5 conseils de conception pour les pièces moulées par injection aux caractéristiques complexes
La conception pour la fabrication (DFM) est la pratique générale consistant à concevoir des pièces de manière à ce qu'elles soient également efficaces à produire. Bien que les meilleures pratiques spécifiques varient selon la technologie de fabrication, l'objectif ultime du DFM en général est d'optimiser la conception des pièces afin de minimiser les coûts de fabrication, sans sacrifier les performances ou la fonction. DFM vous aide également à identifier rapidement les problèmes ou défauts potentiels et à éviter les reconceptions perturbatrices en cours de ligne. C'est pourquoi l'évaluation des méthodes de fabrication possibles est cruciale lors des phases initiales de conception et de prototypage.
La conception intentionnelle et axée sur la méthode est particulièrement importante lorsque vous essayez de produire des pièces avec des géométries complexes ou des caractéristiques complexes. Et bien qu'il existe de nombreuses méthodes de fabrication viables pour produire des pièces aux géométries complexes, le moulage par injection est l'une des plus courantes.
Le DFM est particulièrement important pour les pièces moulées par injection, car l'outillage dur et les moules utilisés pour créer des pièces moulées par injection introduisent un certain nombre de variables qui peuvent avoir un impact sur la conception, notamment la température du moule, la température du matériau et la pression de l'air. De plus, les moules à injection sont coûteux et longs à usiner, et le processus ne devient généralement rentable que lors de la production de pièces en gros volumes. La cohérence et la répétabilité sont donc essentielles lors de la conception de pièces avec des géométries complexes ou des caractéristiques complexes.
Voici 5 conseils clés pour concevoir des pièces moulées par injection plastique avec des fonctionnalités complexes.
1. Tirez parti des fermetures coulissantes pour les clips et les ajustements rapides
Les clips et les encliquetages sont deux formes de mécanismes de fixation qui peuvent être incorporés directement dans la conception du moule d'injection - quelques exemples courants étant les couvercles d'outils et les boîtiers électroniques. Les deux fonctionnent de la même manière :d'un côté du mécanisme, une languette flexible de matériau s'accroche à une fente ou à une poche dans la pièce d'accouplement, sécurisant ainsi les deux.
Les fermetures coulissantes ou télescopiques sont des composants usinés dans un côté du moule qui s'étendent dans l'autre moitié, glissant en place lorsque le moule est fermé. Cela empêche le matériau de s'écouler dans des zones particulières, ce qui permet d'incorporer facilement des fonctionnalités telles que des crochets et des trous (y compris de longs trous traversants) sans avoir besoin d'actions latérales coûteuses, de bosses, d'inserts et d'autres fonctionnalités qui augmentent le coût et la complexité de la conception du moule.
Les fermetures coulissantes peuvent être conçues pour avoir la même languette et la même fente pour correspondre aux clips et aux ajustements rapides de la pièce, créant des fonctionnalités qui s'emboîtent solidement et conservent suffisamment de flexibilité pour se séparer sans se casser. Les arrêts peuvent réduire les coûts de conception et d'exploitation des moules et peuvent également être généralement utilisés comme solution de contournement pour les contre-dépouilles et les éléments en retrait.
En général, la pièce et le moule doivent avoir un minimum de 3 degrés de dépouille pour empêcher le métal de frotter contre le métal, ce qui peut créer un flash et endommager l'arrêt.
2. Choisissez le bon matériau pour les charnières vivantes
Les charnières vivantes, une autre caractéristique du couvercle flexible, sont un excellent moyen de fixer les deux moitiés des composants en plastique moulé par injection (pensez aux couvercles des récipients individuels d'un distributeur hebdomadaire de vitamines, par exemple).
