Prolonger la durée de vie des actifs d'automatisation
S'ils sont laissés à eux-mêmes, les actifs de manutention se dégraderont lentement et finiront par tomber en panne, souvent au moment le plus inopportun. Mais avec un peu de planification, vous pouvez non seulement prolonger leur durée de vie utile, mais aussi optimiser les performances.
Les actifs d'automatisation évoluent généralement en quatre étapes distinctes :conception, exécution, support et optimisation. Dans de trop nombreux cas, cependant, la phase d'optimisation est aléatoire ou totalement ignorée. Les performances atteignent un sommet puis commencent à décliner. Ce processus se produit pour de nombreuses raisons :les personnes qui ont mis en œuvre les systèmes peuvent être passées à autre chose et leurs successeurs ne se sentent pas investis dans le système; il se peut qu'il n'y ait pas de mécanismes en place pour surveiller les performances ; ou les affaires peuvent être si bonnes qu'il y a peu d'incitation à chercher à s'améliorer.
Quelle que soit la raison de ne pas optimiser, l'économie mondiale d'aujourd'hui exige que les entrepôts et les centres de distribution tirent le maximum de valeur de leurs investissements en automatisation. Cela devrait commencer par un audit approfondi à la fois des risques de ne rien faire et du potentiel de prolongation de la durée de vie utile des actifs d'automatisation.
Évaluer le risque
Un audit commence par une analyse des actifs actuels en vue de prolonger leur durée de vie utile. Créez un profil de chaque actif clé de votre installation, y compris les logiciels, les commandes, les appareils électriques périphériques et l'équipement mécanique. Si vous n'avez pas d'inventaire, les fournisseurs de chaque actif devraient être en mesure de le fournir. À partir de là, vous pouvez créer un inventaire principal, catégoriser l'obsolescence potentielle de chaque pièce et son importance stratégique, puis créer un plan pour atténuer ces risques. Chaque couche doit être classée en fonction de son importance stratégique pour votre entreprise, comme suit :
Risque critique : Des actifs qui peuvent affecter l'ensemble de votre système. Celles-ci nécessiteraient un plan de redressement pour atténuer les problèmes à court terme et, à plus long terme, une stratégie budgétaire pour couvrir le remplacement total, si nécessaire, avec des coûts de remplacement échelonnés sur plusieurs cycles budgétaires.
Risque élevé : Composants susceptibles d'entraîner une défaillance partielle du système. Ceux-ci peuvent également entraîner des temps d'arrêt prolongés et nécessiteraient également un plan de reprise et une planification budgétaire à plus long terme, peut-être en équilibrant les coûts entre les dépenses d'investissement et les dépenses de MRO.
Risque moyen ou faible : Cela implique généralement des composants dont la défaillance n'entraînerait pas une défaillance partielle ou totale du système. Les temps d'arrêt sont minimes et les coûts de remplacement peuvent généralement être gérés à partir des budgets MRO. Une bonne stratégie de pièces de rechange visant à disposer de composants de remplacement adéquats peut limiter les risques.
Avec une compréhension de vos risques et une bonne planification, vous pouvez prolonger considérablement la durée de vie de votre système, minimiser les temps d'arrêt imprévus et exploiter les appareils mécaniques, de contrôle, logiciels et électriques à leur plein potentiel.
