Mécanisme de suppression de couche atomique unique basé sur la coupe du cuivre monocristallin :effet de rayon de bord
Résumé
L'objectif ultime de la découpe mécanique est de réduire l'épaisseur minimale des copeaux à une seule couche atomique. Dans cette étude, le mécanisme d'élimination d'une seule couche atomique basé sur la coupe sur du cuivre monocristallin est étudié par une série d'analyses de dynamique moléculaire. Les résultats de la recherche indiquent que lorsque la profondeur de coupe diminue à l'échelle atomique, l'épaisseur minimale des copeaux peut être réduite à une seule couche atomique par coupe mécanique à l'aide d'un outil à bord arrondi. Le comportement d'élimination de matière lors de l'élimination d'une couche atomique unique basée sur la coupe présente quatre caractéristiques, notamment la formation de copeaux par le mouvement de dislocation entraîné par la contrainte de cisaillement, la déformation élastique sur la surface traitée, l'effet de dimensionnement atomique et l'effet de rayon de coupe. Sur la base de cette compréhension, un nouveau modèle de coupe est proposé pour étudier le comportement d'enlèvement de matière dans le processus d'enlèvement d'une seule couche atomique basé sur la coupe, significativement différent de ceux de la nanocoupe et de la coupe conventionnelle. Les résultats fournissent un support théorique pour la recherche et le développement de la technologie de fabrication à l'échelle atomique et proche de l'atome.
Introduction
La coupe mécanique, en tant que l'une des méthodes d'usinage soustractives les plus importantes, a été appliquée pour produire des pièces avec une qualité de finition de surface élevée [1, 2]. Un grand nombre d'études théoriques et expérimentales ont été menées pour clarifier le mécanisme d'enlèvement de matière sous-jacent à l'échelle nanométrique afin d'établir et d'enrichir la théorie de base de la nanocoupe [3,4,5,6]. Les résultats de la recherche contribuent de manière significative à l'application de la découpe nanométrique dans les universités et l'industrie, permettant la fabrication de pièces hautes performances nécessitant une forme complexe et une qualité de finition de surface nanométrique [7, 8]. Cependant, il n'y a toujours pas de rapport sur le mécanisme d'enlèvement de matière dans la coupe à l'échelle atomique et proche de l'atome (ACS), ce qui limite sérieusement les progrès du développement de la technologie de fabrication de nouvelle génération - fabrication à l'échelle atomique et proche de l'atome ( ACSM), c'est-à-dire Fabrication III [9]. De plus, le développement progressif des dispositifs à l'échelle atomique a également souligné la demande de divers processus d'usinage pour atteindre l'ACSM [10].
Dans la coupe à grande échelle conventionnelle, la profondeur de coupe est nettement plus grande que le rayon de l'arête de coupe, où l'enlèvement de matière est réalisé par la formation de copeaux entraînée par le cisaillement de la matière [11,12,13]. En micro/nanodécoupe, comme la profondeur de coupe est comparable ou inférieure au rayon d'arête de l'outil, la formation de copeaux d'extrusion devient progressivement dominante avec une profondeur de coupe diminuant jusqu'à l'échelle nanométrique, ce qui est fortement influencé par les effets de rayon d'arête de coupe [14,15,16 ,17,18,19]. Dans la coupe ACS, comme la profondeur de coupe est encore réduite à une échelle proche de l'atome et même à l'échelle atomique, qui est bien inférieure au rayon de l'arête de coupe, l'effet du rayon de l'arête affecterait inévitablement le comportement d'enlèvement de matière.
De plus, contrairement à la coupe conventionnelle et à la micro/nano coupe, dans la coupe ACS, la profondeur de coupe est non seulement nettement inférieure au rayon de l'arête de coupe, mais également comparable ou même inférieure au rayon des atomes de la pièce. Le comportement pratique d'enlèvement de matière serait modifié à différents rapports de la profondeur de coupe au rayon atomique de la pièce, ce qui est reconnu comme un nouvel effet de dimensionnement, c'est-à-dire l'effet de dimensionnement atomique [20]. Par conséquent, dans la coupe ACS, l'effet du rayon de coupe et l'effet de la taille des atomes doivent être pris en compte. Cependant, il n'y a aucun rapport sur cette question d'une importance critique dans l'étude de la technologie de coupe ACS.
Pour ces raisons, dans la présente étude, l'effet de dimensionnement atomique et l'effet de rayon de bord sur le mécanisme d'élimination d'une couche atomique unique basé sur la coupe sont étudiés en utilisant la modélisation de la dynamique moléculaire (MD).
Ce document est structuré par les sections suivantes. La section 2 présente la méthodologie utilisée, y compris la modélisation et le protocole, la fonction potentielle appropriée. La section 3 présente les résultats de l'analyse et les discussions pertinentes. La section 4 discute du mécanisme détaillé d'élimination d'une couche atomique basé sur la coupe, sous l'influence couplée de l'effet de pointe et de l'effet de dimensionnement atomique. Les résultats de l'étude sont conclus dans la section 5.
Méthodologie
Modèle et protocole de simulation
Comme la profondeur de coupe diminue à l'échelle atomique ou proche de l'atome, il est en effet difficile d'observer expérimentalement le processus d'enlèvement de matière dans la pratique. Dans cette étude, une série de simulations MD sont menées pour analyser le mécanisme d'élimination d'une couche atomique unique basé sur la coupe, en mettant l'accent sur l'effet de dimensionnement atomique de la pièce et l'effet de rayon de pointe.
La figure 1 montre les instantanés de la configuration atomique du modèle de coupe diamant-cuivre, qui se compose d'une pièce en cuivre monocristallin et d'un outil de coupe en diamant. Les simulations sont conduites sur le plan (111) du cuivre monocristallin. Les dimensions de la pièce en x -[1 -1 0], y -[1 1 -2], et z Les directions -[1 1 1] sont respectivement 27, 10 et 5 nm. Au cours des simulations MD, les atomes de la pièce sont divisés en atomes de couche limite, atomes de couche thermostatique et atomes de couche newtonienne, respectivement, comme le montre la figure 1. Les deux couches au bas de la pièce, à savoir la couche limite, sont maintenues fixes sur les simulations MD, pour éliminer l'éventuelle translation de position de la pièce induite par la coupe. Les trois couches atomiques adjacentes à la couche limite sont des atomes de la couche thermostatique. La température de la couche thermostatique est maintenue à 298 K par des méthodes de remise à l'échelle de la vitesse. Les atomes restants de la pièce appartiennent à la couche newtonienne. Dans les présentes simulations, l'angle de coupe et l'angle de dépouille de l'outil de coupe sont de 0° et 12°. Les paramètres détaillés du modèle sont résumés dans le tableau 1. Étant donné que la coupe ACS est de préférence réalisée à une vitesse de coupe inférieure, une vitesse de coupe de 25 m/s le long de la direction [-1 1 0] est utilisée après avoir pris en compte l'effet de la vitesse de coupe et du temps de calcul. coût.
