Nanofabrication de structures périodiques à haute résolution avec un espacement inférieur à 100 nm par polymérisation à deux photons
Résumé
Dans cet article, des approches pour la réalisation de structures périodiques à haute résolution avec des tailles d'écart à une échelle inférieure à 100 nm par polymérisation à deux photons (2PP) sont présentées. L'impact de l'intensité du laser sur la taille des caractéristiques et la qualité de la surface est étudié. L'influence de différents matériaux photosensibles sur la formation de la structure est comparée. Sur la base du caractère géométrique elliptique du voxel, les auteurs présentent une idée pour réaliser des structures à haute résolution avec des tailles de caractéristiques inférieures à 100 nm en contrôlant la position de focalisation du laser par rapport au substrat de verre. Cette enquête porte sur des structures fabriquées respectivement dans le plan le long et perpendiculairement au grand axe du voxel. Les auteurs proposent également une approche utile pour gérer la fabrication de la structure périodique proposée avec une distance périodique de 200 nm et une taille d'intervalle de 65 nm.
Introduction
La demande de réduction d'échelle des appareils augmente rapidement avec les progrès continus de la nanotechnologie ces dernières années. Les structures miniaturisées avec des tailles de caractéristiques inférieures à la limite de diffraction peuvent être appliquées dans divers domaines comme la plasmonique [1], la micro- et nanooptique [2], la nanophotonique [3, 4] et la biomédecine [5, 6]. De plus, les structures avec des dimensions inférieures à la longueur d'onde sont également capables de faciliter les performances de caractérisation à l'échelle micro et nanométrique [7, 8]. Par exemple, les pointes [9] et les nano-antennes [10] peuvent être utilisées pour améliorer les performances de caractérisation des structures à haute résolution en améliorant le confinement de la lumière dans le champ proche, et les réseaux [11] sont capables de transformer les informations optiques du proche. champ au champ lointain.
En ce qui concerne la réalisation de structures à haute résolution, la polymérisation à deux photons (2PP) est couramment utilisée en raison de ses capacités à atteindre une haute résolution et une fabrication 3D [12]. La polymérisation à deux photons est une méthode de fabrication basée sur l'absorption à deux photons (2PA), qui est un processus non linéaire qui permet théoriquement d'atteindre une résolution inférieure à la limite de diffraction. Diverses méthodes basées sur le 2PP, telles que l'ajout d'un photoinitiateur avec une efficacité d'initiation élevée [13], la mise en forme de la phase spatiale du faisceau de désactivation [14], en utilisant des impulsions laser femtosecondes inférieures à 10 fs [15] et 520 nm [16], combinant avec une optique hybride [17] et une lithographie par faisceau optique à sous-diffraction développée [18], ont été appliqués pour réaliser des tailles de caractéristiques à une échelle inférieure à 100 nm. Cependant, ces tailles sont pour la plupart réalisées sur des lignes suspendues ou sur une seule ligne. Il reste toujours difficile de réaliser expérimentalement des tailles de caractéristiques et des tailles d'écart au-delà de la limite de diffraction dans les structures périodiques en raison de l'effet d'échange de diffusion radical dans la région de l'écart lorsque la distance centre à centre entre les caractéristiques adjacentes devient très proche [19]. Néanmoins, quelques stratégies ont été démontrées dans le but d'obtenir des structures périodiques avec une distance d'écart à l'échelle nanométrique. Des cristaux photoniques avec une distance périodique de 400 nm ont été réalisés en ajoutant une molécule d'extincteur dans la résine photosensible [20]. Avec cette approche, la taille de l'espace entre les lignes adjacentes des cristaux photoniques est d'environ 300 nm. De plus, des lignes de réseau avec une distance périodique de 175 nm et une taille d'intervalle de 75 nm ont été obtenues par une technique de lithographie STED [19]. Récemment, il a été présenté qu'un processus de post-traitement thermique simple des échantillons par calcination est capable de réaliser des tailles de caractéristiques jusqu'à environ 85 nm [21]. Les approches ci-dessus ont permis la réalisation de structures périodiques avec des tailles d'intervalle inférieures à la limite de diffraction. Cependant, ils sont assez spéciaux avec un coût plus élevé, des opérations et des procédures plus compliquées par rapport à 2PP.
