Combiner AFP et impression 3D pour une production de pièces flexible
Fondé en 1986, Electroimpact (Mukilteo, Wash., États-Unis) est un fournisseur mondial d'outillage et d'automatisation de la production qui prétend être le plus grand intégrateur au monde de lignes d'assemblage d'avions. Dans le domaine des composites, l'entreprise est connue pour sa technologie de pointe dans les systèmes automatisés de pose de ruban (ATL) et de placement de fibres (AFP) à grande vitesse. Electroimpact souligne qu'il est axé sur l'ingénieur — 400 de ses 600 employés ont des diplômes d'ingénieur — avec des développements conçus et réalisés par la même équipe d'ingénieurs, du concept à la conception, la fabrication, l'installation et le rachat par le client.
En juillet 2020, CW a rendu compte du nouveau système de fabrication additive robotique composite évolutive (SCRAM) de la société. Ici, nous partageons notre entretien avec une partie de l'équipe d'ingénierie de SCRAM :le chef de projet Cody Brown, l'ingénieur en développement de procédés et contrôles Ryan Bischoff et l'ingénieur en mécanique en chef Reese Allen. Leur explication de l'origine, de la mise en œuvre et de l'avenir de cette fabrication additive continue de fibres donne un aperçu de ce à quoi pourrait ressembler la prochaine génération de production de composites.
Visant le FDM à grande échelle
Marron :« Cela fait quatre ans que nous travaillons dessus, mais nous voulions attendre de pouvoir montrer que cela produirait de vraies pièces de qualité aérospatiale. Notre objectif initial était de produire une imprimante 3D à grande échelle pour la fabrication de filaments fondus (FFF) capable de créer des pièces complexes à l'aide de fibres continues. Nous n'avions pas pour objectif de développer un procédé de type AFP, mais alors que nous essayions d'augmenter le volume de fibres et d'obtenir une résistance physique plus élevée dans les pièces imprimées, nous nous sommes heurtés à un mur avec FFF. Ce n'est tout simplement pas un processus approprié pour la consolidation in situ avec une teneur élevée en fibres et de faibles vides. Ainsi, nous nous sommes retrouvés avec un processus qui combine l'AFP composite thermoplastique avec FFF en utilisant un filament chargé de fibres non renforcé et/ou haché. »
Allen :« L'AFP est en fait un procédé de fabrication additive. Dans SCRAM, cependant, nous ne l'utilisons pas de manière conventionnelle avec un outil fixe et dur, mais à la place, nous imprimons un outil que nous pouvons laver par la suite pour créer des géométries très complexes qui sont vraiment structurelles. »
