Contrôler la morphologie de surface secondaire des nanofibres PVDF électrofilées en régulant le solvant et l'humidité relative
Résumé
Ce travail présente une méthode simple et fiable pour générer directement des nanofibres de fluorure de polyvinylidène (PVDF) avec une morphologie de surface secondaire (p. Nous avons clarifié les mécanismes responsables de la formation de ces morphologies en explorant systématiquement les interactions moléculaires entre le polymère, le(s) solvant(s) et la vapeur d'eau. Nos résultats ont prouvé que la formation d'une morphologie de surface secondaire nécessitait la présence de vapeur d'eau, un non-solvant du polymère, à un niveau approprié d'humidité relative. La formation de la morphologie de surface secondaire était dépendante de la vitesse d'évaporation du ou des solvant(s) (ACE, DMF et leurs mélanges), ainsi que de l'inter-diffusion et de la pénétration du non-solvant (eau) et du(des) solvant(s) ). Les résultats de N2 les isothermes physiques d'adsorption-désorption ont montré que les fibres macroporeuses (> 300 nm) présentaient la surface spécifique la plus élevée de 23,31 ± 4,30 m 2 /g et volume de pores de 0,0695 ± 0,007 cm 3 /g, permettant des capacités d'absorption d'huile élevées de 50,58 ± 5,47 g/g, 37,74 ± 4,33 g/g et 23,96 ± 2,68 g/g pour l'huile de silicone, l'huile de moteur et l'huile d'olive, respectivement. Nous pensons que ce travail peut servir de lignes directrices pour la formation de différentes structures de nanofibres macroporeuses, rugueuses et rainurées avec une porosité intérieure par électrofilage.
Contexte
L'électrofilage est une méthode de formation de fibres qui implique des forces électrostatiques pour éjecter et étirer des jets de polymère dans les fibres. Le procédé produit actuellement des fibres d'un diamètre allant de quelques nanomètres à plusieurs micromètres [1]. Différentes morphologies de fibres électrofilées, y compris les fibres perlées [2], les fibres poreuses [3], les fibres à rainures [4], les fibres multicanaux [5], les fibres en ruban [6], les fibres côte à côte [7], les fibres creuses [8 ], des fibres hiérarchiques [9], des nanocomposites en forme de grains de riz [10], des fibres d'ailes de papillon [11], des fibres cœur-gaine [12] et des fibres frisées [13] peuvent être formés en contrôlant les paramètres d'électrofilage [14].
Les nanofibres électrofilées ont montré d'excellentes propriétés telles qu'une surface spécifique élevée, une flexibilité, une facilité de fonctionnalité, une variété de morphologie et de structure, une résistance directionnelle supérieure et une porosité élevée, ce qui en fait une forme de matériau préférée pour différentes applications telles que la récupération d'énergie [15], capteurs [16], filtration [17,18,19], applications biomédicales [20], surfaces autonettoyantes [21,22,23], etc. Des études ont démontré qu'en régulant les morphologies secondaires (p. surfaces, surfaces rugueuses et porosité intérieure) des fibres électrofilées, leurs propriétés et leur comportement pourraient être considérablement améliorés ou modifiés. Par exemple, les fibres poreuses ont été largement utilisées dans une grande variété d'applications telles que la catalyse, la filtration et la recherche biomédicale en raison de l'augmentation de leurs surfaces spécifiques grâce à l'introduction de pores intrafibres [24]. Des fibres rugueuses ont été utilisées pour améliorer le rendement électrique des dispositifs d'énergie de balayage en raison de l'augmentation des zones de friction [25]. Les fibres rainurées ont présenté un grand potentiel dans le domaine de l'ingénierie tissulaire et des surfaces superhydrophobes [26]. De plus, l'augmentation de la surface spécifique et de la porosité conduit à l'amélioration des performances d'absorption [27, 28], de catalyse [29, 30], etc.
Auparavant, nous avons signalé la production de fibres de polystyrène avec des structures et des distributions de macropores accordables en utilisant une buse microfluidique contenant trois canaux qui permet le mélange de liquide à partir de deux canaux d'entrée et l'électrofilage synchronisé du mélange résultant de l'autre canal de sortie [3] . En outre, nous avons rapporté la fabrication de fibres d'acétate de butyrate de cellulose et de polystyrène avec une structure rainurée par électrofilage à l'aide d'un système de solvants mixtes composé d'un solvant à point d'ébullition élevé et d'un solvant à bas point d'ébullition [4, 31].
Dans cette étude, nous démontrons la fabrication de nanofibres de fluorure de polyvinylidène (PVDF) avec les structures de surface macroporeuses, rugueuses et rainurées et les pores intérieurs en utilisant l'électrofilage sans impliquer de méthode de collecte spéciale ou de traitement post-filage. Ici, le PVDF a été choisi comme modèle car il peut être dissous dans différents solvants.