Dans cet article, une enquête expérimentale sur la réalisation d'un dispositif périodique (Fig. 1) avec à la fois des tailles de caractéristiques et des tailles d'écart inférieurs à la limite de diffraction en utilisant 2PP est réalisée. La structure périodique à haute résolution, composée de lignes de réseau avec des piliers situés périodiquement entre eux, a été proposée pour l'amélioration de la résolution de caractérisation de la diffusion interférométrique à transformée de Fourier (IFTS) [22, 23], qui est une méthode de caractérisation des micro- et nanostructures. Il est connu que la résolution spatiale des structures est principalement déterminée par les matériaux photosensibles, le système optique et les paramètres de traitement [15]. Plus précisément, les chercheurs ont signalé que l'orientation de la polarisation du faisceau laser peut affecter les dimensions de la structure [24]. Lorsqu'un laser est polarisé linéairement parallèlement à sa direction de balayage, une dimension de caractéristique minimale peut être réalisée. Par conséquent, le laser utilisé dans les expériences est équipé d'une polarisation linéaire parallèle à la direction de balayage laser dans le but d'obtenir des tailles de caractéristiques plus petites. Sur la base de cette configuration, l'effet de l'intensité du laser sur la taille des caractéristiques est d'abord étudié. Ensuite, l'influence de différents matériaux photosensibles sur la formation de la structure est comparée. Lorsque le laser écrit directement des structures sur un substrat de verre, seule une partie du voxel polymérise la résine photosensible car l'autre partie du voxel se trouve à l'intérieur du substrat de verre. Bénéficiant de la géométrie elliptique du voxel, une idée de réduction de la taille des caractéristiques et de la taille de l'espace en contrôlant la position de focalisation du laser par rapport au substrat de verre est spécialement présentée. Les tailles des caractéristiques des lignes de réseau (fabriquées dans le plan perpendiculaire au grand axe du voxel) et des piliers (fabriqués dans le plan le long du grand axe du voxel) en fonction des positions de focalisation laser relatives sont respectivement étudiées. En conséquence, des lignes de caillebotis d'une largeur minimale de 78 nm et des piliers d'un diamètre de 110 nm sont réalisés. De plus, la structure proposée avec une superficie de 20×20 μ m, une distance périodique de 200 nm et une taille d'écart de 65 nm est démontrée en fabriquant séparément des lignes de grille et des piliers.
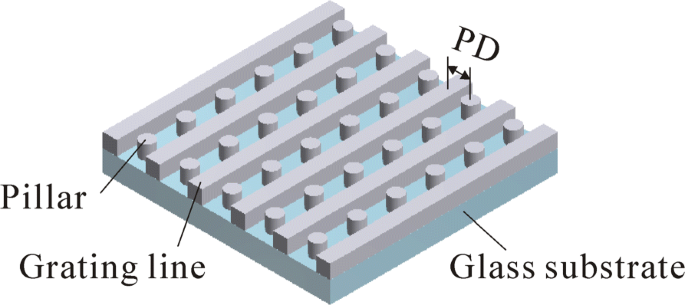
Illustration schématique de la structure périodique proposée. La distance périodique entre les entités adjacentes est représentée par PD
Méthodes
Méthode de fabrication
Les structures présentées dans cet article ont été fabriquées par polymérisation à deux photons. Une illustration schématique de la configuration expérimentale est présentée sur la Fig. 2. Ce système de fabrication 2PP, qui est également disponible dans le commerce [25, 26], est capable de coordonner tous les axes simultanément et d'atteindre la vitesse sur toute la plage de déplacement sans pas à pas ni couture. à une vitesse allant jusqu'à 50 mm/s. Un laser femtoseconde polarisé linéaire avec une sortie doublée en fréquence à 513 nm, une largeur d'impulsion de 60 fs et un taux de répétition de 76 MHz est utilisé. La puissance du laser est contrôlée par une lame demi-onde et un cube séparateur de faisceau polarisant. Des étages de translation à coussin d'air de haute précision avec une plage de déplacement de 15 cm sont également utilisés. Une caméra CCD est montée pour la surveillance en ligne. Le processus de polymérisation peut être surveillé par une caméra CCD en raison de la variation de l'indice de réfraction de la résine photosensible induite par la polymérisation. L'échantillon est constitué d'une gouttelette de matériau photosensible sur le substrat de verre, qui est fixée à la platine de translation avec une résine photosensible sur la face inférieure. Le faisceau laser est focalisé dans la résine photosensible par un objectif de microscope à immersion dans l'huile 100 × avec une ouverture numérique (NA) élevée de 1,4.

