Combinaison de plastiques et de composites pour des pièces de classe A sans outils
La production de pièces composites avec une finition de classe A n'est pas le Saint Graal - il existe de nombreuses entreprises qui le font régulièrement. Cependant, en utilisant l'infusion de résine sans outillage coûteux ou gelcoats et à raison d'une partie par heure ? Eh bien, c'est quelque chose d'unique.
Des plastiques aux composites
Plastics Unlimited a été lancé il y a 25 ans par Terry et Nancy Kieffer, explique leur fils Dakota Kieffer, directeur des ventes et du marketing de l'entreprise. « Ils étaient agriculteurs dans l'Iowa et avaient commencé à chercher une nouvelle industrie en pleine croissance », explique-t-il. « Ils pensaient que les plastiques seraient meilleurs que le soudage ou le travail du bois et ils ne voulaient pas rivaliser avec leurs voisins. Ils se sont penchés sur le moulage par injection, le rotomoulage et le recyclage des plastiques, mais sont ensuite tombés sur le thermoformage et l'ont vraiment compris. (Le thermoformage utilise la chaleur et le vide/la pression pour façonner les feuilles thermoplastiques en pièces façonnées.)
Ensuite, les parents de Kieffer sont entrés en contact avec une entreprise fabriquant des pièces en plastique renforcé de fibre de verre (PRF). « Ils ont vu à quel point le FRP était solide, mais aussi qu'il nécessitait un long processus en plusieurs étapes, environ quatre heures par pièce. Ainsi, seules deux pièces étaient produites par jour », poursuit-il. « Par rapport à notre production de plastiques, ils ont estimé que c'était trop lent. Nous tournions des pièces toutes les 2 à 6 minutes — peut-être même produisions 5 à 6 pièces à la fois — donc des milliers de pièces par jour. Pour combler le fossé, le père de Kieffer a eu l'idée d'utiliser une coque en plastique thermoformé comme outil .
Le résultat est un processus de fabrication de pièces composites sans outil, que Plastics Unlimited appelle Tool-less Engineered Composite (TEC). « Il enlève le gelcoat et étapes de libération de l'outil », explique Kieffer. "De plus, lorsque vous thermoformez, vous pouvez inspecter la surface de classe A et vous assurer qu'elle est parfaite." En d'autres termes, la surface de classe A n'est pas cachée sous un stratifié composite. « Un seul outil de thermoformage était nécessaire, et le processus avait toujours du sens pour nos clients de pièces en plastique. »
Procédé composite breveté
Kieffer note qu'un composite combine deux matériaux pour faire un meilleur matériau que l'un ou l'autre constituant seul. « Nous combinons deux types de matériaux différents et deux processus différents pour fabriquer un meilleur produit. » Notamment, un produit qui comprend du plastique, de la résine et de la fibre de verre pour offrir un mélange unique d'avantages. « Les plastiques résistent bien mieux aux chocs que les gelcoats », explique-t-il. « Il est également possible d'imprimer n'importe quelle texture ou dessin sur le plastique, par exemple un motif de camouflage. Les plastiques offrent également beaucoup de profondeur d'image sans polissage par la suite, ce qui supprime les opérations de finition secondaires. »