À notre connaissance, jusqu'à présent, aucune étude n'a été systématiquement étudiée pour manœuvrer la formation de nanofibres de PVDF électrofilées macroporeuses (> 300 nm), rugueuses et rainurées avec une porosité interne en contrôlant l'humidité relative. Ici, nous avons rapporté l'électrofilage de solutions PVDF à quatre niveaux d'humidité relative (5 %, 25 %, 45 % et 65 %) en utilisant à la fois des systèmes de solvants simples et binaires. L'objectif principal de ce travail est d'étudier la faisabilité de la fabrication de fibres macroporeuses, rugueuses et rainurées avec des structures intérieures solides et poreuses en utilisant différents niveaux d'humidité relative, et de découvrir leurs mécanismes de formation. En étudiant systématiquement l'effet de l'humidité relative sur la morphologie de surface secondaire des fibres PVDF électrofilées, nous avons conclu que l'humidité relative joue un rôle important dans la détermination de la surface et de la morphologie interne des fibres PVDF. Cette étude peut fournir des directives utiles pour la préparation de la structure de surface secondaire des nanofibres par électrofilage.
Méthodes
Produits chimiques et matériaux
Les pastilles de PVDF (Mw =275 000) ont été achetées chez Sigma-Aldrich, Inc. L'acétone (ACE) et le N,N-diméthylformamide (DMF) ont été achetés chez Shanghai Chemical Reagents Co., Ltd., Shanghai, Chine. Tous les matériaux ont été utilisés sans autre purification.
Électrofilage de fibres PVDF avec morphologie de surface secondaire
Afin d'obtenir des fibres macroporeuses, rugueuses et rainurées, 18% d'ACE (w /v ) Solution PVDF, 35% DMF (w /v ) solution PVDF, et 25 % (ACE/DMF) (w /v ) Des solutions de PVDF aux ratios de solvants de (4:1, 2:1, 1:1, 1:2 et 1:4) ont été préparées, respectivement, et chaque solution a été chargée dans une seringue en plastique. Dans ce travail, le rapport de solvant était le rapport volumique et la concentration de la solution était poids/volume (w /v ) (g/ml). Une aiguille de seringue de calibre 21 a été utilisée comme filière, qui a été fixée sur une pompe à seringue (KDS 100, KD Scientific Inc., États-Unis) connectée à un fournisseur de haute tension (Tianjin Dongwen Co., Ltd., Chine). Un tambour collecteur mis à la terre (40 cm de longueur et 20 cm de diamètre) a été placé à 18 cm de la filière, et la vitesse de rotation a été réglée à 2 tr/min pour obtenir des fibres orientées de manière aléatoire. Toutes les expériences ont été réalisées à 20 °C sous différents niveaux d'humidité relative (5 %, 25 %, 45 % et 65 %). La température était ajustée par le système de climatisation central du laboratoire et l'humidité relative était contrôlée par l'humidité environnementale, qui pouvait encore être réglée avec une fenêtre étroite (± 2%) en utilisant un humidificateur/déshumidificateur. Tous les échantillons ont été préparés à un taux d'alimentation et une tension appliquée de 1,5 ml/h et 18 kV, respectivement. Tous les paramètres précédents ont été ajustés pour obtenir des fibres de morphologies différentes et de diamètres similaires.
Diagramme de phase ternaire
Les courbes de point de trouble ont été déterminées par la méthode de titrage à une humidité relative de 65 %. Des solutions de PVDF ont été préparées en dissolvant le polymère dans les systèmes à solvant unique en utilisant ACE et DMF, et des systèmes de solvants binaires en utilisant ACE/DMF à un rapport de solvant de 1:1. Les solutions homogènes acquises ont été titrées avec de l'eau désionisée comme non-solvant. Au début de la turbidité permanente, la composition des solutions et la quantité de non-solvant utilisée ont été notées et tracées dans le diagramme de phase ternaire, qui a été utilisé pour représenter les courbes binodales [32, 33].
Caractérisation
La morphologie de surface et la section transversale des nanofibres de PVDF électrofilées ont été vérifiées au microscope électronique à balayage à émission de champ (FE-SEM) (S-4800, Hitachi Ltd., Tokyo, Japon) après revêtement en or. Des coupes transversales des fibres ont été préparées en les plaçant dans de l'azote liquide et en les cassant manuellement. Le diamètre des fibres a été mesuré à l'aide d'un logiciel d'analyse d'images (Adobe Acrobat X Pro 10.1.2.45) selon les images SEM. N2 des isothermes physiques d'adsorption-désorption (JW-BK132F, Beijing Science and Technology Co., Chine) ont été mesurés pour déterminer la surface spécifique, la distribution des pores et le volume total des pores.
Absorption d'huile
La capacité d'absorption d'huile a été mesurée à 25°C en utilisant la méthode suivante. Ensuite, 15 ml de mélange eau-huile avec un rapport de 1:1 ont été préparés et placés dans un bécher. En outre, 0,3 g du sorbant a été ajouté au bécher pour absorber l'huile pendant 1 h, puis le sorbant humide a été déplacé vers un tamis et égoutté pendant ~ 40 min pour s'assurer qu'aucune goutte d'huile ne reste sur le sorbant. La capacité d'absorption d'huile a été calculée selon l'équation suivante :
$$ Q\kern0.5em =\kern0.5em \frac{m_0-{m}_1}{m_1} $$où Q est la capacité d'absorption d'huile (g/g), m 0 est la masse totale du sorbant humide après absorption d'huile drainée pendant ~ 40 min (g), et m 1 est la masse du sorbant avant absorption (g).