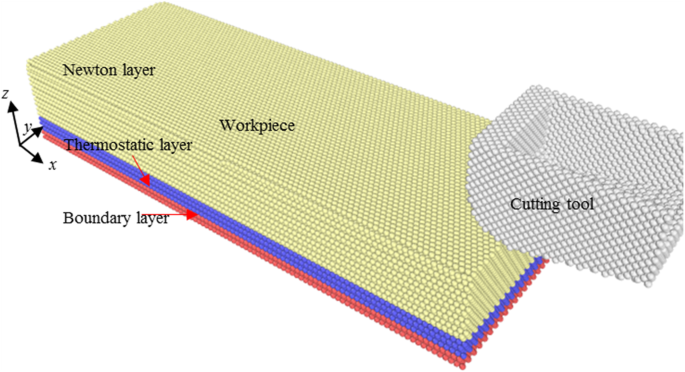
Modèle de simulation pour modèle de coupe au diamant
Fonction potentielle
Le système de coupe cuivre-diamant implique principalement deux types d'atomes, à savoir les atomes de cuivre et de diamant. Dans les simulations MD, les interactions interatomiques doivent être décrites avec précision pour garantir la précision de calcul des résultats de simulation. Ainsi, une sélection raisonnable de la fonction potentielle est d'une importance critique. Dans cette étude, la fonction de potentiel de la méthode de l'atome intégré (EAM) fréquemment utilisée est adoptée pour décrire les interactions interatomiques entre les atomes de cuivre [21]. La fonction Morse est appliquée pour calculer les interactions entre les atomes de cuivre et les atomes de diamant (Cu-C), principalement en fonction du r.
$$ E={D}_0\left[{e}^{-2\alpha \left(r-{r}_0\right)}-2{e}^{\alpha \left(r-{r} _0\droit)}\droit] $$ (1)où E et D 0 se référer à la paire énergie potentielle et énergie de cohésion, α représente une constante, r 0 est la distance d'équilibre, et r est la distance entre deux atomes. Pour les interactions Cu-C, D 0 est de 0,087 ev, r 0 est 0,205 nm [22], et α est 51.40 nm −1 . Pour les interactions entre les atomes de carbone dans l'outil de coupe (C-C), la force de liaison significativement plus forte entre les atomes de diamant que les atomes de cuivre est négligeable. L'outil de coupe est considéré comme rigide lors de l'analyse.
Définition de la profondeur de coupe
Profondeur de coupe (a ) est défini comme étant la distance entre le point le plus haut de la surface de la pièce et le point le plus bas de l'outil de coupe. La taille d'un atome de pièce est généralement représentée par le rayon atomique (r w ). Comme indiqué sur la figure 2, lorsque la première couche atomique la plus haute est destinée à être retirée de la surface de la pièce, théoriquement, la profondeur de coupe maximale utilisée peut être obtenue comme suit :
$$ {a}_{\mathrm{max}}={r}_w+0.5\ast {d}_{layer} $$ (2)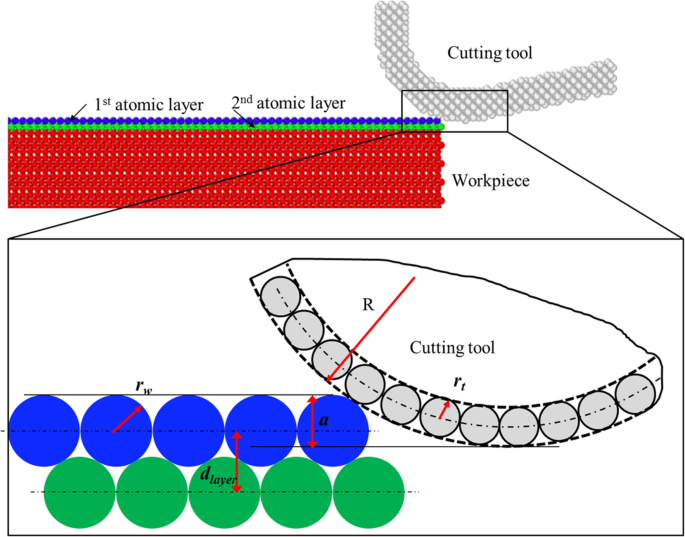
Diagramme schématique pour la définition de la profondeur de coupe dans l'élimination d'une seule couche atomique
Ici, d couche représente la distance d'espacement entre les couches atomiques voisines les plus hautes sur la surface de la pièce. Dans cette étude, toutes les analyses sont basées sur la surface (111) de la pièce en cuivre monocristallin ; par conséquent, le r w dans l'éq. (2) fait référence au rayon des atomes de cuivre, à savoir 1,28 Å. Le d couche est 2.087 Å. Lorsque a est plus grand que a max , le point le plus bas de l'outil de coupe entrera en contact direct avec la deuxième couche atomique et peut induire la déformation du matériau et même son enlèvement. Par conséquent, dans la présente étude, les profondeurs de coupe utilisées sont inférieures à a max (2.32 Å).
Sur la base des résultats, le mécanisme fondamental d'élimination d'une couche atomique basé sur la coupe sera considérablement modifié à diverses combinaisons des rapports de a à R et un à r w .
Résultats et discussion
Selon les résultats de MD, l'effet de dimensionnement atomique et l'effet de rayon de pointe ont grandement influencé le processus d'élimination d'une seule couche atomique basé sur la coupe. Dans les sections suivantes, pour décrire clairement l'effet de dimensionnement atomique et l'effet du rayon d'arête de l'outil, le rapport de la profondeur de coupe (a ) au rayon atomique de la pièce (r w ), a/r w , et celle de la profondeur de coupe (a ) au rayon du bord (R ), a/R , sont employés. Les résultats de l'analyse sont systématiquement étudiés sous les aspects de formation de copeaux, de génération de surface, de déformation souterraine et de comportement de déplacement atomique. Les résultats fournissent des informations détaillées sur les caractéristiques typiques du mécanisme d'élimination d'une seule couche atomique basé sur la coupe.
Formation de puce
Les résultats de l'analyse indiquent qu'en raison de l'effet de dimensionnement atomique de la pièce [20], il existe deux valeurs critiques du rapport de la profondeur de coupe (a ) au rayon atomique de la pièce (r w ), à savoir la valeur critique 1 (C1 ) et la valeur critique 2 (C2 ), qui a divisé le comportement de formation de copeaux en différents cas.
- un.
Le rapport de a/r w inférieur à la valeur critique 1 (C1 ).
La figure 3 montre les résultats de la simulation MD à divers rayons d'arête d'outil à une profondeur de coupe d'environ 1,1 Å. Ici, le rapport de profondeur de coupe (a ) au rayon atomique de la pièce (r w ) est de 0,781.
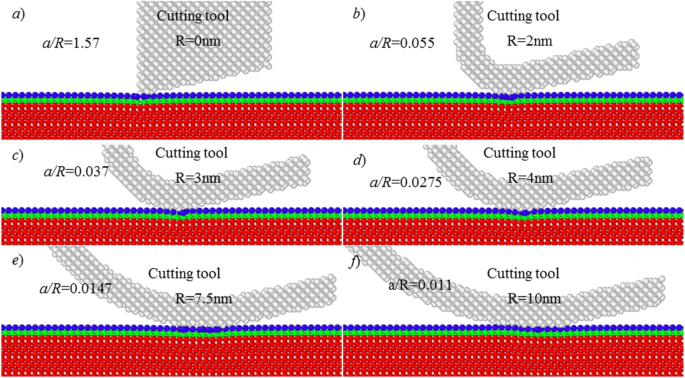
Résultats de simulation à une profondeur de coupe de 1,1
Malgré l'augmentation du rayon de l'arête de coupe, une déformation élastique se produit sur la surface traitée de chaque Cu (111). Il n'y a pas de formation de copeaux et d'enlèvement de matière au cours du processus de coupe. L'étude montre que la profondeur de coupe doit être supérieure à environ 1,1 pour permettre l'enlèvement de matière sur la surface de Cu (111).
