Qu'est-ce que le sable de moulage ? - Types et propriétés
Qu'est-ce que le sable de moulage ?
Le sable de moulage, également connu sous le nom de sable de fonderie, est du sable qui, lorsqu'il est humidifié et comprimé ou huilé ou chauffé, a tendance à bien se tasser et à conserver sa forme. Il est utilisé dans le processus de moulage au sable pour préparer la cavité du moule.
La principale matière première utilisée dans le moulage est le sable de moulage car il présente plusieurs caractéristiques majeures qui ne peuvent être obtenues avec d'autres matériaux. Le sable de moulage est défini comme des particules granulaires résultant de la décomposition des roches, en raison de l'action des forces naturelles, telles que le gel, le vent, la pluie, la chaleur et les courants d'eau. Les roches ont une composition complexe et le sable contient la plupart des éléments des roches.
Pour cette raison, le sable de moulage diffère considérablement d'une partie du monde à l'autre. Dans la nature, on le trouve au fond et sur les berges des rivières et des lacs. Le sable de moulage est classé en différentes catégories selon la nature de son origine.
Les principaux constituants des sables de moulage sont les suivants :
- Silice (SiO2) : 86 à 90 %,
- Alumine (Al2O3)—4 à 8 %,
- Oxyde de fer (Fe2O3) : 2 à 5 % avec de plus petites quantités d'oxydes de Ti,
- Mn
- Ca et certains composés alcalins.
Sable naturel/Sable vert
Il est également appelé sable vert et est collecté à partir de ressources naturelles. Il contient de l'eau comme seul liant. Il a l'avantage de maintenir la teneur en humidité pendant une longue période, d'avoir une large plage de travail de teneur en humidité, permettant de réparer et de finir facilement les moules.
Le sable vert est un agrégat de sable, d'argile bentonite, de charbon pulvérisé et d'eau. Son utilisation principale est la fabrication de moules pour la coulée des métaux. La plus grande partie de l'agrégat est toujours du sable, qui est souvent un mélange uniforme d'une forme de silice.
Il existe de nombreuses recettes pour la proportion d'argile, mais elles établissent toutes des équilibres différents entre la moulabilité, la finition de surface et la capacité du métal fondu chaud à dégazer. Le charbon généralement appelé charbon de mer, qui est présent dans une proportion inférieure à 5 %, brûle partiellement à la surface du métal en fusion, entraînant un dégazage de vapeurs organiques.
Le moulage au sable est l'une des premières formes de moulage pratiquée en raison de la simplicité des matériaux impliqués. Il reste toujours l'un des moyens les moins chers de couler des métaux en raison de cette même simplicité. D'autres méthodes de coulée, telles que celles utilisant la coquille, offrent une meilleure qualité de finition de surface mais ont un coût plus élevé.
Le sable vert (comme les autres sables de coulée) est généralement logé dans ce que les ouvriers de la fonderie appellent des « flacons », qui ne sont rien d'autre que des boîtes sans fond ni couvercle. La boîte est divisée en deux moitiés qui sont empilées lors de l'utilisation. Les moitiés sont appelées respectivement la chape et la fiole de traînée.
Tous les sables verts ne sont pas de couleur verte. Mais considéré comme «vert» dans le sens où il est utilisé à l'état humide (semblable au bois vert). Selon le site Web de la Cast Metals Federation, une autre méthode de coulée consiste à sécher à chaud le sable moulé avant de verser le métal en fusion. Ce processus de moulage au sable à sec donne un moule plus rigide mieux adapté aux pièces moulées plus lourdes.
Sable synthétique
Il s'agit de sable artificiel obtenu en mélangeant du sable relativement exempt d'argile, du liant (eau et bentonite) et d'autres matériaux selon les besoins. Il est préférable de mouler du sable car ses propriétés peuvent être facilement contrôlées en faisant varier la teneur du mélange.
La composition du sable synthétique vert pour les pièces moulées en acier est la suivante.