Résultats et discussion
Pour explorer l'effet de l'humidité relative sur la morphologie secondaire des fibres PVDF électrofilées, 18 % (w /v ) Solution PVDF avec ACE, 35 % (w /v ) Solution PVDF avec DMF, et 25% (w /v ) Des solutions PVDF avec différents rapports ACE/DMF ont été électrofilées.
Fibres électrofilées d'ACE
Les fibres obtenues à partir d'une solution PVDF/ACE à différents niveaux d'humidité relative ont été exposées et comparées (Figs. 1 et 2). Des fibres lisses ont été formées à l'aide d'une solution PVDF/ACE à une humidité relative de 5 % (Fig. 1a et fichier supplémentaire 1 :Figure S1A), tandis que des fibres macroporeuses ont été produites à une humidité relative de 25 %, 45 % et 65 %. (Fig. 1b–d et fichier supplémentaire 1 :Figure S1B-D). La formation de pores de surface doit être attribuée à la séparation de phases induite par la chaleur (TIPS) [24].
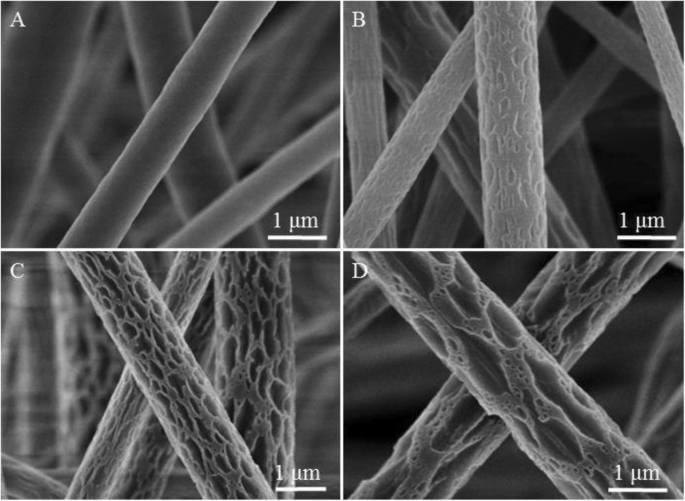
Images SEM représentatives d'échantillons fabriqués par électrofilage 18% (w /v ) Solution PVDF d'ACE à différents niveaux d'humidité relative. un 5%, b 25 %, c 45%, et d 65%
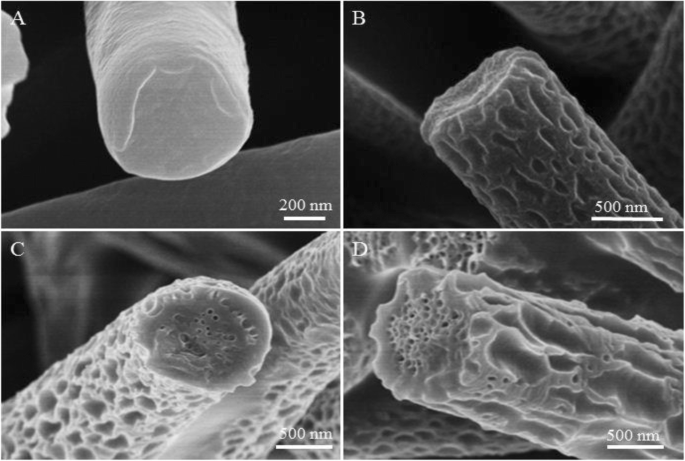
Images SEM en coupe d'échantillons fabriqués par électrofilage 15 % (w /v ) Solution PVDF d'ACE à différents niveaux d'humidité relative. un 5%, b 25 %, c 45%, et d 65%
Pour confirmer le mécanisme de formation des fibres macroporeuses de PVDF formées à partir d'une solution de PVDF/ACE, nous avons vérifié la section transversale des fibres formées à différents niveaux d'humidité relative étudiée. Nous avons constaté qu'à une humidité relative de 5% et 25%, les fibres formées avaient un intérieur solide (Fig. 2a, b), tandis que les fibres avec des pores intérieurs se formaient à une humidité relative de 45% et 65% (Fig. 2c, ré). Ainsi, nous pouvons conclure que les fibres se sont formées avec une surface lisse et un intérieur solide à une humidité relative de 5% en raison de l'absence de séparation de phases. Alors que des fibres macroporeuses avec un intérieur solide se sont formées en raison des TIPS. Alors que des fibres macroporeuses avec des pores intérieurs se sont formées à une humidité relative de 45% et 65% en raison de la coexistence à la fois du TIPS et de la séparation de phase induite par la vapeur (VIPS). En d'autres termes, lorsque les solvants hautement volatils se sont évaporés, ils ont absorbé une grande quantité de chaleur et ont ainsi refroidi la surface des fibres, ce qui les a amenées à se condenser et à attirer des gouttelettes d'eau à la surface des fibres. Lorsque l'humidité relative augmentait, le taux d'évaporation des gouttelettes d'eau diminuait, entraînant une coalescence entre les gouttelettes formées de macro-gouttelettes dont le mécanisme est connu sous le nom de croissance par nucléation (NG) [34]. Une fois que les macro gouttelettes d'eau condensées ont séché, elles ont formé des macropores à la surface des fibres. Alors que la partie des gouttelettes d'eau qui a pénétré dans la fibre a finalement séché pour former des pores intérieurs. Le mécanisme de formation des fibres macroporeuses à une humidité relative élevée est démontré sur la figure 3a. À une humidité relative élevée, le taux d'évaporation des gouttelettes d'eau condensées à la surface des fibres diminuait, donnant à ces gouttelettes plus de temps pour fusionner en raison du NG. Par conséquent, la taille des macropores à la surface des fibres est passée de ~ 50 nm à une humidité relative de 25 %, à ~ 100 nm à une humidité relative de 45 % et à ~ 400 nm à une humidité relative de 65 %. . Toutes les surfaces et morphologies internes obtenues à partir de la solution PVDF/ACE à différents niveaux d'humidité relative sont résumées dans le tableau 1. Il est important de noter que l'augmentation de l'humidité relative de 5 à 65 % entraîne une augmentation du diamètre des fibres de ~ 0,77 à ~ 1,81 μm (supplémentaire fichier 1 :Figure S2A).
