6 Différents types de procédés de coulée utilisés dans les fonderies de métaux
Ici, nous énumérons et discutons de 6 types différents de traitement de coulée couramment appliqués dans les fonderies métallurgiques. Cochez ici pour spécifier les différents types de processus de moulage, les avantages et les inconvénients et les applications de chaque technique de moulage.
Le moulage est un processus de travail des métaux dans la fonderie qui servait à fabriquer des pièces moulées dans toute une gamme d'industries, de l'ingénierie mécanique, des composants automobiles, des pièces aérospatiales aux produits ménagers de tous les jours.
Le traitement de coulée fonctionne sur la fusion du métal, le coulage dans les moules et l'attente de la solidification. Le dégrossissage collecté peut être utilisé directement ou doit passer par d'autres étapes d'usinage.
La coulée de métal est un processus très flexible et peut fabriquer des pièces de forme complexe quelle que soit la dureté du métal, mais uniquement sur la température de fusion du métal. On peut dire que tout métal pouvant être fondu peut être coulé.
Il existe différentes techniques pour traiter le travail des métaux et chaque fonderie investit et se spécialise dans certains types de traitement de fonderie. Dans cet article, nous présentons les 6 différents types de processus de coulée couramment utilisés dans les fonderies de métaux . Vous chercherez la réponse à la façon dont les pièces de fonderie sont traitées par différents types de méthodes de coulée de métal et les avantages et les inconvénients de chaque technologie.
1. Moulage au sable vert
Qu'est-ce que le moulage au sable vert ?
La technique du sable vert a une longue tradition dans l'industrie du moulage, mais elle est encore largement utilisée aujourd'hui en raison de son efficacité. Le moulage au sable vert fait partie des différents types de moulage les plus traditionnels et préférables dans la fonderie de moulage .
Dans ce traitement de coulée, le moule en sable est une production de masse. Chaque moule en sable est utilisé une seule fois et est cassé pour recueillir le dégrossissage.
Différent du moulage au sable de résine, le sable vert présente une teneur en humidité. Le terme «vert» ne concerne pas sa couleur, mais la texture de l'humidité dans le sable. Il a la capacité de se lier naturellement principalement grâce aux agents argileux.
Composition du moule de sable vert
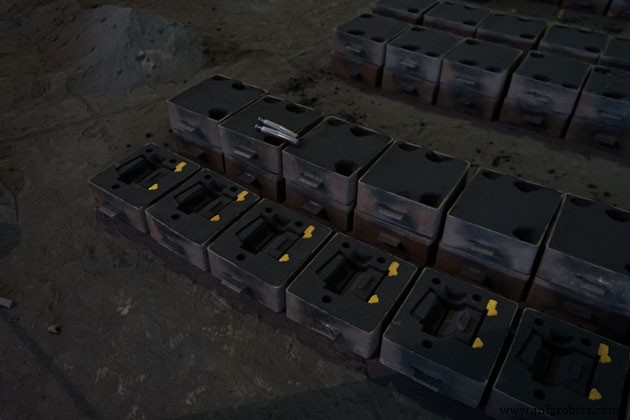
Pour fabriquer un moule en sable vert, la fonderie de métaux associe les composants suivants :
- Sable :sable de silice (SiO2), sable de chromite (FeCr2O4) ou sable de zircon (ZrSiO4) (environ 75 à 85 %)
- Argile bentonite :(5 à 11 %)
- Eau (2-4 %)
- Autres (3-5 %)
Le procédé de moulage au sable vert
Le moulage au sable vert est traité en suivant ces étapes
- Étape 1 :Mélanger le sable selon un ratio. Il est très important que détermine la liaison du mélange de sable. Chaque fonderie de métaux suit le ratio ci-dessus mais ils auront une formule de mélange secrète en ajoutant d'autres agents.
- Étape 2 :Charger du sable dans le mouleur et appuyer sur le motif pour créer la cavité du moule. Aujourd'hui, la fonderie utilise un dispositif de chape et de traînée pour fabriquer le moule en sable.
- Étape 3 :En supprimant le motif, une cavité de moule ayant une forme similaire à la coulée d'intention est créée.
- Étape 4 :Application d'une couche de revêtement sur la surface du moule pour augmenter la brillance de la surface et la résistance à la chaleur.
- Étape 5 :Coulée du métal en fusion dans la cavité du moule et refroidissement. Récupérez l'ébauche et passez à d'autres étapes d'usinage (si nécessaire).