Nouveau sable de silice — 25 %, vieux sable — 70 %, bentonite — 1,5 %, dextrine — 0,25 % et humidité — 3 à 3,5 %.
La composition du sable synthétique sec pour les pièces moulées en acier est la suivante.
Sable de silice net - 15 %, vieux sable 84 %, bentonite - 0,5 % et humidité - 0,5 %.
En plus de cela, il existe certaines variétés de sables spéciaux tels que la Zirconite, l'Olivine etc. Ces sables spéciaux sont plus chers que la silice et ne sont donc utilisés que là où leur utilisation est justifiée.
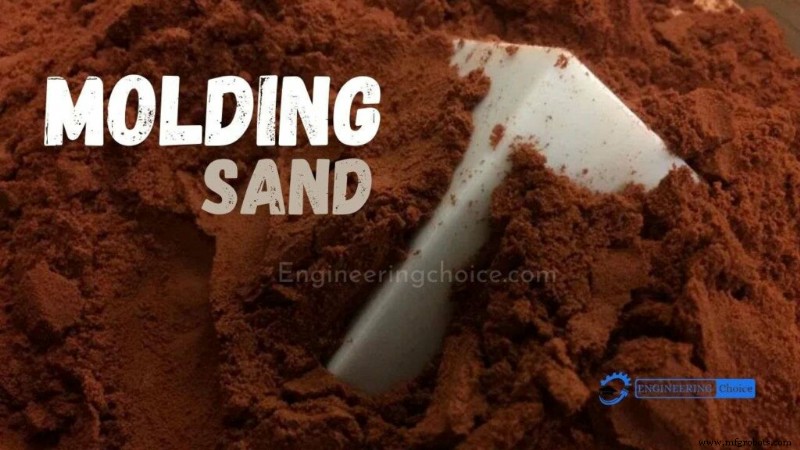
Types de sable de moulage
Les sables de moulage peuvent également être classés en différents types selon leur utilisation :sable de support, sable de noyau, sable sec, sable de parement, sable vert, sable limoneux, sable de séparation, sable de système.
1. Sable de support ou sable de plancher
Le sable de support ou le sable de sol est utilisé pour soutenir le sable de parement et est utilisé pour remplir tout le volume du moule de moulage. Le sable de support est parfois appelé sable noir en raison de l'ancien sable de moulage utilisé à plusieurs reprises qui est de couleur noire en raison de l'ajout de poussière de charbon et de la combustion au contact du métal en fusion.
2. Sable à noyau
Le sable de noyau est utilisé pour fabriquer des noyaux et il est parfois également connu sous le nom de sable bitumineux. Le sable de noyau est un sable de silice très riche mélangé à des liants d'huile tels que l'huile de noyau qui est composée d'huile de lin, de résine, d'huile minérale légère et d'autres matériaux de liaison. Le brai ou les farines et l'eau peuvent également être utilisés dans les gros noyaux pour des raisons d'économie.
3. Sable sec
Le sable vert qui a été séché ou cuit dans un four approprié après la fabrication du moule et des noyaux est appelé sable sec. Il possède plus de résistance, de rigidité et de stabilité thermique. Le sable sec est principalement utilisé pour les gros moulages. Les moules préparés dans ce sable sont appelés moules à sable sec.
4. Face au sable
Le sable de parement forme la face du moule. Il est à côté de la surface du modèle et il entre en contact avec le métal en fusion lorsque le moule est coulé. Le revêtement initial autour du motif et donc pour la surface du moule est donné par du sable de parement. Le sable de parement a un caractère réfractaire à haute résistance. Le sable de parement est composé de sable de silice et d'argile, sans l'utilisation de sable déjà utilisé.
Différentes formes de carbone sont utilisées dans le sable de parement pour empêcher le métal de brûler dans le sable. Un mélange de sable de revêtement pour le sable vert de fonte peut être composé de 25 % de charbon frais et spécialement préparé et de 5 % de charbon de mer.
