Usinage par électroérosion :construction, application, avantages et inconvénients
L'usinage par décharge électrique, également appelé usinage par étincelle, est un processus très différent de la plupart des processus d'usinage conventionnels tels que le tournage et le fraisage CNC. Dans ces derniers processus, des outils de coupe tranchants sont nécessaires pour pouvoir soustraire de la matière de la pièce à usiner. Contrairement au tournage et au fraisage, le procédé EDM tire parti de l'érosion du métal par une série de décharges électriques.
Lisez la suite ci-dessous et apprenez-en plus sur les concepts fondamentaux impliqués dans la fabrication EDM.
Comment fonctionne la GED ?
L'usinage par décharge électrique utilise des étincelles électriques sur la machine d'électroérosion pour éroder certaines parties de la pièce. Ces « étincelles électriques » sont en fait des arcs électriques formés entre deux conducteurs porteurs de courant amenés à proximité l'un de l'autre. Les arcs électriques sont responsables de la génération de chaleur extrême qui fait fondre et évaporer les matériaux électriquement conducteurs. À l'intérieur du système d'un processus EDM, la pièce est connectée à la borne positive ou à l'anode, tandis que l'outil responsable de l'érosion des matériaux est connecté à la borne négative ou à la cathode.
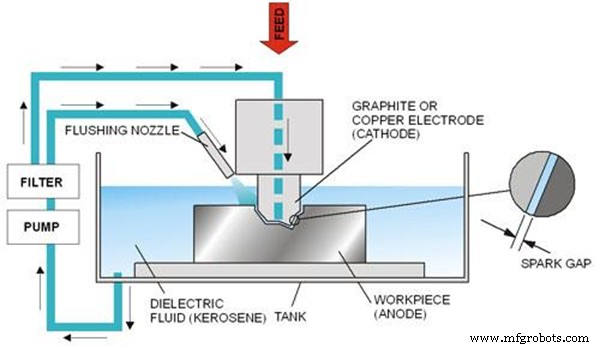
Construction de base d'un système EDM
Pour approfondir le principe de fonctionnement, vous trouverez ci-dessous une ventilation de la construction de base d'un système d'usinage par décharge électrique (EDM).
Ce composant convertit l'alimentation CA en une alimentation CC pulsée suffisamment élevée pour générer une étincelle entre l'outil d'érosion et la pièce à usiner.
Cette partie du système est connectée à la cathode de l'alimentation tout en étant montée sur un poste d'outil. Le profil de votre outil sera exactement le même profil laissé sur votre pièce de travail. Au cours du processus, un très petit espace appelé espace d'arc (identifié par les ingénieurs de fabrication) est maintenu entre l'outil d'électrode et la pièce de travail. Les matériaux les plus couramment utilisés pour les électrodes sont le cuivre, l'alliage de tungstène, le graphite, l'acier et la fonte.
Ce mécanisme contrôle l'alimentation et le mouvement de l'outil dans la machine EDM. L'espace d'arc, mentionné précédemment ci-dessus, est contrôlé de manière critique par un mécanisme de servomoteur programmé.
Ce composant fournit la bonne quantité de tension nécessaire pour la génération d'étincelles et l'entretien de la décharge. La génération de cent mille étincelles par seconde permet de créer une importante soustraction de matière à la pièce travaillée.
L'outil d'électrode et la pièce de travail sont immergés dans un fluide diélectrique tout en ayant le fluide alimenté au niveau de l'espace entre l'outil et la pièce de travail. De plus, le fluide diélectrique doit être réglé pour circuler à une pression constante pour évacuer les pièces métalliques qui se sont érodées de la pièce de travail. Trop de pression de fluide peut entraîner l'élimination rapide des copeaux de métal, ce qui ralentit l'action de coupe. Une pression de fluide trop faible peut provoquer un court-circuit dans le système en raison des copeaux non évacués pendant le processus d'érosion.
Les fluides diélectriques les plus couramment utilisés dans ce processus sont l'eau déminéralisée, le glycol et l'huile de silicone.
Cela complète l'écosystème de la machine EDM car la pièce de travail est connectée à l'anode. Pour rendre le processus possible, la pièce à usiner doit être un bon conducteur électrique.
Type de processus GED
Le processus EDM est classé en différents types en fonction de la forme et de l'approche de l'outil utilisé. Les trois types courants de décharge électrique dans l'industrie sont l'électroérosion à fil, l'électroérosion par enfonçage et l'électroérosion par perçage.
1. Électroérosion à fil
Comme son nom l'indique, la découpe par fil EDM utilise un fil très fin (alliage de cuivre ou de laiton allant généralement de 0,004 pouce à 0,0006 pouce d'épaisseur) qui est maintenu par des guides diamantés pour couper avec précision une forme bidimensionnelle sur une pièce 3D. Le chemin est contrôlé par un programme CNC qui permet de découper facilement des formes complexes. La coupe peut être assimilée à l'avance de coupe d'une scie à ruban et d'un coupe-fromage. Ce processus est généralement utilisé pour découper des matrices d'extrusion de métal, des poinçons et des plaques.
