Temps d'inactivité :définition, causes et comment le réduire
Le temps d'inactivité est une expression que vous entendrez souvent dans l'espace de fabrication et de gestion de la main-d'œuvre, car il est étroitement lié à la productivité.
Il n'est pas exagéré de dire qu'en réduisant les temps d'inactivité, les organisations peuvent voir leur résultat net augmenter. Cependant, pour mettre cela en pratique, vous devez d'abord comprendre ce qu'est le temps d'inactivité et ce qu'il n'est pas.
Dans cet aperçu, nous allons définir le temps d'inactivité, montrer comment le calculer, discuter des causes les plus courantes de temps d'inactivité et décrire les étapes à suivre pour minimiser le temps d'inactivité dans votre organisation.
Qu'est-ce que le temps d'inactivité ?
Temps d'inactivité est une période de temps pendant laquelle un actif (machine ou employé) est prêt et disponible, mais ne fait rien de productif. C'est pourquoi le temps d'inactivité est parfois appelé temps d'attente .
Le temps d'inactivité est lorsqu'une machine attend du matériel d'entrée. C'est un employé de bureau qui attend le retour de la connexion Internet. Un camion sur un chantier de construction attend qu'une excavatrice se déplace pour atteindre son emplacement cible. Il s'agit d'un mécanicien de maintenance qui attend qu'une scie circulaire soit disponible pour terminer son travail.
La raison pour laquelle vous souhaitez comprendre et suivre le temps d'inactivité est qu'il indique l'écart entre votre production existante et votre niveau de productivité théoriquement maximal. En termes simples, chaque minute pendant laquelle votre machine ou votre employé est inactif est une minute de perte de productivité .
Cela étant dit, aucune entreprise ne peut fonctionner à 100 % d'efficacité. Un certain niveau de temps d'inactivité est inévitable. L'objectif de chaque manager ne devrait être que de minimiser le temps d'inactivité, pas de l'éliminer. L'élimination du temps d'inactivité est presque impossible et ne peut être envisagée que pour les systèmes fermés et hautement automatisés.
Temps d'inactivité =temps d'arrêt ?
Le temps d'inactivité ne fait pas temps d'arrêt égal. Alors que dans les deux cas, la machine ne fait rien de productif, la principale différence réside dans pourquoi est-ce que cela se produit.
Dans le contexte d'un temps d'inactivité anormal, la machine est capable de remplir sa fonction prévue mais pour une certaine raison, elle ne le fait pas. Il existe de nombreuses causes possibles de temps d'inactivité de la machine comme :
- pas de matière première d'entrée
- attendre qu'une autre machine termine son travail
- différentes inefficacités de workflow et de processus
- la production doit être ralentie ou arrêtée (pour des raisons telles que l'inventaire à pleine capacité)
- pannes de courant ou problèmes techniques similaires qui ne sont pas liés à la machine elle-même
- …
Lorsque nous parlons de temps d'arrêt de la machine, l'actif n'est pas opérationnel pour l'une des deux raisons suivantes :
- Maintenance planifiée : C'est à ce moment-là que vous planifiez un temps d'arrêt pour effectuer une maintenance préventive sur un actif. Ceci est parfois appelé temps d'inactivité normal parce que l'entretien programmé est quelque chose qui doit être effectué pour maintenir les machines en bon état.
- Panne de machine : Panne inattendue de la machine qui doit être corrigée avant que la machine puisse continuer à fonctionner. Peut être appelé temps d'inactivité anormal car il s'agit d'un événement hors de notre contrôle et qui nuit à la productivité globale de l'entreprise.
D'une manière générale, lorsque nous parlons de temps d'inactivité, l'actif peut s'exécuter mais il ne le fait pas . Et quand on parle de temps d'arrêt des équipements, la machine ne fonctionne pas car elle ne peut pas .
En raison de cette différence, les équipes de maintenance doivent suivre les temps d'arrêt des machines planifiés et non planifiés séparément du temps d'inactivité.
Réduire la maintenance réactive de 73,2 %
Voir les résultats que Red Hawk aime avec Limble
Lire notreÉtude de cas
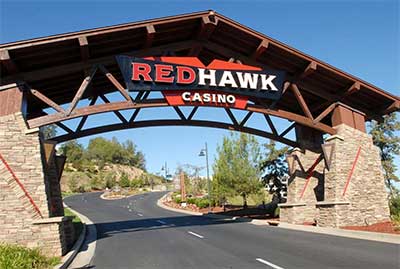
Comment calculer le temps d'inactivité ?
Le temps d'inactivité représente la disparité entre l'heure à laquelle un actif doit être exécuté et le nombre d'heures productives réelles qui ont été consacrées.
Par exemple, dans un quart de travail de 8 heures, un employé peut suivre 7 heures et 20 minutes de travail productif. Cela suggère qu'ils ont eu 40 minutes d'inactivité, en supposant qu'ils aient tout suivi avec précision sur une base temporelle.
Quand on parle de machines, les choses se compliquent un peu car il faut faire la différence entre le moment où une machine vient d'être allumée et le travail productif réel.