- Étape 6 :Répétez ces étapes pour créer suffisamment de moules pour la production de masse.
Caractéristiques du moulage au sable vert
Avantage :
- Il s'agit d'une production économique et peu coûteuse, en particulier en faible volume
- Ne nécessite pas d'investissement de très haute technologie dans les installations de l'usine
- Demander une commande de casting à volume moyen et élevé
- Permettez à tous les alliages d'être versés dans le moule (matériaux ferreux et non ferreux). Plus peut être utilisé pour presque le motif et la conception
- Le sable peut être réutilisé après la collecte du moulage. Cela permet d'économiser le coût des matériaux d'entrée pour la fonderie.
Limites
- Limite de taille de casting. Il peut faire des moulages dans une gamme de poids de 1 à 500 livres. Pour les plus gros, il faut envisager d'autres méthodes de moulage.
- Il n'est pas préférable de jeter des détails de moulage complexes
- Grande tolérance qui nécessiterait plus de traitements d'usinage
- Créer des inquiétudes sur les défauts de moulage tels que l'évent, la porosité, etc. mais peut être contrôlé par les conseils techniques de la fonderie.
Applications de moulage au sable vert
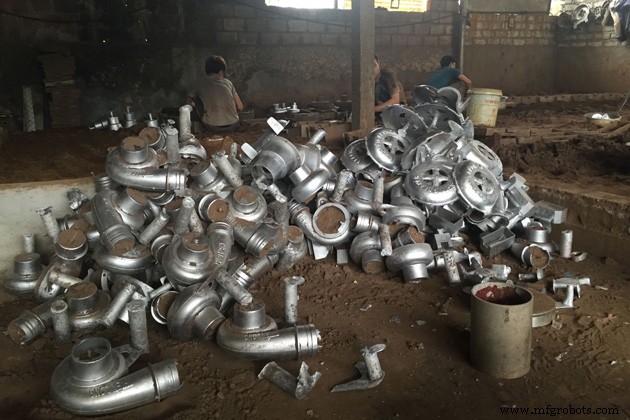
Le moulage au sable vert est très populaire avec une gamme d'applications. En Amérique, 42 % des pièces moulées sont fabriquées selon le procédé de sable vert, tandis que le moulage sans cuisson, en comparaison, en prend 40 % (la deuxième méthode de moulage populaire).
Vous pouvez trouver les pièces de moulage au sable vert, à partir de pièces de décoration extérieure telles que lampadaire, banc, corbeille; détails d'ingénierie, pièces automobiles, aérospatiale, boîtier de pompe au poids de la bouée marine, etc.
En savoir plus sur le moulage au sable vert ici.
2. Moulage au sable de résine furannique
Qu'est-ce que le moulage au sable de résine furannique ?
D'autres types de processus de coulée courants dans les fonderies de métaux sont le moulage au sable de résine de furane. Contrairement au sable vert qui fournit une liaison naturelle, le moulage au sable de résine de furane repose sur certains catalyseurs et liants pour lier le sable. Dans cette méthode de coulée, le sable, la résine de furane et les catalyseurs se mélangent et le mélange de sable s'auto-durcit par la réaction chimique.
Le crépi collecté présente un bon état de surface lisse et une grande précision.
Composition du moule en sable de résine furanique
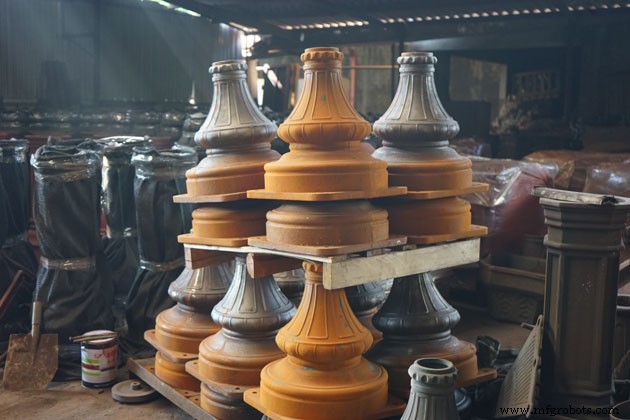
Dans le moulage au sable de résine furannique, le moule est fabriqué selon la formule suivante :
- Sable :sable de silice (SiO2) (40-60 %)
- Résine furannique :0,7-1,3 % selon la masse coulée. Il est nécessaire moins ou sans azote en fonction des exigences de moulage et de la structure des pièces de moulage.