Schéma de principe du système de fabrication 2PP
Matériaux
Les performances de différentes résines photosensibles dans la fabrication de structures peuvent être diverses en raison de leurs propres compositions chimiques et propriétés physiques uniques. Dans ce travail, des résines photosensibles appelées matériau hybride sol-gel organique-inorganique Zr [27] et E-shell 300 (Envisiontec) sont appliquées respectivement pour la structuration. Le matériau hybride Zr est un polymère hybride sol-gel organique-inorganique à base de zirconium à haute viscosité qui est bien connu pour son faible retrait et sa grande stabilité pour la fabrication du 2PP. Les procédures de préparation et d'autres propriétés optiques de cette résine photosensible peuvent être trouvées dans la référence [27]. E-shell 300 est une résine photosensible liquide à base de diméthacrylate d'une viscosité de 339,8 MP a·s. Il peut être utilisé pour l'impression 3D et la fabrication d'appareils auditifs et d'appareils médicaux, ainsi que pour des structures à haute résolution, résistance, rigidité et résistance chimique.
Résultats et discussion
Les paramètres de traitement jouent un rôle important dans la détermination de la taille des caractéristiques des structures. Parmi eux, l'intensité du laser est un paramètre capable d'influencer efficacement la formation de la structure et peut être contrôlé avec précision et commodité. Ce paramètre peut être obtenu à l'aide de la formule donnée dans la réf [28]
$$ {I=\frac{2 P T M^{2}}{\pi w_{0}^{2} f\tau}} $$ (1)où P représente la puissance laser moyenne [4, 28], T le coefficient de transmission de l'objectif/système (T =15% [4]), M 2 la qualité du faisceau avec M 2 =1.1, f le taux de redoublement, τ la durée d'impulsion, et w 0 le rayon du point avec \(w_{0}=0.61 \frac {\lambda }{NA}\) (w 0 223,5 nm). Dans cette formule, \(\frac {P}{f}\) et \(\frac {P}{f\tau }\) indiquent respectivement l'énergie par impulsion et la puissance moyenne par impulsion. L'unité d'intensité kW/ μ m 2 est utilisé à la place de TW/cm 2 (1 TW/cm 2 =10 kW/ μ m 2 ) dans le but d'afficher directement la quantité de puissance réellement focalisée dans la zone du spot, qui a également une plage à l'échelle microscopique (\(\pi w_{0}^{2} \approx 0,16\) μ m 2 ). Ici, une enquête sur l'effet de l'intensité du laser sur les dimensions d'une seule ligne a été réalisée. Le matériau hybride Zr et le E-shell 300 ont été appliqués pour l'étude. La largeur et la hauteur de ligne des deux matériaux par rapport à l'intensité laser I est représenté respectivement sur la figure 3a (matériau hybride Zr) et la figure 3b (coque E 300). Une vitesse de 7 μ m/s a été utilisé pour la fabrication. L'intensité laser I est compris entre 0,67 et 0,78 kW/ μ m 2 (avec une plage de puissance laser correspondante de 1,44 à 1,69 mW) pour le matériau hybride Zr et de 0,78 à 1,02 kW/ μ m 2 (plage de puissance laser de 1,69 à 2,20 mW) pour E-shell 300. On peut voir que la taille des caractéristiques (à la fois le diamètre et la hauteur) augmente avec l'augmentation de l'intensité du laser. Dans le cas du matériau hybride Zr (Fig. 3a), avec une intensité laser d'environ 0,67 kW/ μ m 2 , la dimension latérale d'un voxel peut être réduite à environ 115 nm, ce qui est inférieur à la limite de diffraction (la limite de diffraction \(\frac {\lambda }{2NA}=185\) nm). On peut également calculer que le rapport hauteur/largeur (hauteur/largeur) est compris entre 2,5 et 4. Pour E-shell 300 (Fig. 3b), une largeur de ligne de 178 nm a été réalisée lorsque l'intensité laser était de 0,78 kW/μ m 2 . Cette dimension caractéristique est inférieure à la limite de diffraction (185 nm). Sur la base de l'enquête ci-dessus, on peut conclure que les tailles des caractéristiques sont effectivement influencées par l'intensité laser appliquée. Une taille de caractéristique plus petite peut être réalisée en réduisant l'intensité du laser.