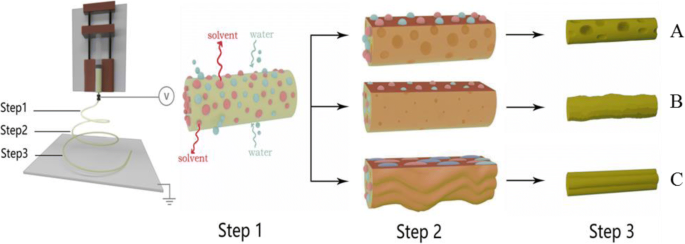
Diagrammes de processus du jet de solution pendant l'électrofilage à une humidité relative élevée. Étape 1 :l'évaporation du solvant et condensation de l'eau, étape 2 :la pénétration des gouttelettes d'eau et génération de pores, et étape 3 :allongement et solidification des fibres. un Fibres macroporeuses, b fibres rugueuses, et c fibres rainurées
Fibres électrofilées à partir de DMF
Ici, 35 % (w /v ) La solution de PVDF a été électrofilée à différents niveaux d'humidité relative (5 %, 25 %, 45 % et 65 %).
Des fibres lisses ont été produites à l'aide d'une solution PVDF/DMF à une humidité relative de 5 % (Fig. 4a et fichier supplémentaire 1 :Figure S3A), tandis que des fibres rugueuses ont été formées à une humidité relative de 25 %, 45 % et 65 % (Fig. . 4b–d et fichier supplémentaire 1 :Figure S3B-D) en raison de l'instabilité de flambement [35] et de l'étirement par force électrique [26]. Selon la section transversale des fibres formées à l'humidité relative précédente étudiée, nous avons trouvé que les fibres à intérieur solide n'étaient obtenues qu'à l'humidité relative de 5% (Fig. 5a), tandis que les fibres à pores intérieurs se formaient à l'humidité relative de 25 %, 45 % et 65 % (Fig. 5b–d). Dans ce cas, on peut dire que les fibres se sont formées avec une surface lisse et un intérieur solide en raison de l'absence de séparation de phases, tandis que les fibres obtenues avec une surface rugueuse et des pores intérieurs en raison du VIPS [24]. En d'autres termes, la diffusion et la pénétration corporatives du DMF et des vapeurs d'eau ont joué un rôle essentiel dans la formation de fibres à pores intérieurs; du fait que la pression de vapeur de l'eau (2,34 kPa) est supérieure à celle du DMF (0,36 kPa) à la température de 20 °C, il est raisonnable de supposer que la vapeur d'eau a saturé la région voisine de l'interface entre l'air et le jet d'abord, puis suivi de son action de non-solvant pour précipiter une gaine de PVDF à la surface du jet liquide. La couche de PVDF solidifié a permis de piéger le DMF à l'intérieur et de ralentir son taux d'évaporation, ce qui a peut-être empêché la vapeur d'eau de se condenser rapidement ou de s'accumuler à la surface pour former de grosses gouttelettes. La vapeur d'eau a pénétré la gaine et est constamment entrée dans la phase PVDF-DMF, entraînant une séparation de phase rapide. La figure 3d éclaire le mécanisme de formation des fibres rugueuses à une humidité relative élevée. Toutes les surfaces et morphologies internes obtenues à partir d'une solution PVDF/DMF à différents niveaux d'humidité relative sont résumées dans le tableau 1. Fait intéressant, l'augmentation de l'humidité relative de 5 à 65 % entraîne une augmentation du diamètre des fibres de ~ 0,8 à ~ 1,79 μm (Fichier 1 supplémentaire :Figure S2B).