Ils sont parfois mélangés avec 6 à 15 fois plus de sable de moulage fin pour faire des parements. La couche de sable de parement dans un moule varie généralement entre 20 et 30 mm. De 10 à 15 % de la quantité totale de sable de moulage est le sable de parement.
5. Sable vert
Le sable vert est également connu sous le nom de sable tempéré ou naturel qui est un mélange juste préparé de sable de silice avec 18 à 30% d'argile, ayant une teneur en humidité de 6 à 8%. L'argile et l'eau fournissent le lien pour le sable vert. Il est fin, doux, léger et poreux.
Le sable vert est humide lorsqu'il est pressé dans la main et il conserve la forme et l'impression de lui donner sous la pression. Les moules préparés par ce sable ne nécessitent pas de support et sont donc connus sous le nom de moules à sable vert.
Greensand est facilement disponible et il possède un faible coût. Le sable vert est couramment utilisé pour la production de pièces moulées ferreuses et non ferreuses.
6. Sable limoneux
Le sable limoneux est un mélange de sable et d'argile avec de l'eau pour former une fine pâte plastique. Le sable limoneux possède une argile élevée jusqu'à 30-50% et 18% d'eau. Les motifs ne sont pas utilisés pour le moulage du limon et la forme est donnée au moule par des balayages. Le sable limoneux est particulièrement utilisé pour le moulage de limon utilisé pour les grandes pièces moulées en fonte grise.
7. Sable de séparation
Le sable de séparation sans liant ni humidité est utilisé pour empêcher le sable vert de coller au motif et également pour permettre au sable de la surface de séparation de la chape et de la traînée de se séparer sans s'accrocher. Le sable de séparation est du sable de silice propre et sans argile qui a le même objectif que la poussière de séparation.
8. Système de sable
Dans les fonderies mécanisées où le moulage mécanique est utilisé. Le sable du système est utilisé pour remplir l'ensemble du moule de moulage. Dans les unités mécaniques de préparation et de manutention du sable, le sable de parement n'est pas utilisé. Le sable utilisé est nettoyé et réactivé par l'ajout d'eau et d'additifs spéciaux.
C'est ce qu'on appelle le sable système. Étant donné que l'ensemble du moule est constitué de ce système de sable, les propriétés telles que la résistance, la perméabilité et la réfractarité du sable de moulage doivent être supérieures à celles du sable de support.
Propriétés du sable de moulage
Les propriétés de base requises dans le sable de moulage et le sable de noyau sont l'adhésivité, la cohésion, l'écrasement, la fluidité, la résistance à sec, la résistance à l'état vert, la perméabilité, la réfractarité décrites ci-dessous.
1. Adhésivité
L'adhésivité est une propriété du sable de moulage pour obtenir le bâton ou adhérer à un matériau étranger tel que le sable de moulage collant avec la paroi intérieure de la boîte de moulage.
2. Cohésion
La cohésion est la propriété du sable de moulage grâce à laquelle les particules de grains de sable interagissent et s'attirent au sein du sable de moulage. Ainsi, la capacité de liaison du sable de moulage est améliorée pour augmenter les propriétés de résistance à l'état vert, à sec et à chaud du sable de moulage et de noyau.
3. Compressibilité
Une fois que le métal en fusion dans le moule s'est solidifié, le moule en sable doit être pliable afin que la contraction libre du métal se produise et cela éviterait naturellement la déchirure ou la fissuration du métal qui se contracte. En l'absence de propriété de collapsibilité, la contraction du métal est entravée par le moule et entraîne ainsi des déchirures et des fissures dans la coulée. Cette propriété est fortement requise dans les noyaux.
4. Résistance à sec
Dès que le métal fondu est versé dans le moule, l'humidité de la couche de sable adjacente au métal chaud s'évapore et cette couche de sable sec doit avoir une résistance suffisante à sa forme afin d'éviter l'érosion de la paroi du moule lors de l'écoulement de métal en fusion. La résistance à sec empêche également l'élargissement de la cavité du moule causé par la pression métallostatique du métal liquide.