Imaginons que vous ayez une machine qui fonctionne pendant 16 heures. Pour cet exemple, disons qu'il a besoin de 10 minutes pour s'allumer, 5 minutes pour s'éteindre, qu'il a une pause de 30 minutes pour le nettoyage et qu'il est arrêté pendant 15 minutes pour un changement d'équipe.
En d'autres termes, la machine est censée effectuer un travail productif pendant 15 heures ou 900 minutes .
On peut facilement imaginer une situation où une machine était au ralenti :
- 5 minutes toutes les heures en attente de matériel d'entrée (75 minutes au total)
- 10 minutes car un changement d'équipe a pris 25 minutes au lieu des 15 minutes habituelles
- 40 minutes parce qu'une autre machine de la ligne de production a subi une panne inattendue
Tout cela équivaudrait à 125 minutes d'inactivité.
Auriez-vous besoin de le réduire à zéro? Pas nécessairement. Peut-être que ces 5 minutes toutes les heures sont également nécessaires aux opérateurs de machines pour prendre les pauses nécessaires ou nettoyer les choses. Cela étant dit, vous voudriez certainement éliminer les temps morts causés par des pannes imprévues de la machine.
Causes courantes du temps d'inactivité
Avant de décrire les meilleures pratiques pour le réduire, discutons brièvement des causes courantes du temps d'inactivité :
- Inefficacité des travailleurs : Les travailleurs ne sont pas des machines et certains sont plus efficaces que d'autres. Ils ont besoin de pauses pour éviter l'épuisement professionnel. Certaines inefficacités sont le résultat du fait que les employés nouvellement embauchés traversent une période d'adaptation. Pour remédier aux inefficacités des travailleurs, vous pouvez travailler à l'amélioration de votre processus d'intégration et développer une culture d'entreprise où chacun doit faire son propre poids.
- Inefficacité des processus et des flux de travail : Des processus de production et d'entreprise mal optimisés, l'attente d'approbations et le manque d'outils disponibles pour exécuter l'ordre de travail attribué sont des éléments que vous devriez examiner pour réduire les inefficacités des processus et des flux de travail.
- Équipement défectueux : Les pannes inattendues de la machine peuvent entraîner de graves problèmes de fonctionnement. Les services de maintenance doivent utiliser un système de GMAO et disposer d'un plan de maintenance proactif pour tous les actifs de priorité moyenne et élevée.
- Accidents et catastrophes naturelles : Des choses qui sont pour la plupart hors de notre contrôle. Il est généralement plus logique d'essayer de se préparer à de tels événements que d'essayer de les empêcher.
Comment réduire le temps d'inactivité ?
Une question que vous devez vous poser avant de plonger dans des conseils pratiques est une chose à laquelle nous avons déjà fait allusion plus tôt :Voulez-vous même éliminer les temps d'inactivité ?
Ceci est particulièrement important lorsque nous parlons d'employés. Vous ne pouvez pas vous attendre à ce que les gens soient productifs chaque seconde de chaque jour. Il y a une raison pour laquelle la plupart des écoles et universités travaillent en blocs de 40 à 60 minutes avec de courtes pauses. Pour éviter l'épuisement professionnel et améliorer réellement la productivité globale, différentes recherches suggèrent un bloc de travail idéal dure entre 50 et 90 minutes avec des pauses de 5 à 20 minutes.
Les choses sont différentes lorsque nous commençons à parler de machines car ce n'est pas comme si elles se fatigueraient, perdraient leur concentration et feraient des dégâts. Cela étant dit, il y a des raisons de ne pas pousser toutes les machines à leurs limites non plus. Bien que les machines ne se fatiguent pas, elles s'usent. Par exemple, certaines machines ont des composants qui ne doivent pas dépasser certains niveaux de température. Un peu de temps d'inactivité peut être juste ce dont ils ont besoin pour se calmer.
Ce sont des cas spécifiques que vous voulez avoir à l'esprit.
Cependant, il ne fait aucun doute qu'un temps d'inactivité élevé est quelque chose qui doit être traité car il peut ruiner une organisation à long terme - soit par une perte de productivité, soit en augmentant les coûts sans ajouter de valeur (cela est particulièrement visible dans les industries de la construction et des transports par le coût du carburant gaspillé des machines et des camions qui sont inactifs).
Voici quelques moyens de réduire les temps d'inactivité et d'améliorer la productivité :
#1) Optimisez votre flux de travail
Comme nous l'avons mentionné précédemment, les inefficacités des flux de travail et des processus sont une cause fréquente de temps d'inactivité. C'est pourquoi chaque organisation doit s'efforcer de repérer et d'éliminer les goulots d'étranglement et autres problèmes causés par ces inefficacités.
La première étape pour résoudre tout problème est de réaliser que vous en avez un. Si vous souhaitez vérifier si le temps d'inactivité nuit à votre service, la première étape doit être de mettre en œuvre un programme de suivi et de rapport du temps productif par rapport au temps non productif.