La résine de furane joue un rôle important dans cette méthode de coulée. C'est un composé polymère avec 75% d'alcool furfurylique + 11% de formaldéhyde + 9% d'ure + 5% d'eau. Le rapport de formaldéhyde et d'urée affecte le temps de solidification et la résistance du mélange de résine, tandis que l'alcool furfurylique (FA) affecte les propriétés de résistance à la chaleur du mélange.
- Catalyseur :agent de solidification et agents d'annexion (30-50 %)
Le processus de moulage au sable de la résine furannique
Les procédés de moulage au sable de résine furanique sont expliqués par le tableau suivant :
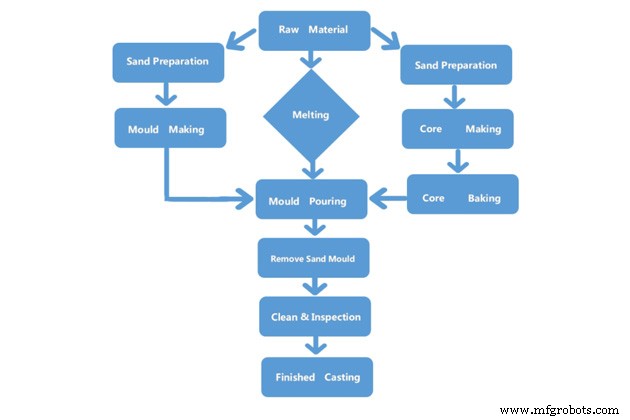
Caractéristiques du moulage au sable de la résine furanique
Avantage
- Tolérance serrée et haute précision
- Il offre une excellente finition de surface lisse par rapport aux autres méthodes de coulée
- Minimiser les défauts de moulage tels que les trous de sable, les trous d'air et le rétrécissement
- Flexible dans la taille de la coulée. Le moulage au sable de la résine de furane peut produire de grosses pièces allant d'une douzaine de kilogrammes à plusieurs tonnes de poids
Limites
- C'est une méthode plus coûteuse que les autres processus de moulage
- Exigence stricte pour les matières premières
- Crée des problèmes environnementaux
Applications de moulage au sable de résine furannique
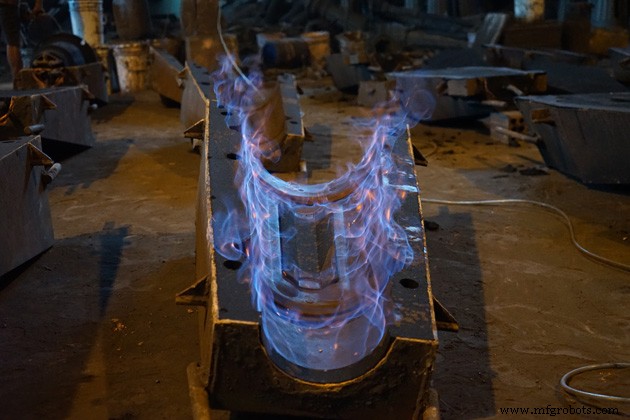
Avec son excellent avantage, le boîtier en sable de résine de furane est souvent préféré pour couler des pièces complexes et détaillées qui nécessitent une grande précision et une tolérance serrée telles que des pièces automobiles, des détails de machines agricoles, des pièces aérospatiales, des moteurs de navires, etc.
En savoir plus sur le moulage au sable de résine furannique ici.
3. Coulée de mousse perdue
Qu'est-ce que la coulée de mousse perdue ?
Le moulage de mousse perdue est une sorte de processus de modèle par évaporation similaire au moulage de précision. Au lieu de cire, le motif est fait de mousse selon la méthode de la mousse perdue.
Contrairement au moulage au sable, ce modèle peut être retiré et réutilisé pour fabriquer d'autres moules, le modèle de mousse perdue peut être utilisé une fois et s'évapore pour former les pièces de moulage.
Pas aussi populaire que le moulage au sable, mais le moulage en mousse perdue est l'un des différents types de processus de moulage qui reste des caractéristiques assez impressionnantes qui conviennent à la production en série de pièces de moulage de petits et moyens détails.