Marron :« Nous pouvons mettre cet outil soluble dans des endroits qui ne sont pas verrouillés afin que vous puissiez créer des cavités internes. L'objectif n'est pas de rivaliser avec nos grands systèmes AFP, mais plutôt de fabriquer un système très adroit aussi proche que possible d'une imprimante 3D. Faire cela avec de vrais six degrés de liberté et de précision est en fait très compliqué. La cellule résultante élimine les attaches et les adhésifs, en fabriquant des pièces intégrées et complexes qui peuvent être itérées très rapidement. »
Haute performance pour l'aérospatiale
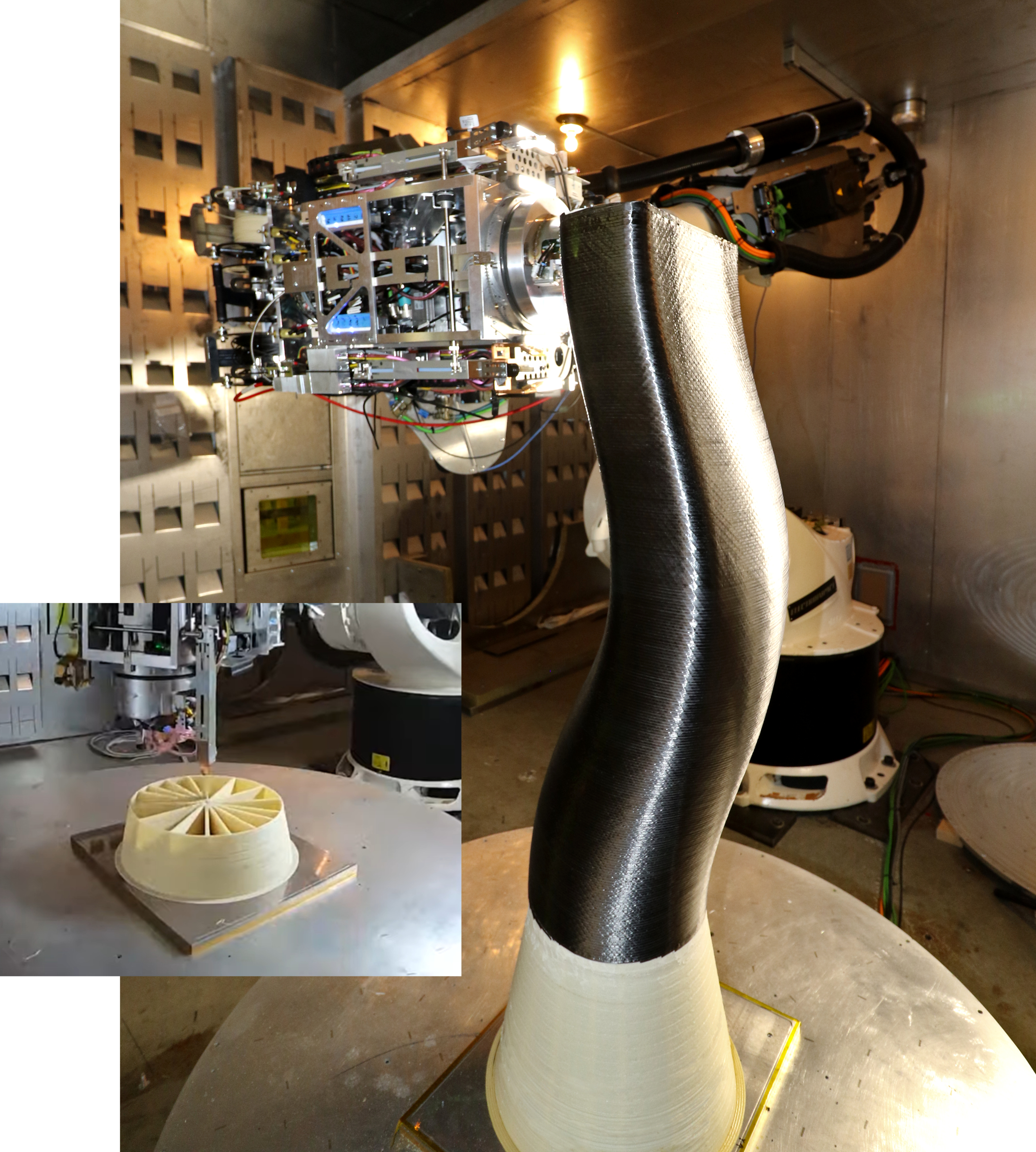
Marron :« Les premières applications que nous ciblons dans l'aérospatiale et la défense mandatées, nous commençons par le PEEK [polyétheréthercétone]. Nous avons ensuite travaillé avec du PEKK [polyéthercétonecétone] et du PAEK [polyaryléthercétone] à bas point de fusion avec un succès spectaculaire. »
Bischoff :« Le coefficient de dilatation thermique [CTE] est votre plus grand ennemi. C'est la raison pour laquelle l'utilisation du PEEK est si difficile :il adore cristalliser et rétrécir. Bien que le CTE des résines PEKK et autres PAEK ne soit pas nul, leur structure cristalline est beaucoup plus contrôlable et donc plus facile à travailler. Les PAEK alternatifs offrent également une bien meilleure aptitude au traitement et une vitesse de superposition plus élevée. »
Allen :« Les gradients thermiques doivent être évités en raison du problème de CTE, vous essayez donc de garder le processus et la pièce aussi isothermes que possible. Sinon, vous vous retrouvez avec un gauchissement. L'utilisation de la chambre chauffée est indispensable, même si vous ne la maintenez pas à une température élevée, simplement pour vous assurer qu'il n'y a pas de courants d'air et qu'une partie de l'impression n'est pas à une température différente du reste. »
Cellule à laser
Marron : « Beaucoup de choses qui permettent ce système n'existaient pas lorsque nous avons commencé, y compris la bande PAEK et le laser compact et haute puissance que nous utilisons, ainsi que le véritable logiciel de FAO de fabrication additive à six axes. »
« La tête SCRAM utilise deux buses d'impression 3D de chaque côté du système AFP [opening image]. L'un est utilisé pour imprimer l'outillage soluble et l'autre imprime du filament en fibres non renforcées ou hachées. Vous pouvez voir que l'un est équipé d'un échafaudage. Celui-ci contient un ensemble de miroirs pour rediriger la lumière laser autour de la pointe de la buse et chauffer le substrat. Cela nous permet d'obtenir une force de liaison intercalaire exceptionnelle par rapport au FFF traditionnel. Les lumières sur le système doivent éclairer la partie pour les caméras [Fig. 2]. Nous les utilisons partout pour que l'opérateur puisse voir en toute sécurité ce qui se passe sans danger du laser. »