2. Electro-érosion par enfonçage
Aussi appelé ram EDM, ce type de procédé EDM utilise des électrodes en graphite ou en cuivre formées dans une forme inversée pour découper une cavité sur la pièce à usiner. L'outil à utiliser est usiné dans une forme inverse de la forme souhaitée à laisser sur la pièce.
L'EDM par enfonçage le rend parfait pour l'usinage de moules à utiliser pour le moulage et le moulage par injection où des formes de cavité complexes sont nécessaires.
3. EDM de perçage de trous
Dans ce type de processus EDM, l'outil d'électrode est utilisé pour couper des trous extrêmement fins et profonds qu'un foret conventionnel peut ne pas être capable de faire. L'outil pour ce processus est conçu de telle manière que le liquide diélectrique est alimenté directement à travers le trou, d'où une électrode creuse. Étant donné que l'EDM de perçage de trous n'est pas réalisé par la méthode d'usinage conventionnelle, aucune bavure ne se forme dans la pièce à usiner. L'EDM de perçage de trous est utilisé pour usiner de minuscules trous en relief sur diverses aubes de turbine, matrices et moules.
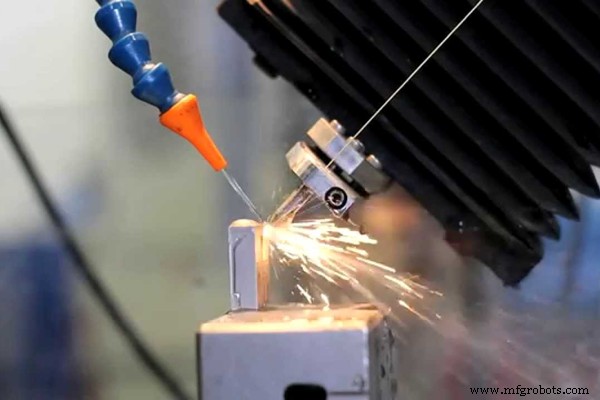
Quelles sont les applications de l'usinage EDM ?
L'usinage EDM est hautement capable de produire des formes et des géométries complexes.
C'est pourquoi généralement, l'usinage par décharge électrique est utilisé pour des applications très précises où l'usinage conventionnel n'est pas capable. Vous trouverez ci-dessous les applications les plus courantes de l'usinage EDM :
Perçage de petits trous
De nombreux fabricants choisissent d'utiliser l'usinage EDM pour percer des trous extrêmement petits car cela réduit le risque d'avoir des outils déviés et endommagés. Les trous usinés par EDM peuvent être de très petite structure et peuvent être vus sur les bords des aubes de turbine, des orifices microscopiques pour les composants du système de carburant, et bien d'autres.
Fabrication de moules et matrices
L'usinage EDM est souvent utilisé comme procédé complémentaire à l'usinage conventionnel dans la fabrication de moules et de matrices. Comme mentionné ci-dessus, le type de coupe de fil est généralement utilisé pour former des ébauches pour les moules, le type de plomb peut être utilisé pour former des formes complexes des cavités, et le perçage de trous peut être utilisé pour créer des trous de libération de pression.
Désintégration des composants
La machine EDM est également utilisée pour enlever les métaux collés dans une pièce de travail qui ne peut pas être enlevée de manière ordinaire. Désintégrer les composants collés signifie détruire ou enlever le matériau. Certaines circonstances incluent des boulons cisaillés sur des trous filetés, des outils d'aspiration sur une pièce usinée ou une goupille coincée sur une pièce très précieuse. En désintégrant les composants, vous arrivez à retirer le métal collé sans endommager la pièce à récupérer.
Composants médicaux
Les produits usinés par EDM ne forment pas de bavures lors de leur fabrication, c'est pourquoi ils sont parfaits pour créer divers composants d'implants médicaux.
Composants aérospatiaux
Il y a beaucoup de caractéristiques sur une pièce aérospatiale qui ne peuvent pas être fabriquées par certains outils de coupe standard, et c'est là que l'usinage EDM entre en jeu. L'usinage EDM est capable de produire des caractéristiques difficiles avec avant tout un disque de rotor de turbine, des fentes minces, des équerres nettes des trous et des exigences très strictes en matière de trous profonds.
Pourquoi l'EDM est-il préféré ?
Hautement capable d'usiner des profils complexes
La liberté de coupe pour l'EDM est moins contrainte que celle des opérations d'usinage conventionnelles. Dans ce processus, diverses caractéristiques qui sont presque impossibles à obtenir grâce à l'utilisation de fraises et de forets peuvent être facilement coupées. Ces caractéristiques comprennent des poches complexes, des trous fins et profonds, des parois minces et d'autres géométries de forme irrégulière.