Le processus de coulée de mousse perdue
Le processus de coulée de mousse perdue suit ces étapes :
- Étape 1 :confection de patrons. Le motif en mousse perdue peut être réalisé par des machines de découpe ou par la méthode de moulage par injection de billes de polystyrène . Le motif peut être un motif complet (conception simple) ou quelques sections ensuite collées ensemble pour former une réplique du moulage intentionnel.
- Étape 2 :revêtement de peinture isolante pour améliorer la durabilité de la surface du moule et protéger de l'érosion et des bris
- Étape 3 : le modèle de mousse est placé dans un flacon entourant le sable non lié et compacté.
- Étape 4 : verser le métal en fusion, évaporer le motif en mousse et former le crépi
- Étape 5 : nettoyage du sable restant et usinage supplémentaire si nécessaire.
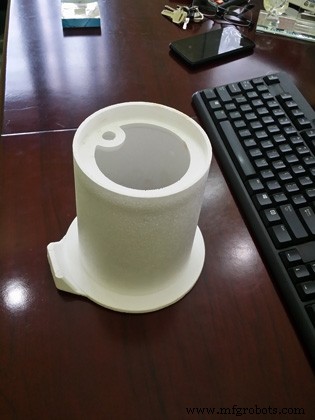
Caractéristiques de coulée de mousse perdues
Avantage
- Conception flexible
- Moulez une forme complexe impensable dans d'autres processus de coulée
- Haute précision et tolérance serrée
- Aucun défaut de noyau, aucun déplacement de moule, excellente finition de surface lisse
- Réduire le temps de traitement
- Réduire les coûts de production et d'investissement
Limites
- C'est plus cher que les autres méthodes
- Ce sera très coûteux pour l'installation ou les petites commandes
Applications de coulée de mousse perdue
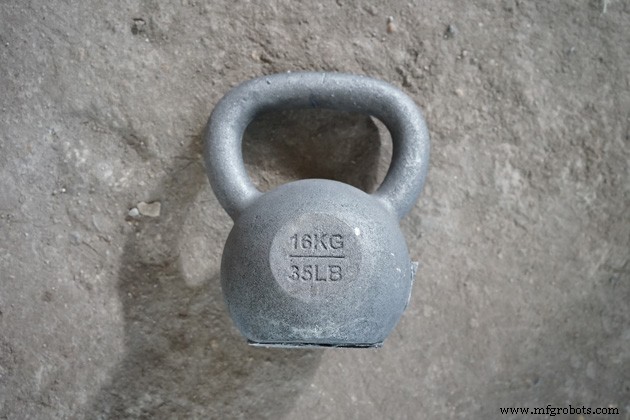
La coulée de mousse perdue ne se limite à aucune conception et type d'alliage. Il s'agit souvent de choisir de fondre des pièces de fonderie complexes que d'autres méthodes ne peuvent pas fonctionner. Par exemple, des pièces détachées automobiles, des éléments de machines de haute précision, des produits de base complexes…
En savoir plus sur le moulage de mousse perdue ici.
4. Moulage de précision
Qu'est-ce que le moulage de précision ?
Le moulage à modèle perdu ou le moulage à la cire perdue est une méthode de moulage avancée utilisée pour mouler des formes compliquées et à parois minces. Ce processus est similaire à la coulée de mousse perdue. Au lieu du modèle en mousse, le modèle en cire jetable est formé par la méthode d'injection puis enduit de plusieurs couches de matériau réfractaire.
En faisant fondre le modèle de cire, une cavité de moule est créée et prête à recevoir le liquide métallique. Notez que le patron n'est utilisé qu'une seule fois et que chaque lancer nécessite un patron.
Cette méthode a les caractéristiques de couler des détails avec une grande précision, il est donc souvent préférable de couler des produits pour l'industrie de la fabrication de machines, en particulier la production de petits détails, de haute précision, sans usinage ou ne pouvant pas être usinés.
Le processus de moulage de précision

- Étape 1 :Réalisation du patron et du moule
- Étape 2 :Injectez la cire dans le moule pour réaliser des motifs en cire.
- Étape 3 :Assemblage des sections de patron
- Étape 4 :Confection de coquillages
- Étape 5 :Déparaffinage par la chaleur
- Étape 6 :Verser le métal en fusion
- Étape 7 :Fracassant
- Étape 8 :Coupure
- Étape 9 :pièces moulées finies
Caractéristiques du moulage de précision
Avantage
Le moulage d'investissement est une approche de moulage moderne avec de nombreux avantages.