- b.
Le rapport de a/r w est supérieur à C1, mais inférieur à la valeur critique 2 (C2 ).
Lorsque la profondeur de coupe est supérieure à environ 1,1 , à savoir, le rapport de a/r w est supérieur à 0,781, un enlèvement de matière se produit sur la surface de la pièce. Comme le montre la figure 4, une partie du matériau est retirée de la surface de la pièce, mais un plus grand nombre d'atomes dans la première couche supérieure est resté sur la nouvelle surface traitée, formant des défauts de surface. De plus, lorsque le rayon du bord augmente jusqu'à 7,5 nm, le rapport de a/R est de 0,019. Dans ce cas, une partie des atomes de la première couche atomique a été pressée dans la deuxième couche et même dans la troisième couche atomique, comme illustré sur la figure 4e, ce qui devrait être attribué à l'action d'extrusion de l'outil de coupe. Cela indique également que l'effet du rayon du bord de l'outil commence à imposer une influence sur le processus d'enlèvement de matière, bien qu'un enlèvement de matière continu n'ait pas pu être obtenu.
- c.
Le rapport de a/r w est plus grand que C2 .
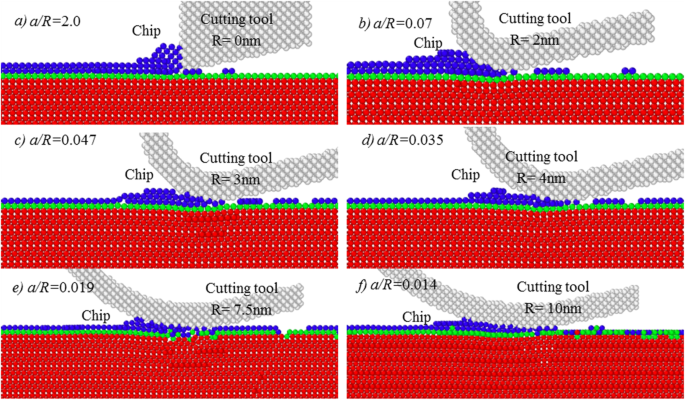
Résultats de la simulation à une profondeur de coupe de 1,4
La figure 5 montre la formation de copeaux à une profondeur de coupe d'environ 2 Å. Ici, le rapport de a/r w =2 Å/1,28 Å =1,563. Par rapport à la figure 3, avec une augmentation de la profondeur de coupe à 2 Å, les atomes dans la couche atomique ciblée pourraient être éliminés de manière continue et stable par formation de copeaux. Cela indique que la profondeur de coupe a été supérieure à l'épaisseur minimale des copeaux de cuivre monocristallin, et que l'épaisseur minimale des copeaux pourrait être réduite à une seule couche atomique avec une profondeur de coupe d'environ 2 Å. Après la coupe, les matériaux de la première couche atomique ont été entièrement retirés de la surface de la pièce.
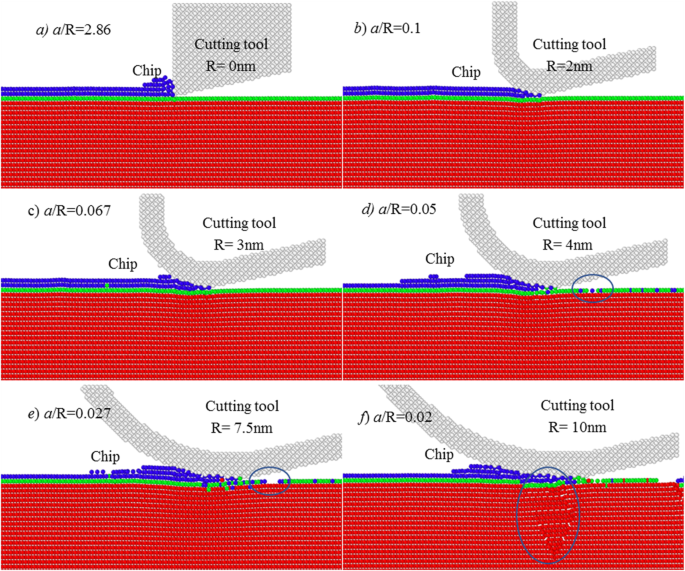
Résultats de simulation de coupe ACS à une profondeur de coupe =2 Å
Cependant, on peut également remarquer sur la figure 5 qu'en raison de l'augmentation du rapport de a/R , les atomes de la première couche atomique subissent évidemment des processus d'élimination différents, en particulier la déformation induite par la coupe sur la surface traitée. À la profondeur de coupe de 2 Å, lorsqu'un outil de coupe tranchant est utilisé, à savoir, le rapport de a/R est de 5,70, seule une légère déformation se produit sur la surface traitée. Lorsque le rayon de pointe augmente jusqu'à 3 nm, le rapport a/R est de 0,134, l'amplitude de la déformation élastique était évidemment augmentée.
Lorsque le rayon du bord de l'outil est augmenté à 4 nm, comme indiqué sur la figure 5d, de nombreux atomes dans la première couche atomique ciblée ont été pressés dans la deuxième couche atomique, formant la nouvelle surface traitée. Au rayon du bord de l'outil d'environ 7,5 nm, une partie des atomes de la première couche est même diffusée vers la troisième couche atomique. Lorsque le rayon du bord de l'outil atteint environ 10 nm, une déformation élastique et plastique évidente se produit, qui peut également être déterminée dans la section 3.3 suivante.
Par conséquent, l'élimination d'une seule couche atomique basée sur la coupe dépend non seulement du rapport a/r w , mais aussi le rapport a/R . Pour obtenir l'élimination d'une seule couche atomique par découpe mécanique, c'est-à-dire l'élimination de matière à l'échelle atomique, les effets de dimensionnement des atomes et l'effet de rayon de coupe doivent être pris en compte, ce qui est très différent de la micro/nanocoupe et de la découpe conventionnelle à l'échelle macro.
Génération de surface
L'un des objectifs de l'élimination de la couche atomique basée sur la coupe est d'obtenir une surface traitée sans défaut avec une structure cristalline idéale. L'effet de dimensionnement atomique de la pièce sur la génération de surface dans la coupe ACS a été étudié récemment [20]. Dans la présente étude, pour indiquer clairement l'effet du rayon de pointe sur la génération de surface dans la coupe ACS, la topographie de surface et la composition de surface de la nouvelle surface traitée sont étudiées comme suit.
Topographie de surface
La figure 6 montre les topographies de surface de la surface de Cu (111) traitée à différents rayons de bord. Ici, une profondeur de coupe de 2 Å est adoptée. Comme le montrent les figures 6a, b, lorsque le rayon d'arête de l'outil est inférieur à 3 nm, les surfaces de Cu (111) avec une structure cristalline idéale pourraient être obtenues. Quant aux défauts sur le côté gauche de la surface de la pièce, ils sont dus à la déformation lors de la coupe-sortie de l'outil. Au cours de la coupe dans une étape à la place, il n'y a aucun défaut de surface formé sur la surface traitée.