Haute précision
Les pièces usinées par la technologie EDM peuvent être précises jusqu'aux plus petites tolérances utilisées dans l'industrie de la fabrication des métaux. Ceci est possible car l'écosystème de l'usinage EDM n'introduit pas de contraintes élevées sur la pièce à usiner et n'a pas de vibrations agressives. En dehors de cela, un processus d'écrémage peut également être effectué pour augmenter sa précision et son exactitude.
Finition de surface sans bavure
La pièce de travail produite à partir de l'usinage EDM sort sans bavure en raison de la nature du processus dans lequel le métal érodé de la pièce de travail se désintègre presque en microparticules qui sont ensuite évacuées. Plus important encore, la découpe EDM n'implique pas d'outils de coupe tranchants tels que des fraises en bout, des scies et des perceuses, c'est pourquoi ce processus ne provoque aucune bavure sur la pièce à usiner.
Peut couper les métaux durs
L'usinage EDM est capable de couper des métaux durs avec une faible force et un minimum d'effort tant qu'ils sont conducteurs. La dureté du matériau coupé n'affecte pas l'ensemble du processus.
Faible stress
Les outils utilisés dans un processus EDM ne touchent pas la pièce, contrairement à d'autres méthodes d'usinage où les outils de coupe entrent en contact avec la surface à couper. Cela explique la contrainte minimale introduite dans la pièce.
Fabrication hautement évolutive
Les processus d'usinage EDM sont très polyvalents en ce qui concerne l'échelle de production, ils conviennent à la fabrication de petits à grands volumes. Ces processus sont hautement reproductibles, ce qui signifie que plusieurs pièces peuvent être fabriquées avec une qualité constante.
Lorem ipsum dolor sit amet, consectetur adipiscing elit. Ut elit tellus, luctus nec ullamcorper mattis, pulvinar dapibus leo.
Quelles sont les limites du processus EDM ?
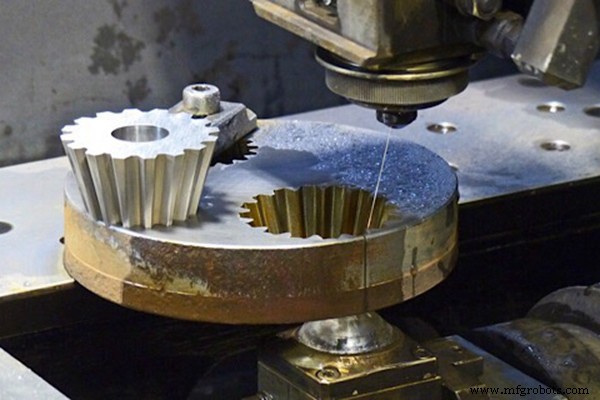
Uniquement applicable aux matériaux conducteurs
La chaleur responsable de l'érosion du matériau sur la pièce à usiner repose sur l'introduction de décharges électriques, ce qui rend l'usinage par électroérosion incompatible avec des matériaux non conducteurs tels que les composites, les plastiques et d'autres matériaux diélectriques.
Faible taux d'enlèvement de matière
Comme mentionné, l'usinage EDM érode progressivement le matériau. Cela rend son taux d'enlèvement de matière beaucoup plus lent que celui des processus d'usinage conventionnels comme le fraisage et le tournage.
Coût de production élevé
Le coût de production de pièces à l'aide de l'EDM implique différents facteurs, tels qu'une consommation d'énergie élevée, une usure excessive des outils et un long temps d'usinage.
Résumé
L'usinage par décharge électrique est un complément très utile à divers processus d'usinage CNC conventionnels. Il tire parti de sa force lorsqu'il est capable de produire des caractéristiques spéciales difficiles à obtenir par le fraisage et le tournage. En plus de cela, le processus EDM a une précision exceptionnelle même lors de la coupe de métaux extrêmement durs conducteurs d'électricité, et il affiche une faible contrainte pendant le traitement.
commande numérique par ordinateur
- Avantages et inconvénients de la coulée de mousse perdue
- Avantages et inconvénients du formage à froid des métaux
- Usinage EDM :construction et principe de fonctionnement discutés
- Pourquoi l'usinage par décharge électrique est-il populaire par rapport aux autres techniques ?
- Qu'est-ce que l'usinage par électroérosion (EDM) ?
- Types de machines à décharge électrique (EDM), avantages et inconvénients
- Usinage de prototype :avantages et inconvénients de la CNC pour le prototypage
- Électroérosion par enfonçage vs électroérosion à fil :principales différences et applications
- Au-delà de la CNC :qu'est-ce que l'usinage par électroérosion ?