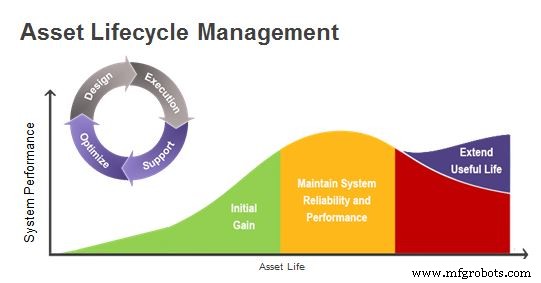
Prolonger la durée de vie du système mécanique
L'utilisation de convoyeurs, de trieurs, de systèmes automatisés de stockage et de récupération et d'autres biens d'équipement représente très probablement le risque le plus élevé et les dépenses en capital les plus élevées dans un entrepôt ou une installation de distribution. Tous les systèmes sont sujets à l'usure et à la dégradation des performances au fil du temps. Le temps de fonctionnement effectif peut être réduit, ou d'autres problèmes, tels que le frottement d'un composant usé contribuant au bruit qui pousse le système au-delà des niveaux acceptables de l'OSHA, peuvent nécessiter une attention particulière. Plus vous pouvez en faire pour prolonger la durée de vie utile de vos systèmes, plus l'impact sur la rentabilité est important.
Bien que le remplacement total soit généralement une dépense en capital importante, la durée de vie du système peut souvent être prolongée en apportant des améliorations au niveau des composants. Un trieur de chaussures en fin de vie, par exemple, peut souvent être reconstruit. Le remplacement d'un composant usé peut permettre au trieur de fonctionner correctement et de maintenir sa disponibilité. Ou, s'il y a un problème de bruit, un produit plus récent conçu pour un fonctionnement plus silencieux pourrait être la solution. Et si la reconstruction ou le remplacement de composants est une option, cela peut souvent être fait le week-end avant la haute saison.
Un autre moyen précieux de gérer le cycle de vie de votre équipement mécanique est une stratégie de pièces de rechange qui correspond à la criticité et au cycle de vie projeté des composants clés. Bien qu'une stratégie ait été développée lors de l'achat du système, les stratégies de pièces de rechange doivent être revues régulièrement à mesure que le système vieillit.
Gestion des appareils électriques
Le fonctionnement optimal de l'entrepôt dépend également de la fiabilité de nombreux appareils électriques, tels que les scanners, les modules d'E/S, les actionneurs et les servomoteurs. Ceux-ci ont des degrés de risque variables, il est donc important d'analyser le risque d'utilisation de chaque appareil à mesure qu'il vieillit. Alors que certains fournisseurs désignent la durée de vie prévue de chaque appareil, d'autres ne le font pas, vous laissant faire votre meilleure estimation.
Une analyse des risques efficace peut offrir des options aux entreprises. Par exemple, dans une analyse des risques effectuée sur les servocommandes, les planificateurs de l'automatisation ont identifié huit servomoteurs Baldor comme se dirigeant vers l'obsolescence, en fonction de leur âge. Une défaillance de l'un d'entre eux aurait pu entraîner des semaines d'indisponibilité avant qu'un remplaçant ne soit trouvé. Confrontée à des dépenses de remplacement pouvant atteindre 80 000 $, l'entreprise s'est vu offrir d'autres options que le remplacement total immédiat.
Si certaines pièces de rechange étaient disponibles, l'entreprise pourrait les acheter et les remplacer progressivement. Il pourrait, par exemple, remplacer immédiatement les quatre servos les plus anciens et conserver ce qu'ils avaient supprimé pour les utiliser comme sauvegardes. Cela prolongerait la durée de vie tout en offrant plus de flexibilité pour répartir les coûts entre les investissements et le MRO.
Modernisation des contrôleurs
La plupart des systèmes de manutention dépendent du contrôle PLC. Parce que leur fonctionnement est simple, les automates ont tendance à durer et la plupart des fournisseurs d'automates annoncent la fin de vie prévue bien à l'avance. Rockwell/Allen Bradley, par exemple, ne prend plus en charge l'automate TI 45, mais, comme annoncé, continuera à prendre en charge son dernier automate ControlLogix.
Plus votre automate est proche de la fin de sa vie, plus le risque de panne est grand et, s'il tombe en panne, il y aura un temps d'arrêt. En fonction des risques, la mise à niveau vers un API plus moderne garantit non seulement le fonctionnement, mais peut également être un moyen d'exploiter davantage la valeur d'autres actifs.