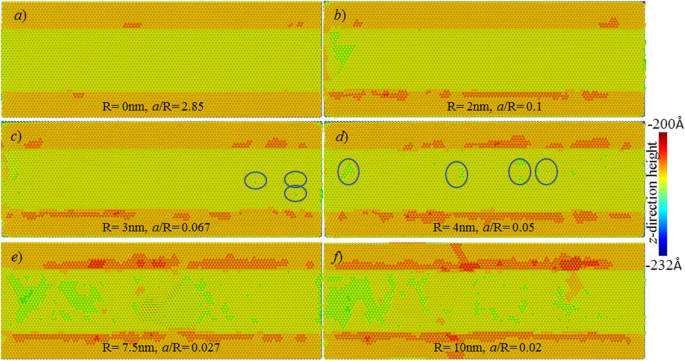
Effets du rayon de l'arête de l'outil sur les topographies de surface. Les atomes sont colorés en fonction de leurs hauteurs dans la direction z
Cependant, à mesure que le rayon du bord de l'outil augmente, de nombreux défauts se forment progressivement sur la surface traitée. Au rayon du bord de 4 nm, de nombreux défauts semblables à des piqûres se forment sur la surface traitée, voir Fig. 6d. En outre, lorsque le rayon de l'arête de l'outil est égal ou supérieur à 5 nm, un grand nombre de défauts de surface se forment, détériorant sérieusement la qualité de la surface. Dans ce cas, plus d'une couche d'atomes a été retirée de la surface de la pièce. Par conséquent, il peut être déterminé qu'à la profondeur de coupe de 2 Å, lorsque le rayon du bord de l'outil est inférieur à 3 nm, l'élimination d'une seule couche atomique pourrait être obtenue sur la surface de Cu (111). En raison de l'effet de rayon de coupe, le rapport de la profondeur de coupe (a ) au rayon du bord (R ) doit être supérieur à un seuil, afin d'obtenir une surface traitée sans défaut via l'élimination d'une seule couche atomique basée sur la coupe. Ici, la valeur critique du rapport de a/R est [0,05, 0,067].
Composition de surface
La figure 7 montre la composition des surfaces traitées à divers rayons d'arête d'outil et la profondeur de coupe de 2 Å. Ici, les atomes verts et bleus sont ceux des première et deuxième couches, tandis que les atomes rouges sont ceux en dessous de la deuxième couche atomique. Comme le montre la figure 7a, lorsqu'un outil de coupe tranchant est utilisé, le rapport a/R est de 2,85, la surface traitée n'est constituée que d'atomes dans la première couche. Ce résultat indique que la première couche atomique ciblée a été complètement retirée de la pièce. De plus, cela signifie que l'enlèvement de matière est effectué sous forme de couche par couche, dans laquelle les matières enlevées ne proviennent que de la première couche atomique ciblée sur la surface de la pièce.
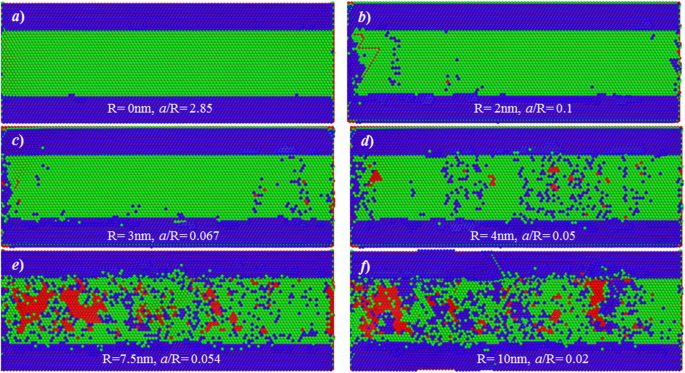
Composition de surface des surfaces traitées. Les atomes sont colorés en fonction du nombre de couche atomique
Cependant, lorsque le rayon du bord de l'outil est de 2 nm et 3 nm, comme le montrent les figures 7b, c, les surfaces traitées sont composées de deux couches atomiques (bleu et vert). Cela indique que bien que l'élimination d'une seule couche atomique ait été obtenue, le processus de génération de surface implique au moins 2 couches atomiques. De plus, lorsque le rayon du bord de l'outil est supérieur à 4 nm, il y a un grand nombre d'atomes de la première couche atomique sur la surface traitée, indiquant que de nombreux atomes de la première couche ont été pressés pour générer une nouvelle surface.
Par conséquent, avec une augmentation du rayon d'arête de coupe, la génération de surface a été considérablement modifiée. Deux types de mécanismes de génération de surface impliqués sont résumés ci-dessous :
- 1.
Couche par couche :la première couche atomique ciblée est entièrement supprimée pour générer une nouvelle surface traitée. Seuls les atomes de la première couche sont supprimés pendant le processus de découpe.
- 2.
Enlèvement multicouche :bien que l'élimination d'une seule couche atomique puisse être réalisée, les atomes au sein de la couche atomique ciblée subissent deux comportements de déplacement typiques. Une partie des atomes serait transformée en puce par un mouvement de dislocation provoqué par une contrainte de cisaillement, tandis que d'autres seraient extrudées dans la surface traitée, sous l'action de l'outil de coupe. Le processus d'enlèvement de matière implique au moins deux couches atomiques.
Mécanisme de déformation du sous-sol
Dans la nanocoupe, il y a une déformation élastique et plastique sur la surface traitée pendant le processus de coupe. Après le passage de l'outil de coupe sur la surface de la pièce, la partie élastique revient en arrière, tandis que la partie déformée en plastique entraînerait une déformation durable [1, 2]. Au fur et à mesure que la profondeur de coupe diminue à l'échelle atomique, dans la coupe vers l'élimination d'une seule couche atomique, il est postulé qu'il n'y a qu'une déformation élastique se produisant sur la surface traitée. Pour le vérifier, les états de déformation du sous-sol de la pièce pendant et après la coupe sont analysés. La figure 8 illustre les structures de défauts dans la sous-surface de la pièce à divers rayons d'arête d'outil. Ici, les atomes sont colorés en fonction du paramètre de centro-symétrie (CSP), et les atomes avec le CSP inférieur à 3 sont omis, ce qui représente ceux avec une structure FCC parfaite.
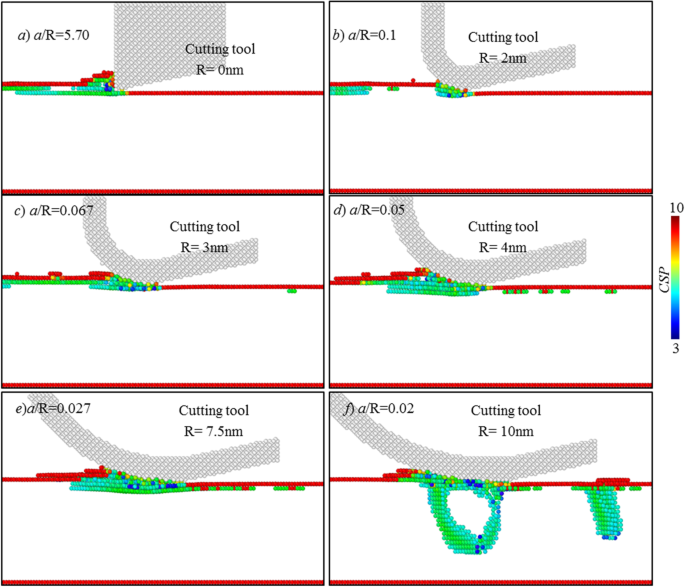
Composition de surface des surfaces traitées. Les atomes sont colorés en fonction de leurs CSP
Lorsque le rayon de l'arête de coupe est inférieur à 4 nm, aucun défaut de sous-surface ne se forme dans la surface traitée. Il n'y a qu'une déformation élastique sur la surface traitée lors de la coupe.