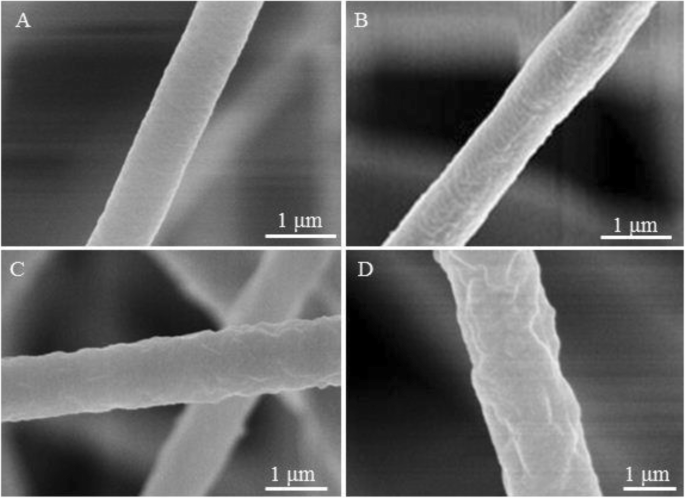
Images SEM représentatives d'échantillons fabriqués par électrofilage 35 % (w /v ) Solution PVDF de DMF à différents niveaux d'humidité relative. un 5%, b 25 %, c 45%, et d 65%
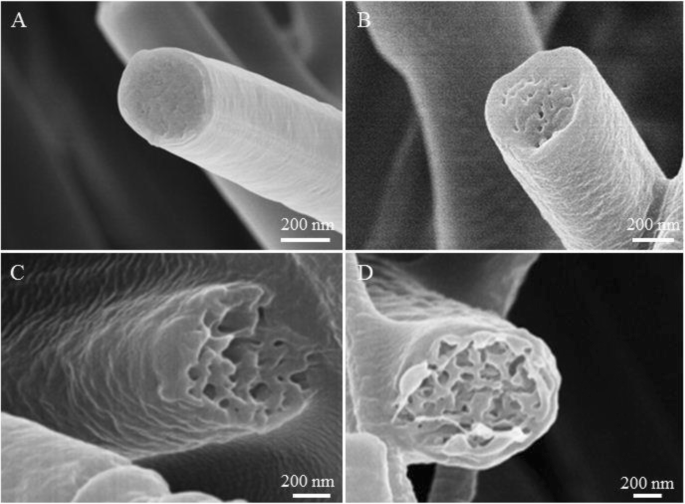
Images SEM en coupe d'échantillons fabriqués par électrofilage 35 % (w /v ) Solution PVDF de DMF à différents niveaux d'humidité relative. un 5%, b 25 %, c 45%, et d 65%
Fibres électrofilées à partir d'une solution de mélange ACE/DMF
Dans ce cas, 25 % (w /v ) Des solutions de PVDF avec différents rapports ACE/DMF (4:1, 2:1, 1:1, 1:2 et 1:4) ont été électrofilées à différents niveaux d'humidité relative. Pour 25 % (w /v ) (ACE/DMF au rapport de solvant de 4:1), des fibres lisses se sont formées à une humidité relative de 5 % (Fig. 6a et fichier supplémentaire 1 :Figure S4A), des fibres à rainures longitudinales peu profondes ont été produites à l'humidité relative de 25 % (Fig. 6b et fichier supplémentaire 1 : Figure S4B), et des fibres à rainures longitudinales de pilier ont été produites à des taux d'humidité relative de 45 % et 65 % (Fig. 6c, d et fichier supplémentaire 1 :Figure S4C, D). Pour 25 % (w /v ) (ACE/DMF au rapport de solvant de 2:1), des fibres lisses se sont formées à une humidité relative de 5 % (Fig. 6e et fichier supplémentaire 1 :Figure S4E), des fibres rugueuses ont été fabriquées à une humidité relative de 25 % (Fig. 6f et fichier supplémentaire 1 : figure S4F), des fibres à rainures longitudinales peu profondes ont été obtenues à une humidité relative de 45 % (Fig. 6g et fichier supplémentaire 1 :figure S4G), et des fibres à rainures longitudinales de pilier ont été produites à la relative humidité de 65 % (Fig. 6h et fichier supplémentaire 1 :Figure S4H). Pour 25 % (w /v ) (ACE/DMF au rapport de solvant de 1:1) à une humidité relative de 5%, des fibres lisses ont été observées (Fig. 6i et fichier supplémentaire 1 :Figure S4I), des fibres rugueuses ont été produites à une humidité relative de 25% et 45 % (Fig. 6j, k et fichier supplémentaire 1 : figure S4J, K), et les fibres à petites rainures des piliers ont été produites à une humidité relative de 65 % (Fig. 6l et fichier supplémentaire 1 :figure S4L). Pour 25 % (w /v ) (ACE/DMF aux rapports de solvant de 1:2 et 1:4), lorsque l'humidité relative ≤ 25%, des fibres lisses ont été observées (Fig. 6m, n, q, r et fichier supplémentaire 1 :Figure S4M, N , Q, R), tandis que les fibres rugueuses ont été produites à des taux d'humidité relative de 45 % et 65 % (Fig. 6o, p, s, t et fichier supplémentaire 1 :Figure S4O, P, S, T).