En plus d'être plus robustes et fiables, les nouveaux automates programmables peuvent disposer d'une bande passante suffisante pour prendre en charge des outils analytiques qui peuvent aider à identifier les tendances, ce qui peut prolonger la durée de vie des systèmes qu'ils contrôlent. De plus, la capacité Ethernet peut favoriser l'intégration du système de contrôle d'entrepôt (WCS) avec d'autres systèmes d'automatisation.
Certaines petites exploitations utilisent des PC pour contrôler leurs usines. Les PC peuvent devenir obsolètes en moins de deux ans et il est généralement plus économique de les remplacer que de les mettre à niveau.
Gestion du logiciel de contrôle d'entrepôt
L'obsolescence de la plate-forme logicielle supportant le WCS est une réalité incontournable. Lorsque le WCS tombe en panne, l'entrepôt est en panne pendant plusieurs jours, voire plusieurs semaines, de configuration et de test.
De nombreux WCS fonctionnent toujours sous Windows 2003, que Microsoft ne prend plus en charge. Votre système continuera à fonctionner sous Windows 2003, mais vous serez seul en cas de problèmes techniques et il peut être risqué de connecter des applications héritées ou tierces à votre WCS. Si vous utilisez Windows 2007 et 2008, vous serez dans la même situation en 2020, lorsque Microsoft débranchera ces systèmes. La bonne nouvelle est que Microsoft, comme la plupart des éditeurs de logiciels, annonce la durée de prise en charge de leurs produits.
Mais cela peut aussi être une opportunité. La mise à niveau vers la dernière version du logiciel pris en charge peut être une dépense abordable qui maximise les performances et réduit le risque de maintenance d'autres actifs. Avec la dernière version, par exemple, les solutions de clients légers deviennent possibles, permettant la consolidation de l'architecture informatique dans un serveur virtuel plutôt que physique. Pour un investissement de 250 000 $ dans des contrôles virtualisés, vous auriez non seulement un système d'exploitation qui serait pris en charge pendant des années, mais vous gagneriez également des avantages en matière de maintenance logicielle, de reprise après sinistre et d'autres domaines, dont le moindre n'est pas l'élimination du besoin de matériel physique. serveurs.
Amélioration durable
Bien que nous nous soyons concentrés sur la phase d'optimisation souvent négligée du cycle de vie de l'automatisation, toutes les phases opérationnelles sont essentielles à l'amélioration continue. L'attention portée à l'extension du cycle de vie lors de la phase de conception peut se manifester dans une conception avec des technologies ouvertes ou des objets d'ingénierie réutilisables, de sorte que les systèmes puissent intégrer les meilleures solutions sans avoir à abandonner la totalité de l'investissement.
Lors de la phase d'exécution, la gestion des actifs peut être améliorée par des systèmes d'exécution d'entrepôt, qui coordonnent les opérations afin que les ressources humaines et l'équipement soient exploités et utilisés efficacement. Et c'est la phase de support où la gestion des pièces de rechange, la surveillance de l'état, la maintenance préventive et d'autres stratégies sont mises en œuvre pour soutenir toutes les mesures d'optimisation qui doivent être prises.
Wynright Corp. (Elk Grove, Illinois), une filiale en propriété exclusive de Daifuku North America, est un fournisseur de systèmes de manutention intelligents.
Système de contrôle d'automatisation
- Automatisation :mise à jour du logiciel du système de vision
- Les effets positifs de l'automatisation agricole
- Un système d'automatisation adaptable en action
- Le système d'automatisation favorise l'accessibilité et la maniabilité
- STAEDTLER :la valeur de l'automatisation dans la fabrication
- Comprendre la valeur de l'automatisation dans la fabrication
- Conseils pratiques pour prolonger la durée de vie de vos poinçons
- Vous connaissez le mieux votre système d'automatisation industrielle, voici ce que nous apportons à la table
- L'élément humain de l'automatisation