Bien que la considération des matériaux soit toujours une considération critique dans la conception et le développement de produits, elle devrait être votre principale préoccupation lors de la conception de charnières vivantes. Le polypropylène, par exemple, est mieux adapté à cette fonctionnalité que le polycarbonate (qui peut être un excellent matériau pour les clips et les ajustements rapides). Selon l'amplitude de mouvement attendue du couvercle, vous devrez peut-être incorporer un rayon au milieu de la charnière pour permettre aux deux parties de se fermer plus facilement.
3. Gardez un œil sur l'épaisseur des murs
L'épaisseur de la paroi doit rester uniforme dans la mesure du possible, car les variations d'épaisseur peuvent entraîner de graves complications. Les pièces dont l'épaisseur de paroi n'est pas constante risquent de se déformer (causées par différentes sections de la pièce refroidissant à des vitesses différentes, ce qui crée une contrainte interne qui plie la pièce de façon permanente).
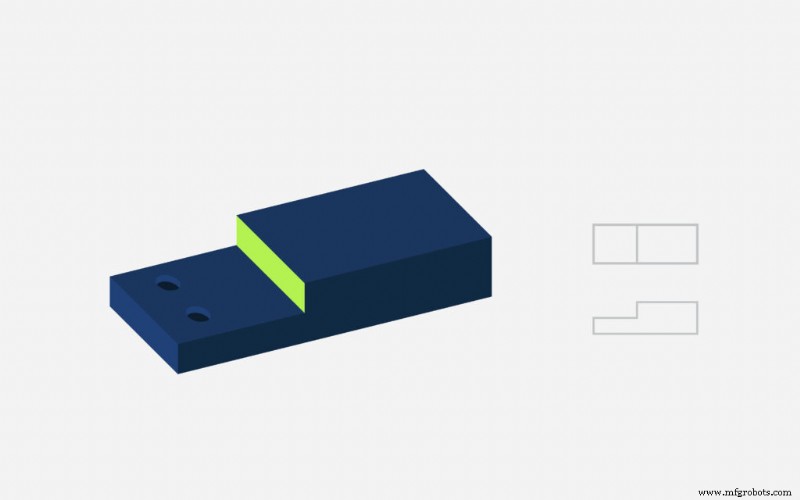
De plus, si les parois d'une pièce sont trop épaisses ou minces, d'autres problèmes peuvent survenir. Par exemple, des parois minces et des nervures de support mal conçues peuvent entraver la fluidité, provoquant des courts-circuits (ou des remplissages de moule incomplets). D'autre part, les pièces avec des parois épaisses et des nervures mal conçues sont susceptibles de développer des retassures ou des impressions sur la surface de la pièce causées par le refroidissement plus rapide de la résine intérieure que le matériau extérieur. Si vous voyez des signes de l'un ou l'autre défaut, il est peut-être temps de réexaminer la conception de votre moule.
4. Ajoutez un brouillon et réduisez la hauteur des éléments hauts
Les caractéristiques hautes telles que les bossages, les nervures et les entretoises peuvent vous obliger à incorporer des angles de dépouille plus importants (généralement jusqu'à 3°) pour garantir que la pièce quitte le moule sans lignes de traînée ou autres problèmes d'éjection. Les bossages et les éléments hauts permettent des inserts filetés et une résistance supplémentaire des pièces, mais ils augmentent le risque de développer des retassures.
De plus, l'augmentation de la hauteur des nervures et d'autres caractéristiques augmente également la profondeur du moule, ce qui augmente le besoin de fraises en bout plus longues, de plus de ventilation et de vitesses de coupe plus lentes pendant le processus d'usinage. Une façon de contourner ce problème consiste à soutenir les bossages avec des nervures verticales périphériques, qui ont des parois plus minces, ce qui réduit les risques d'affaissement.