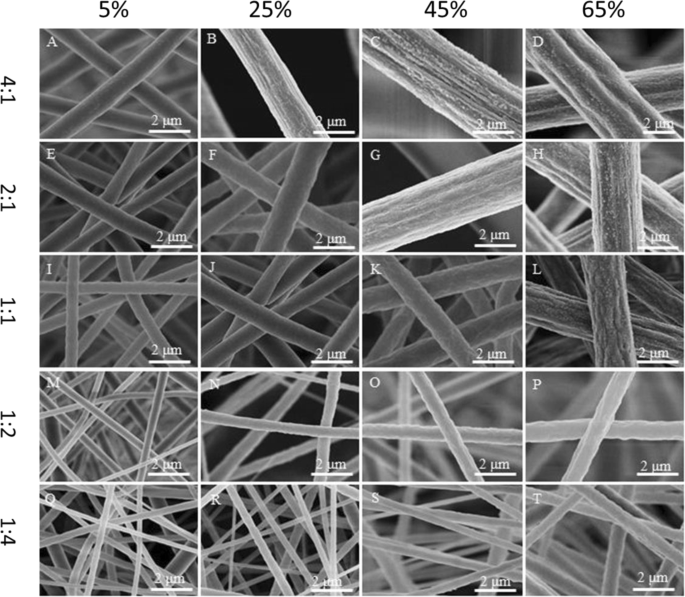
Images SEM représentatives d'échantillons fabriqués par électrofilage à 25 % (w /v ) Solutions PVDF d'ACE/DMF à différents niveaux d'humidité relative (5 %, 25 %, 45 % et 65 %) et de ratios de solvants. un –d 4:1, e –h 2:1, je –l 1:1, m –p 1:2 et q –t 1:4
Pour être plus précis sur le mécanisme de formation des fibres rainurées PVDF formées à partir d'ACE/DMF, nous avons vérifié la section transversale des fibres formées à tous les taux de solvant et différents niveaux d'humidité relative étudiés. Nous avons remarqué qu'à l'humidité relative de 5%, toutes les fibres formées avaient un intérieur solide. Ici, nous concluons qu'aucune séparation de phase ne s'est produite lors de la formation de fibres avec une surface lisse et un intérieur solide (Fig. 7a, e, i, m, q). Aux humidités relatives de 25 %, 45 % et 65 %, toutes les fibres produites avaient des pores intérieurs. Des fibres rainurées avec des pores intérieurs ont été fabriquées par un mécanisme d'allongement basé sur les rides [36]. Dans ce cas, en raison de l'évaporation rapide de l'ECA hautement volatil (pression de vapeur, 24 kPa) et de la séparation de phases, une peau vitreuse s'est formée au début de l'électrofilage, puis la surface ridée du jet s'est formée en raison de la formation des pores intérieurs, et allongé en fibres rainurées par la suite (Fig. 7b–d, g, h, l). La figure 3c explique le mécanisme de formation des fibres rainurées à une humidité relative élevée. La formation de nanopiliers à la surface des fibres rainurées pourrait être due au fait que l'ACE piégé dans les fibres par la peau vitreuse, qui a fait face à une évaporation rapide de l'ACE, mais certains points faibles pourraient encore exister, entraînant la formation de nanopiliers.
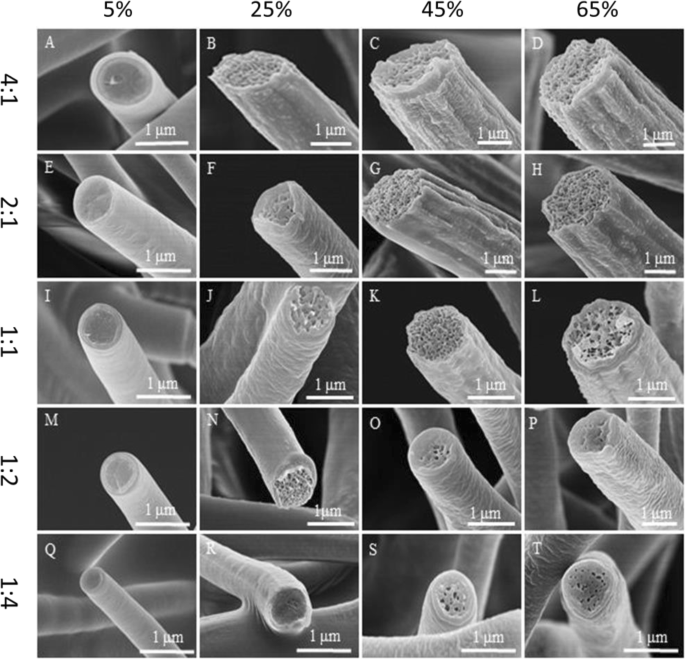
Images SEM en coupe d'échantillons fabriqués par électrofilage à 25 % (w /v ) Solutions PVDF d'ACE/DMF à différents niveaux d'humidité relative (5 %, 25 %, 45 % et 65 %) et de ratios de solvants. un –d 4:1, e –h 2:1, je –l 1:1, m –p 1:2 et q –t 1:4
Des fibres avec des surfaces rugueuses et des pores intérieurs se sont formées à cause du VIPS (Fig. 7f, j, k, o, p, s, t). Des fibres avec des surfaces lisses et des pores intérieurs se sont également formées en raison du VIPS (Fig. 7n, r) [24, 37]. Il est à noter que la largeur et la profondeur des rainures augmentent en augmentant l'humidité relative. Toutes les surfaces et morphologies internes obtenues à partir d'une solution de mélange ACE/DMF à différents niveaux d'humidité relative sont conclues dans le tableau 1. Nous avons remarqué que l'augmentation de l'humidité relative de 5 à 65% entraîne une augmentation du diamètre des fibres de ~ 1 à ~ 3.75 μm , ~ 0,85 à ~ 2,9 μm, ~ 0,6 à ~ 2 μm, ~ 0,35 à ~ 1 μm et ~ 0,26 à ~ 0,7 μm pour les rapports de solvants suivants de 4:1, 2:1, 1:1, 1:2 , et 1:4, respectivement (Fichier supplémentaire 1 :Figure S2C-G).