Comme le montre la figure 8, lorsque le rayon de l'arête de coupe est égal ou supérieur à 4 nm, des défauts de sous-surface sont initialisés. De plus, à mesure que le rayon de l'arête de coupe augmente, le nombre de défauts souterrains augmente considérablement. Lorsque le rayon du bord atteint environ 10 nm, une boucle de dislocation s'est formée et elle n'a pas pu disparaître après la coupe, comme le montre la figure 9e. Il indique clairement la déformation plastique se produisant sur la surface traitée.
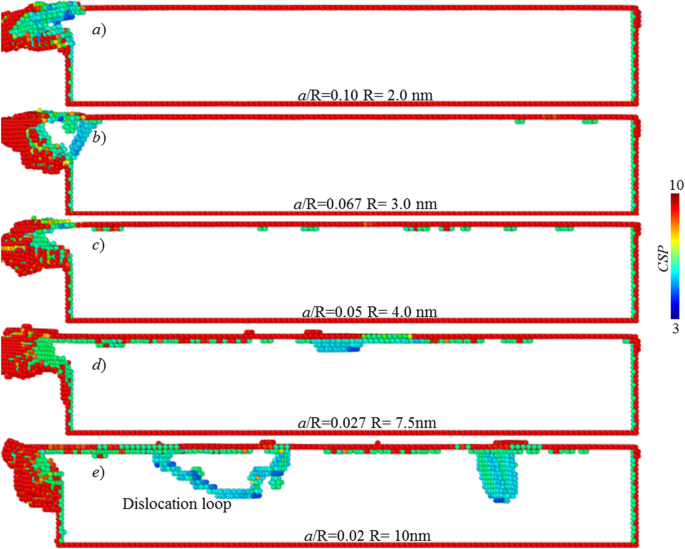
Défauts de sous-surface à divers rayons d'arête d'outil. Les atomes sont colorés en fonction de leurs CSP
Après le passage de l'outil sur la surface de la pièce, la partie déformée élastiquement reviendrait en arrière ; ainsi, des parties des défauts du sous-sol sont annihilées. Comme le montrent les Fig. 9a–c, enfin, il n'y a pas de défaut de sous-surface, lorsque le rayon de l'arête de l'outil est de 2 nm ou 3 nm.
Quant à la partie déformée plastiquement, elle entraîne une déformation durable. Comme le montre la figure 9, lorsque le rayon du bord de l'outil est de 7,5 nm, il reste un petit nombre de défauts sous la surface. Lorsque le rayon du bord de l'outil est de 10 nm, la boucle de dislocation et le défaut d'empilement existent enfin dans la sous-surface de la pièce.
Sur la base de l'analyse ci-dessus, on peut déduire que pour permettre l'élimination d'une seule couche atomique basée sur la coupe, la déformation plastique doit être évitée et seule la déformation élastique est autorisée sur la surface traitée. Il est considéré comme l'une des caractéristiques du processus d'élimination d'une seule couche atomique basé sur la coupe.
Comportement de déplacement atomique
Selon les fichiers de trajectoire MD, le mouvement de dislocation a dominé le processus d'élimination d'une seule couche atomique basé sur la coupe. La figure 10 montre les résultats de la simulation en utilisant différents rayons d'arête d'outil. Au rayon du bord de 2 nm, sous l'action de l'outil de coupe, seule la première couche atomique est glissée le long de la direction de coupe pour former une puce, tandis que les autres restent immobilisées. Il pourrait être considéré comme une section transversale d'une luxation de bord.
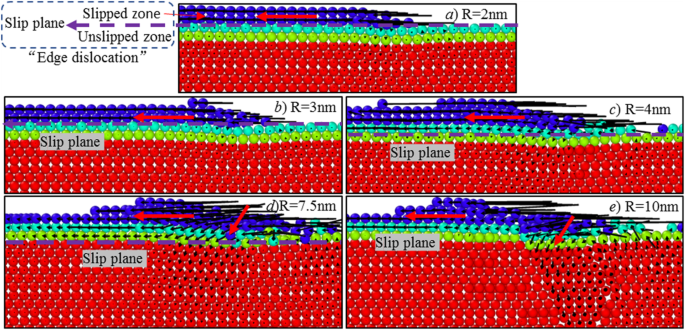
Comportement de déplacement atomique à divers rayons de tranchant
Au fur et à mesure que le rayon du bord de l'outil augmente, une partie du matériau dans la première couche atomique a été pressée dans la surface traitée, induisant le glissement des couches atomiques sous la première couche. De plus, à mesure que le rayon du bord de l'outil augmente, le nombre de couches atomiques subissant un processus de glissement de matériau a tendance à augmenter. Lorsque le rayon du bord de l'outil est de 4 nm, à l'exception de la première couche atomique, la deuxième couche atomique conduit également le glissement du matériau le long de la direction de coupe, comme illustré à la Fig. 10. Lorsque le rayon du bord de l'outil est de 7,5 nm, à mesure que l'outil de coupe avance, les trois premiers les couches atomiques sur la surface de la pièce ont glissé le long de la direction de coupe. De plus, lorsque le rayon du bord de l'outil est augmenté à 10 nm, un grand nombre de matériaux a été pressé pour former une nouvelle surface traitée ; il y a une déformation plastique (voir Fig. 10e) se produisant sur la surface de la pièce, qui peut également être déterminée sur la Fig. 9.
La figure 11 montre le processus de glissement de la couche atomique ciblée le long de la direction de coupe. La zone de la zone glissée est continuellement agrandie avec l'outil de coupe se déplaçant vers l'avant. A la distance de coupe de 17,5 nm, la zone de glissement a atteint une valeur maximale. Par la suite, les matériaux à l'intérieur de la zone de glissement sont continuellement transformés en copeaux ; le volume de puce est également augmenté.
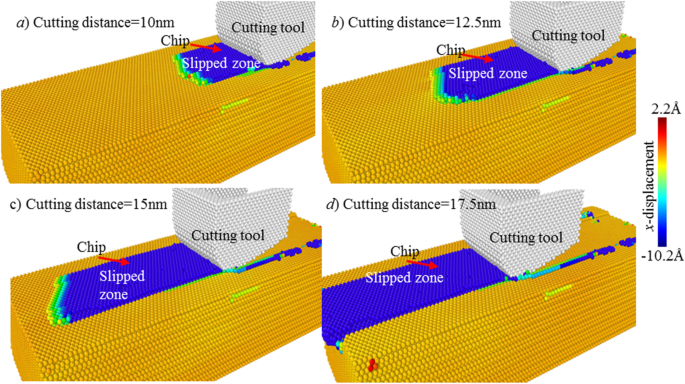
Processus de glissement de la couche atomique ciblée à un rayon de pointe de 2 nm. Les atomes sont colorés en fonction de leurs valeurs de déplacement atomique dans la direction x
Dans l'ensemble, selon l'analyse des sections 3.3 et 3.4, à mesure que le rayon de l'arête de l'outil augmente, le mécanisme de déformation de la subsurface et le comportement de déplacement atomique ont considérablement changé. À différents rayons de bord d'outil, différents nombres de couches atomiques ont tendance à glisser le long de la direction de coupe, tandis que différents régimes de déformation se produisent sur la surface traitée, comme résumé dans le tableau 2. De plus, on peut constater que dans l'élimination d'une seule couche atomique basée sur la coupe processus, la formation de copeaux est régie par un mouvement de dislocation entraîné par la contrainte de cisaillement, très différent de la formation de copeaux dans la coupe et la nanocoupe conventionnelles. Il peut également être considéré comme une caractéristique de l'élimination d'une couche atomique unique basée sur la coupe.