- Par rapport au moulage au sable, le moulage à la cire perdue peut améliorer les détails complexes, les parois minces, la qualité de surface élevée et réduire considérablement les travaux d'usinage. De nombreuses pièces moulées finies peuvent être utilisées immédiatement.
- Il peut fabriquer des produits pesant de quelques grammes à une tonne.
- Peut couler des alliages difficiles à fondre tels que l'acier inoxydable, l'acier fin
- La surface de coulée est très précise et brillante
- Le moulage est moins susceptible de se fissurer ou de se déformer
Limites
- Haute intensité de main-d'œuvre
- Long cycle de production
- Les coûts de fabrication des moules sont élevés
Applications de moulage de précision
Pièces moulées complexes ou en production de masse pour fabriquer des engrenages ; coffres à vélo; disque moto; pièces de rechange dans la grenailleuse … Coulée avec un poids de 0,02 ÷ 100 kg ; épaisseur à 0,3 mm et diamètre du trou à 2 mm.
5. Moulage sous pression
Qu'est-ce que le moulage sous pression ?
Le moulage sous pression est la méthode de moulage sous haute pression et appliquée pour couler des métaux et alliages non ferreux.
Il est utilisé dans le moulage de pièces pour les commandes en gros car l'avantage de cette méthode de moulage est sa productivité élevée et son processus simplifié grâce à l'application d'une ligne entièrement automatisée. Le crépi collecté a une tolérance serrée, une haute précision et une belle finition de surface brillante.
Le processus de moulage sous pression
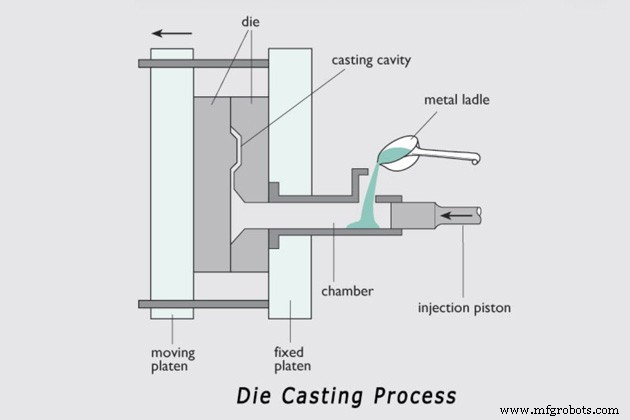
- Étape 1 :Fusion du métal en fluide
- Étape 2 :Verser le métal en fusion dans la chambre
- Étape 3 :Haute pression le système d'injection à piston pousse le fluide dans le moule
- Étape 4 :Attendez que le moulage soit solidifié, puis retirez le noyau
- Étape 5 :Le loquet éjectera l'objet
- Étape 5 :Retirez les matériaux de rebut et continuez le segment suivant
L'ensemble du processus de coulée de la méthode de coulée sous pression nécessite l'utilisation de pistons à haute pression et de presses étanches pour assurer la durabilité de la coulée. Avec le processus de ligne automatique, la qualité de la coulée dépend de nombreux facteurs tels que la composition du métal en fusion, le système de machines, la pression de coulée, etc.
Les caractéristiques de moulage sous pression
Avantage
- Tolérance serrée et haute précision
- Capable de couler des coulées à parois minces même de 1 mm
- Surface de moulage très brillante
- Haute cohérence des dimensions et conception uniforme
- Réduire le travail d'usinage
- Efficacité de la production à haut volume et convient aux commandes groupées
- Lignes entièrement automatiques qui réduisent le coût de la main-d'œuvre
Limites
- Coût d'outillage élevé
- Nécessite un investissement préalable dans les machines
- Limite dans la conception des moulures
Applications de moulage sous pression
Le moulage sous pression est souvent utilisé dans le moulage de petites pièces, les commandes en gros telles que les pistons, les vilebrequins, les boîtes de vitesses, etc. Il peut produire le moulage pesant souvent jusqu'à 5 kg, mais il existe également un boîtier de moulage pour les pièces pesant jusqu'à 50 kg mais le prix est très élevé.
Les alliages utilisés dans le moulage sous pression doivent être uniformes, avoir de bonnes propriétés de dilution lorsqu'ils sont fondus et la composition est stable pour ne pas adhérer au moule, et avoir une résistance plastique lorsqu'elle est chauffée à des températures élevées. Le cuivre, l'aluminium et l'acier inoxydable sont souvent préférés dans cette technologie de moulage.