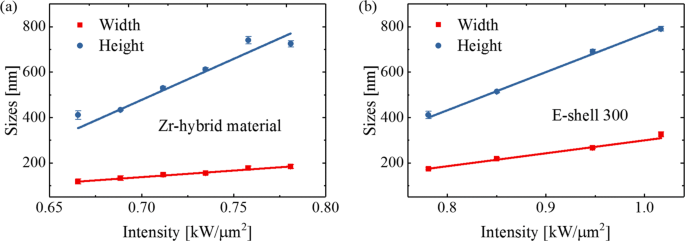
Dimensions de la ligne en fonction de l'intensité laser I . La vitesse utilisée pour la structuration est de 7 μ Mme. Les lignes rouges et bleues sont des résultats d'ajustement linéaire de la largeur et de la hauteur du voxel, respectivement. un La largeur et la hauteur d'une seule ligne en matériau hybride Zr. b La largeur et la hauteur d'une seule ligne en E-shell 300
Influence de différents matériaux sur la formation de la structure par 2PP
Pour l'étude de l'impact des matériaux sur la formation de la structure, diverses lignes de réseau périodiques ont été fabriquées en utilisant les matériaux présentés dans la section « Matériaux ». Une vitesse d'écriture de 7 μ m/s a été appliqué. Les figures 4a et b sont respectivement les images SEM de lignes de réseau périodiques en matériau hybride Zr et E-shell 300 avec la distance périodique (PD , illustré à la Fig. 1) de 1 μ m. L'intensité laser appliquée pour la fabrication était de 1,25 kW/ μ m 2 (correspondant à une puissance laser de 2,7 mW) pour le matériau hybride Zr et 1,02 kW/ μ m 2 (correspondant à une puissance laser de 2,2 mW) pour E-shell 300. On peut voir que les lignes de réseau constituées des deux matériaux sont lisses. Les figures 4c et d indiquent les images SEM de lignes de réseau périodiques en matériau hybride Zr et E-shell 300 avec P D =400 nm, respectivement. Avec la diminution de la distance périodique, l'intensité laser utilisée pour la fabrication est également réduite afin d'atteindre une résolution élevée et d'éviter simultanément la surpolymérisation à l'intérieur de l'espace entre les éléments adjacents. Dans cette enquête, intensité laser de 0,69 kW/ μ m 2 a été appliqué pour la fabrication avec les deux matériaux. Avec la PD réduite , les lignes de caillebotis en matériau hybride Zr sont granuleuses (Fig. 4c), tandis que celles en E-shell 300 ont moins de rugosité (Fig. 4d). La granulation des lignes de réseau en matériau hybride Zr peut résulter d'une polymérisation instable, qui se produit en raison de la proximité de la puissance laser réduite du seuil de polymérisation du matériau. Cette comparaison révèle que l'E-shell 300 est plus adapté à la fabrication de structures avec une distance périodique à l'échelle nanométrique. De plus, toutes les structures observées au MEB sont déposées avec une couche d'or de 20 nm d'épaisseur.
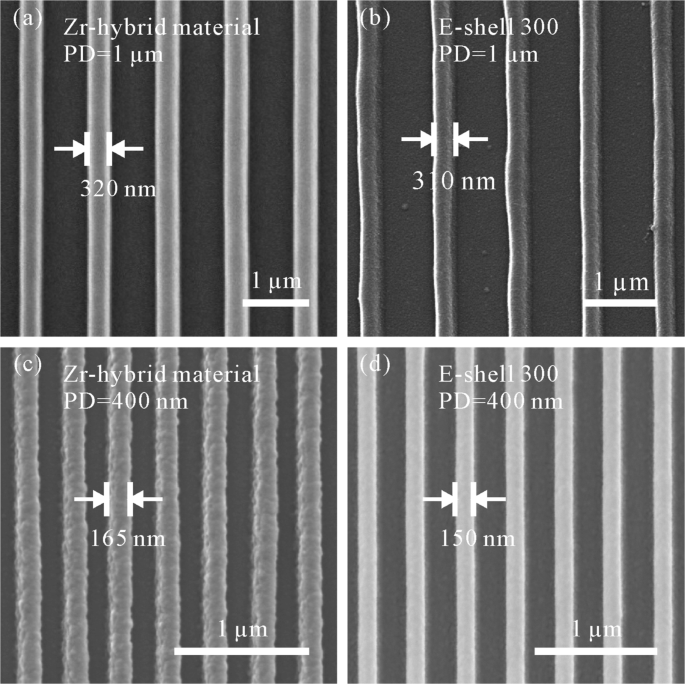
Images SEM de lignes de caillebotis fabriquées avec différents matériaux. La vitesse de fabrication est de 7 μ Mme. un Matériau :matériau hybride Zr ; P D =1 μ m; Intensité laser :1,25 kW/μ m 2 . b Matériel :E-shell 300; P D =1 μ m; Intensité laser :1,02 kW/μ m 2 . c Matériau :matériau hybride Zr ; P D =400 nm; Intensité laser :0,69 kW/ μ m 2 . d Matériel :E-shell 300; P D =400 nm; Intensité laser :0,69 kW/ μ m 2
Enquête sur la formation de la structure par rapport à la position de mise au point du laser
Pour placer les nanostructures sur la surface du substrat de verre, le faisceau laser doit être focalisé à l'interface substrat/photoréserve pendant le processus 2PP. Ainsi, seule une partie du voxel est capable d'initier la polymérisation de la résine photosensible. L'autre partie du voxel est en substrat de verre pour assurer l'adhérence des structures. Puisque la géométrie du voxel est elliptique, une variation de la taille de sa section transversale existe le long du grand axe. Dans la micro- et nanofabrication haute résolution, la variation de la taille de la section transversale des voxels à l'interface du substrat et de la résine photosensible est très préoccupante car elle affecte la formation de la structure ainsi que la taille de ses caractéristiques.