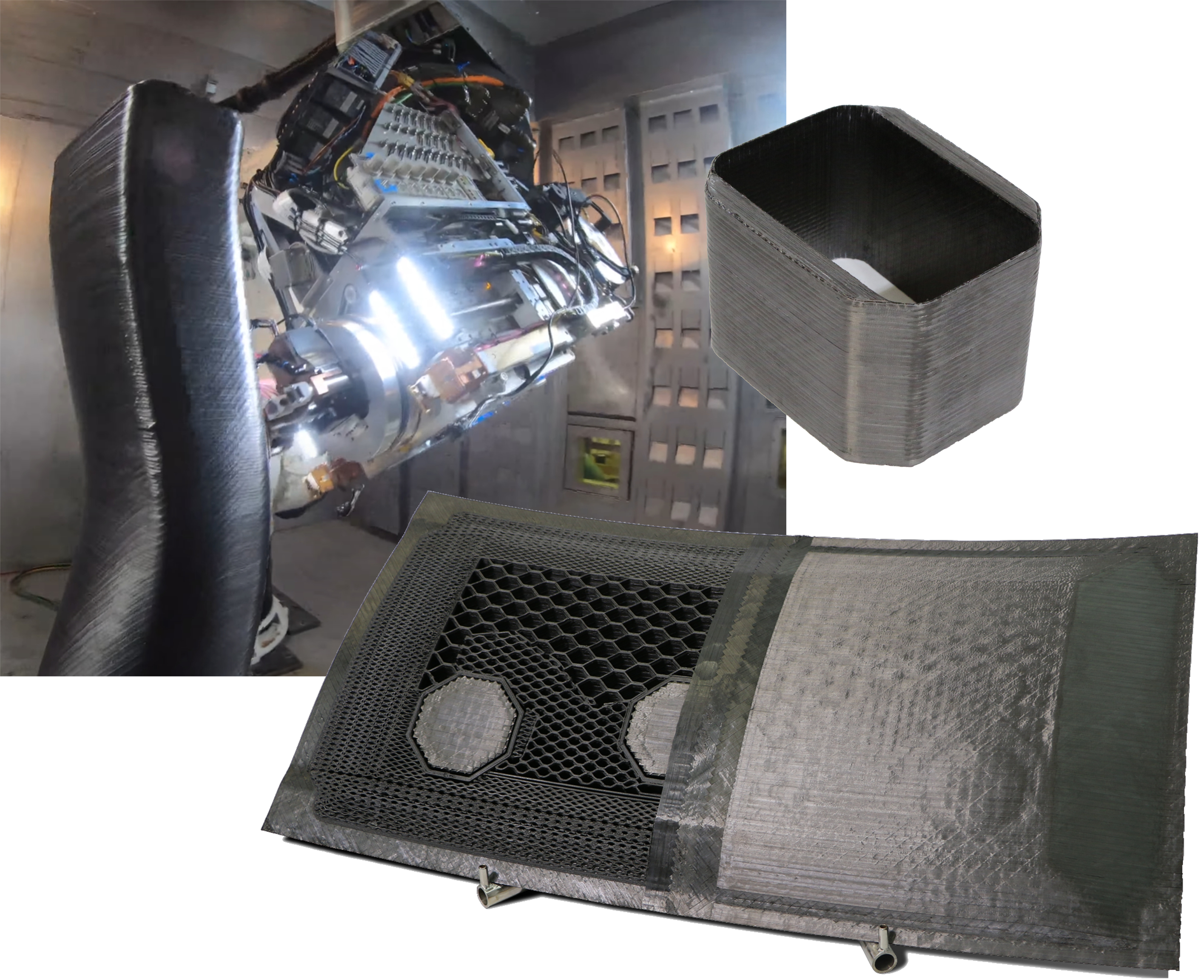
Formats et porosité des matériaux
Marron :« Nous avons utilisé de nombreux matériaux différents, la plupart fabriqués sur mesure selon nos spécifications de fibre, de résine, de volume de fibre et de dimensions. Nous avons récemment expérimenté d'autres câbles refendus disponibles dans le commerce. Les filaments de fibres coupées FFF sont également fabriqués selon nos spécifications en utilisant la même résine et la même fibre que nous sélectionnons pour les rubans de fibres continues. Nous avons utilisé des filaments de 1, 3,5 et 6,35 millimètres de diamètre. Nous pouvons aller plus loin, mais nous n'en avons pas encore eu besoin. »
« Nous atteignons 50 à 60 % de volume de fibres pour l'AFP, mais nettement moins pour les portions FFF puisque celles-ci sont extrudées. La porosité est de l'ordre des procédés traditionnels hors autoclave, mais a considérablement diminué au fur et à mesure que nous affinons le procédé. En utilisant des matériaux de très haute qualité et en laboratoire, nous avons atteint une porosité inférieure à 0,5%, mesurée à l'aide de tomodensitométries. Comme toujours, un grand nombre de variables ont un impact sur ce nombre et lorsque nous produisons des pièces très complexes, il est difficile de maintenir une faible porosité. Nous avons effectué de nombreux tests destructifs et non destructifs de pièces et de coupons fabriqués avec le système. »
Contrôle robotique de haute précision
Bischoff :« SCRAM offre une technologie robotique de haute précision. Les robots standard du commerce sont une solution abordable pour obtenir un mouvement à 6 degrés de liberté pour le placement et l'impression, mais ils sont loin d'être assez précis pour une AFP de qualité aérospatiale. Nous avons commencé à comprendre comment appliquer ces robots aux systèmes AFP aérospatiaux il y a des années. Vous devez vraiment comprendre les principes fondamentaux du système et les problèmes liés à la précision. Nous avons un groupe complet de robots de 60 à 70 ingénieurs, et c'est tout ce qu'ils font. »
« C'est un problème incroyablement complexe d'atteindre une précision de positionnement et de trajectoire élevée. Vous avez des imprécisions dans le robot (CTE du robot, jeu, vibrations, etc.) et dans l'axe externe, des calibrations de point d'outil, un bâti de pièce en rotation et plusieurs autres sources. Ne pas prendre en compte/répondre à l'un d'entre eux peut être catastrophique une fois que vous commencez à imprimer dans un véritable espace 3D. Pour ce faire, nous jetons le contrôleur fourni avec le robot et exécutons le tout avec une CNC Siemens. Nous ajoutons ensuite la rétroaction secondaire brevetée d'Electroimpact sur tous les axes du robot, ce qui nous fait passer d'une tolérance de 30 à 40 mils [0,030 à 0,040 pouce] à ±15 mils [0,015 pouce]. Ensuite, nous appliquons une compensation cinématique d'ordre élevé pour atteindre ±10 mils [0,010 pouce]. »