Dans le moulage sous pression, les alliages d'aluminium sont les plus utilisés par rapport à tous les autres alliages. Aux États-Unis seulement, le moulage sous pression d'aluminium vaut jusqu'à 2,5 milliards de dollars par an. En particulier, le moulage sous pression de l'aluminium représente deux fois plus que toutes les autres méthodes combinées.
6. Coulée en moule permanent
Qu'est-ce que le moulage en moule permanent ?
La coulée en moule permanent, également connue sous le nom de coulée en moule métallique, est un processus de coulée dans lequel un moule est fait de métal comme le moulage sous pression. Il est utilisé pour produire une grande quantité de moulages en utilisant un seul moule réutilisable. Le moule peut être réutilisé plusieurs fois d'où la méthode dite de moulage permanent.
Le moulage en moule permanent convient aux pièces moulées plus grandes que le moulage sous pression, environ 10 kg, bien sûr, il peut être plus élevé, 20 kg voire 50 kg, et le coût sera plus élevé.
Le processus de coulée en moule permanent
Le processus de coulée en moule permanent comprend simplement ces étapes :
- Étape 1 :verser le métal en fusion dans le moule
- Étape 2 :permet le refroidissement et se solidifie
- Étape 3 :ouverture du moule et collecte de la pièce moulée ;
- Étape 4 : continuez ensuite ces processus ci-dessus pour faire autant de coulée que nécessaire.
Notamment, le moule dans ce procédé est fabriqué à partir d'un matériau métallique à haute température tel que la fonte pour pouvoir supporter le chauffage et le refroidissement continus tout en prenant un grand volume.
Caractéristiques de coulée en moule permanent
Avantage
- Résultat de coulée très précis et à tolérance serrée
- Belle finition de surface avec moins de défauts de moulage que le moulage au sable
- Le moulage est une résistance, une ténacité et une ductilité élevées
- La durabilité du moule est élevée.
- Grâce au gain de temps de fabrication des moules, une productivité élevée réduit les coûts de production.
Limites
- Il est difficile de mouler des objets trop complexes, avec de grands murs et du poids
- Les coûts de fabrication des moules sont élevés.
- Il est nécessaire de disposer d'un mécanisme pour pousser le moulage hors du moule, de sorte qu'ils forment parfois une entaille dans le moulage.
Applications de moulage en moule permanent
Ce moule de coulée permanente est le plus couramment utilisé pour couler l'aluminium, le magnésium, les alliages de cuivre et la fonte grise en raison de son faible point de fusion. Convient à la production de masse avec des pièces moulées simples et petites ou moyennes telles que des pistons, des billettes d'engrenages, des ustensiles de cuisine, des détails de machines-outils, des roues d'avion, des pièces de pompe, etc., qui ne pèsent pas plus de 25 kg. Pour les objets de forme interne complexe, il est recommandé d'utiliser un noyau de sable.
Résumé
Le contenu ci-dessus a répertorié et analysé les 6 différents types de processus de casting couramment utilisé dans les fabricants de fonderies de métaux. Dans l'ensemble, chacune de ces techniques de coulée conserve à la fois ses forces et ses limites. En fonction des exigences de coulée et de la demande du projet, les fonderies envisageront le processus de coulée qui convient à l'application.
En tant que l'une des principales sociétés de moulage et de vente en gros sur le marché mondial, VIC est la fonderie de moulage au sable avec trois principales techniques de moulage, à savoir le moulage au sable vert, le moulage à la résine de furane et le moulage à la mousse perdue. Avec ces trois différents types de moulage, nous sommes en mesure de fabriquer toutes les pièces de moulage, de la petite, moyenne, grande taille à la conception de forme simple et complexe. Contactez la fonderie VIC pour un projet de pièce de fonderie OEM par e-mail [email protected]
Processus de fabrication
- Coulage au sable :processus et caractéristiques | Secteurs | Métallurgie
- 10 différents types de modèles de moulage
- Qu'est-ce que la coulée de métal ? - Définition, types et processus
- 4 types courants de procédés de coulée de métal
- Comprendre le processus de moulage au sable
- Différents types de procédés de soudage à l'arc électrique
- Différents types d'équipements utilisés dans le processus de soudage à l'arc
- Différents types de marteaux utilisés dans divers domaines
- Différents types de procédés de formage de tôle