Pendant ce temps, par rapport à la pulvérisation de fibres hachées dans un processus de moulage ouvert, cette technologie brevetée permet une teneur en fibres plus élevée, une qualité supérieure et sans/peu de composés organiques volatils (COV). Il souligne que la pulvérisation de fibres hachées sur les plastiques des baignoires et des spas n'est pas brevetée. «Nous utilisons toujours l'infusion sous vide pour faire de la partie FRP du produit», explique Kieffer, ajoutant «nos pièces ont une finition lisse, nous sommes donc plus un RTM léger avec des plaques de calage. Nous allons toujours au niveau supérieur. Les clients viennent nous voir avec un problème et nous essayons de trouver une solution adaptée à leurs besoins. Nous sommes très innovants et nous brevetons nos nouveaux développements. »
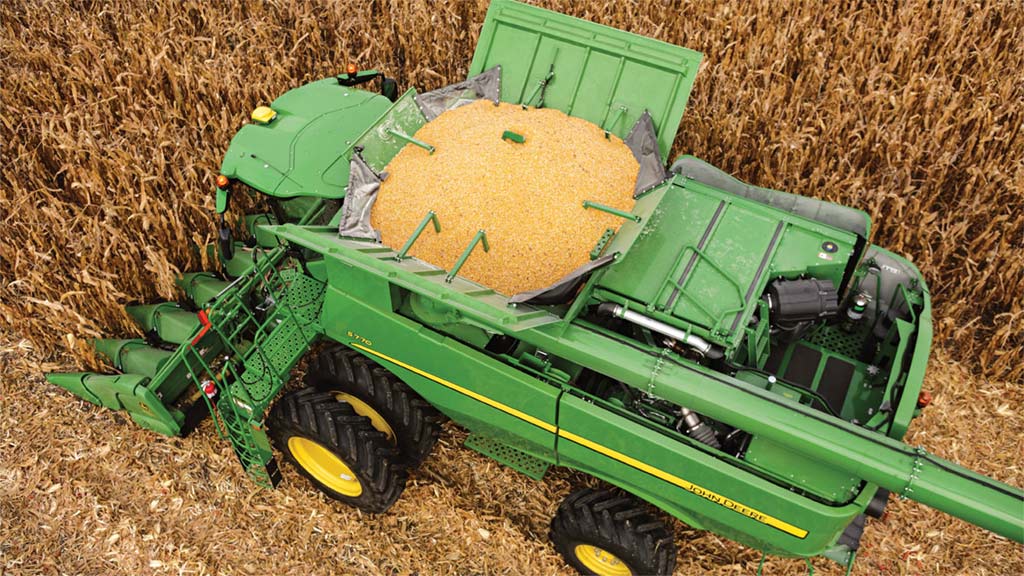
Exemples de pièces
L'une des pièces produites par Plastics Unlimited à l'aide de ce procédé est une extension de trémie à grains pour les moissonneuses-batteuses John Deere fabriquées par Deere &Company (Moline, Illinois, États-Unis). « C'est la partie supérieure de la moissonneuse-batteuse, qui est ouverte, là où se trouve le grain », explique Kieffer. « Comparé au réservoir en acier d'origine, le nôtre est plus durable. Nous le fabriquons avec une finition lisse à l'intérieur et du vert John Deere à l'extérieur avec des inserts noirs dans les coins. Il s'agit de la plus grande extension de trémie à grains disponible et peut se replier à plat. C'est un produit plus élaboré que nos concurrents, avec de la mousse et des nervures ajoutées pour augmenter la rigidité. Certains renforts en acier sont également nécessaires, qui sont en fait moulés, dit Kieffer, « pas liés secondairement ».
Cette combinaison de matériaux et de processus confère une grande résistance à la pièce finie. « Nous avons des vidéos de chutes de blocs de béton sur ces parties », explique Kieffer. En moulant des éléments en acier, il dit que la résistance à l'arrachement peut être 4 à 5 fois supérieure à celle obtenue avec un collage secondaire à l'aide d'adhésifs au méthacrylate de méthyle standard de l'industrie.
Plastics Unlimited peut fabriquer jusqu'à 2 500 de ces pièces par mois, certains des panneaux mesurant 5 pieds sur 7 pieds. "Cela nécessiterait un outillage coûteux, s'il n'était pas fabriqué à l'aide de notre méthode", explique Kieffer, notant que le TEC peut être utilisé pour des pièces assez volumineuses - jusqu'à 8 pieds sur 11 pieds. « Nos pièces peuvent avoir plus de forme et de géométrie que l'acier. C'est important pour nos clients car cela leur permet de se différencier par le style. Notre résistance aux UV est également meilleure que la plupart des gelcoats. »
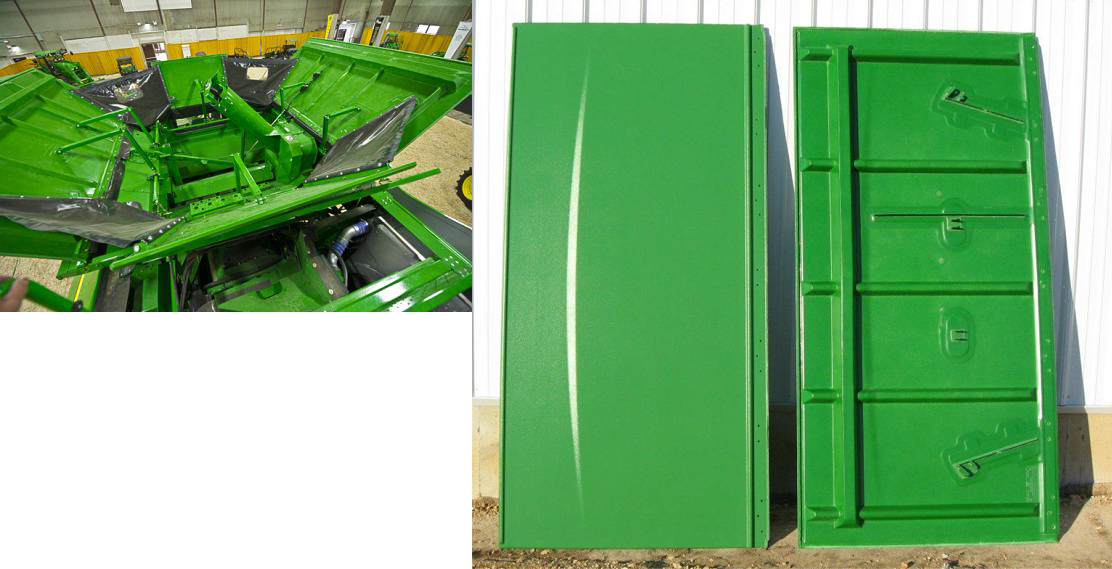
Plastics Unlimited fournit des pièces pour diverses entreprises, notamment les hayons télescopiques Harley-Davidson et Gehl. «Nous fabriquons également des pièces douces au toucher qui ressemblent à du cuir», explique Kieffer. L'entreprise a également fabriqué des composants de camions pour Navistar et des pièces de véhicules récréatifs (VR) pour Winnebago. "Nous privilégions la production en volume, de 100 000 pièces par an à quelques centaines."