La figure 5 est une illustration schématique du réglage de la mise au point laser le long de z direction. La position à l'interface entre la résine photosensible et le substrat est définie comme une position de mise au point de référence z 0 (Fig. 5a). Étant donné que la gouttelette de résine photosensible se trouve sur la face inférieure du substrat de verre, le point de focalisation laser se déplace vers le bas à partir de la position de référence z 0 dans la résine photosensible. La distance entre la position de mise au point laser actuelle z et la position de référence z 0 est représenté par Δz =∣z −z 0 . La région indiquée en vert foncé sur les figures 5b et c représente la région de focalisation laser à l'intérieur de la résine photosensible, qui permet la polymérisation avec une intensité lumineuse supérieure au seuil de polymérisation. Différentes tailles de caractéristiques peuvent être réalisées en plaçant la mise au point laser à différents z postes. Taille de la caractéristique w est caractérisé par la largeur moyenne à mi-hauteur (FWHM, Fig. 5c) des éléments qui sont fabriqués au même z position dans un tableau.
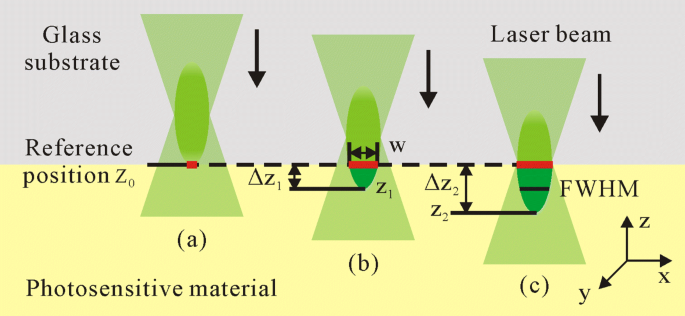
Illustration de la variation de la position du foyer laser le long de z sens
Des lignes de réseau périodiques fabriquées avec différentes positions de focalisation laser ont été obtenues comme le montre la figure 6. La distance périodique (PD ) entre les lignes du réseau est 1 μ m. Avec cette étroite PD , les éléments adjacents commencent à se connecter les uns aux autres par une polymérisation supplémentaire dans la région de l'espace lorsque le laser est focalisé avec Δ z =500 nm (Fig. 6a). Les amas hors des lignes de réseau résultent d'une polymérisation supplémentaire. Au cours du processus 2PP, des radicaux libres sont générés par le clivage de liaison induit par laser dans les molécules photoinitiatrices. Ces radicaux s'accumulent dans les petits espaces entre les éléments adjacents, ce qui entraîne une augmentation de la concentration en radicaux. Cette concentration radicalaire élevée peut dépasser le seuil de polymérisation et ainsi conduire à une polymérisation non souhaitée. De plus, il peut également en résulter une adhésion instable des structures polymérisées au substrat. Dans ce cas, les structures peuvent être facilement emportées pendant le processus de développement. Lorsque le foyer du faisceau laser est plus à l'intérieur du substrat, moins de photoréserve est polymérisée. Comme présenté sur la figure 6b, des lignes de réseau d'une largeur de 78 nm ont été obtenues dans ce cas. Cependant, une faible visibilité de la structure peut également être observée. Par conséquent, il est d'une grande importance d'avoir une position de focalisation laser appropriée pendant le processus de polymérisation non seulement pour une résolution plus élevée mais aussi pour une meilleure adhérence de la structure au substrat.