Force de coupe
Influence de l'effet de rayon de bord
La figure 12 montre l'effet du rayon de coupe sur les forces de coupe moyennes à une profondeur de coupe de 2 Å. Ici, les composantes tangentielle et normale des forces de coupe, à savoir, F t et F n , sont comparés. Comme illustré, pour un outil de coupe tranchant, le rapport de a/R est de 2,85, et le F t de 16,4 nN est évidemment plus petit que F n de 23,7 nN. Au fur et à mesure que le rayon de l'arête de l'outil augmente, les deux F t et F n sont augmentés. Cependant, le F n a montré des amplitudes de croissance beaucoup plus importantes que F t . Cela indique clairement qu'à mesure que le rayon de l'arête de l'outil augmente, la force de coupe normale aurait un effet plus important sur le processus d'enlèvement de matière lors du processus de coupe ACS. Cependant, lorsque le rayon du bord de l'outil est supérieur à environ 3 nm, l'élimination d'une seule couche atomique n'a pas pu être obtenue. Ainsi, une force de coupe normale plus élevée ne serait pas utile pour permettre l'élimination d'une seule couche atomique basée sur la coupe, et une force de coupe normale inférieure devrait être de préférence adoptée.
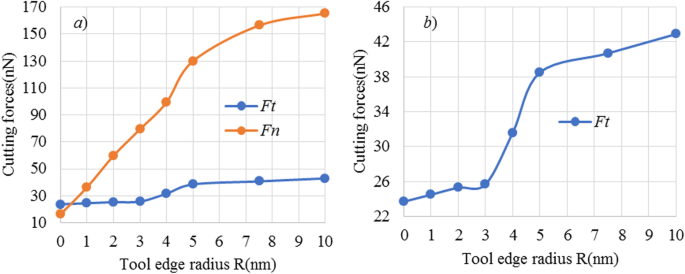
Tracé des forces de coupe en fonction du rayon de l'arête de coupe à une profondeur de coupe de 2
Comme les forces de coupe normales fournissent la contrainte de compression pour permettre une déformation élastique et/ou plastique sur la surface traitée, les forces de coupe tangentielles fourniraient la contrainte de cisaillement à la formation de copeaux. Par conséquent, on peut en déduire que la formation de copeaux dans l'élimination d'une couche atomique unique basée sur la coupe devrait être principalement entraînée par la force de coupe tangentielle. On peut également voir sur la figure 12b que le F t a présenté trois types de changements, ce qui conduit en outre à différentes topographies de surface (voir Fig. 6), dont les suivantes :
Lorsque le rayon d'arête de l'outil est inférieur à environ 3 nm, à savoir, le rapport de a/R est de 0,067, le F t reste approximativement inchangé, et il est toujours inférieur à 25 nN, à mesure que le rayon du bord augmente. Dans ce cas, une seule couche atomique est retirée de la surface de la pièce.
Lorsque le rayon de l'arête de l'outil est de 3 nm et 5 nm, les rapports de a/R sont 0,04 et 0,067, tandis que F t est évidemment augmenté à environ 38,5 nN. Par conséquent, plus d'une couche atomique est retirée de la surface de la pièce, mais il y a un petit nombre de défauts de surface formés.
Quant au rayon de bord supérieur à 5 nm, F t converge aussi progressivement vers une valeur constante. Dans ce cas, plus d'une couche atomique est supprimée. Cependant, un grand nombre de défauts de surface se forment sur la surface et la sous-surface de la pièce.
On peut conclure qu'une force de coupe tangentielle très faible pourrait permettre l'élimination d'une seule couche atomique basée sur la coupe à un rayon d'arête de coupe raisonnable, tel que 2 nm. À son tour, l'élimination d'une seule couche atomique n'a pas pu être réalisée, malgré la force de coupe tangentielle plus importante.
Influence de l'effet de dimensionnement atomique
La figure 13 donne en outre le tracé des forces de coupe en fonction de la profondeur de coupe à un rayon d'arête de coupe de 2 nm. On peut constater qu'au rayon d'arête de coupe de 2 nm, à mesure que la profondeur de coupe augmente, la force de coupe normale et les forces de coupe tangentielles ont toutes deux présenté des changements en trois étapes. Il y a des changements évidents à une profondeur de coupe d'environ 1,1 Å et 1,6 Å. Le rapport correspondant de la profondeur de coupe (a ) au rayon atomique de la pièce (r w ) sont de 0,055 et 0,080, qui sont les deux valeurs critiques susmentionnées de a/r w , C1 et C2, comme décrit dans la section 3.1.
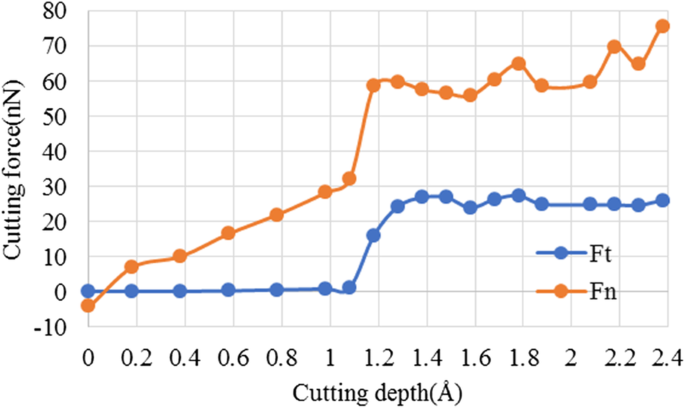
Tracé des forces de coupe en fonction de la profondeur de coupe à un rayon d'arête de 2 nm
When cutting depth is smaller than 1.1 Å, namely, the ratio of a/r w is less than 0.055, F t is always 0 nN, while F n is linearly increased to about 32 nN. However, the cutting forces could not enable plastic material deformation and removal on the workpiece surface. Consequently, there is only elastic deformation on workpiece surface, as shown in Fig. 3.
When the cutting depth is larger than 1.1 Å, but smaller than 1.6 Å, the ratio of a/r w is more than 0.055 but less than 0.080. If this case, F t has greatly increased from 0 nN to about 25 Nn, while F n further increased to about 58 nN. The cutting forces are larger enough to enable material removal on workpiece surface. At the cutting depth of 1.4 Å, there is chip formation and material removal on workpiece surface. But the stable and continuous material removal could not be realized and many defects are formed on the processed surface, as shown in Fig. 4.
When the cutting depth is larger than 1.6 Å, both F t et F n are large enough to enable continuous material removal on workpiece surface. Consequently, chip is stably formed over the workpiece surface, and the targeted atomic layer is continuously removed via chip formation, forming a new processed surface, as shown in Fig. 5b and Fig. 6b.
Overall, both cutting-edge radius effect and atomic sizing effect have an influence on cutting force in cutting-based single atomic layer removal process, thereby changing the material removal and surface generation process.
Discussions About Cutting-Based Single Atomic Layer Removal Mechanism
As per above analysis, both atomic sizing effect and cutting-edge radius effect have a great influence on the cutting-based single atomic layer removal mechanism. As summarized in Table 3, depending on the ratio of cutting depth to workpiece atomic radius(a/r w ) and the ratio of cutting depth to edge radius(a/R ), there are minimum 5 typical cases of material deformation and removal behaviours in cutting-based single atomic layer removal process. In this section, the fundamental material deformation and removal mechanism of each case is summarized.