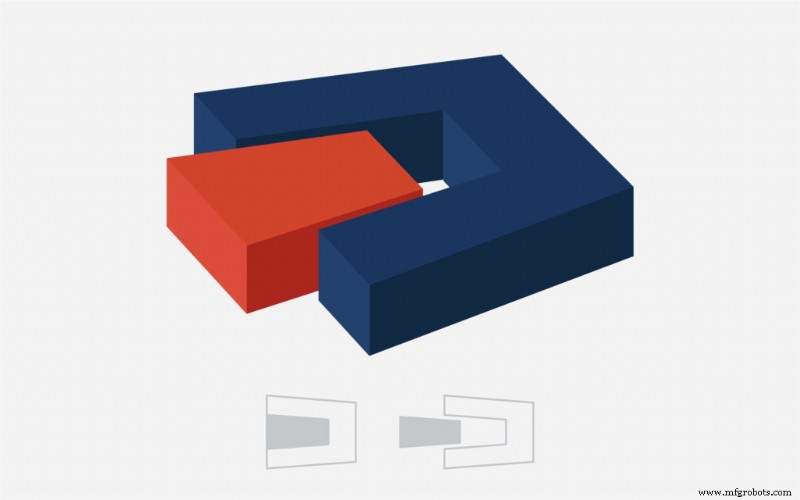
Les bossages inclinés et d'autres caractéristiques augmentent la complexité de la production, car l'axe du bossage ne s'aligne plus sur la ligne de séparation ou la ligne de traction - ce qui nécessite pratiquement qu'un insert doive être chargé manuellement dans le moule avant chaque tir.
5. Soyez stratégique sur le texte et les logos
Du texte (tel qu'un nom de produit ou de société) ou des logos sont généralement ajoutés aux produits moulés par injection. La bonne nouvelle est que les petites tailles de police sont en fait assez faciles à obtenir grâce au moulage par injection, à condition de suivre quelques directives clés.
Tout d'abord, le texte doit être une police sans empattement et la longueur de trait la plus courte (la barre transversale d'un T ou d'un A, par exemple) doit être d'au moins 0,020 pouce de longueur. Un texte en relief est plus facile à lire et à produire qu'un texte enfoncé dans la surface d'une pièce. À moins que le texte ne soit excessivement grand, il ne doit pas dépasser 0,015 pouce de haut.
Enfin, à moins que vous ne travailliez avec des matériaux flexibles comme le caoutchouc de silicone ou l'élastomère thermoplastique (TPE), le texte doit faire face à la direction de la traction si possible. Sinon, des inserts chargés manuellement ou des actions latérales pourraient être nécessaires pour assurer une éjection en douceur.
Commencez à affiner votre conception de moulage par injection dès aujourd'hui
Une géométrie complexe et un degré élevé de complexité des fonctionnalités ne sont pas la fin du monde pour les pièces moulées par injection. En prêtant attention aux facteurs de conception clés tels que la conception du moule, la sélection des matériaux, l'orientation du bossage et le style et la taille du texte, vous pourrez améliorer la fabricabilité (et donc la rentabilité) et la qualité de votre pièce en même temps.
Bien sûr, un partenariat avec un fabricant expérimenté est un autre moyen infaillible de rationaliser les phases de conception et de production du développement de produits. Fast Radius apporte des décennies d'expérience en ingénierie et en conception, et nous travaillons avec diligence aux côtés de chaque client pour nous assurer que vos pièces ne sont pas seulement bien fabriquées, mais qu'elles sont fabriquées de la manière la plus efficace et la plus rentable possible. Contactez-nous dès aujourd'hui pour découvrir comment nous pouvons concrétiser vos conceptions.
Technologie industrielle
- Apprendre à concevoir avec la série E3.pour les équipements industriels
- 5 conseils pour la conception de tôlerie
- 5 conseils de conception pour RIM
- Conseils de conception pour le moulage par coulée
- Multitâche pour les petites pièces complexes
- 5 conseils de sécurité pour travailler avec des machines
- 5 conseils pour la conception de circuits automobiles afin de vaincre les EMI
- Conseils de conception pour le moulage par injection
- Conseils de conception pour l'impression 3D par frittage laser direct de métal