En raison de l'importance de l'humidité relative élevée dans la formation des structures de surface secondaires des fibres de PVDF, nous avons illustré le comportement de phase des solutions d'électrofilage en créant un diagramme de phase à une humidité relative de 65 % (Fig. 8). Le diagramme est divisé en deux zones par une courbe binodale. Le jet de solution est sans nuage et homogène lors de son extrusion de la filière (zone I). Avec le taux de volatilisation élevé de l'ACE, le faible taux de volatilisation du DMF et la perméation subséquente de l'eau dans le jet de solution, la proportion des composants (PVDF, solvant (s) et eau) dans le jet est modifiée dynamiquement pour suivre le chemin indiqué par les flèches. Le jet de solution commence à entrer dans la zone II, après avoir traversé la courbe bimodale, où il se trouble et se sépare en multiphase en raison de l'instabilité thermodynamique [37, 38]. Un solvant plus volatil (ACE) est représenté par une flèche plus raide, ce qui correspond à une séparation de phases plus rapide.
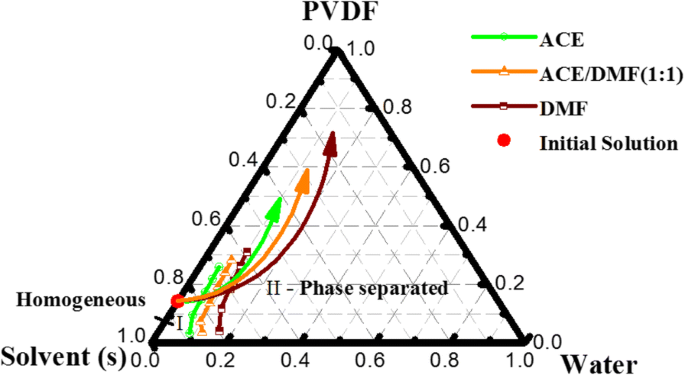
Diagramme de phase du PVDF, du ou des solvant(s) et de l'eau à l'humidité relative de 65%. Le point rouge fait référence à la solution initiale
Afin de quantifier la surface et la structure des pores des fibres, les isothermes d'adsorption d'azote des fibres macroporeuses (Fig. 1d), des fibres rugueuses (Fig. 4d) et des fibres rainurées (Fig. 6l) ayant des diamètres similaires ont été choisi pour comparaison. Les surfaces spécifiques des fibres macroporeuses, rainurées et rugueuses étaient de 23,31 ± 4,30 m 2 /g, 10,26 ± 2,19 m 2 /g et 4,81 ± 0,58 m 2 /g, et les volumes des pores étaient de 0,0695 ± 0,007 cm 3 /g, 0,0182 ± 0,003 cm 3 /g et 0,0135 ± 0,002 cm 3 /g, respectivement (Fig. 9a). Ces résultats étaient coordonnés avec l'adsorption maximale d'azote des fibres macroporeuses, rainurées et rugueuses qui mesuraient 20,06 cm 3 /g, 12,29 cm 3 /g et 7,49 cm 3 /g, respectivement (Fig. 9b). Nous avons en outre confirmé que des mésopores (2-50 nm) existaient dans les fibres macroporeuses, rainurées et rugueuses (Fig. 9c), alors que les macropores (> 100 nm) n'apparaissaient que dans les fibres macroporeuses, ce qui a entraîné leur surface spécifique et volume de pores élevés (Fig. 9d).
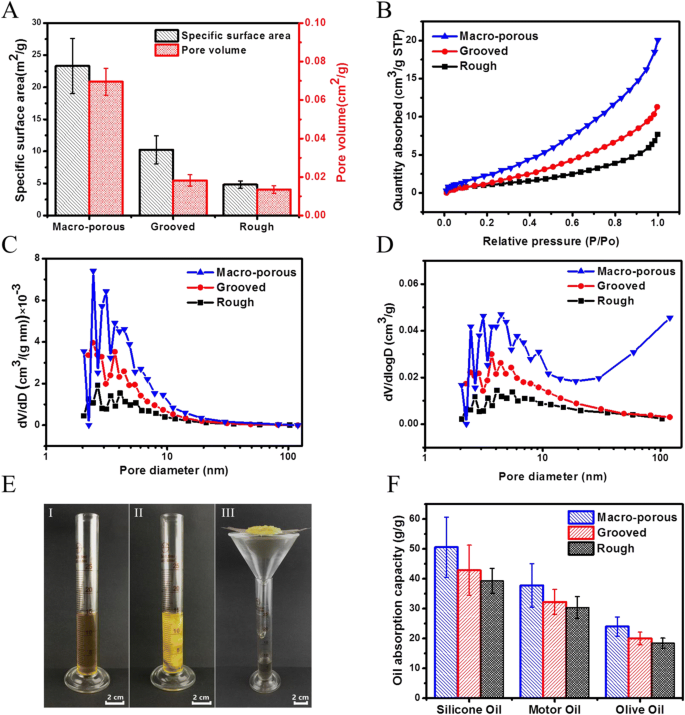
Caractérisations des fibres macroporeuses, rainurées et rugueuses. un Surface spécifique et volume des pores. b Les isothermes d'adsorption d'azote. c dV/dD—courbe du diamètre des pores. d dV/dlogD—courbe du diamètre des pores. e Photos d'absorption d'huile. (I) 15 mL de mélange eau-huile (1 :1) sans sorbant, (II) lors de l'absorption, (III) lors de la vidange. f Capacités d'absorption d'huile
Étant donné que le PVDF est un matériau hydrophobe mais pas oléophobe, les sorbants PVDF peuvent absorber l'huile tout en repoussant l'eau. Nous avons ensuite démontré l'application des fibres macroporeuses, rainurées et rugueuses pour l'absorption d'huile (Fig. 9e). Trois huiles typiques (huile de silicone, huile de moteur et huile d'olive) ont été sélectionnées pour vérifier les différents échantillons.