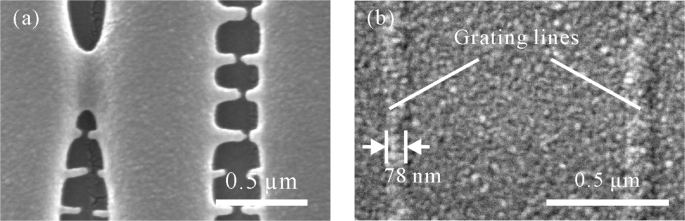
L'influence des positions de focalisation du laser sur la formation de la structure. Matériel :E-shell 300. a Lignes de réseau verticales fabriquées avec une mise au point laser plus à l'intérieur de la résine photosensible. L'intensité laser pour la fabrication I =0,71 kW/ μ m 2 (correspondant à la puissance laser de 1,55 mW), la distance focale relative du laser Δ z =500 nm. Une polymérisation supplémentaire entre les caractéristiques est générée et les caractéristiques adjacentes sont connectées. b Lignes de réseau verticales fabriquées avec une focalisation laser plus à l'intérieur du substrat. L'intensité laser pour la fabrication I =0.65 kW/ μ m 2 (correspondant à une puissance laser de 1,4 mW), la position relative du foyer laser Δ z =0 nm
Quant à l'influence de la position de mise au point du laser sur la taille des caractéristiques, une enquête sur son effet sur les lignes de réseau qui sont fabriquées dans le x −y avion a été effectué. En augmentant la distance relative Δz , des lignes de réseau fabriquées sous différentes positions de focalisation laser ont été obtenues. La largeur mesurée des lignes de grille w l en fonction des positions relatives des foyers laser est tracé comme les points présentés sur la figure 7a. L'intensité laser utilisée pour la fabrication est de 0,85 kW/ μ m 2 (correspondant à une puissance laser de 1,84 mW). La courbe rouge indique un résultat d'ajustement elliptique dans lequel le grand axe est cohérent avec z axe. L'ellipse correspondante a été reconstruite (voir le coin inférieur droit de la Fig. 7a) en utilisant la formule elliptique \(\left (\frac {x}{a}\right)^{2}+\left (\frac {400-y }{b}\right)^{2}=1\), où (400,0) est le centre de l'ellipse, b =90 est l'axe semi-mineur, a =5.65b est le demi-grand axe, x représente la distance relative Δz le long du grand axe, et y représente la moitié de la taille de mise au point L qui est le long du petit axe. Le résultat révèle que la largeur de la ligne suit avec la taille de la section transversale du foyer laser qui change le long du grand axe de la géométrie elliptique du voxel. Lorsque la position relative Δz =50 nm, lignes de réseau avec une taille de caractéristique de w l =130 nm ont été réalisés (Fig. 7b). De plus, en réduisant l'intensité du laser, les lignes de réseau avec w l =100 nm ont été obtenus à la même position de focalisation laser que celle présentée sur la figure 7c.
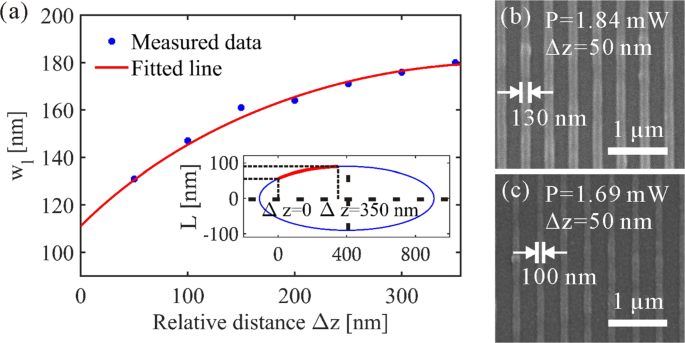
Lignes de caillebotis fabriquées au x −y plan par rapport à différentes distances focales relatives du laser Δz . Matériel :E-shell 300. Une vitesse d'écriture de 7 μ m/s a été appliqué. un Largeur de ligne mesurée et courbe ajustée par rapport à différents Δz . La figure dans le coin inférieur droit est une reconstruction de l'ellipse correspondant à la ligne ajustée. b Lignes de réseau fabriquées avec l'intensité laser de I =0,85 kW/ μ m 2 (avec la puissance laser P =1,84 mW). La distance focale relative du laser est Δz =50 nm. c Lignes de réseau fabriquées avec l'intensité laser de I =0,78 kW/ μ m 2 (avec la puissance laser P =1,69 mW). La distance focale relative du laser est Δz =50 nm
L'influence de la position du foyer laser sur la taille des caractéristiques des piliers a également été étudiée. Les piliers sont réalisés en déplaçant la tache focale orthogonalement au plan du substrat, qui est dans le plan du grand axe du voxel (x −z ou y −z avion). Un seul pilier a été fabriqué en déplaçant le faisceau laser le long de z direction avec une distance de 1 μ m. La figure 8a est l'image SEM de piliers fabriqués avec différentes intensités laser et distances relatives Δz . La distance entre les centres des piliers adjacents est de 400 nm le long de x direction et 500 nm le long de y direction. L'intensité du laser a