In conventional machining, as cutting depth is significantly larger than the cutting-edge radius, the cutting-edge radius effect can be ignored. As the cutting depth is decreased to nanoscale, which is comparable or lower than the edge radius, the edge radius effect can be no longer ignored. In nanocutting, the material removal process is dominated by the extrusion deformation, which is greatly influenced by cutting-edge radius. As the cutting depth is further decreased to atomic scale, except for cutting-edge radius effect, a new sizing effect, atomic sizing effect [20] has a great influence on material removal.
As shown in Fig. 14, in the cutting-based single atomic layer removal process, there are two portions involving in cutting, i.e., nanometric cutting edge and the lowest cutting tool atoms (B ). Such two portions could be coupled to enable single atomic layer removal. The size of cutting edge, regarded as ‘nano-tool,’ is described by edge radius (R ). The cutting edge is the envelope curve of the outermost atoms in cutting tool. Regarding the lowest atoms, as ‘atomic-tool,’ it is described by workpiece atomic radius (r w ). The cutting-based single atomic layer removal is the results of the coupled actions of nano-tool and atomic-tool on workpiece material.
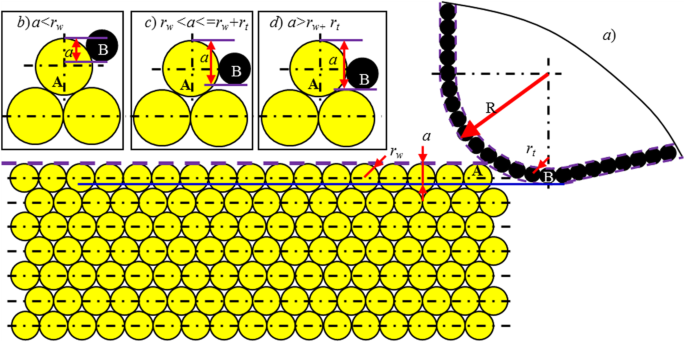
Schematic diagram for cutting-based single atomic layer removal
Firstly, depending on the ratio of cutting depth (a ) to the workpiece atomic radius (r w ), i.e., a/r , there are three kinds of material deformation behaviour in ACS cutting process.
- 1.
The ratio of a/r w is smaller than critical value 1(C1 ).
As shown in Fig. 15, chip formation does not occur, but elastic deformation does occur on the workpiece surface. During cutting process, after workpiece passes the lowest point of cutting tool, the elastically deformed part would recover completely. Consequently, no material deformation and removal occurred on the topmost surface. In such case, the tool edge effect could be ignored. This ratio could be affected by material properties (case 1).
- 2.
The ratio of a/r w is larger than C 1 , but smaller than critical value 2 (C2 ).
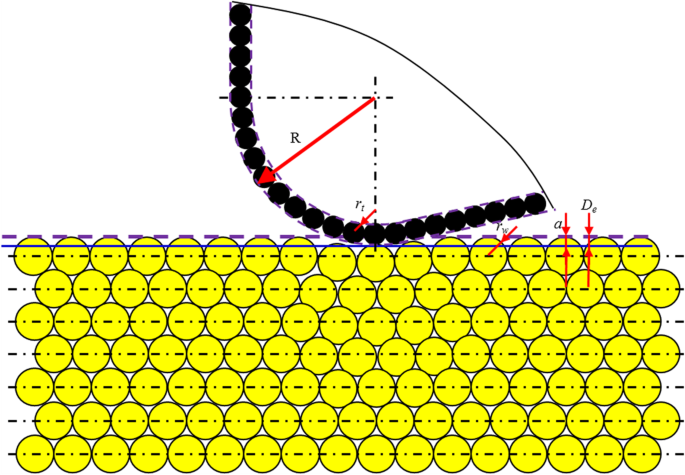
Schematic illustration of cutting-based single atomic layer removal at the ratio of a/rw smaller than C1
As the ratio of the cutting depth to atomic radius (a/r w ) increases to be larger than C1 but smaller than critical value 2(C2 ), there is material removal on the workpiece surface, but it is noncontinuous. In such case, only part of material within targeted atomic layer is formed into chip by shear stress-driven dislocation motion, while others are remained on the workpiece surface. When cutting tool passes over the workpiece surface, the surface quality of the processed surface is seriously deteriorated (case 2) (Fig. 16).
- 3.
The ratio of a/r w is larger than critical value 2 (C2 ).
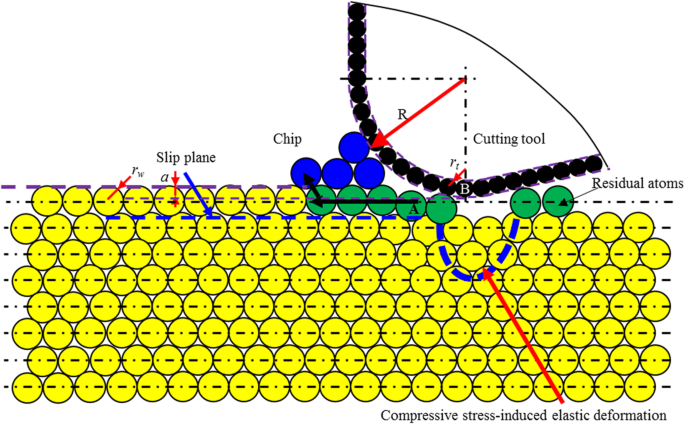
Schematic illustration of cutting-based single atomic layer removal at a/rw larger than C1 and smaller than C2
When the ratio of cutting depth to atomic radius (a/r w ) increases to be larger than critical value, there is a continuous material removal by chip formation during cutting process. In such case, the edge radius effects can no longer be ignored. For ACS cutting process, the maximum cutting depth is subnanometer order. At such extremely low cutting depth, regardless of the nominal rake angle, the effective rake angle is always largely negative. The negative rake face can produce the necessary shear stress to enable chip formation by dislocation motion and the compressive force to enable the elastic and/or plastic deformation on the processed surface.
Depending on the ratio of cutting depth (a ) to tool edge radius (R ), different kinds of elastic and/or plastic deformation process occur on the workpiece surface. There are two threshold values of a/R , namely, threshold value 1 (T 1 ) and threshold value 2 (T 2 ), leading to different material removal processes.
- a.
The ratio of a/R is larger than threshold (T 1 ).
As shown in Fig. 17, there is one atomic slip plane. The workpiece material below this plane would have an elastic deformation. As for the materials above this slip plane, it undergoes a plastic deformation by dislocation motion. A part of materials is also formed into chip by shearing stress-driven dislocation motion, while the other undergoes dislocation slip. After the workpiece passes the lowest point of the cutting tool, the elastically deformed part recovers completely (case 3).
- b.
The ratio of a/R is lower than threshold 1 (T 1 ), but larger than threshold 2 (T 2 ).
