible provoquera des fissures et des déchirures à chaud dans les pièces moulées en métal qui fléchissent beaucoup lors du refroidissement ou qui ont de longues plages de températures de congélation. Pour améliorer la collapsibilité, certains additifs peuvent être introduits.
QCM
1. La perméabilité peut être définie comme la propriété du sable de moulage
A. pour maintenir les grains de sable ensemble
B. pour permettre aux gaz de s'échapper facilement du moule
C. pour résister à la chaleur de la fonte sans montrer aucun signe de ramollissement
D. aucune des réponses ci-dessus
Réponse : Option B
2. Pourquoi le sable de moulage devrait-il être poreux ?
A. Pour que les gaz entrent
B. Pour que l'eau entre
C. Pour que les gaz s'échappent
D. Pour que l'eau s'échappe
Réponse :Option C
Explication : Un sable de moulage est défini comme un sable qui a des trous et peut contenir une certaine quantité d'humidité. Un moulage doit contenir des pores et être poreux afin que les gaz puissent s'échapper librement.
Tout était sur le sable de moulage où nous avons couvert tous les sujets tels que Qu'est-ce que le sable de moulage, décrit les propriétés du sable de moulage, le processus de moulage de sable vert, le sable sec, la collapsibilité et certains QCM basés sur ces sujets.
Technologie industrielle
- Types et propriétés de poudre de tantale
- Sable de moulage :types et constituants | Coulée | Métallurgie
- Propriétés du sable de moulage | Matériaux | Coulée | Métallurgie
- C'est quoi Former ? Types de processus de formage [Notes &PDF]
- Qu'est-ce que le sable de moulage ? - Types et propriétés
- Définition, processus et types de fraiseuses
- Signification et types de processus de fabrication
- Types d'équipement de moulage au sable
- AMPCO® 25 Moulages au sable