Pour réduire le temps d'inactivité des employés, vous pouvez :
- chercher à créer des horaires et une charge de travail plus équilibrés, en particulier pour les projets plus importants avec plusieurs membres d'équipe où une tâche doit être terminée avant que la suivante puisse commencer
- éliminez les tâches administratives inutiles (telles que les (pré)approbations, le suivi d'une chose à plusieurs endroits, etc.)
- créer des procédures d'exploitation claires pour les tâches de routine (dans l'espace de maintenance, cela se traduirait par la création d'éléments tels que des procédures d'exploitation standard et des listes de contrôle de maintenance préventive)
- s'assurer que les employés disposent d'outils lorsqu'ils en ont besoin (qu'il s'agisse d'une clé ou d'un accès à un outil de gestion de projet)
- adopter des pratiques allégées
En ce qui concerne les optimisations de flux de travail pour les machines, vos options sont en quelque sorte limitées car vous ne pouvez pas modifier le fonctionnement d'une machine. Vous pouvez toujours regarder :
- organiser les machines de manière à ce que la sortie d'une machine s'écoule efficacement pour être l'entrée d'une autre machine
- vous disposez de suffisamment de main-d'œuvre qualifiée pour prendre en charge/exploiter les machines
- recherchez des moyens d'optimiser la production et d'augmenter la durée d'activité de vos actifs
#2) Gardez vos actifs en bon état
Le fait inévitable est que les actifs endommagés ne peuvent pas atteindre leurs niveaux de productivité de pointe. Si les actifs ne fonctionnent pas à leur pleine capacité, cela signifie que vous avez une marge d'amélioration.
Voici quelques conseils pour maintenir les actifs en parfait état de fonctionnement :
- mettre les actifs importants sur un plan de maintenance préventive
- mettre en œuvre une surveillance de l'état et une maintenance autonome pour détecter la détérioration des équipements le plus tôt possible
- utiliser des matières premières (premières) de qualité
- réduire le nombre de solutions improvisées et de pièces de rechange de mauvaise qualité et essayer d'utiliser principalement des pièces de rechange approuvées par les OEM
- utiliser la GMAO mobile pour s'assurer que les travaux de maintenance requis sont effectués et à temps
#3) Améliorer le flux d'informations
Cette astuce pourrait facilement être intitulée « améliorer les lignes de communication ” car la notion est fondamentalement la même.
Il existe une théorie selon laquelle la principale raison pour laquelle les entreprises échouent (corruption et pratiques commerciales illégales mises à part) est qu'elles deviennent trop rigides et inefficaces. En d'autres termes, lorsqu'un marché les oblige à changer, ils ne sont pas assez agiles pour mettre en œuvre des changements structurels assez rapidement, et ils se font distancer par leurs concurrents.
Cela correspond bien au temps d'inactivité. Au fur et à mesure que l'organisation grandit, le nombre de tâches administratives augmente également car les services ont besoin d'échanger plus d'informations.
Si une question doit passer par plusieurs niveaux de gestion avant qu'un employé n'obtienne une réponse claire, un temps considérable sera perdu à attendre les approbations.
Une solution consiste, dans la mesure du possible, à éliminer les intermédiaires , définissez clairement qui est responsable de quoi et assurez des canaux de communication directs entre les parties qui dépendent les unes des autres.
D'autres solutions, en particulier dans l'environnement de bureau, consistent à utiliser les solutions logicielles disponibles pour accélérer la communication, automatiser les tâches pouvant être automatisées, suivre le travail et générer des rapports utiles. Par coïncidence, ce sont toutes les choses qu'une GMAO fait pour un service de maintenance.
Identifier, explorer, corriger
Déterminer si le temps d'inactivité est un problème pour votre organisation est souvent beaucoup plus facile que de le réduire.
Le principal défi consiste à trouver la cause première du temps d'inactivité . Une machine tourne-t-elle au ralenti parce que le processus de production est inefficace ? Est-ce parce qu'une machine précédente dans la ligne de production ne fonctionne pas à pleine capacité ? Est-ce parce que les matières premières de mauvaise qualité entraînent davantage d'interventions des opérateurs de machines, ce qui ralentit la production ? Est-ce une combinaison de différentes raisons ?
Bien que la réduction du temps d'inactivité ne soit pas toujours aussi simple que nous le souhaiterions, l'effet qu'elle peut avoir sur vos résultats en fait une poursuite qui en vaut la peine.
Entretien et réparation d'équipement
- Comment obtenir la date et l'heure actuelles en Python ?
- Comment optimiser les systèmes de fabrication et gagner du temps
- Comment réduire la consommation d'énergie dans la fabrication
- 4 principales causes de défaillance d'appareillage de commutation et comment les éviter
- Qu'est-ce que la fumée de soudage ? - Les dangers et comment les réduire
- Qu'est-ce que les éclaboussures de soudure et comment les réduire ?
- Principales causes de panne de machine et comment les prévenir
- Comment réduire le temps de changement avec le SMED et le travail standard
- Comment réduire les coûts de camionnage