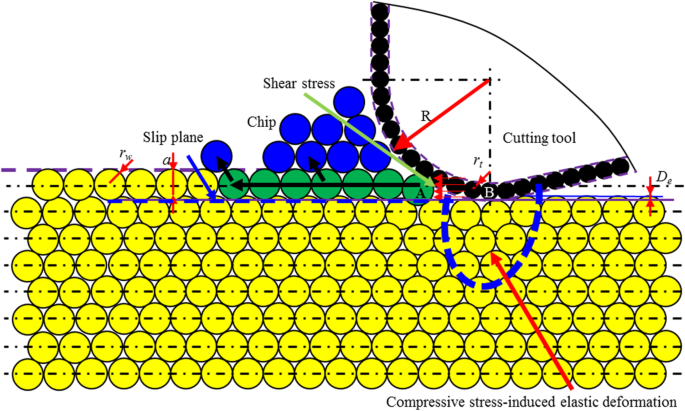
Schematic illustration of cutting-based single atomic layer removal at a/rw larger than C2 and a/R larger than T1
Under the action of cutting edge, minimum two atomic layers undergo dislocation slip, while elastic deformation occurs on the processed surface, as shown in Fig. 18. The cutting edge provides a force to generate the shear stress to enable chip formation by dislocation motion and compressive stress to induce elastic deformation on the processed surface. In such case, part of material within the targeted atomic layer is formed into chip by dislocation motion, while the other is extruded into other atomic layers to form new processed surface. It also drives the slip of other atomic layers on the workpiece surface, leading to the negative dislocation climb. After workpiece material passes the lowest point of the cutting tool, the elastic portion springs back (case 4).
- c.
The ratio of a/R is lower than threshold 2 (T 2 ).
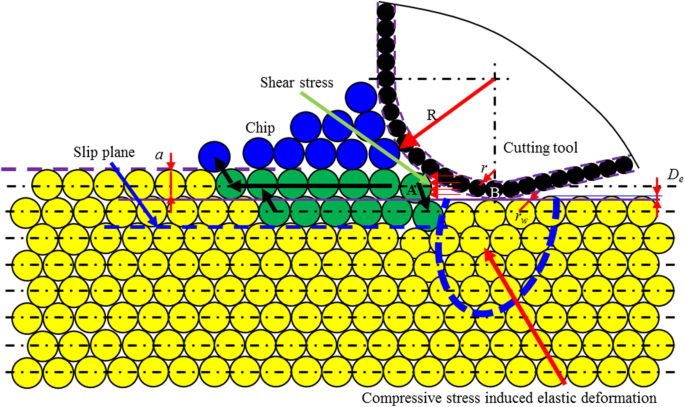
Schematic illustration of cutting-based single atomic layer removal at a/rw larger than C2 , a/R larger than T2 , smaller than T1
As the ratio of a/R decreases to lower than T 2 , there is either no chip formation or extremely small volume of chip formation, but elastic-plastic deformation occurs on the processed surface, as shown in Fig. 19. After workpiece material passes the lowest point of cutting edge, the elastic deformed part springs back. The plastic deformed part (Δ ) leads to lasting deformation. Such ratio is related with material properties, tool geometry and process conditions (case 5).
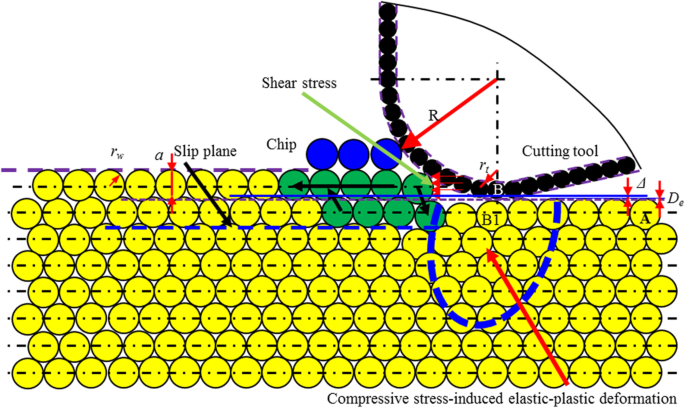
Schematic illustration of cutting-based single atomic layer removal at a/r larger than C2 and a/R lower than T2
Conclusions
In the present study, both of atom sizing effect and cutting-edge radius effect are analysed to investigate their influence on chip formation, surface generation, subsurface deformation, and atomic displacement behaviour during the cutting of monocrystalline copper towards single atomic layer removal. The following conclusions can be drawn.
- 1.
A new model is proposed to describe the underlying material deformation and removal mechanism in the cutting-based single atomic layer removal process, which exhibits four characteristics, including chip formation by dislocation motion, elastic deformation occurring on the processed surface, atomic sizing effect, and cutting-edge radius effect.
- 2.
Both of atomic sizing effect and cutting-edge radius effect have a great influence on the material deformation and removal during the cutting process of monocrystalline copper towards single atomic layer removal. With a specific ratio of cutting depth to workpiece atom radius (a/r w ) and that of cutting depth to edge radius (a/R ), cutting-based single atomic layer removal could be achieved on Cu (111) surface.
- 3.
Chip formation is affected by the ratios of a/r w and a/R . There is a chip formation only when the ratio of a/r w is larger than one critical value (C1) and the ratio of a/R is smaller than one threshold value (T1). Moreover, chip formation is mainly dependent on the shear stress-driven dislocation motion, significantly different from the extrusion-dominated chip formation in nanocutting and shearing-dominated chip formation in conventional machining.
- 4.
Single atomic layer removal can be achieved via layer-by-layer removal and multi-layer removal. The former one refers to that the targeted atomic layer could be either fully removed from workpiece surface. The latter one means that the first atomic layer is partly removed while the remaining materials are pressed into other atomic layers, forming a new processed surface.
- 5.
There is only elastic deformation occurring on the processed surface during ACS cutting process, different from the elastic-plastic deformation in nanocutting. It can be regarded as one characteristic feature in ACS cutting.
- 6.
Depending on the combined effect of atom sizing effect and cutting-edge radius effect, there exist five cases of material deformation and removal processes during the cutting-based single atomic layer removal, i.e., no workpiece material is removed (case 1), workpiece materials are non-continuously removed (case 2), a part of materials is formed into chip while others undergoes material slip via dislocation motion (case 3), a part of materials within the targeted atomic layer is formed into chip while others are extruded into other atomic layers to form new processed surface (case 4), and the elastic deformed part springs back, while the plastic deformed part leads to a lasting deformation (case 5).
Disponibilité des données et des matériaux
Authors declare that the materials, data, and associated protocols are available to the readers, and all the data used for the analysis are included in this article.
Abréviations
- ACS:
-
Atomic and close-to-atomic scale
- ACSM:
-
Atomic and close-to-atomic scale manufacturing
- MD :
-
Dynamique moléculaire
Nanomatériaux
- Technologies avancées de dépôt de couche atomique pour les micro-LED et les VCSEL
- Élimination synergique par adsorption photocatalytique de l'effet magenta basique des nanocomposites AgZnO/polyoxométalates
- Les nanofibres hiérarchiques antibactériennes en polyamide 6-ZnO fabriquées par dépôt de couche atomique et croissance hydrothermale
- Propriétés photocatalytiques des poudres de TiO2 revêtues de Co3O4 préparées par dépôt de couche atomique amélioré par plasma
- Réglage au niveau de Fermi des films ZnO par dépôt de couche atomique supercyclée
- Étude de l'effet de la direction d'impact sur le processus de coupe nanométrique abrasif avec la dynamique moléculaire
- Dépendance de l'épaisseur sur les propriétés interfaciales et électriques dans la couche atomique déposée AlN sur le plan c GaN
- Dépôt de couche atomique amélioré par plasma à basse température de SiO2 à l'aide de dioxyde de carbone
- Coupe à onglet unique par rapport à la scie à onglet double