été augmentée de gauche à droite avec un pas d'environ 0,23 kW/ μ m 2 (correspondant à une puissance laser de 0,5 mW). La distance relative entre la position de mise au point laser z et la position de référence z 0 a été augmenté de bas en haut le long de la direction verticale. La figure 8b montre les diamètres de pilier mesurés w p concernant l'intensité laser et la distance relative Δz . Le diamètre d'un pilier w p est obtenu en mesurant sa FWHM. L'intensité du laser est comprise entre 0,74 et 0,96 kW/ μ m 2 . On peut observer que w p est réduit avec la diminution des deux Δz et l'intensité du laser. Quand Δz =150 nm, un pilier de diamètre w p ≈110 nm a été atteint avec une plage d'intensité laser relativement large (0,74-0,81 kW/ μ m 2 ). Et il existe également une fenêtre relativement stable pour les tailles de piliers lorsqu'un réseau de piliers est fabriqué, comme le montre la figure 8c-d, qui correspond aux images SEM d'un réseau de piliers fabriqué avec l'intensité laser de I =0,74 kW/ μ m 2 et une distance relative de Δz =300 nm. Le rapport hauteur/largeur du pilier est d'environ 2. Cela indique que la reproductibilité du pilier fonctionne très bien.
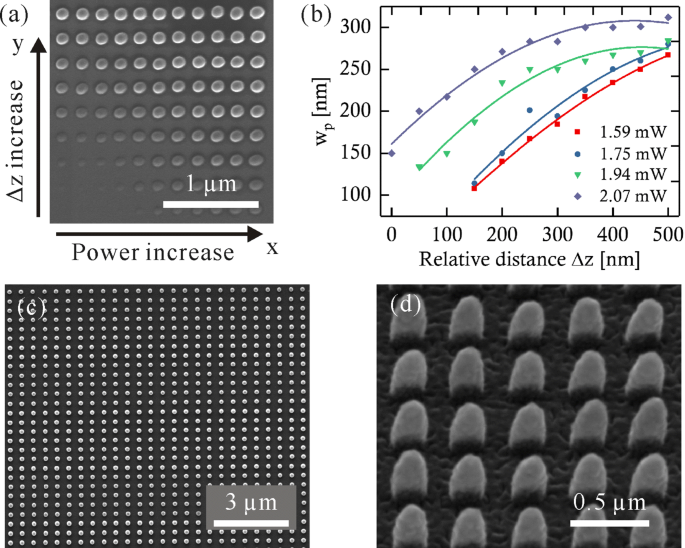
Réseaux de piliers fabriqués avec différentes intensités laser et distance relative de focalisation laser Δz . Matériel :E-shell 300. a Image SEM de piliers fabriqués avec différentes intensités laser et positions de focalisation laser relatives. b Diamètre des piliers mesuré w p par rapport à l'intensité laser I et la distance relative Δz . L'intensité laser est respectivement de 0,74 kW/ μ m 2 , 0,81 kW/ μ m 2 , 0,90 kW/ μ m 2 , et 0,96 kW/ μ m 2 avec la correspondance de la puissance laser 1,59 mW, 1,75 mW, 1,94 mW et 2,07 mW. c Vue de dessus du réseau de piliers. d Image SEM du réseau de piliers vue avec 45 ∘
Fabrication de structures périodiques avec les tailles de caractéristiques et la taille de l'espace en dessous de la limite de diffraction
Sur la base des enquêtes respectives sur les tailles des caractéristiques des lignes de réseau périodiques (fabriquées à x −y plan) et des piliers, la structure périodique à haute résolution proposée composée de lignes de grille et de piliers a été fabriquée. Sa taille est de 20×20 μ m avec une distance périodique de 200 nm entre le centre de la ligne de réseau et le pilier. Dans ce travail, la stratégie consistant à réaliser des structures à haute résolution avec une distance périodique de 200 nm en fabriquant séparément des lignes de réseau et des piliers est mise en avant. Dans ce cas, la distance périodique PD entre les lignes de grille adjacentes et les piliers adjacents est de 400 nm. Au cours du processus de polymérisation, une région d'espacement plus grande existe entre les éléments lorsque les lignes de réseau et les piliers sont fabriqués séparément. Cette région d'espacement temporairement élargie permet de réduire l'accumulation de radicaux, ce qui pourrait conduire à la polymérisation indésirable dans la région d'espacement. Il faut noter que la position de focalisation du laser doit également être ajustée pendant le processus de fabrication. Les structures fabriquées avec une position de focalisation laser incorrecte sont présentées sur les figures 9a et b. On peut voir que les lignes et les piliers sont connectés lorsque la focalisation laser est trop à l'intérieur de la résine photosensible. Les figures 9c–f sont les images MEB de structures avec un foyer laser bien positionné [23]. En plaçant correctement la position de mise au point du laser et en utilisant la stratégie de fabrication fournie ci-dessus, une structure avec des dimensions inférieures à la limite de diffraction (une largeur de ligne de 110 nm, un diamètre de pilier de 135 nm et une taille d'écart de 65 nm) a été réalisée comme indiqué dans 9e.