Vitesse, effecteurs finaux et table d'impression rotative
Marron :« Nous utilisons la consolidation in-situ, donc la vitesse d'application ne sera pas proche de celle des rubans préimprégnés thermodurcissables. De plus, il s'agit d'un robot, et non d'une grande plate-forme à portique rigide (comme l'AFP), qui est conçue pour des vitesses plus élevées. Et la vitesse ne se limite pas à la pose et à l'impression, mais comprend également le délai d'exécution de l'outillage. La véritable mesure est la rapidité avec laquelle vous pouvez avoir une pièce fabriquée numériquement en main ? »
«La partie de la vidéo mesurait 36 pouces de haut (avec la base imprimée, elle dépassait 4 pieds) et son diamètre était de 16 pouces. Si nous fonctionnions sans interruption en équipes, nous pourrions produire cela en quelques jours, ce qui est un temps incroyablement court pour avoir une pièce en main. Les pièces sont également produites directement à partir du fichier CAO, donc si vous avez besoin d'itérer, vous modifiez le CAO, republiez les trajectoires d'outil et imprimez la nouvelle pièce. »
Allen :« Actuellement, pour l'impression de l'outil de support, nous avons un processus à grande échelle basé sur le filament. Le débit est un peu lent, ce qui a un impact sur le temps d'impression. En juillet, nous avons mis en service notre premier effecteur final avec une extrudeuse à vis à granulés. Cela augmentera le rendement mais produira des billes épaisses, nous ajouterons donc également un effecteur de fraisage pour l'usinage de la surface imprimée. »
Marron :« Nous disposerons d'une famille d'effecteurs terminaux compatibles que le robot pourra ramasser et déposer, exécutant une grande variété de fonctions additives et soustractives selon les besoins. La procédure de prélèvement et de dépose de l'effecteur final est entièrement automatisée, ce qui est une caractéristique standard de tous nos systèmes AFP ainsi que SCRAM. L'ensemble de l'effecteur terminal est fixé au robot à l'aide d'un module d'interface de changement d'outil automatique et il existe des supports pour le stockage de l'effecteur terminal. »