Les propriétés typiques de ces huiles sont répertoriées dans le tableau 2. Comme prévu, parmi les trois types de matériaux d'absorption d'huile, les fibres macroporeuses ont montré la capacité d'absorption d'huile la plus élevée de 50,58 ± 5,47 g/g, 37,74 ± 4,33 g/g, et 23,96 ± 2,68 g/g pour l'huile de silicone, l'huile de moteur et l'huile d'olive, respectivement (Fig. 9f). En particulier, les fibres macroporeuses présentaient 1,18, 1,17 et 1,19 fois les capacités d'absorption d'huile des fibres rainurées pour l'huile de silicone, l'huile de moteur et l'huile d'olive, respectivement. De plus, les fibres macroporeuses présentaient 1,29, 1,24 et 1,26 fois les capacités d'absorption d'huile des fibres rugueuses pour l'huile de silicone, l'huile de moteur et l'huile d'olive, respectivement. Ces résultats doivent être attribués au fait que les fibres macroporeuses ont la surface spécifique la plus élevée, tandis que les fibres rugueuses ont la surface spécifique la plus faible parmi tous les échantillons. Parmi les trois types d'huile étudiés, tous les échantillons testés présentaient la meilleure capacité d'absorption pour l'huile de silicone, probablement en raison de la viscosité plus élevée de l'huile de silicone.
Conclusions
Nous avons démontré une méthode appropriée et fiable pour la formation de nanofibres de PVDF macroporeuses, rugueuses et rainurées avec des pores internes. Afin de comprendre le mécanisme responsable de la formation des fibres de PVDF, nous avons testé trois systèmes de solvants (c.-à-d. ACE, DMF et mélange ACE-DMF) sous différents niveaux d'humidité relative (5 %, 25 %, 45 % et 65 %). Nous avons découvert qu'aucune séparation de phase ne se produisait à l'humidité relative de 5% en utilisant les solvants précédents, entraînant la formation de fibres lisses avec un intérieur solide. Nous avons constaté que la formation de macropores à la surface des fibres avec un intérieur solide à une humidité relative de 25 % devrait être attribuée aux TIPS en raison de la pression de vapeur élevée de l'ACE et du mécanisme de nucléation, tandis que la formation de macropores sur la surface des fibres avec des pores intérieurs à une humidité relative de 45% et 65% doit être attribuée à la coexistence des mécanismes TIPS et VIPS. De plus, nous avons constaté que la faible pression de vapeur du DMF jouait un rôle central dans la production de fibres rugueuses avec des pores à l'intérieur par VIPS. Alors que le mécanisme d'allongement basé sur les plis a joué un rôle clé dans la fabrication des fibres rainurées avec une structure intérieure poreuse. Les fibres macroporeuses (> 300 nm) présentaient les meilleures performances d'absorption d'huile de 50,58 ± 5,47 g/g, 37,74 ± 4,33 g/g et 23,96 ± 2,68 g/g pour l'huile de silicone, l'huile de moteur et l'huile d'olive, respectivement. Surtout, notre compréhension des mécanismes responsables de la formation des fibres PVDF macroporeuses, rugueuses et rainurées avec une porosité intérieure peut servir de référence importante pour la fabrication de fibres électrofilées en régulant le solvant et l'humidité relative.
Abréviations
- ACE :
-
Acétone
- DMF :
-
N,N diméthylformamide
- PVDF :
-
Fluorure de polyvinylidène
- CONSEILS :
-
Séparation de phases induite thermiquement
- VIPS :
-
Séparation de phases induite par la vapeur
Nanomatériaux
- Nanofibres et filaments pour une administration améliorée des médicaments
- Production de fibre de carbone et pièces en fibre de carbone :quelles sont les bases ?
- Dévoilement de la structure atomique et électronique des nanofibres de carbone empilées
- Les nanofibres hiérarchiques antibactériennes en polyamide 6-ZnO fabriquées par dépôt de couche atomique et croissance hydrothermale
- Effet du traitement de recuit in situ sur la mobilité et la morphologie des transistors à effet de champ organiques à base de TIPS-Pentacène
- Formation et propriétés luminescentes de nanocomposites Al2O3:SiOC à base de nanoparticules d'alumine modifiées par le phényltriméthoxysilane
- Réglage des morphologies de surface et des propriétés des films de ZnO par la conception de la couche interfaciale
- Électrofilage sur des substrats isolants en contrôlant la mouillabilité et l'humidité de la surface
- Découvrez les avantages de la rectification de surface et cylindrique en interne