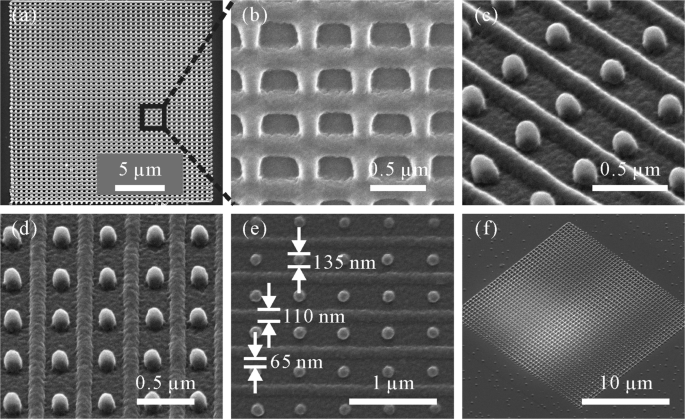
Images SEM d'une structure périodique fabriquée en 2PP avec P D =200 nm. Matière :E-shell 300. Intensité utilisée pour la fabrication des lignes de caillebotis :I =0.83 kW/ μ m 2 ; piliers :Je =0.6 kW/ μ m 2 . La distance focale relative du laser pour la fabrication de lignes et de piliers de réseau est de 300 nm. un –b Structures périodiques fabriquées avec réglage de la position de mise au point laser à l'intérieur de la résine photosensible. c –d Images SEM de structures périodiques avec une position de focalisation laser appropriée. e Vue de dessus de la structure fabriquée avec une position de mise au point laser appropriée. f Image SEM de l'ensemble du tableau
Conclusion
En conclusion, nous avons comparé l'influence de différentes résines photosensibles et paramètres de traitement sur la formation de la structure et présenté le moyen d'améliorer la résolution spatiale et de réduire la taille de l'écart entre les caractéristiques adjacentes en contrôlant la position du foyer laser le long de z direction. L'E-shell 300 s'est avéré expérimentalement être un matériau plus approprié pour la fabrication de structures avec une résolution spatiale inférieure à 200 nm. Nous avons également réussi à obtenir une structure périodique avec une taille d'intervalle de 65 nm et une taille de caractéristique de 110 nm. Les tailles sont bien en dessous de la limite de diffraction d'Abbe. L'enquête plus approfondie sur les performances optiques (par exemple, l'amélioration du signal des images optiques) de cette structure à haute résolution sera intéressante.
Abréviations
- 2PA :
-
Absorption à deux photons
- 2PP :
-
Polymérisation à deux photons
- FWHM :
-
Pleine largeur moitié maximum
- IFTS :
-
Diffusion interférométrique à transformée de Fourier
- NA :
-
Ouverture numérique
- PD :
-
Distance périodique
- SEM :
-
Microscope électronique à balayage
Nanomatériaux
- Structures de support pour l'impression 3D avec du métal — une approche plus simple
- DATA MODUL étend la gamme de capteurs tactiles avec des tailles encore plus grandes
- Apprentissage non supervisé avec des neurones artificiels
- Pionniers de l'AFM récompensés par le prix Kavli
- En accord avec le cœur d'un atome de cuivre
- Modification des perceptions de l'ingénierie :Combler le fossé des compétences grâce à l'ingénierie automatisée
- Tailles plus petites, coût plus élevé :que se passe-t-il avec la rétraction ?
- Gap Inc. accélère les opérations d'entrepôt avec la robotique et l'IA
- Optimisez la production avec la bonne taille d'excavatrice