Kieffer reconnaît que l'injection de fibres longues (LFI) et le moulage par injection de résine (RIM) sont des processus compétitifs, « mais les pièces ne sont pas aussi structurelles que ce que nous faisons. Par exemple, une trémie de moissonneuse-batteuse contient 400 boisseaux, ce qui exerce 10 tonnes de force. Les pièces RIM, qui ne sont pas fortement renforcées, ne peuvent tout simplement pas répondre à ce type d'exigence de charge et l'outillage RIM est très coûteux. »
Développement continu
« Nous effectuons beaucoup de travaux de R&D avec nos clients », déclare Kieffer. « Nous explorons différentes résines, mousses, stratifiés, couches de renfort et finitions, puis leur montrons des prototypes afin qu'ils puissent faire des tests très rapidement. Nous essaierons de rendre la pièce plus manufacturable, en cherchant comment réduire les coûts et améliorer les performances, tout en répondant aux diverses exigences en service, telles que les températures extrêmement chaudes et froides et l'impact. »
Plastics Unlimited compte 100 000 pieds carrés d'espace de production et 75 employés, dont une équipe de trois ingénieurs. Sa machine CNC Thermwood à 5 axes permet la production d'outillage en interne ainsi qu'un prototypage rapide, ce dernier étant important pour les clients qui cherchent à raccourcir les délais de développement.
«Nous travaillons également avec des entreprises de transport en commun et de l'aérospatiale», poursuit-il. « Beaucoup d'intérieurs de métro sont actuellement en FRP avec un gelcoat et une structure en aluminium derrière. Ils ont besoin de légèreté mais aussi d'une finition de surface cosmétique. Nous examinons un large éventail d'applications, notamment médicales, électriques et de construction. »
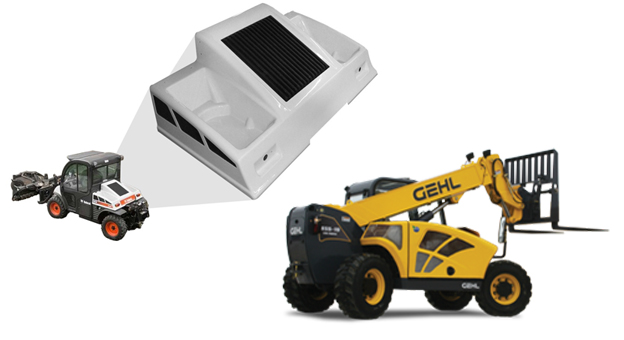
L'entreprise étudie également le thermoformage de plastiques renforcés de fibres de carbone (CFRP). « Nous avons formé des matériaux Tepex et Polystrand et travaillons sur divers développements avec un client médical », explique Kieffer. « Nous pouvons utiliser des matériaux plastiques haut de gamme comme le Kydex et les renforcer avec du CF/époxy pour l'aérospatiale, ou des matériaux comme le polyuréthane, le polycarbonate et l'ABS, qui offrent une belle finition extérieure et sont rentables. Derrière ces derniers plastiques, nous pouvons utiliser des stratifiés polyester, vinylester ou époxy renforcés de fibres de verre. »
Plastics Unlimited opère à l'intersection des plastiques, des métaux et des composites, explique Kieffer. « Nos pièces sont généralement 30 à 40 % plus légères que l'acier. Mais nous constatons que le marché a encore besoin d'un peu d'éducation sur ce que sont les composites et ce qu'ils peuvent faire. Néanmoins, l'entreprise voit beaucoup de potentiel de croissance future. « Tous les matériaux ne fonctionnent pas ensemble, et surtout toutes les résines ne fonctionnent pas avec tous les plastiques », note-t-il. « Nous avons fait tellement de tests et de développements au fil des ans que nous comprenons très bien le paysage et les possibilités. Nous avons une expertise unique et offrons une gamme unique de solutions possibles. »
Résine
- Kubernetes dans Azure :outils et astuces pour réussir
- Modèles et outils de programmation pour le cloud computing
- TPE « Smooth-Touch » pour les nouvelles exigences de conception d'emballages et de pièces
- Pièces de bras de robot pour l'automatisation Pick and Place
- Personnalisation des capteurs à ultrasons pour l'optimisation et le contrôle des processus composites
- Partenaire Victrex et Bond pour l'impression 3D de pièces PAEK
- 20 outils et équipements de soudage de base pour les débutants
- Processus de finition des pièces et des composants
- ENTRETIEN QUOTIDIEN ET PÉRIODIQUE DES CONVOYEURS ET DES PIÈCES