« Le système imprime sur un axe de rotation externe et est contrôlé par la CNC. Nous avons cela parce que le robot seul ne peut pas atteindre tous les points des pièces que nous voulons fabriquer. À terme, nous avons l'intention de mettre le système sur rails pour fabriquer des pièces plus grandes, mais nous voulons d'abord affiner le système à cette échelle. Nous avons discuté de l'utilisation de deux robots, et nous savons philosophiquement comment nous procéderions. (Nous avons produit d'autres systèmes de fabrication multi-robots intégrés.) Mais lorsque vous avez deux robots travaillant dans des zones de travail qui se chevauchent, les commandes deviennent extrêmement compliquées. »
Une future production flexible rendue possible
Marron :« Cette cellule multifonctionnelle apportera de la valeur au client final. Elle n'a pas toujours à produire des pièces thermoplastiques renforcées de fibres continues. En ajoutant l'extrusion et le broyage au dépôt continu de fibres, nous élargissons sa gamme et sa flexibilité. Par exemple, certaines des structures que nous avons démontrées ont des fonctions soustractives dans la construction de la pièce. Le robot vérifie ensuite la surface et ferme cette cavité. Cela n'est actuellement pas possible sans plusieurs étapes, un outillage spécialisé et/ou un assemblage final quelconque. »
« Cependant, il existe un thème encore plus important que la simple production de pièces. À long terme, cette approche a une chance de changer radicalement la façon dont les systèmes aérospatiaux et de défense sont conçus et fabriqués. Une seule ligne de production ne sera plus dédiée à un seul produit. Au lieu de cela, la production sera flexible. De plus, si vous pouvez réduire l'outillage, vous pouvez réduire les pièces de rechange sur l'étagère. Cette flexibilité a des impacts tout au long de la chaîne d'approvisionnement, y compris la réduction des déchets dus à l'expiration des matériaux. »
Bischoff : « Avec une petite poignée de cellules SCRAM et de conceptions numériques, tout ce que vous avez à portée de main est la matière première, par rapport à des dizaines d'outils fixes et de matériaux thermodurcissables à durée de vie limitée. »
Marron : « Nous avons encore du chemin à parcourir avant que la production ne soit vraiment gérée de cette façon, mais vous pouvez maintenant voir clairement comment c'est possible. »
Résine
- ACEO® dévoile une nouvelle technologie pour l'impression 3D avec du silicone
- Les émirats adopteront la technologie d'impression 3D pour les pièces d'avion
- Introduction à l'impression 3D avec frittage laser sélectif
- Impression du fusible 1 avec le fusible 1
- Impossible Objects s'associe à BASF pour l'impression 3D composite
- Broetje-Automation élargit le portefeuille AFP pour la production composite en série
- Partenaire Victrex et Bond pour l'impression 3D de pièces PAEK
- La VDMA va développer une feuille de route pour l'impression 3D avec une feuille de route pour la fabrication
- Pratiques de traçabilité pour la production de pièces d'usinage de précision