5. Fluidité ou plasticité
La fluidité ou la plasticité est la capacité du sable à se compacter et à se comporter comme un fluide. Il s'écoulera uniformément sur toutes les parties du motif lorsqu'il sera percuté et répartira la pression de pilonnage uniformément tout autour dans toutes les directions.
Généralement, les particules de sable résistent au déplacement autour des coins ou des projections. En général, la fluidité augmente avec une diminution de la résistance à vert et vice versa. La fluidité augmente avec une diminution de la taille des grains de sable. La fluidité varie également avec l'humidité et la teneur en argile du sable.
6. Force verte
Le sable vert, après que l'eau y a été mélangée, doit avoir une résistance et une ténacité suffisantes pour permettre la fabrication et la manipulation du moule. Pour cela, les grains de sable doivent être adhésifs, c'est-à-dire qu'ils doivent pouvoir se fixer sur un autre corps et. par conséquent, et les grains de sable ayant une adhésivité élevée s'accrocheront aux côtés de la boîte de moulage.
De plus, les grains de sable doivent avoir la propriété connue sous le nom de cohésion, c'est-à-dire la capacité des grains de sable à se coller les uns aux autres. Grâce à cette propriété, le modèle peut être retiré du moule sans casser le moule, et l'érosion des surfaces des parois du moule ne se produit pas non plus pendant l'écoulement du métal en fusion.
La résistance à l'état vert dépend également de la forme et de la taille des grains, de la quantité et du type d'argile et de la teneur en humidité.
7. Perméabilité
La perméabilité est également appelée porosité du sable de moulage afin de permettre l'évacuation de l'air, des gaz ou de l'humidité présents ou générés dans le moule lorsque le métal fondu y est versé. Tous ces gaz générés lors du processus de coulée et de solidification doivent s'échapper sinon la coulée devient défectueuse.
La perméabilité est fonction de la taille des grains, de la forme des grains et de la teneur en humidité et en argile du sable de moulage. L'ampleur du pilonnage du sable affecte directement la perméabilité du moule. La perméabilité du moule peut être encore augmentée en ventilant à l'aide de tiges de ventilation.
8. Réfractaire
Le caractère réfractaire est défini comme la capacité du sable de moulage à résister à des températures élevées sans se décomposer ni fondre, facilitant ainsi l'obtention d'un moulage sain. C'est une caractéristique très importante des sables de moulage. Le caractère réfractaire ne peut être augmenté que dans une mesure limitée.
Le sable de moulage avec une mauvaise réfractarité peut brûler sur la surface de coulée et aucune surface de coulée lisse ne peut être obtenue. Le degré de réfractarité dépend du SiO2, c'est-à-dire de la teneur en quartz, ainsi que de la forme et de la taille des grains de la particule.
Plus la teneur en SiO2 est élevée et plus la composition volumétrique des grains est rugueuse, plus la réfractarité du sable de moulage et du sable de noyau est élevée. La réfractaire est mesurée par le point de frittage du sable plutôt que par son point de fusion.
9. Propriétés diverses du sable de moulage
En plus des exigences ci-dessus, le sable de moulage ne doit pas coller au moulage et ne doit pas réagir chimiquement avec le métal. Le sable de moulage doit être économiquement bon marché et facilement disponible dans la nature. Il doit être réutilisable pour des raisons économiques. Ses coefficients de dilatation thermique doivent être suffisamment bas.
Processus de fabrication
- Qu'est-ce que le sable de moulage ? - Types et propriétés
- Types d'aluminium :classifications, propriétés et applications
- Qu'est-ce que le polissage, les caractéristiques et les types de polissage
- Qu'est-ce que la tolérance d'ingénierie, les types et l'ajustement ?
- Qu'est-ce que l'usinage par faisceau laser ? - Types et fonctionnement
- Qu'est-ce que la soudure ? - Types et comment souder
- Qu'est-ce que le prototypage rapide ? - Types et fonctionnement
- Qu'est-ce que le sable de moulage?
- Types de métaux et leurs propriétés